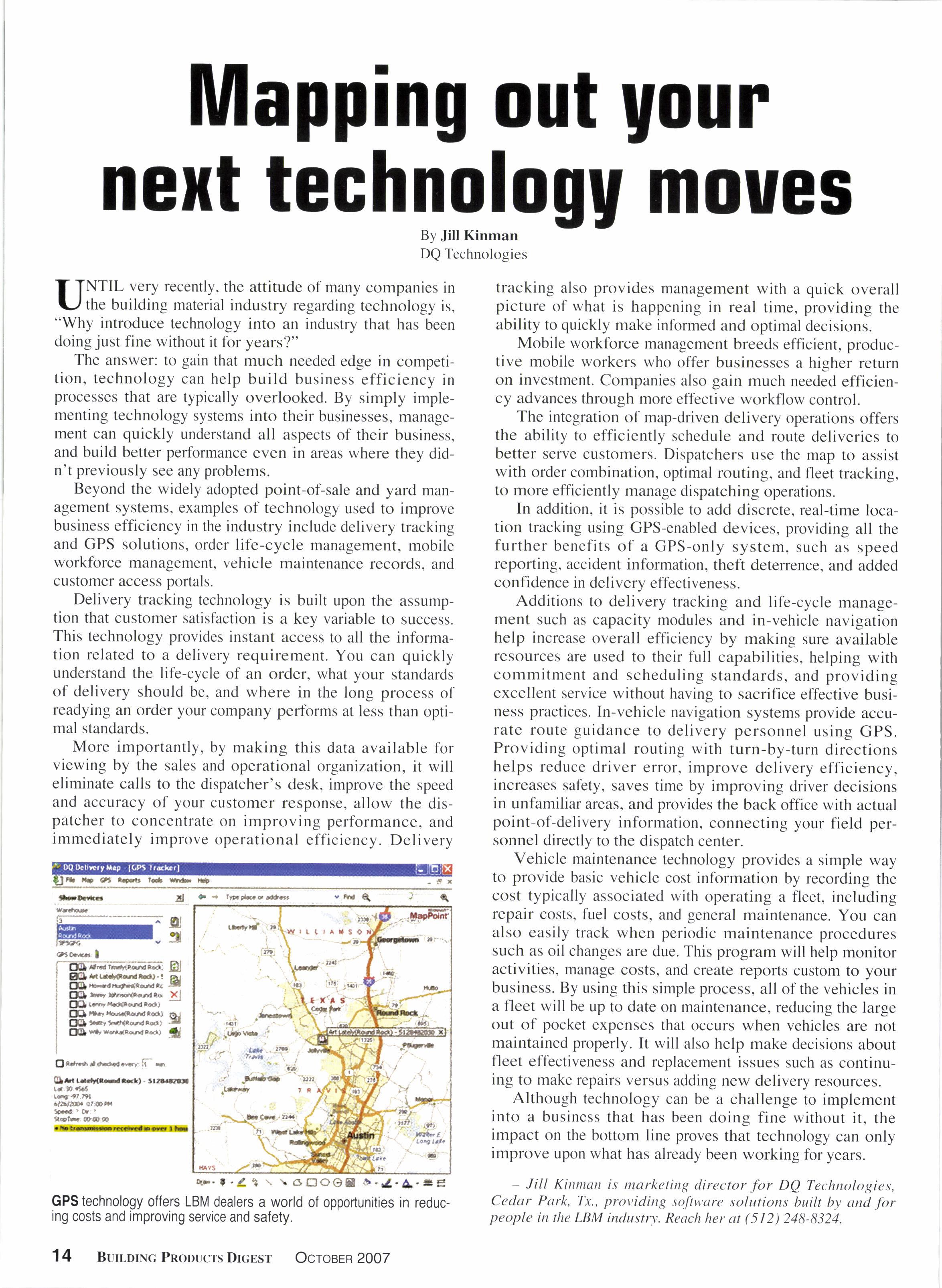
3 minute read
Mapping out Uour next technology moues
By Jill Kinman DQ Technologies
f TNTIL very recently. the anirude of many companies in lL,/ the building material industry regarding technology is, "Why introduce technology into an industry that has been doing just fine without it for years?"
The answer: to gain that much needed edge in competition, technology can help build business efficiency in processes that are typically overlooked. By simply implementing technology systems into their businesses, management can quickly understand all aspects of their business, and build better performance even in areas where they didn't previously see any problems.
Beyond the widely adopted point-of-sale and yard management systems, examples of technology used to improve business efficiency in the industry include delivery tracking and GPS solutions, order life-cycle management, mobile workforce management, vehicle maintenance records, and customer access portals.
Delivery tracking technology is built upon the assumption that customer satisfaction is a key variable to success. This technology provides instant access to all the information related to a delivery requirement. You can quickly understand the life-cycle of an order, what your standards of delivery should be, and where in the long process of readying an order your company performs at less than optimal standards.
More importantly, by making this data available for viewing by the sales and operational organization, it will eliminate calls to the dispatcher's desk, improve the speed and accuracy of your customer response, allow the dispatcher to concentrate on improving performance, and immediately improve operational efficiency. Delivery g tracking also provides management with a quick overall picture of what is happening in real time, providing the ability to quickly make informed and optimal decisions.
Mobile workforce management breeds efficient, productive mobile workers who offer businesses a higher return on investment. Companies also gain much needed efficiency advances through more effective workflow control.
The integration of map-driven delivery operations offers the ability to efficiently schedule and route deliveries to better serve customers. Dispatchers use the map to assist with order combination, optimal routing, and fleet tracking, to more efficiently manage dispatching operations.
In addition, it is possible to add discrete, real-time location tracking using GPS-enabled devices, providing all the further benefits of a GPS-only system, such as speed reporting, accident information, theft deterrence, and added confidence in delivery effectiveness.
Additions to delivery tracking and life-cycle management such as capacity modules and in-vehicle navigation help increase overall efficiency by making sure available resources are used to their full capabilities, helping with commitment and scheduling standards, and providing excellent service without having to sacrifice effective business practices. In-vehicle navigation systems provide accurate route guidance to delivery personnel using GPS. Providing optimal routing with turn-by-turn directions helps reduce driver error, improve delivery efficiency, increases safety, saves time by improving driver decisions in unfamiliar areas, and provides the back office with actual point-of-delivery information, connecting your field personnel directly to the dispatch center.
Vehicle maintenance technology provides a simple way to provide basic vehicle cost information by recording the cost typically associated with operating a fleet, including repair costs, fuel costs, and general maintenance. You can also casily track when periodic maintenance procedures such as oil changes are due. This program will help monitor activities, manage costs. and create reports custom to your business. By using this simple process, all of the vehicles in a fleet will be up to date on maintenance, reducing the large out of pocket expenses that occurs when vehicles are not maintained properly. It will also help make decisions about fleet effectiveness and replacement issues such as continuing to make repairs versus adding new delivery resources.
Although technology can be a challenge to implement into a business that has been doing fine without it, the impact on the bottom line proves that technology can only improve upon what has already been working for years.
Innovation and the abiliry to plan for the future
have been valued by Srrvrnsox Titvrssn Corvrplr.rv for more than a century. As we continue to focus on and practice these core values, we move the vision forward and proudly announce our new name: California Redwood Company. Now more than ever, that vision and our commitment to responsible and sustainable forestry means a dependable supply of consistently high qualiry lumber products into the future. Neu name. New lnok. Same great products and people.
www.ca lif orniaredwoodco.com
