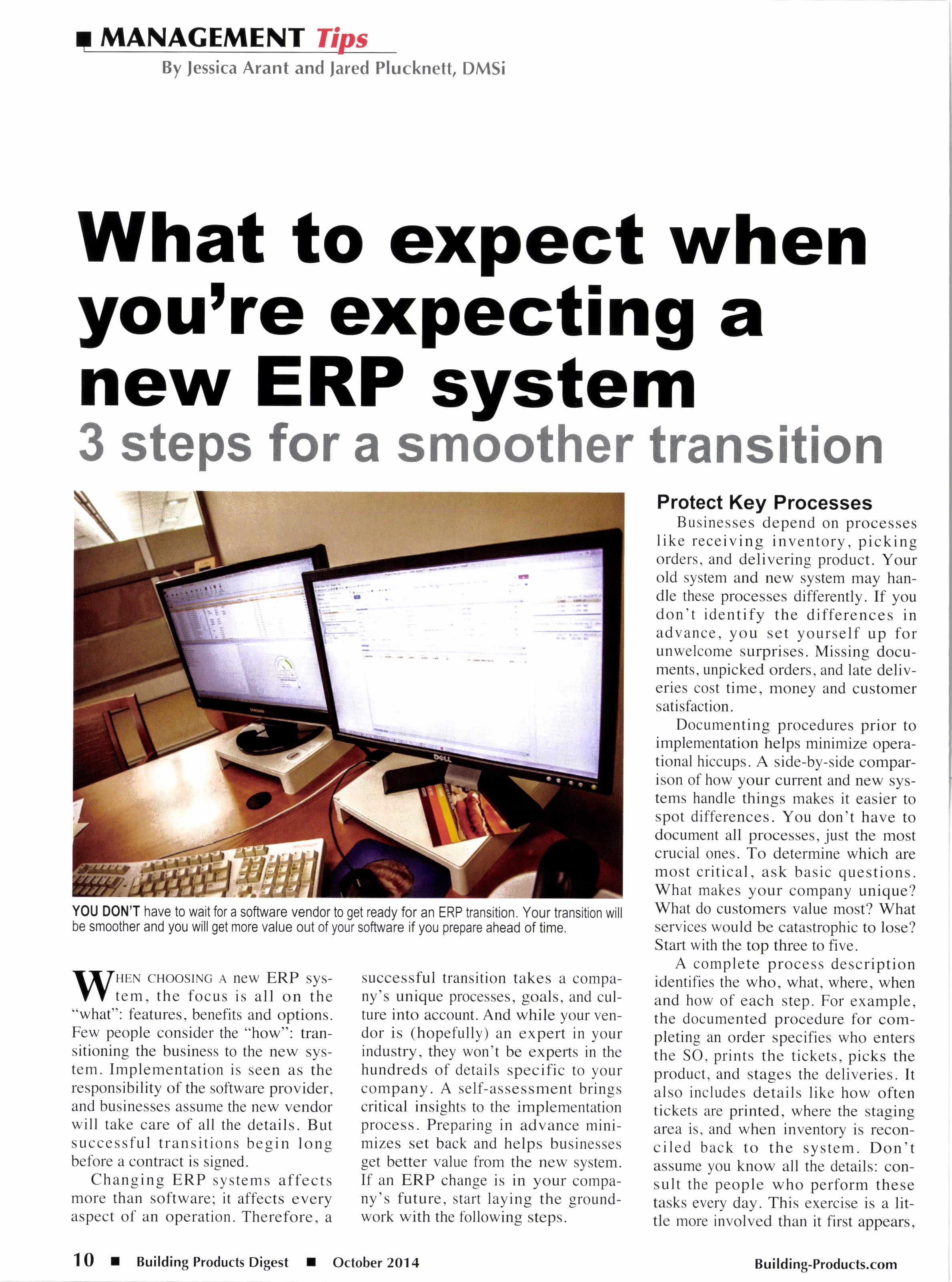
3 minute read
What to expect when youtre expecting a new ERP system 3 steps for a smoother transition
Protect Key Processes
Businesses depend on processes like receiving inventory, picking orders, and delivering product. Your old system and new system may handle these processes differently. If you don't identify the differences in advance, you set yourself up for unwelcome surprises. Missing documents, unpicked orders, and late deliveries cost time, money and customer satisfaction.
Documenting procedures prior to implementation helps minimize operational hiccups. A side-by-side comparison of how your current and new systems handle things makes it easier to spot differences. You don't have to document all processes, just the most crucial ones. To determine which are most critical, ask basic questions. What makes your company unique? What do customers value most? What services would be catastrophic to lose? Start with the top three to five.
ff,/Hrru cHoostNc e new ERP sys-
V Y tem, the focus is all on the "what": features, benefits and options. Few people consider the "how": transitioning the business to the new system. Implementation is seen as the responsibility of the software provider, and businesses assume the new vendor will take care of all the details. But successful transitions begin long before a contract is signed.
Changing ERP systems affects more than software; it affects every aspect of an operation. Therefore, a successful transition takes a company's unique processes, goals, and culture into account. And while your vendor is (hopefullyl an expert in your industry, they won't be experts in the hundreds of details specific to your company. A self-assessment brings critical insights to the implementation process. Preparing in advance minimizes set back and helps businesses get better value from the new system. If an ERP change is in your company's future, start laying the groundwork with the tbllowing steps.
A complete process description identifies the who, what, where, when and how of each step. For example, the documented procedure for completing an order specifies who enters the SO, prints the tickets, picks the product, and stages the deliveries. It also includes details like how often tickets are printed, where the staging area is. and when inventory is reconciled back to the system. Don't assume you know all the details: consult the people who perform these tasks every day. This exercise is a little more involved than it first appears, your current system and imported into your new one. Before importing the data, there's an opportunity to update and standardize it. This is where you can improve the quality.
Pick ticket is automatically printed in the warehouse.
Spend some time documenting the kinds of data problems you currently have. Make sure you involve representatives from sales and purchasing in these discussions. Create standards for naming items, entering attributes, and organizing customer records. Keep a master document of these standards for reference. There will probably be exceptions to every rule. Some items won't fit neatly in the new guidelines. That's why you want to start developing the rules in advance. It will take a while for outliers to reveal themselves, and you'11 probably revise the standards a few times. Allowing plenty of time for this process means you'll be more likely to end up with a solid system that works for your business.
Manage Your Managers
about what to expect during the adjustment: slower employees, lower production levels, longer turnaround times. They'll need to be patient during this time period. Emphasize that these are temporary conditions. Highlight the benefits that will come when everyone masters the new ERP system, like faster processes, less busywork, and fewer errors. Preparing managers ahead of time will make them more likely to stay positive during setbacks. This applies to all levels of the organization. Mid-level managers will feel less pressured if the executive team actively supports the change and demonstrates patience. Conversely, if the c.e.o. keeps complaining about lower production, it will be difficult for anyone to keep a positive attitude.

Warehouse supervisor assigns ticket to first available picker.
BEFORE IMPLEMENTATION, document and compare how your existing system and your new system handle key processes.
so it's vital to start well in advance of switching to a new system. Waiting until the implementation begins means you'll be pressed for time and more likely to overlook something.
Glean Your Data
Information is the lifeblood of a business. The simplest transaction requires pricing. inventory. payment and account records. Unfortunately, most businesses have less-than-perfect data. Inconsistent naming systems. duplicate records, and missing information are common. A business might have three different product codes for the same l0-ft. piece of southern pine: 0204 10SYP, 24l0pine, and 2410StPn. Poor data quality affects every aspect of an operation, from order entry to picking to dispatch.
Your ERP transition is an opportunity for a clean start. As part of the change, data will be exported from
No matter how amazing an ERP system is, business operations will temporarily slow during the transition. It's not just learning new software. Some of your employees have been doing their jobs in a certain way for years. Changing their methods will be challenging and take time. Unrealistic expectations about a fast, easy switch impede progress as impatient managers spread discontent through their departments. Successful transitions require support from the top down. Make sure manasers are clear
An ERP implementation is a window of opportunity. Decisions during this time can bring significant improvements to an organization. Asking an outside vendor to make all those decisions for you wastes the opportunity. Assessing your operation in advance means you will come to the implementation process with clear goals and objectives. It will help get the maximum return on your software investment.
By lan Falivene, Weyerhaeuser