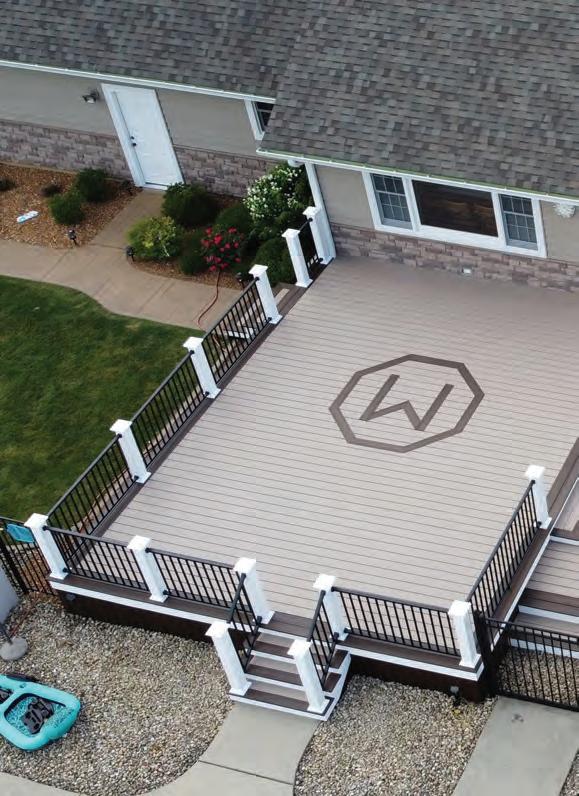
4 minute read
“W” for the Win
A “W” for the Win
How One Builder Matched Its Customer’s Needs With Their Personality
By Sara Graves
AN AERIAL VIEW of The North American Deck and Railing Association (NADRA) 2nd Place winner, Refinished/ Restored Deck 2020. (Photo by Mitchell Construction).
When Mitchell Construction began
building a deck in Manhattan, IL., the homeowner had two concerns in mind: make the decking maintenance free and reuse the main structure. However, with a few strategically placed inlays, and some very personal touches, the deck became a showstopper.
“Maintenance of a home is a daunting task. People are interested in building products that reduce the time and money spent on upkeep. This project started with that same mindset,” said Mike Mitchell, owner of Mitchell Construction in Monee, IL. “The customer was done with sanding and staining wood and wanted something ‘maintenance free.’”
Trex, in color Trex Transcend Rope Swing, was chosen as the best low-maintenance product for the main decking. Grooved boards were chosen for most of the deck, and solid boards for along the outer picture frame border and on the stairs.
And since Mitchell is not a fan of butt seams in the field boards of decking, he worked with the homeowner to not only address the butt seams, but also add a few personal touches to reflect the homeowner’s personality.
It was decided that an octagon “M” inlay in the center of the deck, which represents the first letter of the customer’s last name, would address both needs.
“The octagon started out as a breaker to keep the upper section under 20 ft.,” Mitchell said. “But if you look at the inlay from the other side, it’s a ‘W’ for Win, depending on the season the Cubs are having,” he joked, referring to the customer’s love of the Chicago Cubs. “We were happy to letter up their deck.”
Ironically, some adjustments to the design of the upper deck made the octagon unnecessary in terms of butt seams, but by then the inlay in the color Trex Transcend Spiced Rum had become an important part of the project.
“It was able to stay in purely for aesthetics,” he said. “It really gave some sentimental value to the deck.”
To create the unique inlay, Mitchell made a cardboard template to help with the location of the backing blocks. A track saw was used to cut out the shapes once the main decking was
installed. A multi tool with a wood blade was used to finish the cuts.
A second inlay was installed on the lower deck.
“To reduce the butt seams, we installed a board going in a different direction that ‘sectioned off’ the decking to be under 20 ft.,” Mitchell said. “In this case, the lower deck had the accent color running through as a breaker board which we continued along to define the fire table space.”
An important consideration in adding new framing to the customer’s existing framing on the lower deck was that the existing framing had dried out over time and lost some of its height.
“Any time you add new framing next to existing framing that has naturally dried out over time there can be a height issue. You can’t just rip the new framing down to be the same size as the existing because the new joists will eventually dry out and shrink in height too,” Mitchell said. “If you rip it to fit, after the new wood dries out you will have an uneven deck.
Mitchell said its important to pick the driest lumber and grade it as close as possible to the nearby framing. Then hold the top of the framing even and structurally fasten the new wood to the old, which will help keep the deck flat and forces the shrinking to happen on the bottom of the frame.
"We had similar challenges with the framing added for the picture frame borders and the inlays.”
After the framing was set, a layer of Trex Protect joist tape, which comes in 1-5/8" for the single joists, and 3-1/8" for double joists, beams, and blocking, was installed to maximize the deck’s lifespan. Finally, a few joist hangers were added where missing, and some structural screws were also installed to make sure the deck was safe.
The beauty of the design, Mitchell said, is that the octagon allows future owners to change out the inside with minimal damage. It would be a fairly easy remodel if they wanted to fill it in or add a different design inside the octagon.
By the time the project was done, it came in under $50,000, featured 1,400 sq. ft. of decking and 100 lineal ft. of railing, and included two levels, four sets of stairs, 20 lighted post caps, 14 stair riser lights, and vertical skirting to close off the bottom of the deck.
“I really loved the creative freedom I was given on this project,” Mitchell said. “The customer had some things on the ‘must have’ list, and we had an existing frame to work around, but we still were able to completely transform the space to fit all the needs and wants while maintaining functionality and performance for the deck to last.”
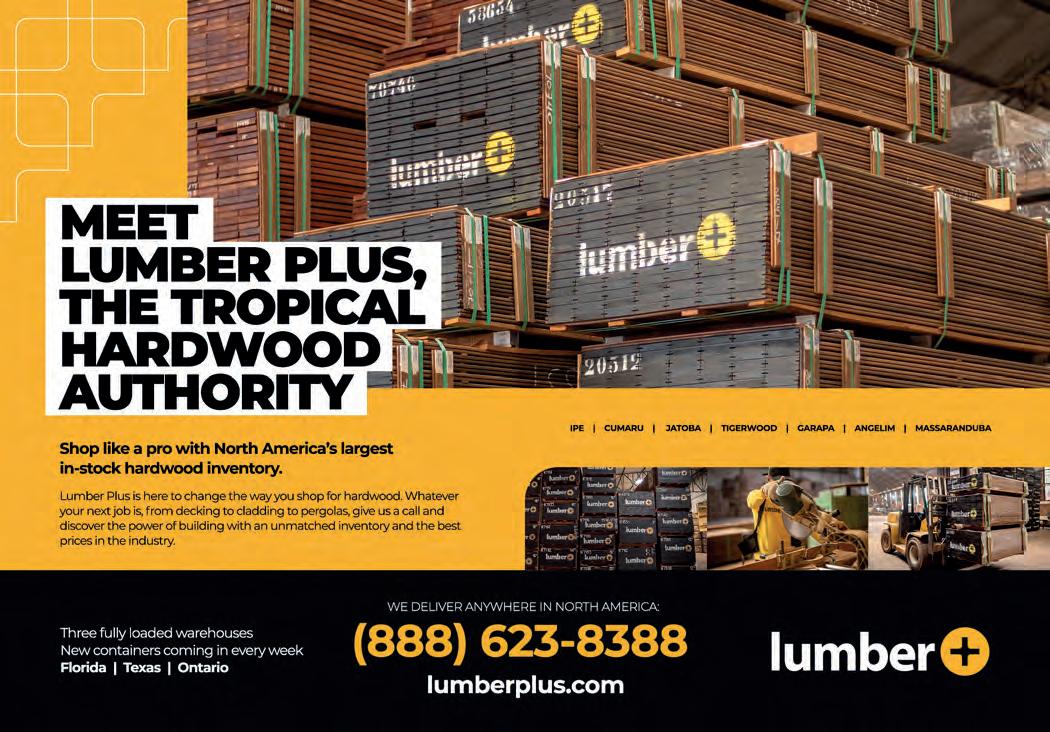