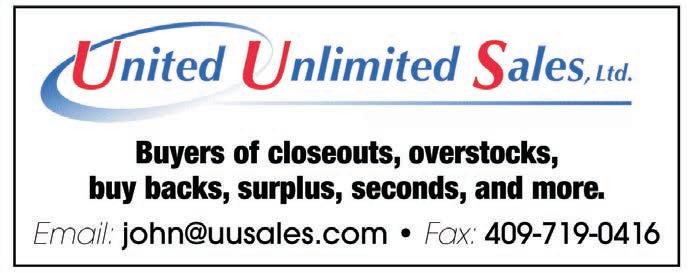
8 minute read
FLASHBACK
from BPD October 2021
Rates: $1.20 per word (25 word minimum). Phone number counts as 1 word, address as 6. Centered copy/headline, $9 per line. Border, $9. Private box, $15. Column inch rate: $55 if art furnished “camera-ready” (advertiser sets type), $65 if we set type.
Deadline: 18th of previous month. Questions? Call (714) 486-2735.
WANTED TO BUY WANTED TO BUY
IN Memoriam
Robert Charles “Rob” Grost, 61, outside salesman with Midwest Timber, Edwardsburg, Mi., died Aug. 19, shortly after being diagnosed with leukemia.
He spent over 40 years in the lumber business. Rob worked for Progressive Affiliated Lumbermen (PAL), Grand Rapids, Mi.; Quality Wood Treating, Lansing, Mi.; and Central Michigan Lumber Co., St. Johns, Mi., before joining Midwest Timber in 2005.
John R. “Rusty” Fuqua, 61, co-owner of Fuqua Sawmill, Ocala, Fl., died Sept. 3. He worked for the family business for more than 40 years.
Benny Eugene Bowers, 82, former owner of Bowers Lumber Co., Thomasville, N.C., died Aug. 4.
He spent many years as an outside sales rep with Cox Wood Preserving Co. before taking over the family lumberyard.
Joseph Berry “Joe” Kelly, 75, CEO and co-owner of PJ Lumber Co., Prichard, Al., died Sept. 1.
He helped found the company in 1977 and most recently operated it with partner Fred Wilson.
SLB, USDA Intensify Promotion of Wood Products
The Softwood Lumber Board signed a Memorandum of Understanding that builds upon its relationship between with the U.S. Department of Agriculture to grow demand for wood products as natural climate solutions. The organizations will jointly explore and coordinate additional market development, research, technological advances, and other activities to expand the use of wood in the built environment.
“Since signing the original MOU in 2015, the SLB and USDA have proudly worked together on many notable initiatives to promote and grow markets for softwood lumber in residential, commercial, and multifamily construction. We look forward to continued collaboration and cooperation for the benefit of the entire softwood lumber industry,” explained Caroline Dauzat, owner of Rex Lumber and SLB chair. “Together, we’re working to accelerate the adoption of innovative wood building system solutions through strategic investments and partnerships in training and support of educational opportunities for construction professionals, sawmills in regions that have lost infrastructure, carbon and climate change resources, and the continued joint funding of WoodWorks.”
Through increased partnerships and co-funding of joint initiatives, the SLB and USDA will achieve shared goals and objectives and deliver them at a rate that is more efficient and effective than working separately. Key initiatives to accelerate adoption of innovative wood building solutions include: • Continuing joint funding of WoodWorks, a free provider of education and technical support related to the design, engineering and construction of commercial and multifamily wood buildings in the U.S. • Promoting carbon-sequestering wood as a means to mitigate climate change through responsible material selection. • Developing initiatives to expand understanding of embodied carbon, life cycle assessments, and the connection to forest management and wood construction. • Creating events to expand connections with large corporations who can use wood products to meet their sustainability goals. • Supporting university and young professional education programs by highlighting the benefits of forests and forest products and how to design and build with them. • Establishing support programs for real estate developers and owners by removing or addressing market barriers to using wood products in new market segments. • Exploring strategies and connections to sawmill investment for locations that have lost infrastructure.
“Transforming buildings from carbon emitters to carbon sinks by incorporating sustainably harvested and produced wood products from public and private timberlands benefits the environment and the economy more effectively than many other climate solutions currently available. This MOU symbolizes the positive impact that industry and government can have when they align on a common ambition and the strategy to achieve it,” said Cees de Jager, SLB president and CEO.
The MOU was signed on Sept. 14 during a quarterly WoodWorks board meeting, an organization that the SLB and USDA jointly fund.
NORTH CAROLINA RELOAD Shaver Reload,
Statesville, NC
• Norfolk Southern Mainline Served • Easy Access to I-85, I-77 & I-40 • Company Owned Truck Fleet • Outdoor and Indoor Storage • 12 Acres Fenced with Security Lighting • 25+ years Reload Experience
(704) 872-3148 • Fax (704) 872-3146 Email Tom Lakeman shavers.reload@gmail.com
Page 60 Amerhart www.amerhart.com
53
57
75
49
85
54
86
43 Avon Plastics www.turboclipusa.com
Bennett Lumber Products www.blpi.com
Boozer Beam www.boozerbeam.com
CMPC www.cmpcmaderas.com
Coastal Forest Products www.ironwoods.com
Coastal Plywood www.coastalplywood.com
Crumpler Plastic Pipe www.cpp-pipe.com
CT Darnell Construction www.ct-darnell.com
47
77
65
34
87
55
Cover II
69
59 DMSi www.dmsi.com
Durgin & Crowell Lumber Co. www.durginandcrowell.com
Elk Creek Forest Products www.elkcreekforest.com
Everwood Treatment Co. www.everwoodtreatment.com
526 Events www.526.events
Forest City Trading Group www.fctg.com
Great Southern Wood Preserving www.yellawood.com
Hardel Mutual Plywood Corp. www.hardel.com
Hoover Treated Wood Products www.frtw.com
72
Cover III
19 Jordan Lumber www.jordanlumber.com
Koppers Performance Chemicals www.kopperspc.com
Lee Roy Jordan Lumber Co. www.lrjlumber.com
25
Cover I, 36 LMC www.lmcdifference.com
Lonza Wood Protection www.wolmanizedwood.com
7
39 Manufacturers Reserve Supply www.mrslumber.com
Maze Nails www.mazenails.com 71
67 North American Wholesale Lumber Assn. www.nawla.org
Northeastern Lumber Manufacturers Assn. www.nelma.org
17
30 Orgill www.orgill.com
a ifi d e h pa ifi d e h m
21, 23
33 Palram Americas www.palram.com
Pennsylvania Lumbermens Mutual Insurance www.plm.com
51 PPG ppgprefi nished m
27, Cover IV Redwood Empire www.buyredwood.com
79 Robbins Lumber www.rlco.com
41
61
3
29
64
76
28
81
45
46
83 RoyOMartin www.royomartin.com
Seneca Sawmill www.senecasawmill.com
Simpson Strong-Tie www.strongtie.com
Siskiyou Forest Products www.siskiyouforestproducts.com
Snider Industries www.sniderindustries.com
Southern Forest Products Association www.sfpa.org
Stella-Jones www.stella-jones.com
Swanson Group Sales Co. www.swansongroup.biz
Timber Products www.timberproducts.com
TIVA Building Products www.tivabp.com
Utah Lumber Co. www.utahlumber.com
5 5
73
9
63
72 West Fraser West Fraser www.westfraser.com/osb www.westfraser.com/osb
Westervelt Lumber www.westerveltlumber.com
Weyerhaeuser www.weyerhaeuser.com
Wild Hog www.wildhogproducts.com
Yakama Forest Products www.yakama-forest.com
58 Years Ago This Month
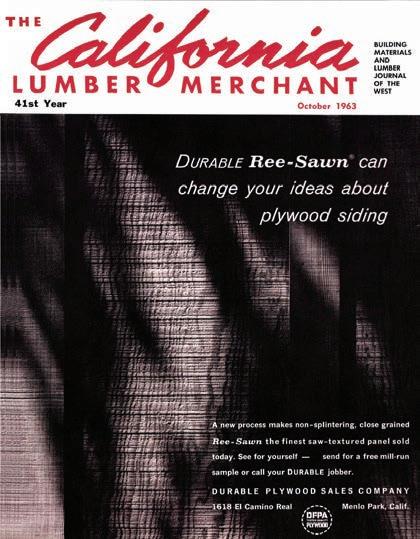
Fifty-eight years ago this month, in October of 1963, BPD’s sister publication, The California Lumber Merchant, covered a slew of technological and design innovations, as forest products companies ramped up their research and development efforts to better serve the ongoing building boom.
Perhaps most notably, Weyerhaeuser Co. unveiled the fi rst commercially marketed, completely prefi nished wood siding.
The new product carried a written performance warranty that the siding would not require repainting for at least seven years and that the factory-applied paint film would never peel or blister. It was initially offered in two sizes of beveled siding (1/2x 8 and 3/4x10) in five light colors (Super White, Seafoam Green, Golden Yellow, Silver Grey, and Desert Sand).
E.M. Williston, technical director for softwood lumber, described the fi nish as a two-coat “breathing paint” of 4-mil thickness. The fi rst coat consisted of blister-resistant baking alkyd resin primer, the same as that on their Primewood siding introduced early in 1962.
The finish coat was a bakedon acylic resin described as “an
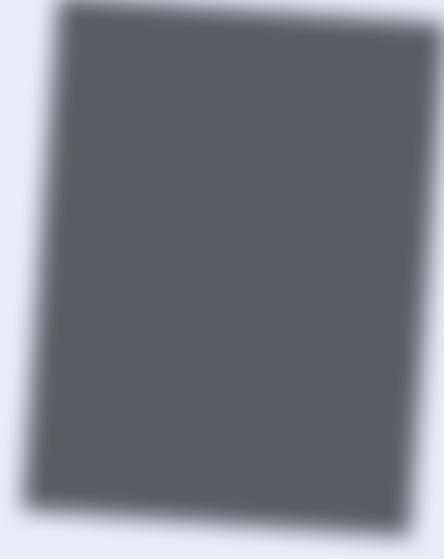

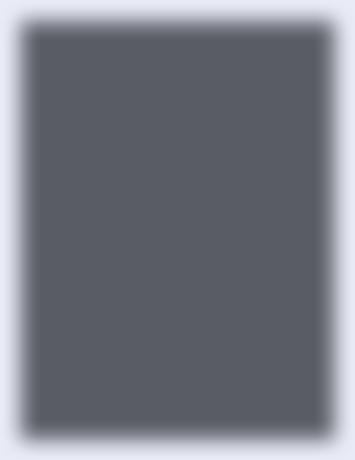
IN THE EARLY 1960s, aerospace industry aerospace industry supplier Rocket Chemical Co. expanded the marketing of their fl edgling rust-prevention degreaser WD-40 to sawmills, through ads in The California Lumber Merchant. THE OCTOBER 1963 issue of The California Lumber Merchant announced the debut of Durable Plywood Sales Co.’s extra-durable Ree-Sawn brand plywood siding. issue
exclusive Weyerhaeuser formula” four years in the making.
Along with the siding, Weyerhaeuser also introduced matching nails with baked-on enamel, plastic snap-on hammer caps to guard against marring paint, prefinished outside metal corners, touch-up paint, and matching PuttyStik pencils for coating cut ends.
The new prefinished siding was priced at about two-thirds more than unfinished vertical grain material. “This means,” Williston said, “that prefinished siding will cost about $100 to $200 more for the average house for material, but this is off set by the savings in painting costs. Most important, the factory prefi nish assures better appearance, longer service life of the paint surface, and less maintenance.”
In other news of October 1963: • Union Lumber Co., Fort Bragg, Ca., became the fi rst member mill of the California Redwood Association to introduce redwood glulam beams.
Branded as “Noyolam,” the beams were offered in sizes from 3x4 up to a “huge” 11x16, in lengths up to 40 ft. Each beam featured up to 20 laminates, each at least 1” in thickness. They also boasted top architectural grade redwood, a waterproof exterior adhesive, and dimensional stability aff orded by kiln drying.
Targeted applications included ridge and roof elements, carports, wide entryways, headers and posts.
“We think we’ve combined the flexibility features of glulams with the proven advantages of kiln dried redwood,” noted VP of sales Sherman Bishop. “And we’re anticipating a good future for the Noyolam in the building industry.”
• National Gypsum announced plans to build its first production facility on the West Coast—a $5-million gypsum wallboard plant in Richmond, Ca.
The facility opened the following summer and is still in operation.
• A record 10 billion bd. ft. of timber was cut from National Forests in fi scal year 1963, a 1 billion bd. ft. jump over the preceding year. The nation’s highest cut was on National Forests in Oregon (3.1 billion bd. ft. from 13 forests), followed by Washington (1.5 billion ft.) and California (1.4 billion ft.).
The harvest included over 1.3 billion bd. ft. of storm-damaged timber, primarily resulting from a devastating storm on Columbus Day 1962 that ravaged the Pacific Northwest.
“Prompt salvage of this valuable timber not only will prevent great monetary losses, but will help fire hazard and risk of further damage from insects and disease in the storm area,” said U.S. Secretary of Agriculture Orville L. Freeman.
For comparison, in fiscal year 2020 about 2.5 billion bd. ft. was harvested from National Forests.