
3 minute read
MARGIN BUILDERS
from BPD July 2021
What dealers should know about selling open-joint cladding systems
Open-joint claDDing systems are growing in popularity—but they require a slightly diff erent approach to the walls behind them.
Open-joint cladding looks exactly as it sounds—siding (usually composite deck planks, exotic hardwoods, or reclaimed barnwood) installed with wider gaps between each board, creating a fresh aesthetic currently catching the eye of architects, designers, and homeowners. While this trend originally began in the commercial sector, it’s catching on in residential applications.
The key to making these systems successful comes down to the durability of the materials as well as the installation details of the envelope itself. For open-joint cladding, the challenge is right in its name: the wider space between the boards, which subject the interior of the wall system to in-
DESIGNED specifi cally for open-joint cladding applications, this UV-rated rainscreen wall system features Benjamin Obdyke’s InvisiWrap UV black housewrap, HydroFlash UV+ fl ashing, and Batten UV rainscreen. The products work together to provide 25+ years of UV exposure behind open siding and can be left exposed for a full year ahead of cladding install. creased exposure to UV rays and moisture. Dealers should recognize that customers may have to adjust the materials they use behind the walls to prevent failures.
WRB Considerations Behind Open-Joint Cladding
Architects often specify a black housewrap behind the open-joint cladding to further enhance the visual appeal. But that doesn’t make this a job for asphalt-based felt paper. When left exposed, felt material may become brittle and fall apart.
Instead, a UV-resistant housewrap that also comes in black can protect against the long-term exposure while also increasing drying potential and protecting against moisture.
Along with UV rays, open-joint systems also are more vulnerable to moisture, as more air and water can get past the primary cladding than with traditional siding installation methods. Cap fasteners should be used to better block water from getting behind the WRB; ideally in this type of installation, cap fasteners should be installed behind the furring strips. Taping all seams in this type of assembly also is crucial.
Builders also will need to consider vapor permeability. With open-joint cladding systems, materials are naturally exposed to atmospheric pressures and humidity levels, which can cause a higher risk of vapor being driven inside the wall system, especially in Southern climates. Typically, the perm rating of the weather resistive barrier and fl ashing materials should be between 10-20 perms for these applications; this range provides breathability while resisting excess moisture from entering the wall assembly.
Even with these installation keys in mind, aesthetics is still part of the conversation, as installers will need to consider what’s showing up in the spaces between siding boards. Combatting potential issues starts in the planning stages by outlining the placement of overlaps and fasteners. This can help reduce their visibility once the cladding is installed, maintaining the visual appeal of the system.
The trend of open-joint cladding likely isn’t going away anytime soon. Dealers can help customers address the nuances of this building system by guiding them toward the right materials and installation techniques that help ensure a long-lasting, durable building envelope.

REDWOOD
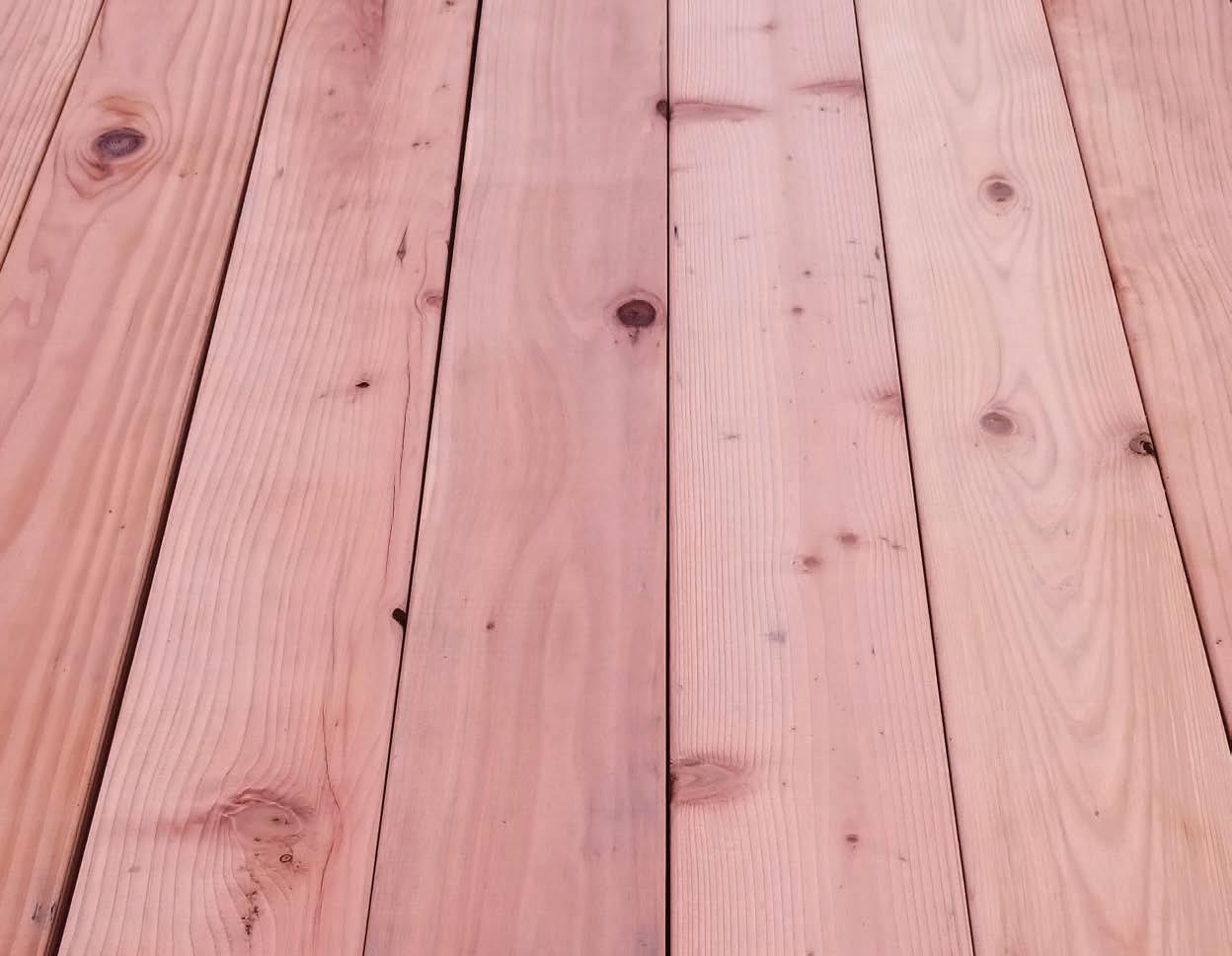
Composite can’t compare.

Like the foods we buy, when it comes to decking, we want natural and real. Redwood is always available in abundance of options. So stock the shelves! Unlike mass-produced and inferior products, Redwood is strong, reliable and possesses many qualities not found in artificial products. They maintain temperatures that are comfortable in all climates.
Redwood Empire stocks several grades and sizing options of Redwood.
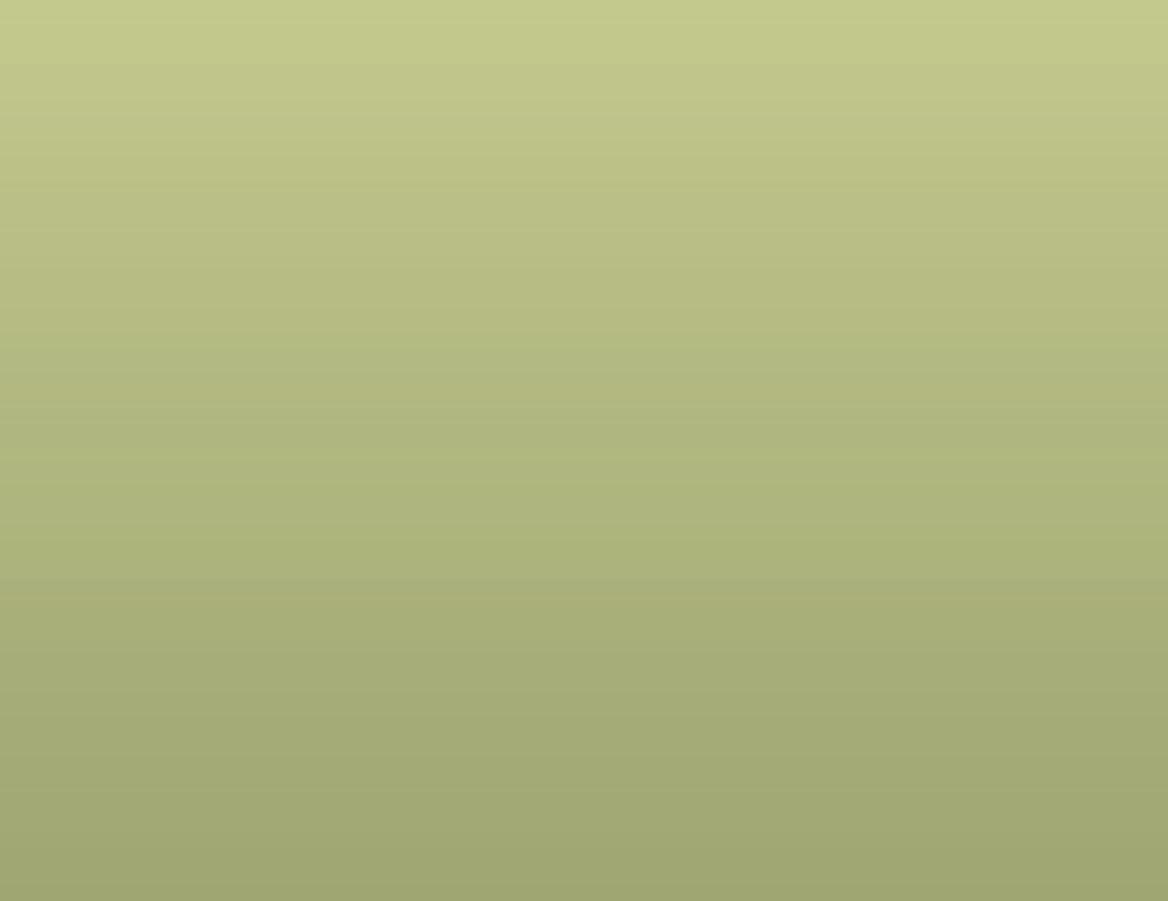
Call us at 707.894.4241
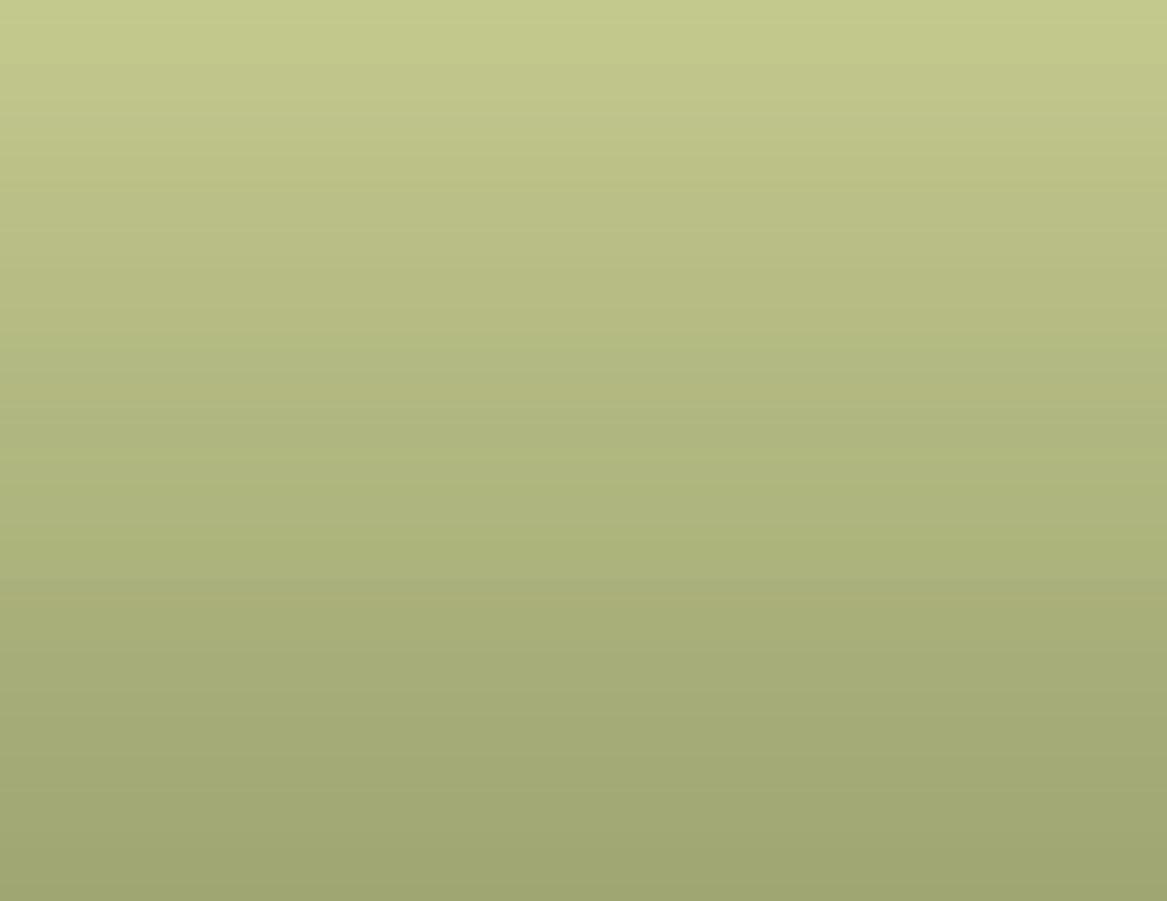