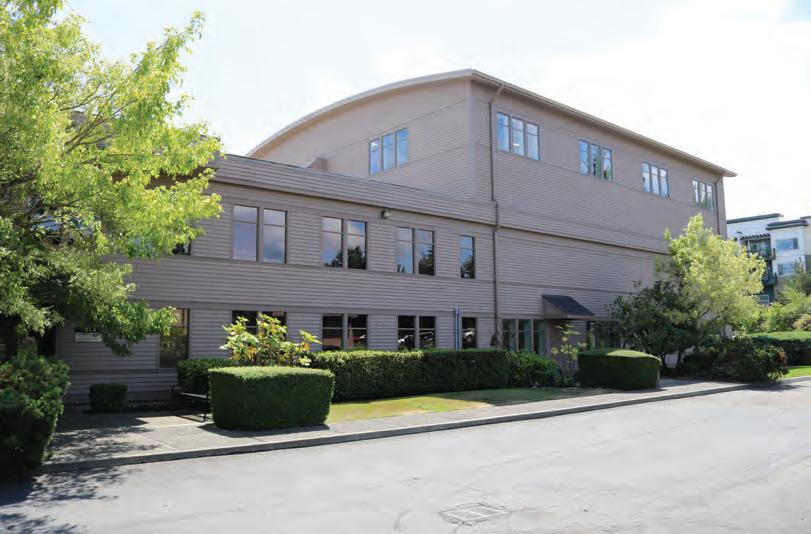
27 minute read
apa On eWp
from BPD July 2022
ONGOING UPGRADES to APA’S wood research and testing facilities in Tacoma, Wa., help the association set the industry’s highest standards to support innovation design and construction. (Images courtesy APA)
Testing 1-2-3
A historical overview of the APA Research Center
Apa – the engineered Wood Association’s Research Center in Tacoma, Wa., has long been recognized as one of the leading wood research facilities in North America. That position has strengthened over the years as facility expansions provide support for new and existing research and testing on engineered wood products and construction systems for the industry.
Today, the association’s 42,000-sq. ft. research center is a state-of-the-art laboratory equipped with modern research and testing equipment and staffed by experienced engineers, wood scientists and engineering technicians.
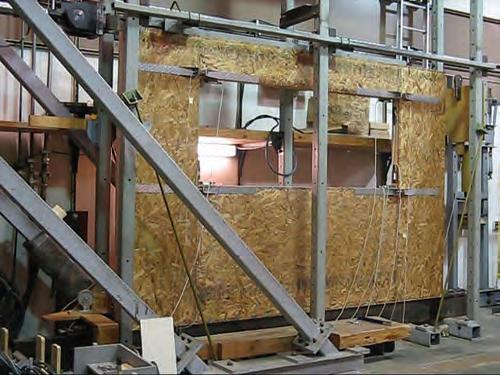
Where It Began – Plywood Panels & Glulams
Built in 1969, the original 37,000-sq. ft. APA Research Center was constructed for testing of typical-sized 4-ft. by 8-ft. plywood panels. As the demand for full-scale tests on modern engineered wood products grew, the building was renovated in 1990 to accommodate other engineered wood products, such as 6-ft. deep by 72-ft. long glulam beams.
Full-Scale Wall Bracing & Combined Shear & Wind Uplift Testing
With the trend toward full-scale structural testing, an extension designed for single-story house tests and test material storage was added to the research center in 2006. The research center extension was completed amid heated debates for wall bracing requirements under the International Residential Code (IRC). APA conducted several series of fullscale single-story house tests to support APA’s and industry’s position on the revisions of wall bracing requirements that were eventually published in the 2009 IRC. Subsequent tests continued for a few years until the completion of the 2012 IRC.
APA focused on full-scale combined shear and wind uplift tests in 2007 and 2008 to show the superior performance of wood structural panels (plywood and OSB) when compared to other competing materials. Results obtained from
those studies supported the 2008 publication of APA System Report SR-101, Design for Combined Shear and Uplift from Wind, which was also adopted by the 2008 ANSI/AWC Special Design Provisions for Wind and Seismic (SDPWS).
Force Transfer Around Openings Tests
In 2009 and 2010, APA conducted a series of full-scale shear wall tests to provide recommendations for the design of wood-framed shear walls with the methodology of force transfer around openings (FTAO) when wood structural panels are used. This study was a collaboration between APA, the USDA Forest Products Laboratory and the University of British Columbia, under partial funding support of the USDA and the Engineered Wood Technology Association (EWTA). The test results provide recommendations for FTAO design when shear walls are constructed with wood structural panels in high seismic zones, such as California, Oregon and Washington.
Full-Scale In-Grade Structural Glulam Testing
From 2011 through 2015, APA conducted full-scale ingrade testing for structural glued-laminated timber (glulam). Results obtained from those tests validated the current glulam design values and responded to the occasional criticism of the lack of systematic full-scale glulam performance data.
I-Joist Diaphragm Design Values
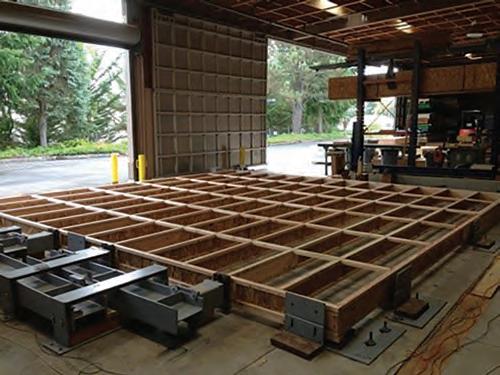
TESTING of a full-scale (24-ft. by 24-ft.) diaphragm using I-joist framing to establish diaphragm design values in light-frame wood construction. INTERIOR of upgraded APA Research Center high bay with new testing capabilities.
In 2016, APA conducted a series of full-scale (24-ft. by 24-ft.) diaphragm tests with I-joist framing on behalf of APA I-joist members. The tests were used to establish the diaphragm design values for common diaphragm configurations used in light-frame wood construction. Results obtained from these tests served as the recognition of I-joist diaphragms for APA I-joist members in APA Product Reports or the evaluation reports (ESRs) jointly issued by the ICC Evaluation Service (ICC-ES) and APA.
Full-Scale Shear Wall Testing of Flexible Structural Sheathing
APA conducted full-scale shear wall tests from 2015 through 2018 on eight flexible structural sheathing materials randomly sampled from the marketplace. Similar tests were also independently conducted at Clemson University and the University of Oklahoma. Results obtained from a combination of about 90 full-scale shear wall tests showed a substantial deficiency (up to 42%) to the published design values for the tested flexible structural sheathing materials. This information is documented in the APA Product Advisory SP-1186, Performance of Flexible Structural Sheathing (Independent Evaluations of Published Design Values).
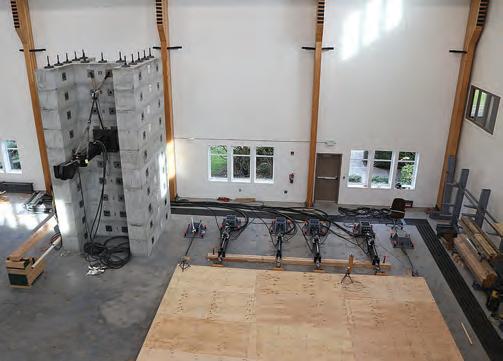
APA Research Center High-Bay Laboratory
Recognizing the trending demand for more full-scale, or even three-dimensional (3D) assembly tests to reflect the growing complexity in timber structures, APA members authorized the construction of a high-bay laboratory at the APA Research Center in 2018. This new laboratory was completed in 2019 by deconstructing a 70-ft. by 75-ft. (5,250 sq. ft.) section of the research center and constructing a new 40-ft.tall open floor (no columns between exterior walls) high-bay laboratory from the ground up.
The building itself is a demonstration of wood’s strength. It is built with laminated veneer lumber studs and purlins and glulam columns supporting a roof structure framed with curved glulam beams. Wood structural panel sheathing was used on the walls and roof, and OSB lap siding was used as the exterior cladding.
The high-bay lab was constructed with a 4-ft.-deep heavily reinforced concrete floor slab using 28 tons of steel rebar and 830 tons of concrete. There are 868 floor inserts with a 100,000-lb. capacity each on the floor at 2 ft. on center. The lab’s ceiling height can readily accommodate a two-story structure for testing.
Looking Ahead
The recent and ongoing upgrades to APA’s research and testing facilities assist APA in setting the industry’s highest performance standards as it continues to support innovative design and construction of timber structures using wood structural panels, engineered wood products and mass timber assemblies.
Currently, a study plan is under development at APA to conduct 3D assembly tests by 2023 to better characterize the performance of wood buildings framed with engineered wood products and sheathed with wood structural panels.
Learn more about APA’s state-of-the-art laboratory and research and testing capabilities by visiting www.apawood. org/technical-research.
– Dr. Borjen Yeh is director of technical services at APA – The Engineered Wood Association.
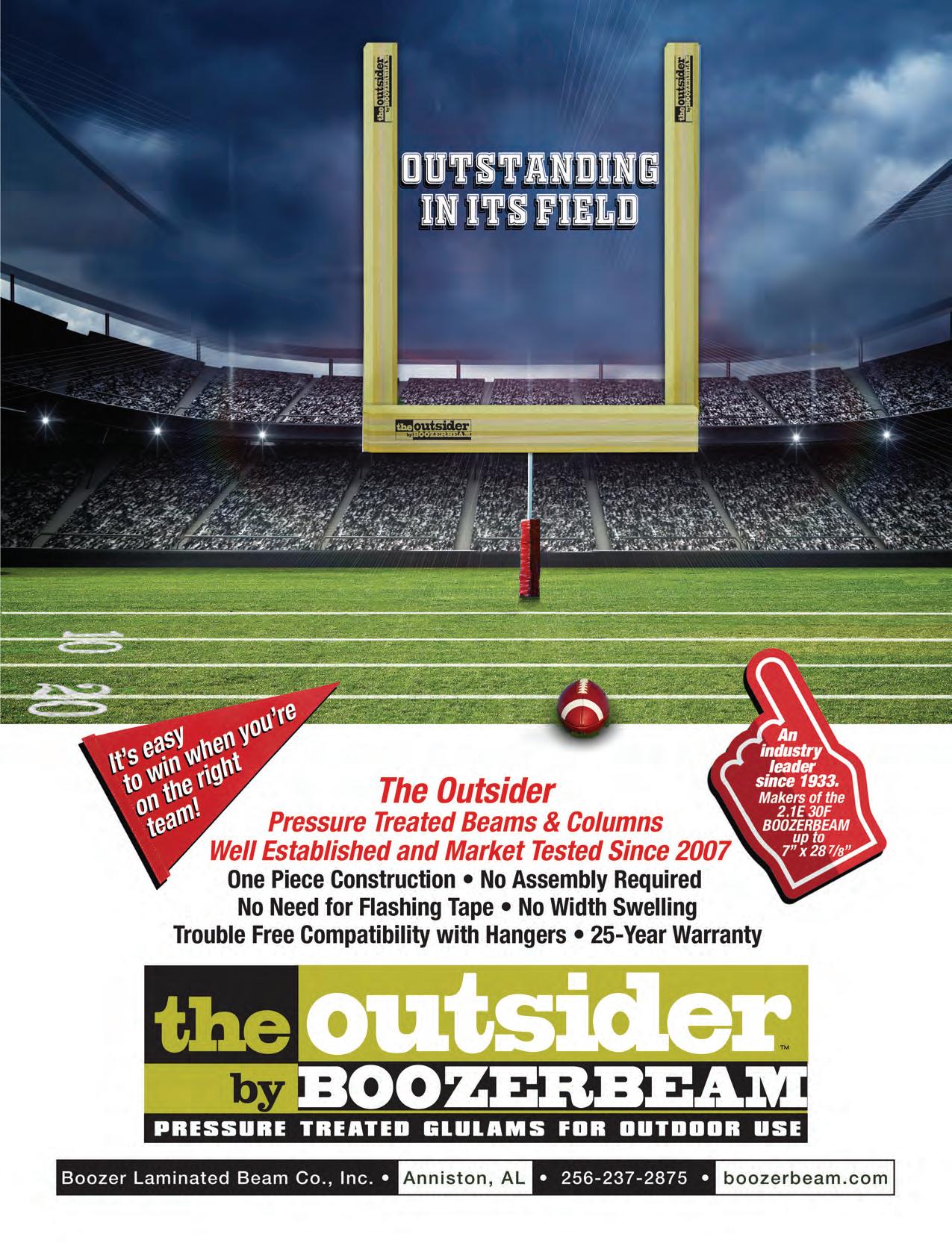

CLT MANUFACTURED in North America are certified to perform
North American CLT vs. imported product
Stringent standard assures consistent value, performance
Cross-laminated timber (CLT) is lightweight, yet extremely strong with superior acoustic, fire, seismic and thermal performance. It offers fast and easy installation, with virtually no waste onsite. CLT offers design flexibility and low environmental impacts, making it a strong alternative to conventional materials like concrete, masonry or steel—particularly on larger construction projects.
CLT manufactured in North America must meet stringent product standards and be certified to the ANSI/APA PRG 320 Standard for Performance-Rated Cross-Laminated Timber. Products manufactured outside of North America may not meet these same performance expectations. APA – The Engineered Wood Association explains key characteristics evaluated in the certification process.
The North American Difference
CLT design standards in the U.S. (the NDS) and Canada (CSA O86) require that the CLT products meet the requirements of and be certified to ANSI/APA PRG 320. When comparing North American CLT to products manufactured elsewhere, it’s important to consider the following characteristics:
Design Property Compatibility
The design capacities published in ANSI/APA PRG 320 were derived analytically using the lumber properties published in the NDS and CSA O86. Imported lumber may have different characteristics, may not be recognized in the NDS and CSA O86 and has published design values that are incompatible with those of North American lumber. Therefore, design properties for CLT products manufactured with foreign species lumber should be carefully examined for compatibility with North American CLT design standards.
Adhesive Heat Durability
The adhesives used in ANSI/APA PRG 320 CLT are required to meet heat durability requirements to ensure the adhesives will not melt at elevated temperatures. The heat durability of CLT adhesives is required by ANSI/APA PRG 320 to be evaluated in accordance with ASTM D7247, Standard Test Method for Evaluating the Shear Strength of Adhesive Bonds in Laminated Wood Products at Elevated Temperatures, and the CSA O177 flame test. Most CLT adhesives used outside of North America have not been evaluated for heat durability. The use of adhesives that have not been evaluated for heat durability could impose a serious life safety concern in the event of a structure fire.
Moisture Durability
CLT moisture durability is required by ANSI/APA PRG 320 to be evaluated based on the same accelerated aging (vacuum-pressure-soak) tests as used for structural glued laminated timber (glulam), which has decades of proven success in structural applications around the world.
The face-bond criteria (the minimum percentage of wood failure and the maximum allowance for gluebond delamination after accelerated aging tests) specified in ANSI/APA PRG 320 for CLT is the same as that for glulam. These mois-
ture durability criteria represent the most stringent requirements in the world for CLT to ensure its long-term performance. Most CLT products manufactured outside of North America have not been evaluated to the same moisture durability and face-bond criteria as ANSI/APA PRG 320. Since moisture durability of imported products have not been evaluated to the same criteria as North American CLT, long-term performance capability is unknown and may pose a risk of decreased structural performance and increased delamination potentials over time.
Fire Performance
Fire resistance of CLT products, when determined in accordance with NDS or CSA O86, is based on the requirements that CLT products are certified to ANSI/APA PRG 320. The rigorous adhesive qualification requirements specified in ANSI/APA PRG 320 ensure the integrity of CLT under the most severe fire conditions. New CLT adhesives are required to qualify with full-scale fire tests in accordance with ASTM E119, Standard Test Methods for Fire Tests of Building Construction and Materials, in the U.S. or CAN/ ULC S101, Standard Methods of Fire Endurance Tests of Building Construction and Materials, in Canada. This is not common practice outside North America.
Most importantly, CLT products certified to ANSI/APA PRG 320-2018 or ANSI/APA PRG 320-2019 are required to use structural adhesives that meet the requirements of the full-scale Compartment Fire Test (CFT) specified in the standards and do not result in the char layer fall-off when exposed to fire, which is known to cause a second flash-over and fire re-ignition. The 2021 IBC and IRC and the 2020 NBC specifically require CLT to be certified to these new standards. Therefore, it’s important the designer, contractor and building official ensure the CLT products comply to these new standards. Most CLT products manufactured outside North America do not use adhesives that meet the stringent requirements of ANSI/APA PRG 320-2018 or ANSI/ APA PRG 320-2019 and could result in a serious fire safety and code-compliance concern.
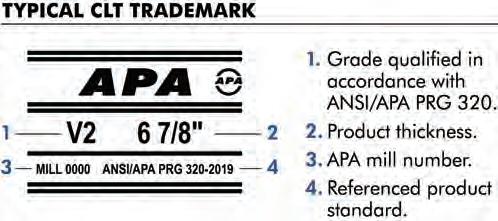
Always Look for the APA Trademark
The APA trademark is your assurance the CLT was manufactured by North American producers whose products have been successfully qualified and certified to ANSI/APA PRG 320. The ANSI/APA PRG 320 standard is recognized in the International Building Code (IBC) and International Residential Code (IRC) in the U.S. and is required for using the design provisions specified in the National Design Specification for Wood Construction (NDS). In Canada, ANSI/ APA PRG 320 is recognized by the National Building Code (NBC) when the product is applied in designs that meet the requirements of CSA O86, Engineering Design in Wood.
Find additional information in Cross-Laminated Timber: North American CLT vs. Imported Product, Form S500, in the APA Resource Library.
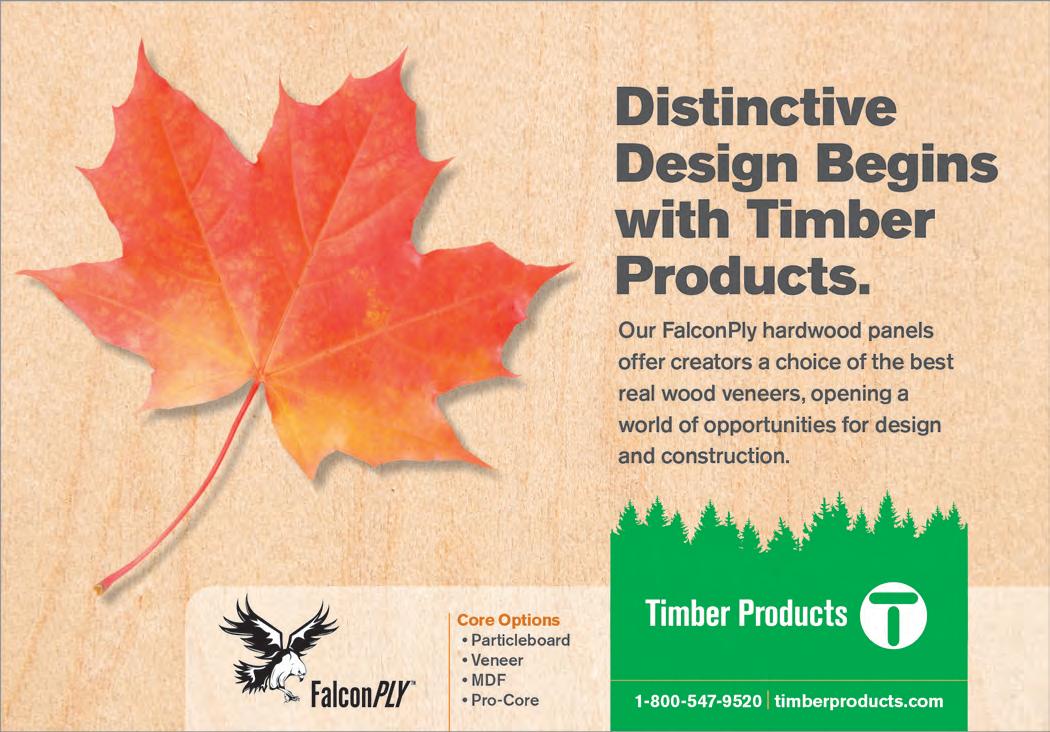
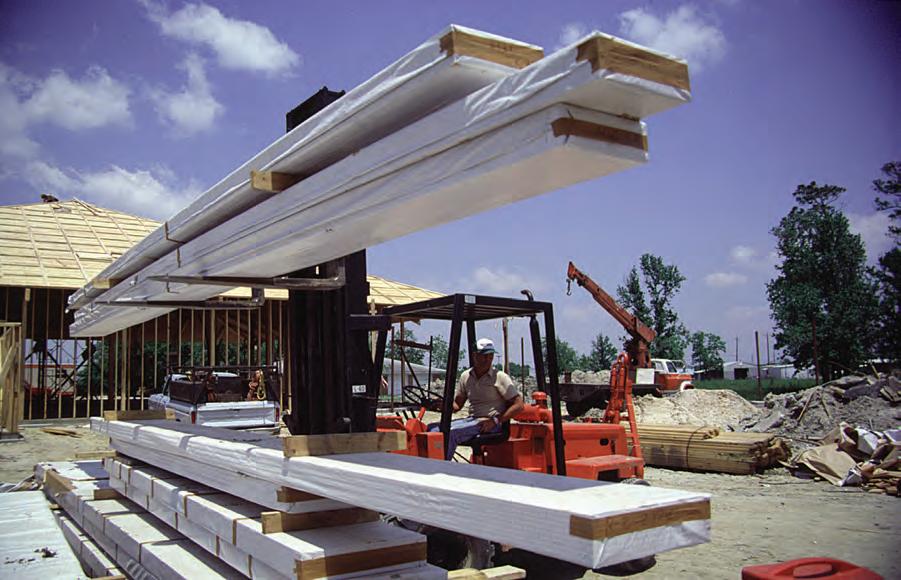
ENGINEERED WOOD commonly leaves the mill protected with wrap, but precautions must still be taken in transit, at the lumberyard, and at the job site.
Best practices for storing and handling EWP
To ensure optimum performance of engineered wood beams, proper storage and handling practices should always be followed. These recommendations help protect beams from damage during shipment, storage and on the construction site.
Glulam
APA trademarked glulam beams are often protected with wrappings when they leave the mill. But care must be taken during loading, unloading and transporting, as well as in the yard and on the job site.
Loading and Transit: Glulam beams are commonly loaded and unloaded with forklifts. For greater stability and handling safety, place beams flat on forks rather than on bottoms (see image at top of next page). Carrying extremely long beams on their sides may cause excessive flexing. Using two or more forklifts, lifting in unison, may help control flex. A crane with slings or chokers may also be used to load or unload beams, however, it’s recommended to provide adequate blocking at all beam edges between the sling and the members to protect corners and edges. Only fabric slings should be used to lift glulam members. Spreader bars can be used to reduce the likelihood of damage when lifting long beams.
Transport: Stack beams on lumber blocking or skids when loading them on trucks. Beams can rest on their sides or bottoms. Secure the load with straps to keep it from shifting. Protect beam edges with “softeners” or wood blocking when strapping down the load.
Storage: When possible, store glulam beams under cover to protect them from rain and sunlight. Place beams on lumber blockings, skids or rack systems on level, well-drained ground. Center beams on blockings or racks to evenly distribute the load. Water-resistant wrappings are another way to protect beams from moisture, dirt and scratches. Because sunlight can discolor beams, opaque wrappings are recommended. Beams can be wrapped individually, by the bundle or by the load. In some instances, the wrappings can be used to protect beams until installation. Sealants on the ends of beams help guard against moisture penetration and checking. The ends of beams should be sealed immediately after trimming.
For long-term storage, cut slits in the bottom of the wrapping to allow ventilation and drainage of any entrapped moisture. Do not expose glulam members to rapid changes in moisture and temperature, such as may occur from temporary heating units.
Structural Composite Lumber
Loading and Transit: Care must be taken to protect SCL in all transit periods—from the point where the product is delivered, to job-site handling and storage, to final installation. Take care to avoid forklift damage. If the ground is unlevel in the storage area, reduce forklift speed to avoid “bouncing” the load. When handling with a crane, pick up the load using a spreader if necessary to minimize handling stresses. SCL prod-

TO PROTECT SCL, store bundles on stickers and use a spreader when lifting with a crane.
WHEN LOADING or unloading I-joists, use a forklift with wide forks and never stack horizontally.
ucts are usually shipped in water-resistant wrapping that protects them from moisture, soiling and surface scratches. Storage: SCL packages should be set on level, well-drained surfaces, with longest materials on the bottom. Lumber bumpers or blocks should be used to keep SCL packages from direct contact with ground—maintain at least 6”-12” of ground clearance. For longterm storage, cut slits in the bottom of the wrapping to allow ventilation and drainage of any entrapped moisture to reduce the possibility of water damage, staining or decay. Store SCL in a covered area whenever possible. Maintain stack height within safe limits and do not store other material on top of SCL.
I-Joists
Loading and Transit: I-joists should never be dropped off the delivery truck. Use a forklift with wide forks to handle long length material or use a boom. Never bounce or jerk loads. Maintain low forklift speeds and smooth braking to prevent accidental dumping. Always keep I-joists vertical when handling and avoid lifting I-joists by top flange. If I-joists are delivered wrapped, don’t open bundles until time of installation.
Storage: I-joists should always be stacked and stored vertically and level—never flatwise. Maintain at least 12” between the ground and the I-joists. I-joists can withstand normal exposure to moisture, but excessive exposure may lead to dimensional changes that affect serviceability. Storing I-joists in a covered area minimizes impacts of weather and moisture. If stored outside, material should be covered to protect from dirt and weather; delay unwrapping bundles until time to install. Use stickers to separate bundles, spacing stickers every 8 ft. and maintaining vertical alignment.
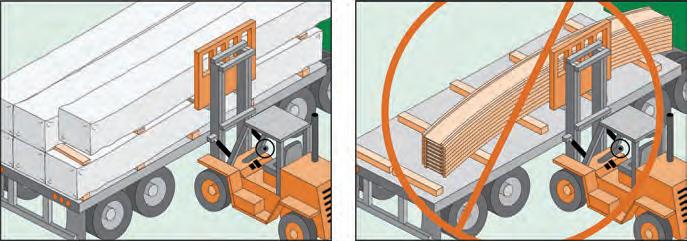
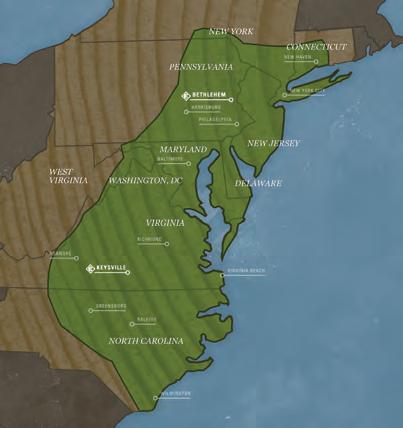
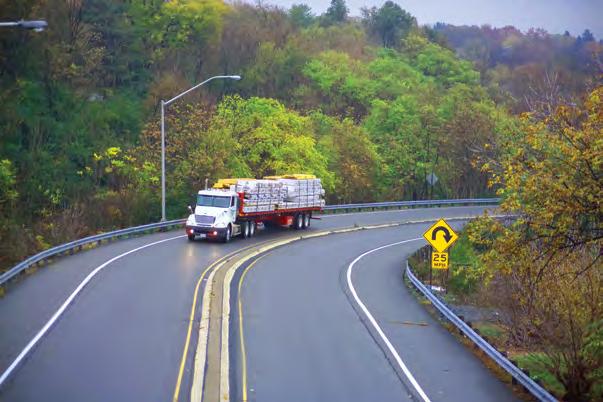
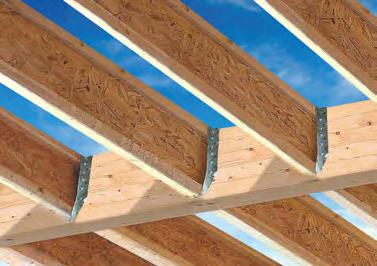
We Know Engineered Wood.
It's what we do!
Now TWO locations serve the Mid-Atlantic and Northeastern US: 1 1245 Easton Road Bethlehem, PA 18015
617 Heartland Drive Keysville,VA 23947 Toll Free 800-700-4788 Tel484-853-3100


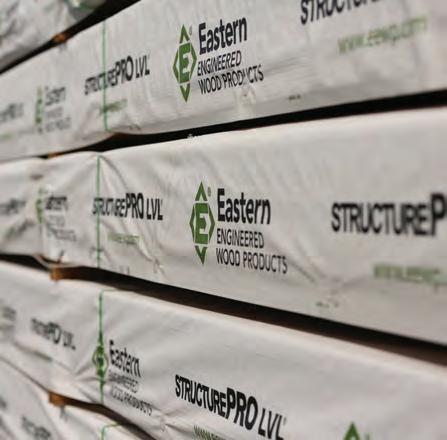
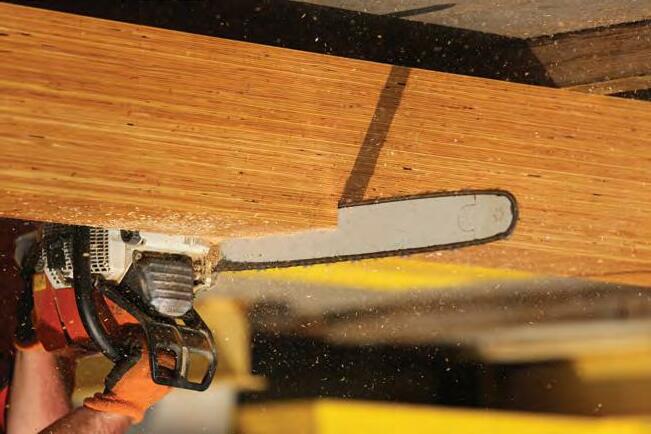
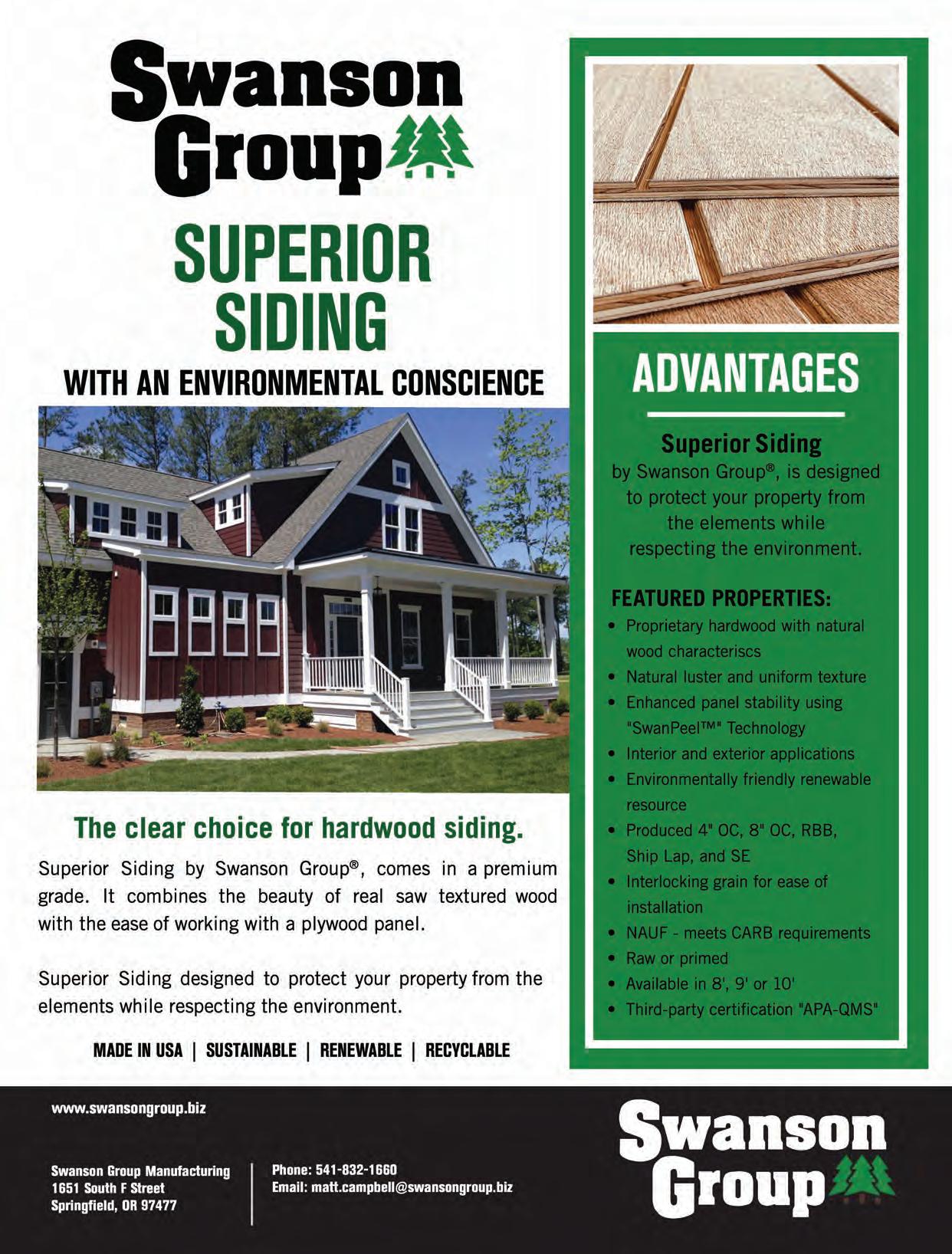
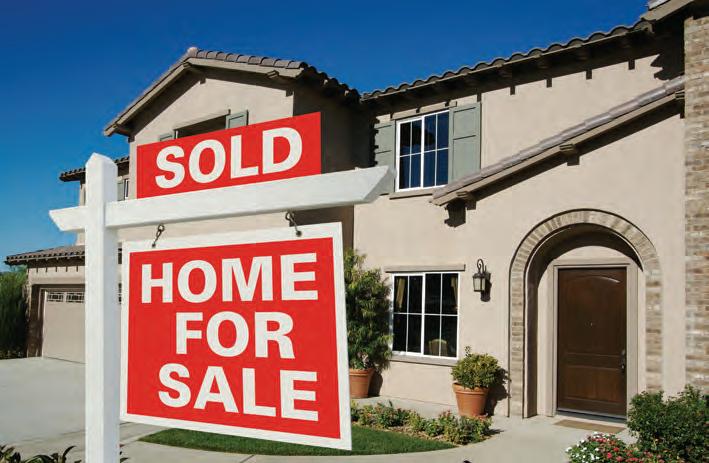
2022 housing industry outlook
Federal Reserve’s inflation fight poses concern
Russia’s invasion of Ukraine has increased concerns regarding the inflation outlook and the steps Federal Reserve policymakers plan to take to put the inflation genie back in the bottle for the next two years. The Federal Reserve appropriately loosened credit conditions to support the global economy when COVID-19 forced the temporary closures of businesses. There was also merit to the argument that disruptions to the global supply chain raised production and distribution costs, contributing to higher goods prices.
However, belief that the inflation increase was “transitory” and price increases would slow in the second half of 2021 appears to have been misplaced. As a result of the Federal Reserve’s effort to monetize the $3 trillion budget deficits run by the federal government in fiscal years 2020 and 2021 to also support the economy, the nation’s money supply increased by 36% from the fourth quarter of 2019 to the fourth quarter of 2021. As shown in Figure 1 at right, inflation has not slowed, as the inflation rate in the U.S. is running in the 6% to 8% range, depending on the measure used.
Federal Reserve to Tighten Policy
Following the March 16 Federal Open Market Committee meeting, Federal Reserve Chair Jerome Powell said the Federal Reserve would be raising the target range for the federal funds rate 25 basis points, and that six more 25 basis point increases are to follow through the rest of 2022. Powell also said the Federal Reserve would start to reduce the size of its balance sheet in May. More recent statements made by Federal Reserve policymakers suggest that they may be more aggressive in tightening credit conditions than Jerome Powell’s March 16 statement.
Prior to March 16, the rate on a 30-year fixed-rate mortgage had risen to 3.85% after starting the year at 3.2%. Since March 16, the rate on a 30-year fixed-rate mortgage has risen by 135 basis points to 5.1% (see Figure 2 on next page). The prospects for further tightening by the Federal Reserve suggest the rate on a 30-year fixed-rate mortgage means we should not be surprised to see a 5.5–6% rate at year-end 2022.
Rising Mortgage Rate Impact on Affordability
The housing markets in the United States, for homeownership or rental, are tight. Vacancy rates in both markets are at record lows. The increase in home prices has been well documented in the business media. Based on the Case-Shiller Home Price Index, the average price of an existing home has appreciated 30% from December 2019 to December 2021. The increase has greatly exceeded the growth in household incomes.
In order to illustrate the impact of the increase in the mortgage rate on affordability, we will call on a recent analysis done by the National Association of Home Builders (NAHB). The parameters for the analysis include the following: • The median price of a new home sold in 2022 is $412,500
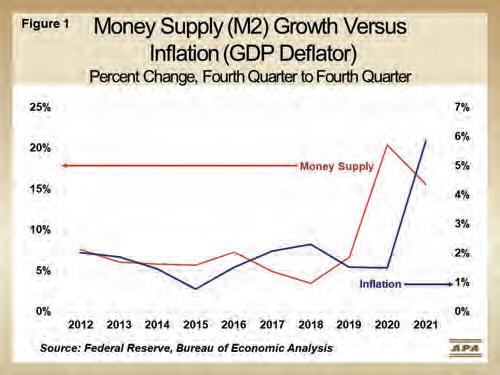
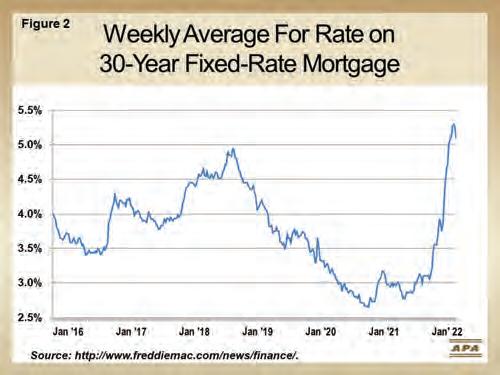
• The amount of household income that can be devoted to mortgage payment, property taxes, and insurance equals 28% • 20% down payment • Range of interest rates on a 30-year fixed-rate mortgage is 3% to 6%.
Shown in Figure 3 below is the income needed to qualify for the mortgage where the interest rate runs from 3% to 6%. At 3%, the qualifying income is near $95,000, and at 6%, near $125,000, an increase of 31.5%.
Using the NAHB estimated distribution of household income for 2022, the number and share of households that can qualify for the mortgage to buy a home with the mortgage rate ranging from 3% to 6% is shown in Figure 4 at bottom. At a 3% mortgage rate, the number of qualifying households is 42 million, and the share of qualifying is roughly 32.5%. At a 6% mortgage rate, the number and share of qualifying households falls to 27.5 million and 22.5%, respectively.
The sense of urgency to buy a home, given the prospects of mortgage rates moving higher, and still attractive margins being realized by homebuilders point to single-family starts running at 1.10 million or more in 2022. Rent increases averaging 17% across the U.S. based on the Zillow Observed Rent Index are sending the signal to apartment developers to build more rental housing. Multifamily starts totaled 474,000 units in 2021, and the forecast calls for multifamily starts to be near 550,000 units in 2022 (see Figure 5).
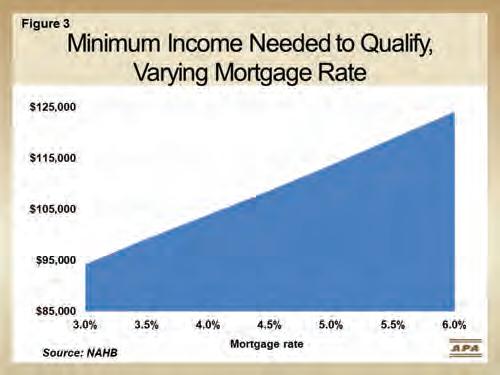

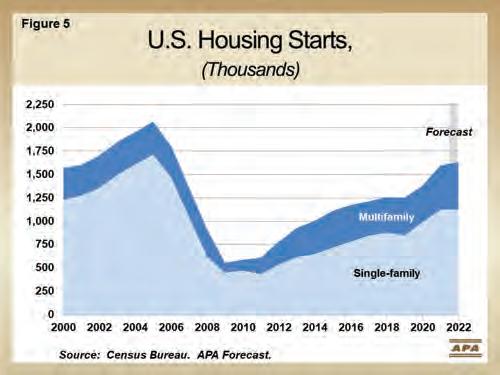
Considerations Beyond 2022
Some housing industry analysts suggest the U.S. housing stock is underbuilt by 3 to 5 million units. If so, this means the prospects for housing starts to average 1.6 million units or more annually through the rest of the decade are positive.
However, there is still great uncertainty regarding the underlying trend in new housing demand driven by household formations. As shown in Table 1 below, population growth has slowed dramatically in the last two years. The increase in the number of people passing away was a function of the coronavirus. Assuming the worst of the pandemic is behind us, the number of deaths should decline. It is unclear, though, where immigration will head after 2022 because there does not seem to be agreement regarding immigration policy in the U.S. Not only does the level of immigration have an implication for prospective household growth, but low immigration points to minimal growth in the labor force and, in turn, potential growth in the U.S. economy.
– Joe K. Elling is director of market research for APA – The Engineered Wood Association.
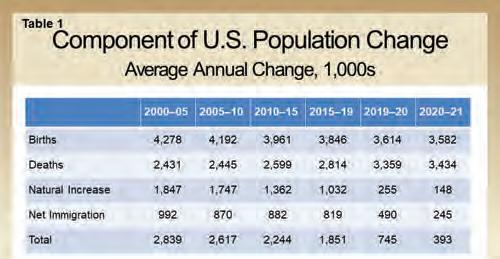
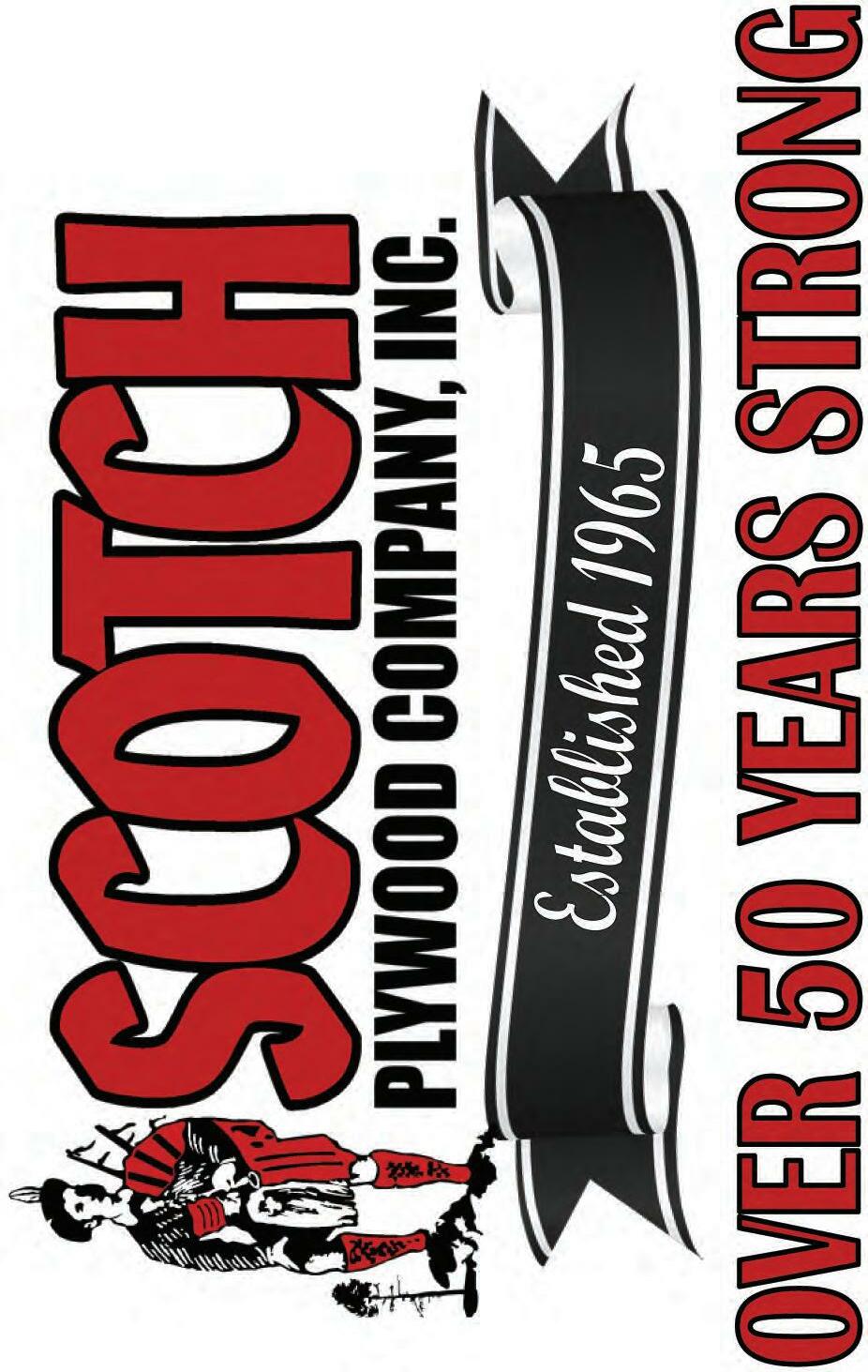
• www.scotchplywood.com 800-936-4424
Fulton, Alabama • 334-636-4424 •
Charlie Doby – Sales Manager Plywood & Veneer Barry Beightol – Plywood Sales Assistant
Formaldehyde and EWP
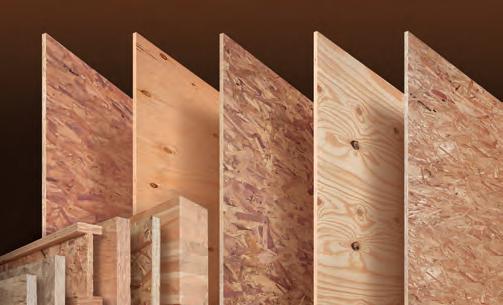
THE INHERENT structural and moisture durability of adhesives used in certified engineered wood products results in very low emissions
This article provides information on formaldehyde regulations that apply to U.S. and Canadian structural engineered wood products including structural plywood, OSB, wood I-joists, structural composite lumber, and glued-laminated timber. Here, “engineered wood products” are defined as wood products recognized in the U.S. and Canadian building codes for structural applications.
Formaldehyde is a naturally occurring organic airborne chemical that can be synthesized for certain industrial uses, such as adhesives used for wood products and in the manufacture of many other household goods, such as medical products, carpets and cosmetics. Because elevated levels of formaldehyde may lead to health concerns, regulations exist to limit exposure. These include limits on formaldehyde emissions from some types of wood products.
In addition, some green building specifications create a preference for low-emitting products. Many green building rating systems often include criteria to address indoor air quality goals, including mitigation of formaldehyde concentrations or formaldehyde-emitting products.
Since most North American construction involves sitebuilt conditions where exposure to weather is expected, the standards for engineered wood products require moisture-resistant adhesive systems. The inherent structural and moisture durability of these adhesive systems naturally results in very low formaldehyde emissions. Note that although cross-laminated timber (CLT) may not be listed as an exempted product below, CLT certified to ANSI/APA PRG 320 is made with moisture-resistant adhesives and has a low formaldehyde emission.
Always look for the APA Mark of Quality. Structural engineered wood products bearing the APA trademark are exempt from state and national formaldehyde regulations. In instances where unmarked structural engineered wood products from APA member mills are sold into applications that do not require a certification mark, the product invoice and an APA certificate of conformance can be used to identify the product as exempt.
U.S. and Canadian Formaldehyde Regulations Applicable to Engineered Wood Products 1. U.S. HUD Manufactured Home Construction and
Safety Standard (CFR 3280.308)
This standard specifies a 0.20 ppm emission limit for plywood and a 0.30 ppm limit for particleboard when tested with the ASTM E1333 Large Chamber Method. The intent
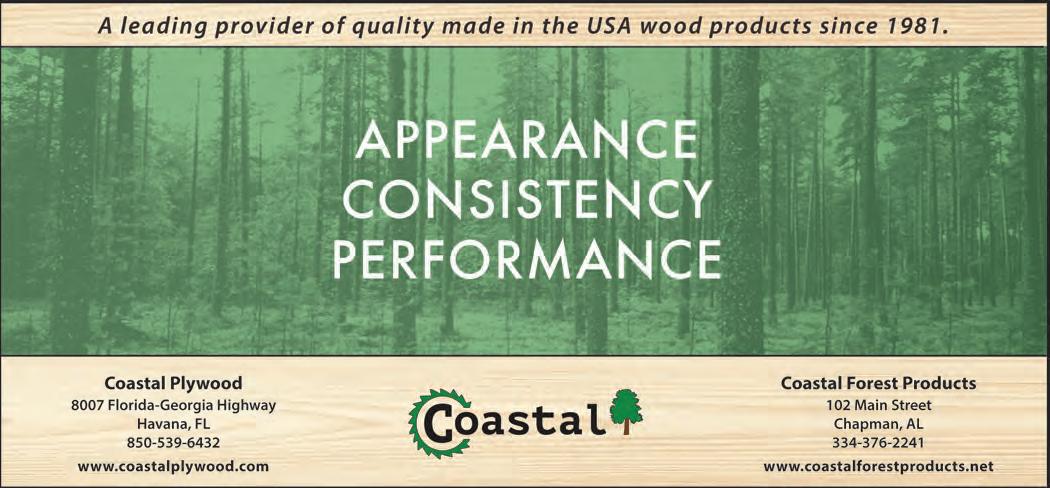
was to regulate the specific nonstructural panel types. Testing during development of the regulations confirmed PS 1 structural plywood readily meets the plywood emission limit; therefore, the regulations explicitly exempt phenolic-bonded plywood from ongoing testing and certification. Hence, the forementioned engineered wood products are either not covered by, or are explicitly exempt from, the HUD regulations.
2. California Air Resources Board (CARB) Airborne Toxic Control Measure (ATCM) for Composite Wood Products (also known as Title 17, California Code of Regulation 93120)
These regulations were developed by a division of the California EPA and took effect in 2009. The scope of the standard covers particleboard, MDF and hardwood plywood. Demonstrated low emission levels of engineered wood products led the CARB regulations to explicitly exempt structural plywood specified to PS 1, structural panels specified to PS 2, OSB to PS 2, structural composite lumber (SCL) to ASTM D5456, structural glued laminated timber to ANSI A190.1, and prefabricated wood I-joists specified to ASTM D5055. These exemptions apply to products trademarked or audited by APA under the APA quality assurance program, regardless of whether the product is used in construction or industrial applications.
3. U.S. Formaldehyde Standards for Composite Wood
Products Act (also known as EPA TSCA Title VI)
This Federal Act was signed into law in July 2010. The EPA published draft implementation rules in July 2016 for implementation of the law in 2018. The emission standard mirrors the one established by CARB and explicitly exempts structural plywood specified to PS 1, structural panels to PS 2, OSB to PS 2, SCL to ASTM D5456, structural glued-lam-
4. Canadian Formaldehyde Emissions from Composite Wood Products Regulations
The Canadian government published the Formaldehyde Emissions from Composite Wood Products Regulations on June 17, 2021. The regulation comes into force 18 months afterward, and the requirements for laminated products will apply five years after the regulations come into force.
The regulations were developed following CARB and EPA TSCA Title VI to allow for uniform requirements for both the U.S. and Canada. Therefore, the Canadian regulations also do not apply to structural plywood specified to PS 1, CSA O121 or CSA O151; OSB specified to CSA O325 or PS 2; structural glued laminated timber specified to CAN/CSA O122 or ANSI A190.1; prefabricated wood I-joists specified to ASTM D5055; SCL, including laminated strand lumber (LSL), laminated veneer lumber (LVL), parallel strand lumber (PSL), and oriented strand lumber (OSL) specified to ASTM D5456; and CLT specified to ANSI/APA PRG 320. CSA O160, Formaldehyde Emission Standard for Composite Wood Products, is a voluntary standard providing the requirements for product sampling, emissions testing, marking and labeling for composite wood products in compliance with formaldehyde regulations in Canada.
Find additional information including formaldehyde emission test results, international regulations and green building specifications in APA Technical Note: Formaldehyde and Engineered Wood Products, Form J330 in the APA Resource Library (www.apawood.org).
INDUSTRY SUPPORT IS OUR SPECIALTY
For nearly 90 years, APA has proudly supported the industry in creating structural wood products of exceptional strength, quality and reliability and helped building professionals create resilient, sustainable and code-compliant structures.
QUALITY ASSURANCE
TECHNICAL AND PRODUCT SUPPORT ON-DEMAND EDUCATION CONSTRUCTION AND DESIGN GUIDANCE
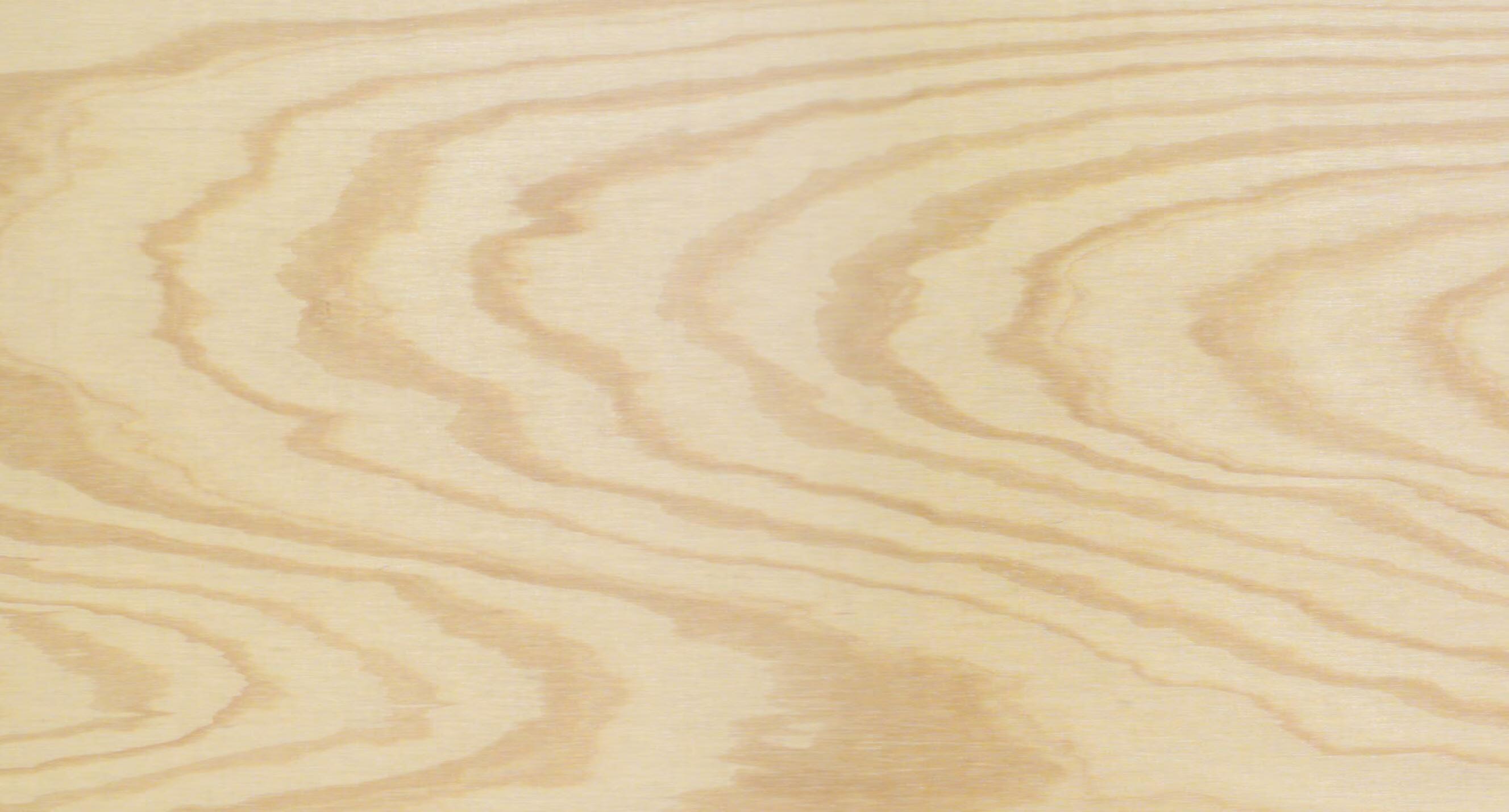
Tap into our expertise and explore our resources at www.apawood.org
A U.S. District Court in Florida has issued a permanent injunction preventing PFS-TECO from certifying Brazilian plywood as meeting the U.S. Voluntary Product Standard for Structural Plywood (PS 1). A coalition of U.S. plywood manufacturers challenged the defendant’s certification of Brazilian plywood as deficient and harmful to American consumers.
The suit alleged false advertising, loss of revenue, and negligence related to the structural plywood failing to meet U.S standards and was therefore unsafe.
The injunction required revocation of all PS 1 certificates issued by PFS-TECO to over a dozen Brazilian mills making structural plywood for the U.S.
According to Michael Haglund, counsel representing the U.S. Structural Plywood Integrity Coalition, “Everyone currently holding this inventory is now on notice that it should be considered off-grade, which means the PS 1 grade stamp on each panel should be obliterated before resale or the panel destroyed.”
The Coalition includes nine family-owned U.S. plywood manufacturers alleging PFS-TECO falsely certified that plywood imported from Brazil met U.S. structural integrity requirements. “The establishment of a strict standard for the veneer quality in Brazil that must be used to manufacture PS 1 plywood is critical to protecting the U.S. plywood industry from the unfair competition of off-grade Brazilian plywood masquerading as meeting the PS 1 standard,” said Gray Skipper, VP of Scotch Plywood, Fulton, Al. “Our mills follow precise recipes in manufacturing plywood to meet the PS 1 standard that are backed up by extensive regionwide testing of the southern yellow pine species we use to make plywood in the South. Brazil has planted these same species that are native to the southern U.S. in a region where pine grows extraordinarily fast and produces veneer that is significantly less dense and therefore less strong than what we use in the U.S.”
In 2021, Brazilian plywood accounted for 11% of all U.S. supply with nearly 1.2 billion sq. ft. sold. The substandard plywood is produced by more than 30 plants in southern Brazil. Although it was stamped PS 1 by PFS-TECO, it experienced large failure rates during testing by APA – The Engineered Wood Association and other laboratories.
Although APA sponsors the PS 1 standard, it was not a party to the litigation. The litigants sought changes to the standard; APA’s standard committee agreed it could be improved. Through a consensus-based process, an updated PS 1 is anticipated later this year.
APA expects the revised PS 1 standard will address concerns brought to light by the litigation and will improve the certification and quality programs supporting the U.S. plywood market.
EPA Scraps Energy Star Mark for Roofs
The EPA retired the Energy Star specification for roofing products effective June 1.
In 2019, the EPA notified roofing industry partners it sought to phase out the specification, and asked for comments. Although feedback was “mixed, a range of commenters supported sunset of the program,” according to the National Roofing Contractors Association.
Several factors spurred the change, in particular the EPA’s belief that robust standards in the commercial roofing sector made the mark obsolete. For residential, Energy Star was considered too binary a label to cover what’s become a complex process. In roofing, the Energy Star mark can no longer be used on labels, websites and other collateral materials.
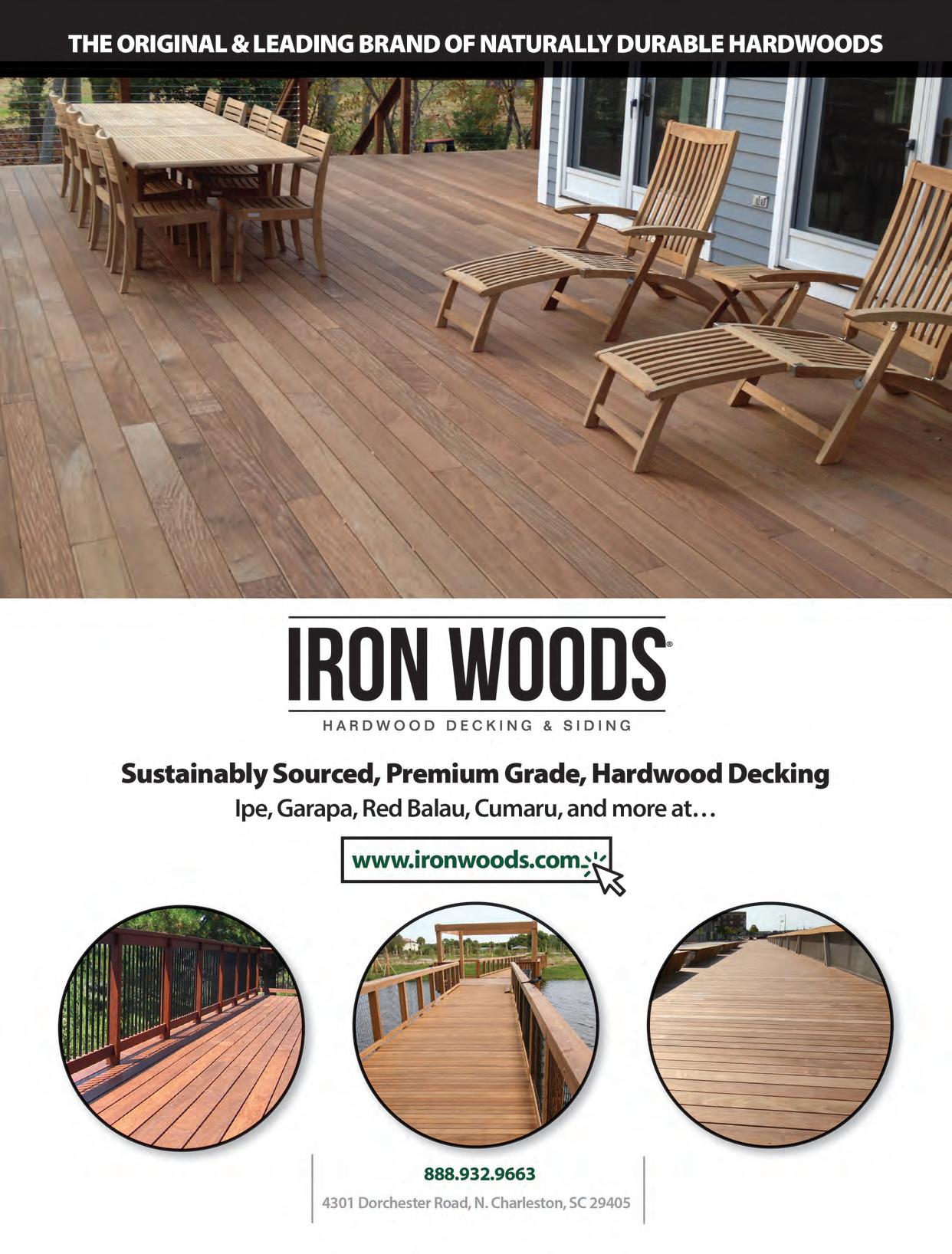