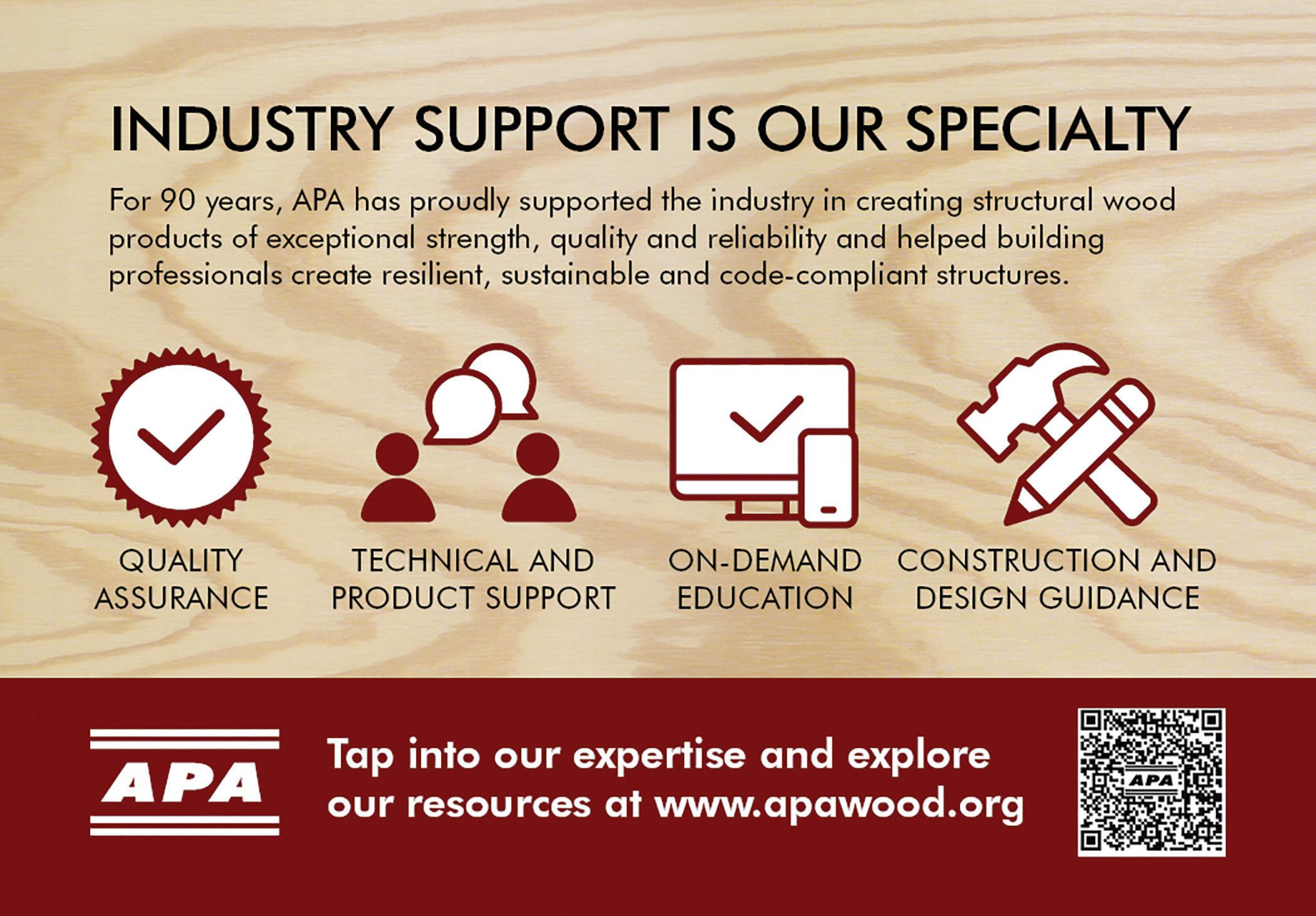
4 minute read
EWP IN SUSTAINABLE STRUCTURES
(Continued from page 46) but often begins with a design that incorporates carbon sequestering materials, such as engineered wood.
Engineered Wood Products and Embodied Carbon
Compared to steel and concrete, engineered wood products typically result in far less emissions because they don’t require drastic changes to the material’s original form and because wood manufacturers often use wood waste to power the manufacturing process, reducing the use of fossil fuels, which have high carbon emissions.
In addition, wood naturally sequesters carbon. Modern forestry standards ensure a continuous cycle of growing, harvesting and replanting of trees. These newly replanted trees absorb more carbon at a faster rate than old, slower-growing trees. It’s this lifecycle of planting, growing, harvesting, sequestering carbon in buildings and replanting that makes wood an excellent sustainable resource.
The Sustainability Benefits of Engineered Wood
Engineered wood products (EWP) not only offer the lower embodied carbon and carbon sequestration benefits of wood, but they provide additional green building benefits including:
• Due to how they are made, engineered wood products can be produced from small-dimension lumber. Engineered wood products therefore also optimize timber resource utilization.
• Engineered wood products are predictable, so there’s less shrinkage, consistent dimensions, less crowning, etc.—and, therefore, less waste.
• Many engineered wood products are available in custom and longer lengths and can be ordered in pre-cut framing packages, all of which further reduce waste.
• EWP manufacturing involves a lower-energy-use process that is more energy efficient than the manufacture of non-wood structural products that typically require a greater level of processing from the raw materials to the final product.
The carbon savings add up quickly when we compare wood floor systems to steel floor systems and wood wall systems to concrete wall systems. According to the Consortium for Research on Renewable Industrial Materials (CORRIM), choosing wood floor assemblies over steel can avoid approximately 22 lbs. of CO2 for every square foot of floor, while choosing wood wall assemblies over concrete can avoid about 15 lbs. of CO2 for every square foot of wall area.
Using wood building materials can reduce the net carbon impact of a project in many ways, particularly because wood emits significantly less CO2 from production than other materials. If carbon storage capabilities are factored in, the benefits of wood become even more significant.
Watch APA – The Engineered Wood Association’s on-demand webinar “Sustainable Structures Built with Engineered Wood,” for a deeper dive into engineered wood’s role in reducing the carbon footprint of the built environment. Visit www.apawood.org/webinars. BP
Read grade rules, span details, and get new promotional ideas for your business.
Sample the variety and versatility of eastern white pine.
Reach more customers by getting listed on NELMA’s Retailer Directory.
Listen to and watch product installation and comparison videos, plus grade representations.
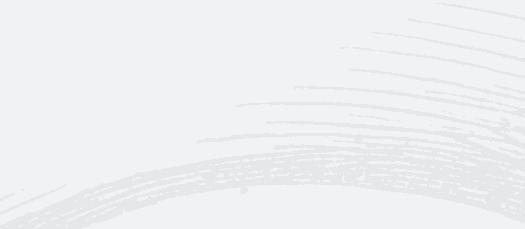
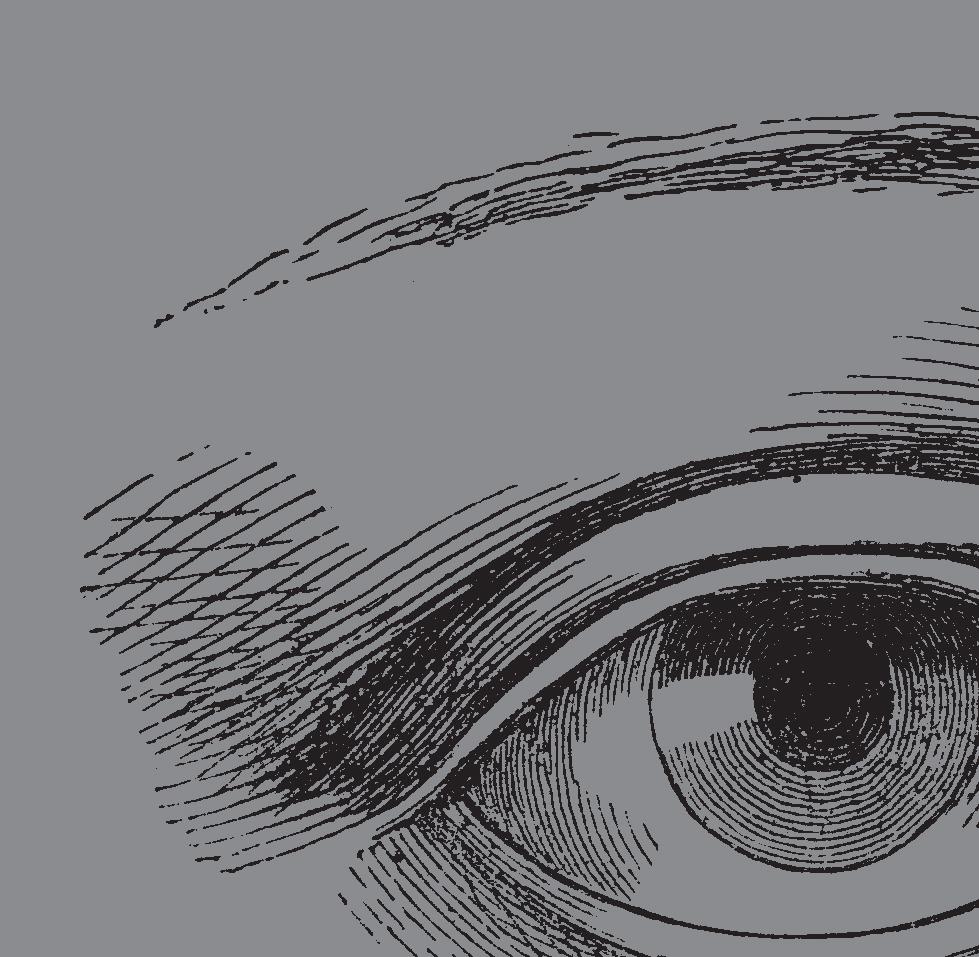
Plastic, concrete or pine? Learn why consumers prefer natural over fabricated.
Use all your senses. Visit nelma.org for all things eastern white pine, spruce-pine-fir and other softwood species grown in the Northeast and Great Lakes region.
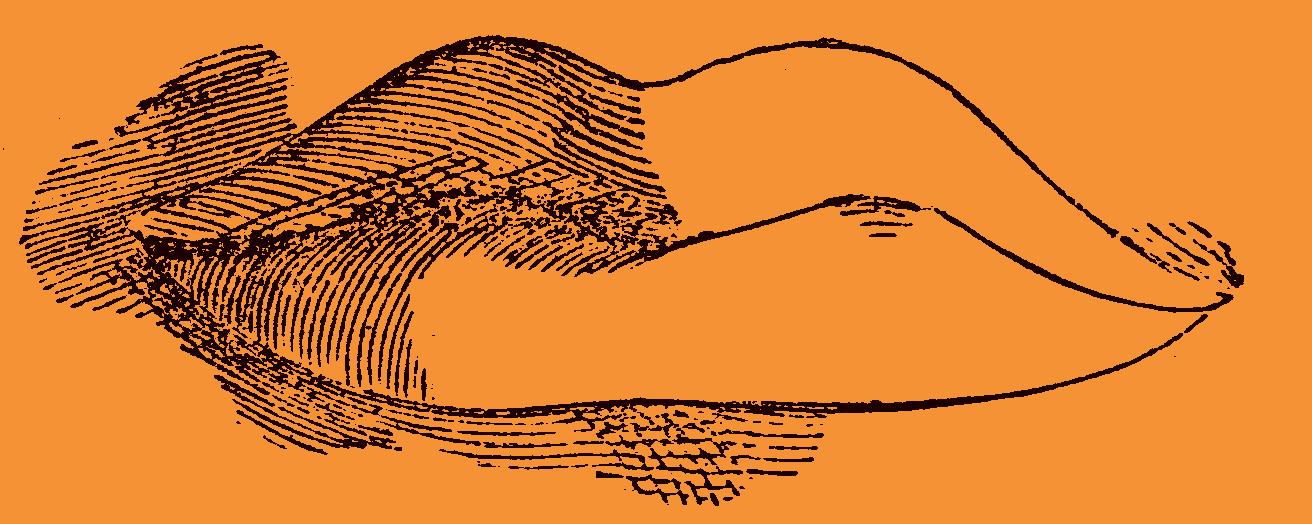
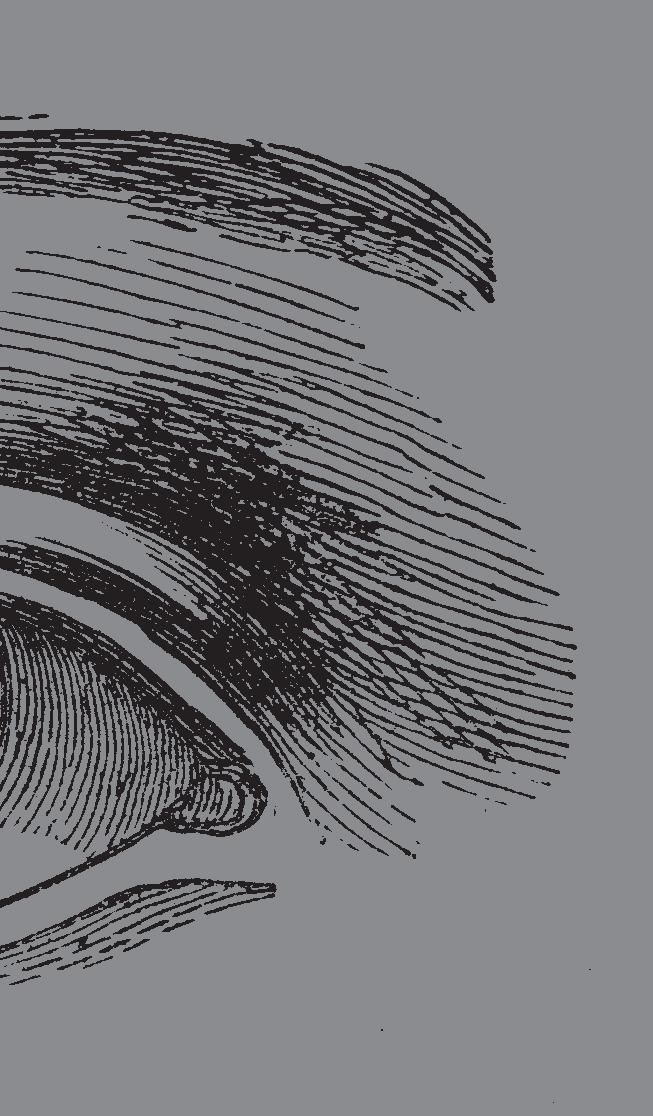
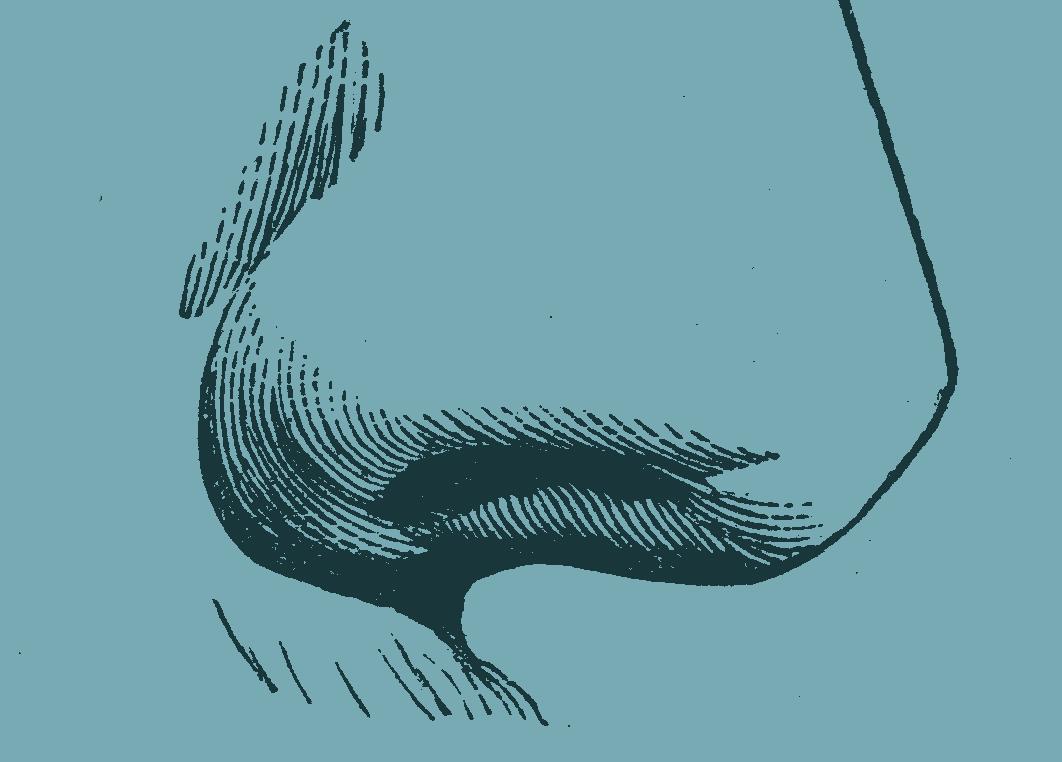
Ever see a paint swatch for wood grades? Scan here to see it. Simply open the camera on your smartphone or tablet, and hold it over this image.
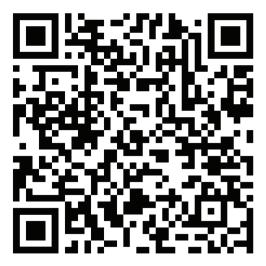

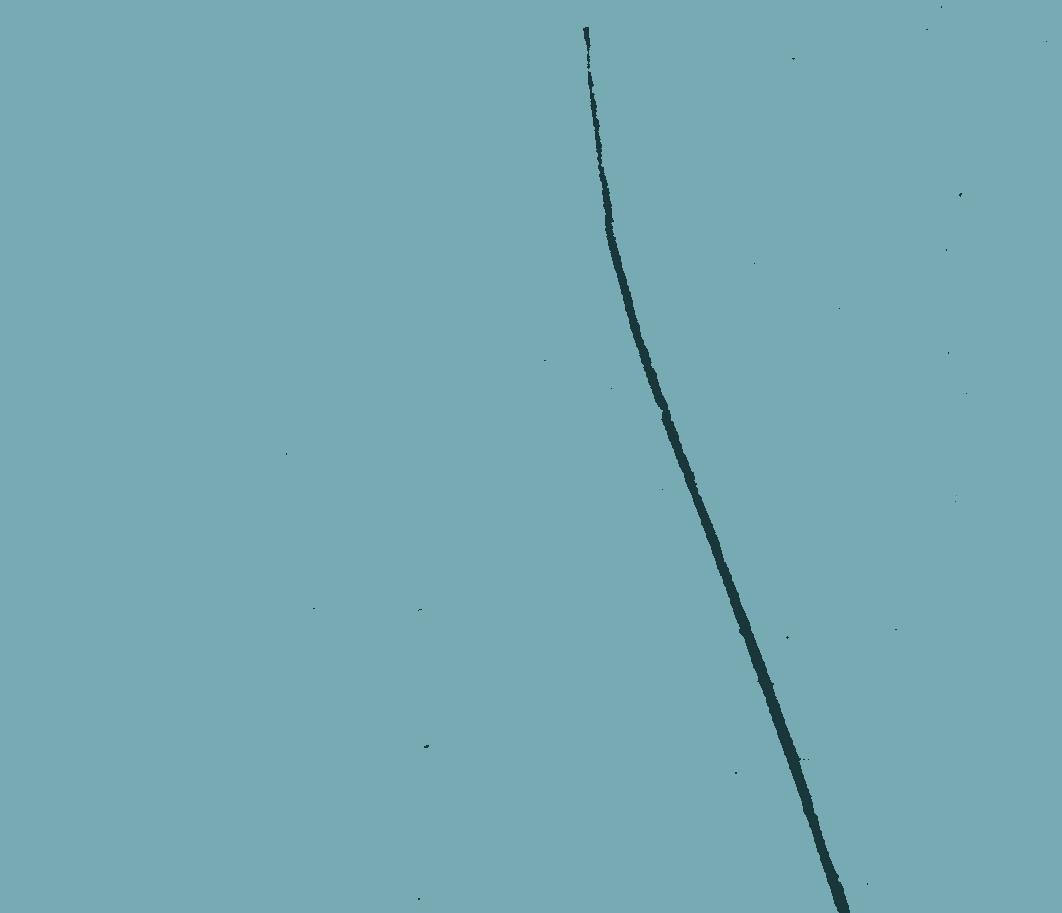
@NortheasternLumberMfg
@WoodInspiration
@wood_inspiration1933
Southern Treaters Get New Equipment
This summer, IWT-Moldrup is supplying three larger treatment plants in the U.S. with integrated semi- or fully automated material handling systems.
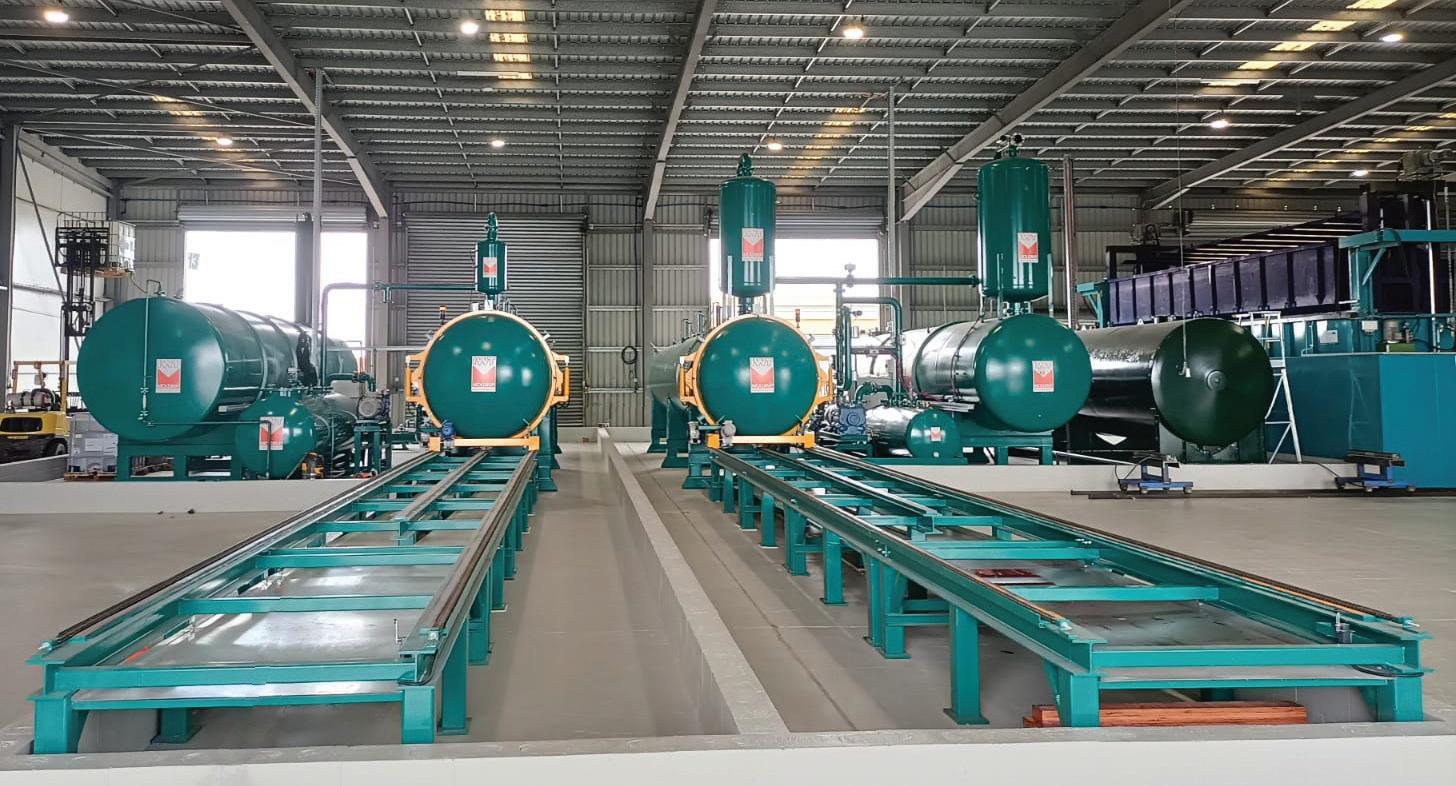
The install at Stewarts Wood Products, Danbury, N.C., includes hydraulic tilting of the pressure vessel, as well as semi-automatic material handling and automated hydraulic in the pressure vessels clamps to keep the wood from floating during the treating cycle. This will provide a drier treated wood and avoid contact between operators and freshly treated wood at the end of the process.
Southeast Forest Products, Louisville, Al., is getting a similar plant to add to its existing treating facilities, whereas late this summer Le Moyen Sawmill, Bunkie, La., will receive a fully automated material handling system. It will not require an extensive sealed concrete drip-pad, since drip-trays are integrated into the material handling system.
Lone Moldrup, CEO of IWT-Moldrup, noted that the plant can be operated by a single operator eight hours a day and, due to the automatic handling system, has an annual capacity of more than 40 million bd. ft.
Over the past three generations, Danish treating equipment manufacturer IWT-Moldrup has supplied more than 1,200 treating plants worldwide. The turnkey solutions are sold through IWT-Moldrup’s U.S. representative, American Wood Technologies, Atlanta, Ga.
G-P COMPLETES TEXAS MEGA-MILL
Georgia-Pacific held a private ribbon cutting June 21 at its Pineland, Tx., facility to mark the completion of an expansion and improvement project that reportedly has created the largest sawmill in the South.
The mill, which has been operating for more than 100 years, recently finished the $120-million, more-thanyear-long overhaul.
Among the improvements were replacing the old 1960s stud mill, the 1960s high-speed planer, and the 1960s continuous dry kiln with modern equipment, and expanding the log storage yard with a new debarking and processing line. G-P also increased available log truck deliveries from 250 to 300 per day, and upped annual production capacity of dimensional lumber from 380 to 450 million bd. ft.
Roseburg To Close Particleboard Mill
Roseburg will permanently end operations at its Taylorsville, Ms., particleboard plant on Aug. 21, after agreeing to sell the facility to an unnamed forest products company for an alternate use.
Roseburg bought the plant from Georgia-Pacific in 2006. It is now among the oldest particleboard mills in North America, and the plant’s press equipment and technology have aged to the point that it can no longer compete with newer domestic particleboard mills and the influx of imported products.
The plant currently employs about 100 workers.
Roseburg will continue producing particleboard in Simsboro, La.
Mercer Takes Over Structurlam
Mercer Mass Timber, Spokane Valley, Wa., acquired Structurlam Mass Timber Corp. and its subsidiaries. Upon close of the deal on June 15, Mercer immediately took possession and continued the operation of Structurlam’s manufacturing facilities, which will now operate under the Mercer Mass Timber brand, including production facilities in Conway, Ar., and Penticton, B.C.
Mercer Mass Timber now holds all of Structurlam’s brand assets, product and project portfolios, and intellectual property.
“This acquisition will allow us to offer our customers a wider range of mass timber products, and to better support their projects with the addition of more cross laminated timber capacity and glulam production capabilities,” said Mercer senior VP Brian Merwin. “Our goal is to become a one-stop shop for all mass timber needs.”
The addition expands Mercer’s expertise, geographic reach, market share, and production capacity for CLT, while adding glulam capabilities (19 million bd. ft.).
Mercer’s hope is that along with increased market share will come greater sway in the standardization of product specifications for mass timber in North America.
Lummus Adds Tiny Home Showroom
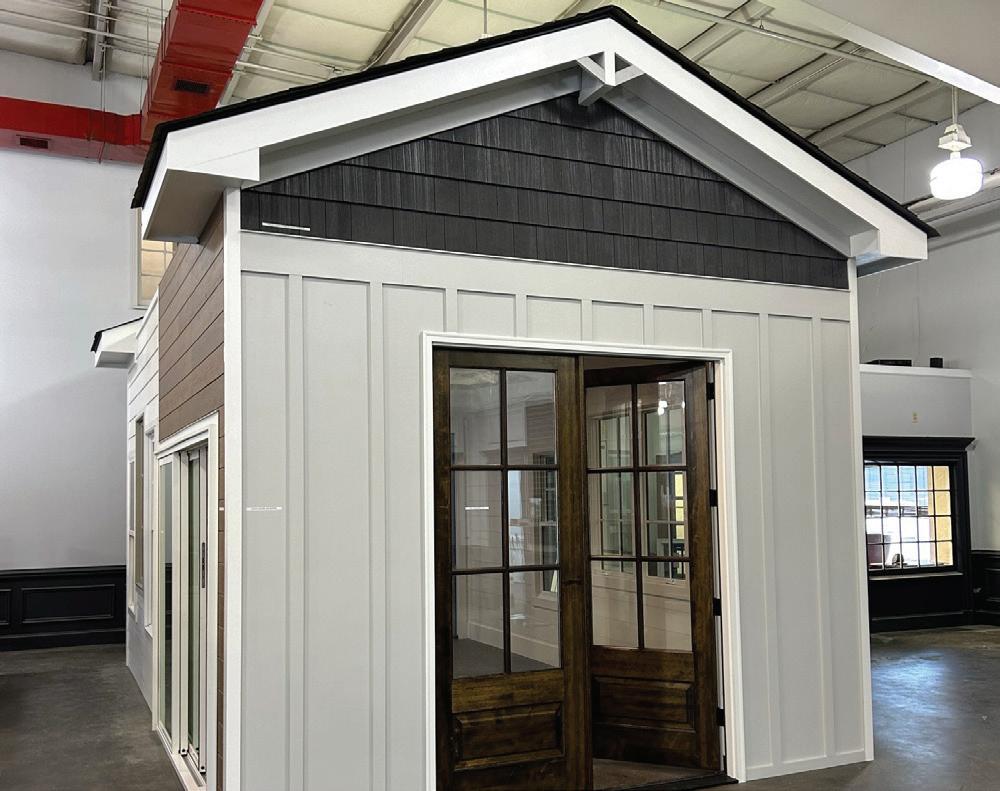
Lummus Supply recently opened a new showroom at its Acworth, Ga., location, showcasing two tiny homes.
Both tiny houses measure 20’x12” and feature the latest windows, doors and materials from James Hardie, Nichiha, Sierra Pacific, Windsor, Quaker, Western Windows/Doors, Therma Tru, Lindsay, Precision Millwork, Wholesale Iron and more. “These are the Cadillac of tiny homes,” said Ashlyn Lummus.