
5 minute read
SOURCING THE BEST SPECIES FOR MILLWORK
from BPD August 2023
------------ BY TYLER SHARPE
CHANGE FOR LESS-expensive, more-resilient, and better-performing products has always driven the building industry. Millwork is no different as we strive to embrace enhanced products, equipment, software, substrates and coatings to deliver improved offerings. In this article, we dive into the history and evolution of how certain species became the prevalent, reliable “go-to” substrates for the millwork industry.
Keeping up with fast paces of change has transformed me into a unique combination of an early adopter and a skeptic. I’m often the first in my circle to try new process improvement apps or explore revolutionary AI plugins. However, I’m also wary of the product’s ability to add value (or even function properly) until I’ve seen them in action in my daily life.
This critical step is often overlooked, since most products work well in controlled environments. Marketing of these products can be positioned where the benefits are staged so effortlessly, it feels unnecessary to consider the downside. For technology, a worst-case scenario could be a security breach or loss of data, so I design situations to test, experience and understand the functionality of these programs before integrating them into my day to day.
As a director of supply for a millwork company, I adopt the same approach to understand products from the inside out, starting with the species and substrate. As a foundation, I recognize that all species have different properties and characteristics. We often can’t match a perfect species for each application, but we can rule out a family of species that are simply not an ideal fit for certain millwork uses. Understanding the technical specifications of the species and requirements of the application enables us to determine that the best species for a stair
HOW THE GO-TO WOODS FOUND THEIR NICHES
stringer may not be suitable for a flat jamb or moulding.
In speaking with colleagues and industry veterans, the trend to experiment with new species started in the ’80s as environmental changes in the United States limited access to the two most prevalent species used for millwork, ponderosa and sugar pine. Ponderosa forest supply was affected by environmental provisions to protect the endangered spotted owl which primarily resides in ponderosa pine forests. Increased logging threatened the spotted owls’ natural habitat resulting in greater protection for old-growth forests. Simultaneously, sugar pine forests were devastated by a fungal disease known as blister rust which spread throughout the forests causing infections, reduced growth rates, loss of vigor, and a sharp decline in available supply.
North American businesses turned to South America for supply due to its abundance of radiata, taeda, Elliotis and Mexican pines. This shift to incorporate imported species initiated industry-wide practices (often developed through a series of trial and error), essentially marrying up certain fibre to specific applications. An example of an early error was substituting ponderosa pine with Mexican pine in edge-glued panels. With many shared features between the species, it was expected to be a well-suited alternative but the Mexican species was considerably less stable and the wider laminations resulted in a warped panel. The solution was to reduce the average lamination width from about 4” down to 1.5” to limit the effect of the less stable wider grain. The net outcome was a higher cost alternative with lower yields, extra labor to assemble and considerable replacement costs for the learning “errors.”
In 2023, we have now accumulated a half century of experience working with species like radiata and taeda pine. The strong reliability of these species for most millwork applications was subsequently leveraged by exporting them in break-bulk to major producers in Asia to transform into lower cost, high quality finished millwork goods. With 50 years of expertise, the industry understands the ins and outs of these species allowing us to predict how they will likely react in a series of applications. Knowing their overall stability, weatherability, screw-holding strength, MoE and MoR among other properties, allows us to compare against applications to determine if these species are suitable.
That’s why sourcing best practices begin with understanding the application and the fundamental needs of the product for successful outcomes. For example, can a 1” screw be a suitable alternative for a 3” screw? While it may not provide the same strength, it could meet the requirements of the intended use. Similarly, the suitability of a species for millwork products depends on the application, construction and expectations of the substrate.
As COVID sparked increased demand, the millwork industry was motivated to investigate different import species similar to what happened in the 1980s. To seek out more supply, we began experimenting with a variety of new import species and substrates. Import data shows tremendous amounts of sibirica pine coming from Northern Europe and local Asian species like Chinese fir, merkussi pine, falcatta, albasia, rubberwood, mahogany, meranti and led to an increased embrace of other engineered alternatives like MDF and LVL (laminated veneer lumber). The choice was service the business with a new substrate or potentially lose out.
I watched our QC teams design extensive destructive testing to better understand the specifications and limitations of each species. Other tests were designed to recreate the conditions of weathering in hot, cold, humid and dry conditions for alternative suitable species. Circling back to my comment on technology, testing in a controlled environment is not a substitute for years of field data that documents the performance and variability over time and in different climates. In laboratory tests it is difficult to capture variations in the substrates from production across different seasons or fibre at different levels of maturity.
I can report positively that our experiences with species like Chinese fir, merkussi pine, and rubberwood were well received and continue to hold up exceptionally well in a wide range of applications. Alternatively, some species responded better in control testing than in the field, one problem species in particular being sibirica pine. This species grows in a cold, dry climate and when imported to the southeast states resulted in checking across the ends of the boards and raised grain on the surface. Further diagnosis led us to understand that the medullary rays of the Siberica contributed to the splits that opened up within the boards.
In the post-COVID era, supply of known millwork species is more accessible and market pricing is trending towards pre-pandemic levels, largely driven by reduced freight costs. However, there are still largerthan-expected volumes of imported Southeast Asian species especially in LVL products entering the U.S. (my assumption is due to their lower price points). LVL is a dimensional panel product with layers of veneer bonded together by glue and can be made from veneers from a wide range of species. Logs for many of these new species are less expensive than pines, plus LVL production gives a better yield on fiber than sawmilling. Some of these species have low densities, enabling shippers to fit more material in a container. Due to their rapid introduction, I question whether these species have been sufficiently tested across multiple weathering cycles for the intended climates and finished applications. Have the logs been harvested legally? Do glues meet emission targets? Does the factory responsibly follow SOPs and lamination best practices? As director of supply, I need to assess the complete supply chain and life-cycle costs:
• What is the cost of movements such as crook or bow in critical components?
• What is the cost of potential screwholding failure?
• Does the product smell funny? Will it grow mold?
• What’s the cost of a delamination and product failure?
• What could be the cost to reputation?
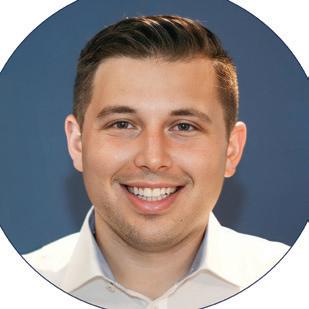
These are the sort of scenarios my team considers when we evaluate new species.
Understanding the product application and the requirements of the substrate and coatings is always the first step. From a strategic sourcing perspective, the specifications of the application are the driver to identify suitable substrates and total cost of ownership is the overall metric. My overall message is to convey the importance of due diligence and ask the right questions in order to make an informed decision. I take pride in being an early adopter, but not at the risk of being the test case. BP