
3 minute read
CHOOSING THE RIGHT WALL SYSTEM
from BPD August 2023
------------ BY ROB YOUNG
HOUSEWRAP OR drainable housewrap? Rainscreen or no rainscreen? Specifying a wall system that will protect the home from moisture and air infiltration means navigating a lot of options. So which system is best for your customers? The short answer—it depends.
A number of factors play a role in determining the ideal products and systems. As a dealer, you can support builders and remodelers by understanding what they should consider when specifying a high-performance wall system. A project’s budget certainly is part of it, but investing in the most suitable wall system, even if it costs a little more up front, is crucial for the longevity and performance of the home.
Decisions ultimately come down to each individual project, its materials, and its climate.
First and foremost, it’s important to understand the building science behind wall systems—how the building envelope breathes, how moisture and air travel, and the role that products and installation methods play. Seek out education opportunities from your manufacturer partners and other building science resources to ensure you and your staff understand how the building envelope works.
Siding Material
Every siding type is different in its makeup and its installation—and therefore how it responds to moisture infiltration. The type of cladding is going to be one of the key factors in deciding between a flat housewrap, a drainable housewrap (which has built-in bumps or ridges to create channels for moisture to drain), or a flat housewrap with an added rainscreen. Always consult siding manufacturer instructions and requirements for the wall system.
Generally, if wood is involved, projects need a full rainscreen (unless the home is in an extremely dry area). Wood cladding can absorb water, which will migrate to the back when the sun hits it. Having a rainscreen in place provides ventilation to dry out the cavity as well as the back of the siding.
High-performance sidings such as fiber cement or poly-ash typically will need a drainable housewrap, with some material instructions and warranties calling for a specific drainage rate.
Vinyl siding sits off the wall and doesn’t absorb moisture, so it typically is installed with a flat housewrap. However, moisture can still accumulate, so a drainable housewrap can add an extra layer of protection. In addition, insulated vinyl siding may have specific requirements for drainability since there is less space behind it.
Geography & Climate
Because building science experts point to rain as the single most important factor to control in order to optimize durability, choosing a building envelope product must be predicated on climate conditions. Winddriven rain is an especially powerful foe, forcing its way into small penetrations in cladding materials and into cracks and holes in the exterior wall.
The main rule, therefore, is that the amount of rain will determine the amount of rain control needed. In areas like the Southwest that receive low rainfall (less than 20 inches annually), a housewrap or building paper should offer sufficient water resistance protection, according to most building experts. In areas that experience moderate amounts of rainfall (20 to 40 inches annually), protection against rain penetration should include an enhanced housewrap. And for wet and/or humid climates, coastal areas, and hilltop exposures receiving high (40 to 60 inches annually) or extreme (60 inches or more annually) rainfall, a ventilated rainscreen assembly is recommended; a rainscreen system is also advised for areas that receive high winds in addition to rain.
Even in dry, less-demanding climates, builders and designers seeking optimum drying and drainage capability may wish to install a rainscreen or drainable housewrap as added insurance against moisture problems. The cost of using these methods up front during construction is small in comparison to fixing moisture-related problems later.
Thinking as a System
Keep in mind that the building envelope is a system of parts. Work with your manufacturer on a systems approach to ensure that each element in the envelope is working together and that the chemical makeup of one product isn’t impacting the performance of another. Most importantly, be sure that each element, including the cladding, is installed so as to properly dry out the wall assembly. For example, a Rainscreen System for Masonry would include a flat housewrap and a vertically channeled rainscreen with a filter fabric.
By asking the right questions and helping customers navigate the different options for creating a highperformance wall system, dealers become valuable resources that keep customers coming back. BP
EPS to Remain Strong
Expanded polystyrene (EPS) will remain the most used type of foamed plastic insulation, accounting for 49% of demand in 2027, according to a new study by The Freedonia Group.
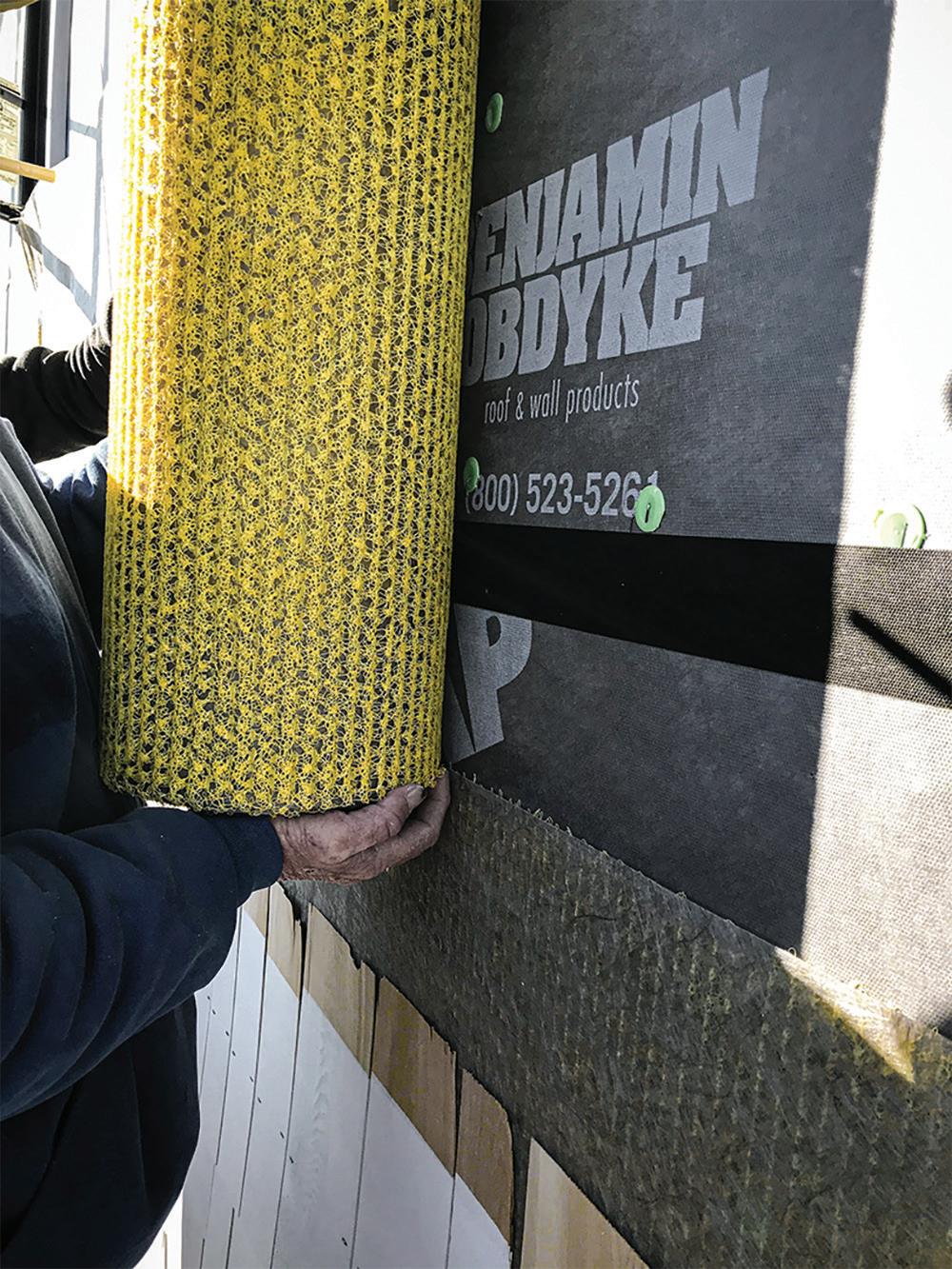
Demand for EPS insulation is expected to grow 3.3% per year to 4.8 million metric tons in 2026, with gains to be bolstered by:
• the ongoing use of concrete building construction methods throughout the world, as EPS used in insulated concrete forms can enhance the insulation of concrete building products without affecting their structural strength
• the rising popularity of prefabricated housing and insulated building panels
• gains in industrial and HVAC equipment production, where EPS is favored due to its low cost, light weight, and ability to be wrapped around pipes
• its continued pricing advantages over competing foamed plastic products, an important consideration in developing markets
Despite a major downturn in construction in India and Central and South America in 2020, ongoing declines in single-family housing construction in China, a severe crash in the Italian and Spanish housing markets early in the historical period, the global foamed plastic insulation market in weight terms expanded at an annual rate of 3.6% from 2011 to 2021.