
9 minute read
WESTERN WOOD PRESERVERS
Treaters re ect on unique challenges of a pandemic year
By Butch Bernhardt
Wood treaters saw sales of preserved wood products skyrocket last year, with a surge in home projects like decks and outdoor accessories. Treaters were hard pressed to keep up with demand as they sought to increase production while dealing with pandemic restrictions at their plants.
THE YEAR 2020 for wood treaters in the West could be summed up in Charles Dickens’ opening line from his novel A Tale of Two Cities: “It was the best of times, it was the worst of times.”
While the pandemic caused much economic damage, the wood products industry—including treaters—saw unexpected, but welcome growth in sales and product prices. And for preserved wood, those positive business trends for are carrying into 2021 and beyond.
Stay-at-home orders and government restrictions on businesses in the early months of 2020 created uncertainty for many treaters. But that uncertainty soon transitioned into other concerns.
“The biggest challenge for our company was to pivot from planning for an expected downturn to scrambling to ramp up production when demand exceeded all expectations,” said Blair Buchanan, senior advisor at Allweather Wood.
Few anticipated that construction activity would rebound so quickly after the initial downturn. For treaters, the boom in remodeling turned up demand for preserved wood, as cash from federal stimulus checks and money normally spent for vacations was directed to home projects such as new decks and outdoor projects.
By summer, instead of bracing for lower sales, treaters faced new problems. “Raw lumber was di cult to source, labor was di cult to hire, and COVID-19 safety protocols were challenging to implement,” said Buchanan.
Treaters tackled the challenge of keeping employees safe while responding to higher sales.
“Because a lot of our business is conducted outdoors, we were able to implement the changes needed to adapt quite well,” said Janis Kristiansen of Western Wood Preserving in Sumner, Wa. “Our facility covers many acres, so fortunately ‘social distancing’ is mainly the norm for us.”
Sourcing lumber for treating became more di cult as sawmills struggled to increase production to ful ll demand. Housing starts, which plunged more than 40% in April, roared back by the summer. Meanwhile, sawmills in the West could only increase production modestly. Competition for the available supply of wood drove prices to record levels.
Since treaters purchase the same lumber products as retailers and builders, nding stock to meet the growing demand for preserved wood was a key challenge.
“Providing more exibility in our supply chain really was the lesson” from the pandemic, said Phil Schumock of Stella-Jones, Tacoma, Wa. “Having the right products ready when customers need them starts months
before the product ships.”
“It did force us to improve the transparency of our forecasting and supply chain planning to identify and resolve shortfalls,” agreed Buchanan at Allweather.
Many of the lessons learned during the pandemic will have a lasting impact at treating companies. Treaters discovered that cross-training sta to cover production operations is an important priority. Enhancing relationships with their sawmill suppliers will take on added importance in the future.
“Having good relationships with mills has helped greatly with getting wood for treating,” said Schumock at Stella-Jones.
Even as the pandemic eases, the outlook for preserved wood remains upbeat. New home construction remains strong, with mortgage rates at historic lows and growing anticipation of an expanding economy. Spending for remodeling is forecast to rise by as much as 4%, which will translate into projects involving preservative-treated wood.
“We’re extremely optimistic,” said Allweather’s Buchanan. “People have a new appreciation for the value of spending time at home with their families, and the desire to improve their outdoor environments will continue.”
“Large segments of the business sector have discovered their employees can e ectively and e ciently work from home, which bene ts home remodeling and improvements,” noted Kristiansen of Western Wood Preserving.
The treating industry will see some important steps in 2021 to get back to business as usual. So just when will things return to normal?
“If I knew that,” quipped Buchanan, “you’d be paying me for my forecast.”
Butch Bernhardt is senior program manager for the Western Wood Preservers Institute (www.wwpinstitute.org).
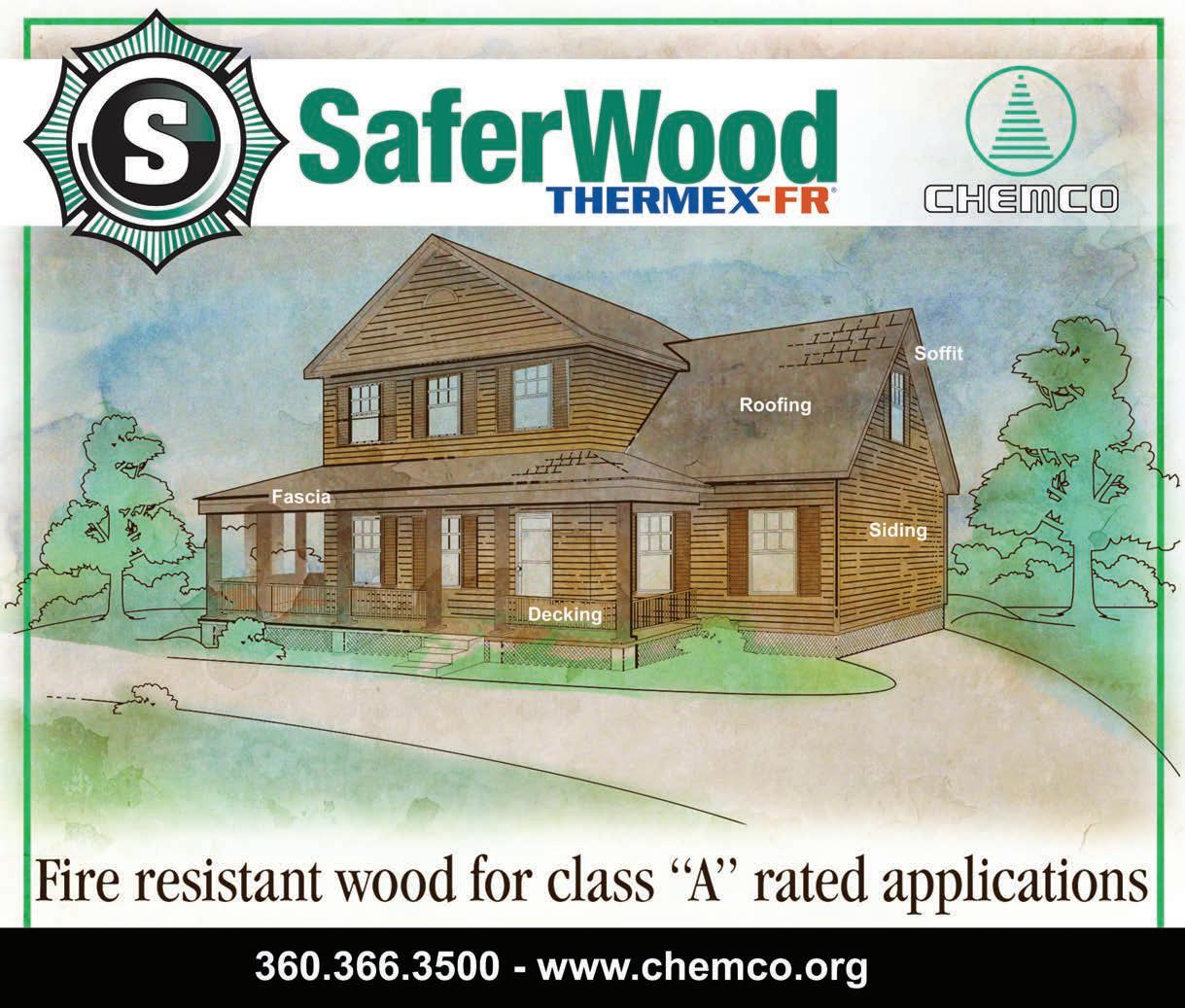
Tales of a treated wood lab tech
The team behind the scenes
By Kim Merritt
SO, THE SHELVES are lled with pressure-treated wood in preparation for the spring rush. Soon, the gardeners and doit-yourselfers will be converging on your store, tired of this crazy cold winter and ready to work on their warm-weather, outdoor projects. You are ready for them because you’re no rookie! You know how important it is for your customers to have quality products and you know that the tags on the end of the lumber is the source to nd all the important information they’ll need to select the right product for their application, including the treating company, preservative

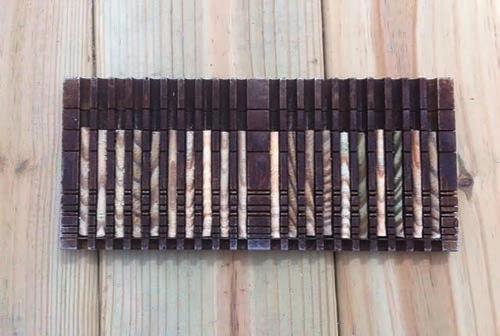
Treated wood core samples are taken periodically throughout each charge to verify the minimum level of penetration is met.
type, appropriate end use, third-party inspection information and even warranty details.
But, have you ever taken a moment to wonder… how do they even check this stu and what really goes on behindthe-scenes? If the answer is yes, let’s grab a lab coat and take a closer look!
Our tale begins at the treating plant. Treated wood producers work hard every day, conducting an in-depth, standardized process of in-plant quality control (IQC), dedicated to providing the consumer with high-quality, sustainable products for a wide range of applications (including your spring garden project). Specialized analytical equipment is used to measure the proper preservative concentration prior to treatment.
For each “charge” or batch of wood treated, core samples are taken throughout the charge to verify that the minimum preservative penetration has been met. A speci ed assay zone of these cores is then collected, dried, ground, homogenized and analyzed as a composite sample to measure the preservative retention. Industry-approved standards require that these composite assays meet a minimum preservative retention suitable for speci ed service conditions. Industry standards further require a certain number of these IQC samples be analyzed and compared to an approved laboratory’s
overall retention analysis to monitor continued accuracy of plant results.
To provide an additional layer of con dence to a plant’s quality system, accredited third-party inspection agencies, such as the Southern Pine Inspection Bureau (SPIB) and its western division, Western Wood Services (WWS), work in tandem with subscribing treated wood producers to approve and independently audit their IQC programs based on industry standards. You’ll notice the distinctive SPIB/WWS quality marks on the end-tags of material quali ed under our third-party audit program which will include the WWPI CheckMark or ICC-ES logo.
Unannounced inspections are conducted by SPIB each month to evaluate in-plant quality control requirements and to sample a prescribed number of charges. These third-party audit samples are evaluated for preservative penetration on-site by SPIB inspectors and are then submitted to the SPIB lab team for retention analysis.
These veri cation and audit processes take your journey a bit further behind-the-scenes as we follow these inspection samples to our laboratory
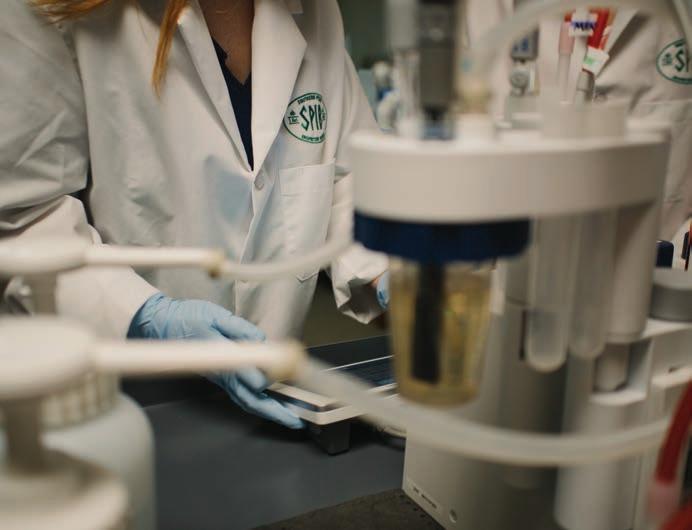
Auto titration analyzes borate or quaternary compounds to determine its concentration.
at SPIB. Using analytical methods approved by the American Wood Protection Association (AWPA), our SPIB team of lab geeks evaluate thousands of in-plant and third-party audit samples for retention analysis every year.
Most people outside of the
(Continued on next page)

laboratory setting may be unaware of the high-level skills required or the methodical processes involved in performing these types of tests. Luckily for you, we’re here to tell you more about how it’s done.
Samples that have been treated with preservatives containing metallic components are initially analyzed by X-ray analysis. When samples are exposed to X-rays, the energy causes changes to occur within the sample’s atoms. The resulting energy produced from those atomic changes can be measured by a detector to determine the amount of preservative in the sample.
Various preservative samples require additional test methods that are more complex as the chemical components cannot be measured directly and must be extracted from the wood sample. This extraction process requires a solution (usually made of alcohol) to be added to a measured amount of sample and the mixture is sonicated for several hours to release the chemicals from the sawdust.
Wood treated with borate or quaternary compounds is analyzed through a process called titration. Titration is the method of determining an unknown concentration in solution by adding a known concentrate of “titrant” in carefully measured amounts until a reaction occurs. The reaction is determined by a color or electrical change within the sample. You probably remember performing titrations in your high school chemistry class.
Some preservative components or co-biocides, such as azoles, for example, can only be identi ed and measured using analysis by Gas Chromatography (GC). The GC process uses a tiny portion of the ltered extract that is pulled up into a syringe and injected into the instrument. As the sample travels through a column, each component reaches the end of the column at di erent times and moves past a detector. The detector can measure these components and record their output as peaks in a chromatogram. Other non-metallic, organic preservative systems contain components that must be analyzed by a similar test method known as high-performance liquid chromatography (a.k.a. high-pressure liquid chromatography or HPLC).
Once all the assays are completed for each component in a sample, the results are combined, and the nal retention result is calculated! Sounds like a lot of work doesn’t it? But the process doesn’t stop here. While this information is certainly vital to evaluate plant performance for each inspection as required by the AWPA, it also provides invaluable cumulative information to identify trends that assist the plant in maintaining product conformance and making any adjustments they deem necessary to consistently meet their treatment goals!
Thank you for taking this inside look with us. Now that you have and your behind-the-scenes appreciation for all the work that goes into the quality of your treated wood products, you can take o your lab coat and send those gardeners and do-it-yourselfers out into the backyard with con dence! The SPIB Lab Team hopes your spring weather is pleasant and those projects look great this year!
– Kim Merritt is director of the Treated Division of the Southern Pine Inspection Bureau (www.spib.org).
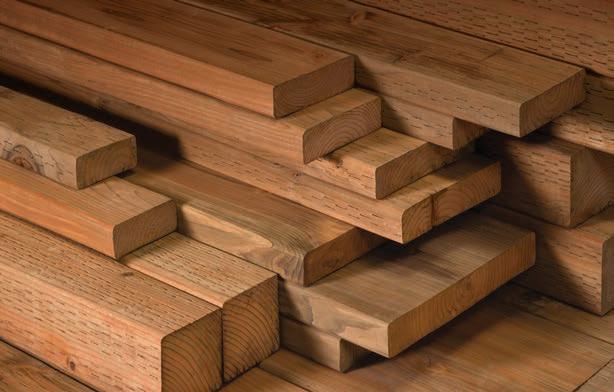
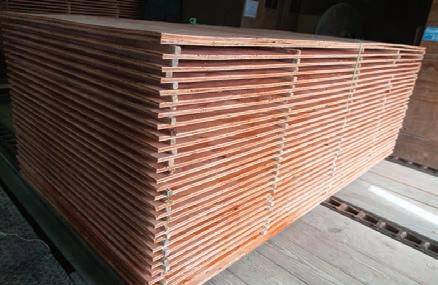
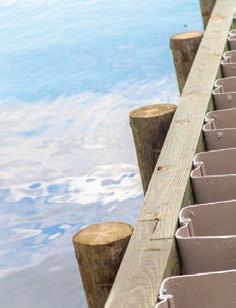
• Full Service Pressure Treated Lumber & Plywood • Cedar Deck Accessories • Specialty Decking Products • Dricon Fire Retardant Plywood & Lumber • Marine Piling • Residential and Industrial Treated Lumber
Tacoma, WA 800-426-8430 Warsaw, VA 800-368-2536
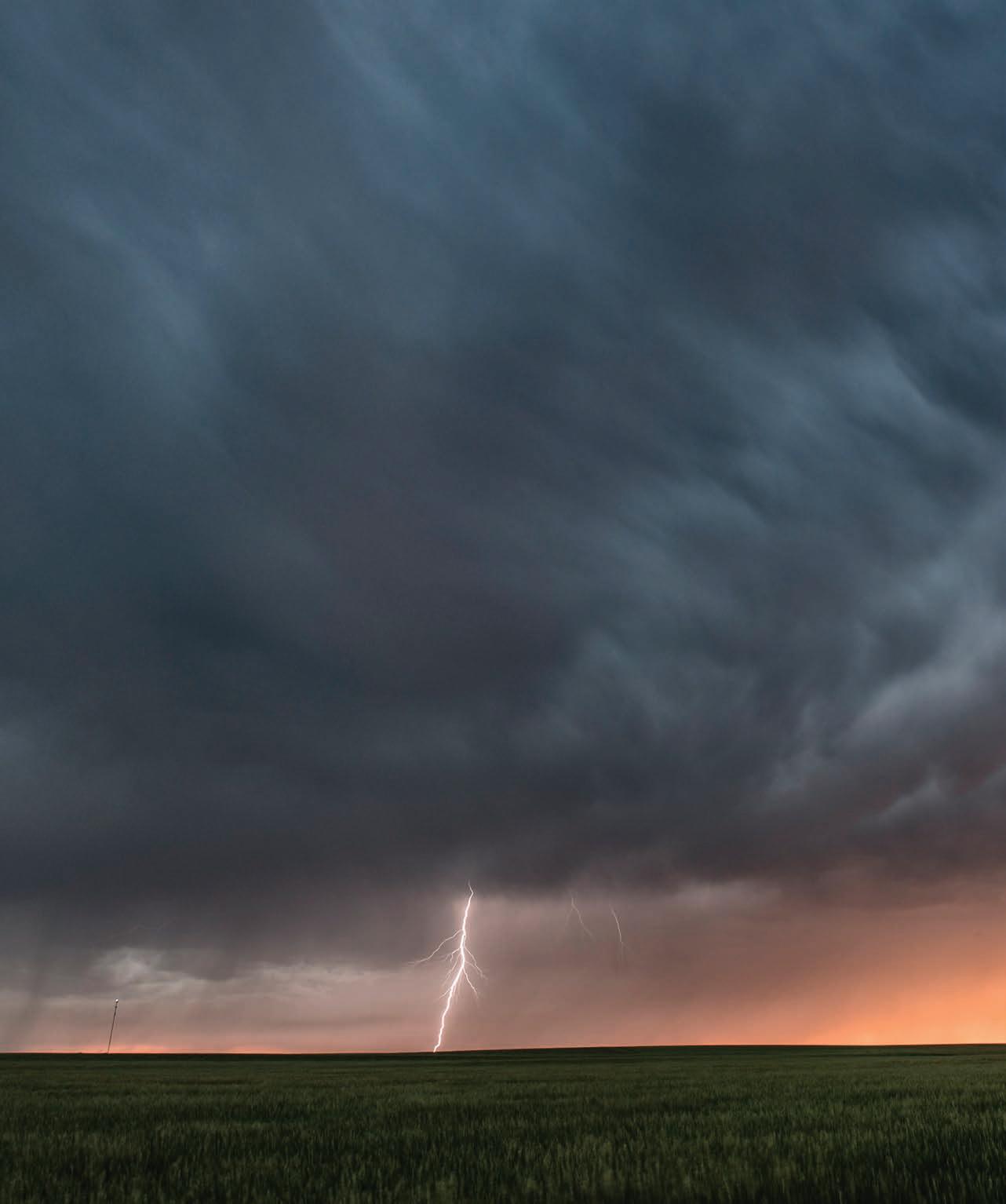