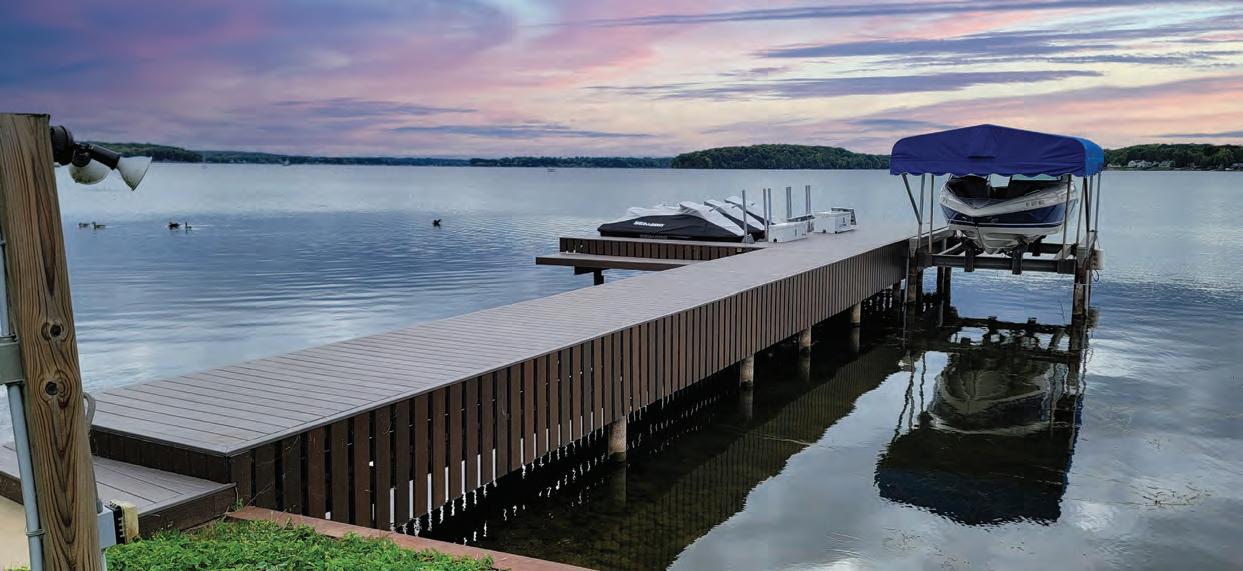
7 minute read
induStry trendS
LATEST CAPPED composite decking offers superior moisture resistance, making it ideal for the marine environment. (Photos by MoistureShield)
New wave of demand for shoreside amenities
There is a growing trend in decking that LBM dealers can help equip their customers to capitalize on: amenities on the water. Deck and dock builders are finding that customers, both homeowners and businesses, are seeking the same comforts seen in today’s luxurious decks on docks and marinas, either near or on the water.
Brandon Martin, owner of Martin’s Custom Tidesides of Sodus Point, N.Y., builds about 30 docks per year and provides everything related to shoreside leisure projects, currently with 18 seasonal and full-time employees. He buys his decking and building materials from HEP sales, with locations in the Central, Western and Southern tier regions of New York State, with one location in northern Pennsylvania. “What we look for in a dealer is the supply of products that can hold up to changing waterfront conditions,” he said.
Brandon’s team covers the large shoreline region of Lake Ontario in New York state, from Hilton to Oswego and south to the Finger Lakes’ 1,000 Islands and Old Forge. As one of very few official distributors of top-of-the-line boat lift and floating dock systems in the lake region, Brandon and his wife, Ashley, also own and operate a marina in Sodus Point, selling boats and boating equipment.
“Homeowners want more dockside luxury with a fully enjoyable experience all year round,” he said. And as much as Brandon was frustrated by the pandemic’s limitations, he said it greatly contributed to this unprecedented demand for outdoor living, especially on the shoreline. “The pandemic spurred a renewed investment in shoreline life—living rooms and dining areas on the dock, nicer boat houses, furniture, outdoor kitchens, hardscapes, fire pits and heaters. They also want more open space and nicer materials, which has also prompted a need for technology.”
This high demand for shoreline luxury decks created a need for better performance and aesthetics beyond what wood could deliver. “We’ve discovered a dock and deck material that checks all the boxes for a marine environment,” said Brandon. “We rely exclusively on capped composite decking for about 90% of the decking on our projects, so superior moisture-resistance and submersion is a must. The other 10% are concrete where deck footings cannot be installed, so we’ll pour a 6” pad of concrete.”
Martin’s crew also required a less heavy, dense material because it’s often hauled down a hill to the water and loaded on barges. Barges are used for construction on the water, to set trusses and have stacks of decking handed off to the crew. From the barges, 8” pipes are driven into the bottom bed with a vibratory pile driver for the framing. “This is back-breaking work, so having a composite material you can manage while everything is moving on the water really matters,” said Brandon. “Mother nature is the biggest challenge with water movement, wind and rain all working against you.”
Rising Tides Cause Dock Exposure
Rising and falling water levels can be challenging for dock builders, because it leaves dock areas that have been under water exposed. “This is where submersible compos-
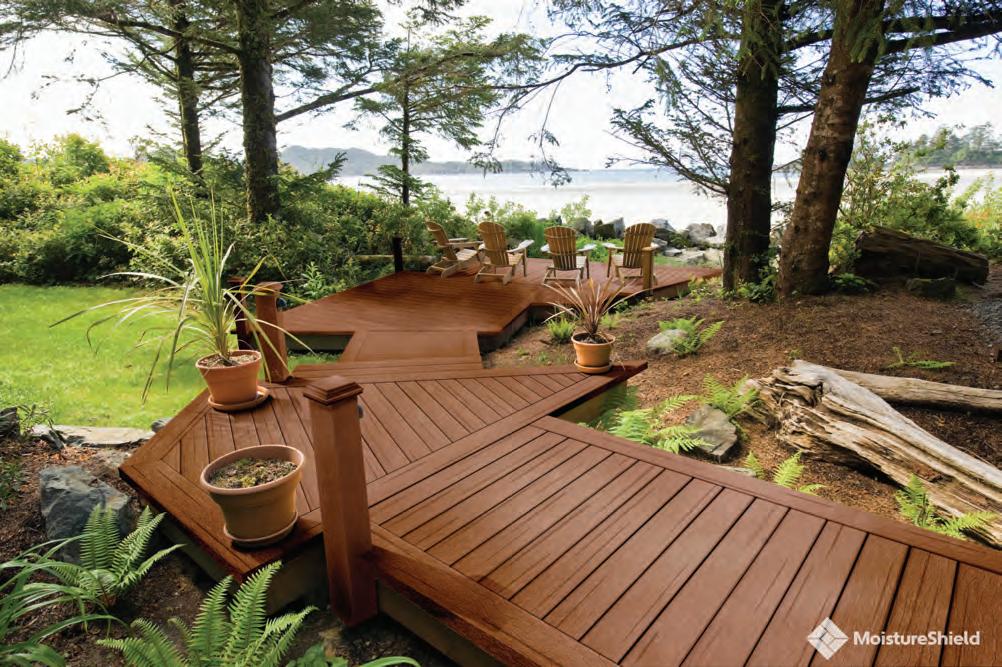
ite deck materials become a gamer-changer for us,” he said. Brandon calls the water line on a dock the “scum line” where some materials can end up looking discolored and stained. As an example, he said there was flooding in 2017 and 2019 where Lake Ontario docks were completely under water. When the water receded, the pressure-treated wood docks were “slimed” and pressure-washing them destroyed the surface; but after discovering a capped composite that could be submerged without damage, he said “there were no marks at all, even after four years, and it looked like the day it was installed. Submersion is huge for our docks, because some materials lose their warranty at 18”—so you need to check the product claims and specs on these products.” CONSTRUCTION IS UNDERWAY on a new TFL plant in Klamath Falls, Or., to meet growing demand in the West. Brandon uses a public boat launch near his marina on Sodus Point that gets constant year-round traffic from boaters and winter fisherman, turning the ramp into “a great showcase for us, because when my customers see how the decking has performed in harsh conditions, they believe it.” Brandon also uses composite boards in a vertical application as side skirting to accommodate unpredictable water levels, so when the water is low, the boats do not go under the dock and get damaged. “Fascia around the dock only covers 12”, so we use the decking vertically to create a bumper for boats and watercraft,” he said. “In a high-water year, the skirt boards can be submerged for months, but the next year that whole board is exposed, so it just needs to be cleaned up and nicely matches the rest of the decking.” Wilsonart Expands TFL in West Wilsonart Engineered Surfaces has broken ground on a new thermally fused laminate (TFL) facility in Klamath Falls, Or. Expected to be fully operational by July 2021, the new facility will feature a quick-cycle press, which will significantly increase its production capabilities on the West Coast. “Our offerings have garnered tremendous support from both specifiers and fabricators,” said Ron Ubertini, VP-product management. “TFL is a key part of that offering, and this next expansion is a continuation of our strategy to enable us to meet growing demand and better serve our customers.”
Splinters and Heat
Splinters and heat are another big problem for docks, Brandon noted, with increased water activities. With splintering, shrinking wood that also creates raised nail heads, shoes and bathing suits get snagged and bare feet are a problem.
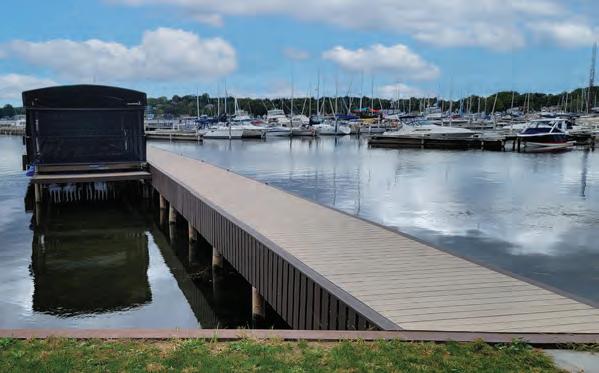
Lowe’s Bulking Up in the West
To meet fast-growing demand for building materials, Lowe’s Home Improvement Centers, Mooresville, N.C., will invest $1.7 billion to update its supply chain—with much of the expansion centered across the western United States.
Over the past 18 months, Lowe’s opened more than a dozen facilities, including in Riverside, Ca.
Over the coming year and a half, the chain is expected to open 50 more cross-dock terminals, seven bulk distribution centers, and four e-commerce fulfillment centers. It recently inked deals for new distribution space in California, Arizona and Washington, among other states.
In October, Lowe’s opened a West Coast e-commerce fulfillment center in Mira Loma, Ca., said to improve two-day deliveries.
Lowe’s has leased 116,934-sq. ft. in a new industrial park in Gilbert, Az., to open a distribution and fulfillment center in early 2021.
It reportedly also agreed to lease 1.2 million sq. ft. at the Benaroya Pacific Northwest Regional Logistics Center in NEW YORK dock used capped composite decking underfoot, as well as for Winlock, Wa. fascia to create a bumper for the watercraft.
Second-Hand Lumberyard Reopens
“If you sit on the edge, your legs can get burned,” he said. “We like that there are new technologies that have given us a great option for keeping surface temperatures lower, even in direct sun. And with composite decking, you get a smoother surface, but no splinters or raised fasteners. The bottom line for Martin’s Custom Tidesides is getting all the amenities of outdoor living as close to the shoreline as possible, with top-of-the-line equipment and docks that add luxury with all the comforts of home. To achieve that, he said you have to build with an eye toward design and technologydriven materials. in Flagstaff After being closed for nearly nine years, E.R.I.C. Building Supply, Flagstaff, Az., has reopened with a new owner. Construction industry veteran Darwin Dahozy purchased the business and inventory, and reopened in early October after a month of prepping the long-vacant space. He admits their current collection of used, recycled and discarded building materials will require more time to organize, so initially will be closed on Mondays through Wednesdays as it continues to “clean up and organize.” Dahozy, 49, moved to the area two years ago looking to – Matthew Bruce is vice president of sales for MoistureShield buy or start his own business, after a career as a welder and (www.moistureshield.com). residential/commercial fencer.
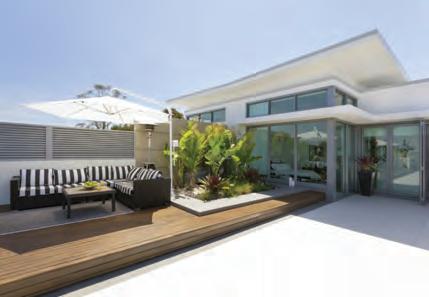
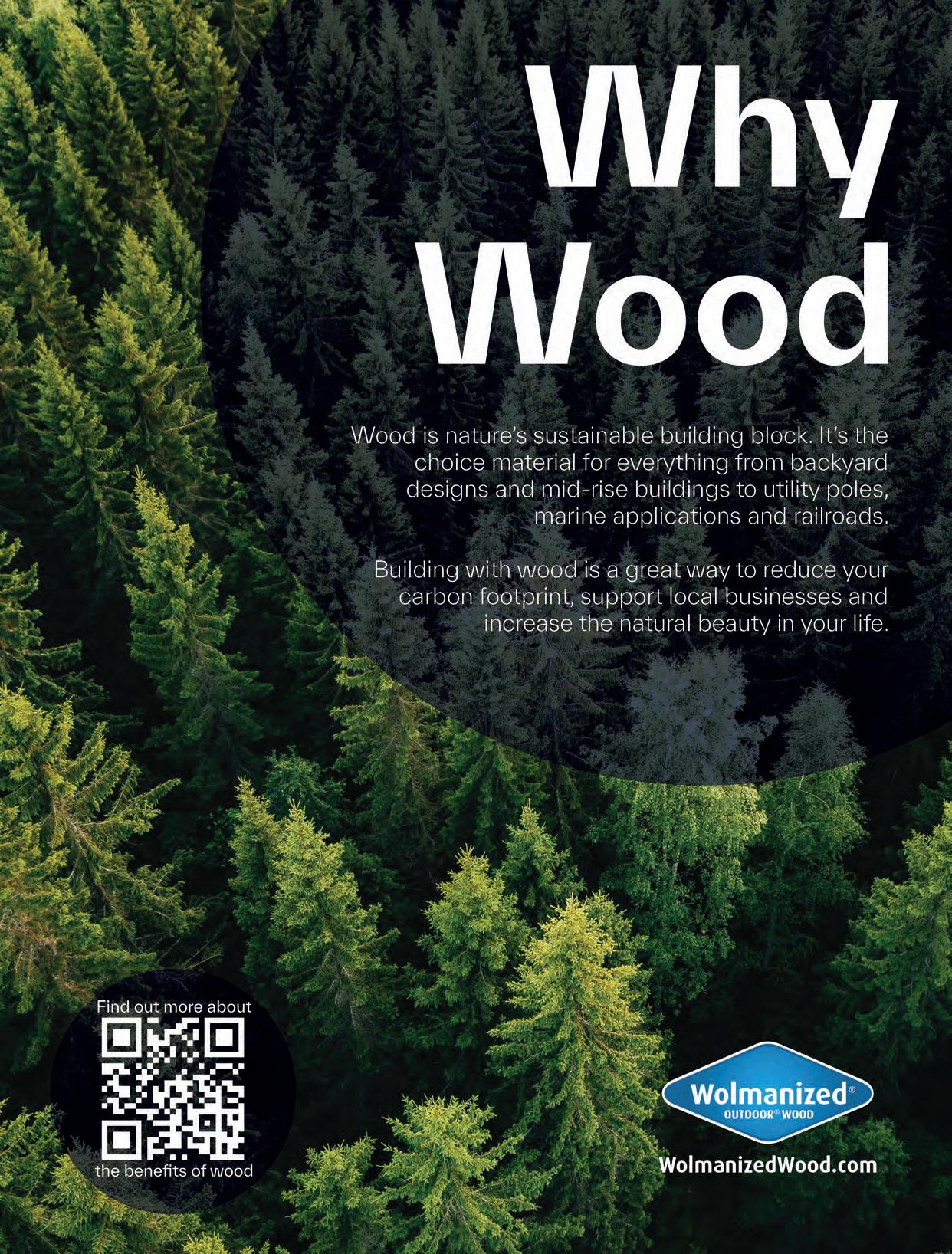