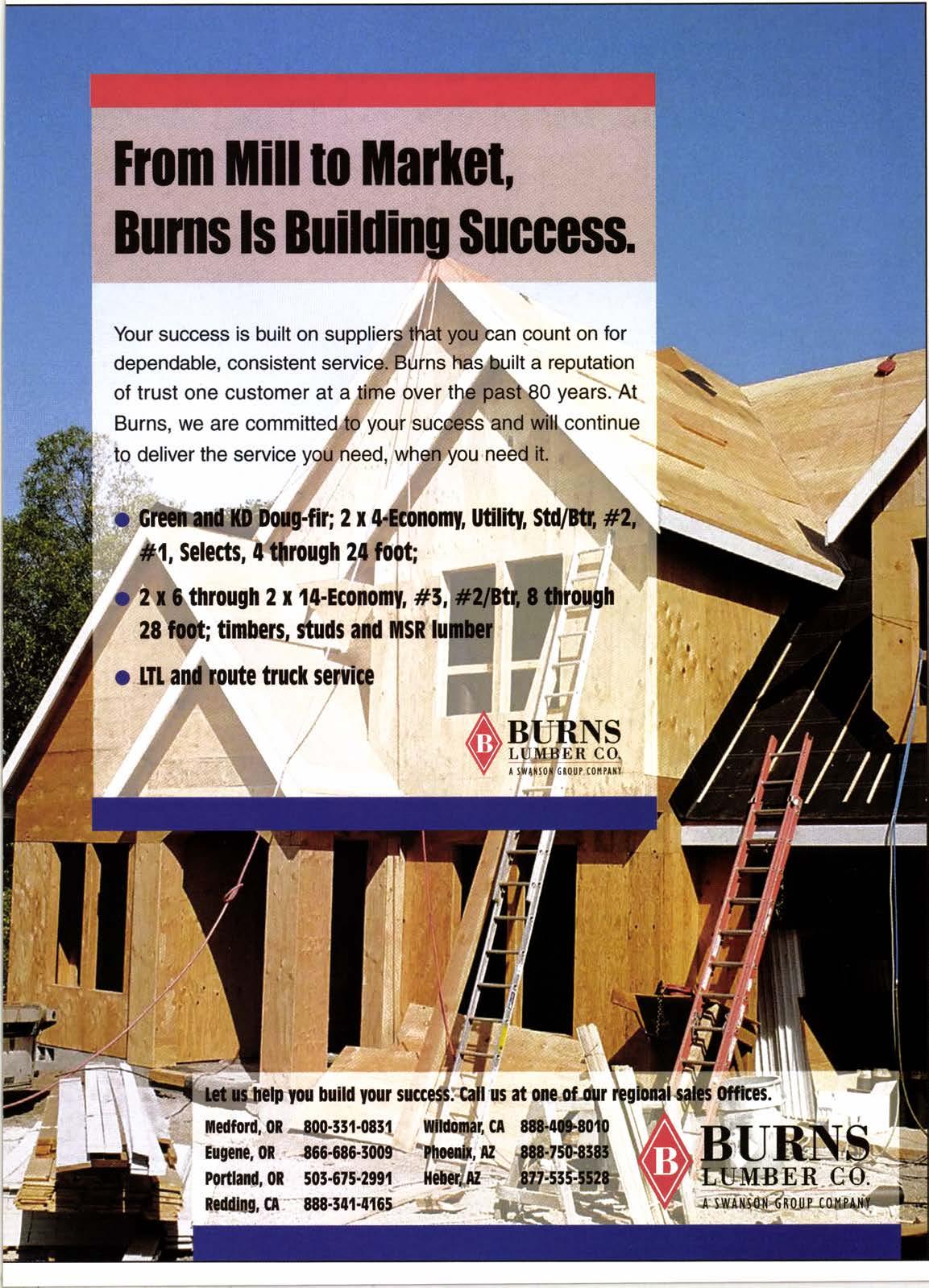
3 minute read
lrom tilill to illarftol Burns ls Buililing $uccg$s.
Your success is built on suppliers that you can count on for dependable, consistent service. Burns has built a reputation of trust one customer at a time over the past B0 years. At Burns, we are committed to your success and will continue to deliver the service vou need. when vou need it.
Green and rul Doug-fir; 2 r 4-Economy, Utility, stdlBtJ, #2, #{, Selects, 4 through 24 foot;
2 r 6 through 2 x {4-EconomU, #3, #zlBtt,8 through 28 f00t; timbets, studs and MSR lumber lTL and route truclr seruice
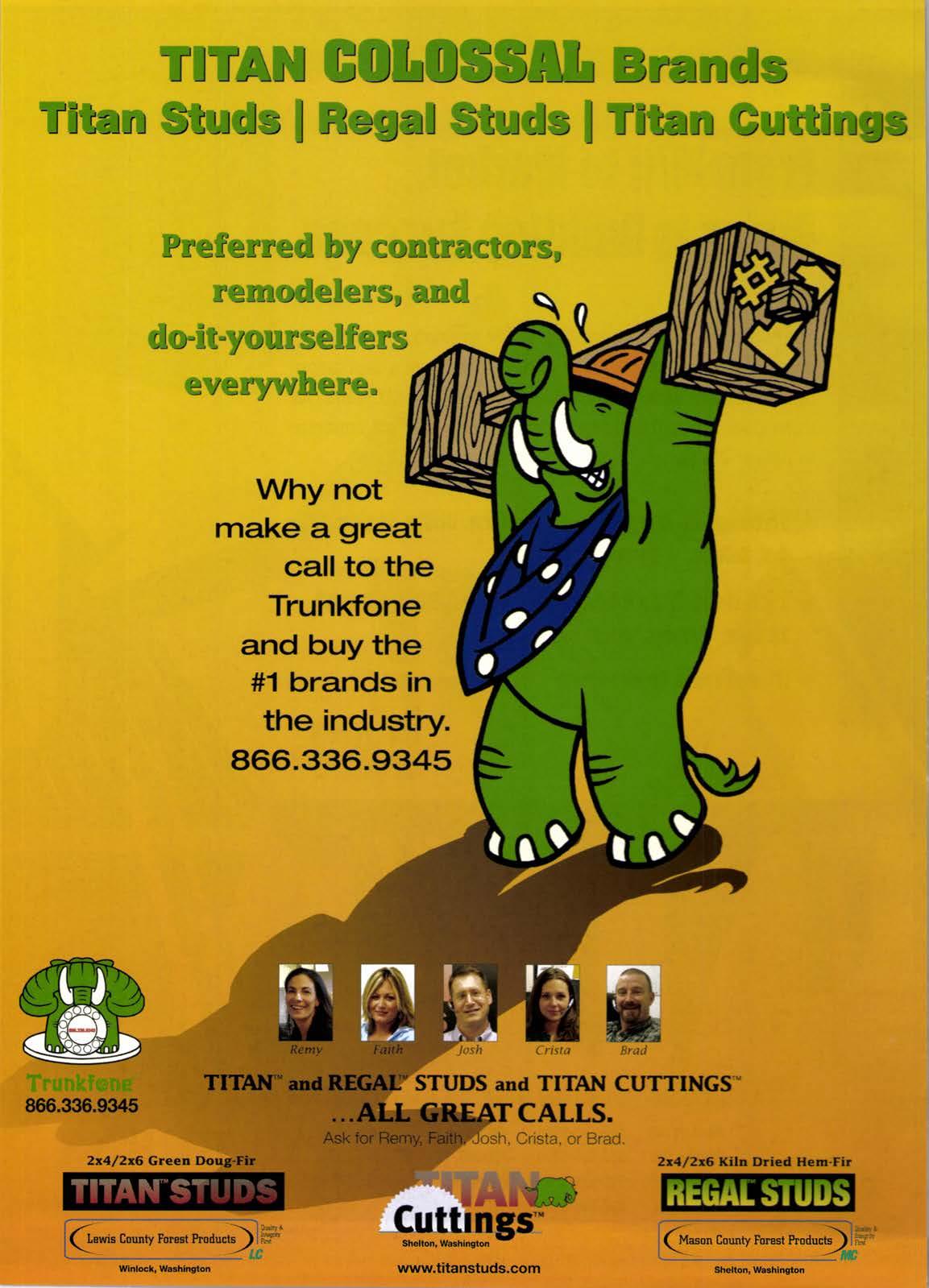
(-rAN companies really attain zero \-,injuries in the workplace? Many executives. managers. supervisors and workers think not.
Imagine for a moment that one of your children has secured his or her first job with a company in your industry. Your child calls you after the first day at work and says, "At the orientation today, they said there is a likelihood that I will either be injured or die on the job while working for this company."
What would your reaction be? If you're like most parents, you'd tell your child not to work for that company. After all, who would want any family member to work in a company where the assumption was that people will be injured or even killed?
When you say, "Zero injuries are not possible in our workplace," you're telling employees that they are likely to be hurt or die at work, just like the previous scenario.
The solution may seem simple, but it works. To attain zero workplace injuries, you must have a goal of zero injuries. Even more than that, you must believe zero injuries is possible and have that belief become the entire company's philosophy.
Current Workplace Safety
There is an increasingly demanding and complex business environment. Managers and employees must make tough choices daily when it comes to production, quality and safety. We often feel like we're being barraged with regulations and rules. In the midst of all this, despite our best efforts, workers get injured on the job.
According to OSHA, more than 5,700 workers died as a result of workplace injury and illness in 2004. The year before, 4.4 million workers were injured or became ill. As a result, companies spend over $50 billion a year on injuries and illnesses.
With all this money going towards safety-related issues, why are workers still becoming injured? Many organizations do not have an over-arching safety philosophy. The demands of competition, globalization, mergers and acquisitions often take priority in the minds of managers and executives, leaving safety on the back burner.
Managers and executives can create sustainable, positive change by developing a philosophy that promotes safety and de-emphasizes compliance. The philosophy must give equal weight to five areas: management commitment, employee involvement, worksite analysis, hazard prevention and control, and health and safety training. Too often, companies focus on only one or two of these areas.
Higher Standards & You
Adopting high safety standards is easier than you may think. In fact, all it takes is four simple steps: l. Understand the five areas that must be covered by the standard: Management commitment. Provide outstanding protection to workers through effective systems and actions by executives and supervisors.
. Employee involvement. Interest and involve workers in safety processes, including audits, accident investigations, suggestion programs, and safety committees.
Worksite analysis. Systematically assess and manage worksite hazards.
, Hazard prevention and control. Commit to safety through preventative equipment maintenance, workplace health processes, hazard tracking methods, and emergency preparations.

Safety and health training. Ensure workers know how to perform all aspects oftheirjob to prevent injury.
2. Develop a safety philosophy in the organization. Ask yourself:
What does my firm really believe about worker safety and health?
. Do executives and supervisors understand their moral and legal obligations about safety and health?
. Do we really believe the company can have zero injuries?
The answers to these questions will tell you what your company's safety philosophy is. You may have to work to educate leaders and get their thinking aligned with the importance of creating an environment where safety and worker health are paramount concerns. but the effort is worth it.
3. Determine the current state of the company's health and safety management program. Then develop a vision of where it should be.
4, Reveal the gap between your current and your future state of health and safety. Only then can you begin to take actions to fill the gaps and create an environment where everyone can go home every day without injury.
- Carl Potter. CSP, CMC and Deb Potter. PhD. CMC are consultants and authors of several books including Zero! Responsible Safety Management by Design. Reach them at Potter & Associates, (800) 2 59 -6209 : www.notte randas s ociate s.c om.