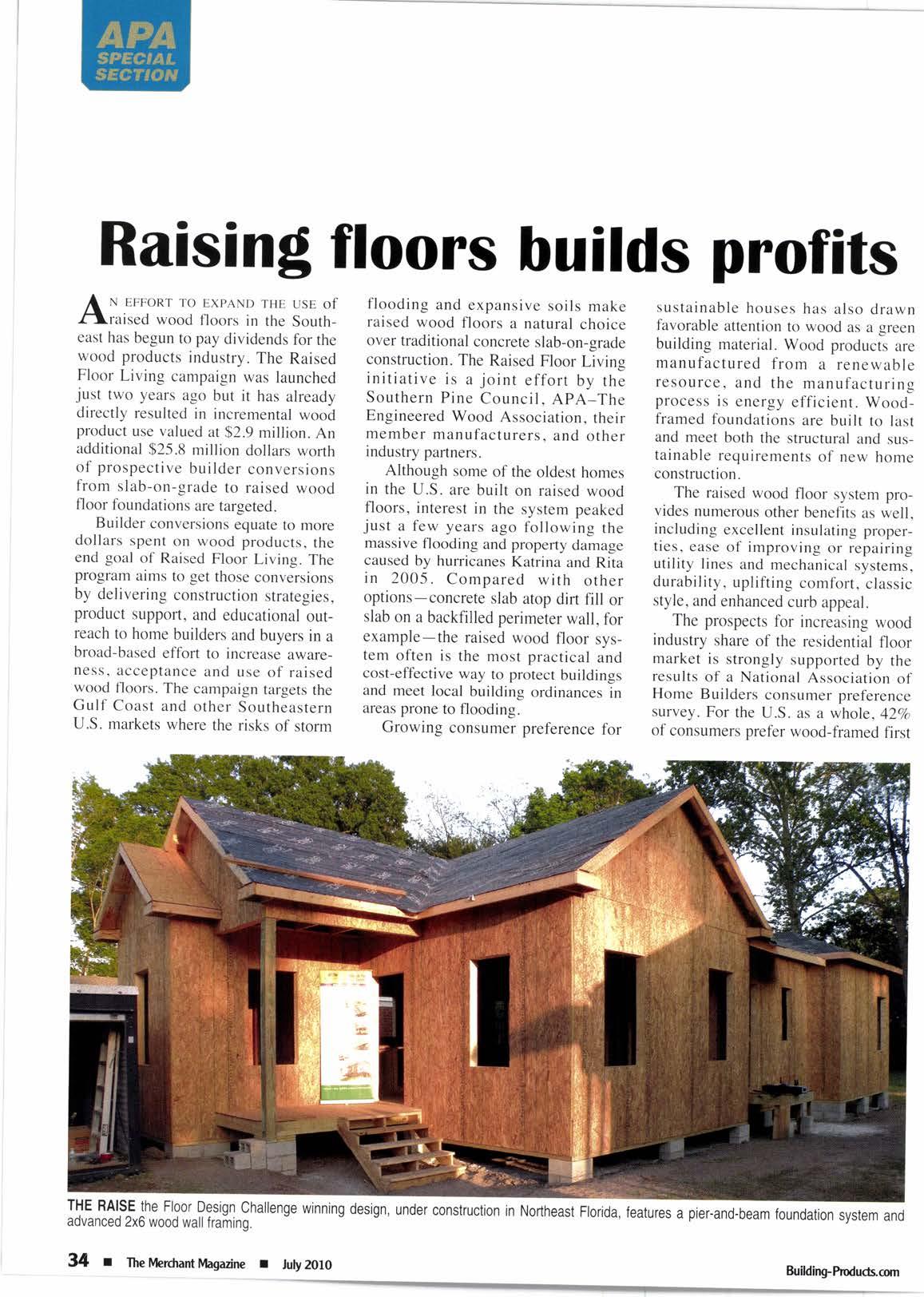
5 minute read
Raising floors builds profits
f, n unnonr ro EXeAND tHe usE of fl,raised wood floors in the Southeast has begun to pay dividends for the wood products industry. The Raised Floor Living campaign was launched just two years ago but it has already directly resulted in incremental wood product use valued at $2.9 million. An additional $25.8 million dollars worth of prospective builder conversions from slab-on-grade to raised wood floor foundations are targeted.
Builder conversions equate to more dollars spent on wood products, the end goal of Raised Floor Living. The program aims to get those conversions by delivering construction strategies, product support, and educational outreach to home builders and buyers in a broad-based effort to increase awareness, acceptance and use of raised wood floors. The campaign targets the Gulf Coast and other Southeastern U.S. markets where the risks of storm flooding and expansive soils make raised wood floors a natural choice over traditional concrete slab-on-grade construction. The Raised Floor Livins initiative is a joint effort by thE Southern Pine Council, APA-The Engineered Wood Association, their member manufacturers, and other industry partners. Although some of the oldest homes in the U.S. are built on raised wood floors, interest in the system peaked just a few years ago following the massive flooding and property damage caused by hurricanes Katrina and Rita in 2005. Compared with other options-concrete slab atop dirt fill or slab on a backfilled perimeter wall, for example-the raised wood floor system often is the most practical and cost-effective way to protect buildings and meet local building ordinances in areas prone to flooding.
Growing consumer preference for sustainable houses has also drawn favorable attention to wood as a sreen building material. Wood produci are manufactured from a renewable resource, and the manufacturing process is energy efficient. Woodframed foundations are built to last and meet both the structural and sustainable requirements of new home construction.
The raised wood floor system provides numerous other benefits as well, including excellent insulating properties, ease of improving or repairing utility lines and mechanical systems, durability, uplifting comfort, classic style, and enhanced curb appeal.
The prospects for increasing wood industry share of the residential floor market is strongly supported by the results of a National Association of Home Builders consumer preference survey. For the U.S. as a whole, 42Vo of consumers prefer wood-framed first
WANT TO GO GREEN? BUT NOT CERTAIN WHAT THAT IS?
SWANSON GROUP HAS THE SOLUTION.
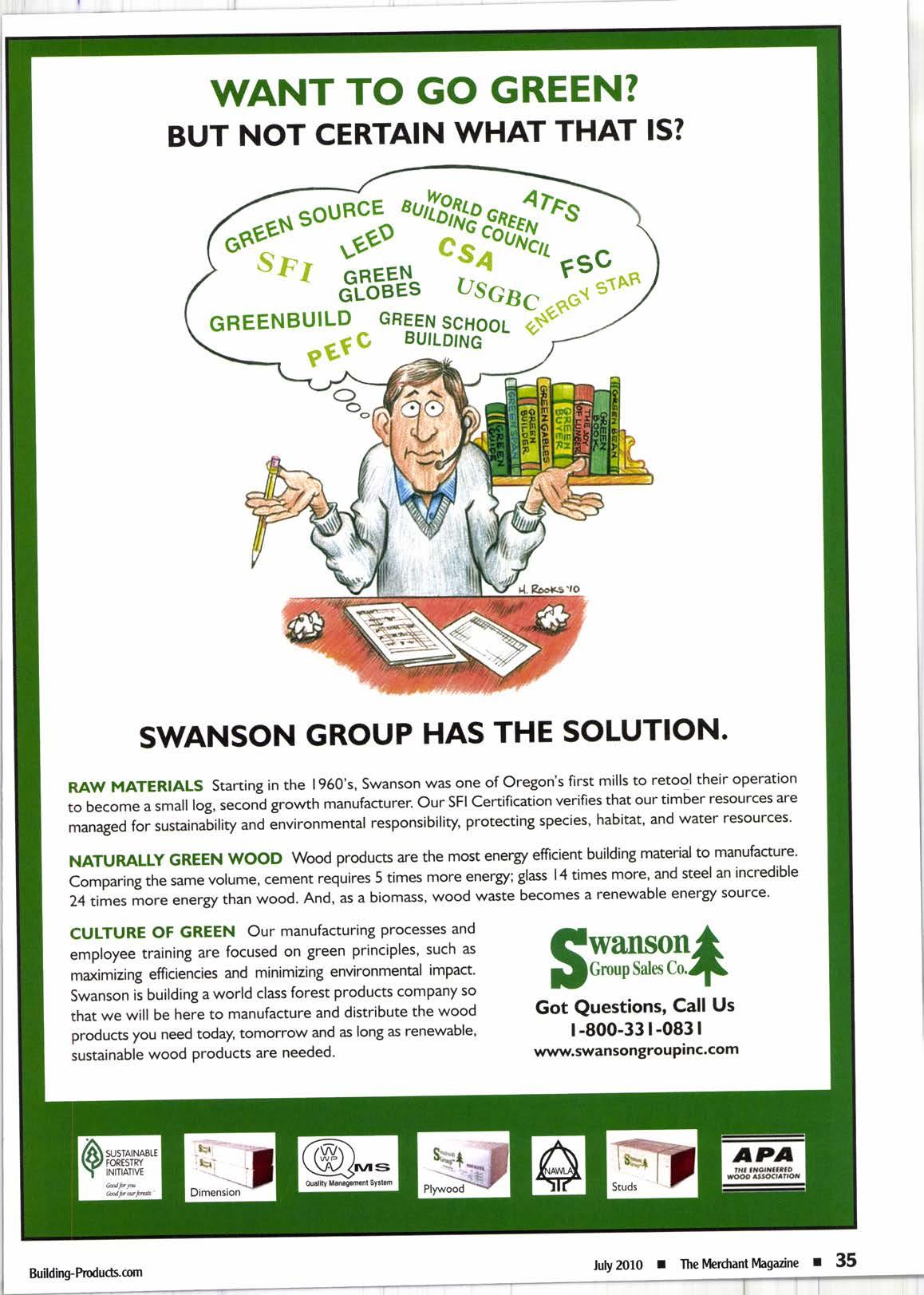
RAW MATERIALS Starting in the 1960's, Swanson w.r one of Oregon's first mills to retool their operation to become a small log, second growth manufacturer. our SFI Certification verifies that our timber resources are managed for sustainJility and environmental responsibility, protecting species, habitat, and water resources'
NATURAILY GREEN wooD wood producS are rhe most energ/ efficient building material to manufacture. Comparing the same volume, cement requires 5 times more enerry; glass l4 times more' and steel an incredible 24 times more energy than wood. And, as a biomass, wood waste becomes a renewable energy source' maximizing efficiencies and minimizing environmental impact.
Swanson is building a world class forest products comPany so that we will be here to manufacture and distribute the wood products you need today, tomorrow and as long as renewable' l floors, compared with 25Vo for concrete slab, according to the survey results. The remaining one third had no preference, were unsure, or didn't know. While the preference for concrete slabs was only 25Vo, conqete represents 53Vo of total first floor area, suggesting a wood floor promotion campaign, such as that now being conducted by Raised Floor Living,-could yield positive results.
| ,rrt"in"bl" wood products are needed.
In Northern Florida, for examplea recent target of the Raised Floor Living initiative-wood currently commands just a I Vo share of the single-family first floor market, providing a substantial target-rich opportunity for market share gain and hence greater demand for wood products. A home with a wood first floor in lieu of a concrete slab creates approximately one-third more business for the dealer.
The Raised Flooring Living program employs a wide variety of educational tools and promotional tactics, including professional seminars and training events, demonstration projects, trade and consumer publicity, advertising. local television coverage. publications and a website (www. raisedfloorliving.com) that features comprehensive raised floor details, construction tips, and other informa- tion. APA activities are aimed at educating builders, framers, designers and building code officials about the merits of wood construction, while SpC is working both to create consumer awareness of raised wood floor features and benefits and to complement APA's design and construction education efforts. Campaign updates are at www.apawood.org/raisedwoodfl oors. Direct interaction with the buildins community through face-to-face meetl ings, educational events, and sales calls is a key to building awareness and acceptance of raised wood floors. Last year, Raised Floor Livins launched its market developmen-t efforts in North Florida with the Raise the Floor Design Challenge, inviting home builders and designers to compete for the chance to design and build an award-winning raised wood floor home. The competition, co-sponsored by the Northeast Florida Builders Association (NEFBA) and the Florida Wood Council, kicked-off with a promotional event at NEFBA headquarters that drew more than 200 buildins professionals. Twenty-three designeri entered the contest.
Construction of the winnins raised wood floor home design be-gan on April l. The building site is doubling as a demonstration home-a classroom for educating local builders, designers and material distributors about innovative products and energyefficient building systems. The first two open houses, which showcased the raised wood pier-and-beam foundation system and advanced 2x6 wood wall framing, drew an audience of more than 110 building professionals, thanks in large part to NEFBA, the local American Institute of Architects, the local chapter of the American Institute of Building Designers, and the local Residential Engineers Associa-tion, all of which widely publicized the events. A third open house is scheduled to highlight energy-efficient building systems.
The positive response to last year's design challenge led Raised Floor Living to coordinate two mini desisn competitions this year in Houstoi, Tx., and Charlotte, N.C. Althoueh smaller in scale than the orisin;l design challenge, the correspoiding Design Your Dream Home promotion for consumers-in which one homeowner from each market was awarded design fees for a raised wood floor home-was heavily promoted through a series of in-depth television features that highlighted the benefits of build- ing raised from the homeowner's perspective.
From 2009 through the first quarter of 2010, Raised Floor Living hosted 69 educational events, demonstrations and seminars in markets like Houston' Charlotte, and Pensacola, Fl., with a total attendance of over 2,400. According to post-seminar surveys. 69Vo of attendees said that they were more likely to build or specify raised wood floors because of the seminar. Another lg%o said they were possibly more likely to build or specify raised wood floors.
Raised Floor Living is targeting national builders and regional builders of all sizes in its effort to influence conversions from elevated concrete slab foundations to raised wood floors. Value-engineering, custom evaluations that help to debunk misconceptions about the economies and longterm performance advantages of wood construction, is a keY strategy.
Raised Floor Living's value-engineering services can include a customized cost-comParison rePort between raised wood floor and concrete slab construction, computer-generated design comparisons, or assistance creating a complete set of archi- tectural and engineering Plans. Though these services represent a significant commitment of time and resources, the effort is validated when a builder decides to convert.
"Displacing concrete slab floors' particularly in traditionally concrete markets, is a long-term challenge," said APA project manager Bob Clark. But the program is gaining momentum, and "we're seeing tangible results in terms of both awareness of the raised floor alternative and actual conversions."
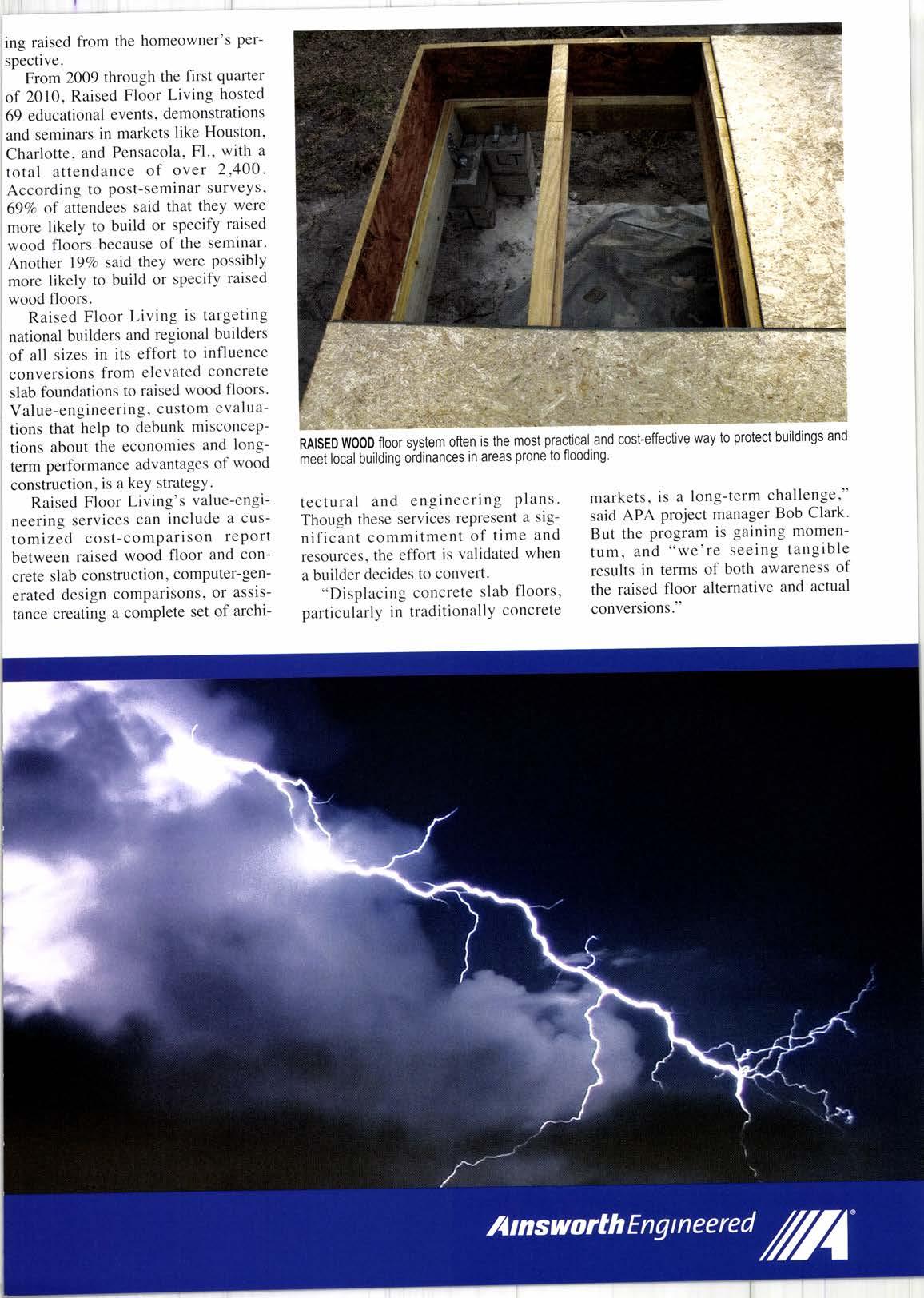