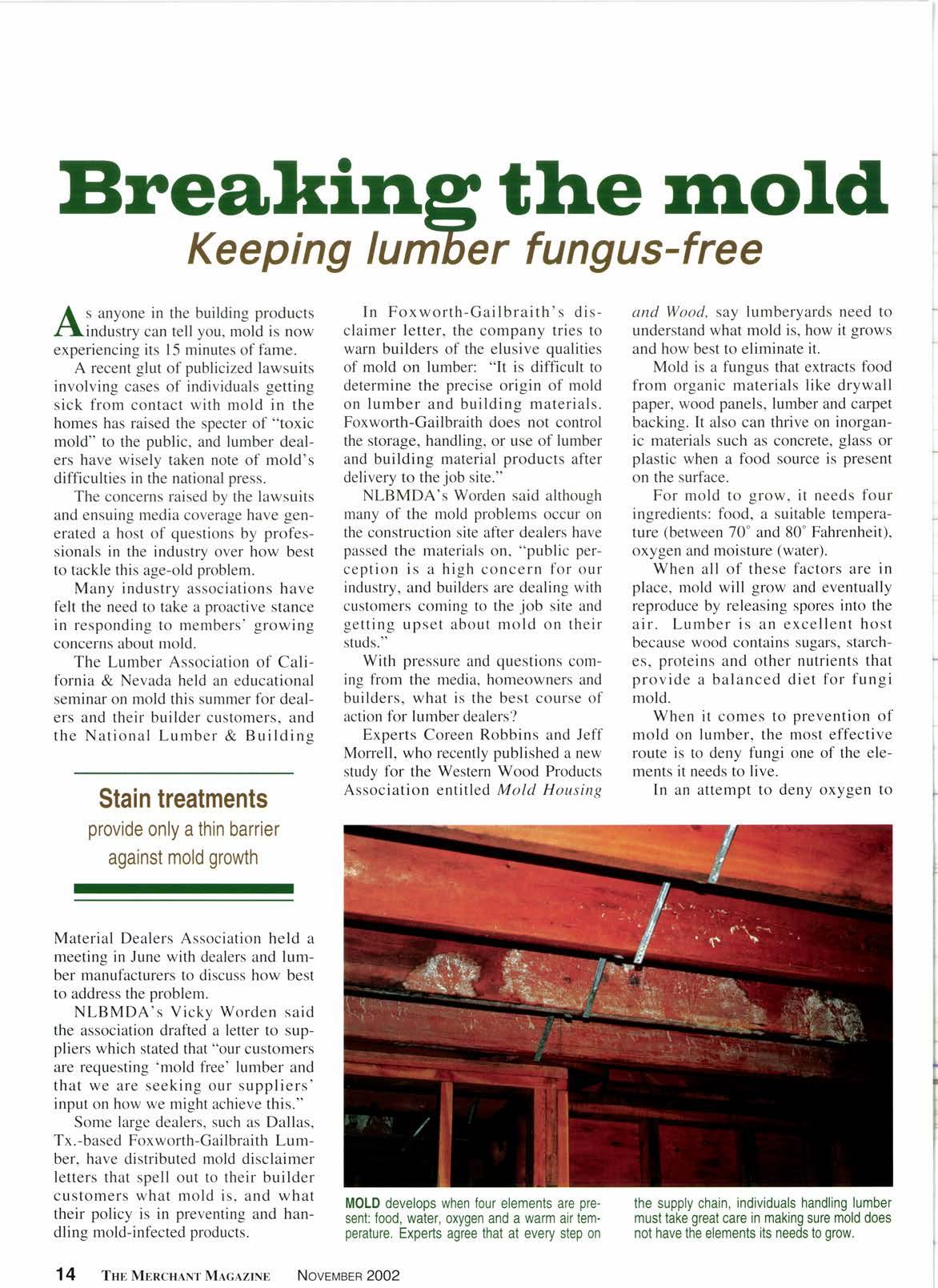
3 minute read
Brea,Irirnef the rnofd Keepi ng turffier fungus-free
f, s anyone in the building products .Cl,industrv can tell vou. mold is now experiencing its l5 minutes of fame.
A recent glut of publicized lawsuits involving cases of individuals getting sick from contact with mold in the homes has raised the specter of "toxic mold" to the public, and lumber dealers have wisely taken note of mold's difficulties in the national press.
The concerns raised by the lawsuits and ensuing media coverage have generated a host of questions by professionals in the industry over how best to tackle this age-old problem.
Many industry associations have felt the need to take a proactive stance in responding to members' growing concerns about mold.
The Lumber Association of California & Nevada held an educational seminar on mold this summer for dealers and their builder customers, and the National Lumber & Buildins
In Foxworth-Gailbraith's disclaimer letter. the company tries to warn builders of the elusive qualities of mold on lumber: "It is difficult to determine the precise origin of mold on lumber and building materials. Foxworth-Gailbraith does not control the storage, handling, or use of lumber and building material products after delivery to the job site."
NLBMDA's Worden said although many of the mold problems occur on the construction site after dealers have passed the materials on, "public perception is a high concern for our industry, and builders are dealing with customers coming to the job site and getting upset about mold on their studs."
With pressure and questions coming from the media, homeowners and builders, what is the best course of action for lumber dealers?
Experts Coreen Robbins and Jeff Monell, who recently published a new study for the Western Wood Products Association entitled Mold Housing and Wood, say lumberyards need to understand what mold is, how it grows and how best to eliminate it.
Mold is a fungus that extracts food from organic materials like drywall paper, wood panels, lumber and carpet backing. lt also can thrive on inorganic materials such as concrete, glass or plastic when a food source is present on the surface.
For mold to grow, it needs four ingredients: food, a suitable temperature (between 70" and 80'Fahrenheit), oxygen and moisture (water).
When all of these factors are in place, mold will grow and eventually reproduce by releasing spores into the air. Lumber is an excellent host because wood contains sugars, starches, proteins and other nutrients that provide a balanced diet for fungi mold.
When it comes to prevention of mold on lumber, the most effective route is to deny fungi one of the elements it needs to live.
In an attempt to deny oxygen to mold, many lumber producers submerge lumber in fresh water. Some mills often duplicate this method by hosing down log decks or storing logs in ponds at the plant.
Material Dealers Association held a meeting in June with dealers and lumber manufacturers to discuss how best to address the problem.
NLBMDA's Vicky Worden said the association drafted a letter to suppliers which stated that "our customers are requesting 'mold free' lumber and that we are seeking our suppliers' input on how we might achieve this."
Some large dealers, such as Dallas, Tx.-based Foxworth-Gailbraith Lumber, have distributed mold disclaimer letters that spell out to their builder customers what mold is, and what their policy is in preventing and handling mold-infected products.
Keeping lumber dry is also another way to prevent mold. The reduction of moisture below 2OVo will generally decrease the likelihood that mold will grow.
Another fertile occasion for fungi growth is when bundles of lumber are exposed to direct sunlight. If the wrapping has trapped in moisture, the increase in bundle temperature will promote mold growth.
Although not a cure-all as some would like tq think, lumber producers can also snuff out mold growth by applying fungicides or antistains to wood surfaces.
It should be noted that stain treatments provide only a thin barrier against mold growth and generally last from three to six months.
If prevention measures fail, then cleaning mold from lumber is often the last course of action.
In cases of small fungi growth, applying a bleach solution, drying the lumber and finally sealing is often a feasible measure.
MOLD often appears on lumber as patchy, black spols, like those seen on the joists above. The EPA recommends that a combina-
When attacking larger mold problems. the lumber should first be allowed to dry as much as possible, say experts.
The Environmental Protection Agency advises that a mold detergent and water are best for most cleanup operations. When cleaning a wood surface, the EPA urges individuals to wet vacuum the area, scrub the mold with a detergent/water solution, dry the lumber and then vacuum it with a