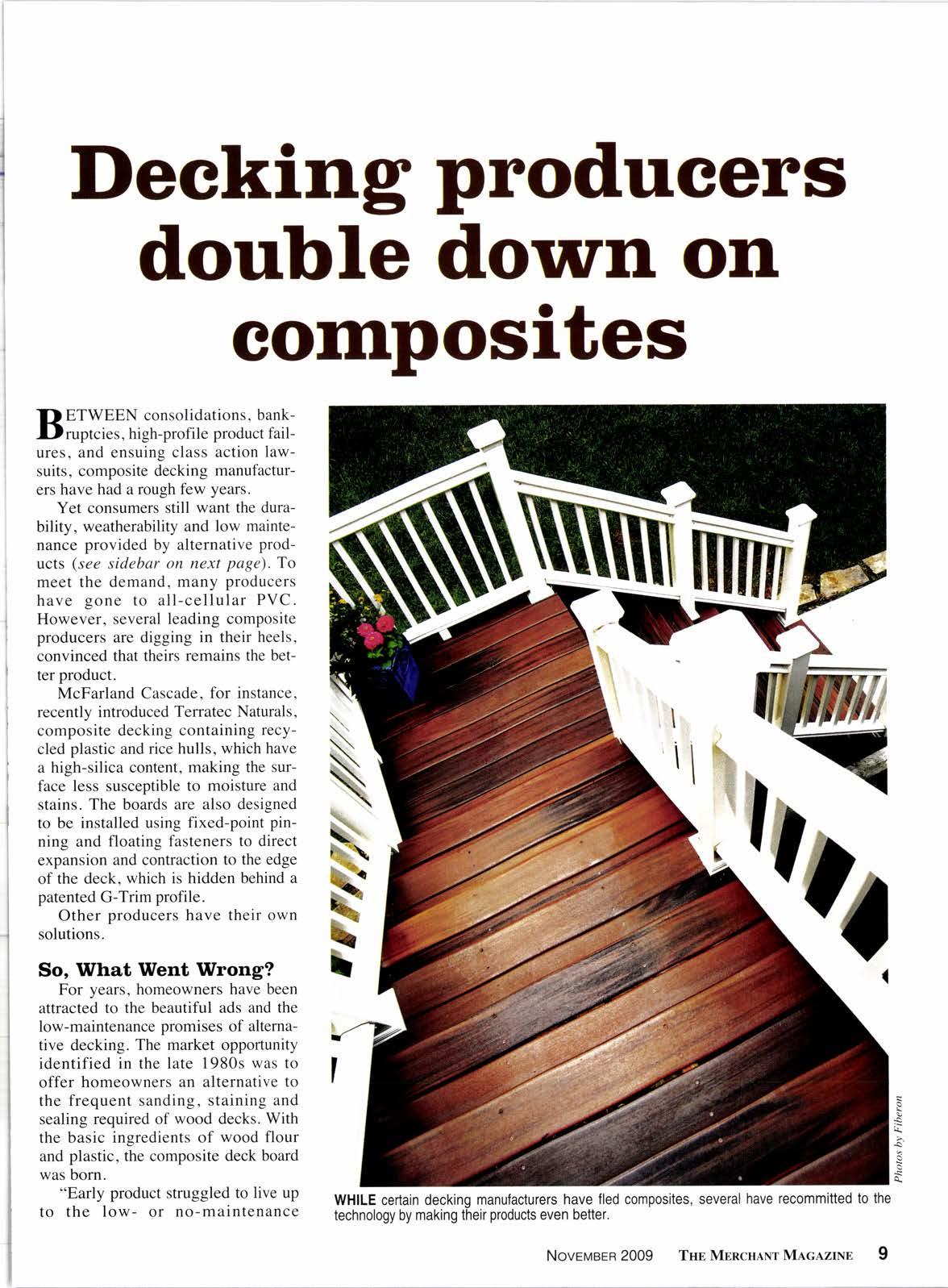
6 minute read
Deeking producers double down on composites
fD ETWEEN consolidations, bank-fD ruptcies. high-profile product failures, and ensuing class action lawsuits, composite decking manufacturers have had a rough few years.
Yet consumers still want the durability, weatherability and low maintenance provided by alternative products (see sidebar on next page).To meet the demand, many producers have gone to all-cellular PVC. However, several leading composite producers are digging in their heels, convinced that theirs remains the better product.
McFarland Cascade. for instance. recently introduced Terratec Naturals, composite decking containing recycled plastic and rice hulls, which have a high-silica content, making the surface less susceptible to moisture and stains. The boards are also designed to be installed using fixed-point pinning and floating fasteners to direct expansion and contraction to the edge of the deck, which is hidden behind a patented G-Trim profile.
Other producers have their own solutions.
So, Wrat Went Wrong?
For years, homeowners have been attracted to the beautiful ads and the low-maintenance promises of alternative decking. The market opportunity identified in the late 1980s was to offer homeowners an alternative to the frequent sanding, staining and sealing required of wood decks. With the basic ingredients of wood flour and plastic, the composite deck board was born.
"Early product struggled to live up to the low- or no-maintenance promises hyped by both the manufacturers and distributors," says Bill Ross, senior v.p. of sales for Fiberon. "And this is still true today of new manufacturing entries into the market. Today there is such a rush to get a product to market that there is often not enough attention paid to the science behind making a product that really performs."
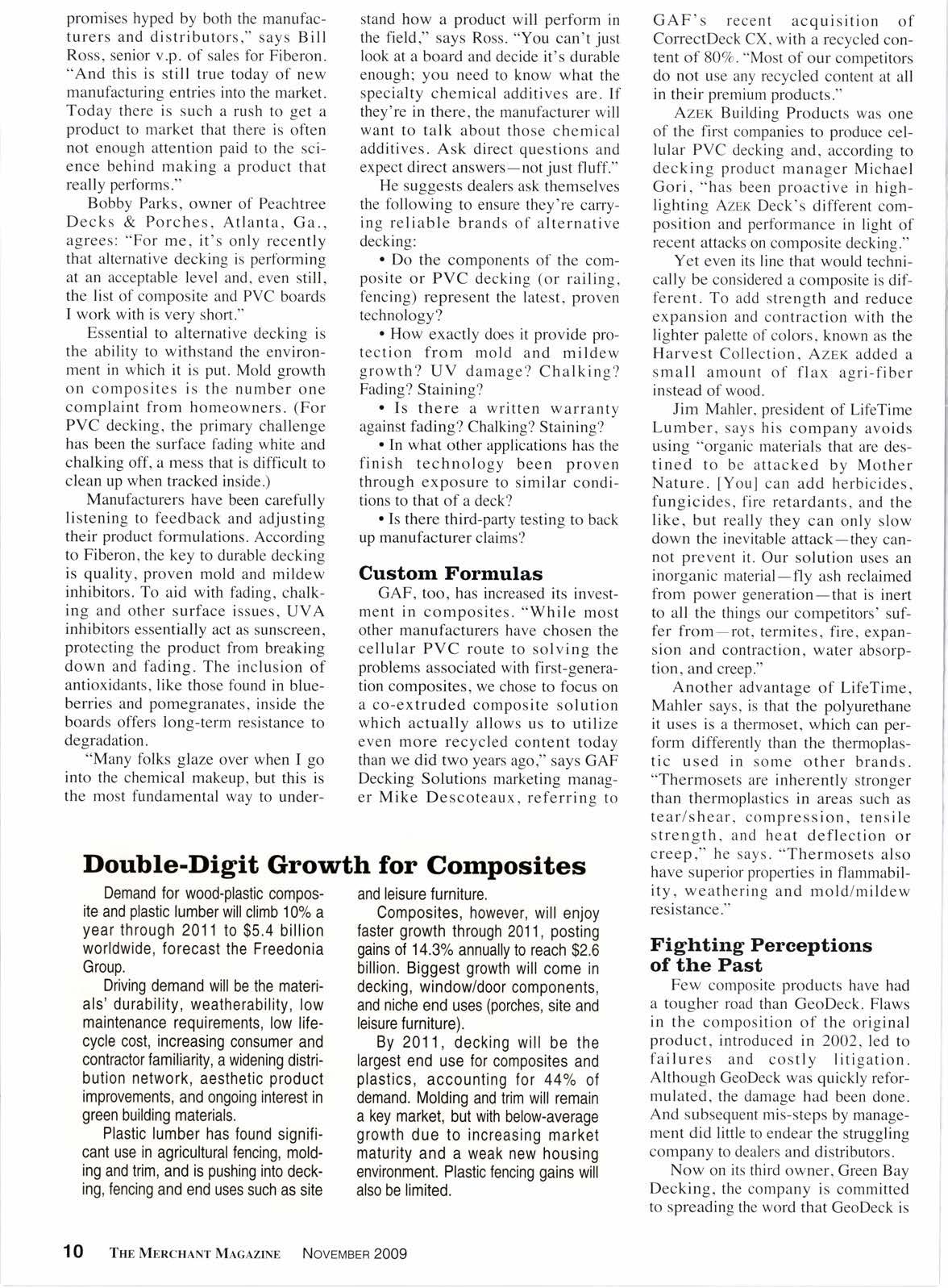
Bobby Parks, owner of Peachtree Decks & Porches, Atlanta, Ga., agrees: "For me, it's only recently that alternative decking is perfbrming at an acceptable level and, even still, the list of composite and PVC boards I work with is very short."
Essential to alternative decking is the ability to withstand the environment in which it is put. Mold growth on composites is the number one complaint from homeowners. (For PVC decking, the primary challenge has been the surface fading white and chalking off, a mess that is difficult to clean up when tracked inside.)
Manufacturers have been carefully listening to feedback and adjusting their product formulations. According to Fiberon, the key to durable decking is quality, proven mold and mildew inhibitors. To aid with fading, chalking and other surface issues, UVA inhibitors essentially act as sunscreen, protecting the product from breaking down and fading. The inclusion of antioxidants, like those found in blueberries and pomegranates, inside the boards offers long-term resistance to degradation.
"Many folks glaze over when I go into the chemical makeup, but this is the most fundamental way to under- stand how a product will perform in the field," says Ross. "You can't just look at a board and decide it's durable enough; you need to know what the specialty chemical additives are. If they're in there, the manufacturer will want to talk about those chemical additives. Ask direct questions and expect direct answers-not just fluff."
He suggests dealers ask themselves the following to ensure they're carrying reliable brands of alternative decking:
Do the components of the composite or PVC decking (or railing, fencing) represent the latest, proven technology?
How exactly does it provide protection from mold and mildew growth? UV damage? Chalking? Fading? Staining?
. Is there a written warranty against fading? Chalking? Staining?
In what other applications has the finish technology been proven through exposure to similar conditions to that of a deck?
. Is there third-party testing to back up manufacturer claims?
Custorn Formulas
GAF, too, has increased its investment in composites. "While most other manufacturers have chosen the cellular PVC route to solving the problems associated with first-generation composites, we chose to focus on a co-extruded composite solution which actually allows us to utilize even more recycled content today than we did two years ago," says GAF Decking Solutions marketing manager Mike Descoteaux, referring to
Double-Digit Growth for Composites
Demand for wood-plastic composite and plastic lumber willclimb 10o/o a year through 2011 to $5.4 billion worldwide, forecast the Freedonia Group.
Driving demand will be the materials' durability, weatherability, low maintenance requirements, low lifecycle cost, increasing consumer and contractor familiarity, a widening distribution network, aesthetic product improvements, and ongoing interest in green building materials.
Plastic lumber has found significant use in agriculturalfencing, molding and trim, and is pushing into decking, fencing and end uses such as site
GAF's recent acquisition of
CorrectDeck CX, with a recycled content of 807o. "Most of our competitors do not use any recycled conte;t at all in their premium products."
Azer Building Products was one of the first companies to produce cellular PVC decking and, according to decking product manager Michael Gori, "has been proactive in highlighting Azer Deck's different composition and performance in light of recent attacks on composite decking."
Yet even its line that would technically be considered a composite is different. To add strength and reduce expansion and contraction with the Iighter palette of colors, known as the Harvest Collection, Azsr added a small amount of flax agri-fiber instead of wood.
Jim Mahler, president of LifeTime Lumber, says his company avoids using "organic materials that are destined to be attacked by Mother Nature. [You] can add herbicides, fungicides, fire retardants, and the like, but really they can only slow down the inevitable attack-they cannot prevent it. Our solution uses an inorganic material-fly ash reclaimed from power generation-that is inert to all the things our competitors' suffer from-rot, termites, fire, expansion and contraction, water absorption, and creep."
and leisure furniture.
Composites, however, will enjoy faster growth through 2011, posting gains of 14.3olo annually to reach $2.6 billion. Biggest growth will come in decking, window/door components, and niche end uses (porches, site and leisure furniture).
By 201 1, decking will be the largest end use for composites and plastics, accounting lor 44o/o ol demand. Molding and trim will remain a key market, but with below-average growth due to increasing market maturity and a weak new housing environment. Plastic lencing gains will also be limited.
Another advantage of LifeTime, Mahler says, is that the polyurethane it uses is a thermoset, which can perform differently than the thermoplas- tic used in some other brands. "Thermosets are inherently stronger than thermoplastics in areas such as tearlshear, compression, tensile strength, and heat deflection or creep," he says. "Thermosets also have superior properties in flammability, weathering and mold/mildew resistance."
Fighting Perceptions of the Past
Few composite products have had a tougher road than GeoDeck. Flaws in the composition of the original product, introduced in 2002, led to failures and costly litigation. Although GeoDeck was quickly reformulated, the damage had been done. And subsequent mis-steps by management did little to endear the struggling company to dealers and distributors.
Now on its third owner, Green Bay Decking, the company is committed to spreading the word that GeoDeck is
"the best overall composite decking solution in the industry."
And the company has invested heavily in independent testing to back its claims. "We have always used third-party testing for our own products, but have recently expanded that to include third-party testing of all competitor products, as well," says president Lanny Jass. "We believe that is important to give customers the best information to evaluate a product's long term performance for their application. We are cunently working with multiple outside research agencies to test our boards and our competitors' boards."
A recent water absorption study, for example, showed that, because GeoDeck contained no wood residue or sawdust, it outperformed competing brands.
Absorption rates directly affect performance, since the presence of water in composites decreases their durability and mechanical properties, including performance during freezel thaw cycling, dimensional stability, and warping. In addition, the higher the water content, the higher the risk of internal decay due to microbiological activity.
Instead of
GeoDecklike McFarland Cascade's Terratec Naturalscontains rice hulls, which reportedly are naturally more resistant to internal microbial activity and water absorption than wood and wood by-products.
"The science behind our products, which has allowed GeoDeck to achieve best-in-class ratings for mechanical strength, stiffness, joist and stair tread span, density, weightper-foot, and now water absorption rates, is unmatched anywhere in the composite decking industry," says Shane O'Neill, director of research & development. "We are, however, never satisfied and will continue to invest in the innovation, quality control, and safety of the product line, as well as our next generation of composite products."
That doesn't necessarily mean there will be a flood of new products. "We are extremely careful about introducing any new products until they are fully tested and/or they are based on proven technology," Jass says. "The standard tests required for building code approval do not always show how products will perform over time in a real world environment."
He differentiates between "functional" deck boards and impressive- looking "decorative" deck boards you might see at a trade show. "How a board looks on a show deck is not necessarily how it will look after several years on a consumer's deck," Jass cautions. "Long-term issues such as mold, mildew, fading and expansion/ contraction have been evident in the industry for some time. With the newer decorative boards, there is little history on performance for scratch resistance, impact resistance, and developing 'wear patterns' in high traffic areas. For decks that will experience relatively high traffic and high use, those factors should be considered and tested over time."
He also suggests working with contractors and builders to make sure they are using the boards correctly, since many call-backs result from improper installation.
With an educated dealer and distributor network, contractors and consumers can choose composites with confidence. "At the end of the day, the customer just wants a product that will withstand the harsh effects of the outdoor environment," says GAF's Descoteaux. "I doubt that they truly care what the material is, but they do want their deck to look good and to be environmentall y friendly."
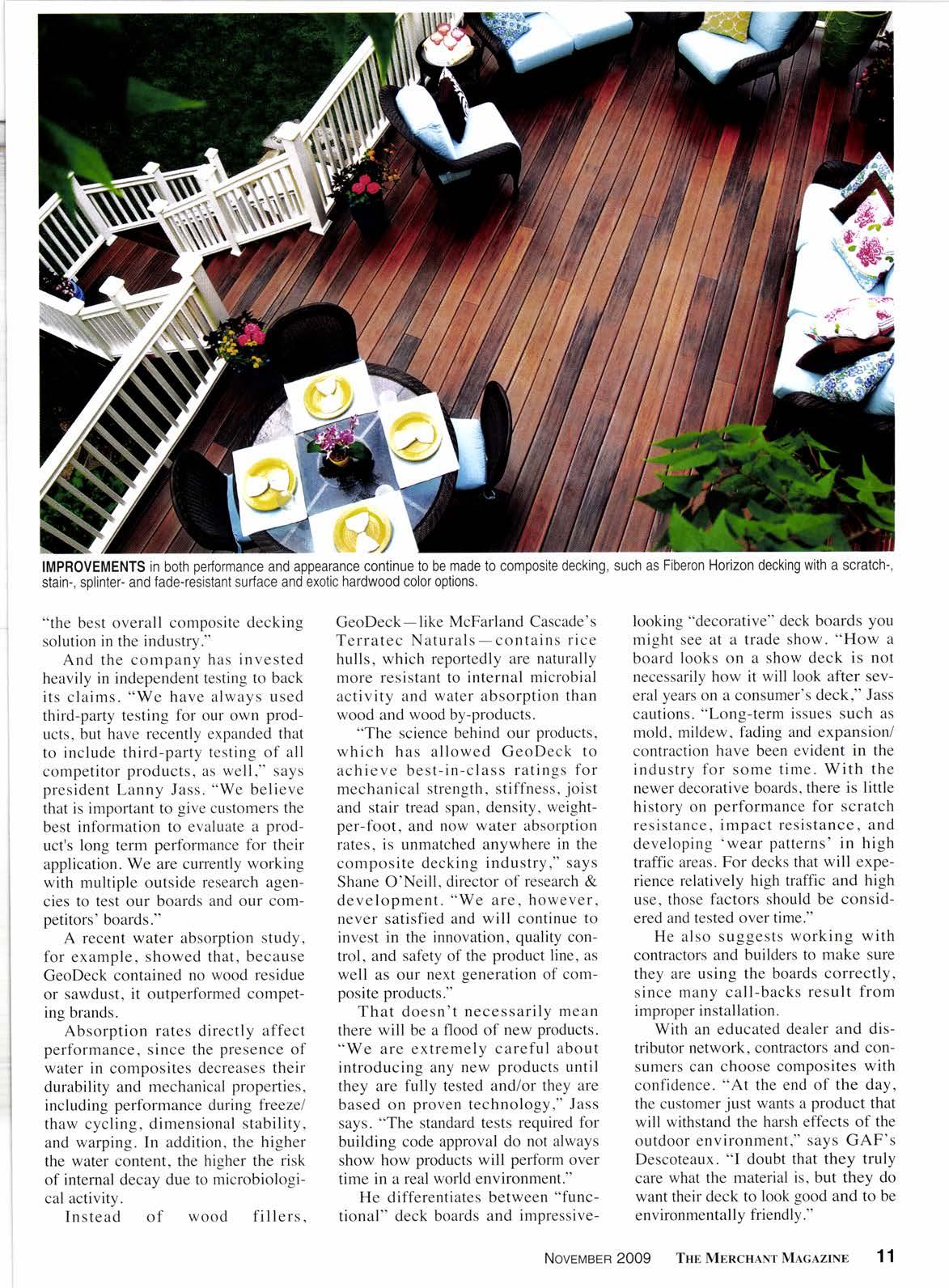