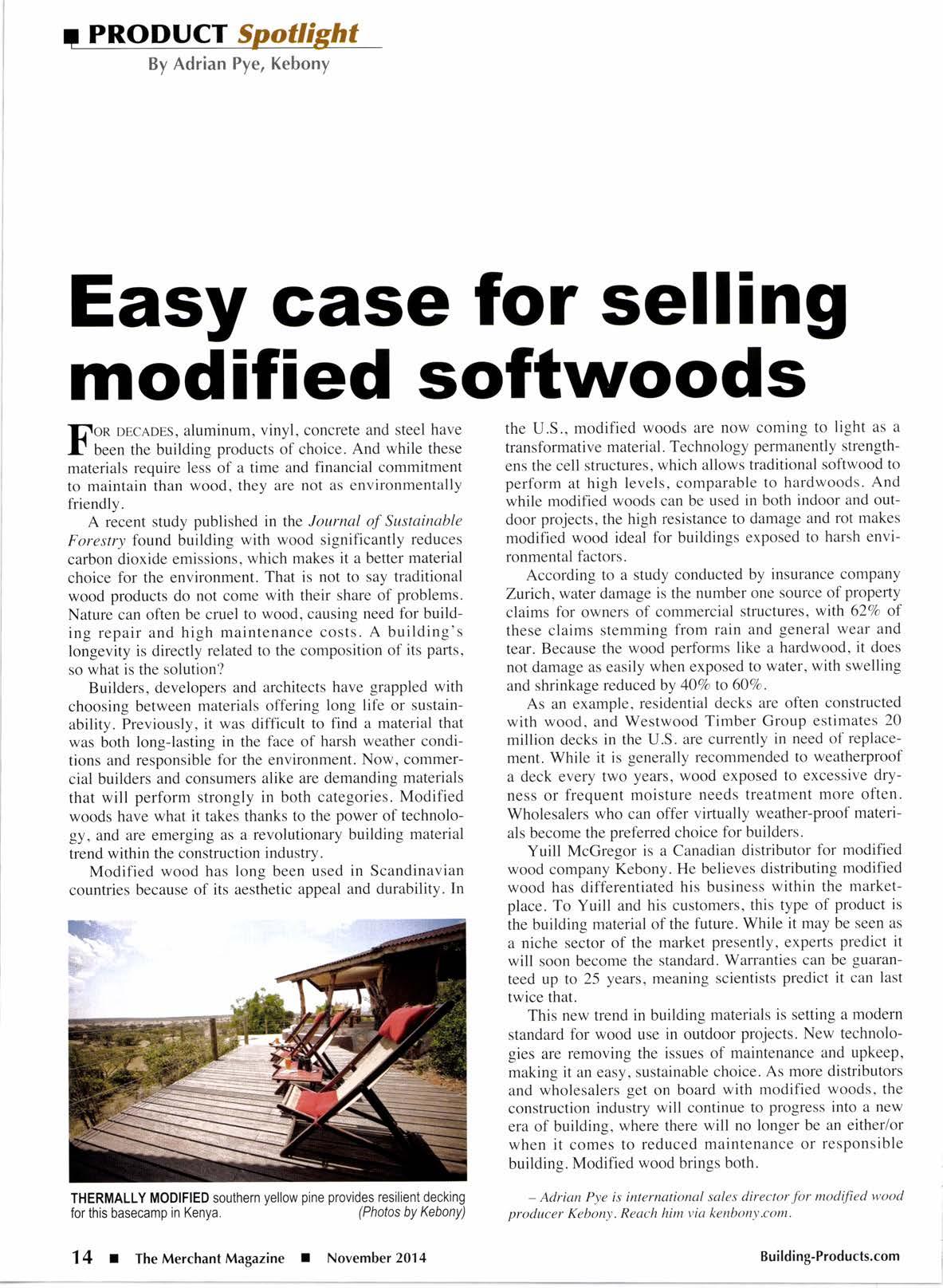
2 minute read
Easy case for selling modified softwoods
Elo* DECADES. aluminum, vinyl, concrete and steel have I-' been the building products of choice. And while these materials require less of a time and financial commitment to maintain than wood, they are not as environmentally friendly.
A recent study published in the Journal of Sustainable Forestry found building with wood significantly reduces carbon dioxide emissions, which makes it a better material choice for the environment. That is not to say traditional wood products do not come with their share of problems. Nature can often be cruel to wood, causing need for building repair and high maintenance costs. A building's longevity is directly related to the composition of its parts, so what is the solution?
Builders, developers and architects have grappled with choosing between materials offering long life or sustainability. Previously, it was difficult to find a material that was both long-lasting in the face of harsh weather conditions and responsible for the environment. Now, commercial builders and consumers alike are demanding materials that will perform strongly in both categories. Modified woods have what it takes thanks to the power of technology, and are emerging as a revolutionary building material trend within the construction industry.
Modified wood has long been used in Scandinavian countries because of its aesthetic appeal and durability. In the U.S., modified woods are now coming to light as a transformative material. Technology permanently strengthens the cell structures, which allows traditional softwood to perform at high levels, comparable to hardwoods. And while modified woods can be used in both indoor and outdoor projects, the high resistance to damage and rot makes modified wood ideal for buildings exposed to harsh environmental factors.
According to a study conducted by insurance company Zuich, water damage is the number one source of property claims for owners of commercial structures, with 627o of these claims stemming from rain and general wear and tear. Because the wood performs like a hardwood, it does not damage as easily when exposed to water, with swelling and shrinkage reduced by 407o to 6OVo.
As an example, residential decks are often constructed with wood, and Westwood Timber Group estimates 20 million decks in the U.S. are currently in need of replacement. While it is generally recommended to weatherproof a deck every two years, wood exposed to excessive dryness or frequent moisture needs treatment more often. Wholesalers who can offer virtually weather-proof materials become the preferred choice for builders.
Yuill McGregor is a Canadian distributor for modified wood company Kebony. He believes distributing modified wood has differentiated his business within the marketplace. To Yuill and his customers, this type of product is the building material of the future. While it may be seen as a niche sector of the market presently, experts predict it will soon become the standard. Warranties can be guaranteed up to 25 years, meaning scientists predict it can last twice that.
This new trend in building materials is setting a modern standard for wood use in outdoor projects. New technologies are removing the issues of maintenance and upkeep, making it an easy, sustainable choice. As more distributors and wholesalers get on board with modified woods, the construction industry will continue to progress into a new era of building, where there will no longer be an either/or when it comes to reduced maintenance or responsible building. Modified wood brings both.

By Scott