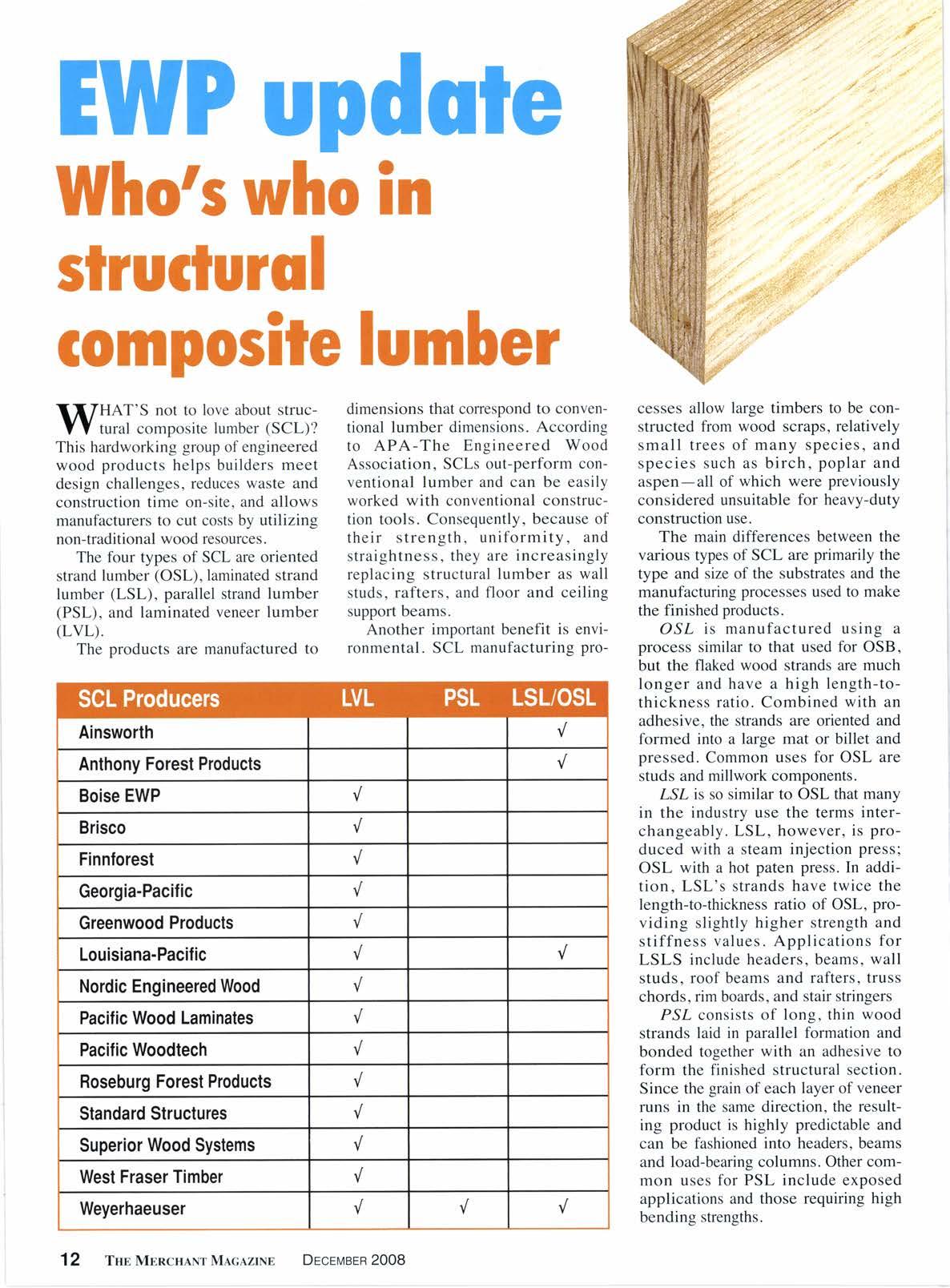
2 minute read
Who's who in slructurql composite lumber
If IHAT'S not to love about strucV Y tural composite lumber (SCLX This hardworking group of engineered wood products helps builders meet design challenges, reduces waste and construction time on-site, and allows manufacturers to cut costs by utilizing non-traditional wood resources.
The four types of SCL are oriented strand lumber (OSL), laminated strand lumber (LSL), parallel strand lumber (PSL), and laminated veneer lumber (LVL).
The products are manufactured to dimensions that correspond to conventional lumber dimensions. According to APA-The Engineered Wood Association, SCLs out-perform conventional lumber and can be easily worked with conventional construction tools. Consequently, because of their strength, uniformity, and straightness, they are increasingly replacing structural lumber as wall studs, rafters, and floor and ceiling support beams.
Another important benefit is environmental. SCL manufacturing pro- cesses allow large timbers to be constructed from wood scraps, relatively small trees of many species, and species such as birch, poplar and aspen-all of which were previously considered unsuitable for heavy-duty construction use.
The main differences between the various types of SCL are primarily the type and size of the substrates and the manufacturing processes used to make the finished products.
OSL is manufactured using a process similar to that used for OSB, but the flaked wood strands are much longer and have a high length-tothickness ratio. Combined with an adhesive, the strands are oriented and formed into a large mat or billet and pressed. Common uses for OSL are studs and millwork components.
LSZ is so similar to OSL that many in the industry use the terms interchangeably. LSL, however. is produced with a steam injection press; OSL with a hot paten press. In addition, LSL's strands have twice the length-tothickness ratio of OSL, providing slightly higher strength and stiffness values. Applications for LSLS include headers. beams. wall studs, roof beams and rafters, truss chords. rim boards, and stair stringers
PSZ consists of long, thin wood strands laid in parallel formation and bonded together with an adhesive to form the finished structural section. Since the grain of each layer of veneer runs in the same direction, the resulting product is highly predictable and can be fashioned into headers, beams and load-bearing columns. Other common uses for PSL include exposed applications and those requiring high bending strengths.
LVL,which is similar to PSL, is the most widely used of the structural composite lumber products. After thin, parallel wood veneers are bonded together in a large billet, they are sawn to desired dimensions for headers and beams, hip and valley rafters, scaffold planking, and the flange material for prefabricated wood I-joists. Compared to conventional lumber, LVL is stronger, straighter, and more uniform. It is also much less likely to warp, twist, bow, or shrink.
What's ahead for SCL? As the market keeps asking for products that conserve natural resources and as manufacturers seek to produce better products at lower prices, their importance is sure to grow.
Iollout fromthe Foll of foger?
Desoite the closure of Canada's largest EWP manufacturer, competing LVL and l-joist producers don't exoect a sudden windfall of demand to come their way.
Four years ago, Jager Building Systems' six plants produced more LVL and l-joists than anyone in the country. But a sharp downturn in residential construction led Jager to shutter two mills, reduce shifts at the rest, and finally, in September, file bankruptcy and close the remaining facilities.
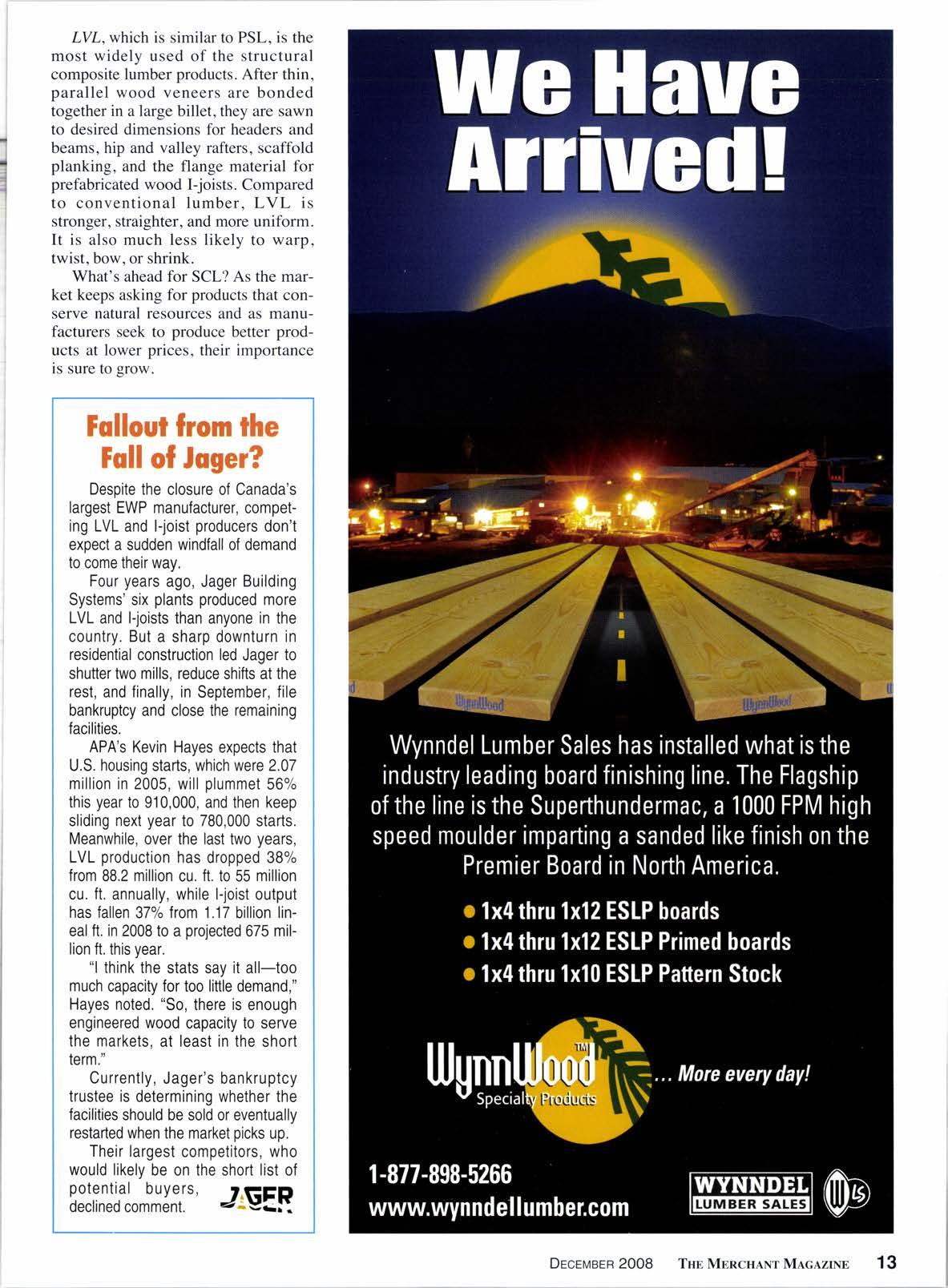
APA's Kevin Hayes expects that U.S. housing starts, which were 2.07 million in 2005, will plummet 56% this year to 910,000, and then keep sliding next year to 780,000 starts. Meanwhile, over the last two years, LVL production has dropped 38% from 88.2 million cu. ft. to 55 million cu. ft. annually, while l-joist output has fallen 37% trom 1.17 billion lineal ft. in 2008 to a projected 675 million ft. this year.
"l think the stats say it all-too much capacity for too little demand," Hayes noted. "So, there is enough engineered wood capacity to serve the markets, at least in the short term."
Currently, Jager's bankruptcy trustee is determining whether the facilities should be sold or eventually restarted when the market picks up.
Their largest competitors, who would likely be on the short list of
How independents can use down market conditions to win customers back from the big boxes
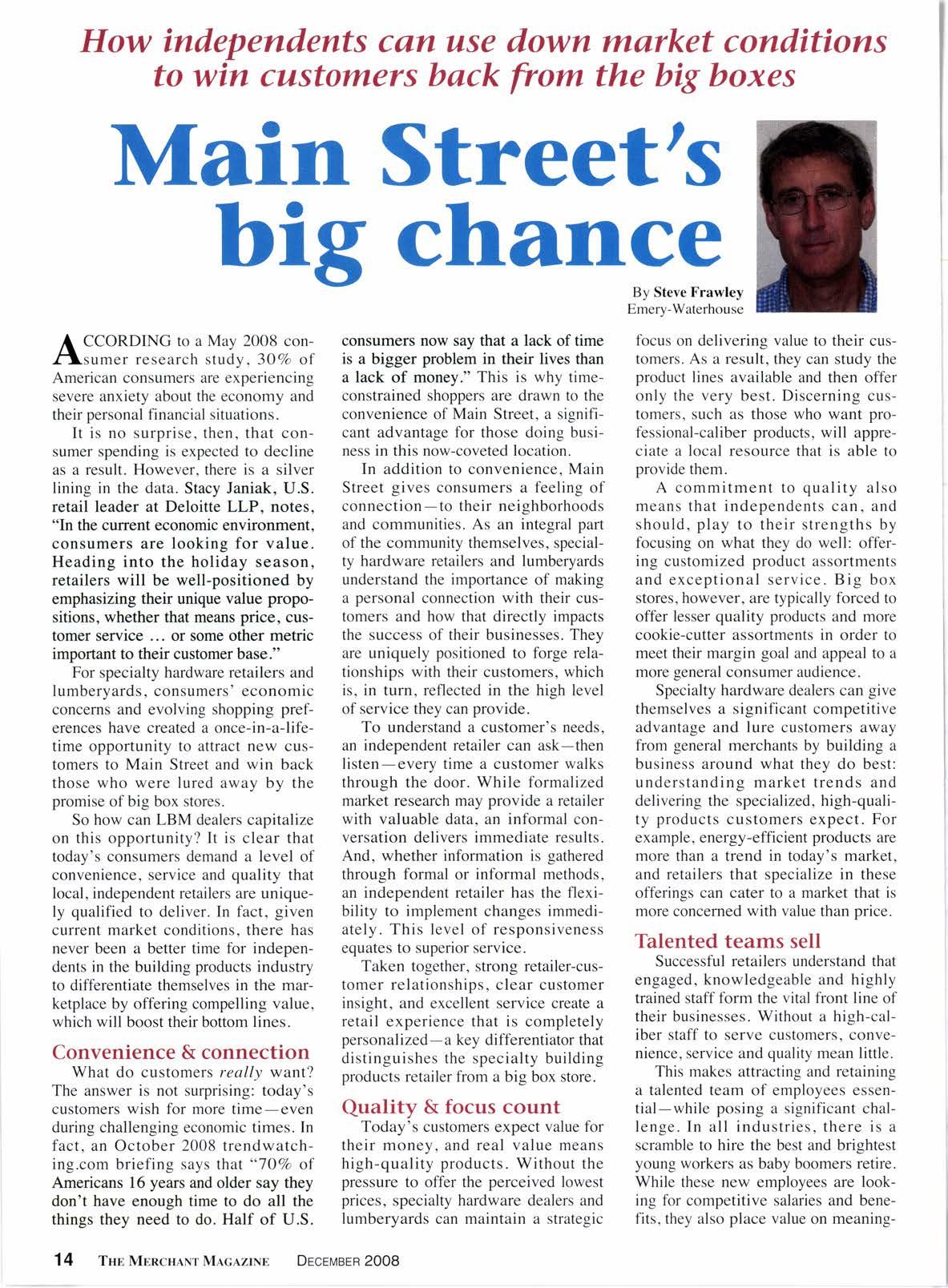