
3 minute read
How to choose the right lift truck for your business
[ron BUILDING MATERIAL dealers
I-' and wholesalers, the lift truck is an essential tool, instrumental in loading and transporting lumber, concrete, shingles, and much more. With so many different types of lift trucks available, matching the right lift truck to the application is critical. Choosing the best forklift for a business-a decision that includes many factors, such as electric versus intemal combustion, new versus used, lease versus buy, among others-will reduce costs and increase efficiencies.
All forklifts need to be replaced at some point, which leads to two key questions: When should customers consider purchasing a new lift truck, and how can they ensure they're buying the right one? The answers will vary, depending on the specific busi- ness and its utilization needs. A lumber company that runs two forklifts an hour a day will not have the same needs as a mid-size dealer with a six lift truck fleet.
The simple rule is whenever annual maintenance costs outweigh the cost of the lift truck lease-payment, it may be the right timeto consider financing or leasing a new forklift. Most lift trucks have an economic life of approximately five years or 10,000 to 12,000 miles, although as technology advances economic life continues to increase.
A business that plans to use a forklift one to two hours a day, or only intermittently, may consider buying a used model. However. a growing lumber company that anticipates constant use and requires high dependability and uptime may find that a new lift truck is a better option and costs less in the long run.
When purchasing a new lift truck, dealer support is part of the decision. Customers without an existing dealer, or those looking for a new one, should ask other regional businesses for recommendations. Always check the dealer's references against local references within the industry. The customer's relationship with the dealer should be a true partnership. A good dealer has the expertise to evaluate the customer's application and recommend a lift truck that matches their exact material handling requirements.
Even if a customer has purchased the same forkliftfor years, a material handling professional should visit the facility to see if anything has changed or if a new technology or attachment can help improve efficiency. In addition, customers should ask the dealer what sort of "value-added" programs they offer. including maintenance programs and specialized fleet management systems designed to measure truck utilization and operating costs.
After establishing a relationship with a dealer, the customer should collaborate with the dealer to choose a lift truck brand that meets the customer's needs. Thanks to significant advances in AC technology over the last decade, electric lift trucks are now more powerful, and in some cases can match the performance and capacity of internal combustion (IC) trucks. While electric forklifts have a higher initial purchase price, they produce no emissions, require less maintenance, and operate at a lower costper-hour than IC trucks. A building materials supply operation that runs primarily in a warehouse with minimal outdoor exposure may consider purchasing electric pneumatic tire lift trucks, especially if they're keen on green products.
However, for the majority of building material dealers, wholesalers, and lumber companies with operations that run outdoors, IC lift trucks with pneumatic-shaped tires are still the most efficient and capable option. These types offorklifts are ideal for lumberyards because they traverse uneven terrain with ease, can be used in inclement weather, and are available in heavier capacity ranges than electric forklifts.
IC trucks run on gasoline, diesel or liquid propane. Because other equipment on site utilizes diesel fuel, many building materials companies find it easiest to purchase a lift truck that also runs on diesel.
Customers who haven't purchased IC trucks in several years may be surprised by how intelligent they've become. Lift truck manufacturers are increasingly developing smarter lift trucks that are able to control performance, enhance safety and detect their surroundings.
Be sure to choose a lift truck brand that offers a strong warranty. A standard "entire truck" warranty may be 12 months or 2900 hours. A standard powertrain warranty may cover 24 months or 4,000 hours.
The question of whether to buy or lease will depend on the size of the business, and will be dictated by its financial constraints. There are advantages to both types of financing-customers should check with their financial consultant to determine which scenario would be best for their busiNESS.
A growing lumber or building supply company may consider leasing rather than buying because it allows the company to utilize the lift truck during its economic life, when it is most productive. A smaller operation that plans to use the lift truck for more than five years may consider financing the purchase, with intent to own the lift truck once it is paid off.
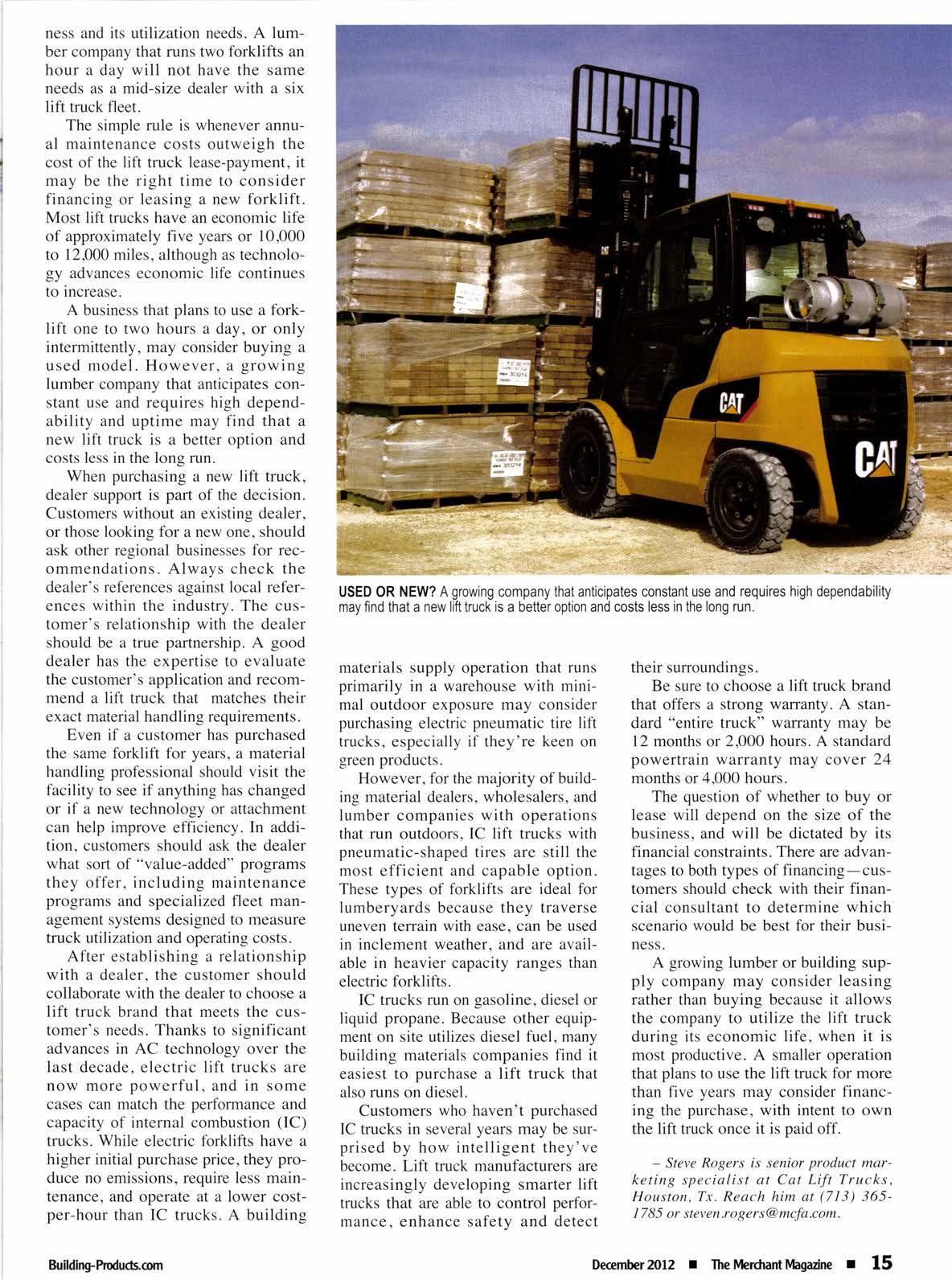
By Carla Waldemar