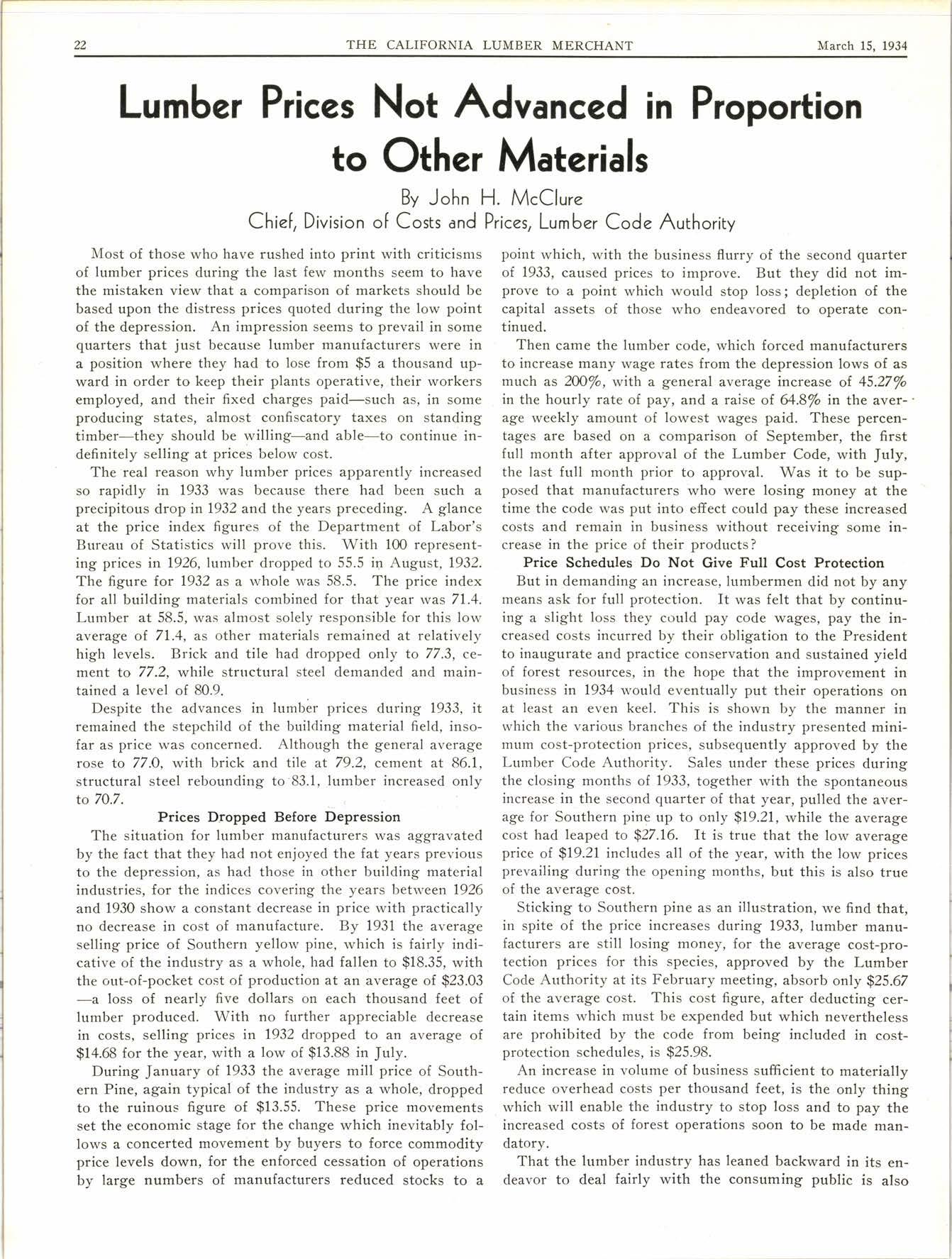
7 minute read
Lumber Prices Not Advanced in Proportion to Other Materials
By John H. McClure Chief, Division of Costs and Prices, Lumber Code Authority
Most of those who have rushed into print with criticisms of lumber prices during the last few months seem to have the mistaken view that a comparison of markets should be based upon the distress prices quoted during the low point of the depression. An impression seems to prevail in some quarters that just because lumber manufacturers were in a position where they had to lose from $5 a thousand upward in order to keep their plants operative,.their workers employed, and their fixed charges paid-such as, in some producing states, almost confiscatory taxes on standing timber-they should be willing-and able-to continue indefinitely selling at prices below cost.
The real reason why lumber prices apparently increased so rapidly in 1933 was because there had been such a precipitous drop in 1932 and, the years preceding. A glance at the price index figures of the Department of Labor's Bureau of Statistics will prove this. With 100 representing prices in 1926,lumber dropped to 55.5 in August, 1932. The figure f.or 1932 as a rvhole was 58.5. The price index for all building materials combined for that year was 71.4. Lumber at 58.5, was almost solely responsible for this low average of 71.4, as other materials remained at relatively high levels. Brick and tile had dropped only to 77.3, cement to 77.2, while structural steel demanded and maintained a level of 80.9.
Despite the advances in lumber prices during 1933, it remained the stepchild of the building material field, insofar as price was concerned. Although the general average rose to 77.O, with brick and tile at 79.2, cement at 86.1, structural steel rebounding to 83.1, lumber increased only to 7O.7.
Prices Dgopped Before Depression
The situation for lumber manufacturers was aggravated by the fact that they had not enjoyed the fat years previous to the depression, as had those in other building material industries, for the indices covering the years between 1926 and 1930 show a constant decrease in price with practically no decrease in cost of manufacture. By 1931 the average selling price of Southern yellow pine, which is fairly indicative of the industry as a whole, had fallen to $18.35, with the out-of-pocket cost of production at an average of $23.03 -a loss oI nearly five dollars on each thousand feet of lumber produced. With no further appreciable decrease in costs, selling prices in 1932 dropped to an average of $14.68 for the year, with a low of $13.88 in July.
During January of 1933 the average mill price of Southern Pine, again typical of the industry as a whole, dropped to the ruinous figure of $13.55. These price movements set the economic stage for the change which inevitably follows a concerted movement by buyers to force commodity price levels down, for the enforced cessation of operations by large numbers of manufacturers reduced stocks to a point which, with the business flurry of the second quarter of 1933, caused prices to improve. But they did not improve to a point which would stop loss; depletion of the capital assets of those who endeavored to operate continued.
Then came the lumber code, which forced manufacturers to increase many wage rates from the depression lows of as much as m%, with a general average increase of. 45.27/o in the hourly rate of pay, and a raise of. 64.8/o in the average weekly amount of lowest wages paid. These percentages are based on a comparison of September, the first full month after approval of the Lumber Code, with Juln the last full month prior to approval. Was it to be supposed that manufacturers who were losing money at the time the code was put into effect could pay these increased costs and remain in business without receiving some increase in the price of their products?
Price Schedules Do Not Give Full Cost Protection
But in demanding an increase, lumbermen did not by any means ask for full protection. It was felt that by continuing a slight loss they could pay code wages, pay the increased costs incurred by their obligation to the President to inaugurate and practice conservation and sustained yield of forest resources, in the hope that the improvement in business in 1934 would eventually put their operations on at least an even keel. This is shown by the manner in which the various branches of the industry presented minimum cost-protection prices, subsequently approved by the Lumber Code Authority. Sales under these prices during the closing months of 1933, together with the spontaneous increase in the second quarter of that year, pulled the average for Southern pine up to only $19.21, while the average cost had leaped ro $27.16. It is true that the low average price of $19.21 includes all of the year, with the low prices prevailing during the opening months, but this is also true of the average cost.
Sticking to Southern pine as an illustration, we find that, in spite of the price increases during 1933, lumber manufacturers are still losing money, for the average cost-protection prices for this species, approved by the Lumber Code Authority at its February meeting, absorb only $25.67 of the average cost. This cost figure, after deducting certain items which must be expended but which nevertheless are prohibited by the code from being included in costprotection schedules, is $25.98.
An increase in volume of business sufficient to materially reduce overhead costs per thousand feet, is the only thing which will enable the industry to stop loss and to pay the increased costs of forest operations soon to be made man. datory.
That the lumber industry has leaned backward in its endeavor to deal fairly with the consuming public is also shown by a comparison of price trends in species other than Southern pine. In spite of the increases in cost made necessary by the code, .wholesale prices of Douglas fir and hemlock have advanced only 3.9/o since code approval. Maple flooring has gone up only 9.1/o, oak flooring 4.9/o, Western pine 14.9/o, and Southern cypress an almost unnoticeable nine-tenths of L/o.
Costs of Distribution
'The foregoing applies to r,vholesale or f.o.b. mill prices. The NRA has prescribed a pricing formula for those subject to the retail lumber code under the terms of which they must add to the cost-protection price and the freight a portion of their cost of selling and administration. This varies from 18 to 25 per cent, according to the difference in these costs in various trading areas. The cost of handling and delivery, varying from $4.8O to $6.00 a thousand, according to labor zones, are then added to determine the minirnum retail selling price.
While it is a fairly well-known fact that inability to obtain proper financing has kept thousands of prospective low-cost home builders from starting construction, the claim has been made that the price of lumber has discouraged building. That this is untrue is readily shown, for the public is indeed willing and anxious to buy lumber at today's prices whenever it can find the funds to pay for it.
The New York Times' Analyst index of general business activity stood at 63.1 in January, 1933, with the figure for lumber at 40.7. Although the general figure had advanced only to 69.8 by December of that year, lumber had gone to 56.0. The fact that a desire on the part of lumber manufacturers to lose less money had not discouraged public patronage is shown in reports of new business made to the National Lumber Manufacturers Association. which serves as the statistical agency of the Lumber Code Authority. Orders received at the mills during the first week of this year, ending January 6, were greater than during any of the four preceding weeks. There was a further increase during the week ending January 13, and an increase of. 26/o over that week in the week ending January 20, followed by another slight increase in the last week of the month. A moderate recession during the first two weeks of February was offset by a marked increase in the week ending February 17, w;th a maintenance of the improved level during the week ending February 24.
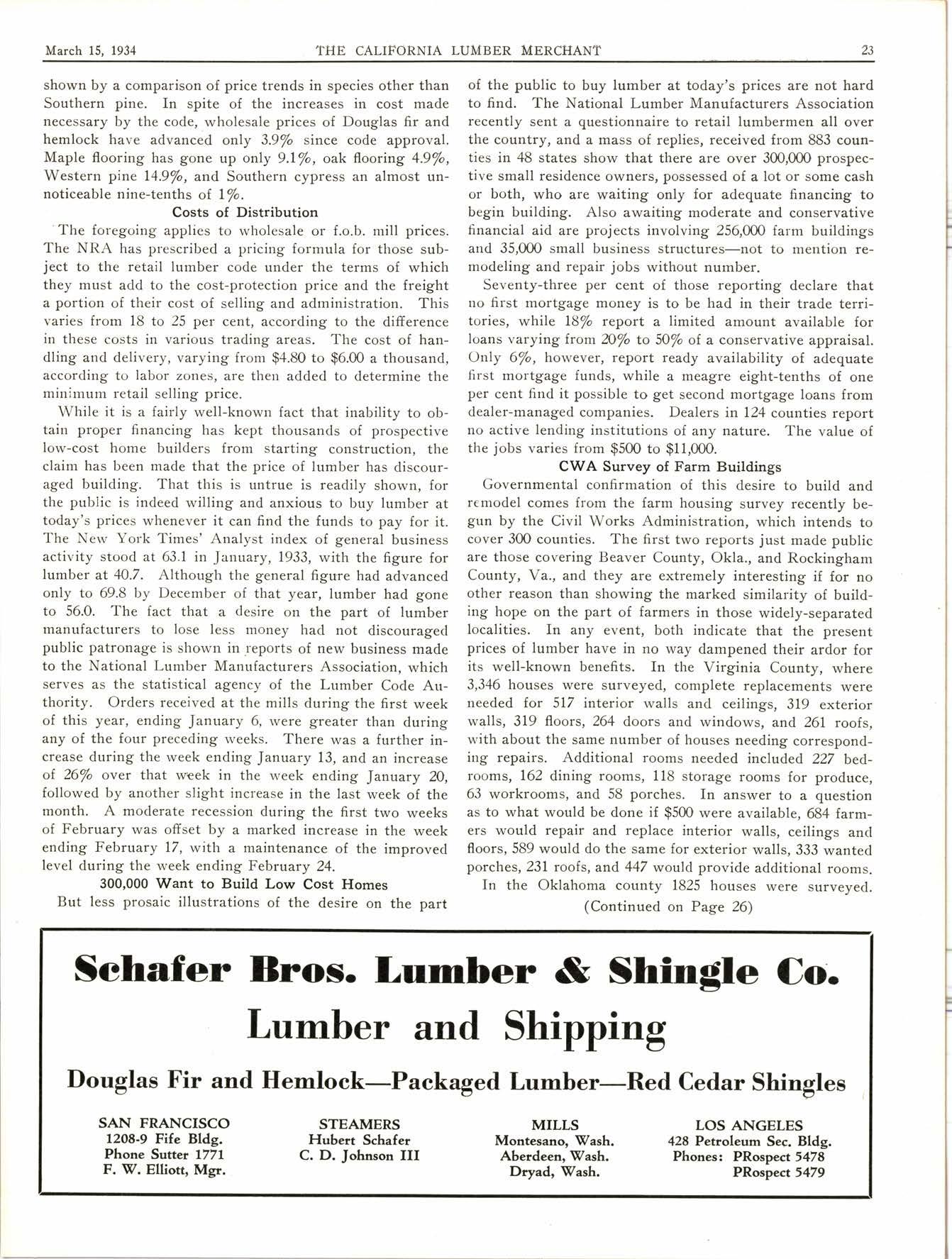
300,000 Want to Build Low Cost Homes
But less prosaic illustrations of the desire on the part of the public to buy lumber at today's prices are not hard to find. The National Lumber Manufacturers Association recently sent a questionnaire to retail lumbermen all over the country, and a mass of replies, received from 883 counties in € states show that there are over 300,000 prospective small residence owners, possessed of a lot or some cash or both, who are waiting only for adequate financing to begin building. Also awaiting moderate and conservative financial aid are projects involving 256,W farm buildings and 35,000 small business structures-not to mention remodeling and repair jobs without number.
Seventy-three per cent of those reporting declare that no first mortgage money is to be had in their trade territories, while L8/o report a limited amount available for loans varying from N/o to fi/o of a conservative appraisal. Only 6/o, however, report ready availability of adequate first mortgage funds, while a meagre eight-tenths of one per cent find it possible to get second mortgage loans from dealer-managed companies. Dealers in I24 counties report no active lending institutions of any nature. The value of the jobs varies from $50o to $11,000.
CWA Survey of Farm Buildings
Governmental confirmation of this desire to build and remodel comes from the farm housing survey recently begun by the Civil Works Administration, which intends to cover 30O counties. The first two reports just made public are those covering Beaver County, Okla., and Rockingham County, Va., and they are extremely interesting if for no other reason than showing the marked similarity of building hope on the part of farmers in those widely-separated localities. In any event, both indicate that the present prices of lumber have in no way dampened their ardor for its well-known benefits. In the Virginia County, where 3,346 houses were surveyed, complete replacements were needed f.or 517 interior walls and ceilings, 319 exterior walls, 319 floors, 264 doors and windows, and 261 roofs, with about the same number of houses needing corresponding repairs. Additional rooms needed included 227 bedrooms, 162 dining rooms, 118 storage rooms for produce, 63 workrooms, and 58 porches. In answer to a question as to what would be done if $500 were available, 684 farmers would repair and replace interior walls, ceilings and floors, 589 would do the same for exterior walls, 333 wanted porches, 231 roofs, and 447 would provide additional rooms. In the Oklahoma county 1825 houses were surveyed.
(Continued on Page 26)