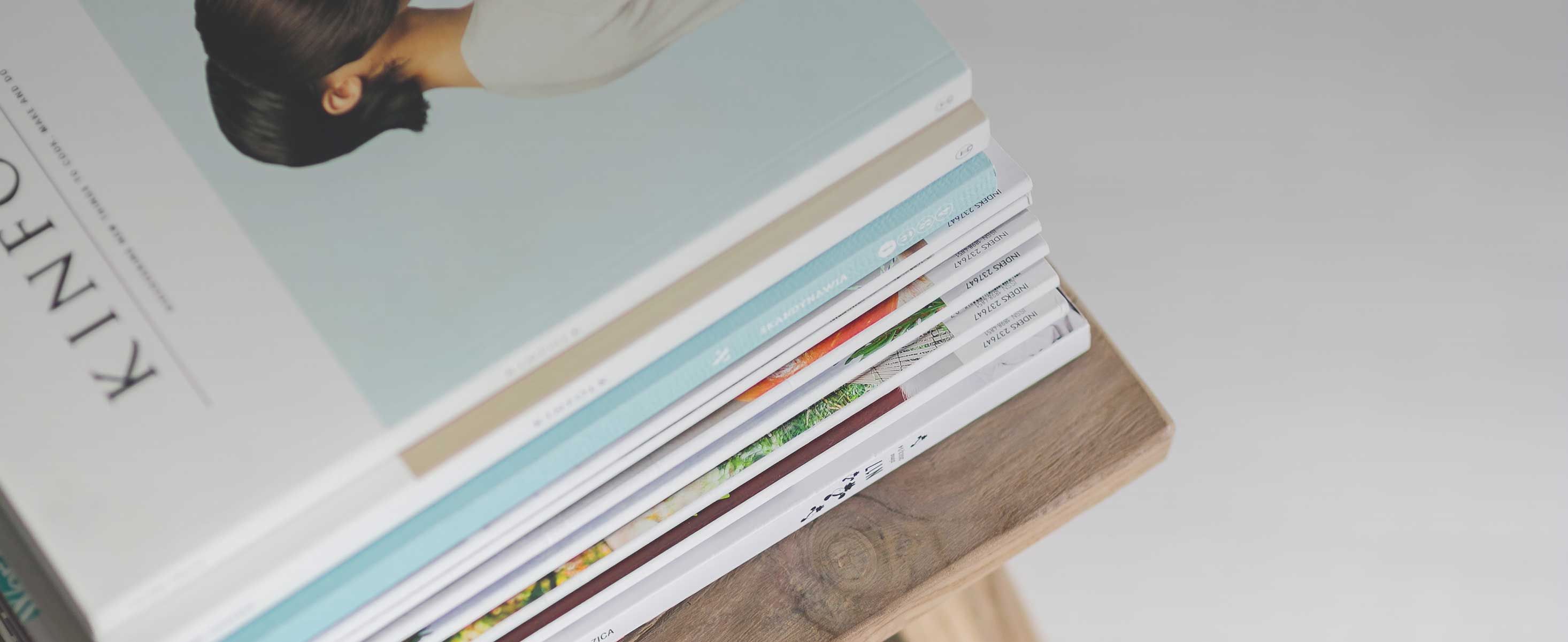
1 minute read
oo.
LOS ANGETES Phonc Klmball rtlt
He's out there with the highest individual fire-power of any soldier on earth. He rolls on more rubber and has more bacon for breakfast, man for man, than any other. And when he's hit, he reaches for his spill-proof sulfa kit with a ninety-seven percent chance that his wound will heal clean.
He depends for all of this on many people and on many things. One of them is a plain wood tank back home.
For the smokeless powder in gun-shell, torpedo, and bomb; the synthetic rubber at home that makes real rubber possible at the front; the pig that yields the bacon; the antiinfective sulfa drugs-all, and many another article of war, are processed at some stage of their manufacture in wood tanks.
Wood tank production, as a result, has quadrupled since 1940 and is still rising. For 1943, the WPB estimates that around 170,000,000 board feet of lumber will go into production of wood tanks.
In many industries, especially where corrosive chemicals are employed in processing, wood is the indispensable tank material. It resists both chemicals and heat better than metal. There is no problem of metallic contamination. There is no turbidity. Workmen cannot receive severe burns.
Oddly enough, steel itself is cleaned in wood tanks preparatory to rolling. The chemicals that clean it would at the same time corrode a steel tank.