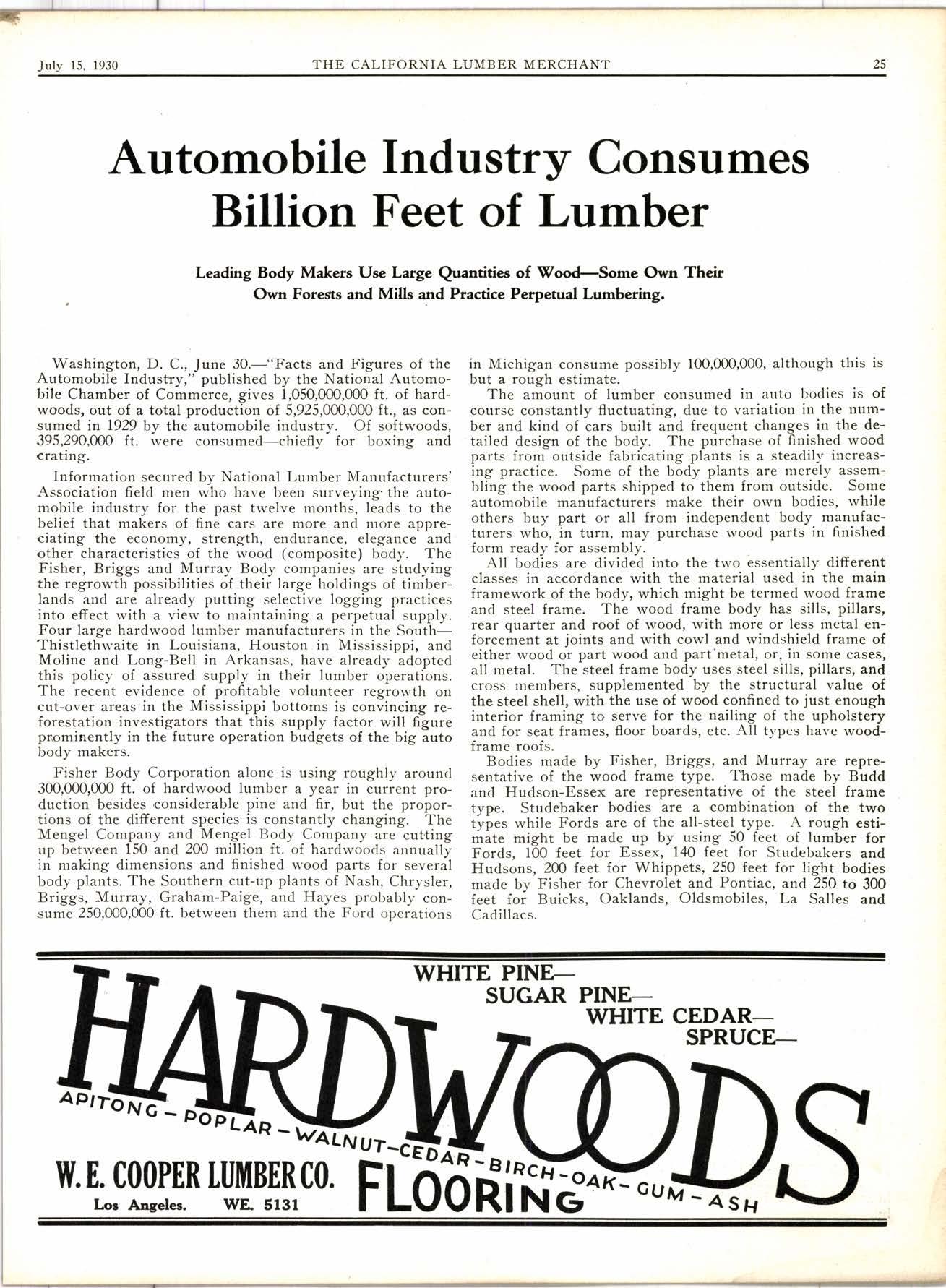
2 minute read
Automobile Industry Consumes Billion Feet of Lumber
Leading Body Makers l-fse Latge Quantities of Wood-Some Own Their Own Forests and Mi[s and Practice Petpetud Lumbering.
Washington, D. C., June 30.-"Facts and Figures of the Automobile Industry," published by the National Automobile Chamber of Commerce, gives 1,050,000,OJ0 ft. of hardwoods, out of a total production of 5,925,000O00 ft., as consumed in 1929 by the automobile industry. Of softwoods, 395,290,00O ft. were consumed-chiefly for boxing and crating.
Information secured by National Lumber Manufacturers' Association field men rvho have been surveying'the automobile industry for the past trvelve months, leads to the belief that makers of fine cars are more and more appreciating the economy, strength, endurance, elegance and other characteristics of the wood (composite) bodl'. The Fisher, Briggs and Murray Body companies are studying the regrowth possibilities of their large holdings of timberlands and are already putting selective logging practices into effect with a vierv to maintaining a perpetual supply. Four large hardwood lumber manufacturers in the SouthThistlethlvaite in Louisiana, Houston in Mississippi, and Moline and Long-Bell in Arkansas, have already adopted this policy of assured supply in their lumber operations. The re'cent evidence of profitable volunteer regrou'th on cut-over areas in the Mississippi bottoms is convincing reforestation investigators that this supply factor will figure prominently in the future operation budgets of the big auto body makers.
Fisher Body Corporation alone is using roughly around 300,000,000 ft. of hardwood lumber a year in current production besides ,considerable pine and fir, but the proportions of the different species is constantly changing. The Mengel Company and Mengel Body Company are cutting up between 150 and 200 million ft. of hardwoods annually in making dimensions and finished wood parts for severJl body plants. The Southern cut-up plants of Nash, Chrysler, Briggs, Murray, Graham-Paige, and Hayes probably consume 250,000,000 ft. between them and the Forcl operations in Michigan consume possibly 100,000,000, although this is but a rough estimate.
The amount of lumber consumed in auto b'odies is of course constantly fluctuating, due to variation in the number and kind of cars built and frequent changes in the detailed design of the body. The purchase of ffnished wood parts from outside fabricating plants is a steadill. increasing practice. Some of the body plants are merely assembling the wood parts shipped to them from outside. Some automobile manufacturers make their orvn bodies, while others buy part or all from independent body manufacturers who, in turn, may purchase wood parts in finished form ready for assembly.
All bodies are divided into the two essentially different classes in ac,cordance with the material used in the main framework of the body, which might be termed wood frame and steel frame. The wood frame body has sills, pillars, rear quarter and roof of wood, with more or less metal enforcement at joints and with cowl and windshield frame of either wood or part wood and part'metal, or, in some cases, all metal. The steel frame body uses steel sills, pillars, and cross members, supplemented by the structural value of the steel shell, with the use of wood confined to just enough interior framing to serve for the nailing of the upholstery and for seat frames, floor boards, etc. A11 types have woodframe roofs.
Bodies made by Fisher, Briggs, and Murray are representative of the wood frame type. Those made by Budd and Hudson-Essex are representative of the steel frame type. Studebaker bodies are a combination of the two types while Fords are of the all-steel type. A rough estimate might be made up by using 50 feet of lumber for Fords, 100 feet for Essex, 140 feet for Studebakers and lludsons, 200 feet for Whippets, 250 feet for light bodies made by Fisher for Chevrolet and Pontiac, and 250 to 3@ feet foi Buicks, Oaklands, Oldsmobiles, La Salles and Cadillacs.