
6 minute read
What Bunting Offers
Aerospace and Defense:
Bunting is a trusted name in aviation, military, and defense applications. Bunting is ITAR registered and DFARS compliant, making us approved to support military and defense projects. Our products have withstood the high standards of many defense related customers and programs. We have supplied magnets and magnetic assemblies on several missile programs as well as magnets and magnetic assemblies used in flight control decks for both commercial and fighter aircraft. We are equipped to meet the most stringent quality and security demands.
Our design process for military and civilian aerospace projects puts your needs first and designs a product to meet them perfectly. We consider critical design issues such as dimensional, magnetic flux, thermal, environmental, and more. We seek to design products that don’t simply “do” a job, but optimise the way that job is done. Our designs go above and beyond in order to reduce cost, reduce weight and size, and increase efficiency. We are committed to durable, lasting products that perform to the highest standard, no matter how harsh the conditions they are operating in may be.

Consumer products:
Bunting’s magnetic capabilities in consumer products are vast. These products are diverse and complex, demanding Bunting’s engineering expertise to find the optimum solution and utilising our production process to manufacture it. For over 50 years, we have developed unique solutions for thousands of customer products. Our unique capabilities, such as our injection moulding capability, allow us to produce highly unique magnets with special features that are unable to be produced by other manufacturing methods.
Bunting has served many different consumer industries in the past, and our magnetic assemblies are essential to making the modern lifestyle we all live possible. Magnets are present in your cell phone, your tablet, your computer, and other electronic devices such as speakers and cameras. Anti-theft devices at department stores utilise magnets in sensors to deter shoplifting. In the home, magnets can be found in every room as they are used in appliances such as home security systems, washing machines, refrigerators, vacuum cleaners, and blenders.
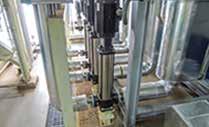
Magnetic Sensors:
Bunting offers first-hand, unmatched sensor/magnet design and industry experience in numerous industries and applications.
Magnetic sensors (sensors activated by a magnetic field) are vital devices in many applications and industry segments. Their primary function is to interact with a magnetic field and convert mechanical motion or position to an electrical signal. These sensors operate with no need for contact, no physical wear or tear, and are able to work through sealed barriers with high reliability. Within a sensor, the role of the permanent magnet is to provide a magnetic field in an air gap. This field can be constant and extremely precise, or vary in magnitude and direction.
When determining the ideal magnet for your application, our engineers help you select the best magnet first in terms of cost-efficiency, grade, and optimised geometry. Our engineering team then goes on to analyse your environmental factors including temperature and humidity; mechanical requirements such as vibration, air gap, tolerances, and electrical conductivity; and your magnetic field strength, orientation, and number of poles required by your sensing IC.
In order to meet the challenging requirements of modern sensor applications, Bunting can provide a full range of materials covering numerous product geometries, grades, and processing operations while achieving superior product quality.
Variety of certifications and compliance for critical applications
Bunting is ISO 9001:2015 certified, ITAR registered and DFARS compliant. Bunting ensures that we have restricted the use of certain hazardous substances (RoHS), namely lead, mercury, cadmium, hexavalent chromium, polybrominated biphenyls and polybrominated diphenyl ethers. Our stock magnets meet or exceed US Magnet Materials Association Standards for physical quality and magnetic properties. All permanent magnet products are RoHS compliant
ITAR-Registered
9001:2015
REGISTERED
Design Engineering Services to assist as needed:

Bunting’s experience, accumulated through decades of providing customers with unique magnetic designs, provides us with valuable insight into the changing needs and rigorous demands of our customers. As a result, our engineers are equipped with extensive knowledge to provide you with the optimum solution for your application. Our team of engineers has extensive experience in many types of magnetic designs and is able to assist in the design and execution of Finite Element Analysis models.
Our design services include:
--Complete engineering, design, magnetic evaluation, and consulting services --Magnetic field mapping --Holding force calculations --Insert and over-moulding designs --World-class design and instrumentation equipment --And more
Torque, Force, and Flux requirements:
Basic problems of permanent magnet design revolve around estimating the distribution of magnetic flux in a magnetic circuit, which may include permanent magnets, air gaps, high permeability conduction elements, and electrical currents. Exact solutions of magnetic fields require complex analysis of many factors, although approximate solutions are possible based on certain simplifying assumptions. Obtaining an optimum magnet design often involves experience and tradeoffs.
2D and 3D modeling:
Magnetic Design has become a critical feature of Bunting’s growth and we seek to work with our customers to realise their ideas. Finite Element Analysis (FEA) modeling programs are used to analyse magnetic problems in order to arrive at more exact solutions, which can then be tested and fine-tuned against a prototype of the magnetic structure. Using FEA models, flux densities, torques, and forces may be calculated. Results can be output in various forms, including plots of vector magnetic potentials, flux density maps, and flux path plots. Bunting uses a suite of 2D and 3D transient FEA modeling packages backed up with specialised design software and a team with many years of experience in magnetics as well as general engineering. This allows us to undertake a wide range of design programs across many industries including automotive, defense, medical, and more, and across many applications, including sensors and Brushless DC (BLDC) motors. The amount of design time ranges from a few hours to many days and we pride ourselves on the cost effectiveness of this service.
Diametric, Radial, Parallel, Arc, and multi-pole magnetisation experience:
The software utilised by Bunting can take full account of the true magnet properties achieved during magnetisation and predict the surface or air-gap flux density waveforms of multi-pole magnets with the actual magnetising fixture that will be used in production. This technique is not restricted to isotropic magnets and can also be applied to permanent magnet assemblies. This is an invaluable capability when it comes to moving from development to production phases within a project.
In addition, it allows us to design magnets with specialised flux density wave forms to meet specific customer requirements, whether it is for encoders, general switching magnets, or rotor magnets for permanent magnet motors. On radially magnetised parts or assemblies it is possible to skew the poles to help reduce cogging torque and for isotropic ring magnets, square waves, trapezoidal, or sinusoidal waveforms can all be achieved, sometimes to within a few percent total harmonic distortion. Increasingly, there is a demand for very complex multi-pole, multi-track systems that require a very careful choice of materials to ensure requirements are met.
Turn-key production line magnetisation system design and development:
Bunting offers customers turnkey solutions for magnetic assemblies, each designed and built around our core magnets. With all of our projects – from a two-piece assembly to a complex product that demands precision design – Bunting strives to meet your exact requirements and complete projects that will reduce cost drivers and develop a repeatable manufacturing process. Plus, we can work with you on your lean manufacturing replenishment program (JIT, Kanban, Dock-to-Stock, etc.) to ensure your parts are always available when you need them.
Bunting can design the assembly, source the magnetic material, integrate the manufacture of the magnet and assembly, coat it, glue it, magnetise it, package it and ship it, all on time and within budget. Our interdisciplinary capabilities make Bunting the ideal choice for the design, engineering, prototyping and manufacturing of magnetic assemblies.
