
12 minute read
SMALL BUSINESS OF THE YEAR
PACIFIC MARINE YACHT SYSTEMS
Shawn Clarke and Jason Reid
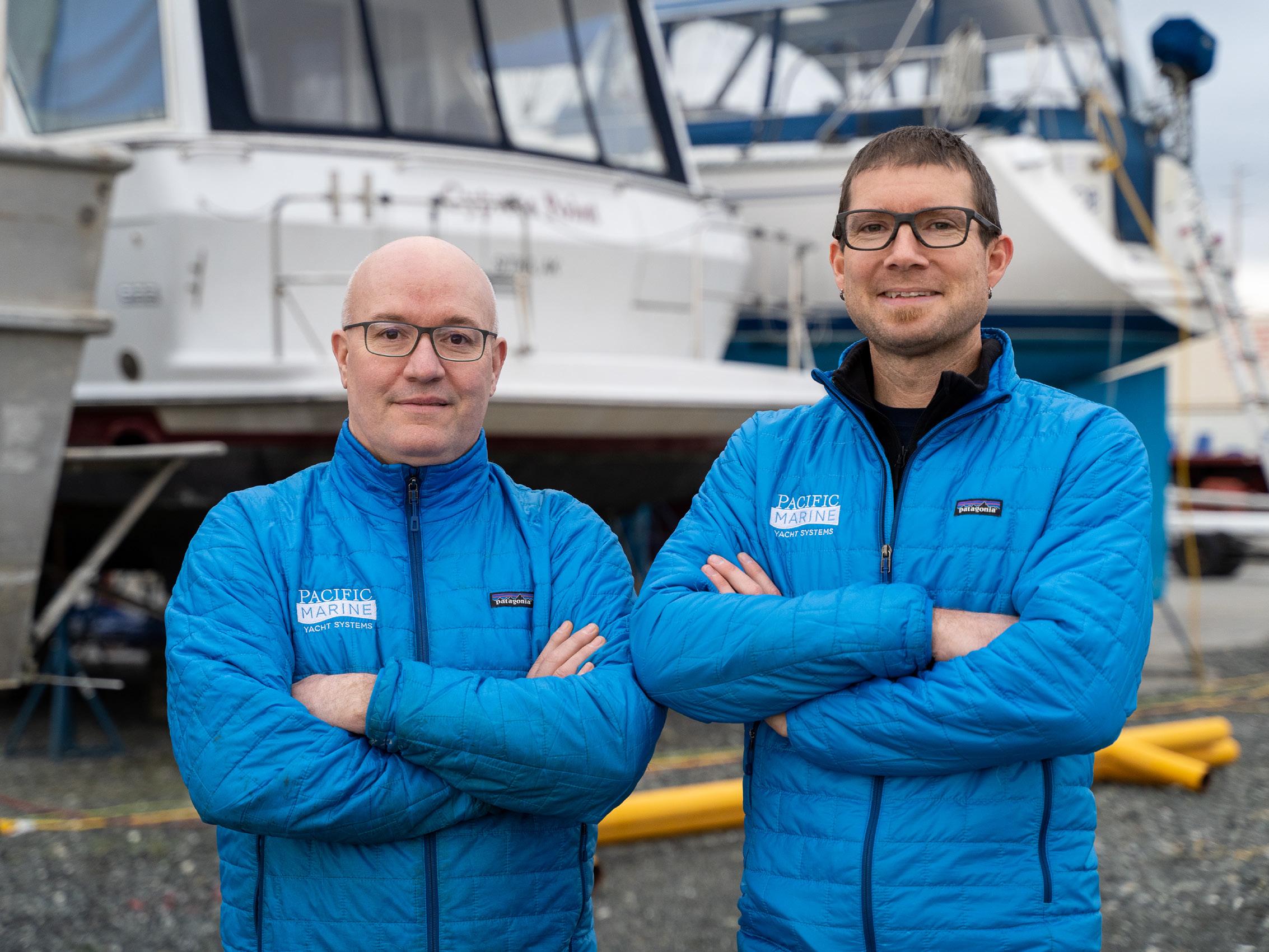
PHOTO: Sattva Photo
Navigating strong growth
Pacific Marine Yacht Systems helps seafarers stay safe, comfortable
Mary Louise Van Dyke
Courtesy photo
Pacific Marine Yacht Systems is successfully navigating the pandemic with partners Shawn Clarke and Jason Reid at the helm.
The Bellingham-based company saw an increase in revenues from $600,000 in 2020 to about $800,000 in 2021; Clarke and Reid anticipate that growth to continue through 2022.
Clarke launched the business, then known as Pacific Marine Electric, in 2011.
“I moved here from Alaska and wanted to start a new business in the marine industry,” he said.
At that time, his electrical skills were his biggest asset.
“I had no idea how to start a business or run a business,” Clarke said.
Reid formally came on board in 2013 after working for Clarke occasionally on an as-needed basis. The partnership allowed them to round out their services with Reid’s skillsets in marine electronic and heating systems.
Six months later, the partners brought on their first intern and hired their first employees as demand for their services swelled. At one point, they had five employees.
Today, the company employs two full-time and one part-time staff members, all hailing from Whatcom County. Among the company’s current jobs are lithium battery system installation, sailboat upgrades and
many calls for heating systems.
During the pandemic, a lot of families, individuals and couples hung out on their boats as an escape, Reid said. Having an onboard heating system allowed boaters to experience longer, more comfortable stays. Children could attend school remotely, providing the vessel was equipped to receive a cell signal.
The company’s services include the sale and installation of lithium batteries, electronics (such as auto pilot and chart plotters), cabinetry, cranes and watermakers.
Watermakers, Reid said, are systems that allow seafarers to make sea water drinkable through desalination or reverse osmosis processes. Clients who make the long voyage to Hawaii or Australia or who venture a few hundred miles offshore utilize these systems to ensure they have enough drinking water while at sea.
Pacific Marine Yacht Systems works with commercial fishing boats and handles the electrical wiring on new craft. The company also preps boats for cruising offshore, making sure all communications, electronics and other systems are working correctly or are replaced or upgraded as needed.
The partners changed the company brand to Pacific Marine Yacht Systems a few years ago when they discovered that many customers didn’t know the company offered other marine services, Clarke said.
The change helped shore up the business, with the main source of new customers now being word-of-mouth from satisfied customers.
Pacific Marine’s customer base includes boat owners from Whatcom County and the greater Puget Sound area. The Port of Bellingham gives out-of-the-area customers — someone from Anacortes, for example — three days of free mooring while the company is servicing the craft.
Looking to the horizon, the partners want to chart a course that allows a good balance between work and home life. Goals include keeping Pacific Marine on course with structured, carefully paced growth, communicating well with customers, and offering good, living wages to experienced crewmembers. ■
BELLINGHAM’S PREMIER GOLF DESTINATION
46th Annual Bellingham Amateur Championship - Sept 4-5 ‘21 2021 & 2019 US Senior Open Qualifer host site 2019 Washington State Women’s Amateur host site
FRONT 9

SUDDEN VALLEY GOLF COURSE
855.506.2219 | www.suddenvalleygolfcourse.com Nestled on the shores of Lake Whatcom is Bellingham’s only golf course community. Enjoy our semi-private 18-hole Ted Robinson designed course for the day or as a member.
Call to inquire about the best membership value in the region or hosting your next golf outing.
BOOK ONLINE TODAY!
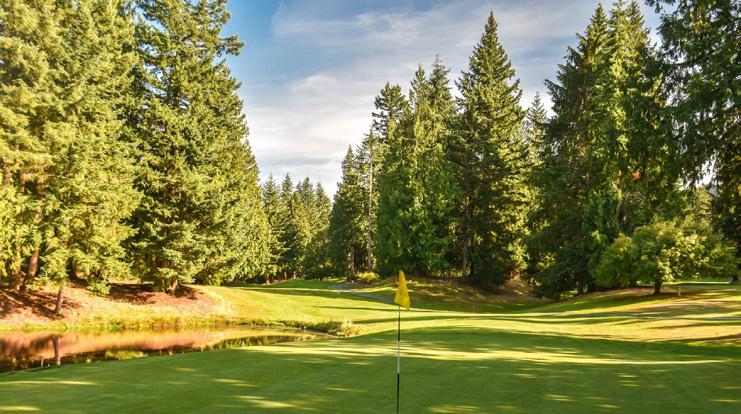

HOLE 6 HOLE 13 HOLE 18
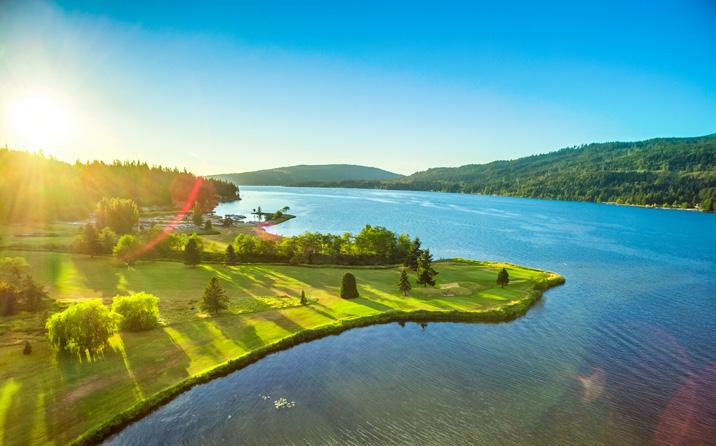
SMITH MECHANICAL
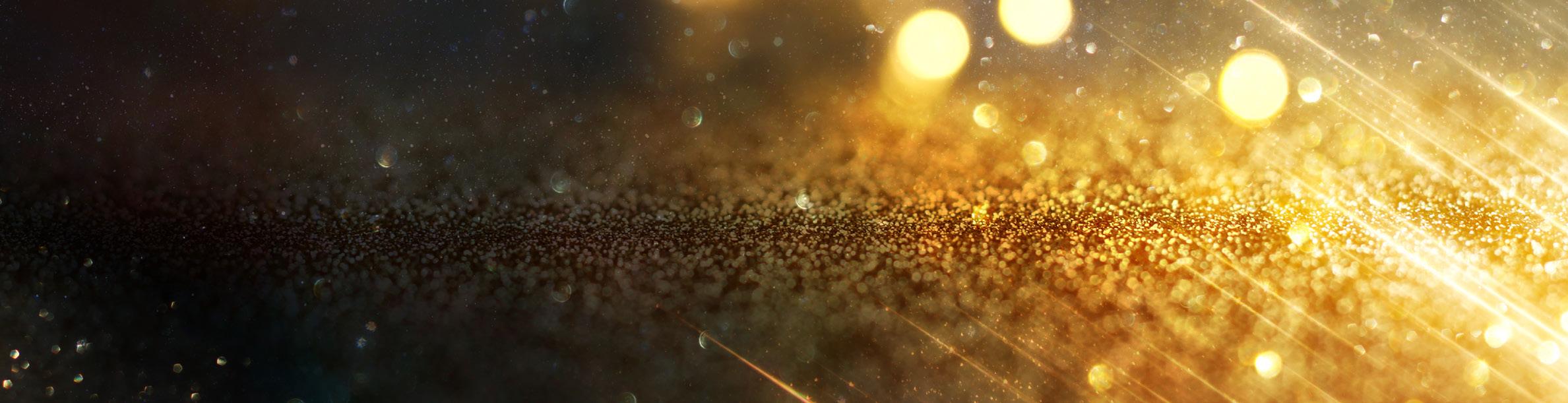
Jared and Shelly Murphy
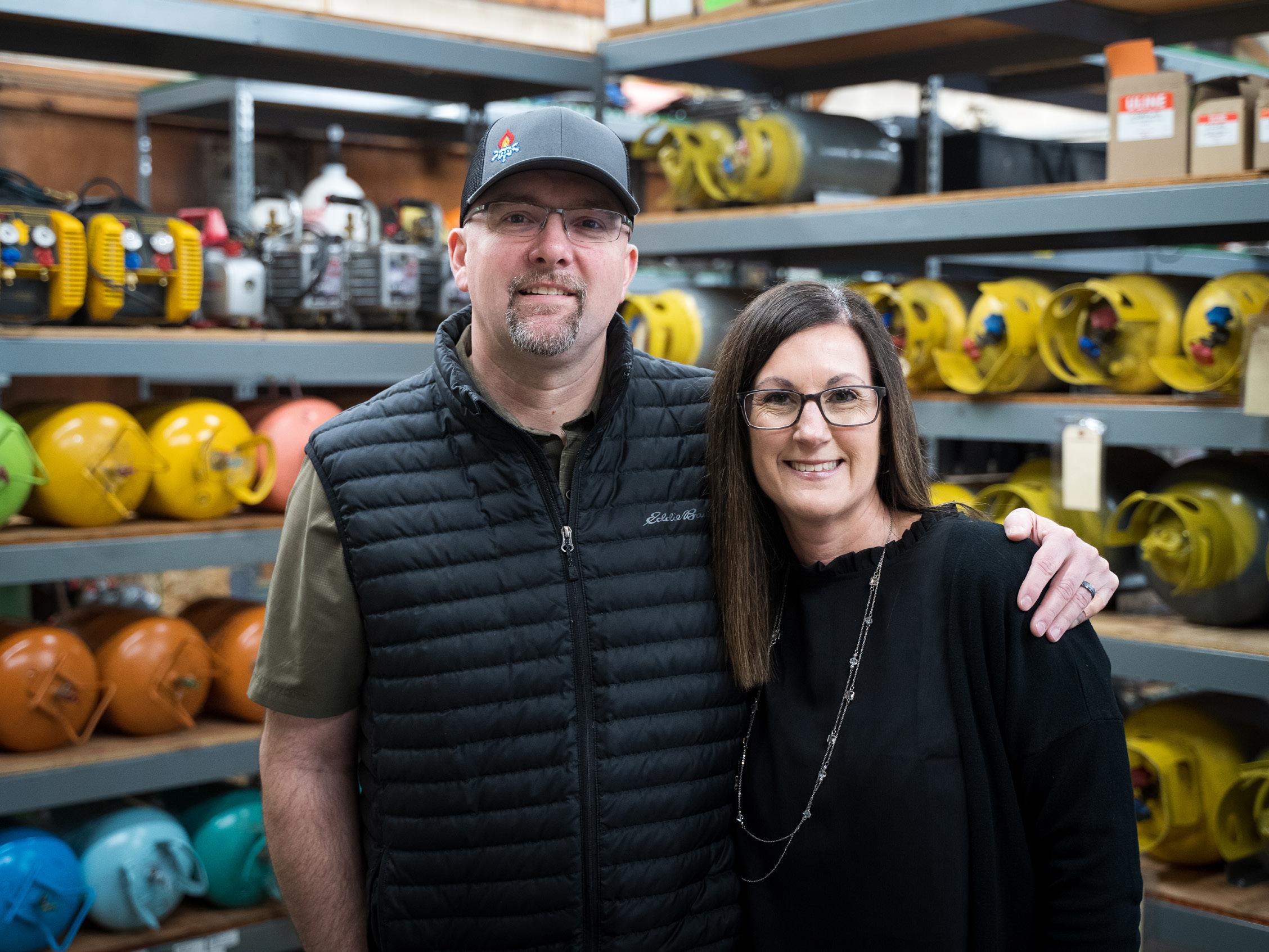
PHOTO: Sattva Photo
Treating people well
Smith Mechanical succeeds by putting others first
Mary Louise Van Dyke
Jared and Shelly Murphy, owners of Smith Mechanical Inc., are looking forward to a bright 2022.
Their goals are to continue looking for ways to improve their processes, help customers and aid employees in their professional growth. The company earned $4 million in 2020 and experienced some growth in 2021.
“Our philosophy is to treat people well, treat employees well, treat customers well,” said Jared Murphy, the company president. “Our faith plays a big part in what we do.”
The Ferndale-based company dates to 1990, when it was started by Steve and Colleen Smith. Jared worked there while still in high school, before he attended Bellingham Technical College for the HVAC/R service technician course and worked for another company. He returned to Smith Mechanical in 2006 to help manage the business. In 2010, Steve Smith announced his intent to retire, which sparked the Murphys’ decision to purchase the company and keep it a locally owned, locally operated business.
“It was, I think, a fairly smooth transition, knowing how transitions can go,” Jared Murphy said.
The business has grown by about 50-60% since they took over in 2010,
he said.
The company employs 25 full-time staff and services an area that includes Whatcom and Skagit counties as well as locations in north Snohomish, San Juan and Island counties. Most of the employees reside in Whatcom County.
Shelly Murphy’s job is in accounting. Jared Murphy, who focuses on management, doesn’t do much on the project side these days.
Smith Mechanical is an HVAC (heating, ventilating and air conditioning) contractor in both the residential and commercial markets. Its system design and services cover a variety of needs, including boilers, furnaces, heat pumps, ductless systems, commercial refrigeration sales and service, water heaters and air conditioning units.
On the heating side, Smith Mechanical’s professionals design, install, service and maintain all sorts of systems, from the more traditional to the newest green energy furnaces that offer efficiency ratings of up to 95%.
One of the company’s recent special projects involved a geothermal system that uses the earth as a source for heating a 20,000-square-foot facility. Other ventures have focused on designing HVAC systems for office buildings and refrigeration for grocery and convenience stores (such as the Community Food Co-op in the Cordata neighborhood), restaurants and other commercial properties. Currently, the company is working on a highend heating system for a five-story building in Skagit County, Jared Murphy said.
Occasionally, the company helps organizations with other needs, such as cleaning up from the recent flood.
Smith Mechanical doesn’t focus heavily on marketing through the web or social media, Jared Murphy said. Most of its customers come through word-of-mouth.
Being successful doesn’t just involve working on big projects, important as they are, Jared Murphy said. More important is “having good relationships with our customers and employers, being good stewards of what God has blessed us with.” ■
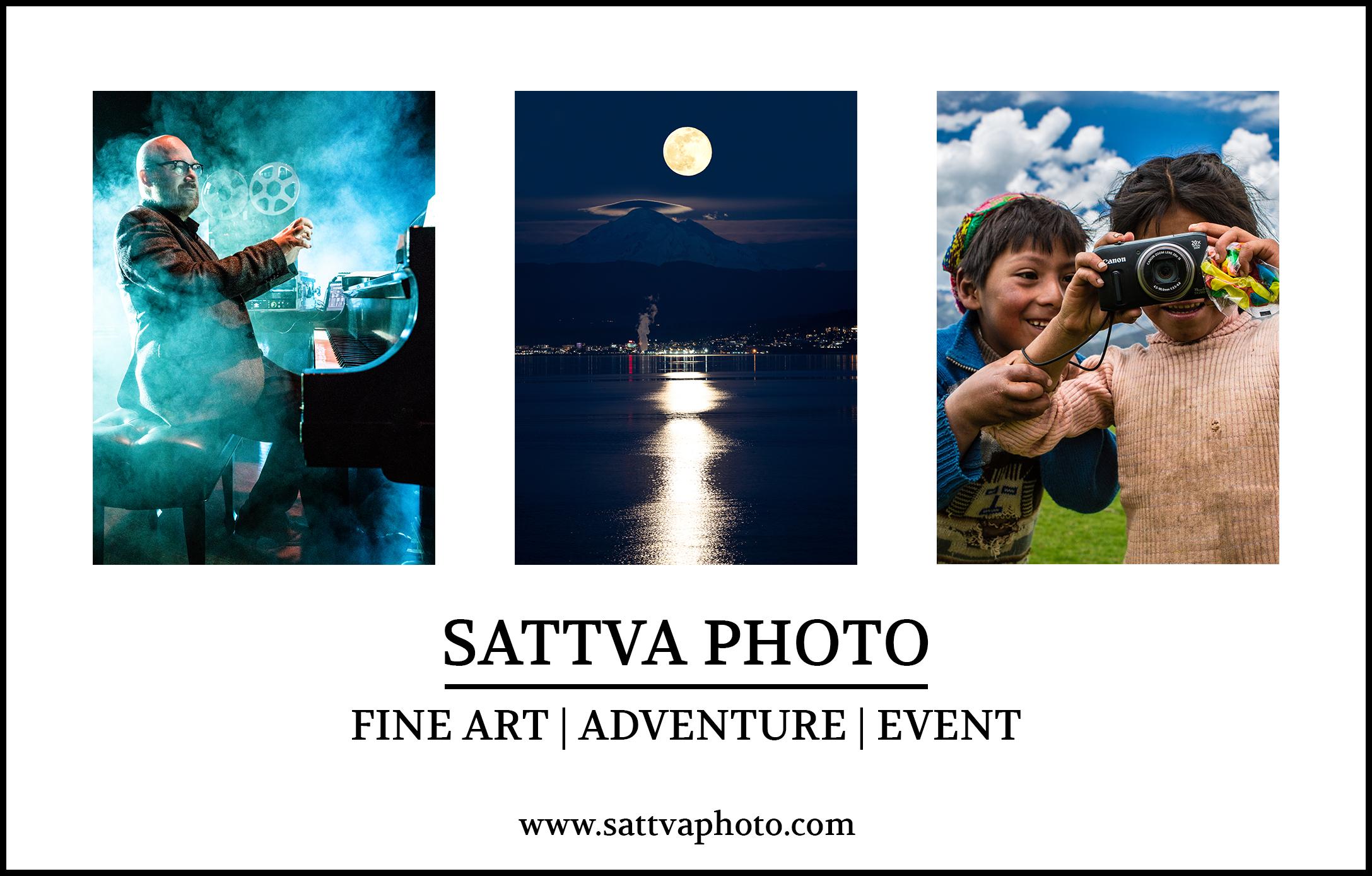
DRAYTON HARBOR OYSTER COMPANY

Stephen Seymour and Mark Seymour

PHOTO: Sattva Photo
Tumbling with the tide
Weathering challenges to produce mouth-watering oysters
Mary Louise Van Dyke
Drayton Harbor Oyster Company is recognized for getting its spectacshell-er products from tide to tables in a timely fashion.
Raising oysters through water quality issues, floods, snow and COVID-19 challenges “has been a journey,” said Stephen Seymour, who shares ownership of the company with his son, Mark Seymour.
A retired fish biologist, Stephen Seymour said the Blaine-based business has grown from a three-person oyster bar to employing up to 18 people at the restaurant and four or five at the oyster farm. With gratuities, staff make a living wage. Staffing issues sometimes occur during the warmer months, with staff moving back and forth between duties at the restaurant and farm.
Stephen Seymour and partners began oyster farming at Drayton Harbor in 1985. Water quality issues forced him to step away in the 1990s, when he went to work for the Washington State Department of Fish and Wildlife.
He credits his then partner Geoff Menzies with keeping the farm operating as a nonprofit, community-supported aquaculture organization while working with government officials to
resolve water quality issues.
“Ultimately Geoff’s the hero,” Stephen Seymour said. “He is the reason we’re still farming oysters in Drayton Harbor.”
In 2013, Stephen Seymour retired from his fisheries job and took over operations, with his son joining him. “We decided to grab the (brass) ring and see if we could make the farm work,” he said.
Oysters are grown and harvested on the farm using a process that utilizes mesh bags that enable oysters to develop a deeper curved bowl through tumbling with the tide.
“There’s nothing like putting oyster seed out there,” Stephen said. “You can barely see them, and you come back a year and half later and there’s just a carpet of them.”
Regular environmental quality checks are done to ensure customers are eating healthy oysters.
Both the November flood and frigid, snowy conditions in late December and early January hampered the harvest. Dicey weather can keep harvesters out of the water (and the oysters in the water), Stephen Seymour said.
Father and son opened a small oyster bar in downtown Blaine in 2015 and expanded to a new building at 685 Peace Portal Way, constructed by developer Peter Gigante. The restaurant features wide-board flooring and ornate tin ceilings salvaged from the original building on that site. It also has a full kitchen.
The tide-tumbled oysters are sold raw to customers to take home and prepare. They also are offered raw or grilled at the restaurant, with options such as wine and beer (think Dark Harbor Oyster Stout, crafted by Atwood Ales of Blaine), Drayton Tacos and po’boys (with choice of oysters, cod or shrimp) and oyster stew, Stephen Seymour said.
Border closures during the pandemic took a toll on company earnings.
“Profit-wise, it’s been nip and tuck,” he said. “Half our business was from Canada when the border was open.”
However, diners are flocking to the restaurant in growing numbers to enjoy a shellfish outing. The company expanded its domed outdoor seating area on the plaza.
“I’m overwhelmed about how this small business supports so many other small businesses,” Stephen said. “It’s true how small business are so much a part of the economy.” ■
— Stephen Seymour, co-owner of Drayton Harbor Oyster Company
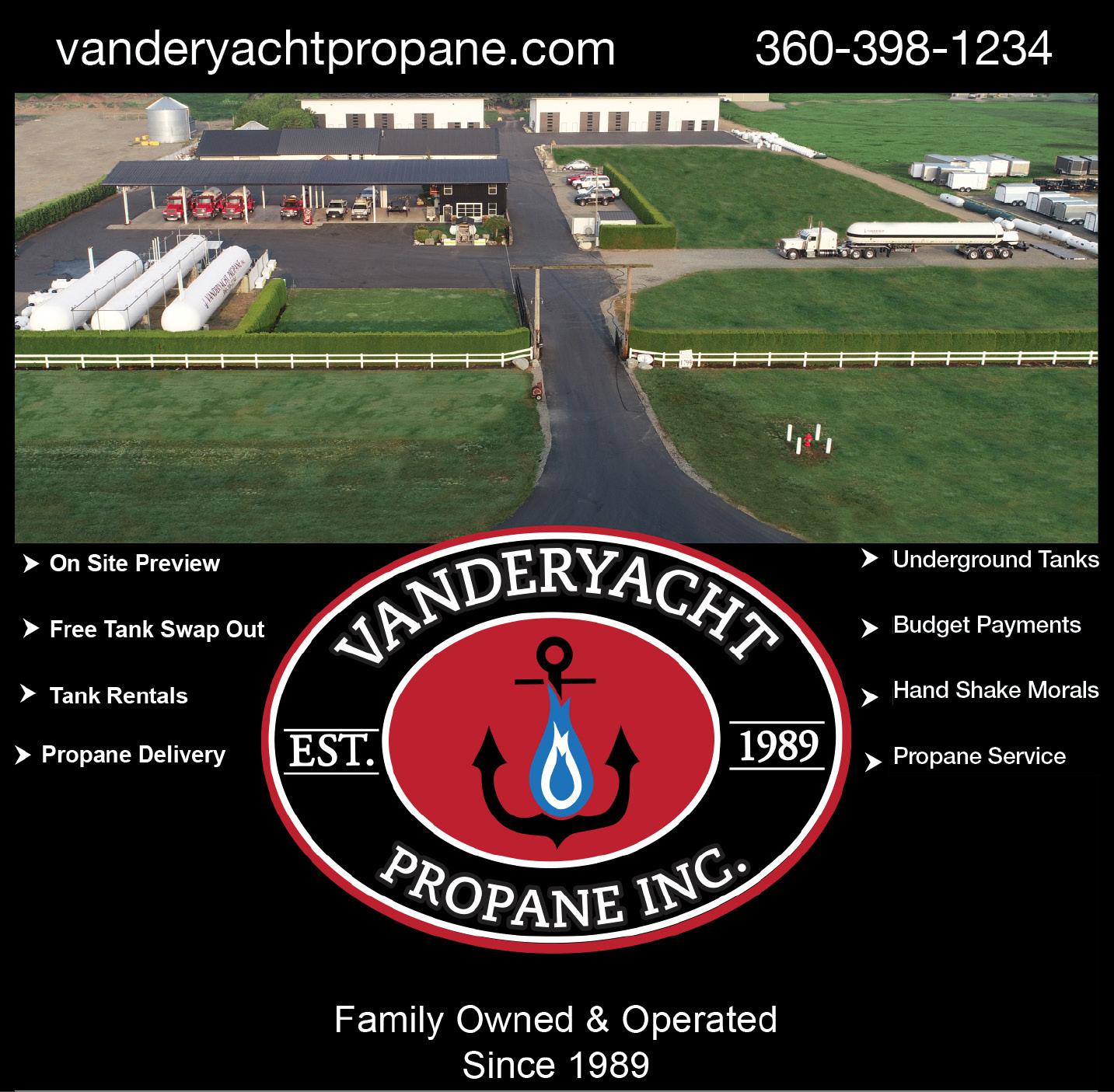
VAN BEEK DRYWALL
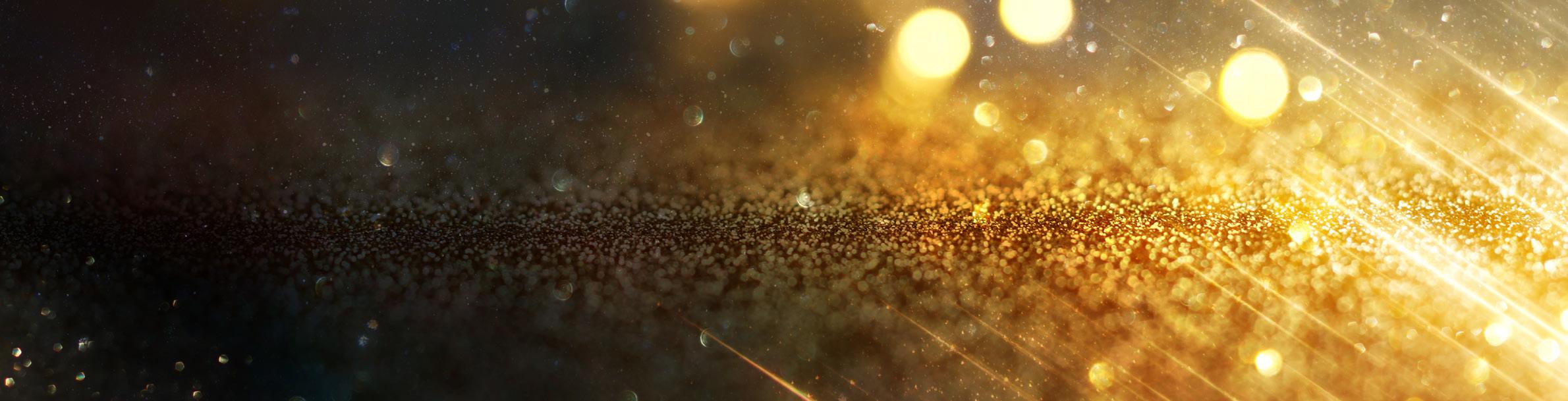
Doug Van Beek
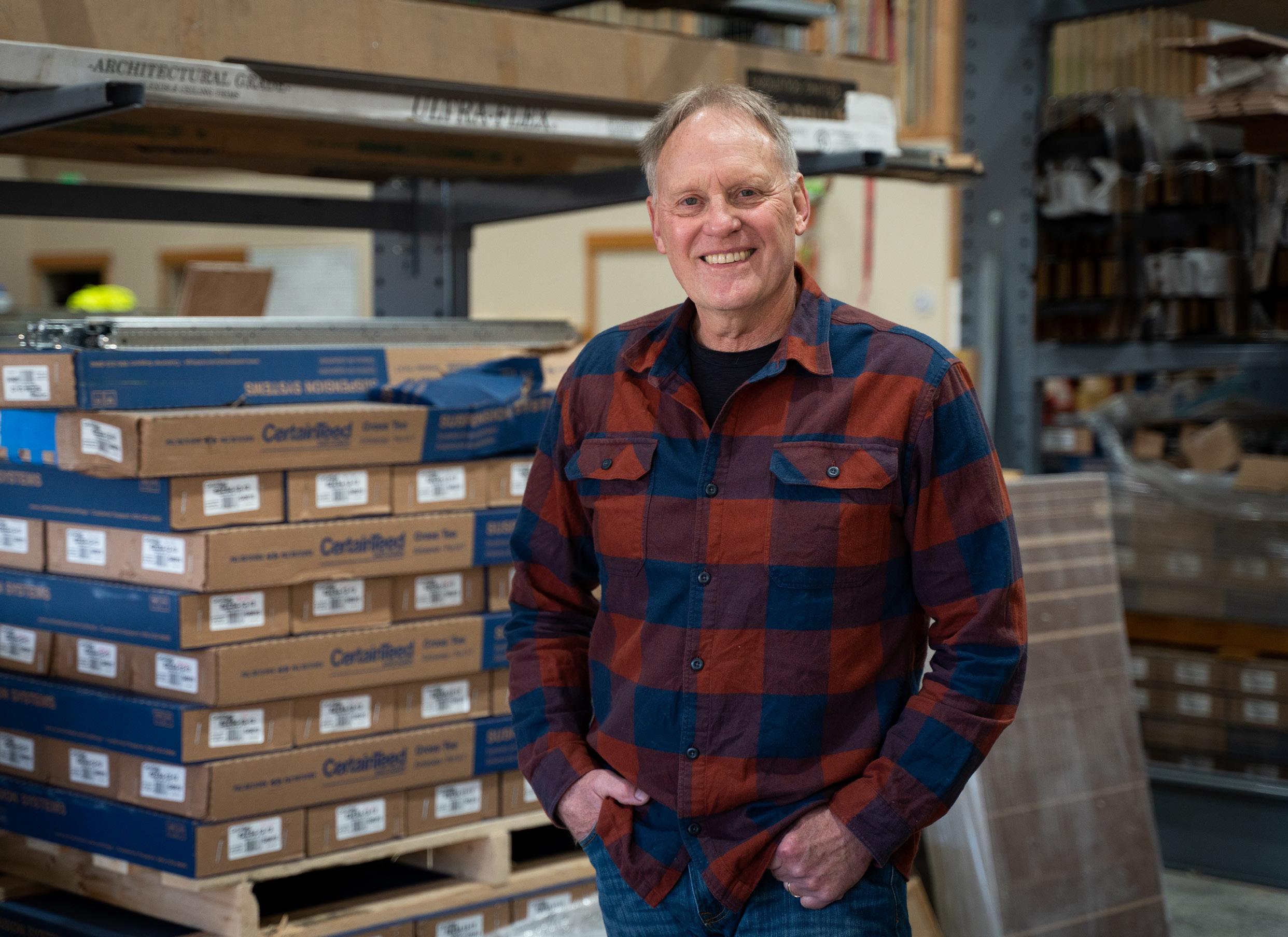
PHOTO: Sattva Photo
Thriving in difficult times
Founded during the ’80s recession, Van Beek Drywall pushes through the pandemic
Mary Louise Van Dyke
Van Beek Drywall Inc. operates under the principle that no job is too small or too large for the company to handle.
That philosophy has proved valuable, with the Ferndale-based company navigating sticky pandemic challenges. Owner Doug Van Beek said company revenues were about $7.9 million in 2021, a drop from $9.8 million in 2020.
The company celebrated its 40th anniversary in December 2021.
Van Beek launched the company at age 22. He had been working for a local business as a drywall finisher but learned that the owner was moving away. Van Beek’s boss encouraged him to get his own business license.
At that time, in the early 1980s, the country was pulling out of a recession, and putting the new company on its feet required time and determination.
“I struggled for several years, and the company slowly grew from there,” Van Beek said.
Whatcom County is a good place to do business, he said, and about 70% of his 78 full-time workers live here. Some staffers have been with the
company for more than 20 years.
Van Beek Drywall’s services include metal stud framing of all types, from structural to ornamental, interior and exterior. Crews also install rigid insulation, acoustic ceilings and specialty wall systems, ceiling and suspension systems, exterior sheathing, and interior finishes. One employee is dedicated to small patchwork and warranty work.
The work is handled by teams that specialize in installation, taping, finishing and cleanup. Wood framing is provided in some cases, and the company uses a local supplier to furnish and deliver the materials.
The projects are mainly commercial, Van Beek said, with most calls coming from longtime clients in Whatcom and Skagit counties and some from farther away in Snohomish and Island counties.
Currently, the company is on a job in north Whatcom County at the new Sumas Elementary School. The November floods put a temporary stop to that task, with much of the town being under water.
“I think there’s going to be a lot of work after COVID with those buildings that have been sitting empty,” Van Beek said.
One of the company’s most exciting recent projects involved installing metal stud framing for the lofty, five-story Fairhaven Tower in Fairhaven.
Other notable jobs involved the Sehome High School reconstruction in Bellingham and student housing projects on North State, Forest and Garden streets in downtown Bellingham.
In construction, there are a lot of fly-by-night guys, Van Beek said — people who work for a short time. Van Beek Drywall has successfully attracted people who are long-term employees and “some of the best craftsmen in the industry,” he said.
The company is nonunion and strives to create a good work environment for employees, Van Beek said. Full-time employees are offered competitive wages in addition to medical, dental and retirement packages.
Van Beek expects nothing to change at the company in the next several years. However, he does anticipate stepping down in the next three to five years, with an employee taking over management.
“Our hope is we’ll be here forever,” he said. ■
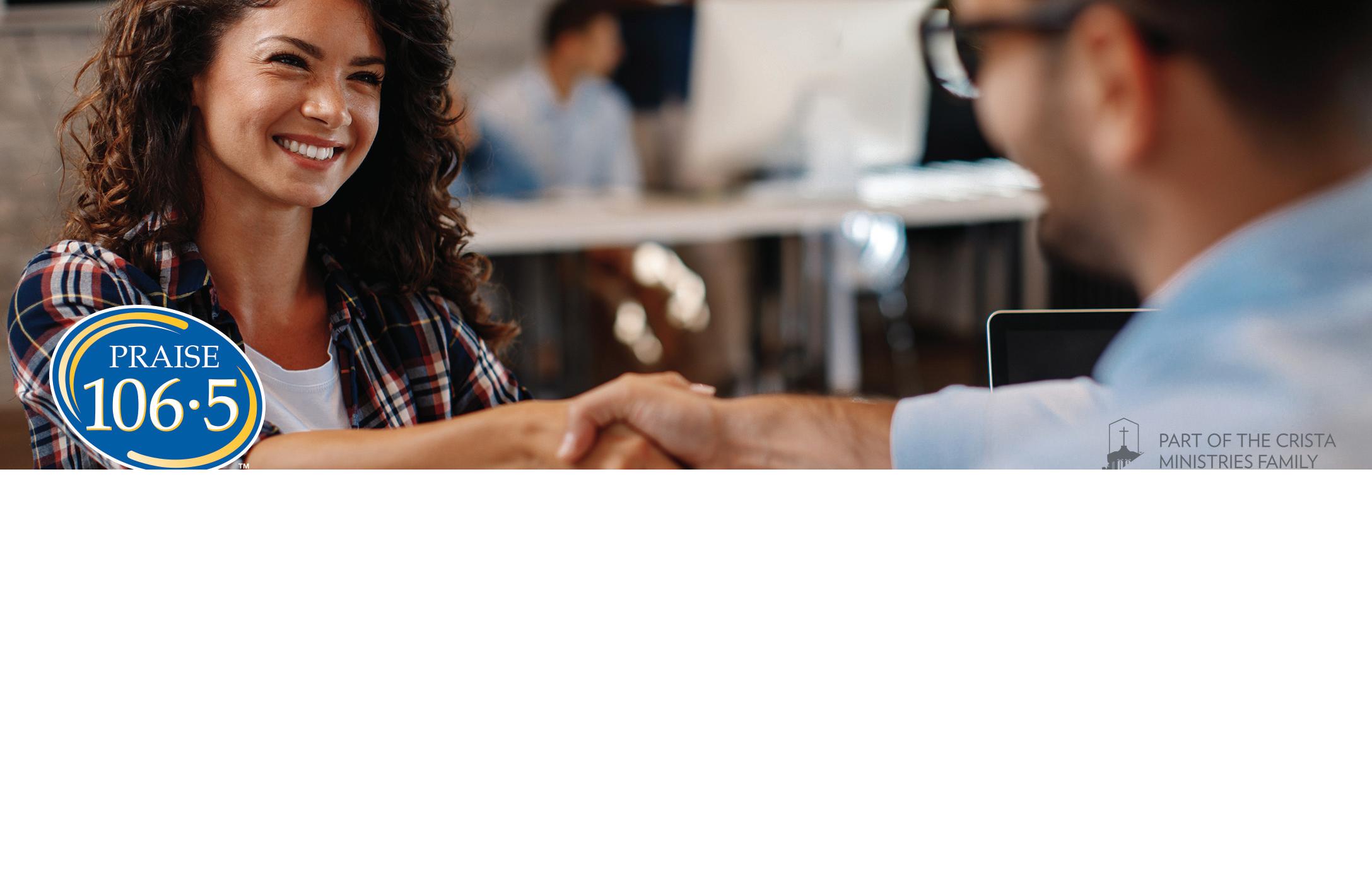

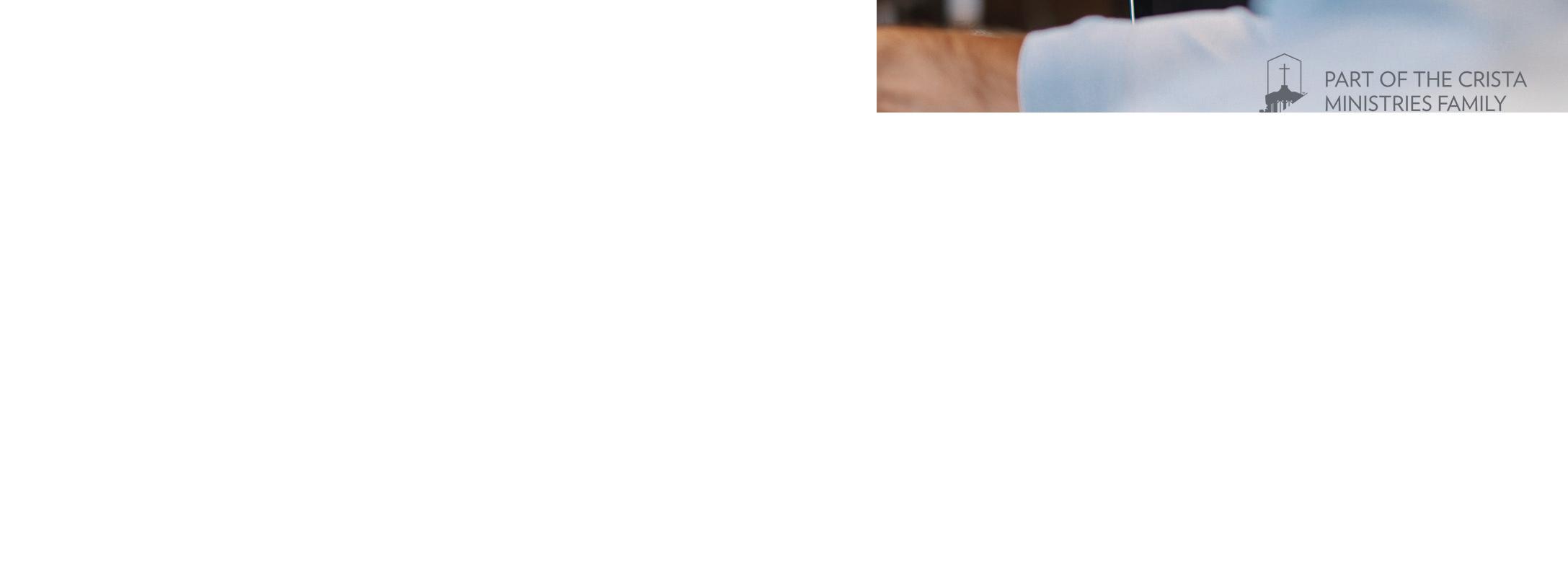

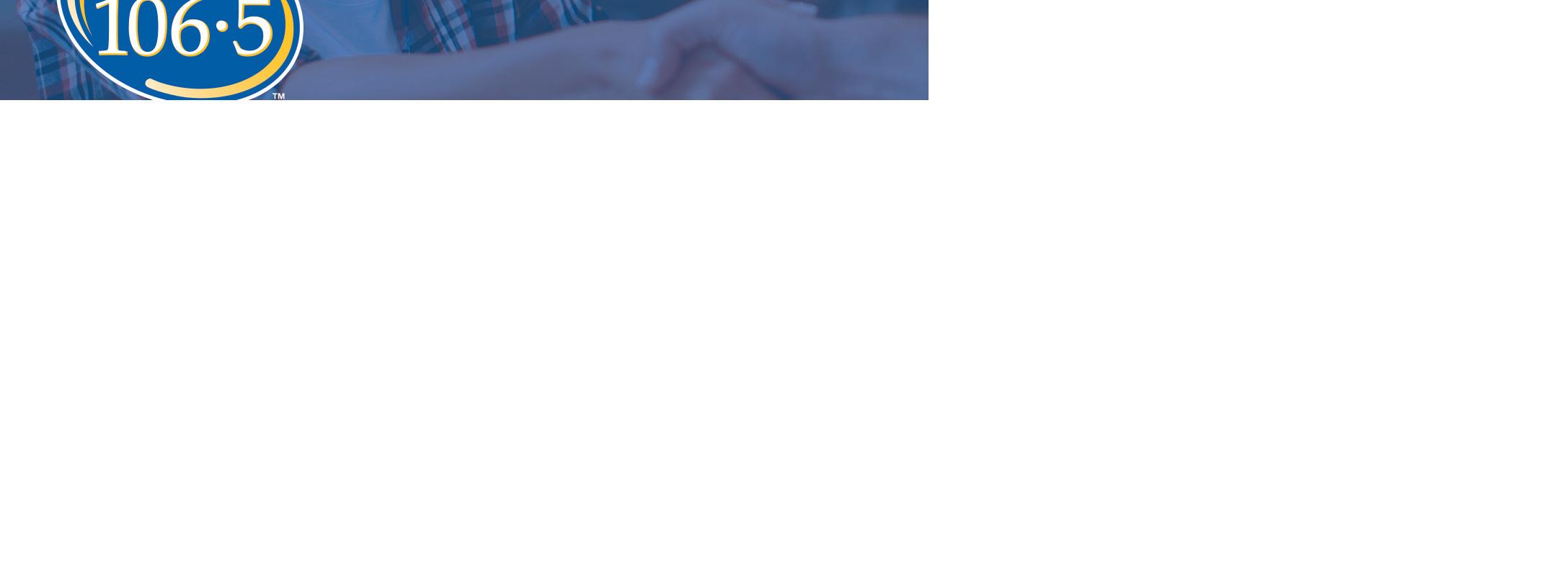
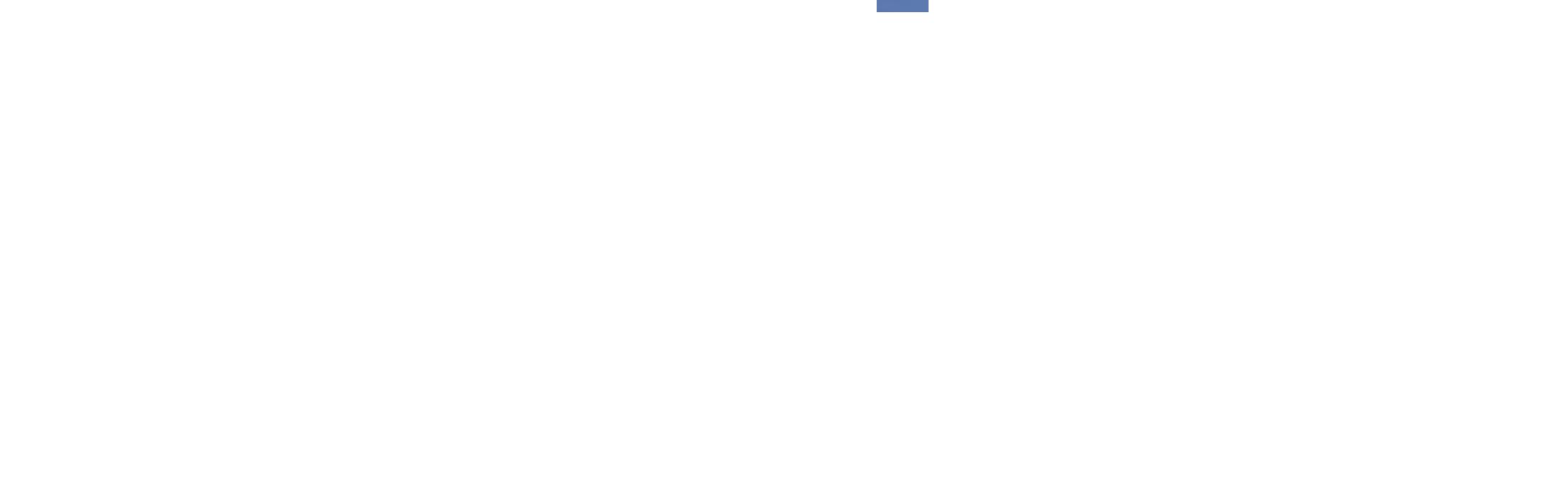

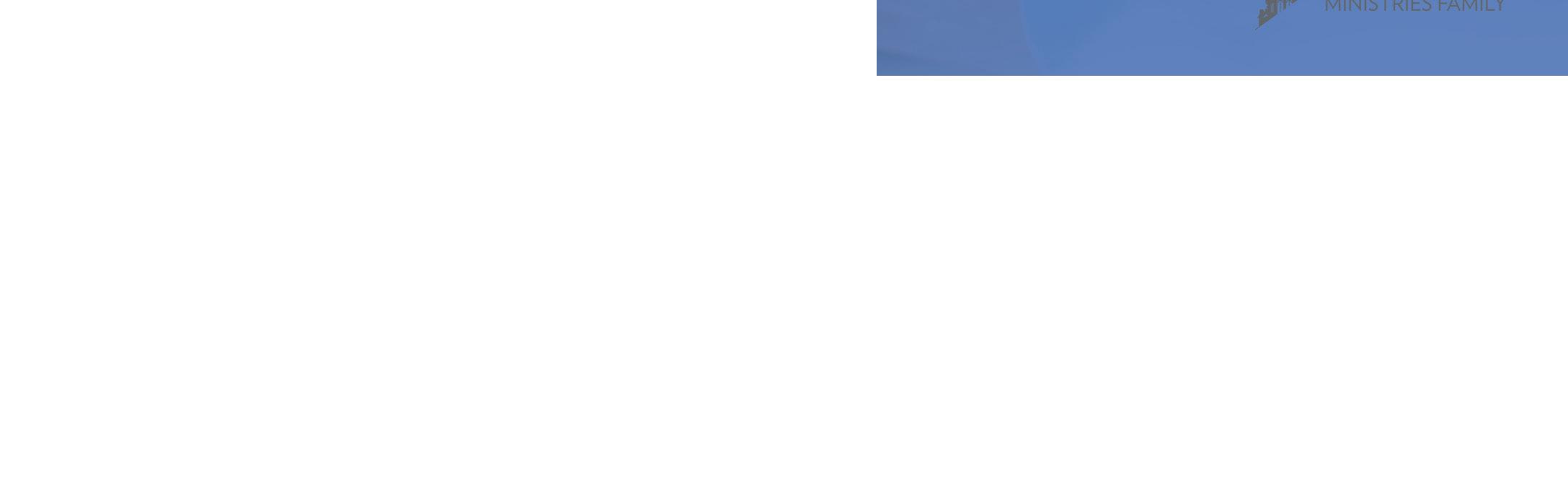

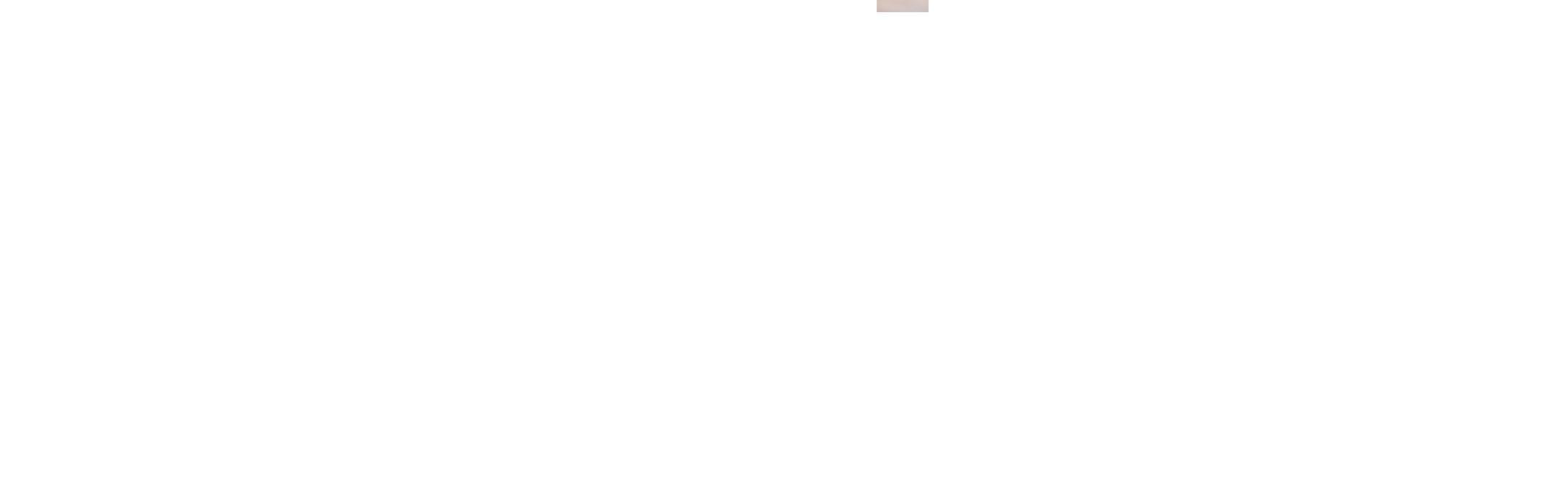

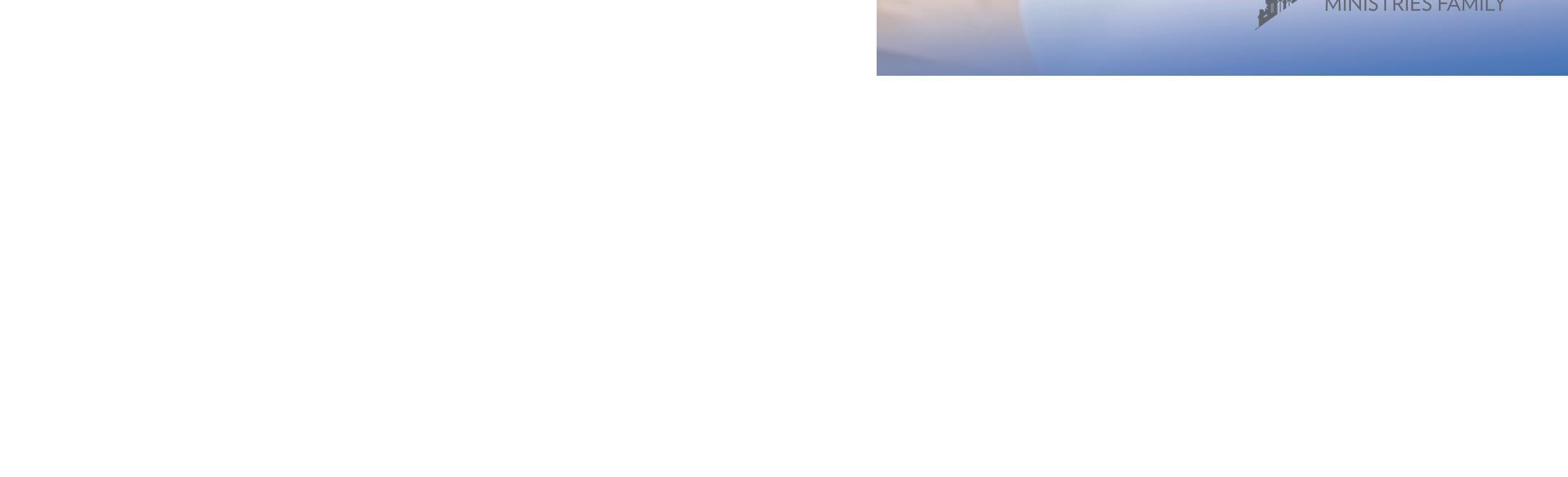
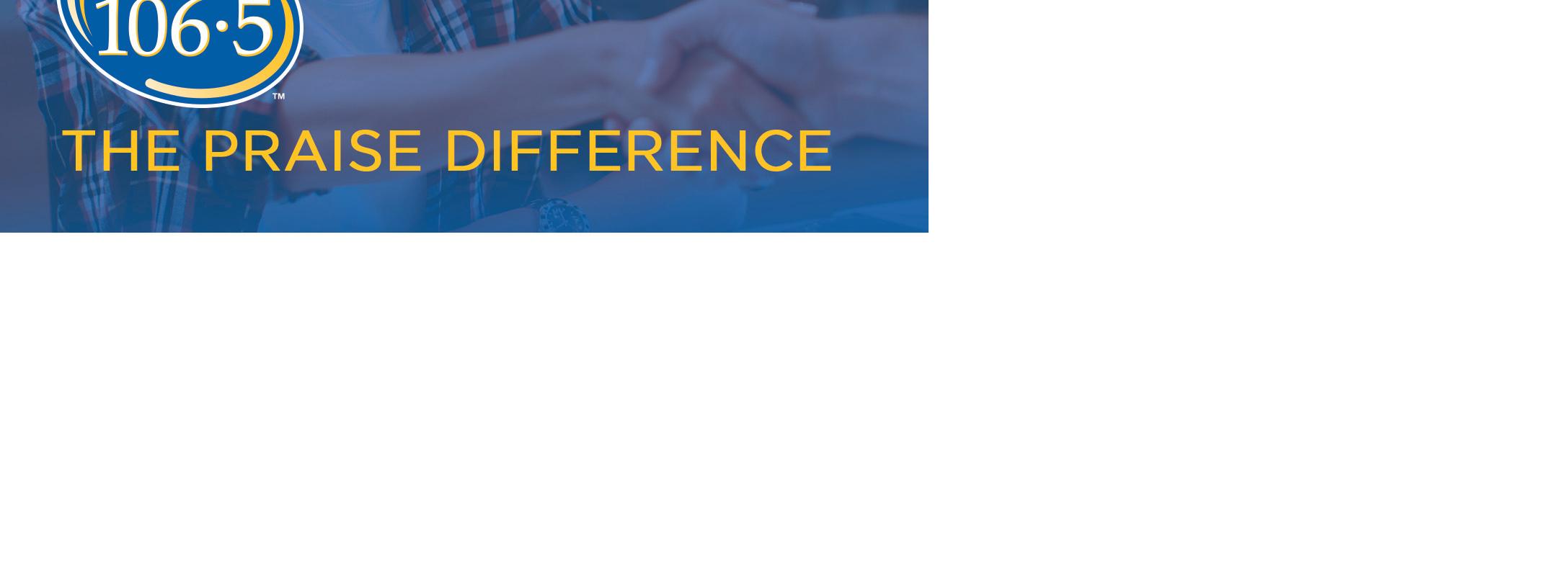
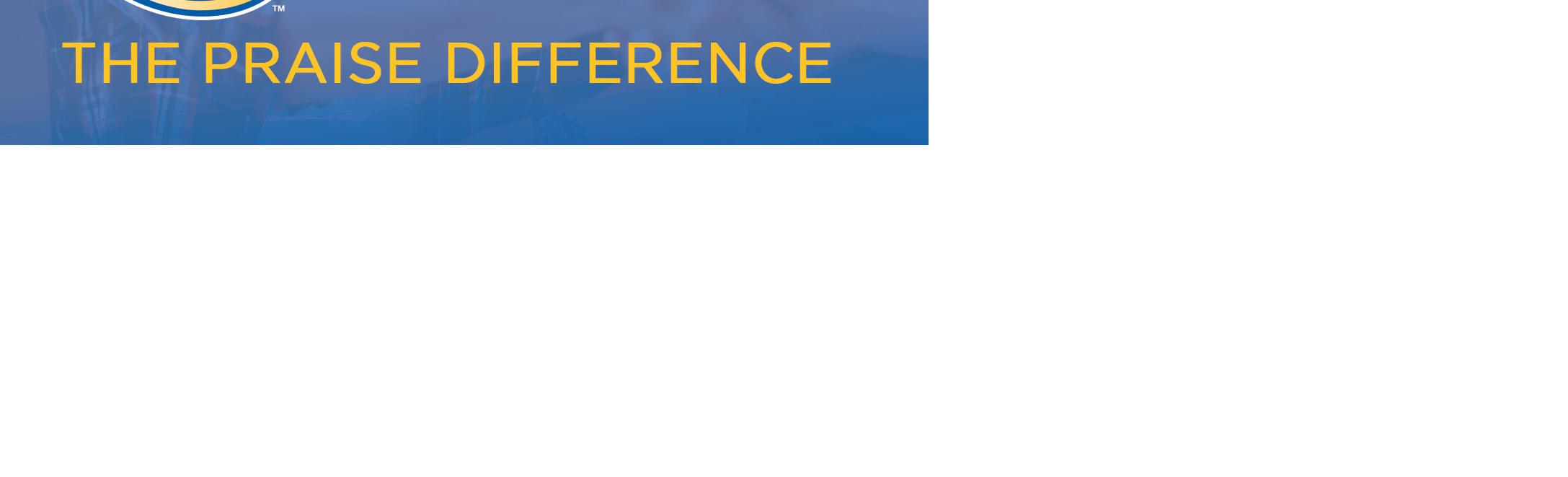
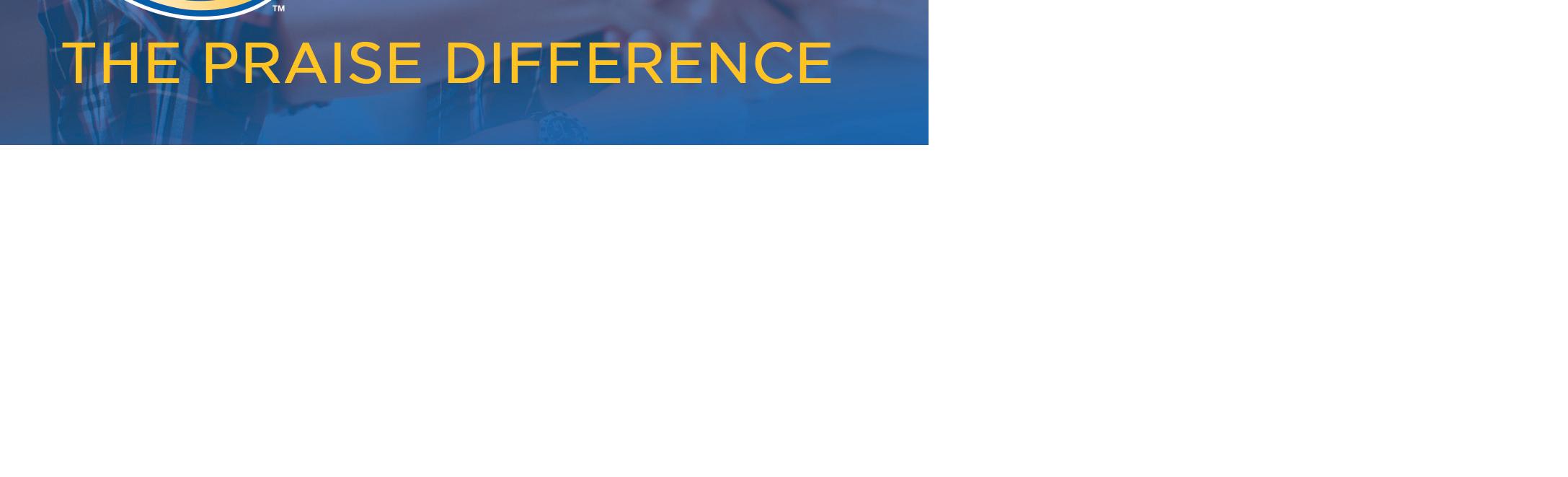
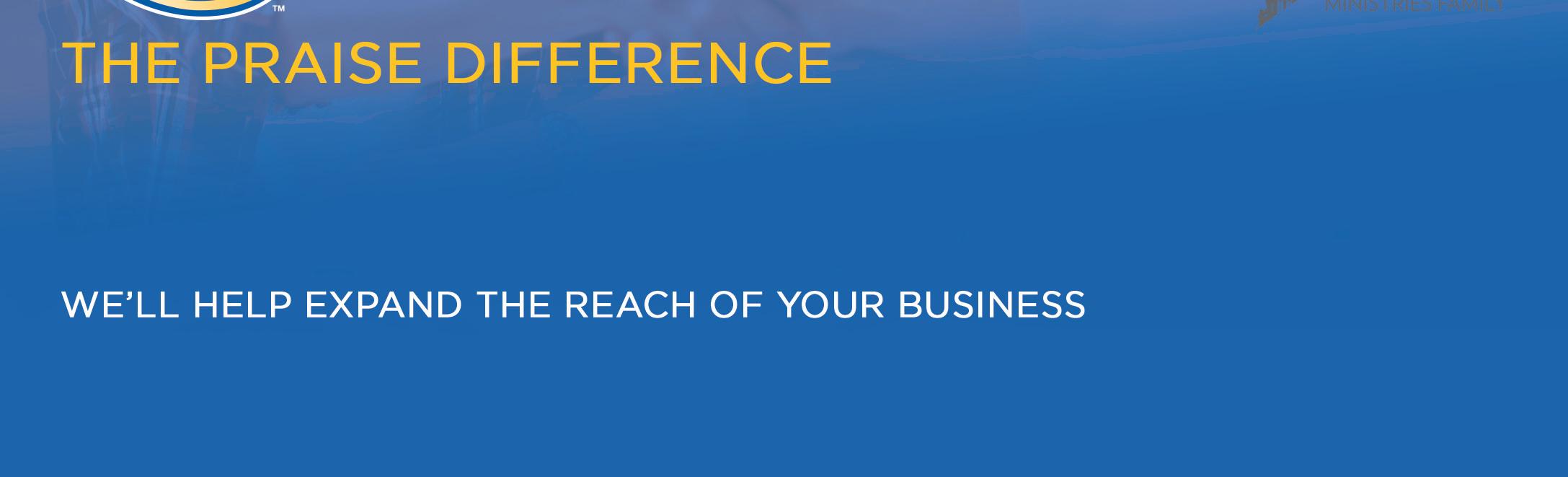
