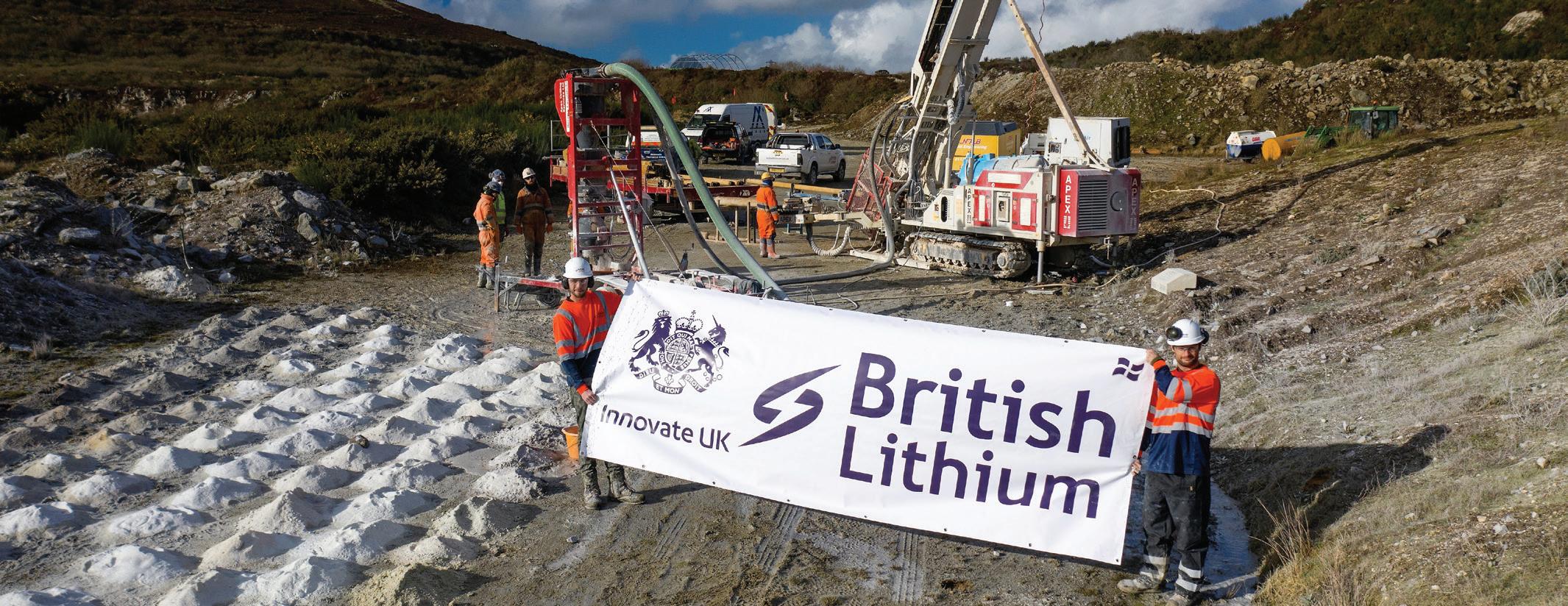
4 minute read
BRITISH LITHIUM
GREEN MINING OF THE FUTURE
BRITISH LITHIUM IS THE FIRST COMPANY TO DISCOVER A SIZABLE LITHIUM DEPOSIT IN THE UK, THE FIRST TO DEVELOP A NOVEL PROCESS FOR EXTRACTING LITHIUM IN A SUSTAINABLE MANNER AND THE FIRST TO PROVE BATTERY GRADE LITHIUM CAN BE PRODUCED FROM CORNISH GRANITE.
ased in Roche, the business has identified a resource of over 100 million tonnes in a former clay mine near St Austell - enough to support a projected annual production of 20,000 tonnes of lithium carbonate. That’s enough to meet one-third of Britain’s likely demand by 2030 when all UK car manufacture converts to electric vehicles.
From the very start, British Lithium’s aim has been to achieve the lowest environmental footprint possible. Car electrification is based on the need for a greener future, yet most lithium production is currently powered by coal in China.
“That’s why we have developed a highly efficient process for concentrating lithium mica without using chemicals and why we will be using renewable energy to power our newly invented Mi-Sep ® technology which has a patent pending,” said CEO Andrew Smith.
British Lithium carried out a scoping study in 2018 to target areas for lithium, which is only found in the brown mica of granite. The work involved field mapping, grab sampling, trenching and drilling to provide a better understanding of lithium mineralisation and grade variability within the deposit.
Mineral processing starts with breaking the rock to a size where the minerals can be separated from one another and extracting lithium from the waste.
British Lithium’s method focuses on minimising chemical use so the waste coming from its plant will not need neutralising. Water composition is essentially unchanged and, because the team will be extracting micas at a really coarse size, the waste material is very similar to building or beach sand.
“Once we have made a lithium mica concentrate, we roast it using lime as a reagent, rather than acid,” said Andrew Smith. “The solution is then purified to produce lithium carbonate.”
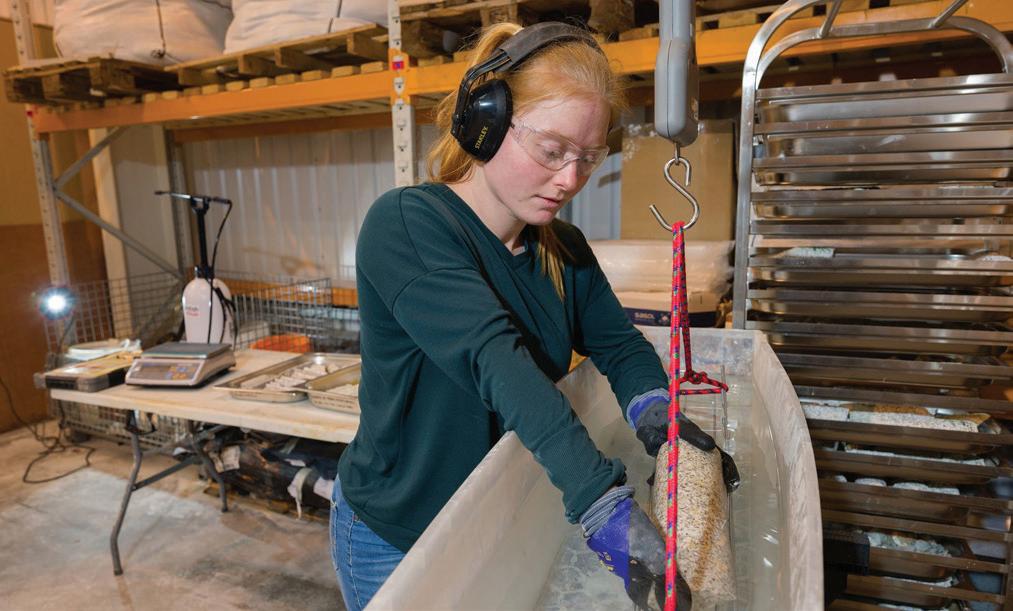
The Government has helped fund British Lithium’s dedicated lithium metallurgical research laboratory in Cornwall – the only one of its kind in the country. Innovate UK is also providing nearly £3m to help develop a pilot plant that should be operational by the end of 2021.
“It’s important to eliminate scale-up risk by producing lithium in real-world conditions at pilot scale,” said Andrew Smith, an engineer who previously ran an international mining team for the Cinovec lithium project in the Czech Republic, currently Europe’s largest lithium resource. “The plant will allow us to collect accurate data on any waste products and emissions, test the energy and water balances and prove our process route. We can also produce sufficient quantities of battery grade lithium to achieve potential customer acceptance and buy-in.
“Pilot scale production represents a key milestone because battery and electric vehicle makers are very concerned about their carbon footprint. Aiming to produce the world’s greenest lithium gives us a huge advantage, but we need to prove what we are saying.
“A million pounds worth of bespoke equipment has already been ordered and we will be producing lithium carbonate here by early next year.”
Cars are the UK’s biggest export, creating £80 billion worth of GDP and over 800,000 jobs. To comply with the government’s recently announced green agenda, the industry needs to transform itself in just 9 years. That means investing heavily in the lithium battery supply chain – especially as Europe has the same aspirations and is already building gigafactories.
“The UK Government’s recently published ten-point plan for a green industrial revolution requires all new cars to be electric by 2030,” said British Lithium Chair Roderick Smith, an acknowledged world expert in extractive metallurgy who spent more than 30 years leading publicly listed Australian mining companies as CEO. “We have been researching and developing our plan for sustainable lithium extraction in Cornwall for the last three years and have already recruited some of the country’s finest minds to our project.
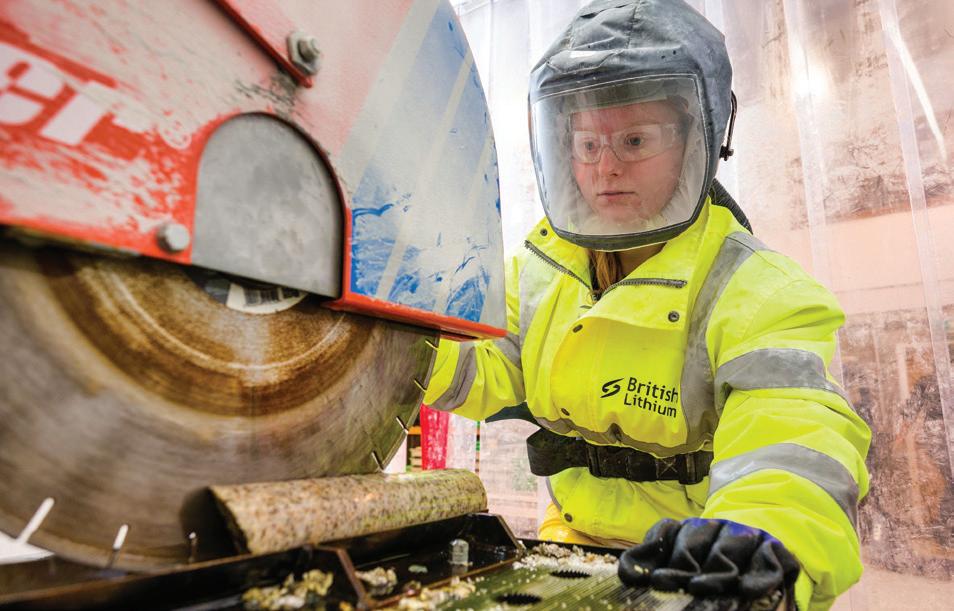
“When we are fully operational, we expect to be employing hundreds of people directly and thousands more through our supply chain. We also anticipate meeting at least one third of the UK’s annual demand for lithium, whilst protecting the environment.”
With a growing team of geologists, metallurgists, technicians and administrative staff, British Lithium looks set for a bright, very productive future.
“I’m confident we have the drive, knowledge and professional expertise to achieve our goals,” said Andrew Smith.
“The work we are doing is crucial and we’re excited about setting a good example and making a real difference.
“Not just to Cornwall, but the UK as a whole.”
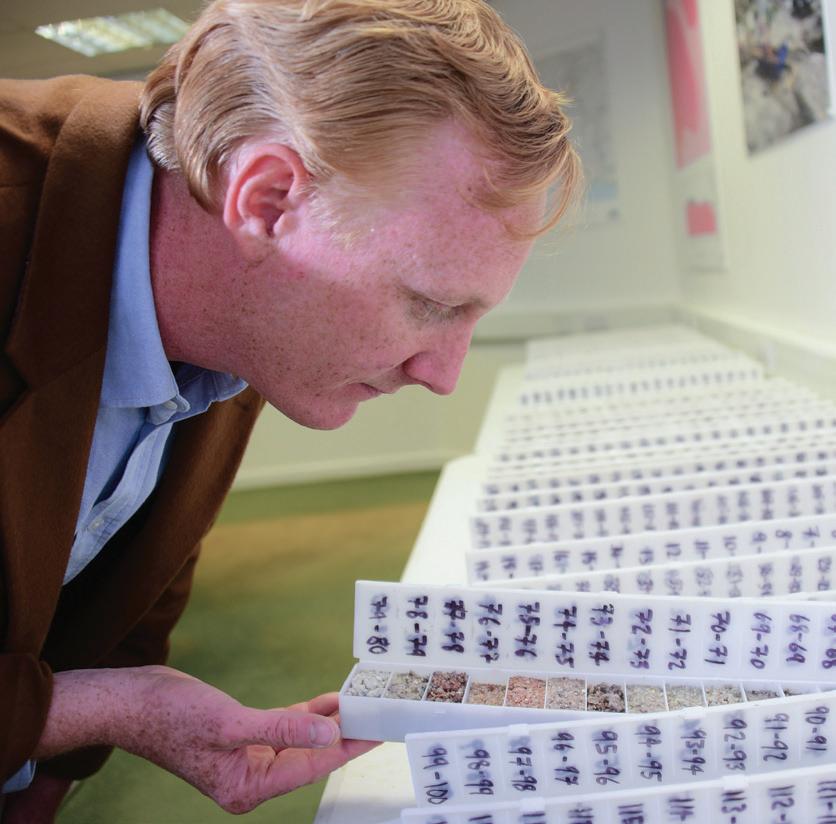