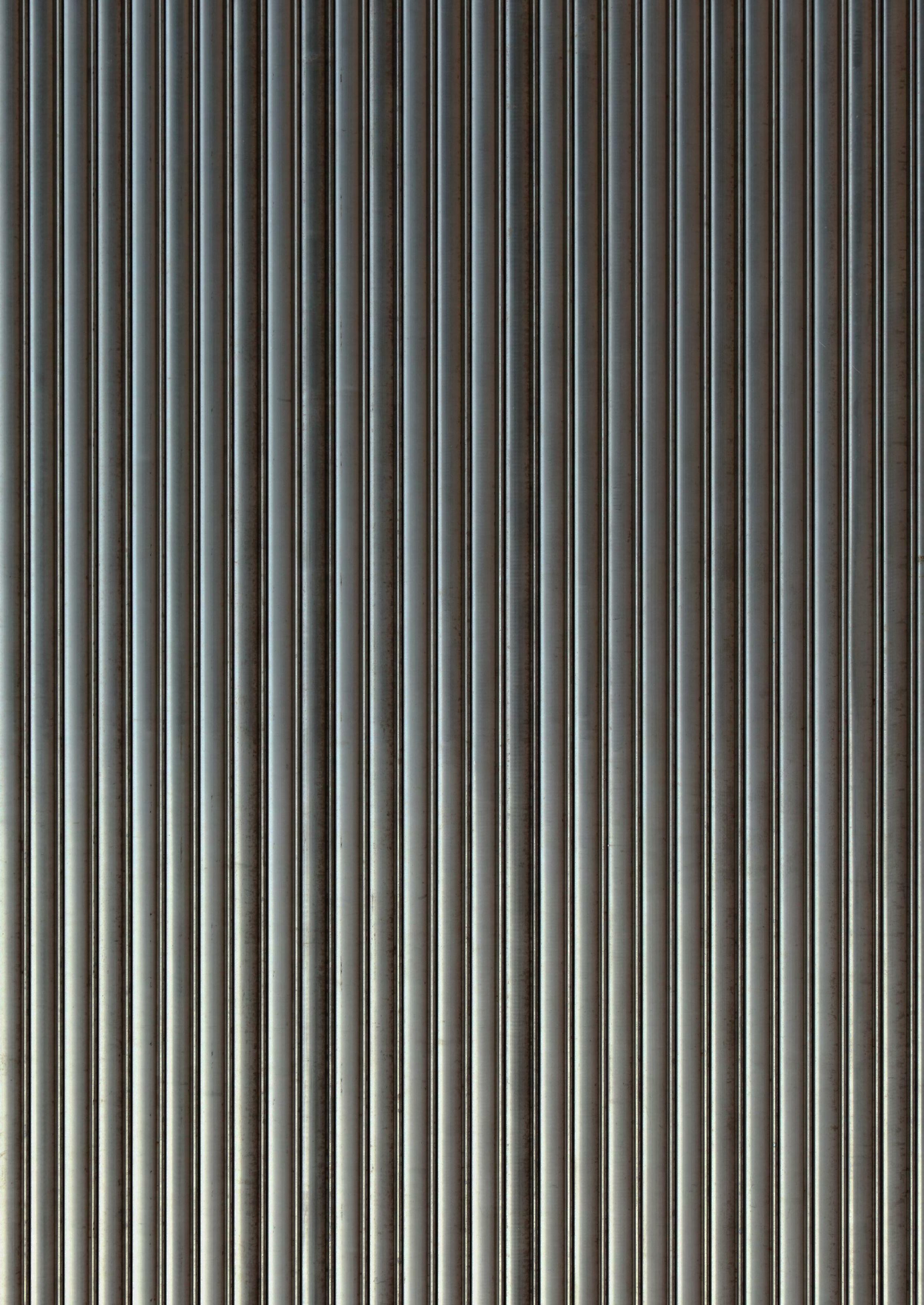
8 minute read
Paralloy & FVC
PROJECT DIRECTED BY Liv Culling
WRITTEN BY Romana Moares
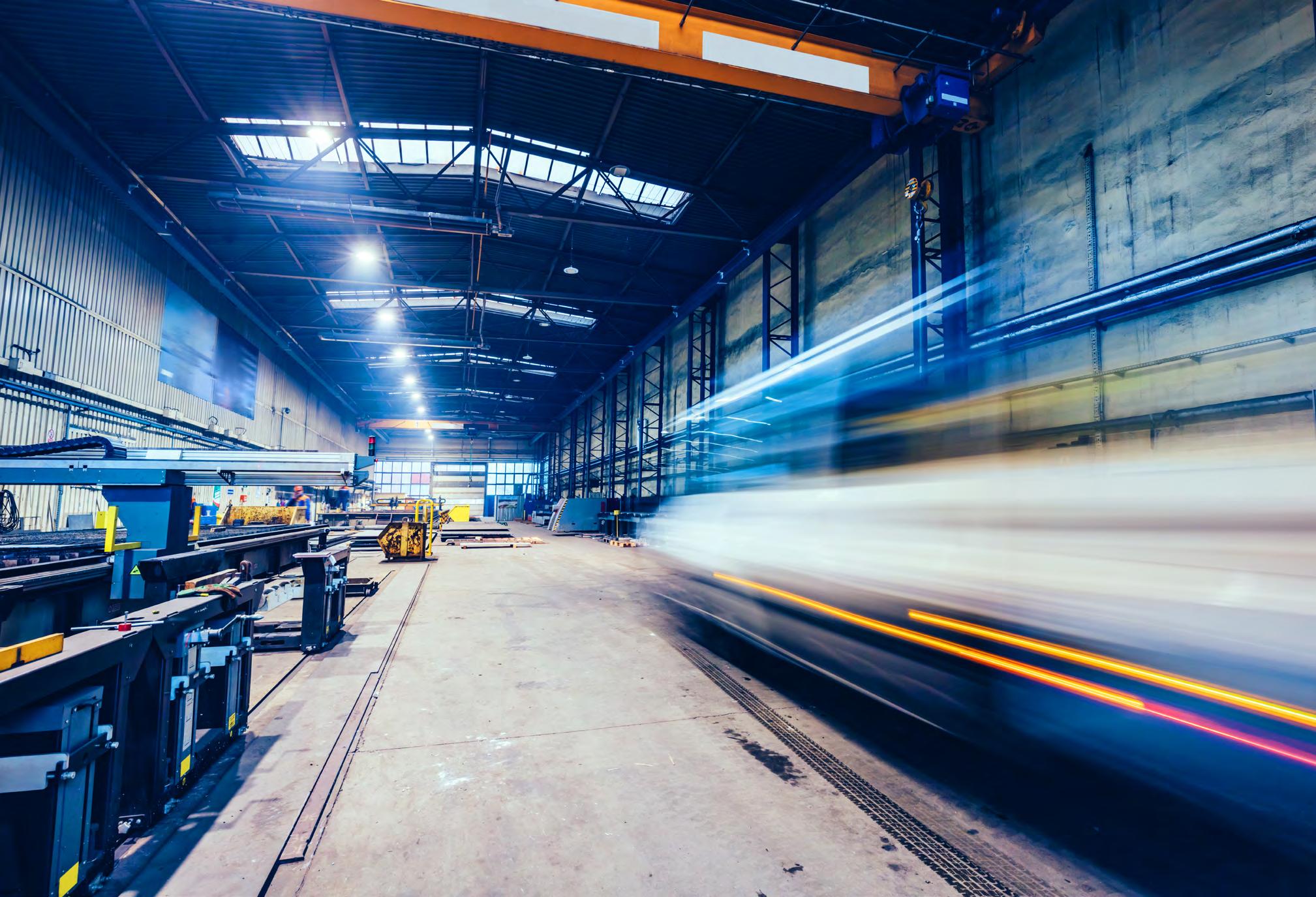
Driving the Modern World
With origins rooted in the UK’s steel industry, Paralloy & FVC take pride in serving many of the world’s most demanding industries. From power generation and transport to manufacturing and critical chemical industries, their high-precision alloy components are used to drive the modern world.
Since its Billingham site opened in 1967, Paralloy has specialised in transforming raw elements into world-class products that power the petrochemical, ethylene, and syngas industries.
From initial concepting to dispatch and delivery, the company provides a comprehensive end-toend service. Combining multiple foundries on one site gives Paralloy a high degree of control over the manufacturing process, and enables it to provide fully-finished precision-machined tubes, components, sub-assemblies and full fabrication leading to quicker turnarounds for its clients.
Over the last few years, the company has gone through a number of organisational and business changes. At the start of 2020, the private equity company Nimbus acquired the Centrifu-
Paralloy & FVC
gal Castings Division of the Doncasters Group, which consisted of Teesside-based Paralloy and South Yorkshire-based FVC, as part of a management buy-out. In June of the same year, the company, now operating as Paralloy Ltd., acquired Express Engineering’s aerospace division and created a new company, Firth Vickers Engineering (FVE). The sister companies complement one another with their individual capabilities – while Paralloy specialises in high-alloy steels for the petrochemical, syngas and iron DRI industries, FVC makes proof machine components for the industrial gas turbine, aerospace and industrial markets. The third business, FVE, which last year re-located to the Tees Advanced Manufacturing Park (TeesAMP) in Middlesbrough, offers fully integrated engineering solutions, including finish machining and sub assembly, quality control and testing.
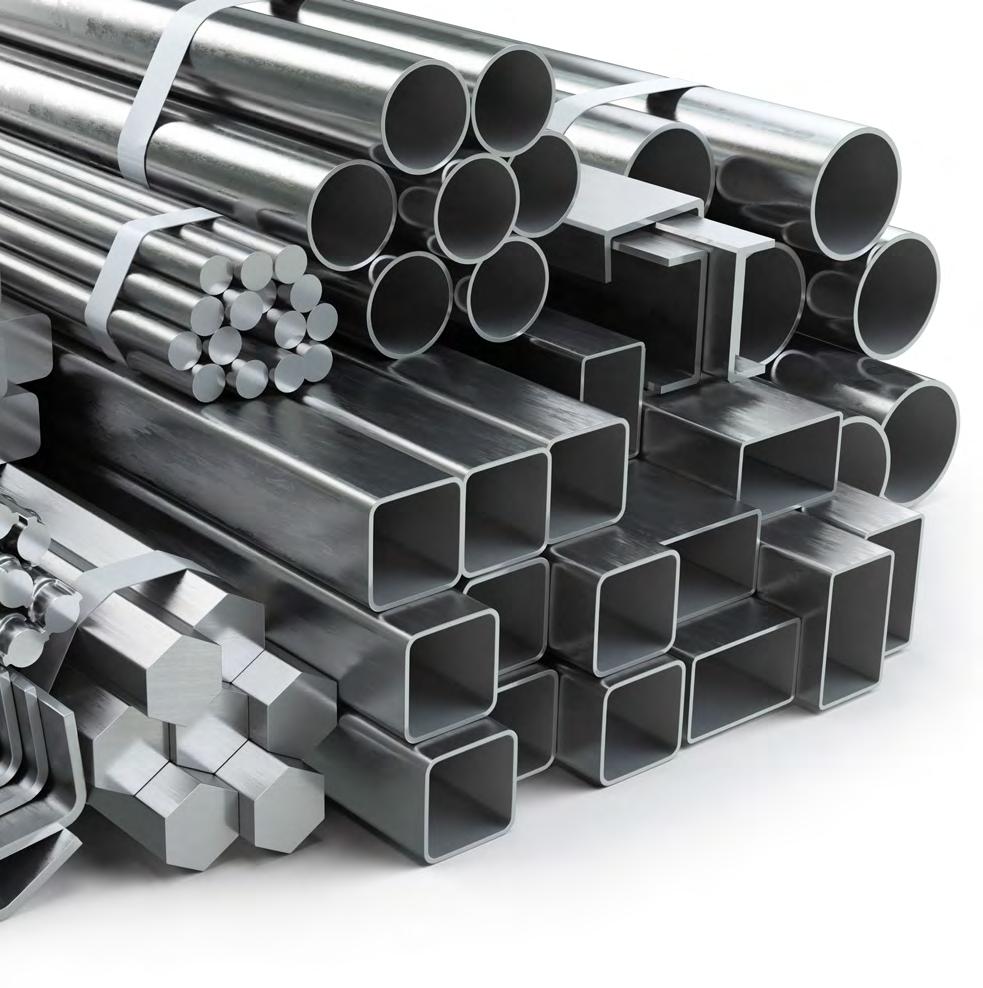
Unique capabilities
Paralloy primarily serves the synthetic natural gas and ethylene cracker petrochemical markets, manufacturing and supplying specialist centrifugal castings in horizontal and vertical configurations in high-steel alloy materials along with static castings, for use in high-temperature furnace applications at the very heart of major petrochemical plants.
The company’s products include steam reformer tubes manufactured in a broad array of materials, including H39WM, H39WMR, including the latest innovation - H39WM+. This material offers superior heat-resistant properties and meets the stringent criteria for steam reforming furnaces with exceptional creep rupture strength and enhanced carburisation resistance.
The ethylene tubes are produced in a range of materials, including OPTIM-AL, which features exceptional oxidation and carburisation resistance properties. Meanwhile, PEP increases plant throughput without compromising reliability and is available in bespoke internal profiles that suit most available ethylene technologies. H46M and H39WM both feature outstanding creep strength and carburisation resistance.
Paralloy also develops and patents its own market-leading alloys for specialist applications including blue hydrogen and low-coking ethylene. The company is one of only a handful of companies worldwide to produce these products and is a key supplier to the blue hydrogen market, which produces virtually no greenhouse gas emissions and is much in demand as firms across the world transition away from polluting fossil fuels.
The sister company FVC is a leading manufacturer of high-quality compressor and exhaust casings for the global aerospace industry, and also manufactures critical centrifugal cast components for civil aerospace, offering high-quality, low-cost, and reliable solutions to the world’s most popular engine platforms. Its specialist expertise in centrispun casting, heat resistant materials, and shaped split casings makes the company the first choice for clients across the globe.
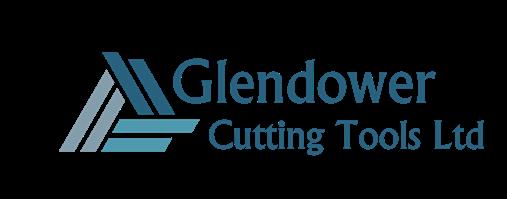
sales@glendower.co.uk
Glendower Cutting Tools have been a cutting tools specialist in Leicester since 1972. We supply all the standard inserts and tooling, but uniquely also manufacture special inserts in our own facility in Leicester.
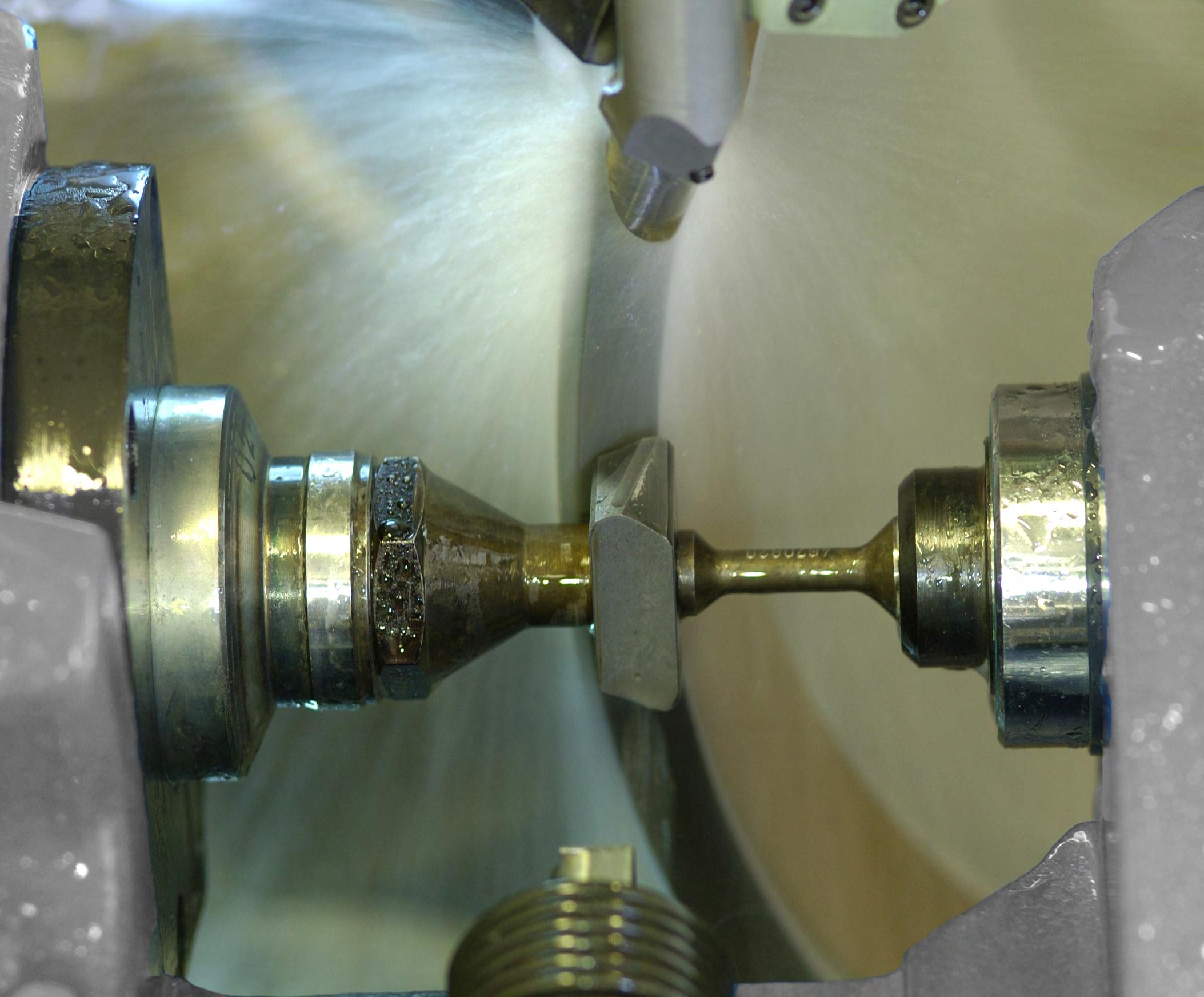

CAPACITY
| Hydramet 12.5 Tonne Insert Press | Vacuum Furnace | | Agathon 250 Plus, 3-Axis Insert grinder | Agathon 250 Ultra, 3-Axis Insert grinder | | Agathon Combi 400, Plus 4-Axis Insert grinder with K-Land & Chipbreaker | | Lapmaster AC400F, dual wheel Insert thickness grinder | | Carbide Saw thickness grinder | Carbide bore grinder | 3 Cutter grinders | | 3 CNC controller creep feed grinders | Brazing and Shotblast facilities | | Solidworks 3D modelling and drawing | CNC Router | Milling Machine |
glendower.co.uk
Glendower Cutting Tools Lakeside Business Park Pinfold Road Thurmaston Leicester, LE4 8AS
Manufacturing Feature
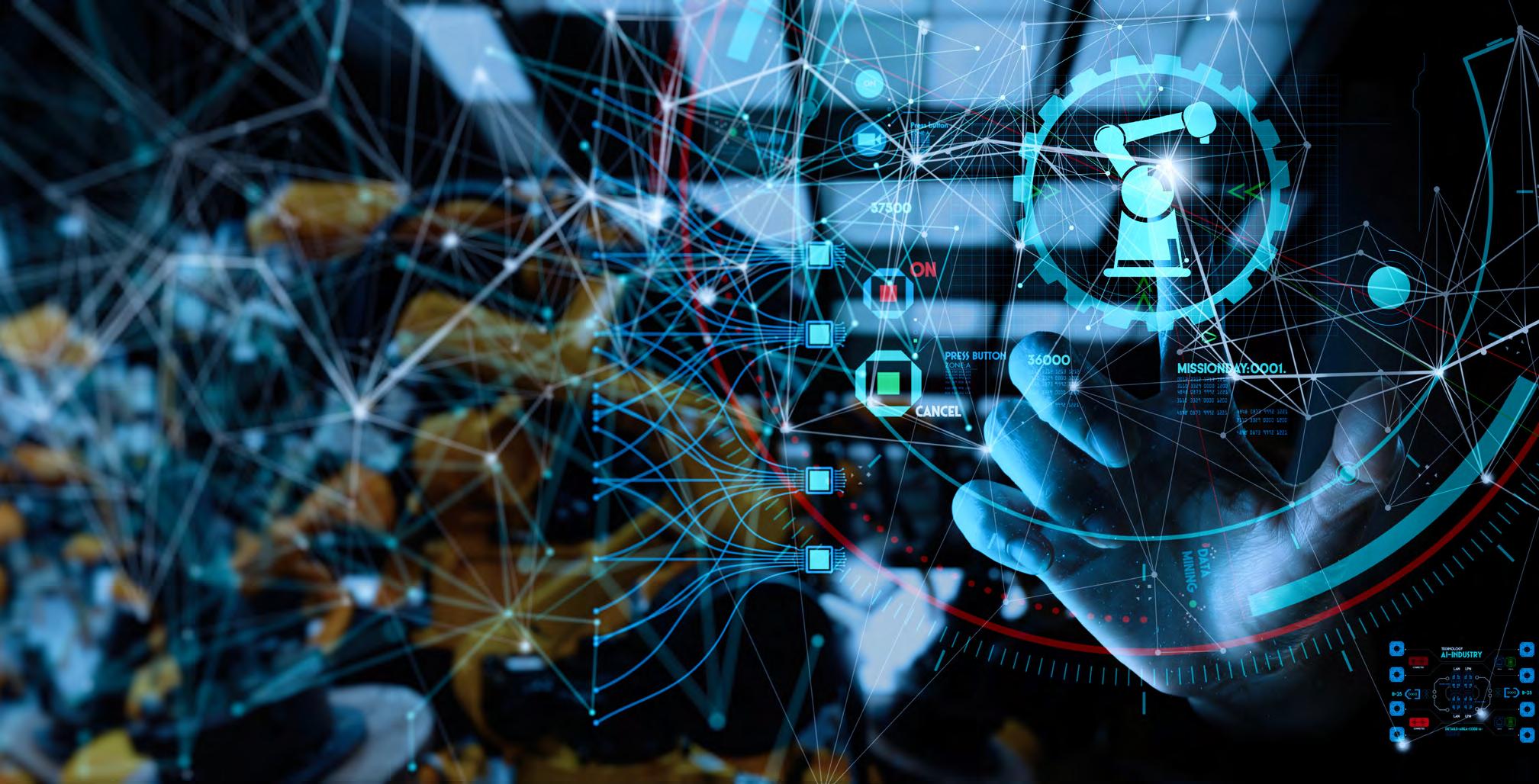
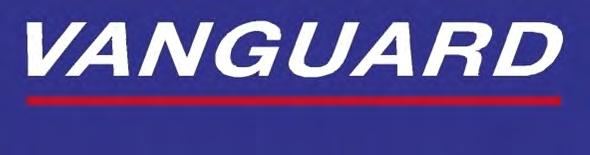

Established in 1974 as Alkron Packing, our name changed 17 years ago to Vanguard Packing Limited.
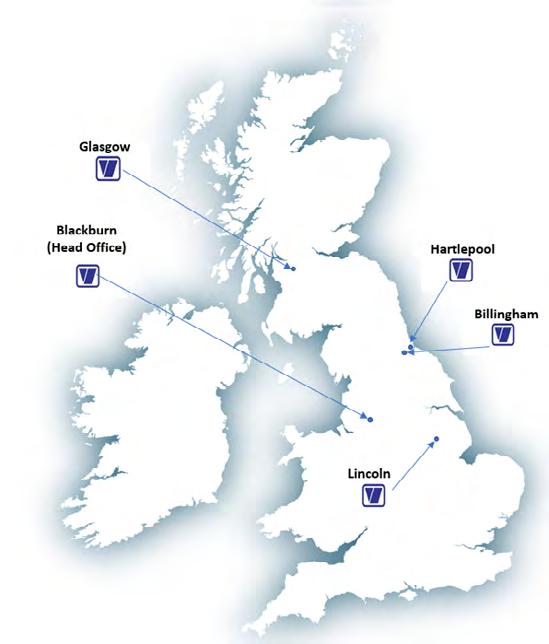
47 years experience of all export packing requirements.
5 sites in the UK, with over 70 employees.
Extensive lean manufacturing C. I. program implemented with and ongoing available Capex of £600,000.
SLA’s established with leading major corporate clients, across the UK.
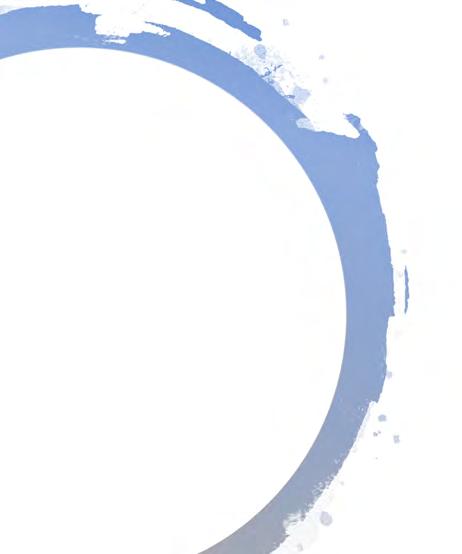
Renewed ISO 9001:2015 accreditation.
We offer high quality and competitive prices along with flexible lead times and tailored export packing to suit your needs.
We are a financially astute company with an excellent credit rating.
www.vanguardpacking.co.uk
01254 668727 blackburn@vanguardpacking.co.uk Find your local site
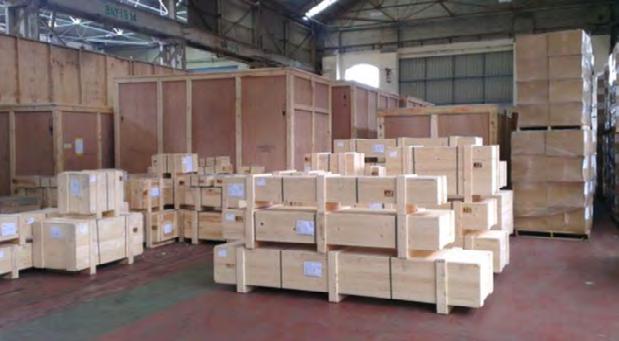
Vanguard Packing Limited Manner Sutton Street Blackburn Lancashire BB1 5DT
Paralloy & FVC
World-class operation
Paralloy & FVC have developed and implemented world-class design and engineering processes that are both time-saving and cost-effective. All of the processes are in-house, including casting, chemical analysis, shot blasting, prepping, sawing, as well as horizontal and vertical boring.
The demand placed on the components in extreme environments necessitates a rigorous approach to manufacturing and testing processes. Each of the alloys are taken through an intensive testing process before they are made available, ensuring only the best, safest products are sold under the Paralloy & FVC name. “As a solution-focused organisation, we have developed a truly adaptable process that accommodates bespoke requirements, such as tailored castings for unique applications as well as a range of products, typically required in bulk volumes. Our methods ensure project delivery that is significantly higher in value and lower in cost compared to other industry providers.”
The company’s production processes are efficient, allowing Paralloy to fulfil orders within incredibly short industry lead-times. Innovation and continuous improvement are key – by working with metallurgical specialists, and furnace designers, the company has developed ground-breaking new materials with wide-ranging capabilities suitable for a broad number of applications.
The research and development efforts drive innovation forward, producing world class products and patents. “Serving both the syngas and ethylene petrochemical markets, our innovative engineers rise to the challenge of providing world-class materials such as Optim-Al, our new anti-coking alloy, and other market-leading innovations designed to provide high operating performance and reliability in the most demanding of conditions.”
Glendower Cutting Tools Ltd
We are a family-owned business based in Leicester we celebrated our 50 year anniversary in March 2022, specialising in the manufacture of carbide cutting tools, we are unique in that we press, sinter & grind all our own inserts at our manufacturing plant in Thurmaston, Leicester.
Producing standard ISO inserts along with bespoke inserts of all shapes & sizes to customers needs, from the best quality powder and ground on the latest state of the art machinery.
We also design Toolholders, cutters & inserts to suit your needs from customer component drawings via our Cad Cam 3D Solidworks system.
We are also main distributors for many cutting tool companies including ZCC.CT, Kennametal, Iscar, Taegutec Dormer / Pramet, Mitsubishi etc. So for all your cutting tool needs contact our sales team and see what we can offer you.
sales@glendower.co.uk www.glendower.co.uk
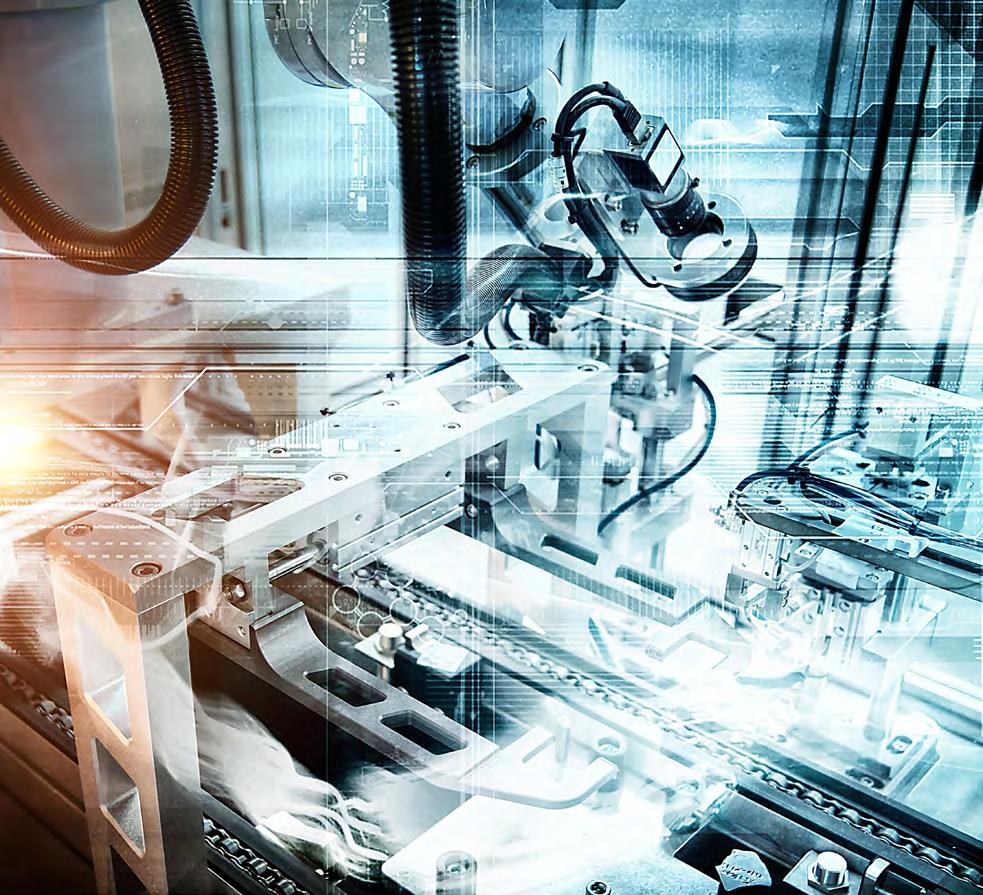
Paralloy & FVC
Forging ahead
Paralloy Chief Executive Robert McGowan affirms that becoming part of the Nimbus Group was good news for the business. “Nimbus’s background and expertise complements our strong management team and we have a partner that understands us, our business and is excited about our future. While we will continue to focus our efforts on building on the great British brands of Paralloy and Firth Vickers Centrispinning (FVC) this transaction has enabled us to uniquely position Paralloy and FVC for more growth, thereby expanding our portfolio, capabilities and market reach.”
Robert McGowan himself led a management buyout two years ago. Since then, then sales have more than doubled and the business has expanded. This success has been recognized by the UK government which has provided a General Export Facility which supports a £15m funding package from Santander UK, with an 80% guarantee from UKEF to support its export-led growth. The funding is enabling Paralloy to fulfil the most exports in its 90-year history, with shipments to North America, the Middle East and Asia-Pacific, as well as to take on higher value export contracts, to open two new sites on Teesside, and create new jobs locally.
The business currently exports 95% of its output to 70 overseas markets. Its customer base includes major companies, including Air Products, Air Liquide, Siemens, Rolls Royce, Exxon, Sabic, DOW and GE, amongst many others. Robert McGowan affirmed that the UKEFbacked funding package from Santander UK has enabled the company to future-proof the business, and provided the working capital to fulfil bigger export contracts. ”It’s truly been a game-changer, helping us focus on building out our order book even more and hiring the right team to support that.”
www.paralloy.co.uk
Manufacturing Feature
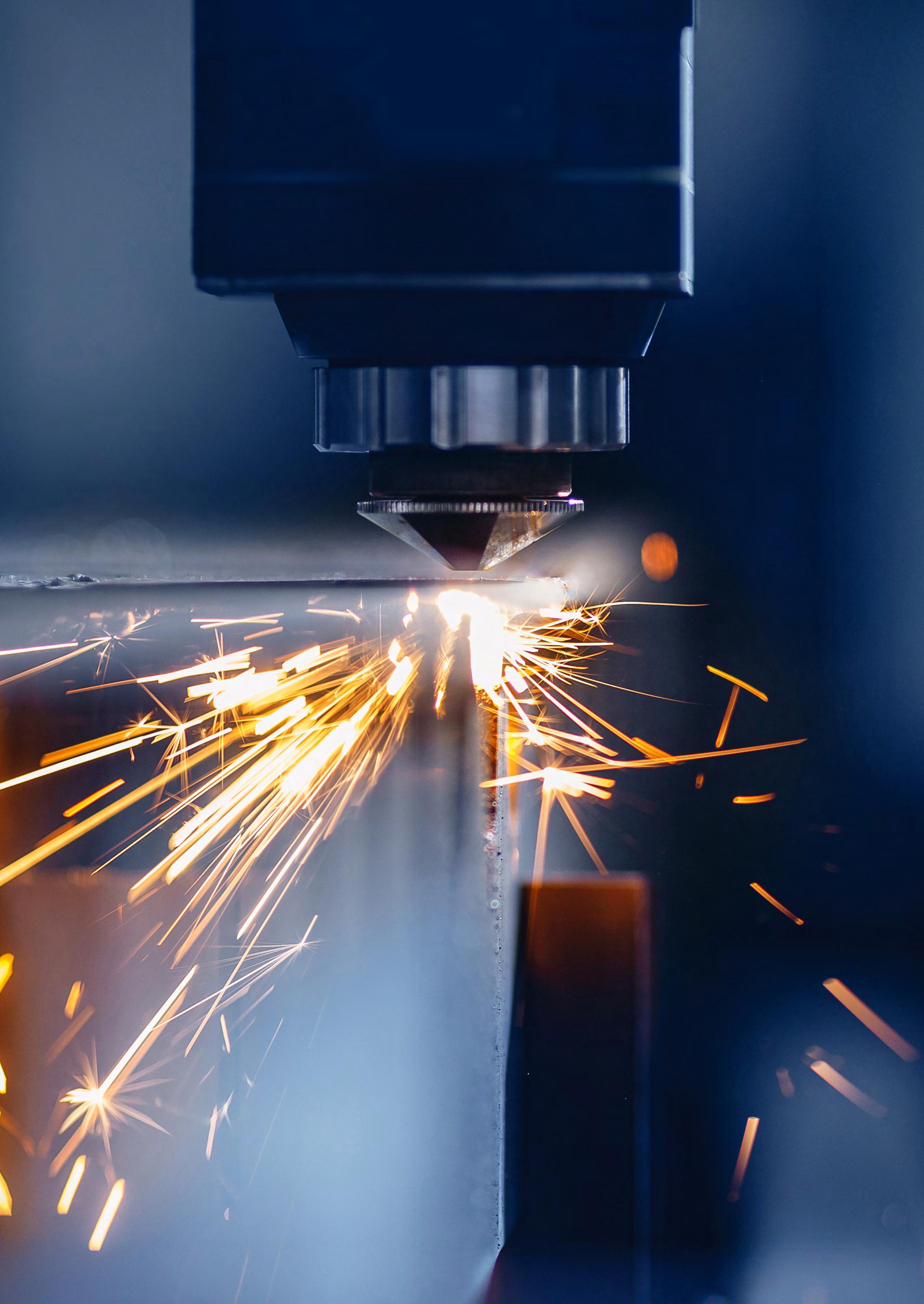