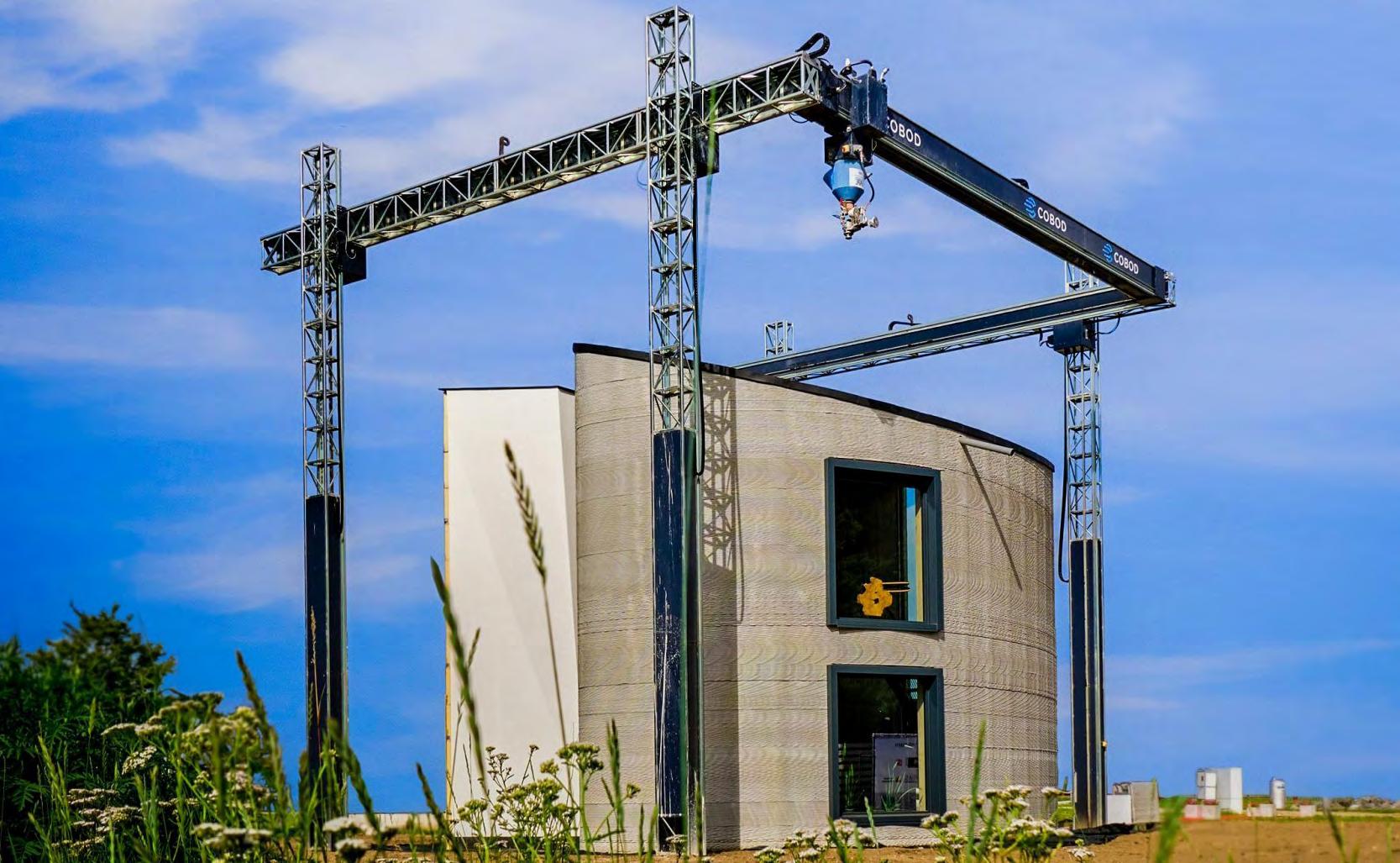
7 minute read
CONPRO
COBOD
“I have always liked new technologies and the application of it to generate new businesses. The construction industry has been labour intensive and unproductive for decades, and after some extensive research I discovered there was the potential to develop a smarter way of construction”.
And so, in 2017, Mr Lund-Nielsen founded COBOD International.
BOD: Building On Demand
Built upon a gantry principle, COBOD’s printer, the BOD2, is the result of years of continuous development, upgrades, and experience. Now, the BOD2 is the world’s best-selling 3D construction printer.
“3D construction printing enables customers to print structures faster, cheaper and with more complex shapes and forms,” explained Mr Lund-Nielsen, “we create the technology, but it’s up to the client how they apply it”.
COBOD’s BOD2 printer constructing a house Although the BOD2 is primarily used to print with concrete, customers can use whatever material suits their project, so long as its 3D printable.
“Customers generally use concrete as this is, so far, the perfect mouldable, cheap, and safe material, it’s printed as a liquid and then sets as a solid,” said Mr Lund-Nielsen, “the extruder can handle up to 10mm aggregates and can therefore print with real concrete, not just mortars”.
The beauty of the BOD2 is its unique advantages. The BOD2 is the fastest 3D construction printer available, with print speeds of up to 1m/s and it only needs to be manned by three operators.
“These features significantly reduce labour costs and optimises the efficiency of the construction site,” Mr Lund-Nielsen explained.
The printer, which is custom made size-wise to suit every client, is made using the highest quality components and implements the latest, state-of-the-art, software. This allows for the automatic construction of concrete structures of many kinds.
Feature
One of the new, taller wind turbine towers that COBOD can produce

Construction Feature

COBOD
Building global credibility
COBOD works in strategic partnership with businesses globally, with examples ranging from Siam Cement Group in Thailand and 14Trees (a joint venture between Holcim and CDC) in Africa to CEMEX in Europe, Mexico, and the US.
PERI, of Germany, has been a valuable strategic partner for COBOD since 2018. Known for its formwork equipment and scaffolding systems, PERI saw the potential for 3D construction printing to storm the industry.
“In 2018, PERI Group acquired a minority share in COBOD,” shared Mr Lund-Nielsen, “since then, our businesses have worked closely together to push the boundaries of 3D construction printing”.
In 2020, PERI realised the first 3D printed residential building in Germany, followed by the biggest European 3D printed building so far - a 380 m2, three-storey apartment block. COBOD also works with American multinational conglomerate, GE, developing game-changing tower structures for wind turbines.
“Current, traditional methods of constructing wind turbine towers limits the heights, and subsequently power, of turbine towers to 80 to 100 metres,” explained Mr Lund-Nielsen, “working in collaboration with GE and Holcim, we have developed an application to print bases directly at site, which will allow for construction of towers 150 to 200 metres tall”.
Wind turbines at this height can generate more than 33% extra power than at the current height.
“Working with these giant multinational organisations adds credibility to our offering and is fuelling our growth. We doubled our turnover in both 2019 and 2020, and then tripled it in 2021. Our strategic partnerships play a huge role in this success,” said Mr Lund-Nielsen.
COBOD now has an order sheet to the tune of €20 million.
3D printing construction project underway in Malawi, Africa
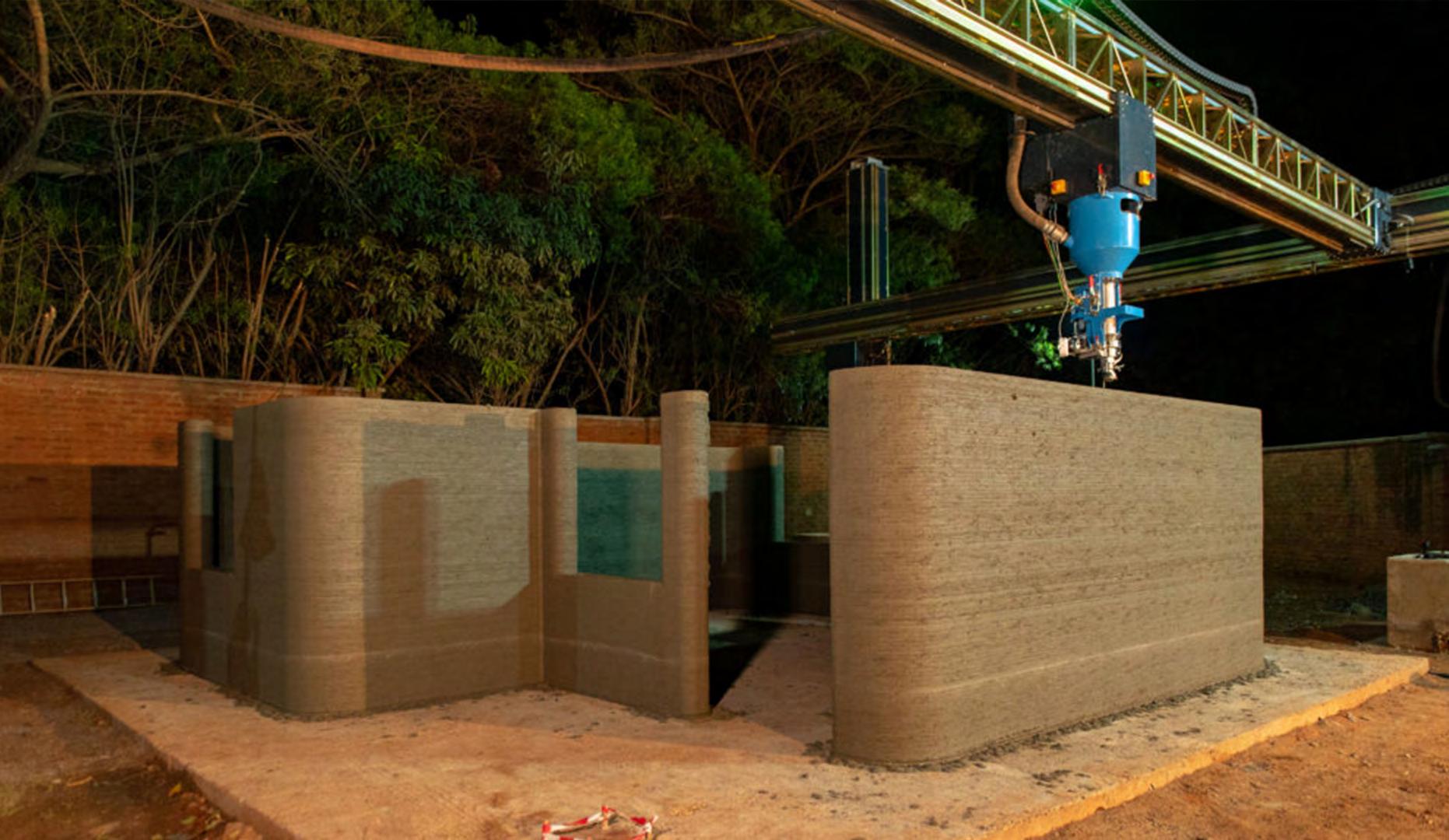
COBOD
The solution to worldwide challenges
COBOD was born from a desire by Mr Lund-Nielsen to tackle the global construction and housing crisis. The business’s research indicates that due to the rapid growth in world population, there will be a huge construction gap, including a shortage of three billion houses in the decades to come.
That, compounded with stagnating productivity due to lack of automation and therefore the cost of construction outpacing general salary increases, means that affordable housing options are hard to come by globally.
The BOD2 printing system from COBOD already has the technology to both extrude concrete and automatically reinforce it afterwards, but Mr Lund-Nielsen sees further opportunity to expand the printer’s functionality to include the ability to also insulate and paint.
Mr Lund-Nielsen also envisions that the printers will be used for more and more applications, other than low rise housing. “We see our technology enabling our partners to print multi-storey buildings, warehouses, storage tanks and even bridges,” said Mr Lund-Nielsen.
COBOD’s 3D construction printing technology reduces the cost of building structures by requiring less manpower, needing less time, and using less material.
Despite using less product, Mr Lund-Nielsen is not blind to the fact that the printer typically uses concrete made with cement, which is criticised for its CO2 output.
SMP Connect
Specially designed for use with 3D concrete printers
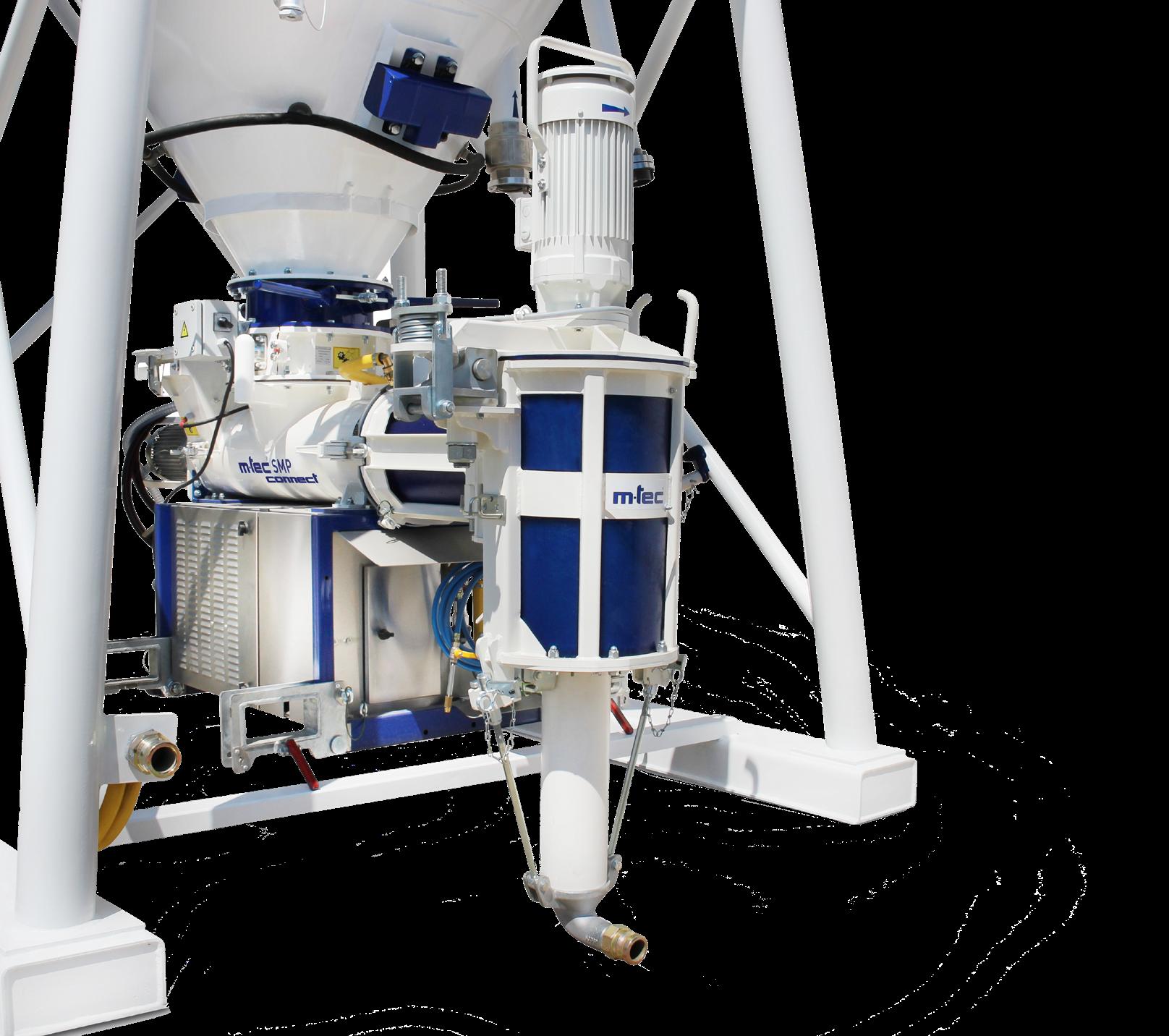
m-tec.com
Construction Feature
“Our customers want to build safe structures, and the tried and tested material for this is concrete,” said Mr Lund-Nielsen.
The CO2 emissions caused by the cement used in the concrete are two-fold - the energy used to melt the cement at 1400 degrees and the calcination of limestone. COBOD’s partners Holcim and CEMEX are working hard to find ways of making cement more sustainable.
“One method that is being explored is the inclusion of different binders, to reduce or remove the amount of limestone used, potentially halving the level of CO2 emitted,” Mr Lund-Nielsen explained.
“Another challenge we face is changing the perception of 3D printing within regulation. When building codes were written, 3D printing wasn’t foreseen. Regulators need to understand that 3D construction printing is just a tool, and the structures built with this tool are no less safe than any other structures”. Are you ready for Building 4.0? For 3DCP and other modern construction technologies?
m-tec has developed the first silo mixing pump to bring networking to the dry mortar sector. Our m-tec SMP connect, in combination with an m-tec silo, enables automated processing of dry mortar in your automation or 3DCP applications. A connection between the m-tec SMP connect, and a higher-level control system can be established via various interfaces.
There are many applications where this advanced silo mixing pump can be integrated into automation processes. With the SMP connect, processes can be implemented easily and securely via conventional interfaces as well as via future oriented OPC UA protocols. For example, the m-tec SMP connect can be integrated into all-embracing safety concepts, optimized process flows, or used for cooperation with robots.
With the SMP connect, you can take the next steps in digitalized communication. The silo mixing pump is specially designed for feeding with silo material. Via the interfaces, it is quick and easy to retrieve information from the SMP connect or to control the silo mixing pump externally, e.g., for 3-D printing tasks in conjunction with robots communicate or for industrial production, where the SMP connect is connected to other machines via the existing plant control system.
www.m-tec.com

Construction Feature
On the precipice of change
Mr Lund-Nielsen believes that COBOD has developed the first 3D construction printer suitable for the mass market and expects much more to come. “I believe we are five years into seeing continued and fast development of this technology and its usage,” shared Mr Lund-Nielsen. “We have just started automating construction and there is much more to be done in the next 20 years”
COBOD sees this development to be in line with three “mega-trends”: automation by robots, sustainability, and the shortage of skilled labour.
Mr Lund-Nielsen anticipates that COBOD will double in size within the next 18 months and plans to establish regional competence centres globally to make the business more accessible to partners and potential customers.
“Seeing is believing with our product, and so we need to enable customers to come and see what our technology can do, as well as speak to our experts,” said Mr Lund-Nielsen.
With this in mind, COBOD has already opened its first regional competence centre in Malaysia, to serve the Asian market. In July 2022 a regional competence centre will open in Florida to support North and South America. Later in the fall, a further regional competence centre will be established in Dubai for the Middle East and African markets.
www.cobod.com
COBOD
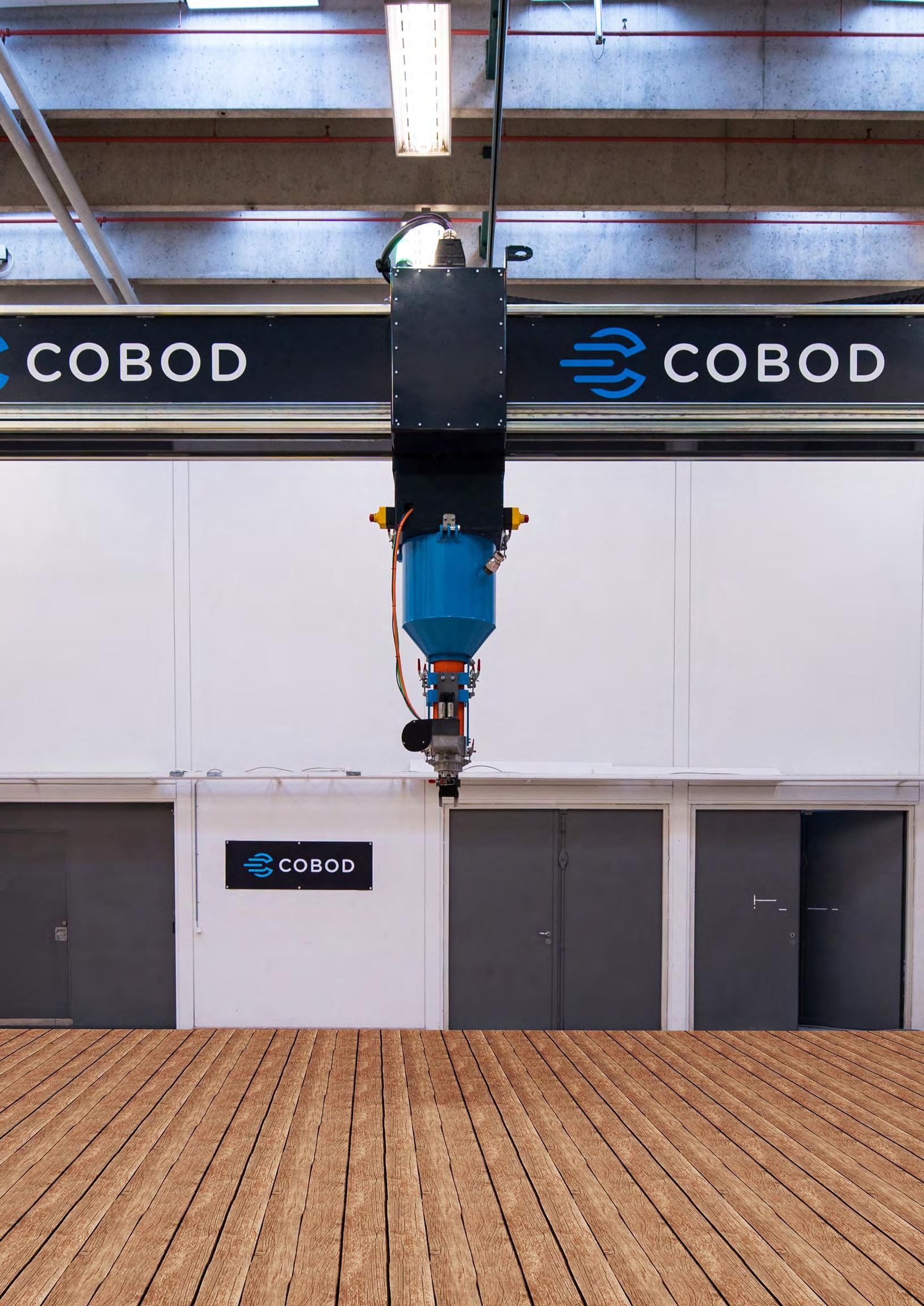