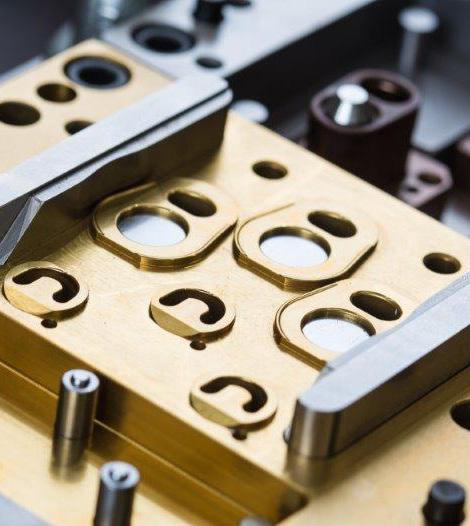
4 minute read
Machines, technology and facilities for canmakers around the world.
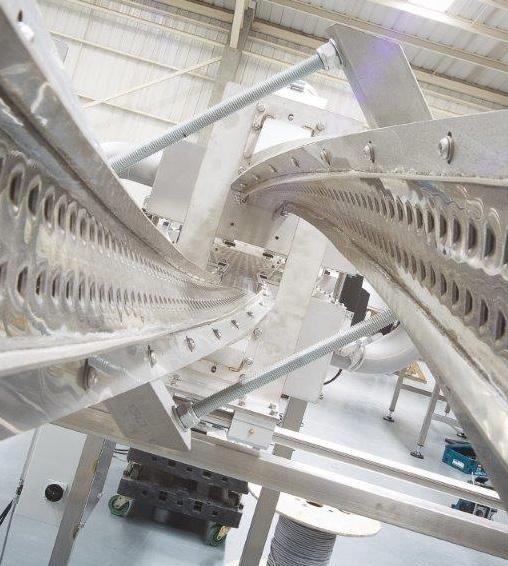
Committed to sustainable equipment and practices that help canmakers produce over 400 billion aluminium cans annually.
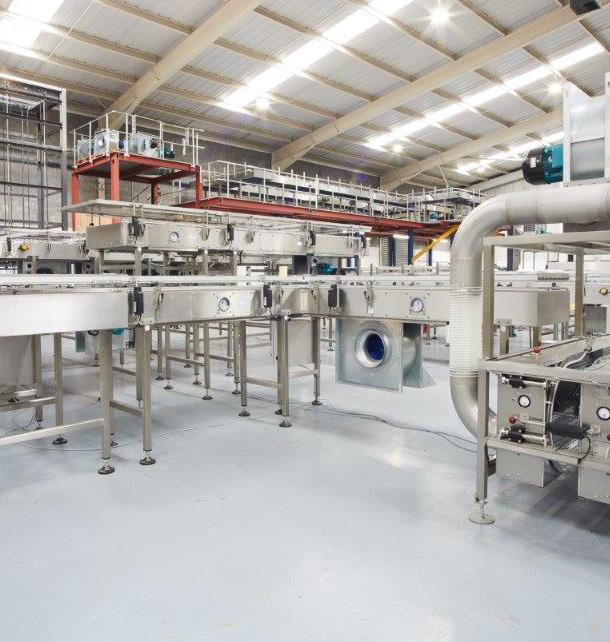


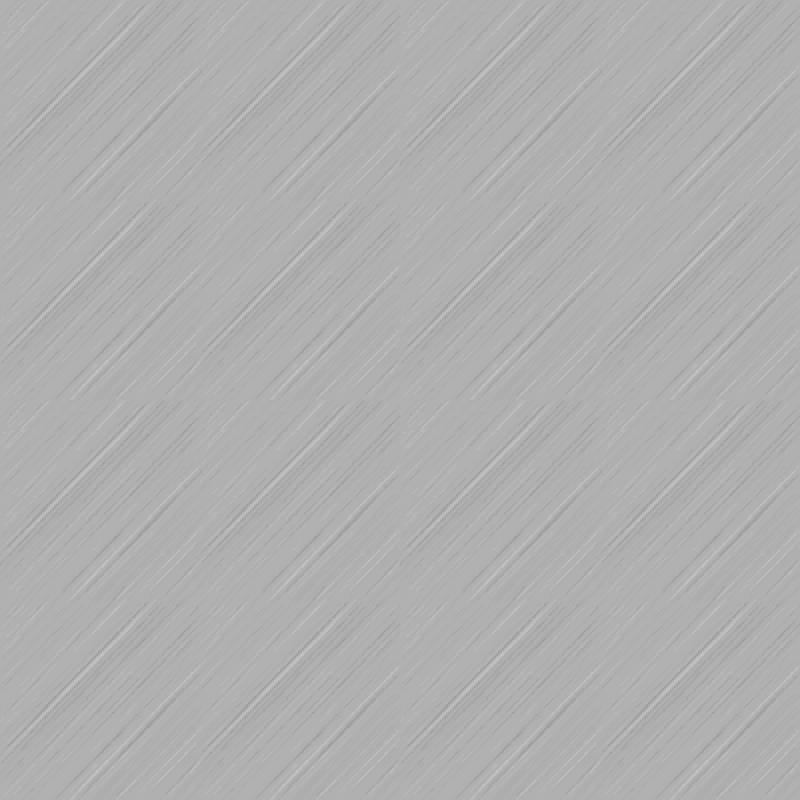
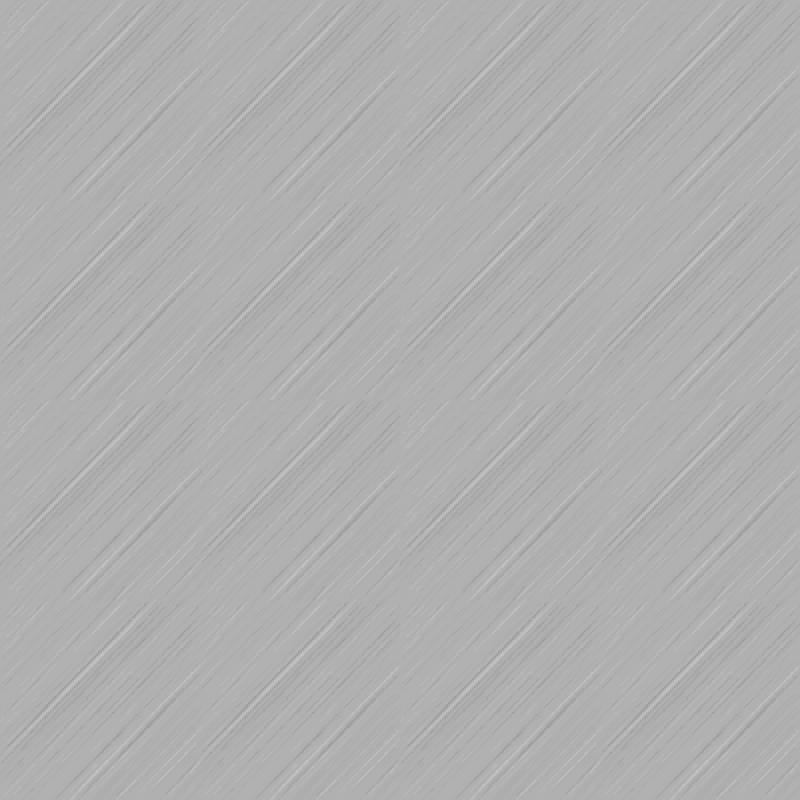
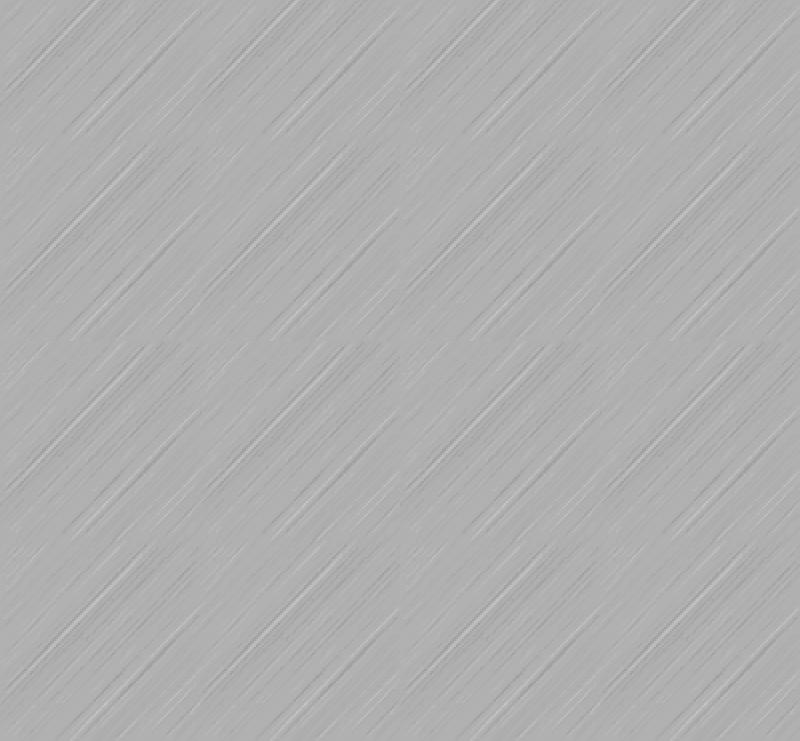
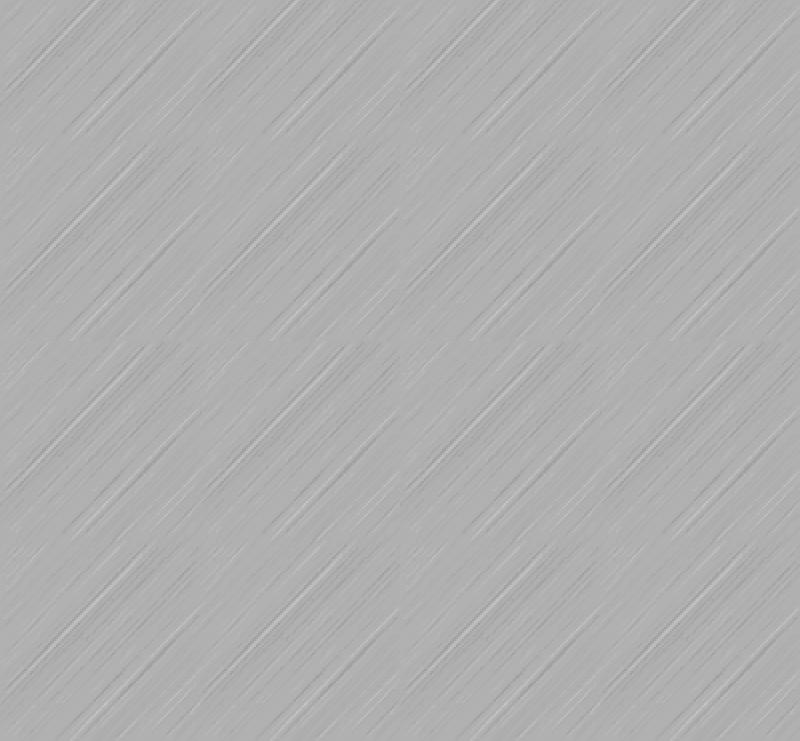
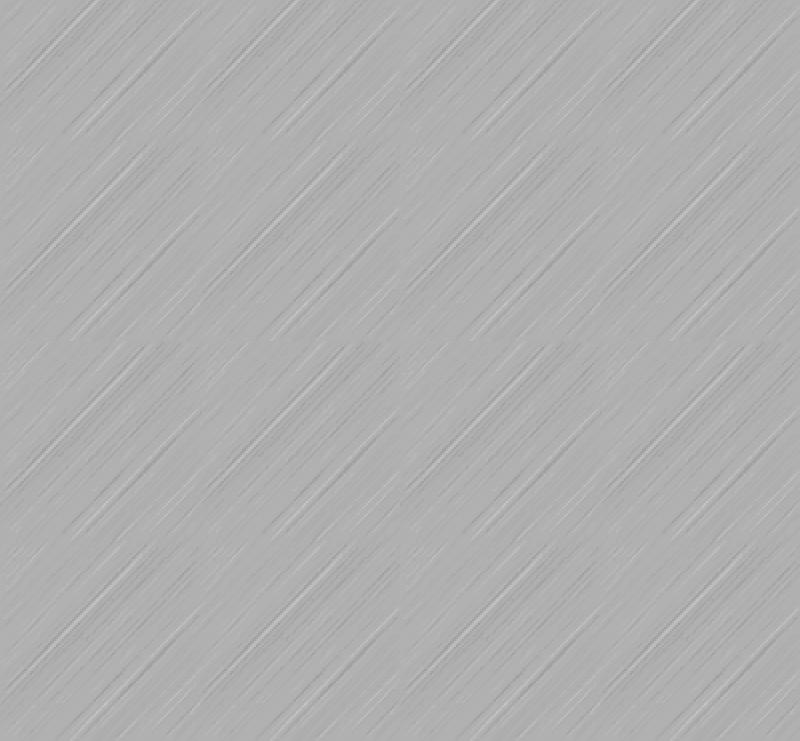
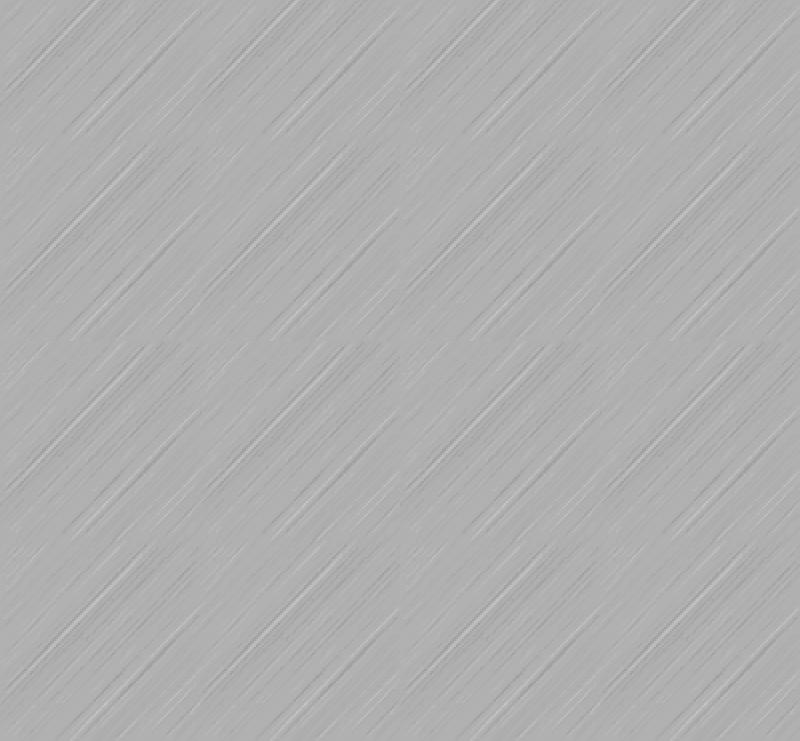
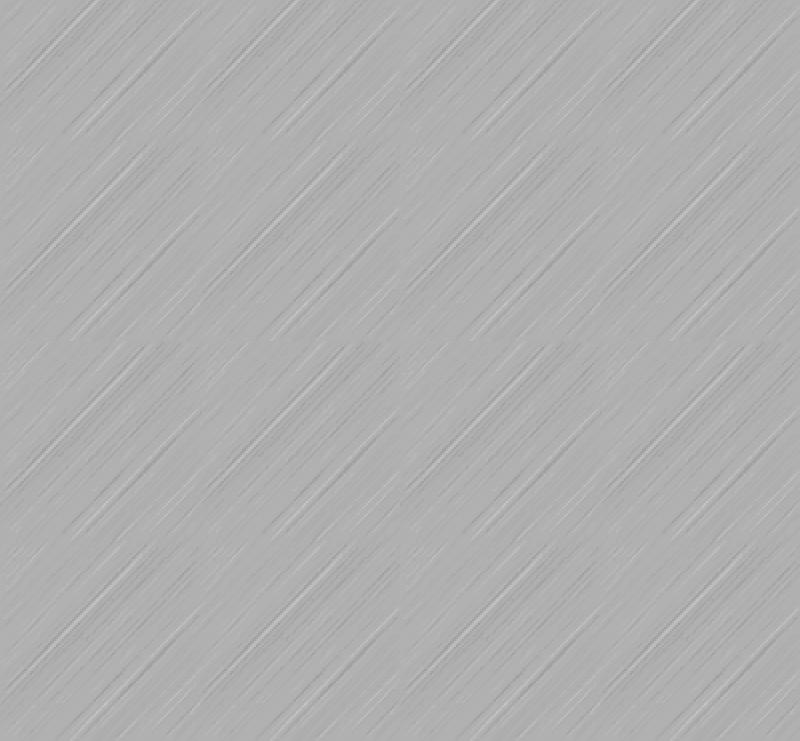
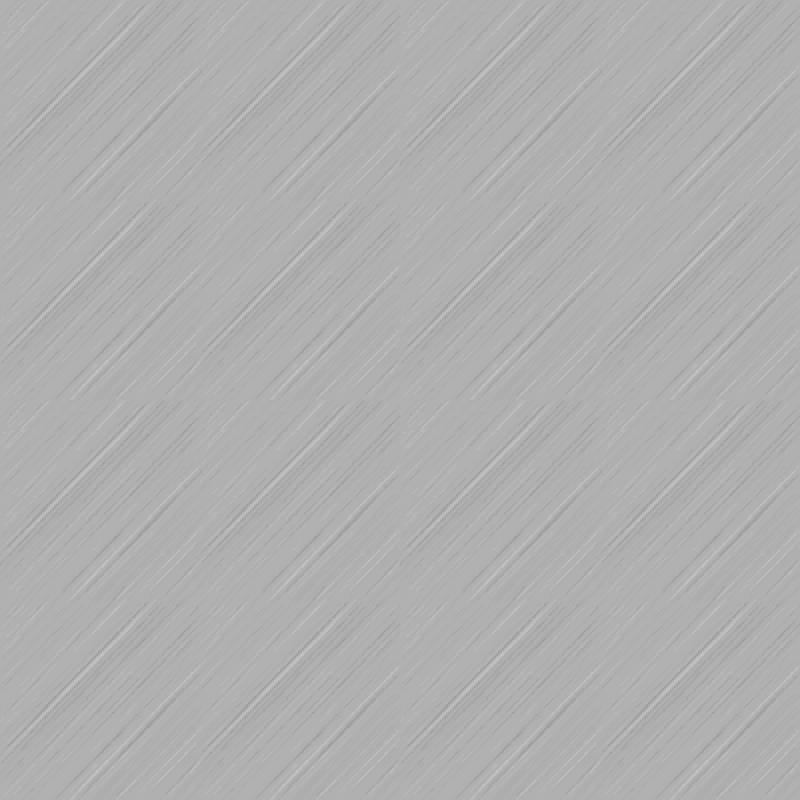
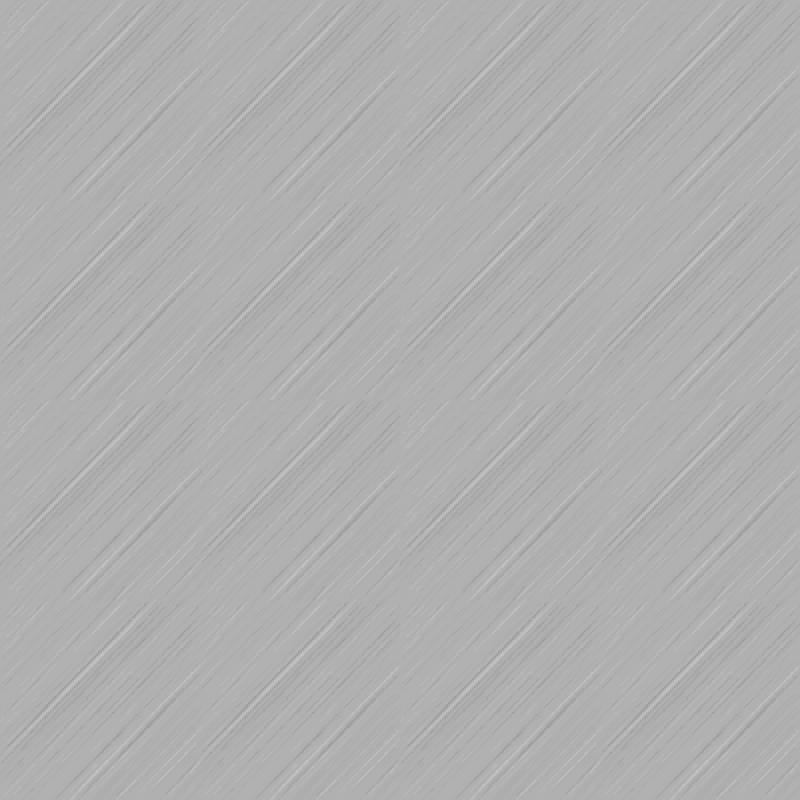
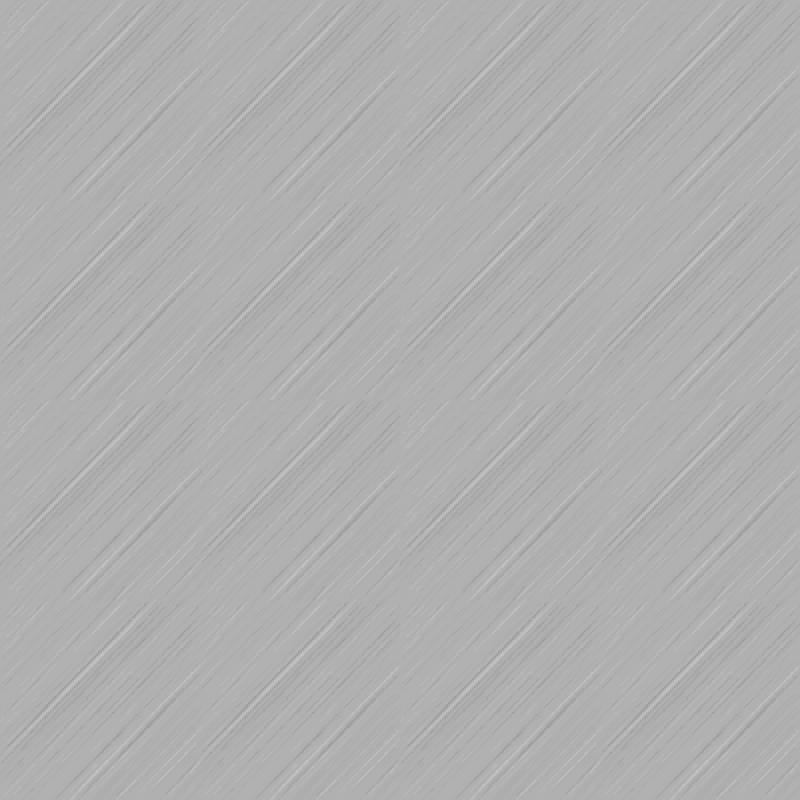



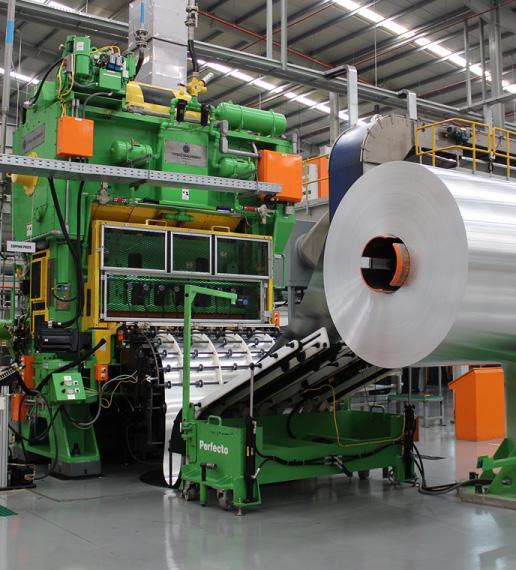
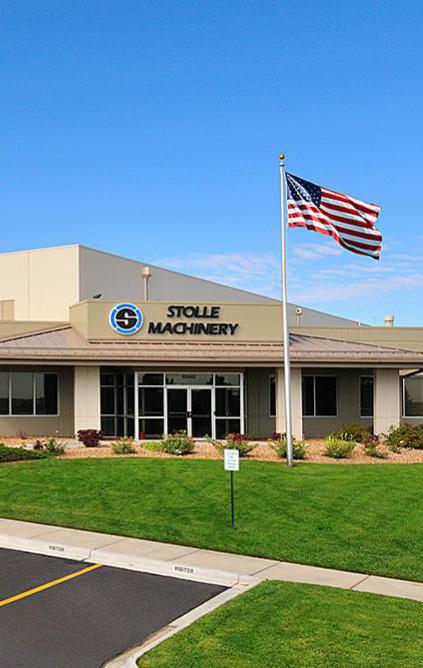
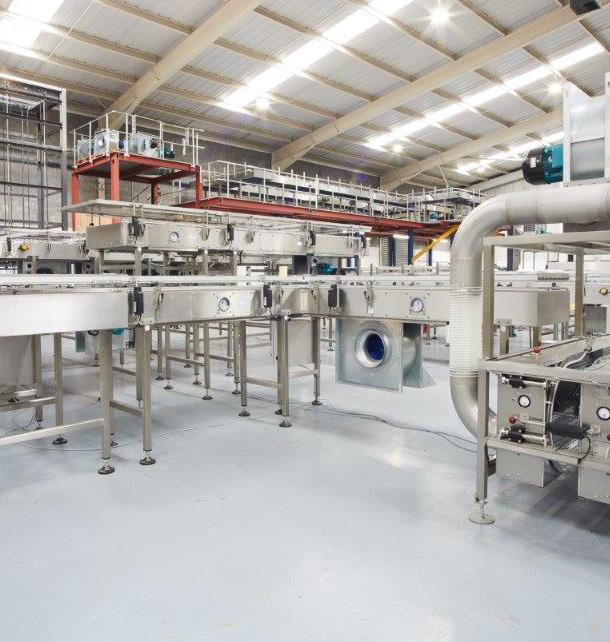
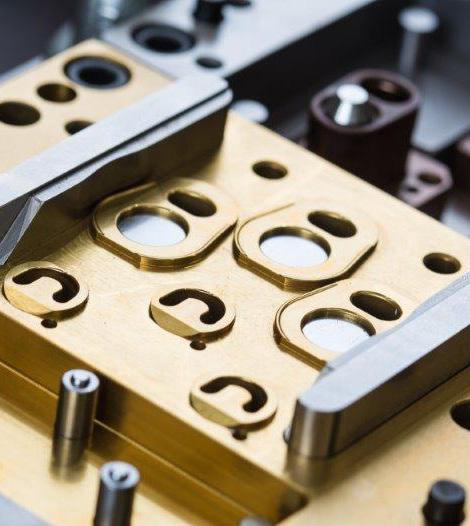
Stolle high speed machines are the backbone of canmaking operations worldwide due totheir proven productivity and reliability. Stolle provides complete solutions at any level –from individual machines, line modules, and rapid service with OEM parts, to the design,build and commissioning of a complete facility. Stolle’s technical leadership means that customers always receive equipment with the latest engineering advances and improvements. Canmakers around the world know that Stolle supports their productivity and profitability.
Stolle Machinery has a rich history that can be traced back 150 years. During this time, the companies that are part of Stolle today developed many of the technologies and processes that have become the standards of metal packaging around the world. From major names in aluminum to small family-named machining companies, Stolle is proud to recognize our legacy companies, and we look forward to continuing our tradition of innovation and growth.
As our “wave of innovation” has indicated for years, Stolle is committed to advancing metal packaging through “A constant flow of sustainable innovations and technology that will benefit customers.” From some of the strongest and most metal-efficient tab designs available, to brilliant new equipment upgrades, to revolutionary new equipment poised to impact the next generation of can making, Stolle continues to make significant investments of personnel and funding to R&D in every area of can making. Stolle’s global technical centers are dedicated facilities developing the advanced technology that future can makers will come to rely on while producing the sustainable machinery features that today’s customers expect.
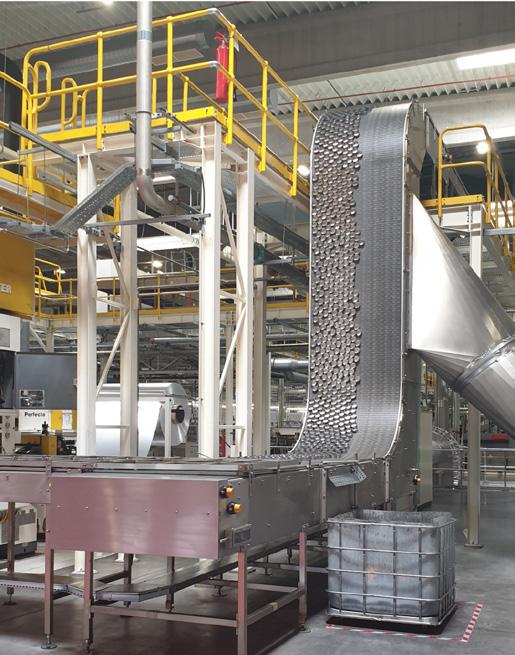
The Engineering Business Segment of Toyo Group represents a component of the company that offers leading technologies, outstanding market positions and business platforms that stress environmental and social responsibility. Consumer packaging is a cornerstone of human happiness, and the Toyo companies lead in the supply of machinery and systems that support the global packaging industry. By maximizing our share of the equipment and processes that supply packaging we are well positioned for long term success through both the opportunity to supply product to meet the rapidly growing packaging segment but also provide continual support for the legacy production systems. The forecast for global packaging is very positive with all business models pointing to continued growth for a decade or more. A global and diverse workforce as well as aggressive efforts in the areas of product and process sustainability ensure that the social and environmental goals that are set out are treated with equal importance as the business and financial goals. Top management aspires to see that the Engineering Business Segment remains in a leadership position both in terms of technology and social responsibility as we all strive to support the next generation of consumers.
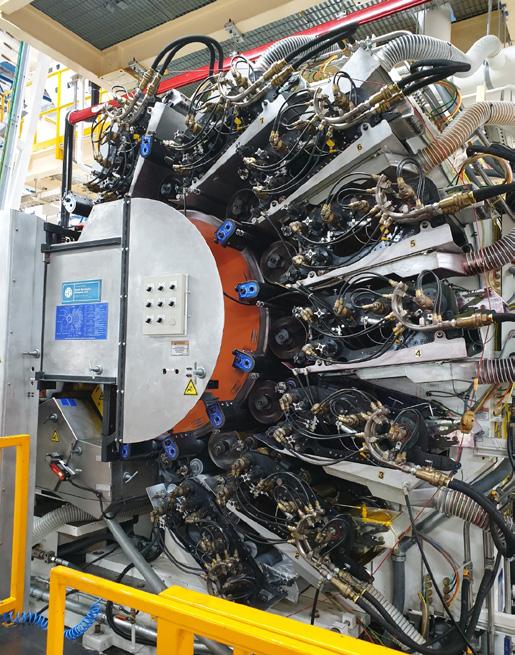
Stolle Machinery’s relationship with Hell Energy and Quality Pack started back in 2015 when the initial plans were laid down for their first can and end manufacturing facility, this was supported with equipment sourced from from our global facilities and the project per se was executed from our Systems division based in the United Kingdom. Working closely together with the Hell Energy Team on the ground in Hungary the plant soon started to evolve and over the following nine months the project was completed. In the years to follow the second line and the end line expansion took place increasing the capacity to over two billion.
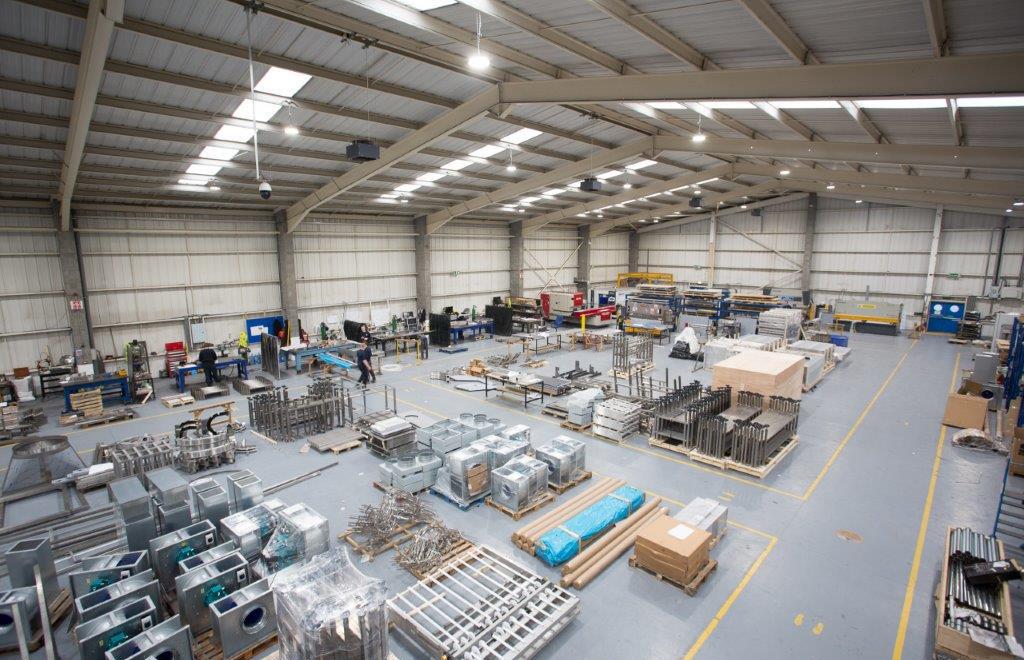
Currently we are directly engaged in the third line which will then take the facility over the three billion marker. Over the years that we have been working together and as mentioned earlier Stolle has invested in further technology to enhance its ability to support the business.
With the exception of the palletiser we are able to provide all of the equipment for the can line, our washer uses 25% of the water of a conventional washer and our oven technology has considerably better energy efficiency. Stolle’s end modules are renowned for their robust design and reliability. www.stollemachinery.com aluminium beverage can factory. The business is also the first in the world to used aluminium that is certified with at least 75% recycled content.
SPDS our Stolle Product Delivery System is the foundation underpinning our commitment to continuous improvement and to the consistent meeting of evolving customer requirements. The company has invested heavily in all divisions as well as in new technology. We pay particular attention to the needs of the industry and understand the necessity for incremental development. To that end our SATO ( Stolle Advanced Technology Operations ) team has been bolstered with a new research and development center in Centennial US to ensure that fresh ideas and creative product development continue well into the future. Quality Pack have also embraced new technology at every opportunity and we continue to work closely together to that end.
As their business has grown it has been a pleasure to be alongside them providing the equipment and systems services to support their ever expanding portfolio.
The 42,000 square foot factory produces 3 billion 250 ml beverage cans and can lids per year using Aluminium “this is considered a really beneficial raw material since it is 100 percent recyclable, infinitely,” shared Péter.
The product is lightweight, reducing transport emissions, and, when recycled, can be back on the shelves within two months.
“The aluminium cans have helped the business to reduce its C02 emissions by 60%, we believe it is the packaging of the future,” explained Péter.

Now, over 95% of Hell Energy’s products come in aluminium cans, with the company aiming to increase this above 99% by 2025.
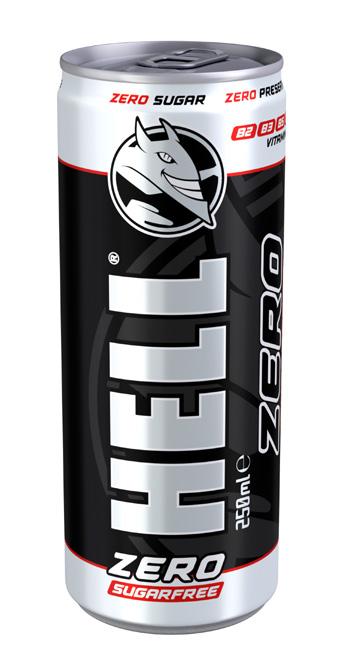
“Our vertically integrated factory complex means that Hell Energy can declare that it manufactures its products entirely by itself without the use of an external source,” he continued.
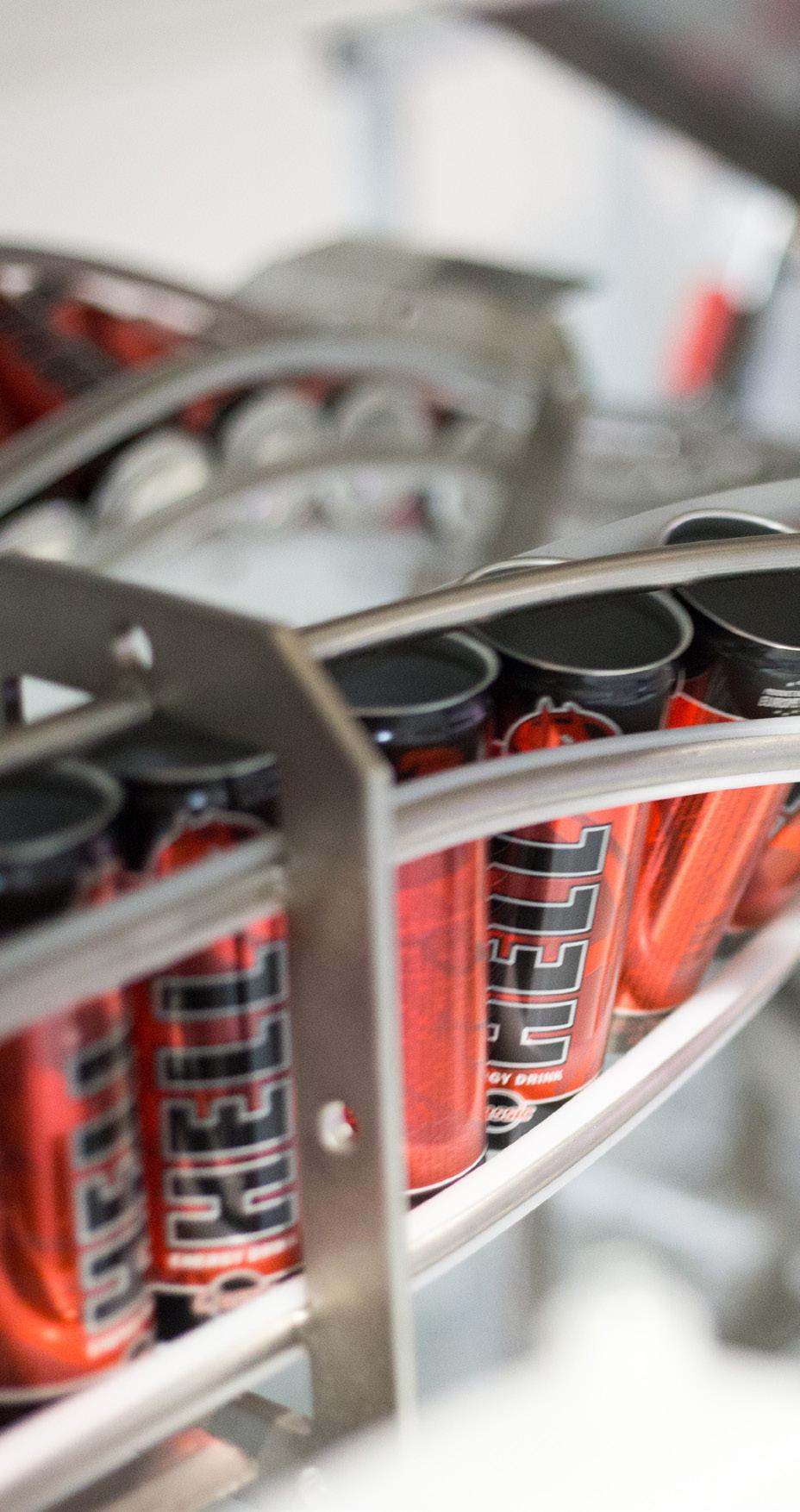
International Stardom
“Hell Energy is a family business which has been founded on providing high quality at affordable prices,” explained Péter.
In the last 17 years the brand has formed significant advertising partnerships to boost its global marketing, including with the AT&T Williams Formula 1 team in 2009, and a long standing relationship with Hollywood superstar Bruce Willis.
A market leader in 10 countries including Hungary, Romania, Greece, and most recently India, Hell Energy has ambitious growth plans.
“Our plan is to increase the availability of our products in UK Key Account chains, and further increase our market share,” said Péter, “we’ll also seek out further opportunities in Western Europe”.
Hell Energy’s biggest project within the next 12 months is building its new production facility, which will double its capacity to 78,000 square metres. In addition, it will look to secure its aluminium supplier contract for the next three years.

And, within the next three to five years the business aims to be a leader in any geographic market it reaches.
“We are in very good shape for the future,” shared Péter.
www.hellenergy.com
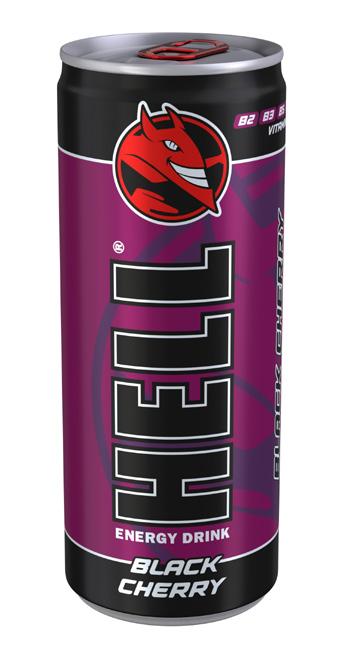
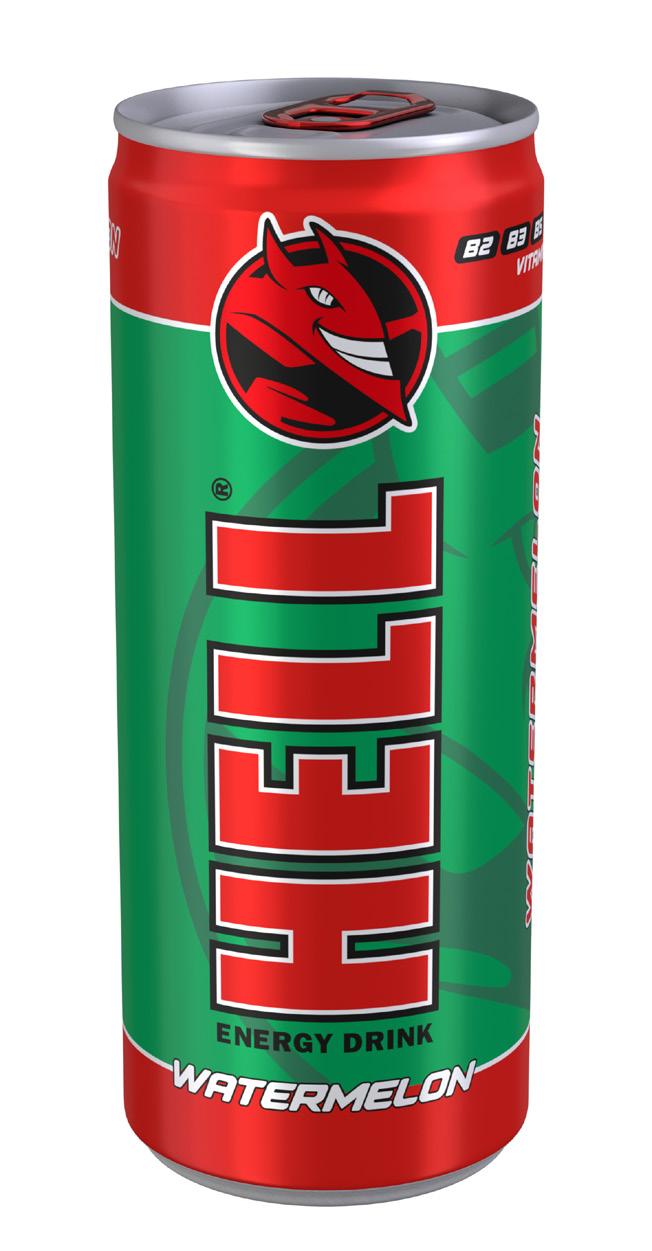