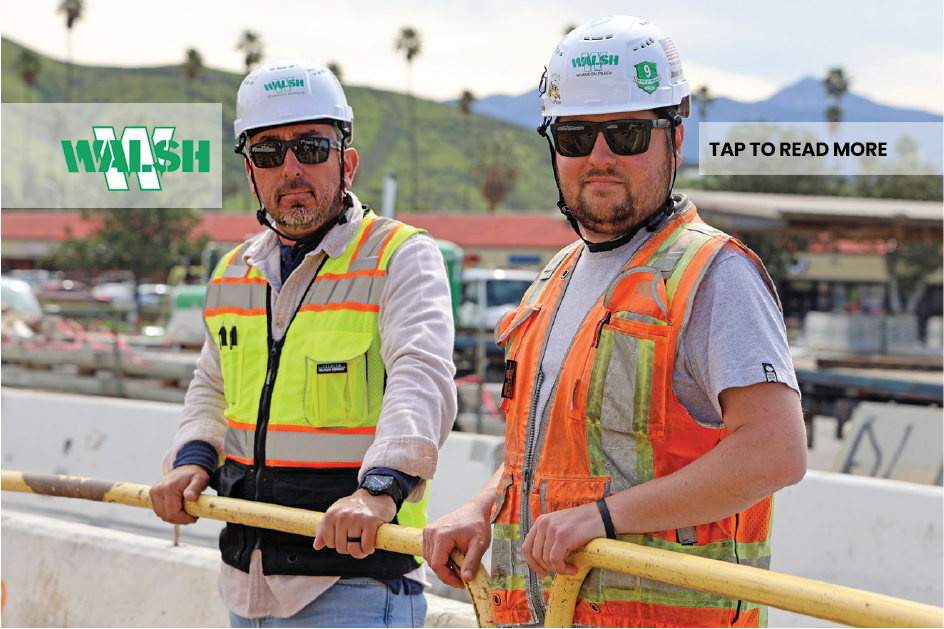
9 minute read
WALSH CONSTRUCTION COMPANY II, LLC Continues Progress on McKinley Grade Separation Project for the City of Corona
By Brian Hoover, Senior Editor / Photos contributed by: Walsh Construction and CMS, LLC.
Getting caught at a train crossing is frustrating. Time feels like it’s standing still as the barriers block the way. The wait seems endless, and irritation builds with each passing railcar. It’s a reminder of the powerlessness when faced with unexpected delays. Visitors and residents of Corona have experienced this frustration firsthand at one time or another when they approached the infamous McKinley Street crossing. Statistics have shown that traffic has been delayed in this area by more than two and a half hours each day. That number was calculated to increase to more than four hours a day by 2035.
To help mitigate the traffic issues and general anxiety created by the delays at the McKinley Street crossing, the City of Corona designed and approved a plan to build a suspension bridge over the BNSF railroad tracks and Arlington Channel that will serve to relieve the congestion in the area. The $60 million construction contract for the McKinley Street Grade Separation Project was awarded to Walsh Construction Company II, LLC (a part of The Walsh Group) headquartered in Chicago.
Walsh Construction Company II, LLC (Walsh Construction) began working on the McKinley Street Grade Separation Project in early 2022 and is expected to have everything wrapped up by the end of 2024. As a part of this project, the new McKinley Street Bridge is being constructed to provide a “grade separation” solution to improve traffic flows where McKinley Street crosses a busy railway line, a canal, and another road, all at ground level. McKinley Grade Separation construction will extend from the SR-91 interchange on the north side to Magnolia Avenue on the south side. The project will provide a new four-lane overhead grade separation at the BNSF Railway double tracks in the area where McKinley Street intersects Sampson Avenue.
Brandon Parry is Walsh Construction’s Assistant Project Manager overseeing the McKinley

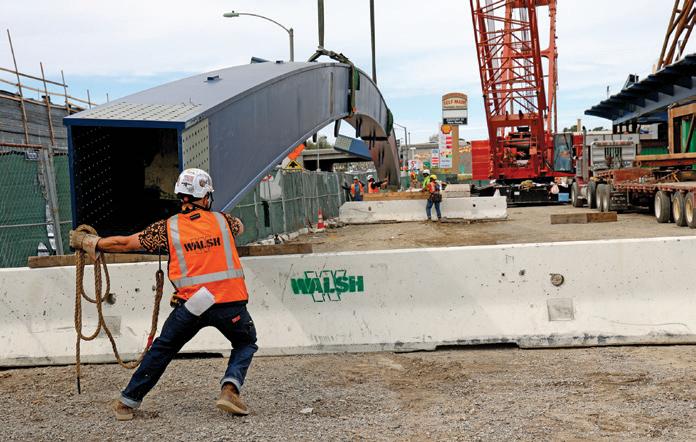
Grade Separation Project. “This is a challenging project on several fronts, starting with the fact that it is located within an extremely tight footprint and in close proximity to numerous private properties,” says Parry. “Then, there is all of the grade changes as we elevate the roadway and tie it into the existing grade, all while keeping traffic flowing smoothly.”
The Bridge
In addition to relieving congestion, the new bridge will also improve mobility and safety for both motorists and pedestrians, as well as improving air quality and noise. Walsh Construction is selfperforming more than half of the overall project, including all of the concrete construction work and bridge erection. The new McKinley Street Bridge will incorporate an amazing 1.8 million pounds of steel and is being erected in a staging area in a yard adjacent to the installation site. A 220-ton Manitowoc 2250 crawler crane is onsite for all of the heavy lifts, including 80-foot-long tie girders. With a span of 286 feet and a width of around 80 feet, the new bridge is being put together in segments. Once complete, it will be moved and installed utilizing a combination of self-propelled modular transporters, hydraulic jacks, lashings, and a rolling jack system.
Above: Mr. Crane’s 220-ton Manitowoc 2250 crawler crane unloads one of six bridge arch ribs on the McKinley Grade Separation Project in Corona.
Left: The 220-ton Manitowoc 2250 crawler crane unloading one of the arch ribs onto temporary storage.
Fernando Barraza is the Senior Superintendent for Walsh Construction on the McKinley Grade Separation Project. “Les Hancock is doing a great job as our superintendent overseeing the erection of the bridge structure. This is an arch bridge with cable hangers that will undergo a couple of stressing sequences,” explains Barraza. “The first stressing sequence will be prior to the move and once in place, a secondary stressing sequence will happen.”

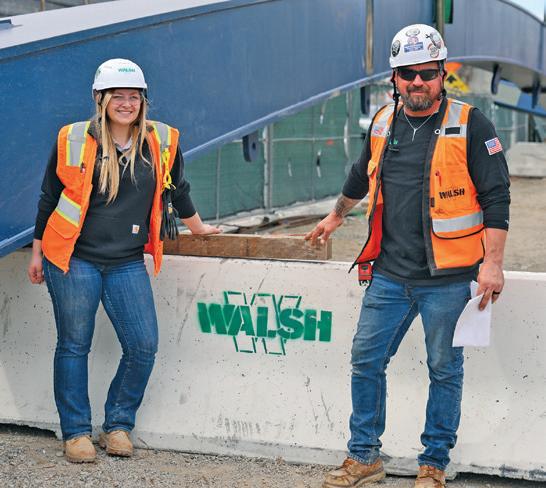
Building Up the Roadway
Parry explains that everything leading into the bridge is being elevated and tied into the existing grade over a 1,900 linear foot stretch of roadway. “The entire area is being built up to become a full roadway structural section that will raise the driving surface of McKinley Street to 30 feet at its highest point,” says Parry. “We are utilizing around 65,000 cubic yards of lightweight cellular concrete fill to build up the roadway section, in addition to importing 5,000 to 10,000 cubic yards of native fill. The final asphalt paving of the roadway section is being performed by our subcontractor, All American Asphalt.”
The project will also add a new loop road across from the SR-91 westbound ramps to connect McKinley Street to Sampson Avenue. The eastbound off-ramp, eastbound loop on-ramp, and the eastbound slip on-ramp at the SR-91 freeway will also be modified. Additionally, nine walls will be constructed to include MSE and Type 5 Caltrans walls. In addition to the construction of 3.75 miles of vehicle lanes, there will be 0.75 miles of sidewalk and five signalized intersections.
Relocation of Existing Utilities
Another segment of the project includes relocating existing water system infrastructure (water, sewage, drainage) within McKinley Street, Estelle Street, and Magnolia Avenue to make room for the new grade separation. The waterline relocation will replace approximately 770 linear feet of aging water pipeline along McKinley Street between SR-91 and Sampson. When complete, this segment of the work will replace 14 water service connections and backflows, three fire services and backflows, and three new fire hydrants after abandoning four existing fire hydrants. “We self-performed the installation of just over 400 feet of new HDPE pipe. All of the pipe was first assembled above ground and

parallel to the existing line. The HDPE was electrofused by our subcontractor, Core & Main, before being slid back into place and tied back in on the upstream side where we installed a new manhole,” says Barraza. “We had manhole 1 just to the east and at an angle to manhole 2. We utilized a temporary bypass to keep the existing sewage flowing while we worked on the new siphon structure. When everything is complete, we will switch everything over to the new line.”
Slide Rail System Protects 22-FootDeep Trench During Replacement of Sewer Siphon Structure
According to Barraza, a portion of the contract was for Walsh Construction to reconstruct the existing sewer siphon structure. They used their Case 110,000 lb. excavator to dig the 22-foot-deep pit and after placing the slide rail system, they got to work overexcavating three feet and structurally backfilling the area. “After the over-



“Committed to Safety & Service”
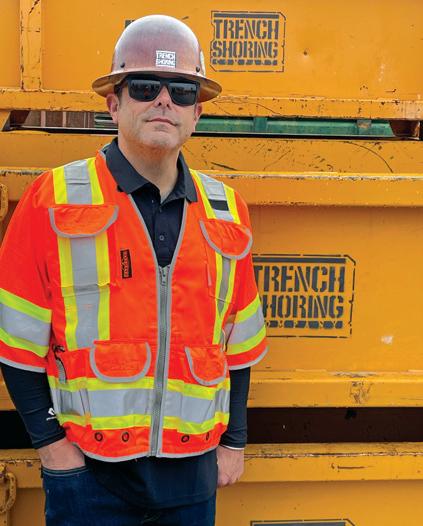
PROVIDED TO WALSH CONSTRUCTION COMPANY II, LLC
FROM TRENCH SHORING COMPANY
• SBH Slide Rail System
• (50) Trench Boxes
From 8’ x 8’ to 10’ x 24’
• Manhole Boxes
8’ x 8’ and 10’ x 10’
4’, 6’ and 8’ high
• Over 100 Steel Crossing Plates
From 4’ x 10’ to 8’ x 20’
• Aluminum Hydraulic Shoring
From 5’ to 18’ in depth
• Pipe plugs excavation and backfill, we installed the required six-inch rat slab, along with a 3-foot concrete foundation for the actual siphon structure,” explains Barraza. stamped engineering designs that help ensure that we go with the proper shoring systems and install them safely and properly.”
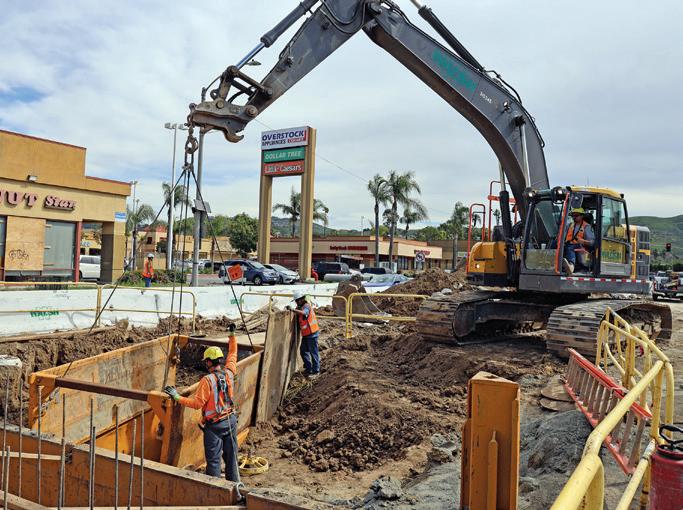
However, before Walsh Construction could begin installation of the new sewer siphon, they had to first demo the old, existing siphon structure. To accomplish this task, Walsh Construction made the call to Trench Shoring Company to rent the necessary slide rail system to support the 22-foot-deep, 27-foot-wide excavation. “We rented the slide rail system from Trench Shoring Company and their certified shoring professionals supported our installation efforts. This included three tiers of shields,” says Barraza. “I always enjoy working with Josh Frakes and everyone from Trench Shoring Company. They are the experts who can provide site specific P.E.
Parry has also worked with Trench Shoring Company for the better part of a decade. “ We can count on Trench Shoring Company to have what we need with quick and reliable delivery and service. In addition to the slide rail system, we also rented trench shields for the runs between manhole 1, 2 and 3,” says Parry. “Josh Frakes has been our representative for the past few years and he has done an excellent job serving our shoring needs.”
Building bridges over railroad tracks to facilitate traffic flow is a pragmatic solution that enhances both safety and efficiency. By elevating the roadway, the need for level crossings is eliminated, reducing the risk of accidents and delays caused by trains passing through. Such infrastructure investments not only prioritize public safety but also contribute to smoother traffic operations, benefiting commuters, businesses, and overall transportation networks.
Founded in 1898, The Walsh Group is a fourth-generation family-owned business providing design, build, finance, and operation services for a wide variety of construction projects. The company is consistently listed among the largest contractors in the United States, and operates out of 21 strategically located regional offices, including a Corona office. The Walsh Group’s portfolio of work stretches across the building, water and transportation markets, and the company is among the largest bridge, highway, transit and airport contractors in America. For more information, please visit www.walshgroup.com. Cc