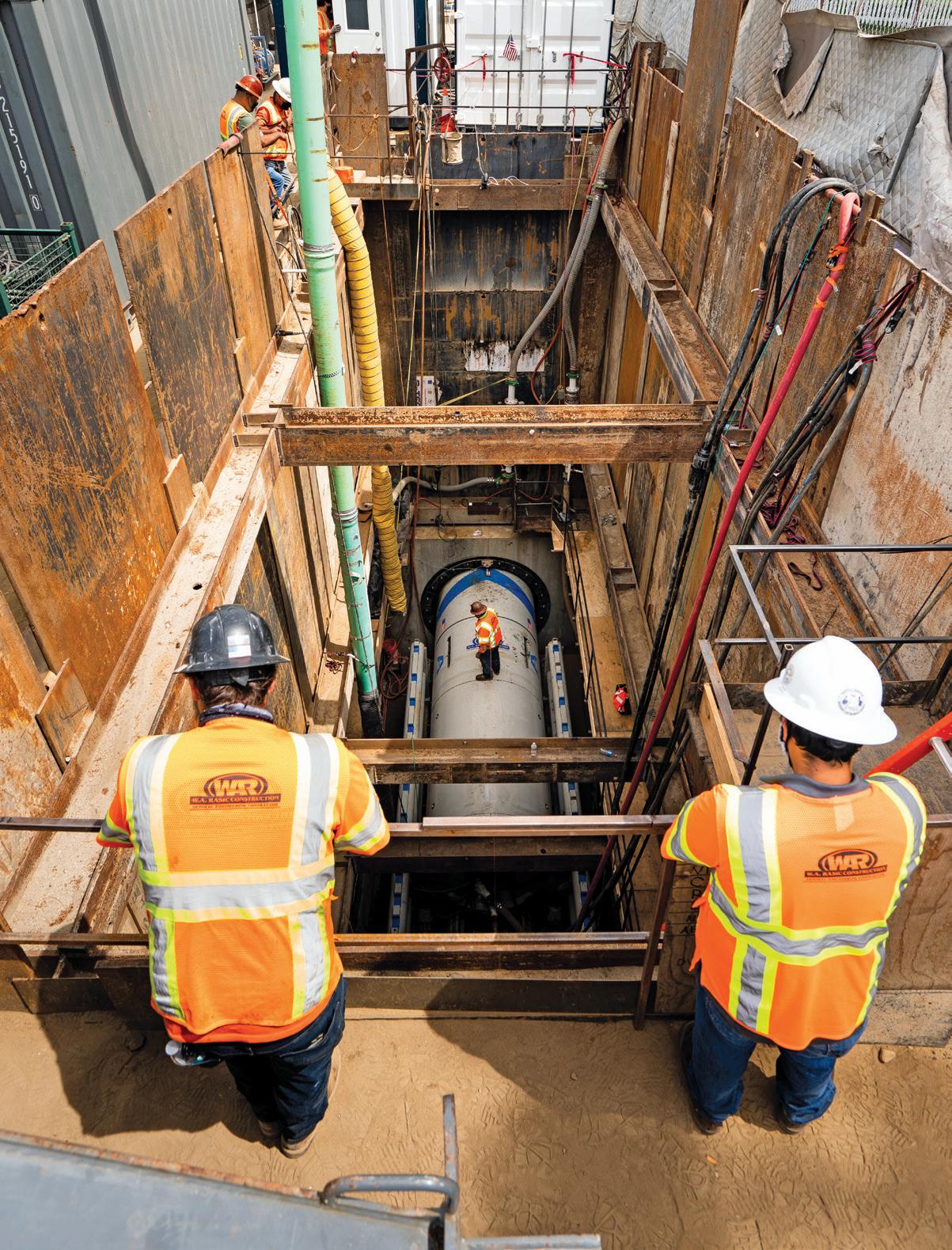
8 minute read
W.A. Rasic Construction

Utilizes Microtunneling Boring Machine Along with Open-Cut Trench Process on City Trunk Line South-Unit 3 Project
By Brian Hoover, Editor
W. A. Rasic Construction has been constructing major infrastructure projects throughout the Western United States for more than 40 years. From gas a nd oil projects and dry utilities, to the $90 million River Supply Conduit Improvement Project, W. A. Rasic delivers safely, efficiently and sustainably.
The Los Angeles Department of Water and Power (LADWP) is the nation’s largest municipal utility, serving an average of 438 million gallons of water per day to Los Angeles residents and businesses. For more than 100 years, the Los Angeles Department of Water and Power (LADWP) has provided the City of Los Angeles with reliable water and power service in a cost-effective and environmentally responsible manner. LADWP has a localized network of 6,730 miles of water mainline (20-inches or less in diameter) citywide serving residents and fire hydrants. There are another 550 miles of trunk lines citywide that deliver water between tanks and reservoirs to smaller water mains. The Water Infrastructure Plan (WIP) evaluates these lines utilizing an Asset Management Program (AM) to balance the long-term costs of mainlines, trunklines and other facilities. The LADWP, therefore, manages a corresponding portfolio of capital projects to maintain and expand the system. The utility’s Water Engineering and Technical Services (WETS) Division uses its Capital Improvement Program Management System (CIPMS) to oversee and manage a ten-year capital water system program currently consisting of over 200 projects with a budget of $6.5 billion.
W. A. Rasic Construction (W. A. Rasic) was awarded the $43,315,000 City Trunk Line South – Unit 3 (CTLS-3) contract and given notice to proceed on August 26, 2019. The CTLS-3 project is scheduled for 1,111 days, which marks the completion date in September 2022. As part of LADWP’s Capital Improvement Program, the CTLS-3 project will replace a 102-year-old water pipeline in North Hollywood that runs along Whitsett Ave. from Vanowen St. to Magnolia Blvd. W. A. Rasic is utilizing open trench and pipe jacking construction to install 5,357 linear feet of 60-inch diameter welded steel pipeline.

City Trunk Line South-Unit 3 project jacking pit with Akkermann SL82P microtunneling boring machine hard at work.
Once complete, the CTLS – Unit 3 Project will comprise approximately 25% of the City Trunk Line South system that will connect the Los Angeles Aqueduct Filtration Plant to the Franklin Reservoir. Construction will rotate among the work areas to minimize traffic impacts along Whitsett Avenue. The project will move in a linear fashion, utilizing 1,171-feet of open-cut and 4,186-feet of pipe jacking construction methodology. CTLS-3 is the third in six units of the overall CTLS that will eventually replace approximately 42,000-feet of 51-inch to 72-inch diameter riveted steel city trunk line from the intersection of Canterbury Ave. and Nagle Ave. to Franklin Tunnel near Coldwater Canyon, south of Ventura Boulevard.
Jeremy Juarez is the division manager for W. A. Rasic and he says that it is important to note the significant amount of time and resources it takes to get a job like this started. “Numerous documents have to be processed and approved before any earth can be moved or pipe placed in the ground,” says Juarez. “We went to work right after hearing that we were awarded the job. This included the entire submittal process for the approved use of the Akkerman microtunnel boring machine (MTBM) by both the LADWP and Bureau of Engineering (BOE), as well as other agencies. We also had to get approval for the 60-inch steel pipe, the 72-inch casing, as well as the traffic control plan phasing, which is another complicated process.”
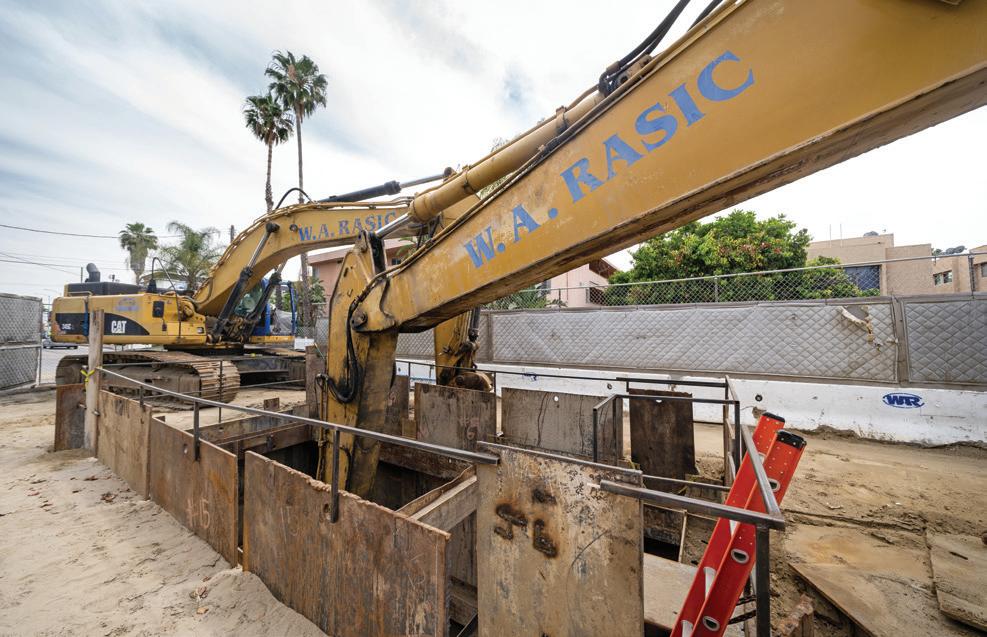
W. A. Rasic excavating one of the 40-foot deep, 40-foot long and 14-foot wide jacking pits on the City Trunk Line South-Unit 3 project in Los Angeles.

Once the approval process of numerous submittals was complete, W. A. Rasic began implementing their traffic control plan, while also installing extensometers and inclinometers to measure displacement and movements around the tunneling area. Next, they set up their survey and began removing any utility conflicts within the initial jacking pit area. “This is a five-tunnel project with jacking and receiving pits, as well as open-cut trenching,” says Juarez. “Each jacking pit is approximately 33 to 45 feet deep, 40-feet long and 14 feet wide, and requires several months to construct prior to the launch of the TBM.” Juarez clarifies that the jacking pit itself is much more than just a hole in the ground. Preparing the pit requires a great deal of engineered shoring, including installing soldier beams, plates, struts and walers. “To properly support the MTBM process, W. A. Rasic pours a 1-foot thick concrete floor, on grade, that is utilized to negate any deflection that may be caused by the positive active pressures acting at the bottom of the shoring system. Further, the slab is there to assist in mitigating any groundwater infiltration. It also helps to negate any soil conditioning material such as bentonite and slurry from infiltrating the pit as the MTBM egresses into the native soil.”
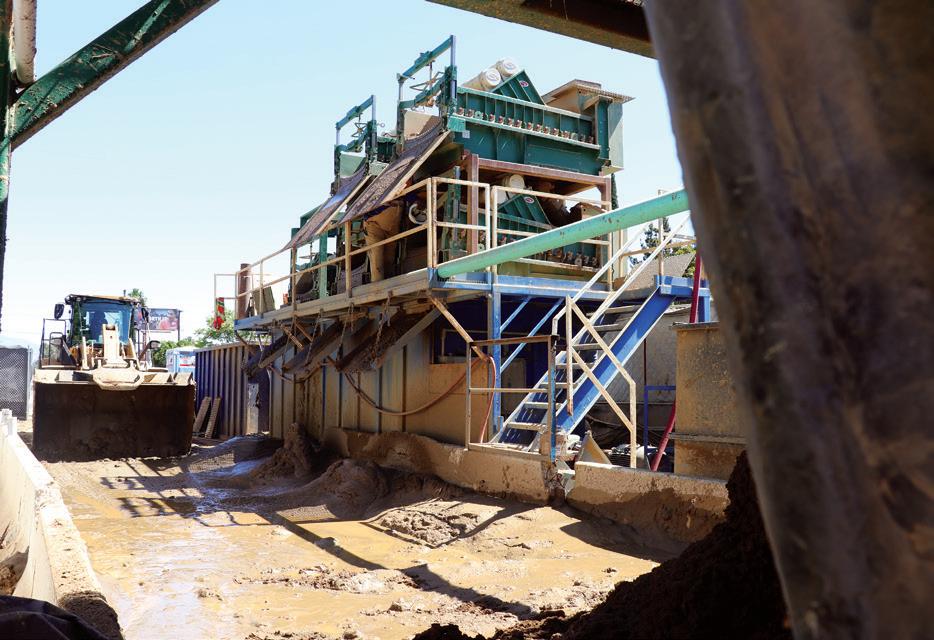
Separators filter the slurry from the microtunneling operation and deliver to slab below for loading and export.

Mike Abbott, W. A. Rasic superintendent operating the Akkermann microtunneling machine from above ground work station.
According to Juarez, the project is built in three individual reaches. Reach one contains two runs that utilize the same jacking pit but has two separate receiving pits. “We bore out approximately 1,000 feet from work area 12, which is the designation we give to the main jacking pit control zone. When that push is complete, we bring the MTBM back and go another 1,000 feet in the opposite direction from the same jacking pit,” says Juarez. “We then jump to reach three, where the same process is repeated and then on to reach two for more of the same. One MTBM machine performs the work for all five bores, and each push will eventually make a connection to the existing DWP trunklines.”
According to the Akkerman website, MTBM’s utilize high pressure jetting nozzles, articulated steering joint with three-point steering control, and hydraulically activated dirt wings to minimize MTBM roll. The guidance system relays all critical operation data to the control container using proprietary control software programs. The MTBM system also includes a live, one-way audio system and camera allowing for system monitoring during operation, in addition to a gas detector and submersible pump. The MTBM is most suitable for saturated and flowing material and pressurized soil under the water table. MTBM’s can drive to lengths up to 1,000 linear feet and are remotely controlled from an above-ground computerized service station. MTBM’s minimize ground surface settlement, as the excavation occurs by infusing the soil with slurry at the face of the bore. The pulverized dirt, rock and sand are then pumped out through the machine using water jets and slurry pumps.
According to Juarez, the extracted material has an almost toothpaste type consistency as it is processed through a separator. The slurry is then ejected onto a slab for wheel loaders and skid steers to pick up and load into 10-wheel trucks for export. “We utilized a similar earth pressure balance shield tunnel boring machine (EPTBM) on the W. A. Rasic /SAK Joint Venture for the River Supply Conduit 5 & 6 project for LADWP a few years back. This is, however, the first time we have utilized the MTBM as the prime self-performing contractor on a project,” explains Juarez. “Mike Abbott is our tunneling superintendent operating the MTBM, and he has many years of experience. Running an MTBM is no easy task, and it requires a great deal of training and experience. We are fortunate to have someone as qualified and experienced as Mike on this job.”
Juarez said they are utilizing 20-foot casing sections that are 72-inches in diameter. They are using 72-inch Permalok® steel casing pipe, which connects quickly and eliminates field butt-welding. Once the casings are installed, the new 60-inch trunkline will follow throughout the project. “Our entire team is doing an exceptional job with some of the best in the industry overseeing the MTBM process. Johnny Juarez is our project engineer, Jeff Ray, general superintendent, Gilbert Estrada, our superintendent, and Horacio Hernandez and Moses Vallejo are the project managers on the job,” continue Juarez. “We also have multiple crews and a foreman overseeing the open-cut trenching section.”



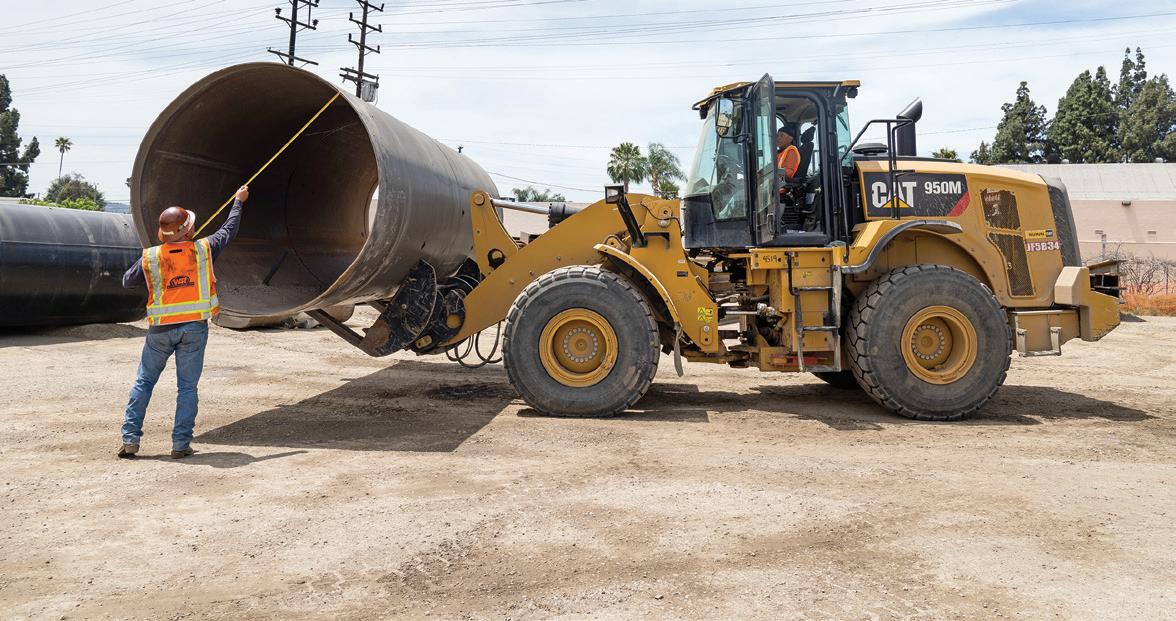
Above: W. A. Rasic delivering 72-inch Permalok® steel casing pipe to jacking pit where it is then lowered in place by a 90-ton hydraulic crane. Once the 72-inch casing is installed, the new 60-inch welded steel pipe is jacked inside and the voids are grouted.
W. A. Rasic designates the open-cut trenching section as Work Area 14. The 1,271-foot open-cut section utilizes beam and plate shoring for the welded installation of 60-inch waterline. “The open-cut section is situated in a tight working area, and we are using our Cat 335F hydraulic excavator here due to its minimum swing radius,” says Juarez. “The open-cut section is fairly simplistic by comparison to the MTBM sections. This is our bread and butter, and we have done a lot of this type of work over the years. Everything is going smoothly, and that has a lot to do with our ability to work closely and efficiently with the various agencies like LADWP, BOE, the City of Los Angeles. We are also fortunate to be working for Pete, Frank and Walter Rasic, who are all very involved in the daily operations and future success of every team member.”
W. A. Rasic Construction specializes in infrastructure projects and is now one of the largest privately-owned utility contractors in the Western United States. With extensive resources, a focus on safety and strict adherence to quality, they consistently deliver on some of the most complex projects, like the City Trunk Line South-Unit 3 project. The company’s foundation is firmly rooted in their family tradition with a continued focus toward an exciting and bountiful future. For more information, please visit their website at www.warasic.com or call their Long Beach headquarters at (562) 928-6111. Cc