
13 minute read
Discovering Hidden Water Waste
With California’s drought crippling more and more communities across the state, identifying ways to reduce water use isn’t only a good idea, it’s the law. Not every solution works for every situation, but if you have a cooling tower at your association, you may have a veritable treasure trove of hidden water waste that you can curb almost immediately. How much water? My association ended up saving around 4.2 million gallons annually – about 40% of our total consumption for the entire building.
Now, before I tell you how we did it, I should mention I’m not an expert in water conservation, cooling tower management or energy efficiency. Like most of you reading this, I’m a community manager with a passion to do the best I can for my association, and that’s what led me to research our problem and find an expert to help identify a solution.
Cooling Tower Logistics
I manage a high rise association that features two cooling towers. Throughout this process, I’ve learned a lot about how cooling towers operate.
Discovering Hidden Water Waste
By Dirk Foster, CCAM-HR.LS
Cooling towers are the last stage of a building’s cooling process, as they essentially transfer heat from interior spaces into the environment in two ways: 1) hot water vapor into the air (evaporation), and 2) warm water purged down the drain (blow-down). By design, these towers consume large amounts of water. For one, the water used for this cooling function must be maintained at a specific volume for the system to function properly, meaning make-up water is added from your domestic water supply as needed. By extension, the larger the tower’s capacity (meaning the larger the volume of water it’s capable of cooling every minute), the more heat it transfers into the atmosphere through evaporation – and the more water it consumes to make up what was lost.
Many cooling towers operate under an “open flow control” process, which involves constant blow down of the water used for cooling. This is because the water that remains in the basin following evaporation has a higher concentration of mineral hardness and requires additional chemical treatment and closer monitoring to mitigate problems, such as scaling, biofilm, corrosion, bacteria and white rust. In short, open flow control is the
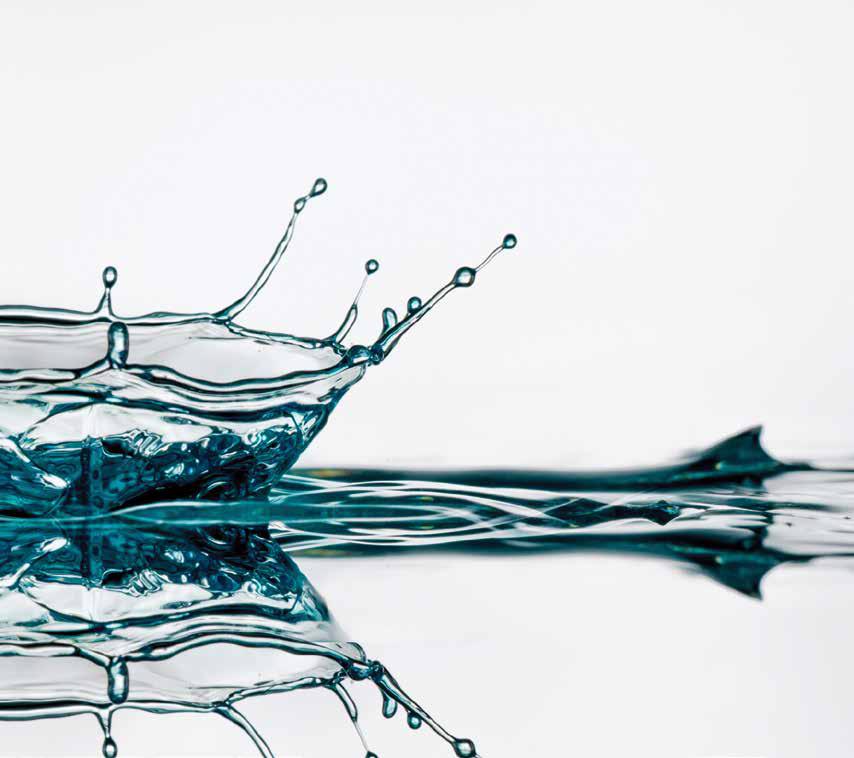
Continued on page 52
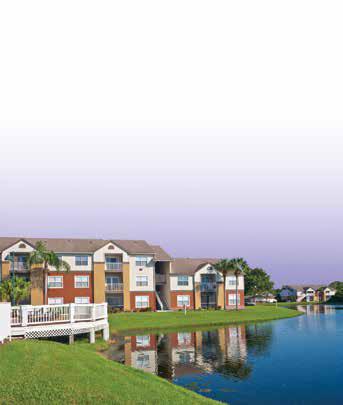
Effective General Counsel
ADA & DEFH Compliance Amendments to CC&Rs & Bylaws Architectural Matters Contracts & Insurance Elections & Recalls Employment Law Legal Opinions Successful Assessment Collection
Timely Status Reports Responsive Paralegals Collectibility Analysis Judicial or Non-Judicial Foreclosures Money Judgment Lawsuits Small Claims Assistance Post Judgment Recovery
949.322.6838 • 619.327.9026 • 760.529.5211 www.AttorneyforHOA.com most cost-effective maintenance program – that is, if you ignore the amount of water wasted.
Battling Industry Standards
In 2007, my building maintenance engineer and I became concerned over how much water the two cooling towers were discharging via blow down. He talked to our water treatment technician while I checked past water bills. Everything seemed to be on track with previous years, but we couldn’t get over the fact that the towers seemed to be dumping water constantly.
We measured the rate of discharge at over eight gallons per minute; over several months the only change to that average was the normal seasonal swings (i.e., when most residents were running the A/C frequently). The blow down equated to nearly 350,000 gallons per month! I thought this couldn’t be normal, especially since we were also losing water to evaporation.
After several months of monitoring, I placed a call to our water treatment company and was surprised when they told me that everything was normal and we had nothing to worry about. They explained that the water had to be purged from the towers because otherwise it could cause damage to the equipment or worse, Legionnaires’ disease. I wasn’t completely convinced, so I called around to check what they told me. After talking to several HVAC and water treatment companies, as well as building maintenance engineers, trade organizations and even a local union, I was astonished to hear the same exact thing repeated to me over and over. One professional with a lifetime of experience in the field of cooling tower management told me open flow control was an industry standard because the alternatives were way more costly.
Basically, the easiest and most profitable way to perform the job from a vendor’s perspective is to allow lots of blow down from the tower so that they can treat with the minimum amount of chemicals. This ensures the best profit margin and easiest sales pitch – as long as clients don’t realize the cost of water wasted.
Implementing the Solution
I started to wonder, if open flow control is the industry standard, how can anyone identify water waste that presumably could have been going on for years? I wanted to know if there was a standard measure of efficiency and contacted an independent water treatment specialist I knew from a previous association. He explained that there was a standard measure called Cycles of Concentration (CoC); it compared the concentration of dissolved solids in your make-up water to that of the circulating water in your basin. I asked him to come out and perform an independent evaluation immediately.
We were a mess! Our cooling towers were old and had been poorly maintained for a number of years. The monitoring equipment only allowed us to achieve a few CoC before requiring blow down – and they weren’t even achieving that because the set point on the
equipment called for a water purge after only one cycle to reduce chemical use. In order for a cooling tower to be 90% water efficient, it needs to achieve at least five CoC.
As soon as I presented the ROI to the Board, we changed water treatment vendors and installed different monitoring equipment. The $150 per month increase in treatment costs and $7,000 worth of equipment was offset that first year by the nearly $30,000 in water savings. Since then, we’ve changed our internal maintenance program for the cooling towers to keep them cleaner; started keeping a daily log of make-up and blow-down water for each tower so we can identify issues immediately; and improved communication between our HVAC equipment and water treatment vendors.
Now our blow-down is less than 27,000 gallons annually – huge progress when compared to the 350,000 gallons per month we used to lose. In fact, our total make-up water used over the last year was just over 415,000 gallons, probably what it was each month back in 2007.
Look, I realize this might sound too good to be true – did we really save that much water?! It may sound like fiction, but I assure you it’s not. (Believe me, I can’t even tell you how many times I’ve double checked my math!) At this point, all I have left to offer you are clichés: Desperate times call for desperate measures. Nothing ventured, nothing gained. To the victors, go the spoils.
But really, these are desperate times, and if you’re willing to think outside the box and take a chance, you may discover hidden water waste that can be turned into savings for your association. When you do that for your association, take the credit due to you, because when one of us wins, the entire industry does. All I did was share my story – you’ll be the one who took decisive action.
Dirk Foster, CCAM-HR.LS is General Manager of Two Eleven Spalding Condominium Association in Beverly Hills.
Cooling Tower Maintenance Tips
Dealing with a wasteful cooling tower at your association? Consider these tips for improving your cooling tower function:
Take a look at your treatment reports and see if you’re achieving the sweet spot of 3-5 CoC – and don’t settle for the minimum. If you can increase from 3 to 5 CoC, you’ll jump from 75% to 90% water efficiency on your cooling towers. If you’re comparing proposals for water treatment, make sure each proposal includes the vendor’s target CoC.
Keep track of the reported make-up and blow-down meter readings or, even better, take them daily inhouse. If you don’t have flow meters installed to take these readings, consider having it done to help you notice problems you might not otherwise see. Such comparisons can help you quickly identify water loss from basin overflow or intermittent leaks that may just seem like heavy drift loss on those hot days when water dries quickly on your roof.
Make sure that your cooling towers are kept clean and chemical reservoirs adequately filled. Scale, microbial growth and other deposits on cooling tower surfaces, act to insulate them and decrease the amount of heat exchange achieved through evaporation, which means more blow-down is required to pick up the slack. This all causes the cooling tower to work harder and can put significant stress on the equipment that relies on the tower to do its job efficiently.
Keep an eye out for corrosion, which can lead to problems with equipment operation and allow for microbial growth. Legionella bacteria, the cause of Legionnaires’ disease, is a concern, but reducing the factors that contribute to its growth, like the presence of other biological matter and organic debris, coupled with a good treatment program, help to keep it in check. Keeping corrosion in check reduces the likelihood that organic materials will collect on tower surfaces and allow for microbial growth.
While you might expect direct sunlight to help prevent microbial growth, it actually promotes the growth of algae, another insulator that robs your cooling tower of efficiency. Direct sunlight can also evaporate water instead of allowing it to be evaporated by heat exchange surfaces, decreasing efficiency and increasing the amount of water required for make-up.
Talk with your water treatment technician about make-up water hardness to find out if anything can be done to reduce it before the water is introduced into the tower. This can significantly improve your CoC and reduce the amount of chemicals required to treat basin water. Believe it or not, recycling water from other rooftop equipment and mixing it into make-up water may be beneficial, diluting the overall start point for water hardness.
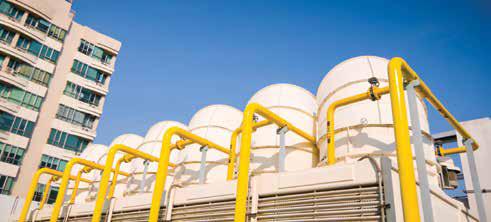
Talk with your treatment company about the equipment and chemicals they are using at your location, with an emphasis on what’s optimal to achieve your target CoC. When we purchased more advanced chemical monitors to improve treatment, the water district gave us a 50% rebate and our treatment specialist took care of all the paperwork, including filing it for us; all we had to do was sign. Even if your company can’t get you a rebate, they should be able to help you with a cost-benefit analysis so you can decide if purchasing advanced equipment will result in an overall savings.
JOIN CACM FOR A GREAT 2016
It’s almost time to renew your manager membership with CACM!
Your commitment to another year of membership will be met with CACM’s dedication to further your opportunities for personal and professional success. Here’s how we plan to support your professional growth in 2016:
California-specific education offerings to help you manage smarter and with more authority Board education tools to help promote you as the expert in every meeting Industry-leading publications, templates and resources to keep you informed and prepared Member discounts on CACM’s courses, events and award-winning certification programs Networking events that connect you to likeminded peers and quality service providers Plus, if you pay your invoice by December 1, you will you will be automatically entered to win a free registration to one of CACM’s 2016 Law Seminar & Expo events – a $300+ value that gives you access to the latest updates on California legislation and legal issues impacting your profession.
Keep an eye out for your dues invoice, which will be emailed to all manager members the first week of November.
We look forward to supporting you and the California community management industry in 2016!
Pay by December 1 for a chance to win your way to a 2016 Law Seminar & Expo!

SESSION SNEAK PEEK
In addition to invaluable networking opportunities and an exhibit hall packed with the latest industry products, CACM’s 2016 Law Seminar & Expo will feature 18 different breakout sessions so attendees can customize their learning experience.
Here’s a sneak peek at two of this year’s sessions:
The Dawn of the Smart Community Find out how cities all over the world are increasing efficiency and improving community life by implementing emerging technologies like networked lighting controls, security and data management, asset management capabilities and more into their infrastructure. Discover financial options available to facilitate these technologies in your associations.
Managers’ Therapy Working with difficult board members and contentious homeowners can take its toll on the most positive of managers. Learn from a panel of long-time managers and industry leaders how they weather trying times and still make the choice to get up and do it again. Engage with other managers, talk through dealing with stress in and out of the office, and explore ways to enhance your work/life balance.
Join us for these sessions and many more professional development opportunities at the Oakland Marriott City Center on February 11-12, 2016 or The Disneyland Hotel in Anaheim on March 17-18, 2016.
Learn more and register now at www.cacm.org.
2016 LAW SEMINAR SESSIONS Choose from these 18 different education sessions, which are designed to appeal to different types of managers and cover various industry hot topics.
EMPLOYERS
• Develop Your Injury & Illness
Prevention Program • Develop Your Social Media
Employee Use Policy
SPECIALTY MANAGERS
• High Rise Community
Engagement • Large Scale Governance • Mastering New Development
Transitions • Managing the Age-Restricted
Community • Commercial & Industrial CID
Management
FACILITY MANAGEMENT HOT TOPICS
• The Dawn of the Smart
Community • Dealing with Second-Hand
Smoke • Wrestling with Rentals in the 21st Century • Practical Implications of the
CA Solar Rights Act
LEGAL TOPICS
• Beyond the Legislative Update • New California Case Law • Lender Certification Dos &
Don’ts • Elections I: Become an Election
Pro • Elections II: From Pro to Expert • Ask the Attorneys
WORK/LIFE BALANCE
• Managers’ Therapy
CALL FOR NOMINATIONS CACM VISION AWARDS
Recognition can be hard to come by in our industry, which is why it’s important for us to honor our own.
Show your appreciation for the outstanding colleagues you know by nominating them for a 2016 Vision Award.
Choose from four categories:
Rising Champion Managers’ Choice Leadership Awards Excellence in Service
Nominations due November 13, 2015.
Download the nomination packet now at www.cacm.org/visionawards.html.
Community Association Loans All the right tools for your next project.
How will you fund your next community project? Get the job done right with the Community Association Loan toolkit. You’ll get custom financing that’s perfect for your budget and your community. Your Community Association Loan toolkit includes: • Competitive interest rates • Flexible payment plans • Innovative loan structures • Fixed rate loans • Non-revolving lines of credit Get the cash you need today.
Lisa Ann Rea VP/Regional Account Executive 805.907.8452 Toll Free 866.800.4656, ext. 7500
lisa.rea@ mutualofomahabank.com Jack Brandt AMS AVP/Regional Account Executive 510.921.0124 Toll Free 866.800.4656, ext. 7579
jack.brandt@ mutualofomahabank.com
Brendan Concannon Regional Account Executive 619.961.6346 Toll Free 866.800.4656, ext. 7480 brendan.concannon@mutualofomahabank.com
Member FDIC • Equal Housing Lender Equal Housing Lende National Corporate Member of Community Associations Institute CACM Affiliate Member
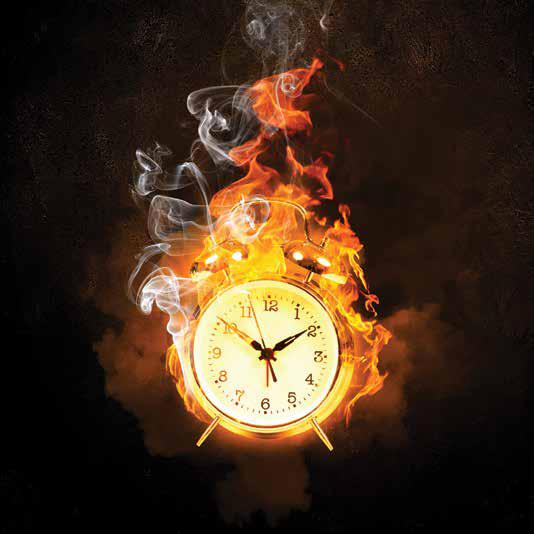
