
58 minute read
Industry News
LTU Launches Construction Safety Research Center
Lawrence Technological University and a group of industry partners have launched the Construction Safety Research Center (CSRC) to make construction workplaces safer across Michigan and the nation. The need for the center is obvious, said CSRC director Ahmed Al-Bayati: 1,061 construction workers were killed in 2019, the largest total since 2007, and more than 200,000 more workers suffered injuries.
Advertisement
Al-Bayati, Assistant Professor of Civil and Architectural Engineering at LTU, is a nationally recognized expert in construction safety. He said the CSRC will continue to strengthen national efforts to reduce fatal and non-fatal injuries through innovative research studies – and turn that research into industry best practices, and then turn those best practices into training materials that can be easily used by construction companies and workers.
“The center’s goal is to reduce workrelated fatalities and injuries by providing construction firms with nationally recognized training, which will be derived from the cutting-edge research that will be conducted by CSRC, in collaboration with our industry partners,” Al-Bayati said. Learn more at www.ltu.edu/engineering/ csrc.
Budget Surplus and a Midterm Battle: A Recap of CAM’s 7th Annual Legislative Breakfast
CAM’s 7th annual Legislative Breakfast, which took place at the Heathers Club of Bloomfield on Friday, October 14th, gave industry professionals an exclusive look at how legislators plan to support Michigan’s construction industry and economy throughout 2023. Conversation revolved around a $6 billion state budget surplus, the status of Prompt Pay, and a contentious midterm election. Despite political differences, both sides of the aisle agreed to support the construction industry in terms of education, infrastructure, and policy.
CAM lobbyist Jason Wadaga of Kindsvatter, Dalling & Associates moderated the event, welcoming state Sen. Dan Lauwers (R) of Brockway, Rep. Sarah Anthony (D) of Lansing, Sen. Jeremy Moss (D) of Southfield, and Rep. Joseph Bellino (R) of Monroe to the legislative panel. Read the full story at www.buildwithcam.com/news/2022-legpanel.
Three New Research Reports Advance Safety
Three recent CPWR reports offer guidance for making construction workers safer on the job. Earlier this year, the organization’s Research to Practice program surveyed nearly 500 people who experienced, witnessed, or investigated a fall incident. In the report, “Underlying Causes of Falls from Heights,” participants cited a lack of adequate planning as a key cause of falls, which continue to result in approximately 300 fatalities each year. A separate study examined struck-by incidents, including barriers to preventing them, measures that can protect workers, and the motivators, resources, and support needed to reduce and eliminate them. Finally, CPWR studied which factors affect the success of safety and health training delivered through distance learning, including recommendations for continuous quality improvement. Visit www.cpwr.com to read the reports.
Over $172,000 Raised at the 18th Annual Building Connections Event
The “Networking Event for Construction Professionals,” Building Connections is the largest annual gathering of the construction community in Southeast Michigan, providing an opportunity for informal business and social interaction while supporting the Scouting program for area youth and their families. This year's Building Connections event was held in an upper-level space at 1 Campus Martius on September 7th. The 2022 event committee is proud to report that $172,340 was raised to support local Scout programs in southeastern Michigan. "The impact these funds will make on the over 25,000 youth in the program is immeasurable," said Jamie Bochenek, Senior Development Director, Boy Scouts of America, Michigan Crossroads Council. Learn more about Building Connections at michiganscouting.org/buildingconnections.
NSC Announces This Year’s Green Cross Safety® Winners
The National Safety Council (NSC) recently honored three organizations working toward and succeeding in preventing injuries and saving lives with its annual Green Cross for Safety® awards. Presented during the 23rd annual Green Cross Celebration, this accolade recognizes the best and brightest in three categories: safety advocacy, safety excellence, and safety innovation. This year’s winners include Mothers Against Drunk Driving (MADD) War Room, U.S. Steel, and Fatigue Science, a provider of predictive fatigue analytics and human performance insights for heavy industry. In addition to recognizing this year’s award recipients, the Green Cross Celebration helped raise more than $625,000 for mission critical initiatives, including safety research, education, and advocacy. Read more at www.nsc.org.
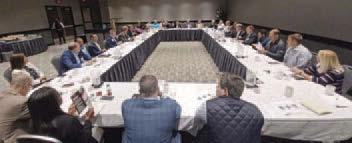
CAM’s Latest Construction Roundtable Addressed a Likely Upcoming Recession
With economic indicators pointing toward a recession, contractors need to revise their business playbooks to remain costeffective and competitive in the 2023 economy. The short-term outlook appears to be challenging – inflation is persisting and raised interest rates have not quelled the trend. However, understanding what makes this recession different will be the key to surviving and thriving in the 2023 economy and beyond. This is just some of the conversation that came out of CAM’s latest Construction Roundtable, which took place at the Somerset Inn on October 12th.
Titled “The New Recession Handbook: Driving Current and Future Enterprise Value in Any Market Environment,” the event included a panel of experts wellversed in the construction economy. This included Alex Calderone of Calderone Advisory Group, David Sowerby of Ancora, and Shawn Spencer of Cogent Advisors. The event was moderated by Matt Gurwin of Doeren Mayhew.
CAM’s Construction Roundtables provide a forum to deep dive into leadership development and best practices for changing your workplace culture. Read the full recap of the October 12th discussion at https://tinyurl.com/ CAMRoundtable2.
New Alliance Protects & Educates Plumbers, Pipefitters, and HVAC Service Techs
MIOSHA and the Mechanical Contractors Association (MCA) of Detroit recently formed an alliance to help more workers in the mechanical construction and service industry to foster safer, more healthful workplaces. The formal alliance agreement will help raise awareness of MIOSHA’s protection initiatives for mechanical service practices, while strengthening education, outreach, and training to protect more plumbers, pipefitters, and HVAC service technicians. Learn more at https://tinyurl.com/ MIOSHAMCAalliance.
CAM's Latest Podcast Highlights the Ace Mentor Program of America
The 10th episode of CAM's Building Michigan podcast welcomes Vince DeLeonardis, CEO of AUCH Construction, and Jeff Chandler, President of VTC Insurance Group. Hosted by Kevin Koehler, the President of CAM, this episode dives into the ACE Mentor Program and the many ways in which it is building Michigan's future construction workforce.
Founded in 1994, the Ace Mentor Program of America is a free, awardwinning after-school program designed to attract high school students to careers in architecture, construction, and the engineering industry. Listen to the podcast at www.buildwithcam.com/news/ ace-podcast.
The MIOSHA Training Institute Introduces a New Pilot Course
MIOSHA recently announced that it has developed a new course on required written programs, called MIOSHA General Industry Safety Documentation – Are You in Compliance? On October 12th, the MIOSHA Training

Institute piloted this full-day course at Grand Valley State University in Grand Rapids. The program is an in-depth review of MIOSHA’s general industry safety required written programs, inspections, and permits. Participants learned what programs require written policies or documentation such as reporting and recording of occupational injuries and illnesses, emergency exits, and personal protective equipment. MIOSHA will add the new course to its list of electives for the General Industry Level 1 Certificate Program in the coming year. Learn more at https://tinyurl.com/MTInewprogram.

McLaren Greater Lansing’s Replacement Hospital Wins 2022 National Merit Award
McLaren Greater Lansing has announced that its new hospital project won a National Award of Merit in the Healthcare Facilities category from the Design-Build Institute of America (DBIA). The McLaren Greater Lansing hospital project was one of three health care projects from across the country to win this award. The project consolidates two existing Lansing hospitals into a new 562,000-square-foot hospital adjacent to Michigan State University. The nine-story, 240-bed hospital is nestled within a 39-acre, $601 million
health care campus.
“From day one our design-build teams worked together with our clinicians to build a hospital that is not only beautiful, but provides the best experience for our patients and visitors,” said Kirk Ray, President and CEO of McLaren Greater Lansing. “We are thankful for this recognition and look forward to providing our community with quality health care services they need to get care close to home.”
The hospital was also selected as one of the 12 outstanding construction projects featured in the 2022 CAM Magazine October Special Issue.

CAM affinity
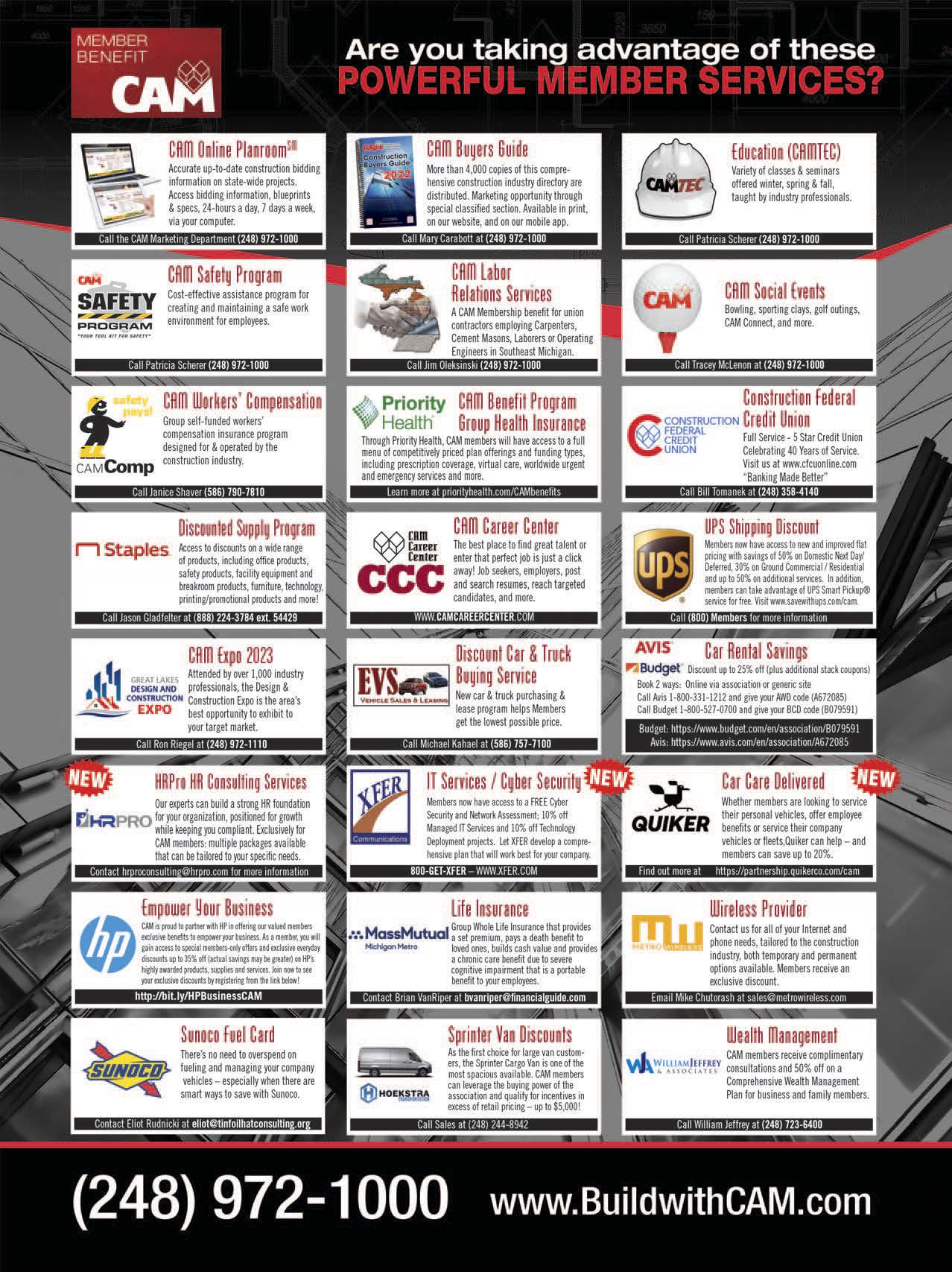

By TODD DROUILLARD AIA, NCARB, National Manufacturing and Product Development Sector Leader, HED
HOW THE A/E CAN INFLUENCE SAFETY: THE POWER OF 3D MODELING
Safety is a topic that is usually brought up during the start of construction and oftentimes at owner meetings, toolbox talks, and other contractor-led meetings. Architects usually attend these meetings during construction administration but rarely get involved or have much to offer to the safety conversations. But how can the architect influence safety on a project? In the architectural and engineering (A/E) industry, we usually attribute safety to the design of safe buildings through building codes, national standards, and good design practices.
All the items listed are of utmost importance to the architect or engineer, but how can we ensure that the buildings are operationally safe to the users? By using 3D modeling, we can fly through the project early in the design development stage and illustrate to building managers, maintenance personnel, and owners the locations and placement of critical equipment that will require regular maintenance. This review during the design process is critical not only for the coordination between disciplines, but also for the visual review of objects that could pose a hazard during construction and/or occupancy.
In the placement of rooftop equipment, for example, a 3D BIM model can be used during the design to indicate where the removable panels and controls are located so it is clear that the distances from the edge of the roof are being met for safe operation. Shut-off valves, point-of-use controls and operations can be placed closer to a clear working service to avoid having to use other means for access. By modeling equipment and piping on the roof, tripping hazards can be avoided or crossover means can be designed to traverse potential hazards. Frequently used items such as ladders, stairs, platforms, and elevated surfaces can be illustrated so that all parties involved in building operations can provide input on the size and locations to ensure that the functionality is appropriate for the task.
Other areas where the architect and engineer can influence safety is both inside and outside of the building footprint. Exterior drive aisles, pedestrian walkways, exit paths, truck entry and exits can all be modeled with simulations to illustrate frequency of use and avoid potentially dangerous intersections. Early in the design, it can be determined if barriers should be placed to separate vehicles and pedestrians or if redirection and signage will be necessary. Inside of the building, pedestrian simulations can be modeled to avoid similar dangers. Buildings that have machinery or equipment active within can be modeled and potentially simulated to aid in the layout of pedestrian aisles, means of egress, and simply to avoid dangerous interactions between humans and machines. In public-facing buildings such as schools, community buildings, airports, cultural facilities, and other occupancies, defensible design practices can be modeled and scenarios simulated to aid in a practical design that security experts can review and comment on during the design phase. The review can be as simple as modeling exterior and interior illumination levels both to avoid potential hiding locations to more complex simulations requiring experts in blast mitigation and other security consultants.
In a more analytical way, architects and designers have been using simulations in the design of buildings to study how the structure will respond to natural disasters such as high winds, earthquakes, and most recently floods and hurricanes. This data can be shared and illustrated as a basis of design to accommodate building codes, but may also generate discussion of additional ways to make the building safer. The more data and understanding that the architect, engineer, owner, and contractor has on this building design contributes to a safer building.
Manufacturing and warehouse projects where employees are exposed to active machinery, moving vehicles, elevation
changes, and other process hazards can and should be reviewed by the architect, owner, and process engineering team. Per OSHA statistics, injuries within the manufacturing and warehouse occupations have been consistently trending down over the past 10 years; however, they still account for a high majority of workforce injuries. Routine work tasks within these types of occupancies can be reviewed within a 3D model to study worker ergonomics and machine-to-human interactions. It can also aid in the addition of protection screens, identification of hazardous zones, and the design of physical barriers with the goal of making the workplace safer.
Research and development and laboratory projects can also benefit from a safety review during the design of the building within a 3D model. Buildings where the primary function of the testing and research consists of destructive means and laboratories of all types including analytical, biological, medical, incubator, production, and research usually contain some level of hazard that needs to be mitigated and can benefit from a safety review from the users who know and understand the process and dangers.
Finally, the architecture and engineering disciplines can help the construction community build safer buildings. We will not instruct or direct means and methods of construction, as the builders and contractors are still the most knowledgeable and most responsible for this work. But in the early stages of construction, the 3D model can be used to verify construction sequencing and can be used by builders in a similar fashion used during design to avoid potential construction-related hazards.
In summary, the 3D model can be a powerful tool to properly communicate across all the parties involved in the development of a project. Beyond helping to aid the design team in the development of a safer project, it is an important tool to avoid potential costly changes during construction.
About the Author: Architect Todd Drouillard, AIA, NCARB, is the National Manufacturing and Product Development Sector Leader at HED, a national architectural and engineering firm headquartered in Southfield. Todd is also the 2023 AIA Michigan Vice President-Elect.

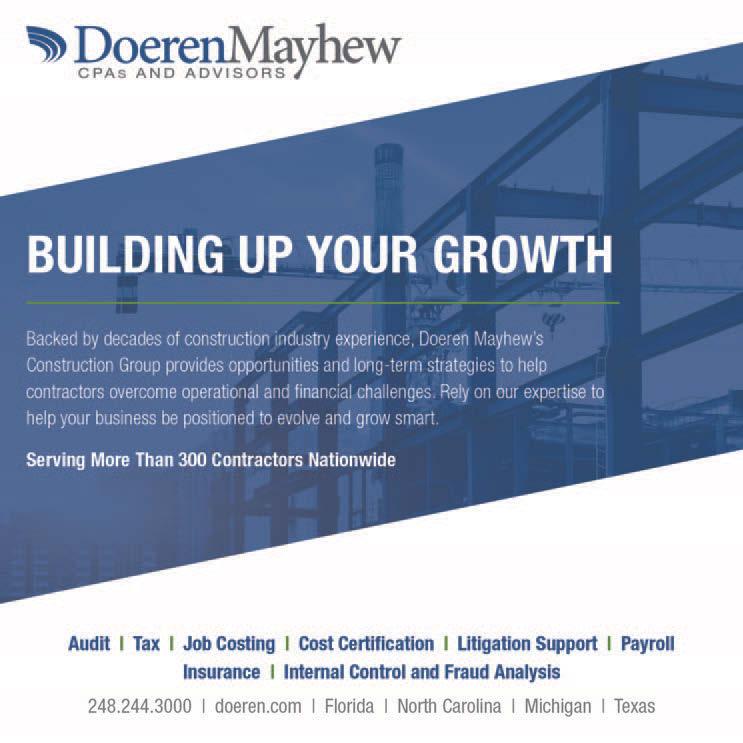
According to the Bureau of Labor Statistics, women account for 1.2 million of those employed in the construction industry, or about 1 in 10. While the statistics indicate that the number has remained flat, hovering around 9 percent for the last several years, I have personally witnessed an encouraging trend that has women moving beyond office and accounting roles into leadership and management roles.
When I started my career in construction in 1997, I was often the youngest person in the room and almost always the only female. Twenty-five years later, while I’m never the youngest anymore, I am happy to say that the number of women has steadily increased. Over the two decades, I have seen many instances of female entrepreneurship, daughters taking over for fathers, women being promoted into senior leadership positions, an increase in female representation on jobsites, and a more welcoming attitude toward women in the industry.
When I was asked to contribute an article to the safety issue of CAM Magazine, I thought it would be a terrific opportunity to highlight a few outstanding female safety professionals. Their experience ranges from being relatively new to their role to having decades of experience, and each of them is a testament to the valuable skills women bring to the construction industry.

GABRIELA ROSALESJENSEN is a Safety Manager for GallagherKaiser. She moved from Mexico to the United States eight years ago and was originally hired for document control. She knew nothing about construction but learned quickly, sharpening her English speaking and writing skills, and was asked to assist with safety when the company landed a contract for a large project in Mexico. Her current responsibilities include overseeing and managing a team of safety supervisors for the Gallagher-Kaiser jobsites in Mexico, as well as providing training to field personnel and management for the entire company throughout Canada and the United States. Gabriela obtained her law degree from Tecnologico de Monterrey in Mexico and graduated Summa Cum Laude.
A SPOTLIGHT ON WOMEN
IN CONSTRUCTION AND SAFETY
By Tracey McLenon, V.P. of Operations, Construction Association of Michigan
LISA MACAULEY is the President of Proficient Training and Consulting. She has been in the construction industry since 2008 and founded Proficient in 2014. Prior to beginning her construction adventure, Lisa was a hospital lab technician. She went back to grad school at Wayne State University to complete her master’s degree in Occupational and Environmental Health and landed an internship at the Marathon Oil Refinery. From there, she worked at a steel coating mill, then a mechanical contractor, and eventually opened her own training and consulting business. Today, Lisa’s team of safety consultants provide training and consulting services to a variety of construction firms throughout Michigan.
MANDY VENNING, CHST, is the Environmental Health and Safety Director for Braun Construction Group. Her overall responsibilities include program development and
implementation, managing employee education, incident prevention, and onsite safety audits. She graduated from Madonna University with a degree in Occupational Health and Industrial Hygiene. After an internship with Toyota, she moved on to construction safety and, this year, is celebrating 20 years in the industry.
TRACY NELSON, CHST, CIT is the Loss Control Consultant at CAMComp Workers’ Compensation. Her primary responsibility is to help CAMComp members identify the gaps in their safety plans and assist them with written programs and training to be MIOSHA compliant. After applying for an apprenticeship at the Operating Engineers in the late ‘90s, she worked for several companies including Posen Construction and Walter Toebe Construction. In 2016, Tracy finished her bachelor’s degree in Criminal Justice. She went on to complete all seven certificates offered by the MIOSHA Training Institute, became an authorized OSHA Outreach Instructor, and is a certified First Aid/CPR/AED instructor.
KATHLEEN (KATHI) DOBSON is the Safety Director for Alberici Constructors, and she has been with them for over 23 years. Kathi oversees Alberici’s safety program at a corporate level, helping set up projects, assisting with site plans, and addressing staffing needs. Kathi travels to various sites to act as a liaison at the project for automotive, heavy industrial, energy, and mining divisions of the company. She is a member of ASSP’s Standard Development Committee and the national A10 Construction and Demolition Consensus Standards Committee. She was recently appointed to a two-year term serving the National Advisory Committee on Occupational Safety & Health (NACOSH), and she is also past-president of the Detroit chapter of the National Association of Women in Construction (NAWIC). Kathi has a nursing degree from Mercy College of Detroit and, prior to her career in construction, she spent 10 years working in a hospital.
What drew you to the construction industry?
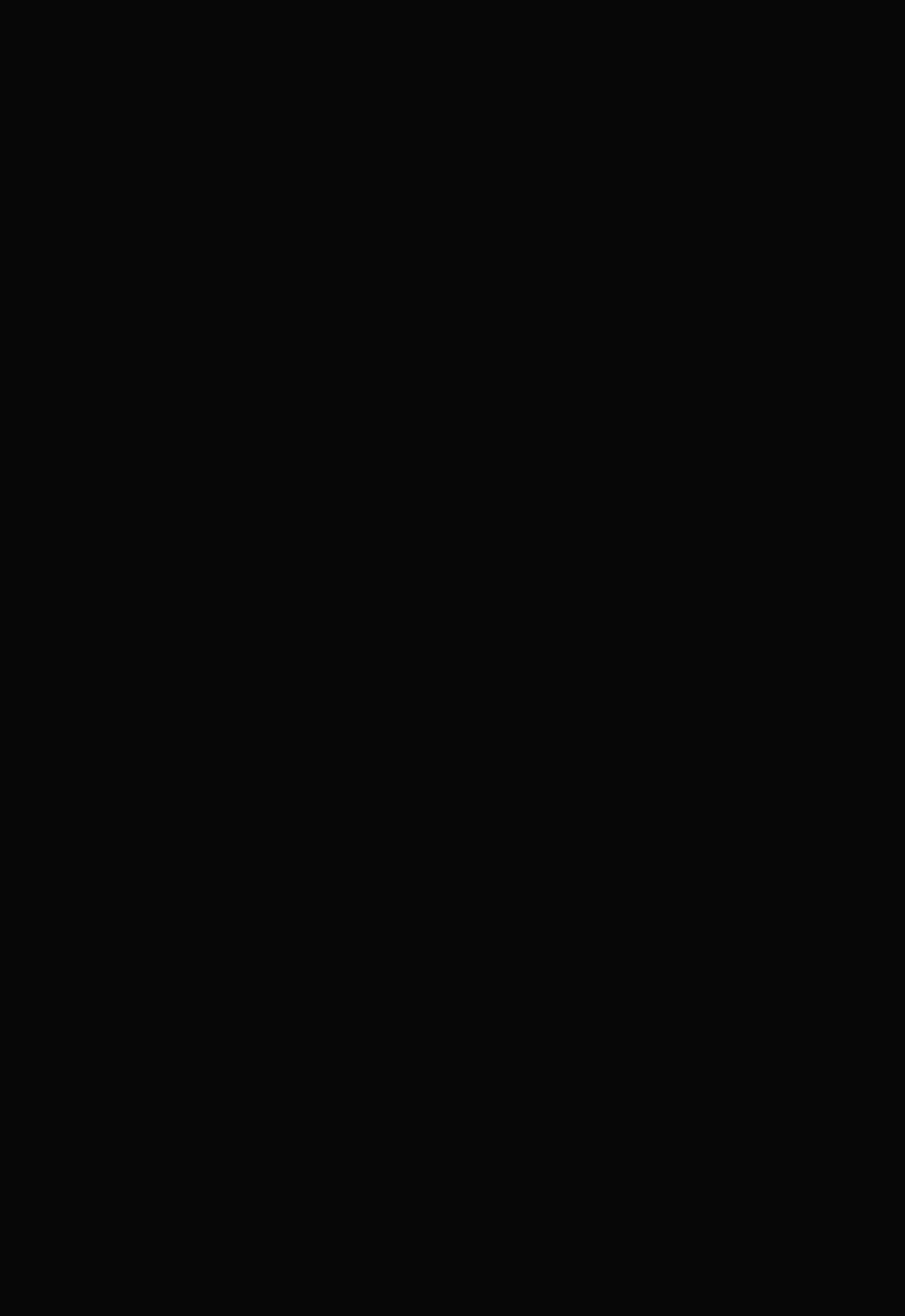
GR: I am a lawyer and used to practice labor law. When I moved here from Mexico eight years ago, I wasn’t sure if I wanted to continue to be a lawyer, but I knew I wanted to get a job doing something where I was helping people. In law, 80 percent of the work was pro bono and I enjoyed helping people and knowing I was doing something good. I realized that having a safety culture would make a difference in people’s well-being. If I could make a positive impact, it would be good for people and would keep them safe and able to go home.
LM: I was working midnights at a hospital lab, and there wasn’t a lot of opportunity. I looked at all of the masters’ programs and selected Environmental Health and Safety with a focus on industrial toxicology. When I first started my internship at the Marathon oil refinery, I was clueless. When they were talking about “fall protection,” I thought they were talking about wardrobes for this time of year! While there, I was working with a lot of the contractors at Marathon. After the internship, I went to Double Eagle Steel and then moved on to De-Cal. MV: I went to school for Occupational Safety and Health, which to me didn’t translate to construction safety. I envisioned that I would end up working for GM or Ford and had even interned at Toyota with the hopes of securing a full-time job there after graduation. During the internship, Toyota was putting an addition on their building, and they had the interns do the safety on it. We knew nothing about construction, but we wound up doing pretask plans and working side by side with the superintendent from Barton Malow. I liked it so much better than logging Material Safety Data Sheets in the company database or busting people for not wearing safety glasses in the lab. There was so much going on, it was changing every day, and it was exciting. I knew right away this was more my speed than the general industry side of things.
TN: Back in the late 90’s, I was dating a carpenter and working as an underground utility locator. When that company went out of business, I had to figure out how to replace my income. My boyfriend at the time told me that the Operating Engineers were accepting apprentices. I applied and never looked back.
KD: It was very serendipitous. I was working as a nurse for about 10 years and I got hurt. After two back surgeries, I couldn’t go back and do the same type of work I was doing in the hospital, so I took a job as an occupational nurse in a manufacturing facility. In that role, I was going on audits across the country, reviewing injury and illness records, assisting with case management, and reviewing all of the OSHA-related issues, like training and paperwork. As I got deeper into the role, I began to manage outside contractors with the maintenance department, making sure that they had their safety plans prepared, and I went through the OSHA 10 and 30 training to broaden my knowledge about construction safety. When I got laid off by the manufacturer, I sent my resume everywhere, and Alberici called me in.
Did you have a mentor that led you to your current role?
GR: My boss, Jeff Lorentzen. He knew from day one that I wasn’t from Michigan and I had a language barrier. He was always very kind and he knew I was going to be struggling, not only with learning the OSHA standards, but also that I had to translate everything in my head first. He has been a great leader to me. He is the one always pushing me, saying,

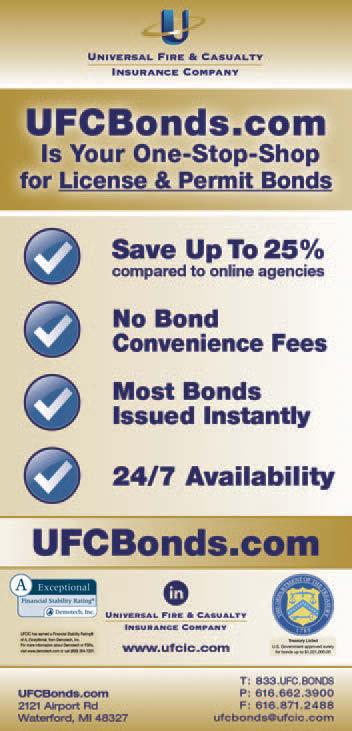
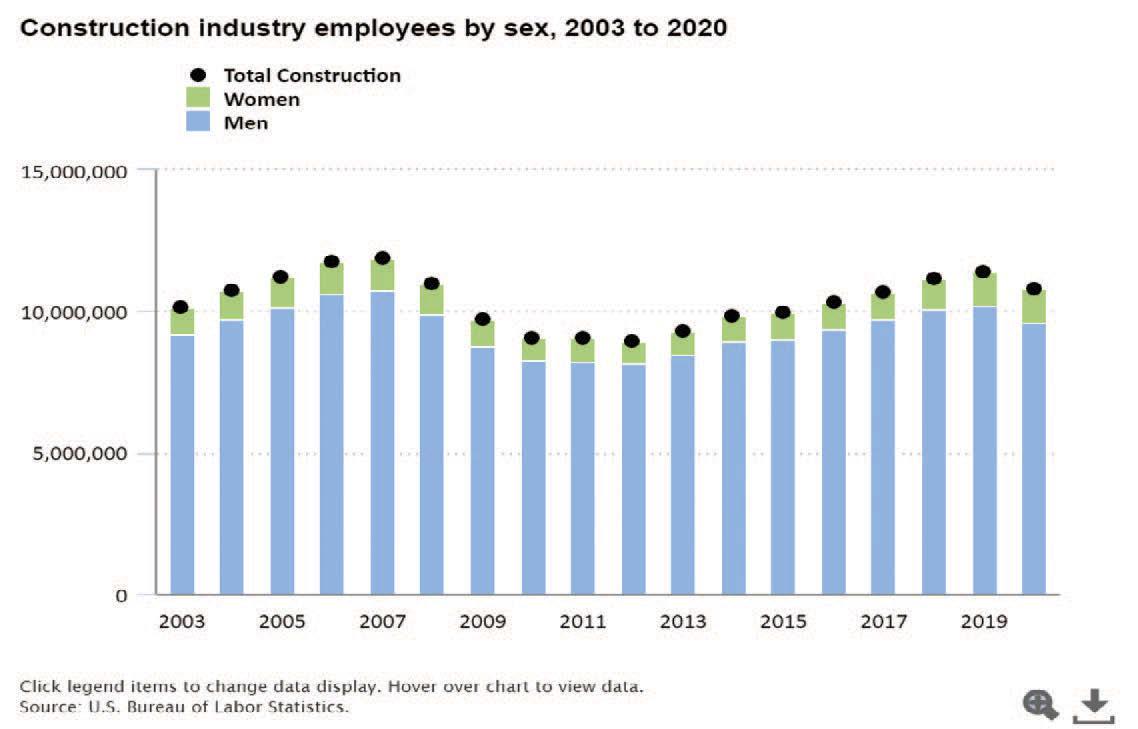


“you can do this, you can do more.” If he wasn’t my boss, I wouldn’t be where I am.
LM: I had a mentor at Marathon and I learned everything there. My mentor was Jim Kenyon, who is now an Industrial Hygienist at MIOSHA. It was his job to show me the ropes, and I needed that — I just didn’t have any background in industrial safety. He would quiz me on things. Just being at Marathon was a great place to do an internship because there is so much going on there. There are contractors and chemicals and confined spaces, so you got a really good dose of every kind of safety there.
MV: Patrick Moore, who was the safety director at JM Olson at the time. He plucked me from the general industry side of things and set me right in the middle of this construction world I knew nothing about. He took me on every site visit, safety audit, MIOSHA inspection and even brought me along on a fatality investigation. He knew I needed to see things firsthand in order to fully understand the construction processes and how it all begins with safety. He was not afraid to put me in situations where I was going to learn what I needed to learn and understood not all education comes from a book or a classroom.
TN: One of the crane instructors, Brian Newsome, overheard me talking to other operators as I was telling them that I wasn’t really digging the program. After lunch, he took me out back to the old P&H yellow crane, aka “Friction Rig.” I took that as a challenge, and I ran with it. I would later become certified to run several other types of cranes. Then I had another mentor, a fellow Operating Engineer, who was very helpful to me and later another good friend of mine got me into Fermi, the Nuclear Facility which allowed me to work in the manufacturing industry, and it changed my life. I was no longer a seasonal employee. I was working all year long with all of the various tradespeople.
KD: The regional manager at the manufacturing facility Colleen Davlin was my original mentor. Without her, I wouldn’t have separated myself from those nursing responsibilities. At Alberici, I’ve had many champions, including LeRoy Stromberg and Tom Taylor, who opened the door for me and helped lead me to personal and professional growth opportunities.
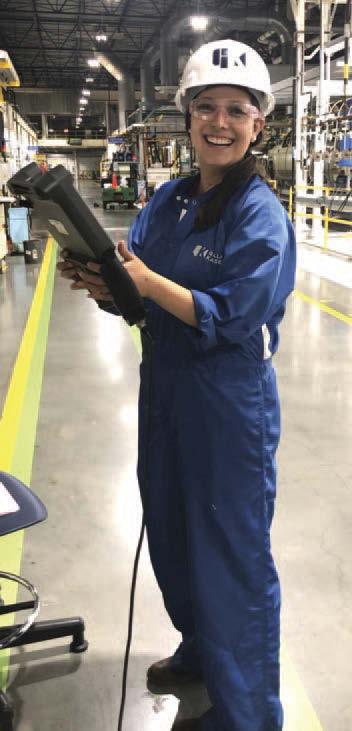
What do you love about construction?
GR: When I started document control, I started to realize this was really cool. First, we have dirt and then you end up with a building with robots painting cars. I started to take an interest in the whole process. First, every day is different, no day is ever the same. I like that. I am the kind of person that likes to go, go, go. The next thing is seeing the project from beginning to end. Because we work in construction, we have the latest technology too, so we get to see all of this new technology. Lastly, whenever the project ends and you have zero incidents and you can go home and breathe. I love that sense of achievement that everything went well.
LM: I really like that there are so many different places that we get to see. Especially the downtown Detroit area, new jobsites where they are remodeling buildings. Or going to Ford Field or Comerica Park, were you see the inside of things. You would never get that experience somewhere else.
MV: It’s the ever-changing, nothing’s the same, new environment. No two projects are the same, and I love that. TN: I have always loved the flexibility, the opportunity for growth and advancement, and often working in a different place.
KD: It’s the knowledge that I’m helping others to do things better, safer, and smarter—and hopefully, I’ve had an impact on the workforce that I’ve been working directly with, as well as the overall construction industry where I’ve been involved in some national affiliations. What are the advantages to being a woman in construction?

GR: I think as women, we can facilitate discussion and communication.
LM: I guess you stand out, because it’s always 20 men and you‘re the only woman in the room, so people remember who you are.
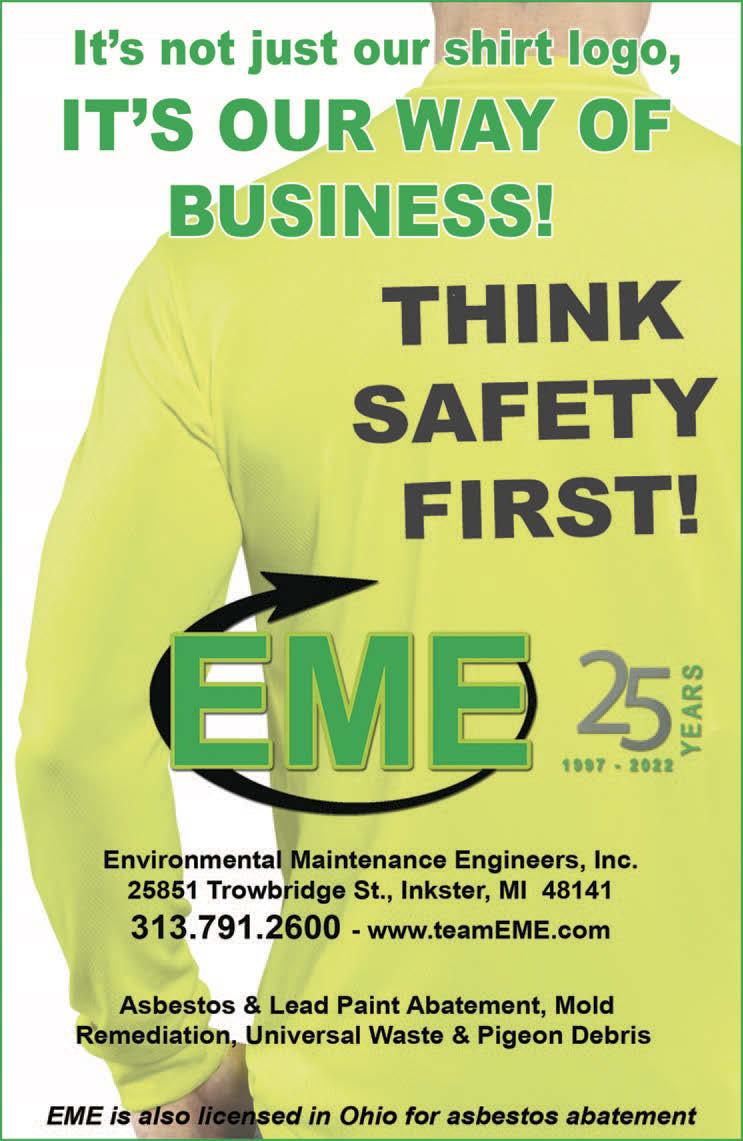
MV: There’s not very many of us and I think because of that, it opens up opportunities for management and leadership roles. I like the strong community of women. Since there are so few of us, we band together, help each other out, and lift each other up.
TN: The opportunity for personal growth and knowledge within the industry is huge. As women, we are able to adjust and adapt to the ever-changing needs of being out in the field. We are able to make and create lasting friendships and networking partners along the way. We learn skillsets that allow us to be independent and self-sufficient. Often times, we give more than 100% in order to prove ourselves out there, causing us to succeed in ways many don't.
KD: The advantage for women is that we quickly learn to adapt. I think we’ve done a pretty good job of figuring things out. Most men will lift something, hoist something, or move something around without taking the few extra seconds to think, how can we Iift this better? Do things better? I think men are more risk-taking than women are. In general, we as women tend to keep ourselves safer because we pause before we do things.
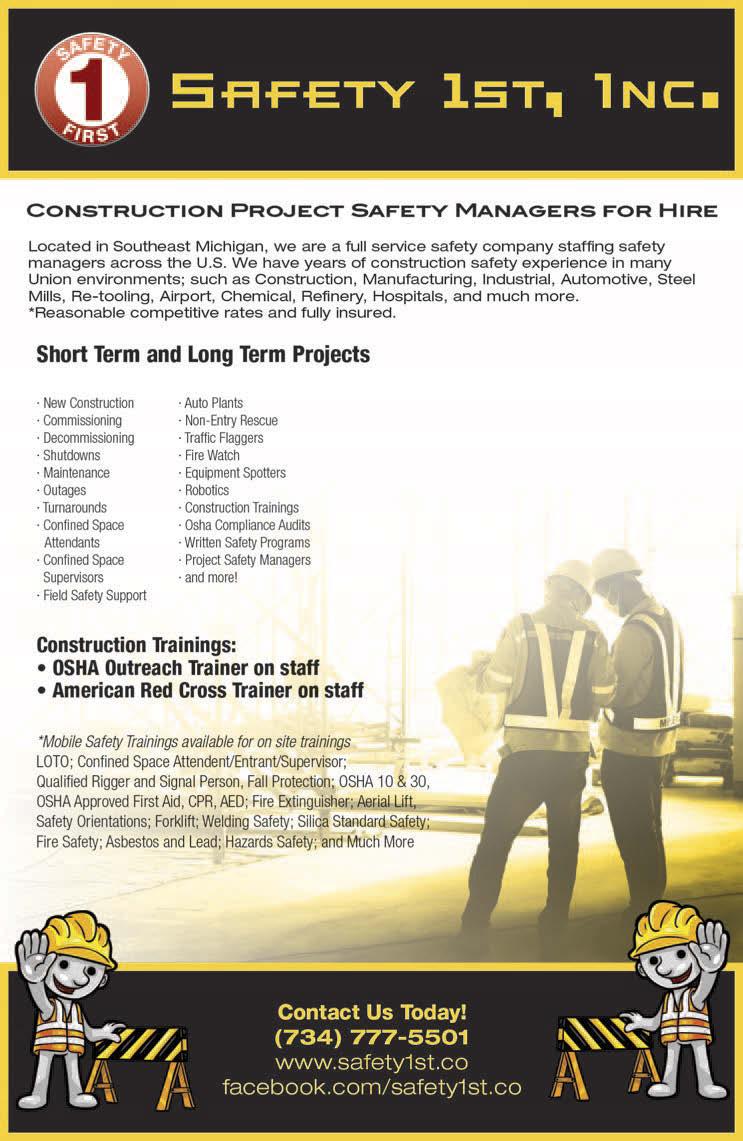

What have you achieved in your career that you are most proud of, or what is your most memorable moment?
GR: One was when I directed my first meeting in English. I was in a room of 40 men – I was the only female – and I remember standing there and they were all sitting and I thought, they’re really listening to me in another language! When I finished, I got my point across and they didn’t look at me like, “what did she just say?” Another proud moment was when I led my first solo shutdown, and everyone went home safe.
LM: I am most proud of starting a company from scratch and growing it into a successful business that provides livelihoods for a really great group of people.
MV: About five years after I was working at JM Olson, the director of safety management at Madonna University contacted me and was surprised to learn that I was working in construction. After talking with him, he brought me in and we worked together to create curriculum to develop two construction classes for the program. He even let me teach a couple of the classes. I was only 25 or 26 years old teaching 23 and 24 year olds as an adjunct faculty member.
TN: Every step of the way, I never stopped learning. I started out on a roller, and then someone let me on a dozer, then a backhoe, a boom truck, and then the cranes. And I finally started a career as a safety consultant. I am most proud of where I am today.
KD: I’ve been involved in some national initiatives, including metal health awareness. In 2015, I became aware of the high rate of mental health issues – depression, anxiety, suicide in the construction industry – so I started approaching it from a training perspective. I was doing things with NAWIC, and I got with my counterpart who was doing things for AGC. I feel very pleased that I was
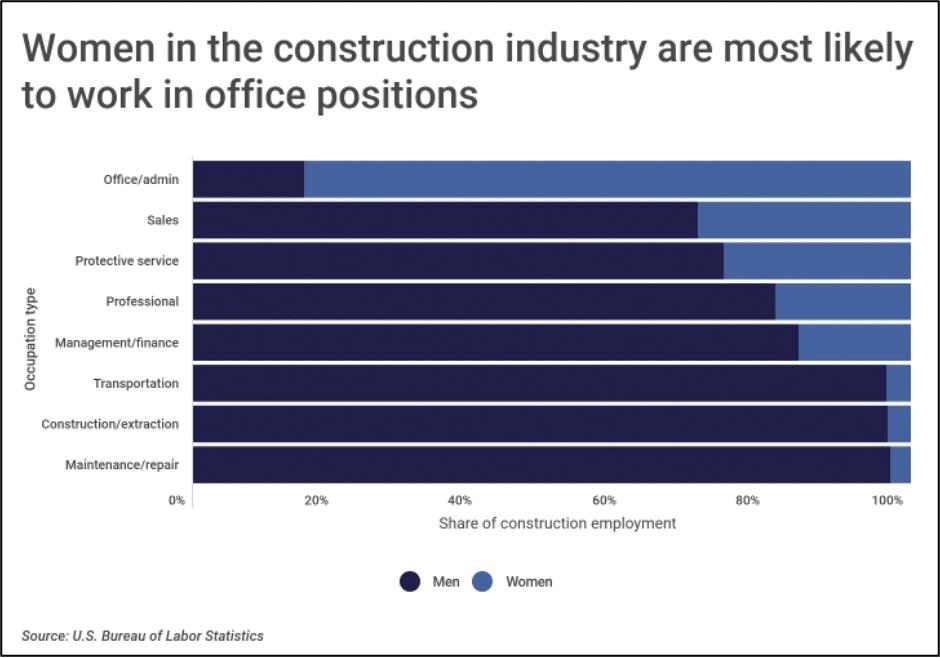
on the cutting edge of bringing that awareness to the construction industry. The other thing that I’m proud of is getting myself involved in national organizations. I’m on the NACOSH committee, and I’m one of the co-chairs on their heat stress awareness program. I’m on a committee called A10, which is construction and demolition standards. I am the chair of the sanitation committee. It’s one of the leading adverse conditions that women find themselves in. When that standard comes out, I’m going to show up as the chairperson of that, and it will affect millions of people. It’s really overwhelming when you think of it like that.

Has there ever been a situation where you were discounted by someone because of gender, and how did you respond?
GR: Yes, I get doubted and questioned a lot. Sometimes it’s because I’m young. Sometimes it’s because I’m a female. What I’ve found to be effective is that I stand my ground and try to explain the rules based on evidence. It’s something I’ve had to work on to get their trust and to know that I’m there to make sure they’re okay. I’m not out to “get” them or inconvenience their work — I’m there for them.
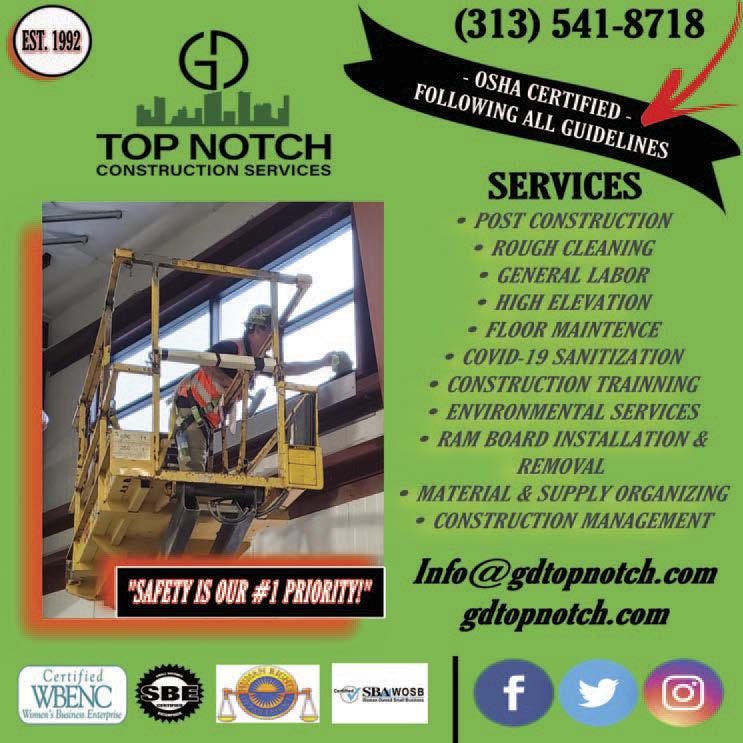
LM: There has not, and I think that’s because I have a master’s degree. I think women have to be more educated than men. Also, you have to have thick skin. The worst thing that you can do is go on the jobsite like, “I’m the boss here.” No one responds well to that.
MV: I honestly feel like being a woman in this field, we get more respect. I think the men are more inclined to help you. Working at the same company for 20 years speaks volumes about that. I love our guys. I have felt welcomed here since day one.
TN: Absolutely, all the time. When I showed up as a crane operator, they were laughing at me assuming I was the flagger. Often I spent the first few hours proving myself, until I became recognized in the industry. I had to prove myself in safety as well. I try to handle everything with a smile and show them with my actions.
KD: As a woman, it’s really tough to be the only one. When I started at Alberici, I was working at a plant and I didn’t see another woman in the field for six or seven months. I’ve been threatened on a job because I tried to enforce rules. I had to learn to work with construction trades. The biggest light bulb that came on was when I accepted that I might be really good, I might be smart, I can write pre-task plans, but when I learned to understand the skills and abilities of the field personnel, it made all the difference in the world. Saying, “Tell me about your work. Tell me what bothers you. Tell me where you hurt at the end of the day,” makes the workers open up and express their concerns.


How do you think we can attract more women to this industry?
GR: I think what can help is to keep promoting STEM as well as any trades work in grade school and high school. Also, telling them about the benefits of working in construction. Also, I think that promoting, highlighting, and celebrating women in construction could help pave the way.
LM: It’s up to the unions to recruit for the apprenticeships and show that women are welcome. I think there’s a long way to go, as far as women in construction. It’s not an easy industry for women.
MV: I would recommend starting young. I made it all the way through college and didn’t even know that careers in the construction safety industry was even an option. At the career expos and other high school events, we need to send women to go over and talk to the girls. I think people need to know that there are a lot of great opportunities. There’s not enough of us, and we have fun. I have more fun at work than most of the women I know. The one thing that is a downside for us is the porta potty situation, and you can quote me on that!
TN: We’ve come a long way, but I think we need to make it a safer environment for women. A female mentor is important. I’ve been a mentor to many women in construction, and the young girls coming up today need us to stand up for them.
KD: For one thing, we need to start very early on to educate people about the good career that construction can provide. We have to embrace DEI (diversity, equity, inclusion) tenants. We have to be unified in better working conditions for women, because those better working conditions for women will translate into better working conditions for everybody. Women are often the last people to be brought on a project and the first ones to be laid off. It’s tough for a superintendent or foreman to see what their real skills are, but if you give those women an opportunity to prove themselves, that’s when they can advance.
What advice would you give to other women considering a career in construction / safety?
GR: First, find a mentor. Having a mentor is crucial. There are a lot of things you won’t learn from the books, that you won’t learn from your OSHA certifications. A lot of things are going to have to be learned from your front-line supervisors, from your mentors, and from putting on your boots and your hard hat and walking the site. The second is to have confidence in your competence, your decisions, and your training. Try to get as much training and certification as possible, as well as field experience.
LM: Get as much on-the-job experience as you can. The more experience you have, the more confidence you have — and that’s the only way you’re going to be able to stand toe-to-toe with someone who is arguing with you. If you know what you’re saying and you have that belief in what you’re saying, because you know it’s the right thing, then you have that confidence. You learn a lot more out on the job than you do in the classroom.
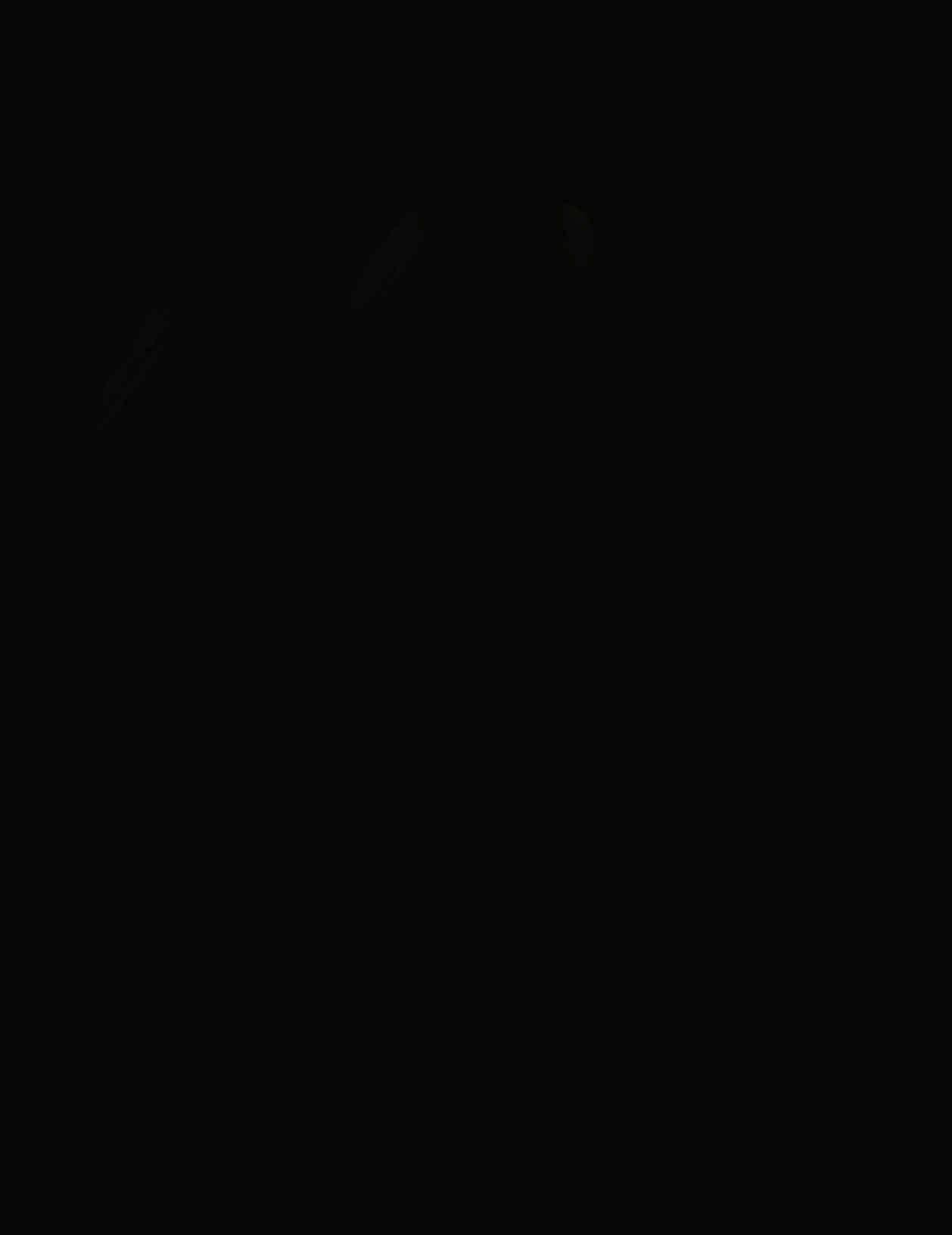
MV: I would say that confidence matters. Break free of the stereotypes. Women are just as capable in this field as men.
TN: Never stop learning. Educate yourself, go to that training hall, go to every MTI class, mentor with other people, and network. If you don’t know something, google it or take a class. Reach out to contacts who can help you get where you want to be. But always keep your smile. KD: When I think about advice for new people coming into the industry, whether it’s a woman or a man, I’d say that it’s going to be a bumpy ride. There are going to be twists and turns and detours that you never thought were imaginable. You’re going to run into roadblocks and challenges that no one ever told you about. But if you persevere through those things, if you take up those challenges and challenge yourself to do better and do more, and if you ask for those opportunities, you’re going to get those opportunities.
Sources:
Cities with the Most Women in Construction
One in Ten Construction Workers Is a Woman
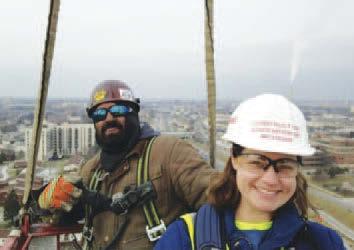
About the Author: Prior to joining the CAM team in 2011, Tracey McLenon held various roles in the construction industry, including parts runner, dispatcher, customer service representative, project cost accountant, executive assistant, and safety director. She has presented construction safety training to hundreds of individuals, including Detroit building inspectors, mechanical inspectors, students at Oakland Community College, and individuals employed by CAM member companies. Currently, she serves as the Vice President of Operations for the Construction Association of Michigan.
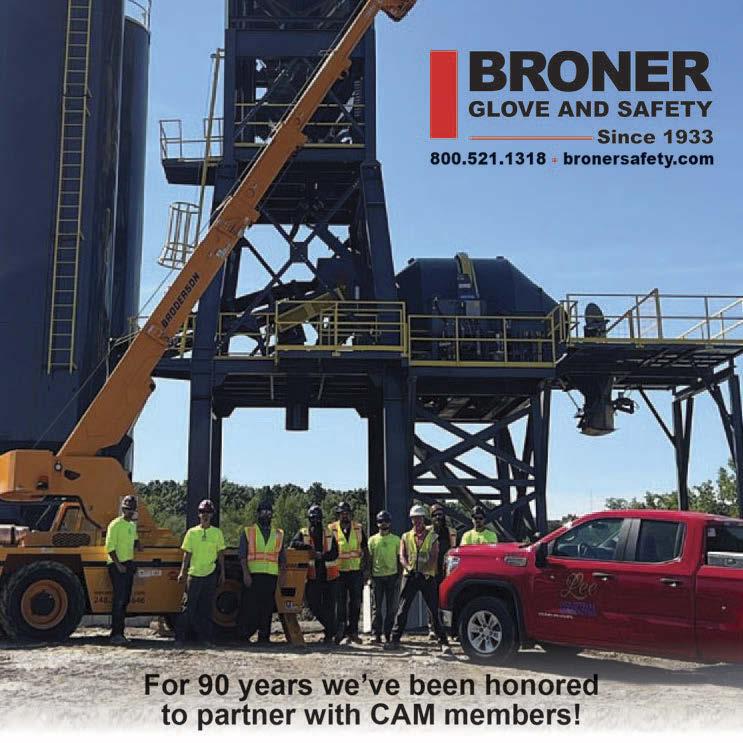
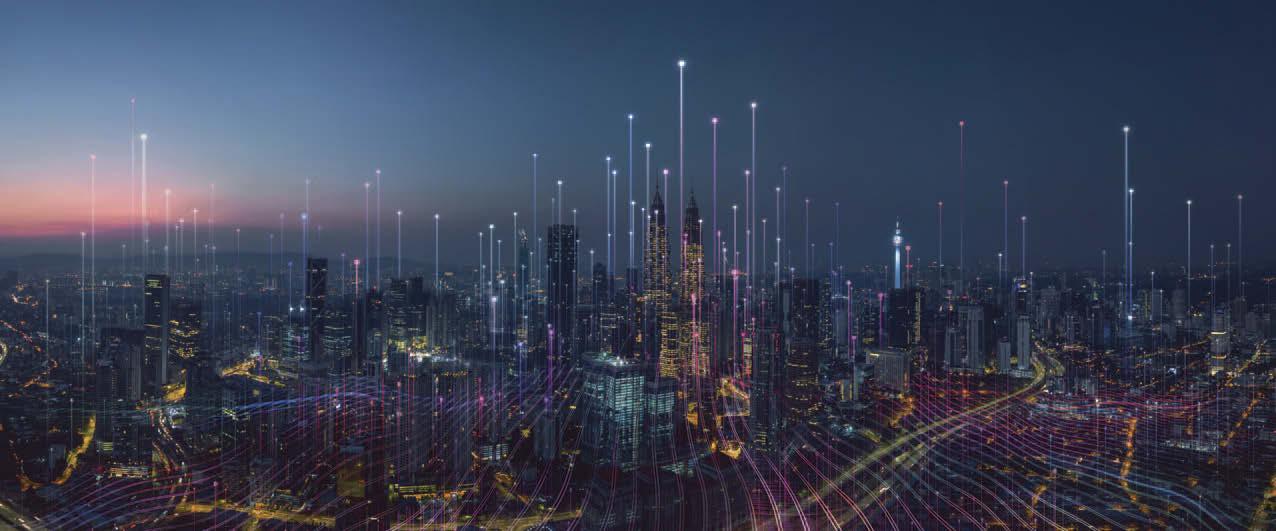
Traveling the Technology-Driven Road to Safer Work Sites
By Brett Gaudreau, Director of Health & Safety, Roncelli, Inc.
Roads? Where we’re going, we don’t need roads! For years, the construction industry has adopted this attitude when it comes to incorporating advanced technology in day-to-day operations. Those days are in the past. When you enter a commercial construction project now, it looks a lot different than 15 years ago. Tradesmen are using tablets, drones are flying, and robots are building. It is easy to conclude that the future is here.
Incorporating new technology in any industry has been considered a step forward. Technology has proven to increase efficiency, reduce production time, eliminate human error, and increase profits. The construction industry is no different, and COVID-19 hit the accelerator forcing companies to make safety programs more efficient through technology.
Safety Documentation Goes Digital With the ever-changing government mandates and many construction projects deemed as essential, companies had to react quickly to stay working safely. COVID-19 health screenings and questionnaires were created and tracked digitally to eliminate unnecessary close contact and allow for contact tracing when needed. Safety orientations held in a job trailer with multiple trades sitting next to each other for 45 minutes wouldn’t work during the pandemic. The answer was creating digital videos to review safety procedures and processes to be accessed via a QR scanner or web address.
Tradesmen entered their training and drug test requirements through an online portal prior to arriving on the project. Project owner and contractor meetings, which reviewed weekly safety performance, were transitioned from in person to online. All of these changes proved that it was possible to incorporate advancing technology into our safety programs and remain successful.
Roncelli recently transferred all project safety documentation from paper to digital. Subcontractors working on our projects are required to digitally submit pre-task plan(s) covering their full scope of work, daily field reviews, equipment inspection sheets, and all other necessary safety documentation. Always striving to improve our sustainability goals, going digital was a bonus. Prior to this, contractor safety paperwork was stored in folders on site and in the main office. To reduce time in managing the folders, and to save a few trees along the way, digital was the best solution. We now store all of our safety documentation in a contractor management software system. That software, like many other contractor management systems, gives the ability for Roncelli, subcontractors, owners, and architects to easily access safety documentation at a click of a button, 24/7. When you enter our projects in the morning, you will see trades huddled up using tablets to review the day’s work tasks, potential hazards associated with those tasks, and control measures to prevent those hazards. When finished, the
trades sign the daily documentation, which is stored digitally in the system. This has increased efficiency within our projects, and our safety teams can now quickly review which subcontractors are following the proper procedures and which subcontractors could use additional coaching to bring them up to our expectations.
The Importance of Human Interaction While there are many positive advantages of using technology in our safety program, we have started to see deficiencies in too rapidly transitioning our safety operations to digital – we began to experience a decline in vital human interaction. When processes go digital, you begin to lose face-to-face interaction. For example, when reviewing digitally imported safety documentation by a trade supervisor, feedback is given digitally in a comment section and sent back for revision with no human interaction. If the trade supervisor didn’t complete a step or experienced interferences, we didn’t have full understanding of why. To correct this, we created a process that, if deficiencies are found in the submittal process, they are to be addressed immediately in person. This way, our team can have a conversation and dissect the root cause of the deficiency and assess if additional training is needed.
As we adopted a digital system, another important lesson learned was that some subcontractors and trades were struggling with the new technology. To combat this, we provided mandatory training on our digital procedures with all who were supervising trades. We also implemented a mandatory notice process when a supervisor is replaced or cannot attend training. Just because the regular supervisor is out for the day doesn’t mean safety takes a day off. The new process ensures that a temporary or new supervisor is brought up to speed immediately.
We also looked at improving our morning meetings with supervisors of trades on site. Continuously reviewing the new tech and processes helped instill a more positive consistent completion rate. Open discussions between different trades and managers about what processes work correctly and what could be modified has helped with incorporating our technology improvements on a dayto-day basis.
Preventing injuries, incidents, and near misses is the focus of a successful safety program, and incorporating technology is a proven effective method to strengthen your safety program and become more efficient. With any new change comes new challenges. We all must be mindful of disconnecting human interaction and losing the important everyday communication – the information that people divulge in a digital comment is almost always less than what you will get from a conversation. If you are not getting good participation or spotty responses to your new digital processes, personal follow-up is critical to success.
I am excited to see what the future holds for advancing technology in the construction safety industry. It's clear that we need to embrace and steadily travel the technology-driven road. But to travel the road safely, digital technology should always be partnered with face-to-face, human communication.
About the Author Brett Gaudreau is responsible for ensuring the overall health and safety of Roncelli’s team members, trade partners, and customers. Brett’s career in construction began with bricklaying before he moved into telecommunications for safety management. He brought his knowledge of safety and construction experience to Roncelli in 2016. Since then, he has enhanced Roncelli’s positive safety culture while reducing accidents and injuries. His most recent accomplishment was leading Roncelli in achieving five million work hours with zero lost-time injuries. He is well versed in many areas of construction, including automotive, healthcare, government, and energy and has recently become a Certified Healthcare Safety Professional.

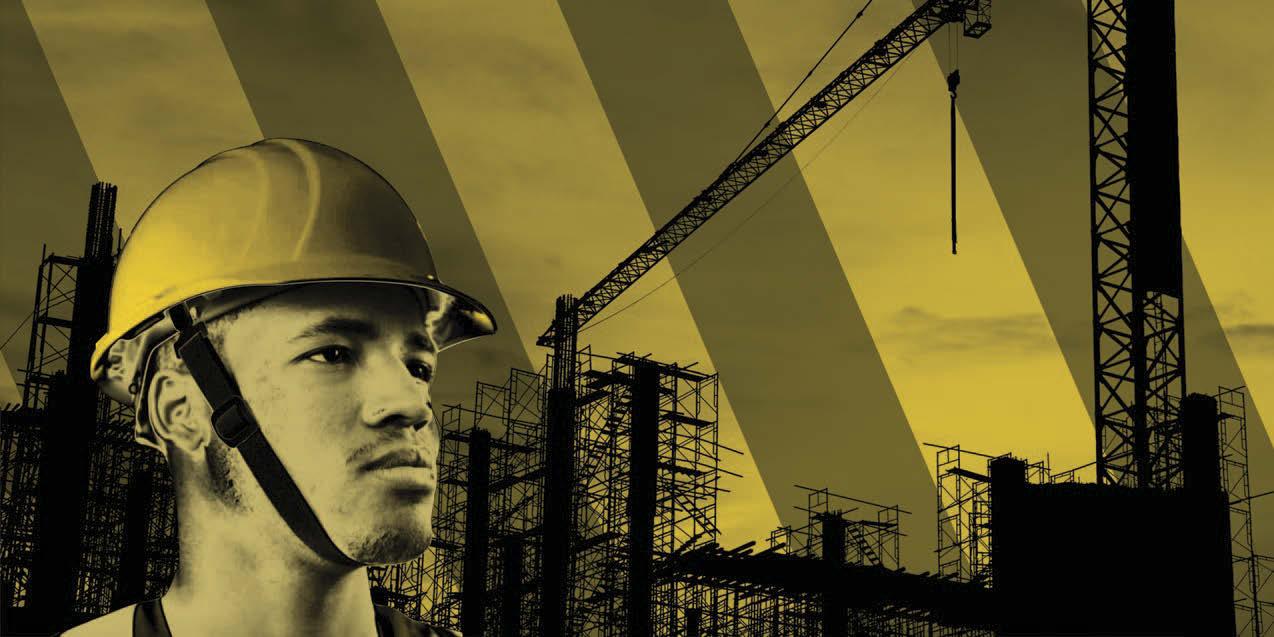
You have all heard it before – the number one cause of deaths in construction is falling from elevation. According to the Bureau of Labor Statistics, there were 1,008 construction fatalities in the United States in 2020 – 35 percent of that number (351) is attributed to fatal falls.
For many years, both the Federal Occupational Safety and Health Administration (OSHA) and Michigan OSHA have been emphasizing the hazards of falling and have been promoting awareness of fall prevention. This includes an emphasis on fundamental provisions such as personal fall arrest systems’ (PFAS) anchorage requirements, guardrail specifications, focus on the conventional methods of fall protection, and a litany of concepts and requirements found in CFR 1926.500 and MIOSHA CSS Part 45.
Has all of that emphasis resulted in fewer fatalities? No. In fact, the number of construction fatalities for which roofs, ladders, or scaffolds was the primary source grew from 2011 to 2019. Why, with all these resources available, are the numbers still climbing?
I have been working with MIOSHA as a construction safety officer since 2003, and for the past decade plus as a consultant and educator. Often when I share my background in the industry, I will be asked in a hushed voice, “What are some of the worst cases you’ve worked on? Tell me about the grizzliest fatalities.”
My response is always the same: “The worst cases? The worst cases are when the victim doesn’t die. When someone dies, it sucks, and it takes a lot for the people involved to get past that point. When someone doesn’t die but suffers a lifealtering, disabling injury, they become a burden to their loved ones indefinitely. That is when my heart breaks.”
One day, I was out with a friend showing her what I do. We had lunch at a Chik-fil-A and, as we were sitting in the parking lot, we watched a construction worker standing on the eighth step of a 10-foot stepladder, drilling into the exterior brickwork of the building. He was facing the ladder squarely and even had a coworker holding the base of the ladder steady.
I asked my friend if she saw anything wrong or dangerous in the scenario. She replied, “Well, he isn’t wearing his helmet.” I responded, “Yeah, his hard hat.” I chuckled a bit, recognizing that there was really no head hazard. “Well, he doesn’t really need one,” I said. “I guess the hammer drill could bite and possibly strike him in the side of the head.” She retorted, “Well, what about when he falls off the ladder? He’s going to hit his head.” I began to chuckle again, and then I caught myself and turned to her and said, seriously, “You’re right. But if he was wearing a hard hat, it would probably fall off as he was falling.”
We carried on from there to observe a roofer. He was walking and working along the flush roof edge of a strip mall, approximately 28 feet up. We continued to digest fall hazards and the expectations of
fall protection. She kept remarking on how confident he was, just walking around up there. I added, “Yeah, and he does that every single day! How long before he trips or missteps?” The obvious answer is: eventually.
I couldn’t stop thinking about her observation about the hard hat. It got me thinking about my very first job as an electrical apprentice. I was on a cooperative generating plant in Windsor, Ontario. Believe it or not, Unistrut in Canada doesn’t have pre-punched holes every two inches. So as a first-year apprentice, I had the task of drilling holes in strut so that we could run conduit on the strut hangers. As I would bend over to drill holes in the strut on the concrete slab, my hard hat kept falling off. I wasn’t concerned because I was all by myself on a concrete slab in the middle of a field, but my general foreman came out to me with a chin strap in his hand. He handed it to me and told me to put it on my hard hat. I looked at him skeptically. “Well, I’m watching you drill those holes, and your hard hat keeps falling off,” he said. “It ain’t gonna protect you if it isn’t on your head!” I felt like such a dork with this chin strap on my hard hat.
Years later, I began working as an enforcement safety officer. During that time, I worked on many accidents – a lot of them were fall-related. Only one fall accident that I ever worked on resulted in death. Incidentally, it was a fall from only about three-and-a-half feet above the object struck, resulting in blunt force trauma and internal bleeding. I thought about all the other falls that didn’t result in death. In every single incident, except one, the victim was wearing a hard hat. And every injury –except one in which a 27-foot fall resulted in pelvic and femur fractures – was a head injury.
I recall years ago, watching the Discovery Channel and documentaries of engineering and construction marvels of the world, noticing how other workers across the globe always wore those hockey helmets or rock-climbing helmets. It made me question: Are Americans not protecting against the number one injury from the number one hazard, all the while saying they are emphasizing fall hazards with hopes of moving the needle progressively without ever talking about actually securing head protection?!
Why is this? People don’t want to look like dorks? Because it can’t be the cost – a hard hat chin strap will run you about $10. The cost of not addressing the number one cause of injury and death in the construction industry is mortally high … by the lives affected, the opportunities missed, and resources lost.
America! The number one cause of death and severe injuries on construction sites is head trauma from falls! If your hard hat is not actually attached securely to your head, it is not providing you any protection … nor is it bravado.
About the Author: Bryan Renaud has been working for Michigan OSHA since 2003, serving roles as a Safety Officer and Safety Consultant. He assists industry partners with understanding workplace safety and health regulations using a pragmatic approach. Bryan is also an instructor with the MIOSHA Training Institute, which offers a full spectrum of construction seminars throughout southeastern Michigan. Bryan gratefully attributes his 10-year career as a journeyman electrician for his passion to pursue progressive, real-world, HR-focused business solutions.
OSHA mandates that construction companies follow the guidelines set forth by the American National Standards Institute to achieve compliance with head protection regulations. In other words, OSHA establishes the rules construction companies must follow, and ANSI Z89.1 details specific steps needed to comply.
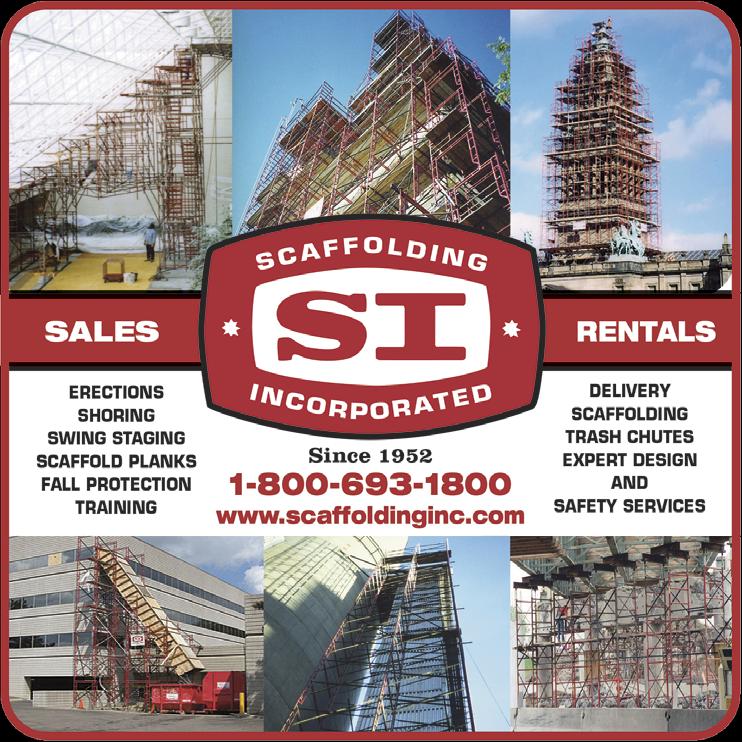
Soaring Eagle’s Guest Room Renovation Completed Seven Months Early

This spacious lounge is part of a premium guest room suite. Photos courtesy of Dave Trumpie, Trumpie Photography

The Soaring Eagle Casino & Resort Guest Room Renovation exemplifies how leveraging Lean principles and adopting a spirit of continuous improvement can lead to world-class results. Despite navigating numerous challenges and delays working within an active luxury resort, the team of Simpson Associates PC, Granger Construction Company, and its trade contractors reached substantial completion approximately seven months ahead of the initial GMP schedule, generating about $17 million in potential additional revenue opportunities for the project owner.
Soaring Eagle Casino & Resort is a premier AAA Four-Diamond gaming and hospitality destination in Mount Pleasant. The Saginaw Chippewa Indian Tribe of Michigan owns and operates this seven-story casino-resort, offering guests top-name entertainment, award-winning dining, high-stakes bingo, and a full-service spa. Given these amenities, Soaring Eagle is one of the top 50 casinoresorts in the United States, according to TripAdvisor reviews.
The approximately 270,000-square-foot project was the first major renovation completed since the facility opened in 1998. The project included the renovation of 516 guest rooms, technological advancements, and infrastructure upgrades to the plumbing, heating, ventilation, and air conditioning systems. According to the owners, this project represents their continued commitment to providing a first-choice destination and to offering great experiences to their guests. The results of this $81 million project include an enhanced level of luxurious designs, contemporary furnishings, and modern technology, including mobile check-in and keyless entry into guest rooms.
SCHEDULE Work was parsed into three phases to allow the owner to continue operating about 213 rooms while each phase was taken offline. With an initial scheduled GMP of about 26 months, the team started work in January 2020, expecting to reach substantial completion in March 2022. However, even after identifying significant complications that could have easily added nine months of delays, the team reached substantial completion seven months early in October 2021. The schedule and work of each phase included: • Phase 1 – Completed in late December 2020, Phase 1 involved demolition and reconstruction of 189 rooms on floors two through seven in the center area of the hotel. The new mechanical, electrical, and plumbing infrastructure needed to support the guest room renovations was completed in the first-floor section directly in the center of the client’s active and secure operations within the back-ofhouse area of the hotel.
• Phase 2 – Phase 2 involved renovating 121 guest rooms on floors two through five, as well as conference and fitness rooms. By implementing lessons learned in Phase 1,the team was able to improve flow, sequencing, and quality for Phase 2, ultimately delivering this phase ahead of schedule.
• Phase 3 – Phase 3 included renovations to the spa and pool, along with the completion of the final 206 guest rooms.
Again, by implementing lessons learned in previous phases, the team completed
Phase 3 ahead of schedule.
This premium suite offers dining or meeting space, an extensive lounge in the center, and a bedroom and sitting area at the far end of the above photo.
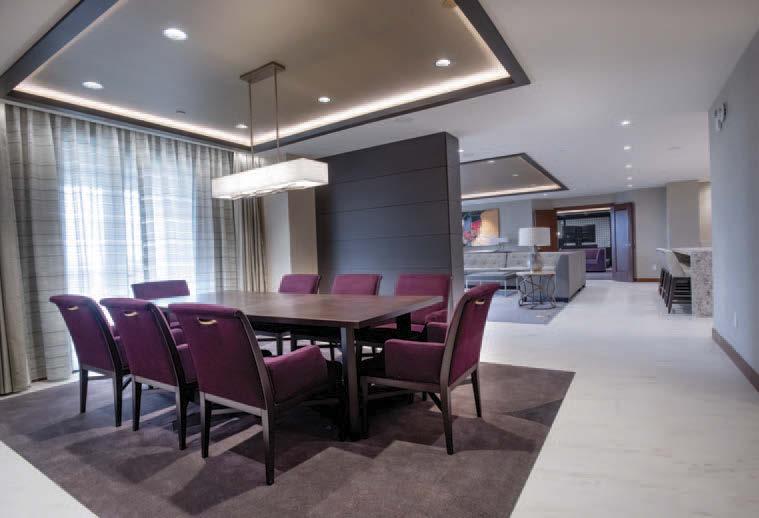
UNIQUE CHALLENGES Several unique factors required the team’s increased attention to innovation, collaboration, communication, and planning from preconstruction through punch-list checkout.
Client: This was the project team’s first time working with the Saginaw Chippewa Indian Tribe of Michigan. As a sovereign nation, the Saginaw Tribe had additional levels of government and community engagement not typically found in commercial construction projects.
The resort facility’s significant revenue stream for the Saginaw Chippewa nation generated a high level of vested community interest in the project. Additionally, the entire project took place inside of an active luxury resort; any downtime or interruption to guest experiences could cause significant, negative financial impacts for the owner.
If 516 rooms were down at any time during this project (with rooms averaging about $200 a night), the Saginaw Tribe stood to lose approximately $100,000 of revenue every day that rooms were unavailable. Therefore, the team needed to be especially mindful in formulating all aspects of scheduling and construction to ensure minimal impact to owner operations and revenue streams. Potential Schedule Delays: The team encountered two factors resulting in potentially 11 months of unanticipated schedule delays: hidden conditions and the COVID-19 pandemic. Regarding the first, within week two of construction, the team discovered hidden conditions requiring measures well beyond what was planned for in the GMP. This could have resulted in about three months of delays per project phase since the work would require measures that locked the team out of their sequencing and kept the team from moving past step one in the critical path.
Regarding the second, because this project fell during local spikes in the COVID19 pandemic, the resort and project team shut down to only critical operations for a one-and-a-half to two-month period. To overcome these challenges, the team worked with the owner to re-sequence and identify critical start and stop points to create a good flow throughout the remainder of the project.
This approach turned a two-year project schedule – which could have been a threeyear project schedule with delays causing potentially $35 million in lost revenue for the hotel – into a 17-month schedule with $17 million of potential gained revenue for the owner in addition to construction cost savings. These successful results were especially important given the owner’s status as part of a sovereign nation and the impact of the resort’s revenue on the overall annual revenue of the Saginaw Chippewa nation.
Even equipment selection played a role in accelerating the project schedule. The demolition contractor, Asbestos Abatement, Inc., purchased a rotating telehandler – one of less than a dozen in the country –specifically for use in this project. Called the Manitou MRT 3255 Privilege Plus, the rotating telehandler “allowed for material haul-out and haul-in operations to happen simultaneously,” said Granger Project Manager Michael O’Rourke. “It provided significant flexibility to pull ahead on subsequent phases as we did not need to wait to erect tower hoists.”
LEAN MINDSET Given the highly repetitive nature of the 516guest room renovation portion of this project, the team saw an early opportunity to engage Lean principles throughout construction. While a few team members had dabbled in implementing some Lean principles on past projects, it was an entirely new concept for most of the team. Fortunately, everyone bought into the idea, and the team now credits this as the overarching factor in the

Artwork and fabric patterns in many of the guest rooms honor Anishinaabe culture. Tucked in a nook in the photo’s righthand corner, a beverage unit – present in almost every room – offers guests a place to chill their drinks of choice. Following Lean principles, the team reduced the touch points necessary for beverage unit installation from six to three.

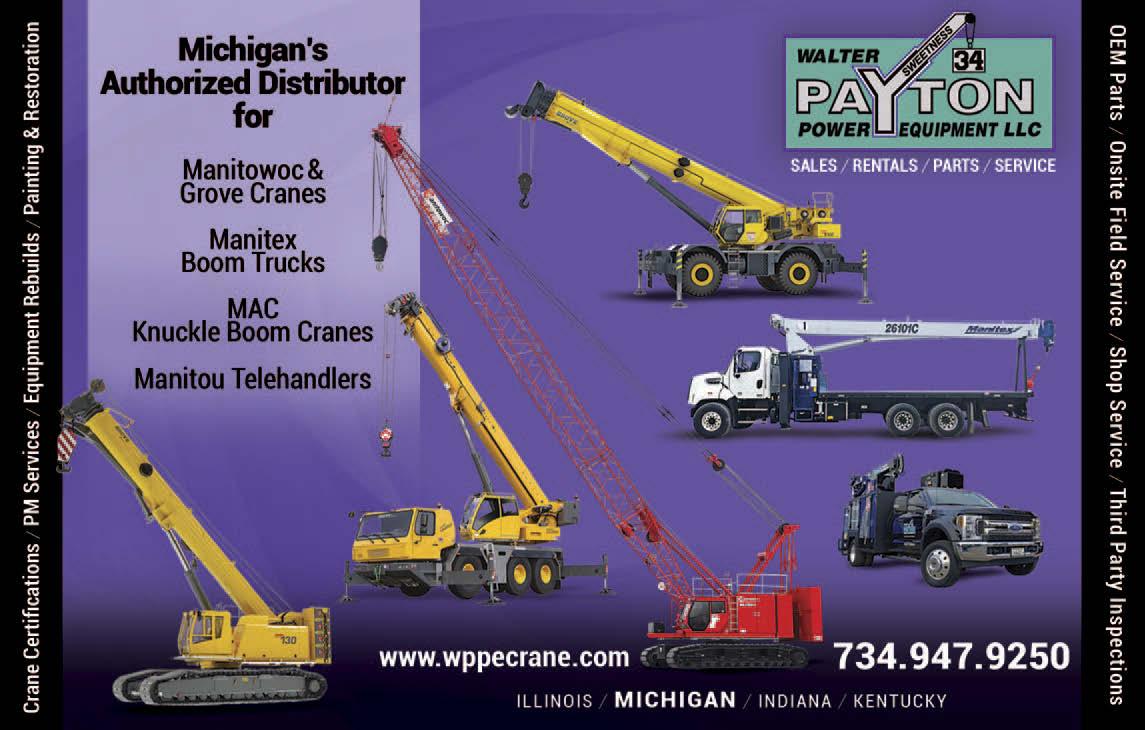
project’s success. Overall, in applying ideas, such as Last Planner Principles, phasing, batching, bottleneck identification, and various processes for sharing lessons learned, the team was able to continually improve throughout the project, reducing waste while increasing efficiency and quality.
Meetings: By frequently meeting with the sole purpose to review lessons learned and retrospectives, the team was able to continuously improve with every phase of construction. During these meetings, team members would share perspectives on past inefficiencies and opportunities for improvement. These meetings also helped build a commitment to trust and open and honest communication across all subcontractors and partners.
The team also incorporated daily huddles as an opportunity for team members on the jobsite each day to meet and coordinate daily schedules, agree upon individual responsibilities, priorities, and commitments, and identify and resolve any constraints. Similarly, the team used afternoon check-ins to review promises made and promises kept that day, as well as potential reasons for changes in plans and look-ahead planning for the next day.
Batch Modifications: During Phase 1, the team was approaching the 516-guest room renovation portion in batches of three rooms per week. However, the team realized this batch size was proving too small for many subcontracting partners, making their ticket management in Touchplan unwieldy.
Knowing they wanted to increase the batch size in Phase 2, the team reviewed the critical path and identified which subcontractor required the longest time for completion. They asked this subcontractor what the maximum number of rooms was they thought feasible for completion each week and used the answering “15 rooms” as the new batch size for all partners to meet.
The team tracked every phase of the project in a warranty tracker to help look for efficiency opportunities. This data also showed a significant drop in claims as the project progressed and the team became more efficient with weekly batches. For example, in Phase 1, the project averaged about 0.6 service request claims per day. By Phase 2, this dropped to about 0.23 per day,


This guest suite, complete with a cozy fireplace, is one of 76 different room types in the 516-room Soaring Eagle Casino & Resort Hotel. Windemuller Electric built and assembled all rough-in and finish components in their shop in Kalamazoo. Called electrical kitting, this prefabrication process reduced waste and improved efficiency, quality, and safety.
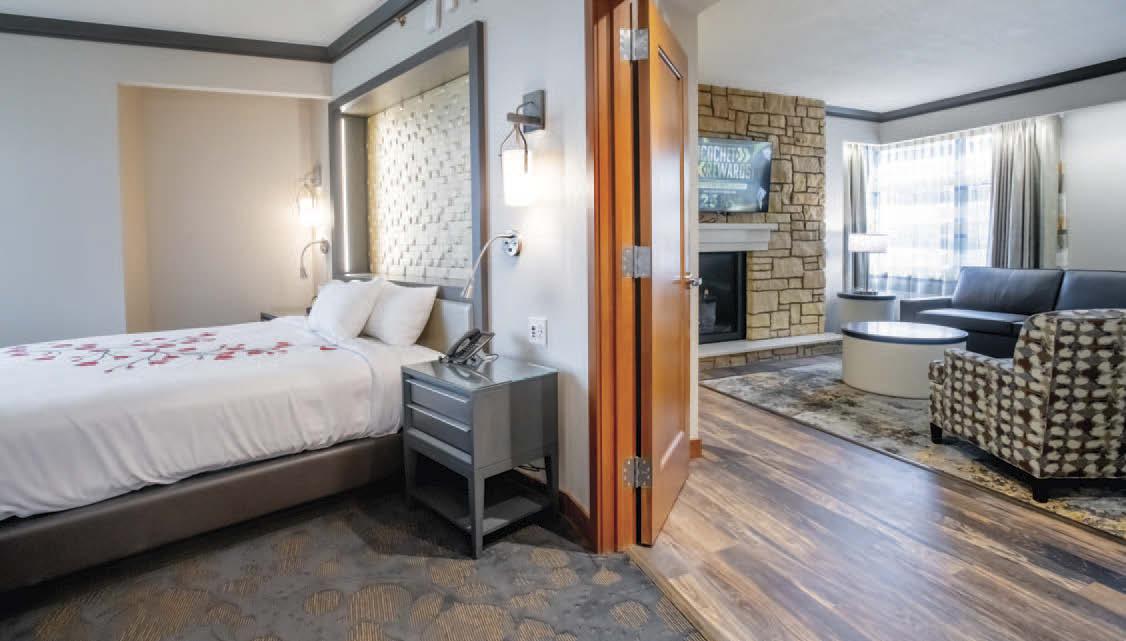

and by Phase 3, decreased below 0.1 per day on average. In all, the team noted the key to successful batching lay in everyone’s willingness to be open and communicative throughout the project, constantly sharing ideas for improvement. No idea was treated as a bad idea.
Cost-Benefit Analysis: During the project, the team found room for improvement in yet another area, namely guest room doors. Initially, the plan was to salvage, refinish, and reuse all doors. However, during the first two phases, the team’s tracking revealed that it was taking on average six to twelve hours of labor per door, including moving doors toand from storage during renovation.
By conducting a cost-benefit analysis, the team was able to calculate that ordering new doors in place of refinishing the salvaged doors would reduce labor time and would eliminate associated warehouse storage and painting material costs. In all, this cost-benefit analysis led the team to shift to using new doors in Phase 3, which accounted for over 300 doors alone in the project. This also provided the owners with a better-quality product overall.
Prefabrication: Throughout the project, the team found opportunities to leverage prefabrication to help reduce waste and improve efficiency, quality, and safety. The first instance of leveraging prefabrication began during postbid conversations with Windemuller Electric. Windemuller proposed providing electrical kitting for the 516-guest room renovation. For all rough-in and finish components, Windemuller would build and assemble everything in their shop in Kalamazoo, then send color-coded bins, customized with instructions and materials for every room.
The resort hotel has 76 different room types, so every five to six rooms are different than the next. This could have proven very challenging to manage in the field. Prefabricating this portion of the project helped with efficiencies, as well as safety and overall jobsite cleanliness. This prefabricated kitting process also ensured extremely detailed, as-built documents for the owner, since Windemuller provided drawings with every room kit.
The success with electrical kitting helped foster additional conversations with other subcontracting partners to explore the potential for prefabrication opportunities. For example, John E. Green Co. built a fab shop on site; in this space, one person assembled all risers and shower valves. Similarly, Granger Construction’s general trades team identified an opportunity to start prefabricating all guest room shelf brackets. As team members witnessed the success of each new prefabrication idea, the process continued evolving throughout the project.
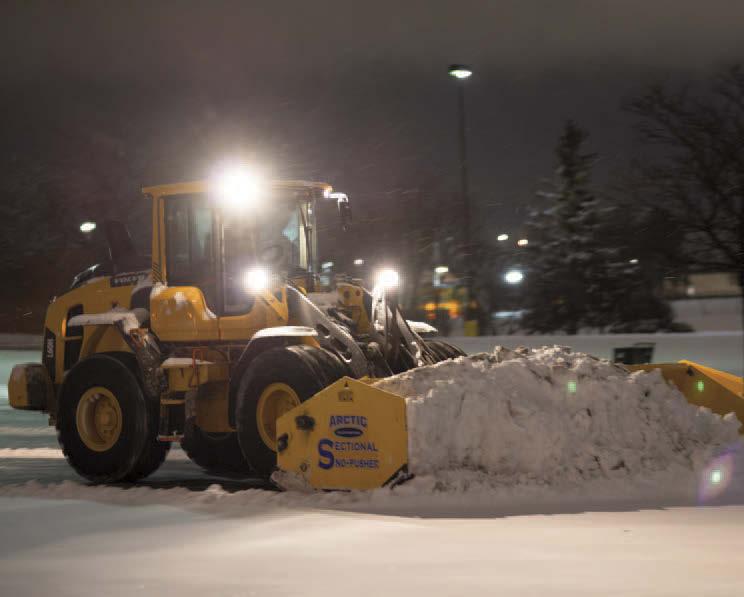
Bottleneck Reduction: As the team looked for prefabrication opportunities, they, similarly, were identifying where bottlenecks were occurring on the project. One such instance was the beverage center units located in 99 percent of the guest rooms. The team calculated that it took six touch points just to complete installation of these units in Phase 1. Moving into Phase 2, the team realized they could reduce the touch points to three by simply sending out the access panels for the beverage centers to a casework shop for plastic lamination.
Initially, the team would place the access panel, then have the electrician move the access panel four to five times while trimming out the room, requiring the painter to do touch-ups after installation. However, by switching from the painted access panel in the field to a prefinished one, they could wait until the electrician and everyone else was done in the room before setting the access panel in place. This approach eliminated handling the access panel multiple times and eliminated the need for touch-ups. Lessons-Learned Mentality: The team’s success at the Soaring Eagle Casino & Resort Hotel exemplifies their approach to continuous quality improvement. For instance, one complete room was finished for use as a mock-up. The team learned from this initial installation to improve upon details and to review material selections and installation sequencing, as
PUSH SNOW PUSH BOUNDARIES
Gearing up for snow season? Be ready for anything when you have the combined power of oo and rctc on your side. With the reliability and performance of Volvo paired with the adaptive and efficient design of Arctic, snow will never put a freeze on your operations. Get the snow removal equipment you need from your partner in preparedness, Alta Equipment Company.
Contact our nearest branch:
Burton | 810.744.4840 Detroit | 313.394.1811 New Hudson | 248.356.5200 Sterling Heights | 248.356.5200
844.Go2.ALTA
Byron Center | 616.878.7450 Gaylord | 989.731.9988 Sault Ste. Marie | 906.259.8313 Traverse City | 231.943.3700
www.altaequipment.com
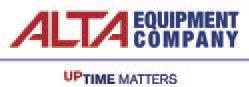
well as to determine the process for making immediate improvements.
As rooms were completed in phases, the team created a web-based warranty and punch-list application for reporting defects based on defect category. The application allowed the team to notice trends in defects, enabling them to react and prevent the repetition of any issues. The team tracked the number of defects during the project to demonstrate that the improvements made resulted in an increase in quality.
FFE: Given the large scope and challenging nature of this project, the team had an intended flow of work. Communicating that flow internally between the team, who was living and breathing the project, was one thing; integrating with Soaring Eagle’s operations was another. The owner had to know where and when their own team members could start managing furniture, fixtures, and equipment (FFE).
As a communication aid, the team created a live tracking schedule and updated it twice a week. The live tracking schedule was sequenced to a map, enabling the owner to visually see which rooms their own team could enter and on which days to work on what. This helped pull ahead owner occupancy significantly.
Thanks to this well-executed application of Lean principles, Granger Construction and the entire project team delivered the renovation of 516 guest rooms seven months early, giving each returning or prospective guest even more of an opportunity to – as Soaring Eagle’s website states – “Immerse yourself in luxury and escape the everyday.”
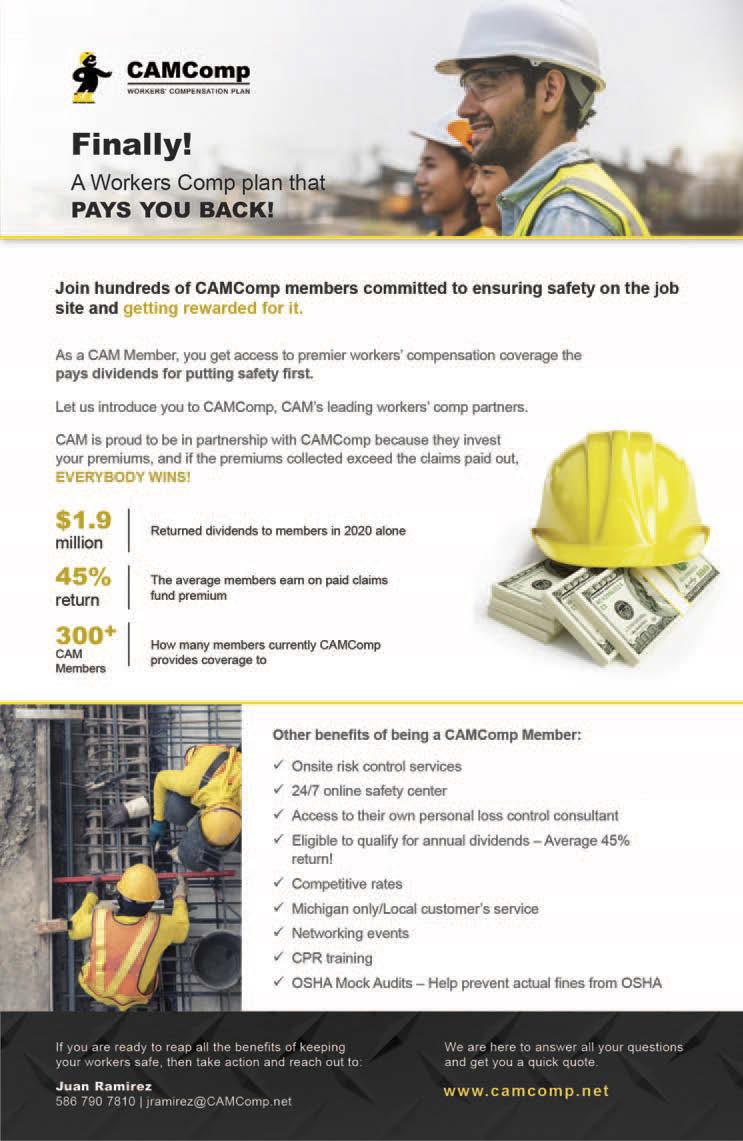
-Content courtesy of Granger Construction Company and CAM Magazine editorial staff
The following are some of the major participants in the Soaring Eagle Casino & Resort Guest Room Renovation Project:
• Caulking & Sealants – RAM Construction
Services of Michigan, Inc., Livonia • Communication & Low Voltage – Pro-Tech
Cabling Systems, Inc., Clare • Drywall & Acoustical – Metal Arts
Construction, Mt. Pleasant • Electrical – Windemuller Electric, Inc.,
Wayland • FF&E Integration – LEAP Hospitality,
Liberty, Missouri • Fire Alarm Systems – Summit Companies,
Traverse City • General Trades – Granger Construction
Company Construction Services, Lansing • Glass & Glazing – Lansing Glass
Company, Lansing • Hard Tile – Master Craft Carpet Service,
Inc., Plymouth • Painting – Detroit Spectrum Painters, Inc.,
Warren • Plumbing, Mechanical, Fire Suppression –
John E. Green Co., Cincinnati, Ohio • Selective Demolition – Asbestos
Abatement, Inc., Lansing • Soft Flooring – William Reichenbach
Company, Okemos • Window Coverings – Fabtex, Inc., Orange
County, California
A widescreen and a table with a waterfall edge are other amenities of this premium suite’s meeting space and/or dining area.
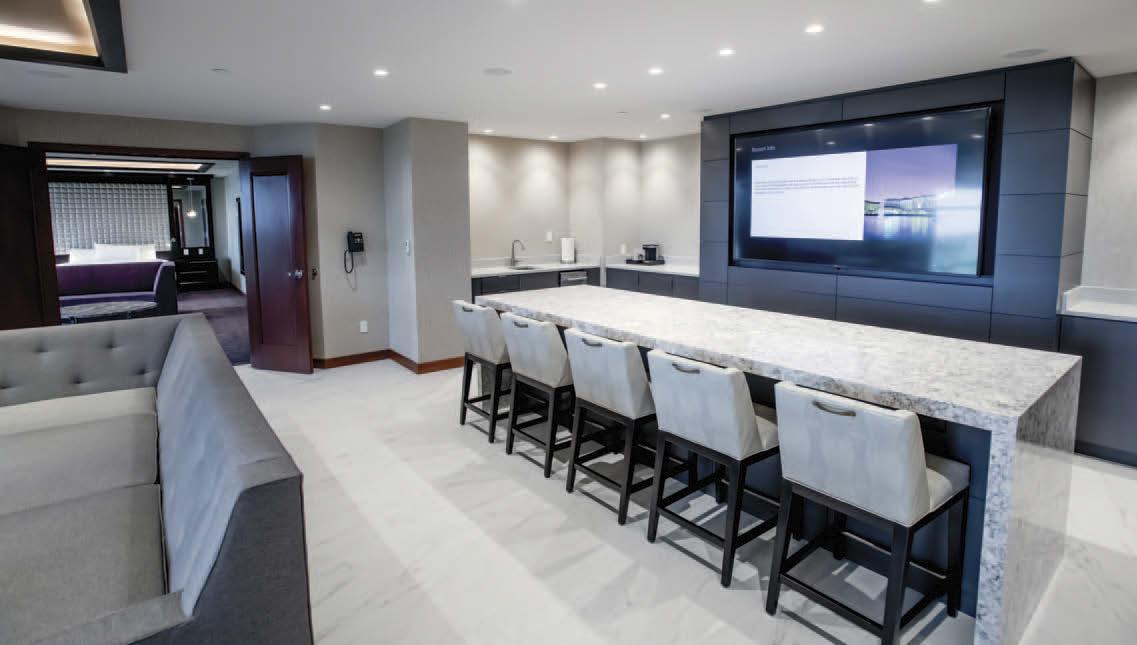
