
7 minute read
Out and About
Hladun receives grant for research
By Murray Green
The Alberta Innovates’ Carbon Fibre Grand Challenge is accelerating the development of pathways for large-scale production of carbon fibre.
They are advancing manufacturing products from Alberta’s bitumen. “Carbon fibre’s high strength, stiffness and corrosion resistance, coupled with its light weight, make it better than many conventional metals and polymers used in transportation, infrastructure, construction and consumer products,” explained Tony Hladun of Camrose, one of the recipients of a grant.
“Back in 2015-16, when the NDP were elected they had an initiative to look at uses of oil other than burning it. It was called the Bitumen Beyond Combustion Initiative,” explained Tony. “They wanted to know what to do with heavy oil. It was environmentally driven and they wanted sustainability. At that time, one of the ideas that I had from my previous engineering work was the idea of making carbon fibre. It can be made from heavy oil because it is basically carbon and hydrogen but it is quite a complex manufacturing process. Deanne Morrow and I couldn’t get the province to move on it then, so we stopped.”
Alberta’s abundant bitumen feedstock is uniquely well-suited to advanced manufacturing applications and significantly less expensive than existing sources. The potential to dramatically lower input costs for advanced materials opens the door to large scale production demands and markets around the world. As a result, the global carbon fibre market is expected to grow ten-fold due to uptake from the automotive industry alone.
“During the first research period I made a connection with Clemson University in South Carolina. They are the world experts in carbon fibre manufacturing. When this Carbon Fibre Grand Challenge came along in January, I teamed up with them to put a bid in together. The research is done at Clemson and I am the project coordinator and the liaison with Alberta Innovates, which is the government agency sponsoring the work,” said Tony.
Commercial markets for non-combustion products from bitumen could quadruple the current value of Alberta’s bitumen output. Markets for carbon fibre and other asphaltene products are valued at an estimated $84 billion annually. GHG emissions would be reduced at the point of consumption as bitumen is diverted from combustion.
“Clemson has some Alberta heavy oil and they are using their technology to actually make carbon fibre. Over the next four or five months they are going to see what quality they can get and to see if it is a viable process,” shared Tony.
Successful Carbon Fibre Grand Challenge phase one projects from Alberta, across Canada and around the world will accelerate development of this technology significantly. Top labs are now working to produce carbon fibre from Alberta’s bitumen-derived asphaltenes.
“There are many uses of carbon fibre, but the three main uses of it are in blades of large windmill generators, in cars and transportation, and in the construction of new aircraft. You can greatly reduce the fuel consumption when half of the plane is carbon fibre. Carbon fibre is six times stronger than steel and half the weight of aluminum, so it is very strong and very light,” added Tony.
Other uses are for sporting equipment such as hockey sticks. “You could make canoes that weigh 10 pounds so that anyone could
Tony Hladun
carry over his/her head. Another use is in building construction. Now you mix rebar with cement to make it stronger. Rebar can rust, but carbon fibre will never rust away and it will last a lot longer. Right now it can be used in making construction repairs. We need to see how cost effective it is for other uses.”
Many winners will provide additional resources toward the challenge projects beyond the Alberta Innovates’ $1 million investment in phase one.
“Carbon Fibre derived from Alberta’s bitumen is a significant opportunity for Alberta to diversify our natural resources sector, create jobs, open new markets and grow the economy,” said Tanya Fir, minister of economic development, trade and tourism
“Alberta has the potential to transform global advanced materials markets and produce billions in new revenue for the province from bitumen feedstock. By bringing the best ideas from around the world into Alberta, we can expedite the development of these new technologies and position Alberta as a leader in this area,” said Laura Kilcrease, CEO, Alberta Innovates.
“The Carbon Fibre Grand Challenge is delivering on the promise of innovation and creating chemistry for a more sustainable and prosperous future for Canada’s natural resources. As a leader in the chemistry industry, BASF is proud to support its success,” said Daniel Hebert, head of business development-western Canada, BASF.
Zetetic Associates of Camrose, Hladun’s company, is researching valueadded conversion of Alberta bitumen into high performance carbon fibres. He received $49,500 and partners with Clemson University in South Carolina on research with Professor Amod Ogale and his students. In total, 20 universities and research companies received grants to study all aspects of carbon fibre.
Alberta Innovates’ Carbon Fibre Grand Challenge (‘CFGC’) is a $15 million, three-phase competition with the objective of accelerating the development of large-scale production pathways for short and continuous carbon fibre from bitumen-derived asphaltenes and promoting their use in manufactured products.
“Carbon fibre is an important part of the future because of the indestructible nature of it. When I started, that was a positive thing to build upon, not a negative of the oil industry. Right now, carbon fibre sells for $10 a pound. It is expensive, but the object is to make it cheaper. When you look at the value of heavy oil, a barrel weights about 400 pounds. If you could convert a barrel of heavy oil into carbon fibre, now this is simplified, but it has the potential to be $4,000 a barrel. Now a barrel of oil is $40, so you can see the incentive to try and make carbon fibre. You tremendously increase the value of heavy oil,” Tony explained.
“The process involves heating the oil, so that is a good use of the natural gas that we have as well. It is not seen as carbon free, but it is a low emissions use of
Enjoy a
at your

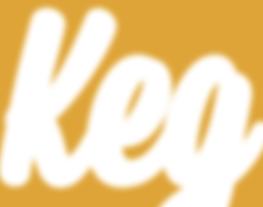
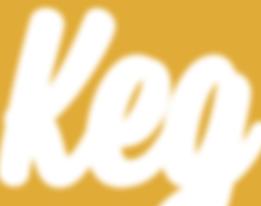






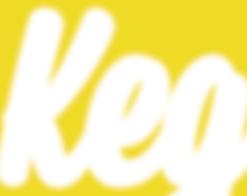

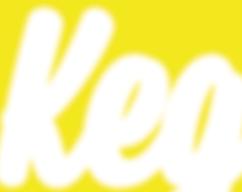

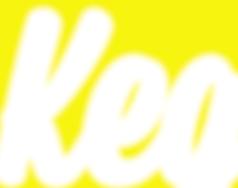
ONLYONLY $ 120 30 LITRES
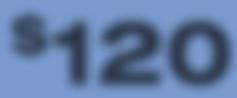




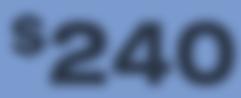
ONLYONLY $ 240 59 2 /3 LITRES
1.89 L GROWLER $ 12 REFILLS
FRESH BEER MADE RIGHT HERE.
in the Norsemen Inn 780-672-9171 www.norsemeninn.com
the fuels. Using natural gas is a way to add value to the product,” suggested Tony.
“Canada is the world’s fourth largest oil producer, so our oil industry is huge. It will help that industry be sustainable and environmentally friendlier. We want to be less wasteful and build things that last.”
The CFGC is part of the Bitumen Beyond Combustion (BBC) program–an initiative by Alberta Innovates to create a multibillion-dollar, value-added industry around the development of non-combustion products and their production technologies, derived from bitumen contained in Alberta’s oil sands.
The oil sands are amongst the world’s largest hydrocarbon resources, with proven reserves of approximately 170 billion barrels and current production of three million barrels per day. At present, most bitumen products are destined for energy generation by combustion (such as gasoline, diesel, and heating oil). BBC diverts bitumen away from combustion but creates advanced value-added products for the future.
Continued to page 30
BEER CLUB Alberta Craft Beer Tasting Saturday, Aug. 29 at 7:30 p.m.
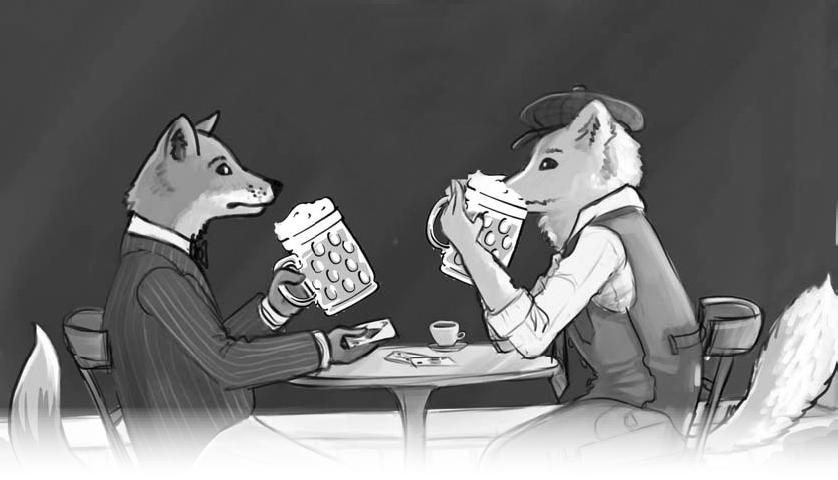


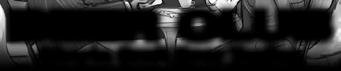
Beer 101 with Cole Boyd of