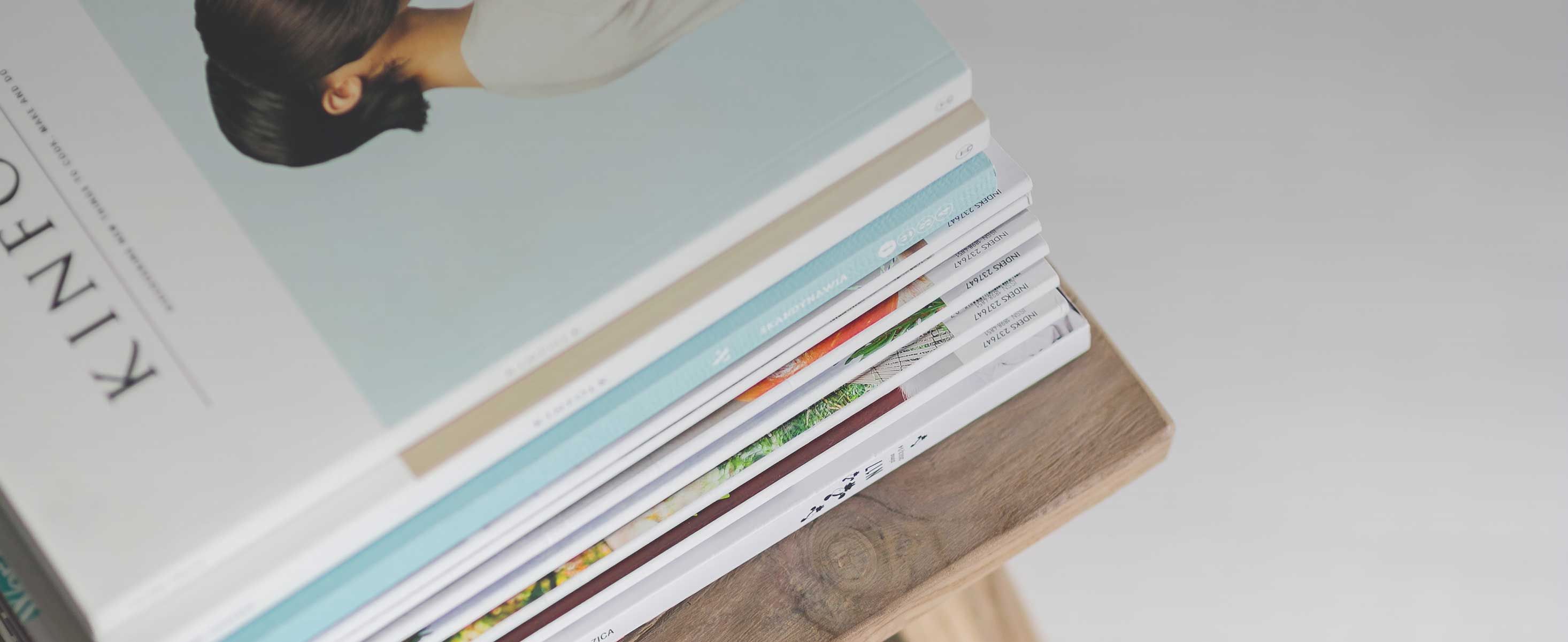
2 minute read
Mining methods
The preparation process is crucial in readying coal and minerals for the marketplace. This step assures that the resource sent to the end user is of the highest possible quality. In the case of coal, there is also an environmental benefit — physical coal cleaning can remove as much as 90 percent of the inorganic, or “pyritic,” sulfur that could otherwise contribute to emissions during the combustion process.
Preparation plants crush and screen coal and employ a circuit of cleaning techniques to remove non-coal materials and separate the coal into different quality grades.
And for some minerals, including structural materials like sand and gravel, washing and separating for size is typically all that is involved.
For metallic ores, however, it is a different story. The number and complexity of steps in processing these ores is often directly related to the complexity of the ore itself and the degree of purity needed for the end product.
In order to separate the mineral from surrounding ore, the first step is typically to transport the ore to a mill, where the mineral is concentrated. The process begins by crushing or grinding the ore to the degree of fineness needed to extract the mineral material contained within. Then the mineral is physically separated by leaching (using a percolating liquid to remove soluble parts), flotation or solvent extraction.
Flotation is a chemical and physical process in which the ground ore is mixed with water and a foaming agent. The slurry is then agitated, much as if in a washing machine, and bubbles are created. The mineral material attaches to the bubbles and floats to the top to be skimmed off. This process makes it possible to access lower-grade mineral deposits that otherwise would not be utilized. Solvent extraction-electrowinning (SX-EW) is a process that is used in copper production. The process uses electricity to extract the metal from a solvent solution and attach it to a cathode. SX-EW has increased in use since the mid-1980s partly because it can recover copper from lower grade ores that otherwise could not be processed.
For both coal and minerals, the processing step is referred to as beneficiation – the processing of coal and ores to regulate size, remove impurities and improve quality. Some minerals undergo further refinement, sometimes by a smelting process, to obtain the desired degree of purity. Once this level of purity has been achieved, the mineral is ready for commercial use, whether gold for electronics and jewelry, copper for plumbing or electrical wire, or one of many other potential end uses.
U.S. Per Capita Consumption of Minerals and Coal, 2018
Mineral Pounds
Cement Clays Coal Copper Iron Ore Lead Phosphate Rock Salt Sand and Gravel Stone Zinc
675 155 4,206 12 256 12 182 384 7,345 9,924 6
Manganese Uranium (2014) 6 0.15
NMA calculations based on preliminary USGS, EIA and U.S. Census Bureau data.