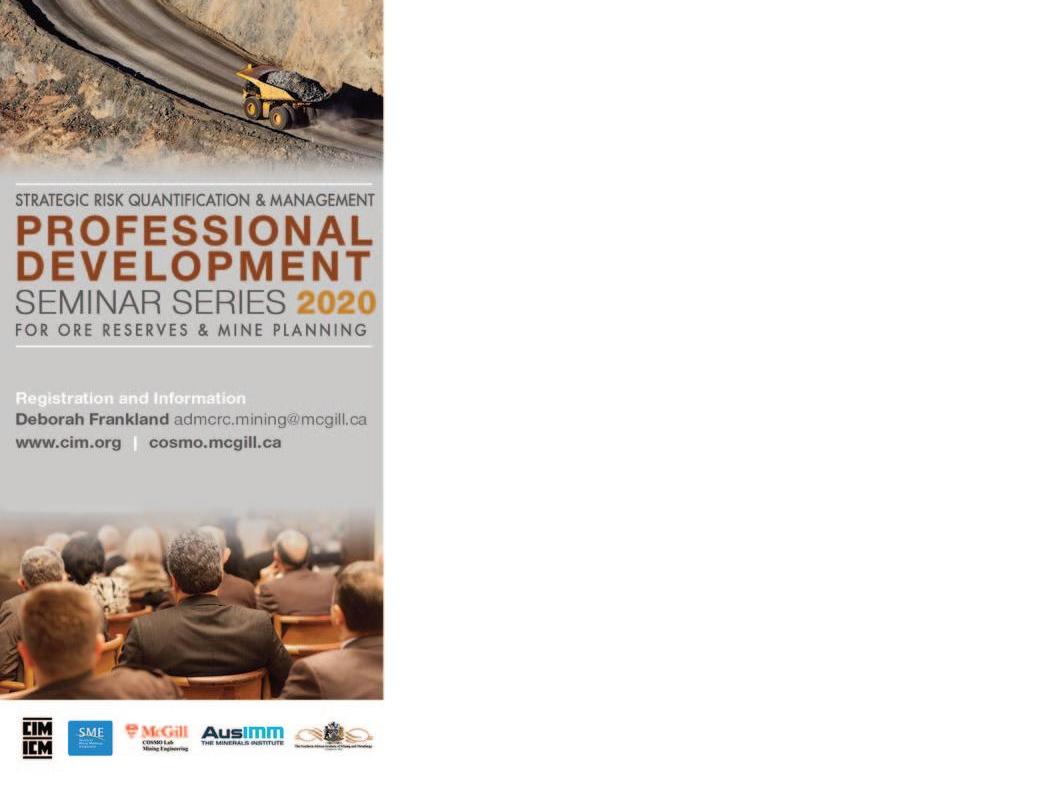
26 minute read
Guidelines for remote site inspections
How to perform a remote site visit
By Avakash Patel, P.Eng
Mine site visits have long been held in high regard by prospectors, mining companies, regulators and investors. There is no doubt that having a technical team available to view any asset and provide observation and opinion is critical to understanding the asset. Most professionals agree that the cleanliness and hygiene of a site, facility, operation and their respective sub-parts reflect the management, project, operation and culture in general. Given the many restrictions on travel under the current circumstances and the possibility that at least some could remain in place for an extended time, remote visits where a professional or a team view and observe a site without being physically present demand special attention.
A site visit is normally used to validate information and data on a particular property. During any site visit, even a remote one, a number of peripheral observations happen naturally that can help form an opinion on the property, management and operation.
A remote site visit can never completely replace an actual site visit.
The intent of this guideline, adapted from a larger guideline on mine site visits, is to provide as much information as possible about remote site inspection to reduce the risk of a desktoponly or data-room review. The word “virtual” is not used here because this guideline covers actual site visits, where both images and sounds are live, not created in computer graphics. Many engineering, procurement and construction management companies produce virtual 3D models that are based on engineering design, but 3D models are generally not as-built, and in some cases, a follow up physical inspection is necessary for certain disciplines. A remote site visit can reduce the risk of reliance on reports and data without personal physical confirmation, and if performed properly, the information and data validation will be sufficient to reduce the risk associated with a desktop-only review.
Prior to a remote site visit
Prior to the site visit, the maximum possible data and information should be gathered. It is helpful to ensure that the data is evaluated, understood and assessed for any gaps that the site visit may need to address.
A parallel site team should be established to carry out the visit. Each remote discipline lead (RD) responsible for the visit should be assigned a local counterpart site inspector (SI) who will collect and transmit the required site sensory information. Although preferable, it is not required that the SI be a specialist in the discipline of the RD. Each SI should be provided instruction regarding how to properly use any communication, measurement or documentation equipment.
There are two parts to the technology required to carry out a remote site visit. The first is real-time communication methods, including compatible software for transmission and reception. The second is the equipment and the software necessary to gather and transmit sensory information. This equipment can vary from a simple smartphone or tablet to surveying and measurement tools, including helmet cameras, eye glass cameras, microphones, and drones. Full agreement must be made on the technologies to be used for a remote site visit. A trial run is recommended to ensure the equipment and software works and to ensure the SI can successfully use it.
It is recommended that a two-part meeting between RDs and SIs be held to coordinate the site visit. The first part of the meeting should include the entire team to highlight the scope and intent of the visit*. The second part is for each RD to coordinate with his or her respective SI individually.
A number of activities need to be performed in preparation for part two, including but not limited to: • The RD should provide an agenda and plan for the locations and areas they would like the SI to visit. • The RD should send through the main elements to examine in each area. This will be the map/schedule for the remote site visit. • The RD and SI should discuss the merits and weaknesses of the plan and finalize the actual “tour route” or “remote map.”
Mobile communication devices need to be tested in all regions of the visit and facility. If live communication is not possible, then the method for storage and transmission of information must be agreed to. A recorded method can be used for instruction and for feedback when live communication is not possible. Ensure all communications devices are fully charged and have backup sources of power.
The preferred methods of communication should be Wi-Fi or cellular, but if these are not available, then the site technology would govern how communication can happen between the RD and SI. A smartphone or helmet camera with audio is best suited for the SI.
Do a trial run. The SI should ensure that he or she can view what the camera lens captures. In the case of phones, the front camera can be used, and in the case of helmet cameras a remote or heads-up display can be used. Also make sure that photos can be taken directly by the RD through an application or by taking screen shots. The SI may also take and send photos to the RD. Upon approval and instruction, the SI can also take short videos as necessary.
During the actual inspection, the RD will instruct the SI to move the camera slow and steady for optimal video, or to zoom in and out as necessary or to move closer or farther away or a different direction, so there must be agreement on the camera movement terms (i.e., pan, directional movements, zoom in/out) and calibration.
For safety, it is critical to emphasize to the SI the importance of being aware of surroundings and watching where he or she is
walking or stepping to avoid trips or falls. The SI must keep his or her eyes on the walk path at all times, not on the display of the device transmitting information.
Once the RD and SI work through the above details and do a trial run, they should be ready for the inspection. In some instances, periods with no Wi-Fi or cellular connection or delayed audio or video transfer may present a challenge, but it is generally not a significant barrier to completing an effective inspection.
Finally, a full schedule should be developed to match both physical inspection and interview time. This needs to be coordinated to have live conference video to discuss observations and address questions with operational, maintenance, project, and/or management personnel before the date of the visit to establish on-site availability or at minimum availability for communication.
Remote site visit
For a comprehensive remote inspection, it is recommended that the SI does two site inspections, on top of the trial run. This will allow for communications issues and errors, and for changes in real time differences in observance. Two separate inspections will provide the RD the opportunity to go through the first transmission and create a comprehensive list of items to capture that were missed during the first inspection. A second inspection will give the SI the opportunity to prepare to capture items that were not captured during the first inspection.
When possible, if matching “tour routes” or “remote maps” between multiple disciplines, it is possible that the second inspection can be a team or grouped inspection, with one SI serving multiple RDs. This is only possible once each RD has completed the first inspection, and has conferred with other RDs on the team to see if synergies exist.
A final report should be provided by the SI of what was inspected, viewed or observed. It should include schedules, dates and times as necessary, and it should be provided to the RD as proof and documentation of the remote site visit. This documentation is critical to establishing a record of what was requested to be viewed and what was actually viewed.
Technologies
There are a number of technologies that can serve for remote site inspection, including smartphones or tablets, helmet cameras, eye glass cameras, microphones and drones. Keep in mind that since there are practical limitations of control, timing, capacity, accuracy, depending on the complexity of the technology, more than one technology should be used to complete the remote site visit. The redundancy can bridge any gaps between the technologies used.
CIM
This column was excerpted and adapted from “Mine and Mining Project Site Visit Guidelines: A Practical Approach.” Read the full guidelines to performing remote site visits at https://www.rpmglobal.com/wp-content/uploads/2020/04/ Mine-and-Mining-Project-Site-Visit-Guidelines-A-Practical-Approach.pdf. Avakash Patel, P.Eng., is President – Advisory and Consulting Americas at RPMGlobal. He has worked for junior and major mining companies, as well as for top-tier EPCMs. He has been involved in various stages of project development and his experience spans multiple commodities and locations globally.
Strategic Mine Planning with New Digital Technologies, Risk Management and Mineral Value Chains
At the time of a continuing rebound of metal markets, learn how the application of new digital technologies can add substantial value to strategic mine planning and asset valuation. The new technologies and related tools integrate technical risk management while capitalizing on the synergies amongst the elements of mineral value chains through their simultaneous optimization – from mines to products to markets. INSTRUCTORS Roussos Dimitrakopoulos, McGill University, Canada and Ryan Goodfellow, Newmont Goldcorp, USA • DATE September 2020 • LOCATION Montreal, Quebec, Canada
Geostatistical Mineral Resource Estimation and Meeting the New Regulatory Environment: Step by Step from Sampling to Grade Control
This course is designed according to the latest regulations on public reporting of Mineral Resources. It aims at showing how state-of-the-art statistical and geostatistical techniques help answer the requirements of those regulations in an objective and reproducible manner. A particular emphasis is put on understanding sampling and estimation errors and how to assign levels of estimation confidence through the application of resource classification fundamentals. In addition to a solid introduction to mining geostatistics, this course provides a comprehensive overview of industry best practices in the broader field of Mineral Resource estimation. INSTRUCTORS Georges Verly, Wood, Canada and Roussos Dimitrakopoulos, McGill University, Canada • DATE September 21-25, 2020 • LOCATION Montreal, Quebec, Canada
Five 5.6-megawatt, high-efficiency Wärtsilä generators provide power to Agnico Eagle's Meliadine mine in Nunavut. Heat recovered from the generator engine exhaust is circulated through the mine site, providing heat to surface buildings and underground operations connected to the hot-water loop.
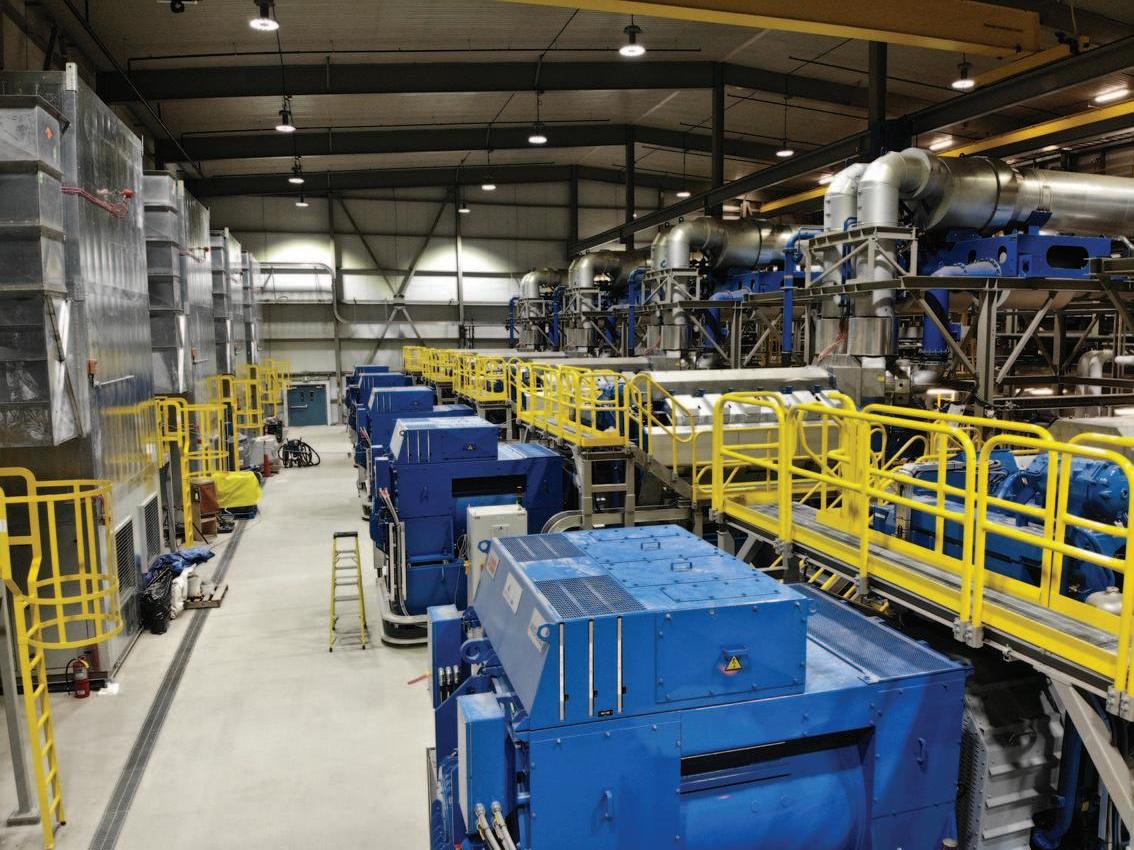
Taking heat
High-efficiency gensets, fuel flexibility and smart load-shedding help cut diesel needs at Agnico Eagle’s Meliadine cogeneration plant
By Herb Mathisen
The construction and commissioning of Agnico Eagle’s Meadowbank mine – the gold miner’s first foray into the Far North – was an educational experience with a steep learning curve. Logistical, operational and human resource challenges tested the company’s ingenuity and taught it a lot of lessons about how to bring a mine into production and keep it operating: lessons that Agnico Eagle applied to Meliadine, its second mine in Canada’s Low Arctic.
Those learnings extended to the powerplant as well. Meadowbank’s heat recovery system – using by-product thermal energy from electricity-producing generators to heat operations – worked well in theory, but not so much in practice. “Mostly, people design as if the gensets are going to be running full steam, super hot, whereas we know that, in general, they always run a bit lower to keep some reserve and make sure there are no blackouts,” said Nicholas Allen, a mechanical engineer at BBA. The engineering firm was brought in to optimize the plant between 2012 and 2014. “As soon as you go off of that perfect operation, it’s not efficient at all.”
But getting the most out of heat recovery systems is crucial in Nunavut, where Agnico Eagle relies on diesel for all of its energy on site. “We have other mines in southern Quebec and more down south in other countries. At those mines, we’re thinking about energy optimization but we take it to another level in Nunavut,” said Éric Lavoie, an electrical engineer with Agnico Eagle who worked closely with Allen on the design of the plant at Meliadine (which was commissioned in November 2018; the mine began commercial production in May 2019). “In Nunavut, we’re counting every kilowatt that is available, and we’re saying, ‘Okay, what can we do with that energy?’”
Steps to recovery
To maximize heat recovery at Meadowbank, BBA focused on small, specific measures – like developing cleaning procedures to improve recovery rates from generator engine exhaust –while also looking at the bigger picture. They [had] never officially formalized their risk tolerance for blackouts, said Allen. This is important because powerplant operators do not pay for fuel but can feel responsible for outages, so it is common that they run all engines at lower loads. Although this burns more fuel, it gives operators an immediate reserve to tap into if the load spikes or a generator unexpectedly shuts down. Allen and his team put a question to Agnico Eagle’s brass: “How many blackouts do we want per year and how much money are we losing during these blackouts? Is this better than running all the engines lower?” As a result, generators were run hotter, at a higher load factor, improving heat recovery rates.
These and other changes cut diesel use by roughly two million litres per year at Meadowbank, without any substantial equipment improvements or upgrades. When it came time for detailed design of the cogeneration plant at Meliadine, Agnico Eagle’s next project in Nunavut, the company again turned to BBA, asking the company to incorporate the lessons of Meadowbank.
Right away, Agnico Eagle wanted to involve operations in the design process and commissioning of the power plant, so Meliadine staff knew how to run the systems properly to achieve the desired heat recovery rates. “It’s a hard one because the more we want to recover, the more the systems become complex,” said Allen. “If the users don’t operate the systems correctly, we can design the greatest powerplant, but it will not be as efficient as it’s supposed to.”
The system BBA designed injects thermal energy recovered from the gensets into a hot-water loop that heats the processing plant and all other surface buildings connected to the network. A second loop continues on to heat air in the underground mine to roughly two or three degrees Celsius, before returning to the plant, where the cooled water is heated up again. The entire heat distribution system runs more than five kilometres in total. Allen said it reliably heats the surface buildings but requires some help to heat the underground mine when the temperature drops below -25 Celsius.
The total efficiency of the cogeneration plant is about 80 per cent, according to Allen. “In other words, each kilogram of diesel contains about 43 Megajoules. From that, about 19 Megajoules are converted to electricity, and another 16 Megajoules into heat during the winter,” said Allen.
Reliability is huge
A crucial factor to consider with off-grid powerplants is reliability. A generator failure can shut down production operationwide, and that can get expensive. To minimize this problem, Agnico Eagle implemented load-shedding, which allows the operator to run the engines at optimal loads to get the most efficient performance from the generators. “If one engine instantly stops for some problem, then you can load-shed, for example, the cafeteria or the lodging, or a certain part of the process you know you can stop without affecting productivity,” said Allen. “There was no additional investment. It was just thinking about the network in a smart way. If something does go wrong, you just load-shed a sector that you’ve chosen in advance.” This gives the operator time to start up a back-up generator and power returns to affected areas minutes later.
Agnico Eagle also built reliability into the Meliadine plant by purchasing five 5.6 megawatt, high-efficiency Wärtsilä generators. These 720-r.p.m. gensets run at a low speed, meaning less wear and tear on the engine and better reliability. They are also five per cent more efficient than the 900-r.p.m. generators at Meadowbank. This gain in efficiency translates to roughly 2.5 million litres of diesel saved every year.
But it’s more than that, explained Allen. Agnico Eagle can ship in fuel only four months each year when the ice goes out of Hudson Bay, so this reduction means fewer storage tanks, less fuel to transport to site by ship and fewer trucks on the road. It also translates to a decreased risk of spills and fewer greenhouse gases emitted. “There are a lot of advantages to reducing diesel consumption when you’re up North.”
BBA made the business case for the more expensive gensets. There was more than diesel savings to consider with each behemoth, 100-tonne generator, too. “Lower speed for the same power means a bigger engine. That’s why it’s more expensive,” said Allen. “You also need more space in your building, a bigger foundation.” Agnico Eagle made the investment because the payback on what these generators cost, versus the generators at Meadowbank, was only about two years – Meliadine’s current projected mine life is 12 years.
Getting the generators to site posed a few logistical challenges, considering Nunavut lacks a deep-water port. Each generator was moved off a ship anchored in deep water and onto a multi-axel trailer sitting on a barge. When this barge came to land the trailers were towed onto the beach and then travelled 35 kilometres to Meliadine. Five generators as well as eight 50tonne, prefab cogeneration plant buildings were moved this way. A late summer in 2018 pushed back the schedule.
Fuels for the future
From the very start, Agnico Eagle insisted on de-risking Meliadine by ensuring its plant could be compatible with liquid natural gas (LNG) and renewable power. The rationale made sense: if the mine uses many tens of millions of litres of diesel per year and that price goes up by even $0.50, the company is stuck and operating costs increase by tens of millions.
Dual-fuel generators that run on both diesel and LNG already existed on the market, said Allen. “But the problem is if you’re using dual-fuel but running on diesel, you’re actually three per cent less efficient while waiting for [the possible incorporation of] natural gas [at a later date].” After speaking to many manufacturers, Finnish company Wärtsilä proposed an option where Agnico Eagle could easily convert its generators to LNG at a later date. “They are efficient as diesel engines, but if you do want to convert them to dual-fuel, then you only take two weeks, you pay that money at that time for conversion and you’re ready to operate on them,” said Allen. The company could stagger the genset switchovers so the operation would not be affected.
The plant can also integrate renewable energy. “We’ve been doing internal studies on a wind farm and we have been working on that for a couple of years now,” said Lavoie. “We’re saying that we need to again keep our minds open and look for opportunities.”
That flexibility to alter course with the winds of change means the longer Meliadine produces gold, the more Agnico Eagle is rewarded for the up-front investment and planning it put into its cogeneration plant. CIM
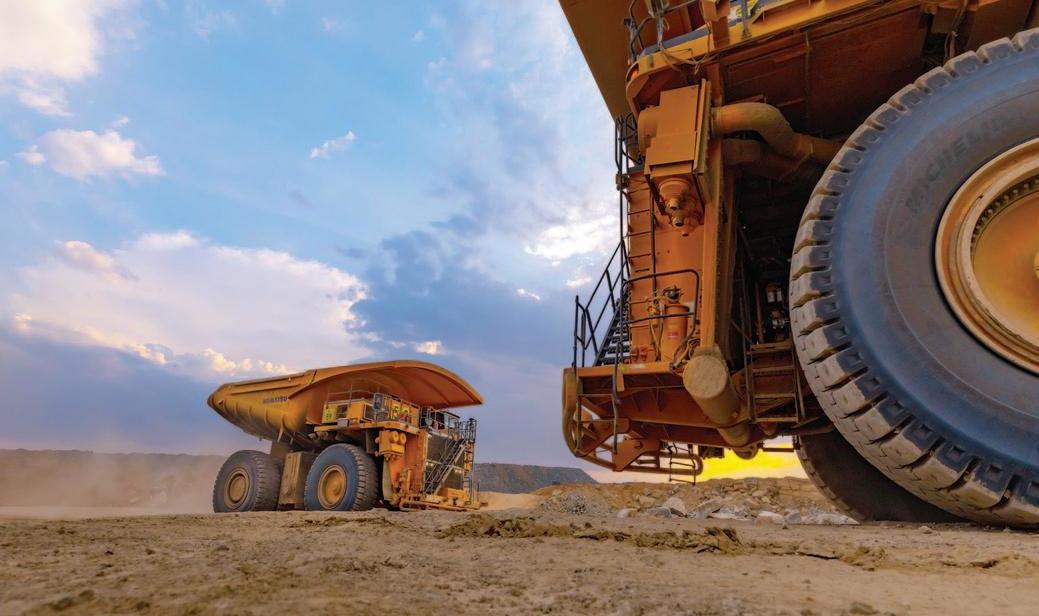
Anglo American plans to add a hydrogen-powered haul truck to its existing fleet at the Mogalakwena Central Pit platinum mine.
The elements of hydrogenpowered mining
With regulations being written, trials underway and companies considering adoption strategies, hydrogen’s time may finally be here
By Ian Ewing
Hydrogen power has long been hailed as the energy of the future – but always seemingly a few years away. Despite decades of research, development and incremental gains, the use of hydrogen energy is today still mainly limited to a handful of niche industrial applications. But the case for hydrogen has strengthened, and in the mining industry, the pieces are finally coming together.
Mining companies are trialling the technology, including, Anglo American, which is creating its own hydrogen-powered open-pit haul truck. Hydrogen technology companies are also interested in the mining market. DynaCERT (which produces a hydrogen-injection system for diesel engines), for instance, has partnered with Sudbury-based mining equipment supplier Total Equipment Services to create a Sparta-branded underground mining utility vehicle that is being tested at a currently unnamed northern Ontario mine. Also, in anticipation of hydrogen’s eventual use at operations, standards are being written to regulate safety and usage best practices and to give miners enough confidence in hydrogen to consider using it.
Marc Bétournay is one of the people writing those standards. As a principal research scientist at CanmetMINING, part of Natural Resources Canada (NRCan), he has been working since 2000 to make hydrogen mainstream. Now, he thinks it is ready. “It’s entirely possible that within three years there will be hydrogen fuel cell vehicles on the surface at mine sites,” he said. “That is where it’s going to begin.”
While the hydrogen-power researcher’s enthusiasm is understandable, he isn’t alone in seeing the potential of the fuel source.
“Hydrogen is the energy of the future,” said Dominique Beaudry, corporate director for innovation at Agnico-Eagle, explaining that hydrogen power is one way mining can respond to climate change. “We are very interested,” she said, but added that her company has only just started working on its case study for hydrogen.
Glencore Canada also sees a future with hydrogen. The company has trialled hydrogen at the Raglan mine, by using a hydrogen loop with electrolyser and fuel cells to store excess energy generated by a wind turbine for later use – and it is now exploring underground fuel cell vehicles as well. The obstacles to uptake – expense, safety and technological readiness – are open questions. The operational changes required and incomplete or non-existent guiding standards and best practices make adoption intimidating. And where is the need?
On the surface
The potential energy savings are attractive enough to Anglo American that it is sidestepping the traditional mining OEMs by doing its own conversion of a 290-tonne diesel haul truck into what the company said is the world’s largest hydrogen-powered mining vehicle. Anglo American staffers (along with engineering support from U.K.-based Williams Advanced Engineering)
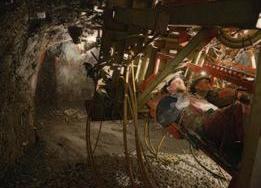
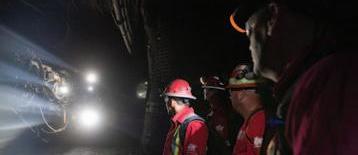
developed the conversion processes and the miner turned to suppliers such as Vancouver’s Ballard Power Systems to provide components.
The truck’s diesel engine is being replaced by a hydrogen fuel cell module paired with a scalable high-power modular lithiumion battery system, controlled by a high-voltage power distribution unit delivering in excess of 1,000 kWh of energy storage according to Williams Advanced Engineering.
Anglo American partnered with ENGIE, an energy services company, to provide on-site hydrogen generation capacity as well as storage and dispensing facilities at the open-pit Mogalakwena platinum mine in South Africa, where the haul truck will be used.
“Refuelling is a specific area we are focused on,” said Anglo American spokesperson Katie Ryall, “since it’s a major benefit of SAFETY - First, Last and Always. hydrogen, in that you can refuel much faster compared to charging a battery electric vehicle.”
“We can now generate our own fuel on site, eliminating our reliance on importing fuels and decoupling ourselves from the oil price,” she added. “The haul truck use case is very compelling, from an economic, environmental and technical perspective.”
Ryall said this project will help address the reliability and safety questions around this fuel source. She sees commercially ready solutions for mining three to five years away, with adoption in the open-pit environment first.
Ryall explained that the company has set out “ambitious” carbon and energy targets for 2030, and that hydrogen infrastructure will help enable a move to net zero carbon emissions. “To decarbonize our operations, developing a zero emission solution for materials movement is necessary. In the mobile application, hydrogen is well suited to the 24/7 activities at the site, where production is paramount and asset utilisation needs to be very high.” Under the earth
The biggest single driver in the move to hydrogen underground may prove to be regulations surrounding diesel particulate matter (DPM) in underground environments. Since DPM in confined spaces was declared carcinogenic by the World Health Organization in 2012, regulatory agencies have implemented increasingly stringent limits. “There are limitations currently on the books for all the mining jurisdictions in North America, and elsewhere,” said Bétournay.
The options for mines are to increase ventilation, or to decrease the quantity of DPM they emit. The cost of ventilation can be breathtaking. Instead, by removing diesel from underground, an operation can save 25 to 50 per cent of its ventilation costs, said Bétournay. “You could be talking about hundreds of thousands to millions of dollars per year per mine.” Ryan Sookhoo, director of new initiatives at Hydrogenics, a hydrogen technologies company observed, “there are some natural synergies for a zero emission vehicle to be used in a mine. observed. The carbon footprint of a mining operation and the ventilation requirements [underground] are primarily driven by the emissions of the vehicles in the tunnels. And miners can pay a high price for the fuel and the vehicles, because they can be fairly remote.” Hydrogen vs. electric
Some of the benefits of hydrogen – reducing the carbon footprint, cutting down on energy costs – are already being

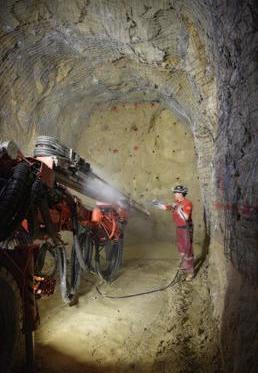

Providing full service mining solutions and innovation around the world since 1962. EXPERIENCE • Shaft Sinking • Raise Mining • Mine Development • Underground Construction • Contract Mining • Engineering & Technical Services • Raiseboring • Specialty Services AFRICA | ASIA | AUSTRALIA EUROPE | NORTH AMERICA SOUTH AMERICA
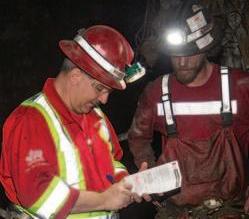
addressed by electrically powered vehicles, which have gained acceptance in underground mines. That acceptance is expected to grow over the coming years. According to the Hadapsar, India-based research company, MarketsandMarkets, ”electrical mining equipment is estimated to have a major stake post-2030, accounting for more than 40 per cent of the overall mining equipment market.” The company also predicts that “the electrification of mining equipment in Canada is estimated to be much faster than in the US and Australia.”
While some may question if hydrogen can find a niche for itself given the earlier adoption of battery electric vehicles (BEVs) or if hydrogen is even needed, analysts Bernd Heid, Martin Linder, Anna Orthofer, and Markus Wilthaner at McKinsey & Co. make the case why there’s a role for it. In an article entitled “Hydrogen: The next wave for electric vehicles?” they outline the argument for hydrogen’s adoption.
“Hydrogen and batteries are often portrayed as competing technologies, and batteries have received a lot of attention in recent years (‘proton versus electron’). The relative strengths and weaknesses of these technologies, however, suggest that they should play complementary roles. Battery electric vehicles exhibit higher overall fuel efficiency as long as they are not too heavy due to large battery sizes, making them ideally suited for short-distance and light vehicles. Hydrogen can store more energy in less weight, making fuel cells suitable for vehicles with heavy payloads and long ranges. Faster refueling also benefits commercial fleets and other vehicles in near-continuous use. How the technologies relate will depend mostly on how battery technology will evolve and how quickly cost reductions from scaling fuel-cell production can be realized.”
There is another argument in favour of hydrogen: In remote locations where mines are forced to generate their own electricity, hydrogen-powered vehicles could be an attractive alternative to BEVs, especially if the mines rely on diesel or natural gas generators to produce electricity.
Hydrogen hybrids
Hydrogen proponents are anticipating that fuell cell electric vehicles (FCEVs) will eventually become the dominant mining vehicle architecture, rather than battery electric.
Hydrogen powered vehicles could offer similar use cases and physical and logistical infrastructures as diesel vehicles, with lower ventilation costs and none of the health risks. Modular fuel cells would allow full-shift endurance and similar power output as diesel engines. The vehicle architectures would be similar to battery electric vehicles currently in use or under development. “Usually the battery or electric drive train model is a precursor to the fuel cell,” noted Sookhoo. “A fuel cell vehicle is 90 per cent an electric vehicle.”
To achieve this vision, the vehicle OEMs will need to get on board. “The next step in the market is to basically have the OEMs who already supply vehicles in the mining industry come to the table,” said Sookhoo. Once work begins in earnest, he predicts it will take about five to seven years to produce a commercialmodel fuel cell mining vehicle.
Setting standards for hydrogen usage
The primary document governing the use of hydrogen in Canada is the Canadian Hydrogen Installation Code (CHIC), the 2020 version of which is going to public review shortly. For the first time, the CHIC will contain a section on hydrogen in mining. “It’s sort of generic requirements and statements, just to make sure that this application is reflected,” explained Andrei Tchouvelev, a hydrogen standards and codes expert. But, he added, several provinces have formally adopted the CHIC into their regu latory process, and others are following.
Compared to other commercial and industrial uses of hydrogen, surface mines and vehicles can already use largely the same standards and design criteria. Underground, there are additional challenges to overcome. Confined spaces amplify the potential effects of any released gas, in terms of both ignition and suffocation risk. Adequate ventilation is needed to maintain the concentration below the lower flammability limit (LFL) of hydrogen in case of leaks or damage, particularly in an environment where ignition sources abound. The ventilation requirement is less than that for diesel, but may require careful design of refuelling or dispensing points to ensure adequate airflow in those areas.
“The next step is to be more practical, to look at the potential architecture of the vehicle and the configuration of a specific mine,” said Tchouvelev.
But he thinks the industry is well positioned to make that step. “The amount of safety knowledge that has been accumulated [to date] is significant,” he added, mentioning research that has been conducted into hydrogen dispersion behaviour underground, training and emergency response requirements, and sensor technologies for leak detection. In designing dispensing architectures, Tchouvelev said, “We can lean on the experience with conventional [above-ground] refueling stations. It’s not like people are starting from scratch.”
Part of that accumulated knowledge comes from the mining companies themselves, as Agnico Eagle, along with Glencore, Vale, Eldorado, and others, have been participating in hydrogen working groups led by NRCan, proving technologies and use cases, sharing research data, developing best practices, and identifying gaps in industry codes and standards for the use of hydrogen in the mining context.
Approaching the starting point
Perhaps all this means that hydrogen is right where it has always been: a few years away. But beyond mining hydrogen is already a US$120 billion industry, with over 65 million tonnes produced annually. Increasing adoption in other industries, including public transportation (buses and trains), warehousing (where hydrogen-powered forklifts are becoming common), and shipping (everything from UPS trucks to container ships) points to momentum that the mining industry might be wise to take advantage of.
“If you wait too long, you’re going to end up taking the fuel cell that was already designed for a train and having to adopt it to mining,” cautioned Sookhoo. “But if you get into the discussions now, maybe you can get a fuel cell that’s the perfect hybrid between a train engine and a mining engine, and leverage the volume and cost savings from that synergy.”
Bétournay thinks that work will begin soon. He said some battery electric equipment manufacturers have already been approached by mining companies looking for hydrogen fuel cell vehicles. And at a roundtable discussion in December, he added, “the consensus on hydrogen ranged from ‘it’s an interesting option’ to ‘when can we start using it?’” CIM