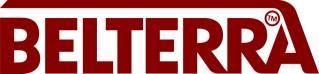
66 minute read
SEL 007 Preventative Maintenance
Document Identification SEL 007 Page Number 1 of 1
Preventative Maintenance Program shall be adhered to as per ISO policy and programs.
Look into:
- FRM 007 – Branch Equipment Inventory List
- FRM 008 - Equipment Maintenance Form
- Quarantine Area for defective tools and procedures
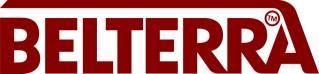
Document Identification SEL 008 Page Number 1 of 9
1.0 POLICY STATEMENT
Belterra Corporation recognizes that ongoing training and communication are a vital part of the company’s Safety Program. The Company will provide all safety and related training that is necessary to minimize losses of human and physical resources of the company.
It is the responsibility of every employee to communicate information about Belterra’s Safety Management System to peers, contractors, our clients and any other individual with whom we do business. The Company believes that sharing information is an input that leads to safe human behavior. We encourage that each individual take time out to acknowledge good behaviors, and bring to attention any unsafe work practices or conditions to the individuals attention or their direct reports immediately.
Belterra Corporation will ensure that all supervisor and field staff have the knowledge and skills to safely execute their tasks, and information on risk and risk management strategies are communicated throughout the organization.
2.0 PURPOSE
The purpose of training and effective communication is to: Establish an effective communications link between all levels of employees at Belterra; Diffuse potential job disruptions by providing a forum for discussion of critical safety issues; Exchange information regarding specific safety matters; Grow our safety culture and reinforce commitment to the Health and Safety of our team, and Obtain a “Loss Free” workplace through education.
This training and communication program includes information on: New employee orientation; Worker retraining; Competencies; Internal transfers within Belterra; Documenting and tracking safety training’s; and Conducting and documenting effective safety meetings
The information in this program does not take precedence over OH&S Regulations. All employees should be familiar with the OH&S Act and Regulations.
3.0 TRAINING
Front line supervisors, lead hands and “hands-on” managers are responsible for day-to-day enforcement
of the safety program. It is critical that they are given the tools to enable them to execute this role confidently and diligently. The Company will ensure that all Supervisors receive training in the following: Leadership for Safety Excellence or equivalent; Belterra’s recorded webinar on “Documentation workshop for supervisor and managers; Due Diligence training
The training will occur within 30 working days of the individual becoming a Supervisor.
3.1 NEW EMPLOYEE ORIENTATION
The following guidelines shall apply to all New Employee orientations:
Before Orientation Starts Orientation Content After Orientation
Proof of CSTS training where Worker familiarization with Complete a general workers required (technician, inside & company policy, company rules, orientation questionnaire to outside sales, and H&S responsibilities. determine the supervisors/foreman). A review of hazard assessment and comprehensiveness of the Proof of documentation to methods of identifying existing & presentation support your designation e.g. for potential hazards. Complete an “Employee safety officers, a CSO certificate, Table of Content – Corporate H&S Information Form. This for supervisors, Supervisory Manual information is maintained
Leadership Training Certificate Emergency Procedures in a confidential employee etc. Injury management return to work file and is used to manage Any other valid safety trainings / program any condition that could certificates available e.g. forklift, Belterra’s Drug and Alcohol policy negatively impact the
WHMIS, H2S etc. Any information necessary for health and safety of the Collect copies of all training specific job requirements. worker. certificates relevant to the An opportunity for the worker to Site Tour – worker will workers profession. ask questions attend a walk around of the Where written handouts, work rules branch to include: are used, employees are to be given - Emergency sufficient time to read the stations/muster points materials. - First aid station / room The Company’s “Employee - Wash area & worker Handbook” shall be issued to each facilities, bulletin board new employee. etc.
3.2 RETRAINING:
As a refresher, retraining on critical tasks such as Lockout-Tagout, PPE Compliance, Machine Safeguarding, etc. shall be carried out from time to time.
Re-trainings shall also be considered when there is an accident or incident or when someone has been observed that someone is being unsafe.
3.3 COMPETENCIES:
A competent worker is defined as adequately qualified, suitably trained, and having sufficient experience to safely perform work without supervision or with only minimal supervision.
To effectively assess the competency of the workers, the supervisor/manager will review
“Job Specific Competencies” and copies of the worker’s training certificates. The supervisor/manager within 30 days of hire shall observe worker performing tasks to verify competencies. Supervisor /manager makes the decision to enrol field technicians in the apprenticeship program. Completed documents shall be uploaded to share-point, and forwarded to HR respectively. The competency documents will be managed and updated in accordance with the apprenticeship program for all field workers by the HR department. Workers not meeting competency criteria or those that do not perform tasks safely and efficiently shall be retrained once, and further decisions shall be agreed upon by HR and the branch manager on case-by-case basis. Competencies shall be carried out on all individual performing “hands-on” tasks.
The following instances require the completion and verification of competencies prior to assigning tasks to workers unsupervised:
Equipment – operators must be deemed competent on each specific piece of equipment they are assigned to operate, including Power Mobile Equipment. Grinder / Buffer– Any worker assigned to operate a grinder must be deemed competent in its operation before use Operating a slitter machine Operating a punching hole machine Knife use Rigging / hoisting Belt Winder Winches (air or electric Belt installs Pulley lagging (cold bonding) Fall protection, and Confined space
3.4 INTERNAL TRANSFERS:
Prior to officialising the internal transfer, manager should contact the branch the employee is
transferring from, to discuss training needs and past performance, and to identify potential training gaps. Trainings Needs Assessment Form should be completed to capture this information (FRM 035 – Training Needs Assessment).
Once an employees starts in the new branch, he/she should be placed in an “observation period” for 2-4 weeks, to assess whether additional training is required. During this period, the transferred employee shall work with another employee to learn and understand branch specific needs and customer requirements.
3.5 DOCUMENTING AND TRACKING SAFETY TRAININGS:
Completion of all mandatory and recommended trainings will be captured in the “Training Manager” software. All managers and branch administrators have access to “Training Manager” software.
3.6 CONDUCTING AND DOCUMENTING EFFECTIVE SAFETY MEETINGS:
Safety meetings are the backbone of Belterra’s safety and health training Program. Both workers and managers will take part in various types of safety meetings to: Reinforce positive behaviors Exchange ideas to correct anything that’s unsafe Share lessons learnt.
Types of Safety Meetings at Belterra include: Shift safety meetings Monthly safety meetings (JHSC or Staff meetings) Regional quarterly meetings
3.6.1 Shift Safety Meetings. Each shift shall have one “shift safety meeting”. These meetings shall be captured in the Field Level Hazard Assessment (FLHA). Supervisors/lead-hands must ensure that shift safety meetings address safety concerns including any hazards identified by the workers. All workers including Belterra’s subcontractors must be part of the meetings, and sign off to confirm their attendance. All shift safety meetings must be held at the beginning of the workday (either in the shop or at customer site(s)). Housekeeping, PPE compliance, weather contributing factors, controlled product use, and site specific concerns are some of the topics that should be addressed in these meetings.
Any suggestions and/or unanswered questions for later discussions must be documented in “section 3” of the FLHA (FRM 004) on the sections under “Identified Hazard” and “Control Measures to be Used Prior to Starting Work”.
Supervisors and safety officers are expected to address issues within their authority. Any issues arising that require additional corrective action will be coordinated by the supervisor/safety officer with the branch manager.
3.6.2 Monthly Safety Meetings:
Monthly safety meetings give worker an opportunity to discuss activities & issues such as inspections and corrective measures taken, and incidents either at Belterra or at customer sites.
The Corporate H&S department shall prepare monthly meetings for distribution to all branches. The following will be included in the meeting report, for review with crew: - Workplace incidents in the past month; - Monthly safety stats; and - Training materials from time to time with a set of quiz, as and when the need arises.
Manager /Branch Safety Officers / Representatives shall include additional information as part of the meeting such as: - Revision of Safe Work Practices or a Procedure - BOP communication - Belterra’s Observation Program (BOP) – share five high risk
BOP’s from previous month. Consider all recommendations and/or suggestions for further improvements and take actions accordingly; and - Branch specific Near Miss communication
All meetings must start with a safety moment.
3.6.3 Regional Quarterly Meetings:
The Regional Vice Presidents (RVP) shall facilitate these meetings each quarter. The meeting shall include provincial branch managers, safety officers / representatives, the President/CEO, Corporate HSE and any other individuals as per the RVP’s discretion. An agenda shall be sent to the workers a week or two before the meeting. Agenda items must include:
Workplace incidents/accidents in the past quarter with mitigation plans implemented Quarterly /Annual and Provincial OH&S Statistical reporting; Provincial OH&S Reporting; Discussion of Corporate goals and objectives Update on any upcoming projects
3.6.4 Guidelines for Conducting Safety Meetings:
Start on time; you may lose participant interest if there are unnecessary delays Stick to timeframes and the meeting agenda. However, if you get a good discussion going, use discretion about cutting it off too soon Start the meeting by complementing the employees on some recent good work Give the talk in your own words and when you deliver your talk: - Relate to the audience’s attitudes, abilities, and interests - Make sure your audience hears and sees you talk - Use brief demonstrations, displays, or news articles. This would be a good opportunity to go through Belterra’s OH&S monthly newsletter as well. - Involve your audience by encouraging questions and discussions
- Keep your message clear and understandable. - Answer spleen and unspoken questions. Your workers will always have the following questions in mind: What does it mean to me? In addition, what’s in it for me? - If a question arises that cannot be answered immediately, inform the crew when an answer can be expected, and give assurance that a follow up will be performed. - Maintain control. Do not allow the meeting to develop into a wasteful, time-consuming session. If necessary, make a statement at the beginning that “only safety issues” will be discussed. This will give a “rule” to reference if the meeting should become disorganized, and will help to focus the group and dispel any misconceptions about the purpose of the meeting.
4.0 WORKER INFORMATION AND COMMUNICATIONS
Bulletin boards will be utilized in conspicuous locations for communicating health and safety information. The safety officer and/or safety representative will be responsible for updating the board. Information may include: General Safety Bulletins Milestones/Achievements/Awards Monthly Safety Newsletters Workplace Inspections and Incidents Company Safety Rules and Policies Emergency Response Information H&S materials as mandated by the Company or the Law.
Monthly OH&S Newsletters will also be utilized to communicate information to workers. The corporate HSE department the first Friday of each month shall release safety newsletter. All workers having company email access shall be forwarded a copy by the corporate office. It is the responsibility of the branch managers and safety officers / representatives to ensure workers with no email access are made aware of the newsletters by posting these on the bulletin board. Newsletter articles can also be used as part of safety crew talk during the monthly safety meetings.
5.0 RESPONSIBILITIES
5.1 SENIOR MANAGEMENT RESPONSIBILITIES: Demonstrate and communicate that health and safety are as important as cost savings and production gains Consistently communicate their vision and expectations for health and safety Ensure communication links are established with all levels of employees at Belterra Encourage branch level management to consider safety in all their business decisions Demonstrate their personal commitment to safety Providing leadership training to managers and supervisors. Provide a measurable health and safety matrix with key performance objectives and indicators to evaluate awareness and provide recognition.
5.2 MANAGERS RESPONSIBILITIES: All managers need to routinely and consistently communicate – through words, actions and readily available information – their commitment to health and safety.
Managers must consistently: Discuss the importance of safety in Belterra including our safety policy and “Mission to
Zero” goals with all employees and contractors Emphasize to all employees and contractors that “Safety is Everyone’s Responsibility” Make sure every individual clearly understands safety standards in this manual and not allow any deviations unless approved by the Corporate H&S department. Encourage and support open and honest communication Reinforce safe behaviors through positive reinforcement or correct unsafe behaviors through appropriate corrective action. Communicate with workers their expectations and specific goals for safety Communicate all issues affecting workers health and safety Ensure that safety information, e.g. safety standards and lessons learnt from incident and potential incidents, is available to all their workers Ensuring that time is allocated for training in each safety element and work practice or procedure and that its contents meets all legislative and regulatory requirements. Ensure that any person who provides training is competent to provide the training and is provided with adequate time and facilities to provide the training. Ensuring that employees that are promoted or transferred are re-oriented to the new position or location. Ensuring that employees that perform specialized work have the required competencies and certifications.
If an employee has previous experience in industry and is able to establish to the satisfaction of the person directing the training program that the worker has received training equivalent to training required by the program, the person directing the training program may accept the worker’s previous training as meeting all or any part of the requirements of the program.
The Worker Training Checklist (FRM 036) is to be used to identify training requirements.
5.3 SAFETY OFFICERS / REPRESENTATIVES RESPONSIBILITIES: Develop, maintain and periodically review the training of workers to ensure that they are adequately oriented and educated to identify hazards and carry out their duties safely and that an appointed competent person directs the training program. Keep employee records of all training provided to each worker through the program and ensuring a copy of the record is readily available to workers. Ensuring that there is a written competency assurance process for individuals managing hazards and risks.
5.4 SUPERVISORS AND LEAD HANDS RESPONSIBILITIES: Ensuring that new or modified equipment and/or processes are formally assessed and that training is adequate for the new safe work practices and procedures. Ensuring that new workers receive orientations before the first day of work and that the New Worker Orientation Checklist (FRM 001) is completed.
Ensure that no employee under your supervision is untrained on the tasks assigned to him or her.
5.5 WORKER RESPONSIBILITIES: Workers are responsible for attending any designated training and communicating their understanding of the contents of the program, either verbally or by written examination, where required Take reasonable care to protect themselves and others who may be affected by their actions or omissions Make proper use of safety equipment, clothing and devices Cooperate with the health and safety committee or safety representative Cooperate with other persons regarding workplace safety and health matters Practice their “OH&S Rights”: - Right to know. Every worker has the right to know about hazards in the workplace and which precautions must be taken to prevent injury or illness from these hazards. - Right to participate. Every worker has the right to participate in safety and health activities at the workplace, including in the joint workplace safety and health committee, or as a worker representative, for example - Right to refuse unsafe work. Every worker has the right to refuse work for anything that the worker believes will cause immediate and serious, or long-term effects on their safety and health or the safety and health of others. - Carry out duties or exercise safety and health rights, as set out under The Manitoba Workplace safety and health act without being subject to discriminatory action (Province of Manitoba only)
No Worker shall under any circumstances:
Carry out any work if, on reasonable and probable grounds, the worker believes that there exists an imminent danger to the health & safety of the worker. Carry out any work if, on reasonable and probable grounds, the worker believes that it will cause to exist an imminent danger to the health or safety of the worker or another worker present at the worksite. Operate any tool, appliance or equipment if, on reasonable and probable grounds, the worker believes that it will cause to exist an imminent danger to the health and safety of that worker or another worker present at the work site.
Imminent danger can be a danger that is not normal for that type of work, or a danger under which a worker in that type of work would not normally do the work.
A worker who refuses to carry out work or who refuses to operate a tool, appliance or equipment shall, as soon as practicable, notify their supervisor (or their safety officer in the absence of a supervisor) of the refusal and the reason for the refusal.
The worker is to remain at the work site unless advised otherwise by the supervisor and may be assigned to other work assignments the worker is reasonably capable of performing.
On being notified, the supervisor shall investigate and take action to eliminate the imminent danger.
The supervisor will also ensure no worker is assigned to use or operate the tool, appliance or equipment or to perform the work for which a worker has made a notification, unless the worker assigned is not exposed to imminent danger or the imminent danger has been eliminated.
The supervisor will prepare a written record of the worker’s notification, the investigation and the actions taken and give the worker a copy of the record.
Forms
Worker Right to Refuse Notification to Employer (FRM 032). Employer Response to Worker Right to Refuse Notification (FRM 033).
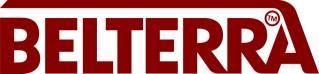
Document Identification SEL 009 Page Number 1 of 5
1.0 INTRODUCTION
1.1 PURPOSE
The purpose of workplace inspections is to identify existing and potential hazards with work methods and practices, tools, equipment, machinery, materials, building and environment so that the hazards are controlled or eliminated.
1.2 POLICY
It is the policy of Belterra Corporation to maintain a comprehensive program of health and safety inspections at all its workplaces and facilities. Inspections are an essential method of identifying existing and potential hazards for corrective actions. They are also a means of determining the level of compliance with established standards for hazard controls, safe work practices, job procedures and safety rules.
2.0 RESPONSIBILITIES
2.1 BRANCH MANAGERS RESPONSIBILITIES
Branch managers should be aware of the conditions that exist in the workplace and the various procedures necessary to carry out the work process. Branch Managers should review inspection reports and ensure that proper action is taken to correct any hazards that are reported.
Branch Managers should also: Provide the resources to carry out regular inspections; Ensure that all workers are provided with the education and training need to understand their responsibility and to co-operate with those conducting workplace inspections; Ensure that the JHSC members take an active role in workplace inspections; Review workplace inspection reports;
2.2 CORPORATE HEALTH & SAFETY COORDINATORS RESPONSIBILITIES
Ensure workplace inspection procedures are developed and that it meets the regulatory requirements; Act as subject matter expert to management, CSO, and safety representatives
2.3 CONSTRUCTION SAFETY OFFICERS OR SAFETY REPRESENTATIVES
Consult with JHSC members and management about scheduling workplace inspections; Ensure workplace inspection procedures are reviewed annually
Monitor implementation, follow up, and evaluation of corrective actions; Act as a subject matter expert to employees and management at branch level.
2.4 JOINT HEALTH & SAFETY COMMITTEE MEMBERS & SAFETY REPRESENTATIVES RESPONSIBILITIES
Co-operate with the employer in scheduling workplace inspections; Actively participate in workplace inspections; Make recommendations for corrective action to the employer; Monitor implementation, follow up, and evaluation of corrective actions; Regularly monitor the effectiveness of workplace inspections and make recommendations for improvement when appropriate; Review workplace inspections procedures;
Joint health and safety committee and Worker health and safety representatives should also Review each inspection report to identify any trends that may be developing in the workplace. A proper analysis over time may reveal:
A need for training in certain areas; Why incidents are occurring in certain areas; The need to establish priorities for corrective action; A need to develop or improve safe work practices, and Problem areas that may require more hazard analysis.
2.5 SUPERVISORS RESPONSIBILITIES
Continuous inspections should be carried out by supervisors and foremen each time they pass Through their area of responsibility. Supervisors are accountable for the safety of workers under their control. Therefore, they should be constantly on the lookout for any hazard that might arise in the work areas.
Supervisors should ensure:
That workers are carrying out preoperational checks when and where they are required; Participate in regular planned safety inspections; Monitor implementation, follow up and evaluation of corrective actions.
2.6 WORKERS RESPONSIBILITIES
Fill in the Pre-Operational-Checklists as required. E.g. - Daily Drivers Checklist; - Vulcanizer Inspection – Primary - Forklift Pre-Operational Checklist
Document Identification SEL 009 Page Number 3 of 5 Inspect their work areas for hazards to ensure that they will not be injured as a result of their job. This may mean nothing more than watching out for hazards or it may mean a detailed pre-job inspection checking out equipment before use. Carry out actions implemented from workplace inspections to ensure that they will not be injured as a result of their job.
3.0 PROCEDURES
3.1 PREPARATION
As part of the Inspection Program, each branch will endorse a preventative maintenance of all its tools, equipment, machinery, facilities, and environment to ensure that safe operating conditions are met.
Select trained team members who are familiar with the workplace including members of the JHSC team. The effectiveness of an inspection depends on the ability of the team members to identify hazards. This requires: - A good knowledge and understanding of the nature of industrial processes, tasks and operations, - The relevant safety requirements and standards, and - The full range of hazards associated with equipment, machines, processes and the work environment.
Checklist should be available to ensure no area is missed during the inspection.
Utilize FRM 009 – “Facility Safety Inspection Checklist”; Have available information from the previous inspection reports and incidents. Check on any WCB, Fire, or other agencies inspection report.
3.2 ACTUAL INSPECTION
No work place can be considered perfectly safe. As a result, all work places including offices, storage areas and maintenance areas need to be inspected. Inspect areas that are not generally used as work places too, such as parking facilities, or storage facilities.
Your checklist should include inspection of these areas. Your checklists are your points of reference, but do not limit yourself to the items on the lists. When other hazards are identified, they have to be recorded and appropriate steps taken to address them.
Identify and record actual and potential hazards posed by buildings, equipment, the environment, processes and practices; Record any hazards requiring immediate attention; Determine whether existing hazard controls are adequate and operational. Ask for suggestions or recommendations from workers.
3.3 WRITING REPORTS
Record any unsafe actions or conditions observed during your inspection tour. FRM 010 – Facilities Safety Inspection Report shall be utilized to document the findings. The document should contain the location of the condition or action observed.
Hazard rating should be given to each action documented. The A, B, C rating method will be used to rate items observed during the safety inspection. The reason for this system is to highlight the degree of severity of those hazards and to assist both the inspectors and the employer in carrying out corrective actions.
Recommend corrective action and assign accountability for ensuring corrective action by a certain date. Communicate written inspection report to the management, the supervisors and the safety committee. Completed inspection reports shall be posted on the health and safety board within one week after the inspection has been completed.
3.4 IMPLEMENTATION AND FOLLOW-UP
Analyzing of inspection reports is one of the primary functions of the work place committee and the work place health and safety representative.
Corrective action should be taken as soon as possible on any deficiencies noted in the Inspections. Feedback on this action must be conveyed to the inspection teams, posted on bulletin board and shared in the monthly or staff meetings.
Hazard rating is classified as following: A – Any condition or practice that has a potential for causing loss of life, body part and/or extensive loss of structure, equipment or material. This means that immediate corrective action is required. Activity should be discontinued until the hazard is corrected. E.g. a worker by-passing a safety guard switch B – Any condition or practice with the potential for causing a serious injury, illness or property damage. Urgent situations require attention as soon as possible. E.g. forklift trucks are rounding a blind corner into a loading area without stopping, a worker is using an olfa knife without wearing proper cut resistant safety gloves. C – Any condition or practice with a probable potential for causing a non-disabling injury or non-disruptive property damage. These types of hazards should be eliminated without delay but the situation is not an emergency. E.g. there is an oil spill in an area that is not utilized by the workers.
4.0 TYPES OF SAFETY INSPECTIONS
4.1 FORMAL PLANNED INSPECTIONS
Formal inspections are planned, systematic and periodic examinations of the workplace which are conducted by a team consisting of both management and the safety committee. These inspections are formally documented with the use of a checklist and a report that includes recommendations for corrective actions.
Planned inspections are also the time to check on other persons who have inspection responsibilities to ensure that they are being done according to regulation and established standards.
The planned inspection will be conducted on monthly basis.
4.2 INFORMAL UNPLANNED INSPECTIONS
Informal inspections are ongoing inspections continually conducted by supervisors and workers as part of their job responsibilities. Hazardous conditions are noted and are either corrected immediately or reported for corrected action. These inspections do not usually generate inspection reports.
Examples may include a supervisor’s walk-through a worker’s daily equipment check.
Informal workplace inspections are not scheduled and will not require a checklist. However this will still be considered an important means of recognizing hazards.
4.3 SPECIAL INSPECTIONS
A special inspection will be conducted when there is a malfunction, an accident, or purchase of a new machinery / equipment.
Special inspection must, where feasible, include the participation of members of the joint committee or the worker health and safety representative.
Special inspection will also be carried out when there is an installation of a new piece of equipment or a change in a work process or procedure, which may prompt an update to the inspection checklists or guidelines
5.0 TRAINING
Inspection should be done by employees who are familiar with the work process and the areas they are inspecting.
Branch Managers must ensure that training and educations is provided to individuals so they understand their responsibilities, and know how to conduct workplace inspections effectively.
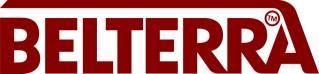
INCIDENT INVESTIGATION POLICY & PROCEDURES
Document Identification SEL 010 Page Number 1 of 8
1.0 Purpose
The purpose of the Incident Reporting and Investigation Policy is to make certain that incidents are investigated according to the injury, or injury potential of an event, in accordance with company policy and OH&S legislation. This will help to control further losses of human and material resources by identifying and correcting unsafe acts and conditions that lead to an incident.
This policy applies to any and all work-related incidents and close calls that affect company employees and others who are performing work for the company.
2.0 Policy
All employees and sub-contractors working for the company are required to report all incidents and near misses, including ergonomic issues, soft tissue damage and any signs or symptoms of musculoskeletal (MSI) injury to their supervisor, safety representative, or company contact. All incidents will be reported and a follow up and / or investigation conducted as per severity of the incident as per company and regulatory requirements.
Some incidents are immediately reportable to Workers Compensation Board. These include:
An injury or accident that results in death. An unplanned or uncontrolled explosion, fire or flood that causes a serious injury or that has the potential to cause an injury. The collapse or upset of a crane. The collapse or failure of any component of a building or structure necessary for the structural integrity of the building or structure. An unplanned or uncontrolled chemical release.
Incident sites should not be disturbed unless the safety of workers is at risk
Belterra Corporation uses the word “incident” rather than “accident” because there is an inherent belief by many people that accidents just happen and cannot be prevented. We use the word incident because we believe that all incidents can be prevented. Belief that all incidents can be prevented will drive the level of investigation to determine causes that could otherwise be missed.
Employees shall report all incidents as soon as possible to their immediate supervisor / safety representative and assist in the investigation when requested.
Every employee present at an incident when it occurred or who has information relating to the incident shall provide to the investigator any information in respect to the accident that is requested.
Branch manager shall ensure that all investigations are conducted promptly by a trained and competent individual and that reports are forwarded to the respective individuals in a timely manner. Reference SEL 015A - Injury Management Return to Work Process.
Incident reports will be reviewed by the branch manager or / or other senior management as appropriate to the severity or potential severity of the incident.
Action items from incidents will be documented and tracked for completion and follow-up by the Joint Health and Safety Committee (JHSC) members, and/or Safety Representatives in collaboration with the branch manager at all times.
Implementation of action items will be monitored and reviewed by the JHSC. Safe work procedures will be reviewed by the JHSC after an incident to ensure that changes required by the investigation findings are implemented and that they meet or exceed provincial requirements.
Injuries or incidents resulting from ergonomic hazards must be investigated.
3.0 Incident Classification Definition
Belterra Corporation records and reports to two separate entities as following: Injury Reporting as per WCB – Canadian Standards Injury Reporting as per Contractor Sites – USA Standards
3.1 INJURY CLASSIFICATION AS PER CANADIAN STANDARDS: A reportable injury is (or is claimed to be) an injury arising out of and in the course of employment with any of the following immediate or subsequent characteristics:
The worker loses consciousness following the injury. The worker is transported or directed to a hospital or other place of medical treatment, or is recommended by such persons to go to such place. The injury is one that obviously requires medical treatment. The worker has received medical treatment for the injury. The worker is unable or claims to be unable by reason of the injury to return to his or her usual job function on any working day subsequent to the day of injury. The injury or accident resulted or is claimed to have resulted in the breakage of an artificial member, eyeglasses, dentures or a hearing aid
3.2 INJURY CLASSIFICATION AS PER CONTRACTOR SITES – USA STANDARDS:
Fatalities A death resulting from a workplace incident.
Lost Workday Incident A work related injury which results in the employee being off work beyond the day of the incident
Modified Duty Incident A work related injury that results in a physician ordered change to the employee’s regular job duties beyond the day of the incident. This includes the employee being prevented from performing one or more of the routine functions of his/her job, and/or a change to the employee’s work schedule.
Medical Aid Incident
A work related injury that involves medical treatment from a health care professional followed by immediate return to work without restrictions. Medical treatment includes issuance of prescription medication, wound closing, removal of foreign bodies from a wound (complicated), removal of foreign bodies from an eye (except irrigation and cotton swab) treatment of infection, treatment of 2nd/3rd degree burn, positive x-ray diagnosis, issuance of a rigid means of support, vaccine (except Tetanus), cutting away dead skin, admission to hospital, and requirement for a follow-up visit. First Aid A work related injury that typically does not require attention from a health care Incident professional and may include restricted duties. First aid includes visits to health care professionals solely for observation, single dose medication or antiseptic, nonprescription medication, wound covering, removal of foreign bodies from a wound (uncomplicated), issuance of non-rigid means of support, tetanus immunization, cleaning of wound on skin surface, drilling a nail to relieve pressure, drinking of fluids to treat heat stress, and massage (except when prescribed by a health care provider). Near Miss A near miss occurs when an incident is narrowly avoided. It may have resulted in no consequences or minor consequences, but the potential for more severe consequences was great.
Vehicle Incidents Work-related incidents which involve a worker-used vehicle on any roadway and which result in damage over $1000 excluding normal wear and tear.
4.0 Responsibilities
4.1 Branch Manager or Designate A workers safety is of utmost importance, thus the branch manager shall ensure that the worker has been attended to and transported to a medical clinic or appropriate place for observation and care when and where required. A branch manager (or an operations manager in the absence of the branch manager) shall participate in all incident investigations.
Branch manager must report the incident to the Corporate H&S department as soon as possible. A preliminary report must be forwarded to the executive group ASAP, and no later than 24 hours of the incident. All investigations requiring immediate notification to WCB will be attended by the appropriate management personnel.
4.2 Supervisor & Safety Representative A supervisor and or safety representative must advise new and returning workers of the requirement to report all incidents including near misses. An annual reminder to all employees to report incidents is recommended. A supervisor must investigate incidents in a manner that is timely and appropriate to the circumstances and severity of the incident.
4.3 Worker A worker will report to the supervisor/safety representative all incidents including near misses. A worker will attend the incident investigation process unless unable to do so as a result of injury. Workers may choose to report a near miss using the company’s form “Near Miss Reporting”, or verbally to their supervisor, who will be responsible for completing the document.
4.4 Joint Health and Safety Committee (JHSC) Member or a Safety Representative A JHSC member should be included in an incident investigation. If not available, another employee knowledgeable in the investigation process may participate and contribute in the investigation process. Where there is no Joint Health & Safety Committees, a safety representative shall be part of the investigation process.
5.0 Reporting Procedures
Incident Reporting and Investigations Belterra Corporation has an obligation to make certain that all our employees, sub-contractors, volunteers and visitors are aware of the importance of and requirements for reporting and investigating near misses and other incidents. Investigations of near misses provide a learning and improvement opportunity to help prevent someone from being injured.
An investigation is held to prevent recurrence, not to place blame.
5.1 Definitions
Incident: An incident is any event that has resulted in or has the potential to result in an injury.
Incidents may include property damage, personal injury, death, close calls or near misses.
An employer must immediately notify the Workers’ Compensation Board of the occurrence of any incident that: - resulted in serious injury to or the death of a worker - involved a major structural failure or collapse of a building, bridge, tower, crane, hoist, temporary construction support system or excavation - involved the major release of a hazardous substance - was an incident required by regulation to be reported. Incidents that are required to be investigated by the Workers Compensation Act:
An employer must immediately undertake an investigation into the cause of any incident that: - resulted in injury to a worker requiring medical treatment - did not involve injury to a worker, or involved only minor injury not requiring medical treatment, but had a potential for causing serious injury to a worker - was an incident required by regulation to be investigated.
5.2 Workplace Incident Reporting and Investigation Procedure:
Step 1: The incident is reported by a person to the supervisor/ first aider / safety officer or representative, or the manager. (An incident involving an employee may be reported by others to the company where the injured employee is unable to do so.)
Where the branch manager is not informed, above individuals must ensure that the branch manager is contacted immediately.
Step 2: All attempts must be made to visit the incident site by the branch manager or the safety officer. The site shall be preserved until the investigation is complete, and if safe to do so. Photographs, sketches and other evidence collection should be undertaken promptly.
Note: Incidents requiring immediate notification to Workers Compensation Board (WCB) will require communication with WCB board officers with regard to site access and preservation of evidence.
Step 3: The Regional Vice President and corporate H&S department is notified of the incident by the branch manager.
Step 4: The direct supervisor or designate shall now complete a preliminary investigation report (FRM 011) with all information collected, i.e. witness statements, pictures of the scene and other information collected etc. ) Step 5: The preliminary report is forwarded to the H&S department (on the day of the incident).
Step 6: Branch Manager, Corporate H&S and other competent individual(s) shall work with the direct supervisor, and the injured worker where possible, and assist in the completion of the investigation. The investigation must be carried out by those knowledgeable about the type of work involved and, if reasonably available, with the participation of a JHSC member or a safety representative.
All investigations shall be led by the branch manager or it’s designate.
Investigation report shall not be accepted unless 5”Y” has been completed
Step 7: The completed investigation report shall then be forwarded to the executive group by the corporate H&S department. This must be done within 24 hours at a minimum
Step 8: All Workplace Injuries must be reported to Workers Compensation Board as following: BC – A preliminary report at a minimum must be submitted to WorkSafeBC within 2 business days. ON, MB, SK, QC, AB – Reportable injuries must be reported within 3 business days
Step 9: An “Incident Review Meeting” shall be scheduled within a week of the incident by corporate H&S department. Participants must include the President & the CEO, the Regional Vice President (province of incident), the branch manager, the safety officer / representative, injured worker and his immediate supervisor.
Results of the “follow-up” meeting shall be documented with a follow by corporate H&S to ensure completion and compliance.
Step 10: Safety Officer / Representative shall record all “Action required “as the result of an investigation in the Corrective Action Log (CAL) format which shall be tracked for completion by the JHSC or safety representative.
JHSC/Safety Representative will evaluate any future risks that recommendations or corrective actions could create.
JHSC/Safety Representative will monitor the effectiveness of any changes or implementations. JHSC/Safety Representative will communicate the recommendations and corrective actions to all relevant parties.
Step 11: All investigation reports will be forwarded to the JHSC. The JHSC will review the reports for completeness and determine if additional investigation or distribution is required. Note: All investigations that require notification shall be forwarded to the Workers Compensation Board after it has been review by the JHSC and approved by company’s management or as directed by WCB.
An industry safety alert will be issued through the company if findings from the investigation could help others prevent injury.
6.0 Injury Management Return to Work Process Map
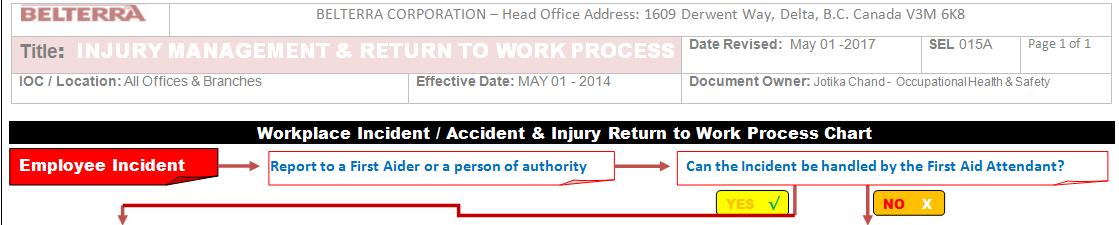
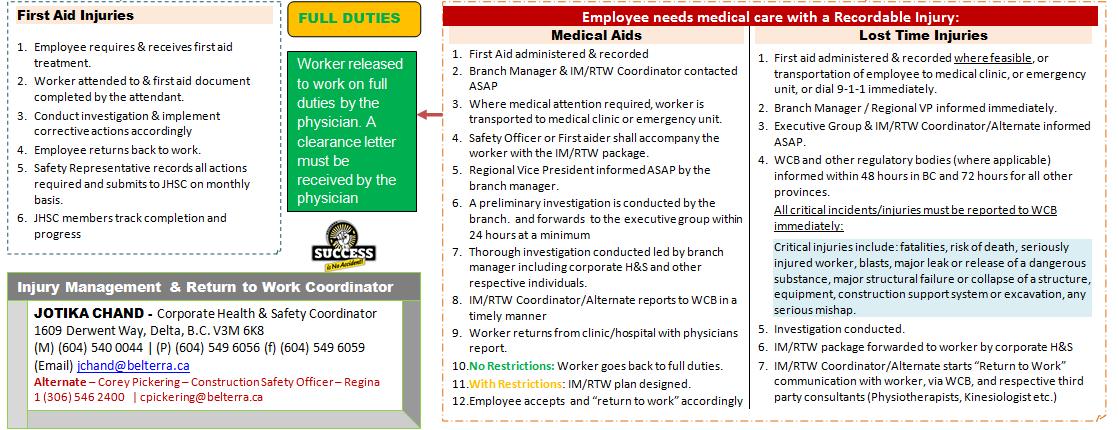
7.0 Training
Managers, supervisors and JHSC members must be familiar with this policy and associated forms. Training in the investigation process and the company’s specific policy and forms will be determined by company management and communicated to the JHSC.
The requirement to report and investigate near misses and other incidents will be covered during new employee orientation.
8.0 Review
This policy should be reviewed at least annually, or when revision is required. Incident investigation historical records should be reviewed annually by the JHSC in order to: Confirm that action required was implemented Determine if the action was effective in prevention of recurrence Identify trends
Determine areas for improvement.
9.0 Records
Copies of incident investigations will be electronically filed on a company Intranet (Share-point) or kept in a secure filing area.
10.0 Corrective Action Log
A Corrective Action Log (CAL) is used to record deficiencies and is included with the JHSC monthly minutes. The CAL is updated and posted every month. It identifies an issue, determines the appropriate action, assigns the action to a person, assigns a date for completion of the action, and has an actual completion date. CALs are reviewed monthly by the JHSC for completion and determination as to the whether the deficiency was addressed to prevent recurrence. CAL’s are reviewed monthly by the JHSC for completion and determination as to the whether the deficiency was addressed to prevent recurrence.
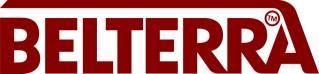
EMERGENCY PREPAREDNESS & RESPONSE
Document Identification SEL 011 Page Number 1 of 22
1.0 INTRODUCTION
1.1 Purpose
This document provides a formal guideline to all Belterra branches, so they can establish a formal procedure to be followed by all employees and visitors in the event of an emergency requiring the evacuation of the building
The purpose is to evacuate the building including at customer sites in a safe and prompt manner, in order to avoid and/or minimize the risk of hazard exposure to employees and visitors.
1.2 Policy
It is the policy of Belterra Corporation to develop and implement a formal Emergency Evacuation procedure, as part of its Occupational Health & safety program.
2.0 DEFINITION
2.1 Emergency Coordinator refers to the person in charge having overall responsibility for the branch’s emergency organization. 2.2 Fire Captain refers to the person having overall responsibility for the prompt evacuation of the branch and acting as a liaison between the Emergency Services Providers and the company
2.3 Floor Warden refers to the person within the responsibility of coordinating the prompt evacuation of a specific group or work area.
2.4 Emergency Services Providers refers to the fire department, ambulance services and the police
2.5 Evacuation in this plan refers to the prompt egression of the building
3.0 FIRE PROTECTION MEASURES
Below is a brief description of a number of fire protection measures, and other Emergency Response Plan equipment, which may be present in your branch building or at a customer sites. You should be familiar with the locations of these in your branch; location of these at a customer site shall be reviewed during communication of the emergency procedures and prior to beginning any work.
3.1 Emergency Equipment:
3.1.1 Air horn 3.1.2 Emergency pull stations 3.1.3 Mega-Phone 3.1.4 Pager 3.1.5 AED – Automated External Defibrillator 3.1.6 Spill Kits 3.1.7 Respirator protection kits 3.1.8 First aid kits etc.
3.2 Exits
An exit is a part of a means of egress that leads from the floor area it serves to an approved open space.
3.3 Fire and Emergency Access
Fire and emergency access allows firefighters and their equipment to gain access to the building. These areas should be clearly marked. Parking in front of the exit area is a violation of the Fire Code and strictly prohibited.
3.4 Portable Extinguishers
Portable extinguishers are intended as a first aid measure to cope with fires of limited size by trained personnel. The units should be clearly identified on the Fire Plan of the building and readily available. The basic types of fires are classes A, B, C. Portable extinguishers are rated for the corresponding classes of fire.
3.5 Standpipe and Hose System
A standpipe system is an arrangement of piping, valves and hoses outlets installed in a building in such a manner that water can be discharged through a hose and nozzle for extinguishment of fire. The system is connected to water supply that permits an adequate supply of water to the hose outlets.
3.6 Automatic Sprinkler System
An automatic sprinkler system is a series of underground and overhead piping designated in accordance with fire protection engineering standards. The system is connected to a water supply such as a storage tank or municipal water supply. The heads and device is usually activated by heat from a fire and discharges water over the fire area. The fire sprinkler system should be checked on monthly basis by a qualified / competent individual
3.7 Emergency Lighting
Emergency lighting ensures that exits, corridors, and principal routes providing access to exits are illuminated in the event of power loss. Emergency lighting fixtures should be indicated in the floor plan. Monthly checks should be done to ensure that these equipment are in proper working state all the time.
4.0 EMERGENCY PROCEDURES
Each branch emergency evacuation procedures should capture all these criteria’s and more if required under their jurisdictions: 3.8 Identification of possible emergencies – e.g. 3.8.1 Medical 3.8.2 Fire 3.8.3 Severe weather 3.8.4 Chemical spill 3.8.5 Extended power loss 3.8.6 Other ____________
3.9 Procedures for dealing with identified emergencies 3.10 The identification, location and operational procedures for emergency equipment
3.11 Emergency response training requirements 3.12 Location and use of emergency facilities 3.13 Alarm and emergency communication requirements 3.14 First aid services required 3.15 Procedures for rescue and evacuation 3.16 Designated rescue and evacuation of employees
5.0 DRILLS
Fire drills are an important component of the Emergency Preparedness and Evacuation Program. Fire drills determine whether the emergency personnel and the staff respond in a timely manner to carry out their duties. It determines whether all workers can competently respond in accordance with the emergency fire and evacuation procedures. Fire drills also assess the ongoing effectiveness of the emergency procedures under different fire scenario conditions. As per the National Fire Code, fire drills will be conducted on annual basis or once every 12-month period.
6.0 MAINTENANCE AND INSPECTION
Listed below are portions of the Fire Code, which requires that checks, inspections and/or tests be made periodically of equipment and facilities.
6.1 Definition of Key Words:
Checks: means visual observation, to ensure the device or system is in place and is not obviously damaged or obstructed. Inspect: means physically examination, to determine that the device or system will apparently perform in accordance with its intended operations of function Test: Means operations of device or system to ensure that it will perform in accordance with its intended operation of function
6.2 Portable Fire Extinguisher
Criteria Inspect all portable extinguishers
Inspection Frequency Monthly Subject to maintenance Annually Hydrostatically test carbon dioxide and water type extinguishers Every 5 years Empty stored pressure type extinguishers and subject to Every 6 years maintenance Hydrostatically test dry chemical and vaporizing liquid type Every 12 years extinguishers Recharge extinguishers after use or as indicated by an inspection or As required when performing maintenance
6.3 Sprinklers
Criteria Inspection Frequency
Check that unsupervised sprinkler system control valves are open Weekly Check that air pressure on dry pipe systems is being maintained Weekly Test sprinkler systems using alarm test connection Monthly Test sprinkler supervisory switches and other sprinkler and fire Every 6 months protection system supervisory devices Check sprinkler supervisory transmitters and water-flow devices Every 2 months Check exposed sprinkler system pipe hangers Annually Check all sprinkler heads Annually Inspect dry pipe valve priming level Annually
6.4 Emergency Lighting Unit Equipment
Criteria The unit equipment shall be checked to ensure the emergency lights will function when primary power is lost Pilot lights checked for indication of operating conditions (battery charging means that it is energized) Ensure battery surface is maintained clean and dry Ensure terminal clamps are clean and tight as per battery manufacturer’s specifications Ensure unit is secure in its location Emergency lighting unit equipment annual testing Inspection Frequency Monthly
Quarterly
Monthly Monthly
Monthly Annual
6.5 Means of Egress
Criteria Inspection Frequency
Inspect all doors in fire separation if any
Monthly Maintain exit signs to ensure that they are clear and legible As required Maintain exit lights to ensure they are illuminated and in good repair As required Maintain corridors and hallways free of obstruction As required
7.0 RECORDS AND DOCUMENTATION
As per the National Fire Code requirements, all test and corrective measures must be retained for a period of two years after they were made.
8.0 TRAINING
8.1 All employees must be trained to ensure a safe and orderly emergency evacuation, including training on the use of fire extinguishers, a refresher on how to use the AED etc.
At Belterra, while on customer sites, the Customers’ emergency evacuation procedures shall take precedence. Customer’s emergency procedures shall be communicated with all workers prior to beginning their shift at the site. All employees are to be aware of the actions required, but should follow the instructions set by their supervisor, site rules and site contacts.
9.0 DOCUMENT REVIEW & REVISION
The Emergency Response Plan shall be updated whenever a new piece of machinery is introduced in the branch, changes to operations, and or personnel. A formal review of the Emergency Response Plan shall also be performed after an emergency.
10 MEDIA RESPONSE
10.1 Designation of Company Spokesperson:
The President and CEO is the designated individuals as Belterra’s principal media contact and company spokesperson(s).
Depending on the situation, an individual external to Belterra Corporation may be asked to be a spokesperson on a particular issue due to their knowledge, experience and expertise. The company spokesperson(s) will work with that designated spokesperson to prepare them for the media interview as needed.
10.2 Guidelines for Talking with the Media:
A reporter, producer or other news media may contact you for a number of reasons, for example; to get information about a recent unexpected event such as natural disasters, theft or arrests, accidents or injuries, or regulatory actions etc.
Refer all media calls to the corporate office spokesperson(s). Please do not say you are not allowed to talk to a reported or have to get permission to do so. Instead, tell the reported: “Belterra Corporation policy is to refer all media inquiries to the corporate spokesperson(s)”. You can reach then at (604) 540-0044.
Whenever taking a call from the media, the same courtesy and professionalism in which we approach customers should be displayed towards the media. Then, contact the corporate spokesperson and inform that you have been approached by the media.
Do not let a reporter compel you to answer questions on the spot. It is always beneficial to prepare in advance in order to provide accurate and relevant information.
10.3 Guidelines for Photographs and Film:
A similar process as described above will be used when someone from the media is requesting permission to take photographs or to film inside our facilities. Refer the caller to corporate spokesperson(s).
No one will be given access to your facility for a photo or filming without approval from corporate spokesperson(s), and equally important, corporate spokesperson(s) will not give approval without talking in advance with the Regional Vice President, and the branch manager of the facility.
10.4 Unannounced Reporters:
A reporter or a camera crew may show up unannounced at your facility. This is most likely to occur in crisis situation at one of our facilities or at one of our customer sites. When dealing with reporters and camera crews who may show up unannounced, the branch manager and staff should act with the same courtesy and professionalism as we approach our customers.
Contact corporate spokesperson(s) immediately and let them know which news source is there. Corporate spokesperson(s) will contact the camera crew’s news room or the print photographer’s editor for clarification.
Although we cannot prevent the media from photographing or filming the exterior of our facilities, we will contact their news room and / or editors for clarification.
The media cannot enter our facility to photograph or film without permission.
11.0 OTHER EMERGENCIES
11.1 FIRE
WHAT SHOULD YOU DO AT THE BEGINNING OF YOUR SHIFT Confirm that you have two safe exits. Know where the fire alarm manual pull station or other emergency sounding device is at your location. Know where the fire extinguishers are at your location.
On discovering a fire, raise the alarm by shouting FIRE! to alert anyone in the immediate vicinity.
Leave the fire area. Sound the air horn / fire alarm. Fight the fire ONLY if it is SMALL and you are not alone, and you have been trained in the use of the fire extinguisher. o Always keep yourself between the fire and the exit. o Do not put yourself in danger. Evacuate through the NEAREST safe exit in an orderly manner.
11.1.1 If You Hear The Fire Horn / Alarm:
Leave for the nearest exit in an orderly manner. Do not collect personal belongings and prolong your stay in the building. This will place you in danger.
11.1.2 Evacuation Procedures:
Evacuate through the NEAREST safe exit in an orderly manner Assist persons requiring assistance Proceed to the __________________________________________________ STAY CLEAR of arriving fire department while proceeding to the assembly area. Gather for roll call Remain at the assembly area / muster station to participate in the roll call.
Do not talk while roll call is taking place. Do not re-enter the building until the Fire Department or the Emergency Coordinator advises all is clear.
11.1.2 Emergency Coordinators Responsibilities:
Phone 9-1-1 OR delegate someone to report a fire at your address:
_________________________________________________ Delegate a person to direct the fire emergency team to the building Take a roll call at the assembly area Report any missing persons to fire department / emergency personnel
11.2 EARTHQUAKE
During an earthquake... drop, cover and hold on
11.2.1 If You Are Inside, Stay Inside. DO NOT run outside or to other rooms during shaking. DROP down onto your hands and knees (before the earthquake knocks you down). This position protects you from falling, but allows you to still move if necessary. COVER your head and neck (and your entire body if possible) under a sturdy table or desk. If there is no shelter nearby, only then should you get down near an interior wall (or next to low-lying furniture that won't fall on you), and cover your head and neck with your arms and hands.
HOLD ON to your shelter (or to your head and neck) until the shaking stops. Be prepared to move with your shelter if the shaking shifts it around.
11.2.2 If You Are Outside:
Move to a clear area if you can safely do so; avoid buildings, power lines, trees, signs, vehicles and other hazards.
11.2.3 If You Are Driving:
Pull over to the side of the road, stop and set the handbrake. Avoid overpasses, bridges, power lines, signs and other hazards. Stay inside the vehicle until the shaking is over. If a power line falls on the car, stay inside until a trained person removes the wire.
11.3 TORNADOES
Don't assume that because you may not live in an area that's specifically prone to tornadoes that you're not at risk. Anywhere a thunderstorm can appear, a tornado can too.
The amount of concentrated damage they can inflict is stunning. As with most storms, the best way to handle a tornado is to get out of its way and steer clear.
11.3.1 Your Emergency Kit Should Contain a “Reliable Emergency Radio” that can be battery
operated or has a hand-crank or other manual charger for when you don’t have power.
11.3.2 Familiarize Yourself With The Warning Signs:
Tornadoes are usually accompanied by other strong storms, like thunderstorms or
Hurricanes, but not always. Watch the sky—the sky will get dark suddenly, and you may hear a loud rushing sound - almost a roar. The wind may pick up for a while, but suddenly die down. Watch for clouds beginning to rotate in a circular pattern. Tornadoes may strike quickly. The trademark funnel cloud is a good sign, but the cloud doesn't take on that tone until the cloud descends or debris is picked up. They may be transparent before that.
11.3.3 Seek Shelter Immediately:
If you cannot get to a basement or lowest level of the building, stay low and get away from windows or exterior walls. The goal is to get as many walls and structure between you and the storm as possible, and to keep you away from flimsier things like windows, siding, or flying debris. Shelter in a basement or lowest level of the building is the safest place to be in.
11.3.4 If You Are Driving:
If you're driving and cannot get to shelter, get out of the vehicle. o Lay face-down, hands over your head in a ditch or a noticeably lower level next to the roadway, away from the vehicle. If you can't get out or cannot get lower than your vehicle, shelter in your vehicle. o Lie down or bring your head below the level of the windows, and try to cover the back of your head with a seat cushion, pillow, coat, or blanket. If you're driving and see a tornado, do not try to outrun it. Pull over immediately and shelter with one of the two previous methods. Avoid overpasses, bridges, tall buildings, and flying debris.
11.4 BOMB THREAT OR SUSPICIOUS PARCELS
11.4.1 If You Observe a Suspicious Object, Or Package:
Avoid handling; never open or excessively handle any letter or package that you believe is meant to cause harm. Not all dangerous packages or envelopes look suspicious, and not all suspicious looking packages are dangerous. You must always use your best judgement. If you are concerned for any reason, do not handle the package. Call 911
Characteristics of Suspicious Packages / Letter:
Odd smell or sounds coming from the package; Oily stains, leaking or seepage from the package; Wires protruding from the package; Written directions indicating only a specific person is to open the package; Excessive postage, no postage or non-canceled postage; Excessive use of tape or unprofessionally wrapped packages, or a rigid or bulky envelope; Misspelled words, poor handwriting, printing or typing; Sloshing or ticking sound; Fictitious or unfamiliar return address; Distorted handwriting, homemade labels, or cut-and-paste lettering on the package address.
11.4.2 If You Receive A Bomb Threat Via a Letter or Note, dial 911 immediately, and do the
following:
Make note of all persons that you know handled the note. Avoid excessive handling of the note. The police will want to check for fingerprints. Follow all instructions from responding emergency personnel. You may be asked to assist the police and fire departments when they arrive, because you are far more likely to recognize something out of place than they are Police and Fire officials will conduct a detailed bomb search. Evacuate if ordered to do so.
11.4.3 If You Receive A Bomb Threat via Phone:
Any person receiving a phone call bomb threat should remain calm and ask the caller:
When is the bomb going to explode? Where is it right now? What does it look like? What kind of bomb is it? What will cause it to explode? Did you place the bomb? Why?
Keep talking to the caller as long as possible, listen carefully and try to determine the following:
- Time of call. - Age and sex of caller. - Speech pattern, accent, possible nationality, etc. - Emotional state of caller. - Background noise.
Report the incident to Police by dialing 911. If at all possible, have another person call 911 while you maintain a conversation with the caller. The police will handle all such threats. Evacuations will be ordered only if police or fire officials determine they are necessary.
11.5 POWER OUTRAGES
During a power outage, you may be left without heating/air conditioning, lighting, hot water, or even running water.
If you do not have a battery-powered or crank radio, you may have no way of monitoring news broadcasts. In other words, you could be facing major challenges.
11.5.1 Have A Basic Emergency Kit:
You may have some of the items already, such as a flashlight, battery-operated radio, food, and water.
The key is to make sure they are organized and easy to find. Would you be able to find your flashlight in the dark?
11.5.2 Ensure That All Employees Are Safe And Know What To Do.
Do not forget to check restrooms, storage and other areas in case anyone needs help. Do not put yourself in danger; carry a flashlight or candle etc. if you are accounting for the rest of the individuals. Stay calm and in a group, and be aware of your surroundings. Do not isolate yourself from the rest of the group if possible. Limit cell phone use to conserve battery life Once everyone is accounted for, unplug if possible – electronics and equipment in the event of a sudden power surge when the power returns. Keep calm and stay quiet. Await directions from the emergency personnel or person of authority.
11.6 MEDICAL EMERGENCIES
Call 9-1-1 or follow site specific instructions. ALWAYS stay on the phone until the person answering the call ends the conversation.
If you suspect a head or spinal injury, DO NOT MOVE the victim unless there is an immediate life threatening emergency.
11.6.1 In The Event Of A Medical Emergency:
Do not move the injured person unless there is danger of further harm. Keep the injured person warm. Do not exceed your training or knowledge when attempting to render first aid.
11.6.2 To Start Rescue Breathing: (victim is not breathing, but has a pulse):
With victim’s head tilted back and chin lifted, pinch the nose shut. Give two slow breaths. Breathe into victim until chest gently rises. Check for a pulse (on neck). If there is a pulse but victim is still not breathing, give one slow breath every 5 seconds (12 times). Re-check pulse and breathing every minute. Continue rescue breathing as long as victim is not breathing, or until medical assistance arrives.
11.6.3To Give CPR: (victim is not breathing AND has no pulse)
Find the notch where the lower ribs meet the breastbone. Place the heel of your hand on the breastbone. Place your other hand on top of the first. Position your shoulders over your hands. Compress 15 times using a smooth, even rhythm. Give 2 slow breaths (see above for details). Do three more sets of 15 compressions and 2 breaths. Re-check pulse and breathing for about 5 seconds. If there is no pulse, continue sets of 15 compressions and 2 breaths. Continue until medical assistance arrives or until victim starts breathing and has a pulse.
11.6.4 To Stop Bleeding:
Apply pressure directly onto the wound with a sterile gauze, clean handkerchief or bare hand. (Try to locate a moisture barrier, such as a clean garbage bag, to protect yourself from fluid contamination). Maintain a steady pressure for five or ten minutes. If victim is bleeding from an arm or a leg, elevate it. Stay with victim until help arrives.
11.6.5 In The Event Of Burns Or Chemical Burns:
Remove the victim from the source of the burn only if it is safe for you to do so. If a chemical is involved, wear gloves or other protective gear. Cool the burn by flushing with large amounts of water. Use water close to room temperature. For chemical burns, also remove any contaminated clothing. Loosely cover the burn with a dry clean or sterile dressing. For electrical burns, make sure the power source is off before making contact with the victim. If victim is unconscious, do not move unless there is an immediate danger. Loosely cover the burns with a dry clean or sterile dressing.
11.6.7 Abdominal Thrusts For A Person Choking (HEIMLICH MANEUVER):
Get behind the victim. Wrap your arms around the person’s waist, just above their navel. Clasp your hands together in a double fist. PRESS IN AND UP IN QUICK THRUSTS. Be careful not to exert pressure against the victim’s rib cage. Repeat procedure until choking stops.
All acute injury & illnesses must be reported and recorded. These records will be kept for a minimum or three years
11.7 FLOOD EVACUATION AND RETURN PROCEDURES
These procedures will address the potential health and safety hazards that may be presented when a Belterra Corporation facility is flooded by water due to environment conditions.
Main Electrical Disconnect is Located: Belterra Corporation – (Branch Location)
Main Gas Supply Valve Located: (write down exact location of “main gas supply valve” Ensure availability to flashlights for safe evacuations and return
POTENTIAL HAZARDS
11.7.1 Electrical Hazard – Risk of Shock, Electrocution and Fire:
If the facility has been flooded, electrical hazards may exist long after the water dissipates. Even if water is not visible in a building, the interior structure may be soaked and still present an electrical hazard.
If the electrical main switch was NOT turned off prior to evacuation, do not enter the building until a qualified electrician has determined it is safe to do so.
Do not enter flooded buildings that may contain energized electrical wiring or electrical appliances.
Stay clear of anything that could conduct an electric current such as metal pipes, metal ladders, and even damp wood. Do not touch damp walls.
11.7.2 Leaking Natural Gas or Propane Tanks – Potential Fire or Explosion:
Preventative Action: Shut Off Lines. If lines damage or leaking or if water covered the gas meter or if there is smell (rotten egg smell) or there is evidence of a gas leak, contact your local gas provider or fire department at 911. Eliminate all potential ignition sources.
11.7.3 Structure Damage – Potential failure of building material. Loose material, broken glass, hazardous debris
Preventative Action: o Conduct a perimeter check. o If serious damage noted, contact building inspector or structural engineer. o Flood water can damage building foundations causing shifting or settling, which may damage gas piping systems
11.7.4 Sewage and Bacterial or Mold Growth – Potential Health Hazard
Preventative Action: Wash affected areas with a solution of one part household bleach to ten parts water. PPE: Rubber Gloves, Rubber Boots, Eye protection, N95 respirator. Frequently wash hands with soap.
PROCEDURES Follow all instructions given by local authorities and emergency personally. Evacuate when instructed to do so immediately if building begins to flood. Return only when authorized to do so.
11.7.5 Prior to Water Entering Building:
Turn off equipment Turned OFF the main electrical power switch. Using the “LEFT hand rule to minimize the potential harm that can result from an arc flash. Stand to the RIGHT of the box. Using your LEFT hand, with your
FACE turn to the RIGHT, away from the box, place the switch into the OFF position. o Do not attempt to turn off main electrical power switch once water has entered the building. o Do not cross damp floors to shut off the electrical power at main switch. Turn off main gas supply valve to facility Remove chemicals to elevated area to reduce the chance of contaminating electrical equipment and water.
Do not drive through floodwater; Water may be deeper than it appears and levels can rise quickly. Stay away from down power lines – report to provincial hydro supplier: Prior to returning to a facility that has been flooded, ensure that electrical services have not been reactivated until a qualified electrician has determined that it is safe to activate.
11.7.7 Use Extreme Caution When Returning To The Facility After A Flood
When electrical equipment has been in water, it cannot be turned on again without risk of shock or fire. Do not enter flooded buildings that may contain energized electrical wiring or appliances. Do not turn on main electric switch or use electrical equipment or appliances that have been wet until they are serviced by a qualified electrician to ensure system integrity If a generator is used for backup power, make sure it and all connected equipment is in a dry and wellventilated location.
11.8 RAIL CAR DERAILMENT
Due to the close proximity of the train tracks, there is the potential that a train carrying chemicals could de-rail and release a potentially toxic chemical which could put workers in the area at risk of injury and/or illness.
11.8.1 In The Event Of a Rail Car Derailment:
Listen to the news/radio reports for information and further instructions. Follow the instructions of emergency personnel (police/fire) Evacuate or shelter-in-place as instructed.
11.8.2 Shelter-In-Place:
Call 911 to communicate to Emergency Personnel your location and number of employees sheltering in place. Remain at the location “Shelter-In-Place” until instructed by emergency personnel (police/fire) to evacuate. o Turn off ventilation system so as not to draw contaminated air into the work area o Close all exterior doors o Listen to radio for any updates o Evacuate when instructed to do so.
11.8.3 Evacuate:
When instructed by emergency personnel Shut down equipment if time allows Exit quickly in an orderly fashion Sweep the area to ensure facility evacuated Post note on door to indicate to emergency personnel that building is evacuated and how you can be contacted (provide cell phone number)
Note To Read: BUILDING EVACUATED. Contact < enter name> at <enter phone number>
11.9 BLIZZARDS AND WINTER STORM
11.9.1 In The Event Of a Severe Snow Storm:
Listen to the news/radio reports for information and further instructions
If the Ministry of Transportation closes your required road of travel, remain at the location “Shelter-In-Place”. Wait-out severe snow storms whenever possible
11.9.2 Commercial Truck Drivers:
Ensure vehicle is in good working condition and winterized o You should always have more than ½ tank of fuel at all times during winter season. o The tire pressure should be checked o Lights working, and o That you have winters on. Reduce speed – meeting time schedules is not a priority – safety is. Do not engage in other activities or multi task when driving. Do not use cell-phones, eat, or smoke. Keep your focus on the road, and both hands on the wheels as much as possible. Do not travel on road -ways closed by the Ministry of Transportation. Be aware of your personal safety when being outside of the vehicle o Be caution of potential slip hazards o Be cautious of potentially being hit by other vehicles Wear a hi-vis vest whenever outside of the vehicle Be aware of where you position your body relative to potential hazards o Do not turn your back on on-coming vehicles o Do not stand where vehicles travel
11.9.3 WHAT ELSE CAN I DO?
When a winter storm hits, stay indoors. If you must go outside, dress for the weather. Outer clothing should be tightly woven and water-repellent. The jacket should have a hood. Wear mittens – they are warmer than gloves – and a hat, as significant body heat is lost through the head.
In wide-open areas, visibility is limited during heavy blowing snow or a blizzard. You can easily lose your way. If a blizzard strikes, do not try to walk to another building unless there is a rope to guide you or something you can follow. If you must travel during a winter storm, do so during the day and let someone know your route and arrival time. If your car gets stuck in a blizzard or snowstorm, stay in your car. Allow fresh air in your car by opening the window slightly on the sheltered side – away from the wind. You can run the car engine about 10 minutes every half-hour if the exhaust system is not blocked with snow. Check the exhaust pipe periodically to make sure it is not blocked. Remember: you can't smell potentially fatal carbon monoxide fumes. To keep your hands and feet warm, exercise them periodically. In general, it is a good idea to keep moving to avoid falling asleep. If you do try to shovel the snow from around your car, avoid overexerting yourself. Overexertion in the bitter cold can cause death as a result of hypothermia from sweating or a heart attack. If snow is excessive or a roof shows signs of distress, contact a professional who is experienced in safe snow removal procedures. Unsafe procedures may cause personal injury and structural damage. Prevent access to areas under roofs where snow could fall.
11.10 NATURAL GAS LEAK
Natural gas is lighter than air and will rise and diffuse rapidly when it escapes in an open area. In its pure stature, natural gas has no odor. The “rotten egg” gas smell is an odorant added to the natural gas as a safety precaution. It is there to let you know when natural gas is in the air.
Call <enter gas company> and the fire department immediately Keep everyone away from the area.
11.10.2 If You Smell Natural Gas Inside The Building (smells like rotten egg):
Leave the building immediately Assemble at the meeting area to be accounted for Call <enter gas company> or call 911 for the fire department using a cell phone.
11.10.3 Hazard: Natural Gas is Flammable:
Do not light any flames Do not smoke Do not use phone in the area of the leak Do not turn light switches on or off Do not operate any electrical switches or appliances Avoid all possible sources of accidental ignition (i.e. static electricity or any other explosive source 11.10.4 Natural Gas Is An Asphyxiate:
Natural gas acts as an asphyxiate by displacing oxygen in the air. Displacement of air by the gas may lead to shortness of breath, unconsciousness, and death rom hypoxemia. 11.10.5 Carbon Monoxide:
Carbon monoxide (CO) is a dangerous gas that you can't see or smell. It happens when a car is running inside a garage/ warehouse or in the shop Carbon monoxide can make you very sick. When you breathe this in, it gets into our blood and stops the oxygen from getting to our brain. If you're sick with carbon monoxide poisoning, it might feel like the flu: Headache Upset stomach or throwing up Feeling so tired you can't sit up Fuzzy vision Getting really dizzy when you stand up You can often tell the difference between the flu and CO poisoning because you won't have a fever, everyone in this space will feel sick, or the symptoms might disappear when you leave the area. You can help prevent CO poisoning by reminding the grown-ups in your house to use and test a carbon monoxide detector.
Carbon Monoxide detectors senses too much CO in the air. When it does, it will make a loud beeping noise to warn you about the danger.
When you hear this alarm, it is best to leave the area. Open doors and windows to let in fresh air Open the doors and windows to let in fresh air.
If someone is feeling really sick and you think it might be carbon monoxide poisoning, call 911 and go outside to get some fresh air while you wait for help to arrive.
11.11 FREEZER REFRIGERANT LEAK
Inhalation of high concentrations of vapor is harmful and may cause heart irregularities, unconsciousness, or death. Vapor displaces oxygen, potentially creating an environment with not enough oxygen to sustain breathing.
IN THE EVENT A REFRIGERANT LEAK IS DETECTED:
Evacuate building – move all people to fresh air (outside) and direct to emergency evacuation meeting place; away from the doors into the building. If safe to do so, close valve. Ensure effective ventilation – open and leave building doors to the outside open for air circulation. Contact <Enter contractors name and phone number> If the leak is a high volume leak, which is resulting in a quick release of large quantities of refrigerant, call 911 – fire department to report an emergency leak of refrigerant. Do not re-enter the building until the building has been determined safe by contractor. This requires the work area’s oxygen level to be measured using a gas monitor. Do not re-enter until the Oxygen level has been measure and it meets the oxygen levels considered safe to work in (20.9% by volume) If the oxygen level cannot be determined, call the fire department

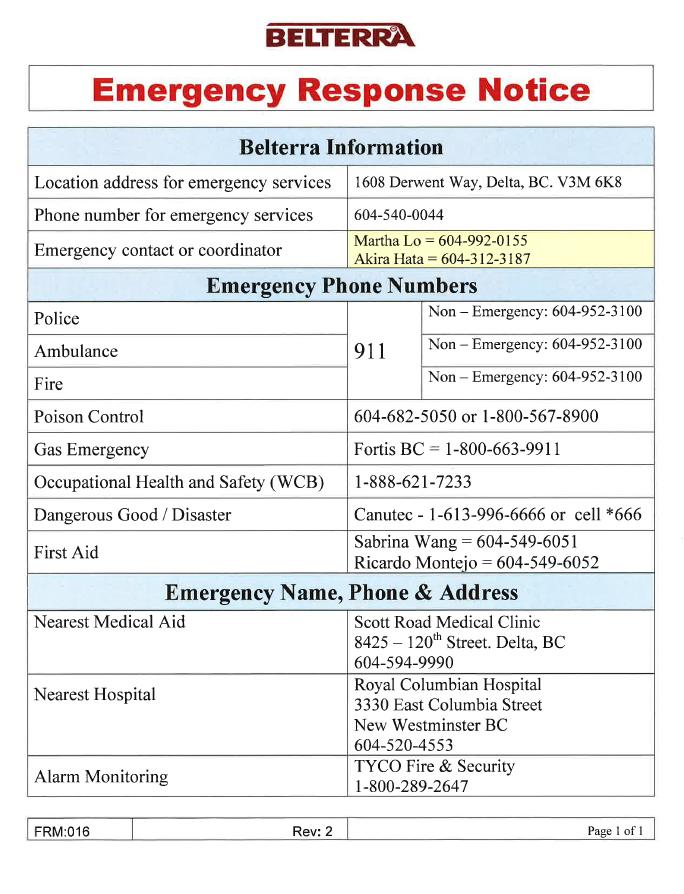