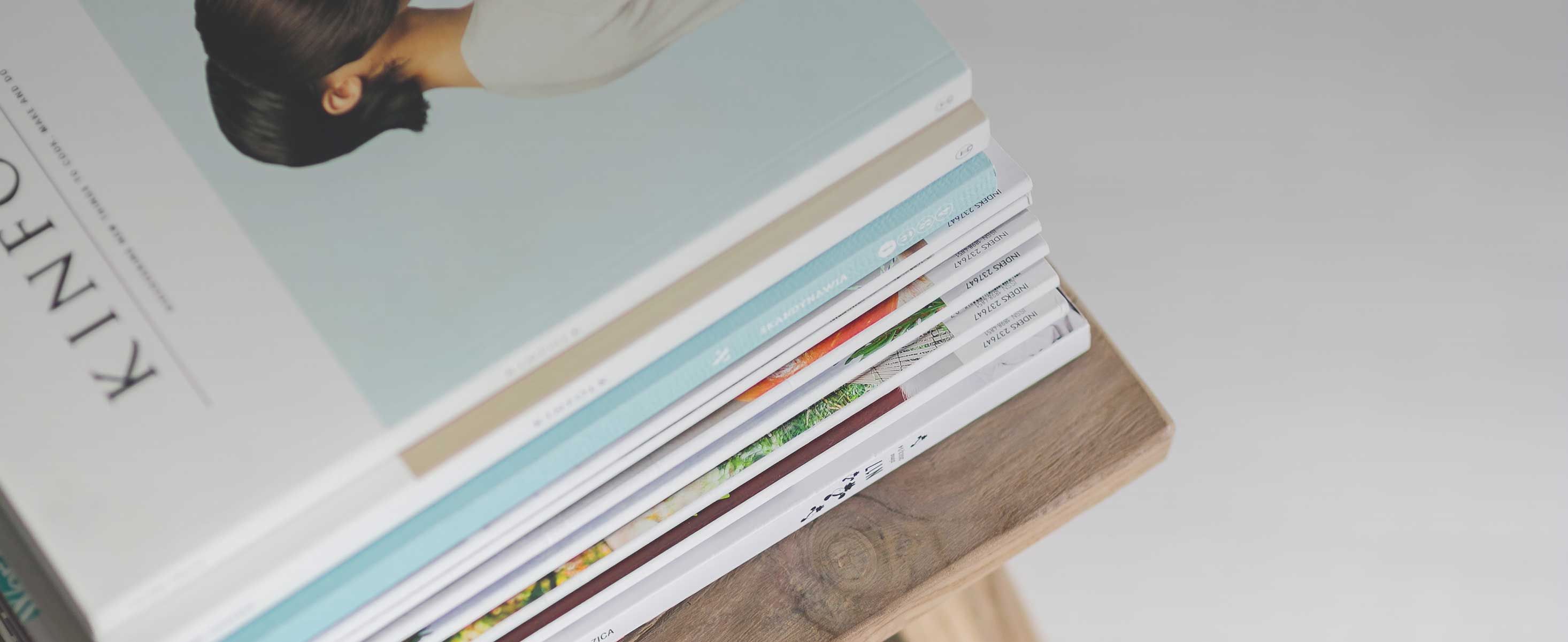
9 minute read
You can take the lad out of Yorkshire
Canford has enhanced its reputation as the supplier of choice for high-quality custom metalwork in the broadcast and pro AV industries over recent years. From its facility in Portand, Dorset, UK, Canford is now regularly involved with the world’s most prestigious live sports broadcasting, infrastructure projects and is regularly manufacturing connectivity solutions for major recording studios. Key to this success is the huge wealth of experience on the team at Canford. Design and technical staff work hand-in-hand with clients who get direct access to our skilled team at Portland. Customers might raise an eyebrow when their call to Portland is answered by a friendly, if not a little difficult to understand, Yorkshireman! In between brews, Gavin Drake heads up our Portland Manufacturing Team and hails from Elland (a little known town up North!).
Canford Marketing & Graphic Designer Jennifer Cassidy caught up with Gavin to ask how on earth he ended up at Canford on the Isle of Portland.
You have been running our metalwork facility on the Isle of Portland in Dorset for over 22 years but can you tell us a little more about yourself?
My life began 54 years ago in a little Northern town called Elland which is situated between Huddersfield and Halifax and is in the industrial heartland of what was the West Riding of Yorkshire. I was born into a stereotypical working class family. The middle son of 6 siblings. Growing up in such a large family we had very little but never went hungry and we were happy. In a time before computers and smart phones life was somewhat more straightforward and consisted of going to school before being let loose in the locality to cause a reasonable degree of mayhem (probably just below the level where the Police might be involved as that would never end well in those days!). I became street wise at a fairly early age and that stands me in good stead to this day, along with the classic Yorkshire trait of being friendly if a little too blunt on occasion. There is also that strange sense of humour that comes as standard with the odd accent and dialect….
You mention school. Did you enjoy it and what did you achieve?
I went to the local comprehensive. Despite being one of the brightest pupils I fell out of love with school in my early teens and stopped making an effort, I left at 16 with few qualifications. This wasn’t unexpected for me or many of my peers. Our social groups had few aspirations and the belief that our paths were to leave school at the first opportunity, and go on to manual work within a factory as our parents had done before us. I initially secured an engineering apprenticeship within a local company at 16 but was let go at 18 by the owner who decided I wasn’t cut-out for a career in engineering! From there I moved on to working within a plastic injection moulding company where I remained for 11 years before moving to the South.
On that note what exactly brought you to the South of England?
So over 11 years at the injection moulding company I’d worked my way up to the position of Materials Supervisor supporting the Purchasing Manager in procuring and managing raw materials and components. I had also gained a significant amount of production experience and an excellent understanding of how things worked, or as was more often the case didn’t! In 1996 our Managing Director left to purchase a large injection moulding company in the New Forest. He subsequently offered me a better role within this company and seeing the opportunity to progress I moved my entire family 270 miles South to somewhere I’d barely heard of before (I initially thought it was in Germany until I discovered that was actually the Black Forest…..). It initially went very well and within 2 years I had been promoted to Operations Manager with full control of production and purchasing.
This was sadly where the good news ended as before I was able to fully take up the role the company was forced into closure.
So from here how did you end up joining Canford in late 1999?
I subsequently secured a role as Production Manager at an Electronics company in Southampton some 20 miles away from where I lived. I thought long and hard before accepting the position because the idea of a 40 mile round trip every day did not appeal. This company then decided they were moving to Wimbledon and there was no way I was making that round trip every day so I was on the move again.
This is where my Canford journey begins. I had sent my CV to a local recruitment company where the story goes that it landed on the desk of one of their consultants at exactly the
same time as a job description from Canford Audio based in the North East who were looking for a Production Manger to join their recently acquired operation in Portland. It was apparently the easiest match he had ever made as the two just fitted perfectly with the exception of the fact I lived 60 miles away from Portland in the New Forest. Again until that point I had never heard of Portland other than as the children’s television series Portland Bill!
So then there was the interview which was held in a hotel on Portland - not on site? Later I discovered the reason was a fear that anybody who saw the state of the factory would never accept the role! It’s fair to say that the interview went well and shortly afterwards I had a job offer for a role that would now mean a 120 mile trip every day! Being unemployed wasn’t an option nor was Wimbledon so I decided to accept and thought I could cope for a few months whilst I looked for something else…..
But it’s now 22 years later and you are still here! Why?
Indeed! Well to begin with the factory just needed a little TLC and upgrading so not the complete disaster zone. The other little omission from both the job description and my interview was that the role wasn’t just that of Production Manger but actually General Manager. In many ways that really sparked my interest as with overall control there was an opportunity to put everything I’d learned so far in my career into practice without any real obstacles in my way. The staff were a good team but had gone through a pretty rough period under the previous ownership and moral was low. The existing working practices also left much to be desired and certainly contributed to the demise of the previous company before Canford stepped in to save it. It was however a blank canvas with lots of potential if it could be turned around. The 120 mile/3 hour round trip every day became thinking time and very much a catalyst for the changes that needed to be made. I found myself not only enjoying the role but also the journey to and from work. Every day was an 11 hour day but I was loving it! This was however only part of the story. It became apparent that Canford is different from many employers. You are very quickly made to feel part of a close knit team and the whole thing becomes a lot more personal. It was less about a salary and more like a family, where you just want to make it work for everybody involved. I want to stop short of saying it’s becomes a lifestyle but deep down I know I’m lying! My one consolation is that I am not alone and many members of the “Canford family” both at Portland and Washington have length of service records that are similar to or extend well beyond my own.
Picking up on your comment regarding a blank canvas with lots of potential. How has this played out?
I knew little about the broadcast market when I started but Canford had chosen to save the company as there was a significant demand for video patching connectors. Despite its damaged reputation the Portland site did have the experience, skills and equipment to produce them, albeit at the time rather badly. Changing the culture, attitude and mentality was very much stage 1 along with introducing strict manufacturing and quality procedures to give customers confidence again in both the product and availability. Having stabilised the business, stage 2 was to expand it with a realisation that simply making connectors wasn’t going to be sufficient to fully support the operation going forward. A little analysis of the market quickly identified a need within the industry for a metalwork provider who could manufacture 19” rackmount connection panels and associated solutions to a high quality within reasonably short lead times. The decision wasn’t a difficult one and we began investing heavily in equipment as we set off along our new path. We employed a dedicated sales resource but what became apparent very quickly was a need for the customers to have direct access. So alongside my normal day to day role I became more involved with developing sales. At the same time our requirement for sub contract plating, printing, painting and engraving services increased and I suddenly found myself with a company van and the responsibility for dropping off and picking up product each day. In a few short years I had gone from accepting a role as Production Manager to now being General Manager, Portland Sales and to cap it off the company van driver! Looking back it’s fair to say we haven’t done too badly in the last 22 years turning a failing business into what it is today - a market leader within our particular industry. This was just reward for our excellent vision at the start and a lot of hard work since.
So what does the future hold?
Well my plan has always been to retire at 60 and scarily that isn’t too far away now. It may prove to be easier said than done, as Canford is a huge part of my life. I already have a succession plan in place for the Portland operation. Alongside this I also appreciate that I have for many years now held a broader role within the group where I am seen as a senior member of the management team, with a good understanding of both the business and its various markets. It is with this in mind that I have recently accepted a position as a director of Canford Group Ltd such that I can now also play my part in shaping the future of Canford Audio as a whole and ensuring our success for many more years to come. This was not an easy decision for me as I have never seen myself as a director; however, I do feel that in order to protect the “Essence of Canford” we need stability and direction from within rather than externally via people that may fail to understand our rather unique but very successful approach! In reality it is the management team that has run Canford so effectively in recent years with the board of directors simply providing support and guidance where required. That will not change nor hopefully my plan to try and retire in just over 5 years…….