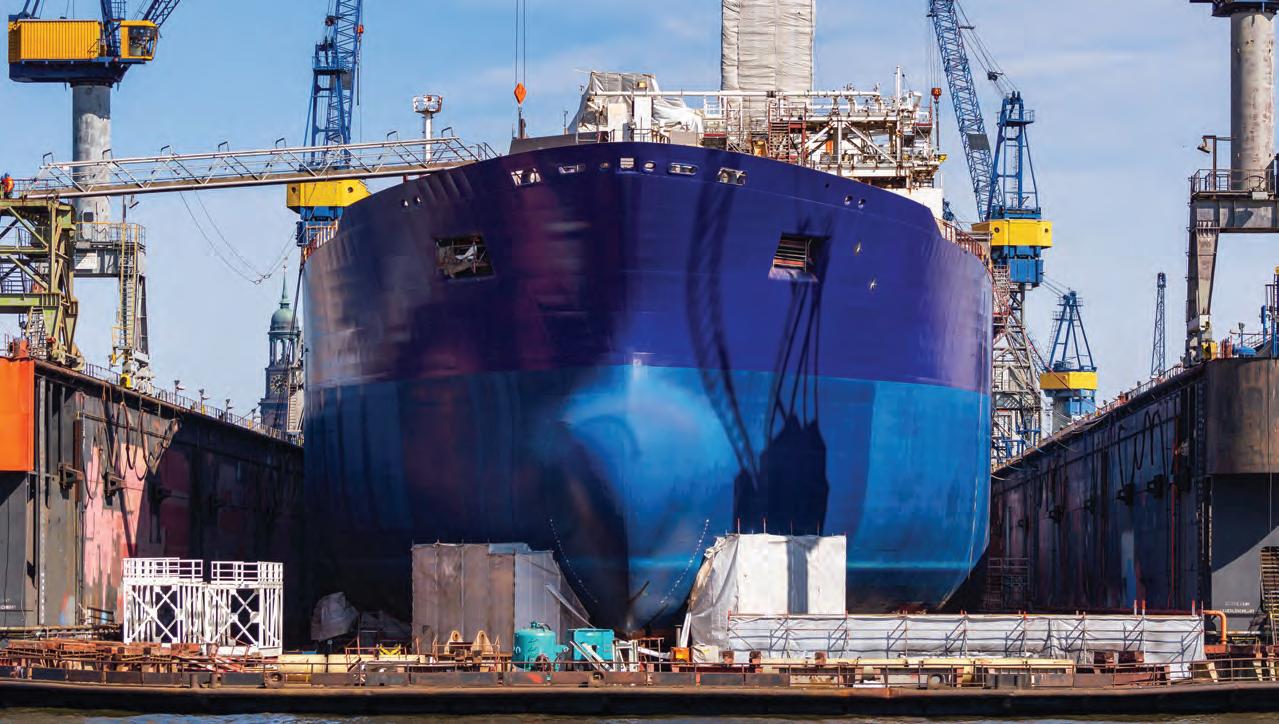
3 minute read
Finding the fault
Bruce Swales , Managing Director –
Asia-Pacific, Envista
Forensics, asks the key question of why did this vessel’s engine fail right after an overhaul
Picture this, a vessel owner seeking to overhaul the engine in a vessel engages a shipyard to carry out the overhaul. The engine is overhauled and during post-overhaul sea trials the engine fails. The vessel is returned to the yard, and the vessel owner is up for either the repair of the engine (best case) or worst case, the replacement of the engine.
Vessel owners and insurers frequently ask: Why did this vessel’s engine fail right after an overhaul? Because of that, Envista has investigated such failures multiple times.
In Envista’s experience, there are two common reasons for the above scenario frequently playing out. The first is using non-OEM parts (third-party manufactured parts, often referred to as spurious parts) and the second is poor workmanship by the workers carrying out the overhaul work.
USE OF NON-OEM PARTS
Non-OEM manufactured spare parts can seem financially attractive as they typically cost significantly less than genuine OEM parts. However, it is important to note that the quality and reliability of these parts can vary greatly and may not be held to the same standards as genuine OEM parts. The risks when using non-OEM parts include the following: a) Lack of compatibility and poor fit; b) Potential for lower quality and reliability, as well as reduced durability; c) Lack of OEM support; d) Warranty concerns; e) Potential for decreased engine performance; and, f) Compatibility with future upgrades/repairs.
Point a), lack of compatibility and poor fit, has been the cause of several engine failures that Envista has investigated. Typically, a main or big end bearing does not have the correct tolerances. Often, the part is manufactured from inferior quality materials, which can cause it to wear out much quicker or fail outright.
Poor Workmanship
Poor workmanship is a common occurrence seen by Envista, not just with third-party overhaul companies but also with OEM service technicians.
Common problems include bolts not being torqued to the correct tightness, wrong tolerance parts installed, incorrectly installed bearing shells, dirt on bearing surfaces and defective or leaking injectors re-installed.
Surprisingly, even very basic workmanship issues occur. A good example of this is a failure Envista investigated in Asia involving oil starvation caused by service technicians forgetting to remove rags pushed into oilways during engine disassembly to stop foreign particles from entering the oilways.
The engine was reassembled, started and left idling. Not long after, the engine shut down because of a low oil pressure alarm, but not before damage occurred to bearings and journals. Investigations found rags still in the oilways.
This happened not just on one engine but on two simultaneously being overhauled in the same vessel. This case was particularly surprising because service technicians from the OEM carried out the overhaul work.
Five Ways To Minimise The Risk Of Failure
First, while cost is important, one of the factors associated with such failures is the push to carry out overhauls at a very low cost. Unfortunately, this carries significant risks associated with workmanship and the use of spurious parts.
Second, engage only reputable shipyards to carry out the overhaul and vet their overhaul team or subcontractor if a subcontractor is being used regarding their specific experience with your engine model. Better still, engage the OEM or the OEM’s authorised service agent to carry out the overhaul (although, as per the oilway rag example above, even OEM service teams can make fundamental mistakes).
Third, specify that only genuine OEM parts are to be used. Demand receipts verifying genuine parts that were purchased or consider purchasing the required parts directly from the OEM. Spurious parts may be very tempting as they usually cost far less. However, they are lower cost for some obvious reasons, such as poor quality control or inferior materials used.
Fourth, consider directly supervising overhauls being carried out. While the cost of having a supervisor onsite during the overhaul may be high, the cost of your vessel’s extended downtime, if a problem occurs, will likely be far more.
Fifth, ensure purchase orders or contracts clearly state the full scope of work to be carried out and clarify the specific responsibility of each party involved (for example, the vessel owner, shipyard and overhaul contractor).
WHAT CAN INSURERS DO?
As a vessel insurer, to assist with recovery from the third-party responsible for causing the damage, it is essential to engage a reputable causal expert to confirm the precise root cause of failure and the party or parties responsible for that. The earlier an expert is engaged after a failure, the better, as there is a greater chance of the expert obtaining all necessary evidence before it is lost.
As the insurer of the party allegedly responsible for the damage, defending a recovery claim, it is also important to engage a causal expert to allow for the best opportunity to understand the facts surrounding the failure and resultant damage and whether the insured was indeed responsible and to what degree.
Vessel engines failing quickly following overhaul is certainly not uncommon. It happens reasonably frequently. The causes of such early failures usually boil down to either poor workmanship from the overhaul team or the use of spurious parts that are substandard. The reason behind this is often the vessel owner wanting to minimise overhaul costs perhaps a little too much.
As multiple parties are usually involved in the overhaul process, subrogation is common in these cases. As in any recovery attempt, insurers and their legal teams need to arm themselves with as much factual information about causal factors and responsibilities as they reasonably can to maximise their chance of a successful recovery.