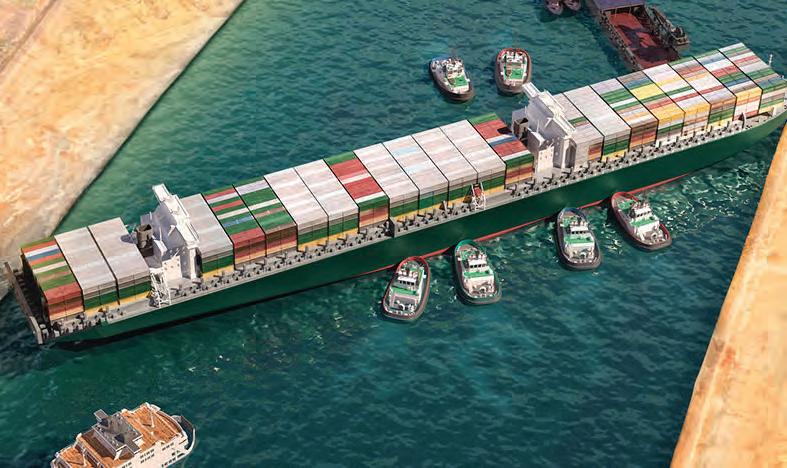
5 minute read
Contingency planning
From the grounding of the Ever Given in the Suez Canal to the continued congestion at major ports in China, the last two years have shown multiple instances of supply chain disruption around the world.
A stitch in time…
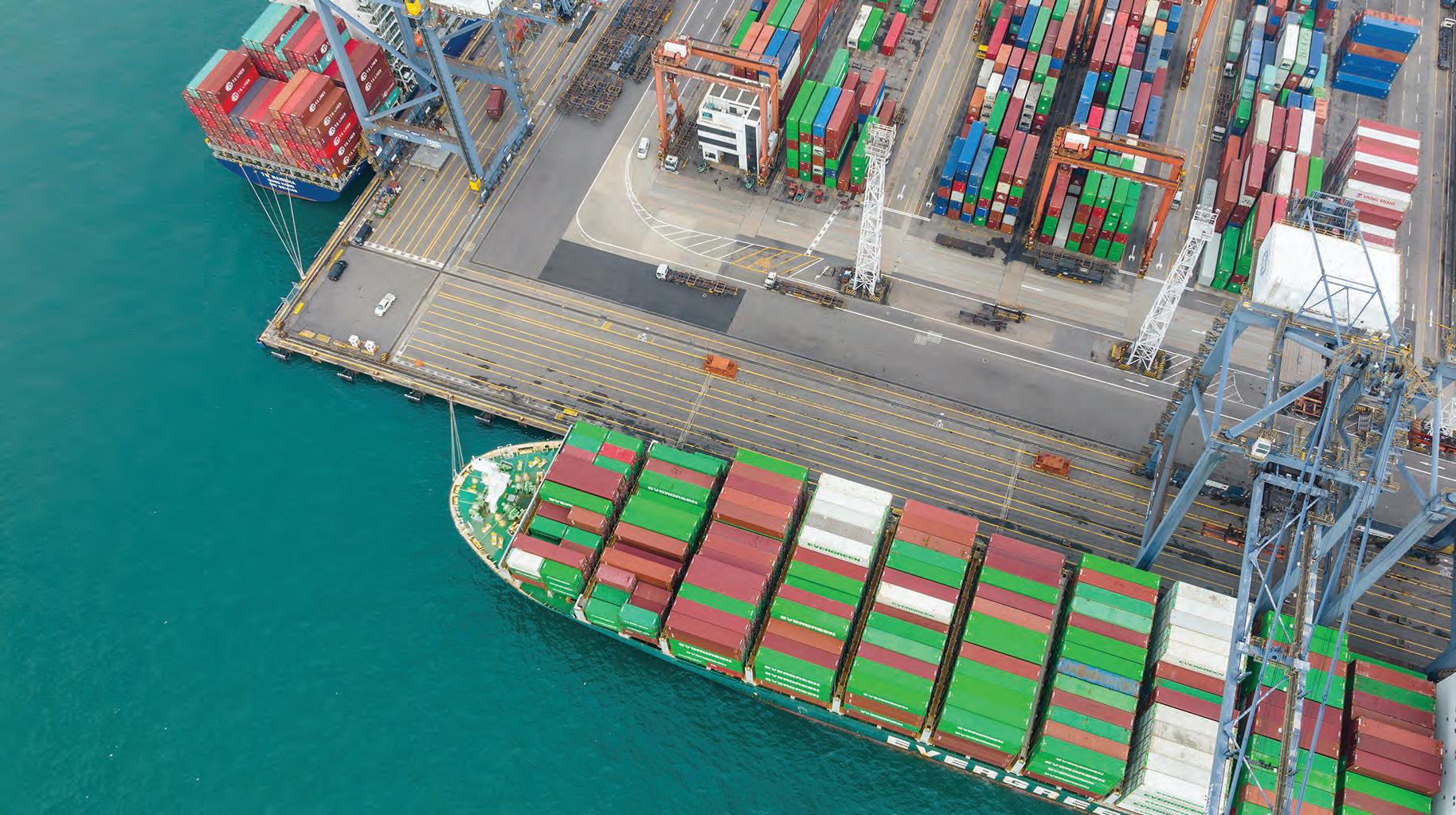
Jack Gould, Inland Marine, Transportation & Logistics Practice Leader at AIG in the US, argues that the experience of the last couple of years means that we must all take contingency planning more seriously as we await the arrival of the next ‘black swan’
If we have learnt anything from the past two years, it is that major disruptions to supply chains can and do happen. Now is the time to leverage those lessons and build in the right contingencies for the next shock that comes our way.
From the grounding of the Ever Given in the Suez Canal to the continued congestion at major ports in China, the last two years have shown multiple instances of supply chain disruption around the world.
The complex and interconnected nature of global trade means that an event in one part of the world can ripple through supply chains in ways that may not have been anticipated.
We have seen such disruptions time and time again, most recently when a global shortage of semiconductors – in part driven by the restrictions of the past two years - hit automotive production.
It has caused companies worldwide to question their supply chain risk management and the inherent vulnerabilities of practices such as just in time (JIT).
NON-PHYSICAL DISRUPTIONS
The last two years have also revealed that sources of disruption are not always physical in nature, as has often been the case historically.
There is currently a macroeconomic strain on logistics capacity because of the shift to greater consumption of physical goods within some sectors and among some consumers fuelled by robust household balance sheets.
We see that supply chain disruption can also be caused by labour shortages, price fluctuation due to supply and demand, cyber-attacks, and contingent business interruption (CBI), among other things. We are in an increasingly risky and unpredictable world, where the source of shocks cannot always be anticipated.
STRIKING THE RIGHT BALANCE
A balance must be struck between the price efficiencies of lean manufacturing and the need to ensure robust contingencies are in place, including some stockpiling of goods. Business continuity and long-term stability and profitability depend on ensuring that this balance is right.
Recent events have shown some of the pitfalls of excessive reliance on suppliers in concentrated geographies.
Many popular global manufacturing hubs are exposed to natural catastrophes, can be prone to political instability or are simply more likely to be impacted by disruptions to transportation and logistics. They may also be more difficult to monitor and audit on a regular basis.
As a result, a growing number of companies are reassessing their supply chains, identifying their critical partners and asking whether it is feasible to source goods and components from suppliers closer to home with onshoring and near shoring increasing.
Again, there is a trade-off. In Western service economies it generally costs more to source onshore, but, there is less risk of disruption and more flexibility in designing effective business continuity plans. Despite these growing intentions, inventories remain at historically low levels, representing the legacy of JIT and continued vulnerability.
TAKING A HOLISTIC APPROACH
Despite growing headwinds, many organisations remain in a profitable position. Now is the time to prepare for the shocks that may come down the line, and to build in buffers that will enable companies relying on multiple inputs sourced from around the globe to better absorb future disruptions.
While it is not always possible to predict where such disruptions will arise, many economic experts have stated that in the near term we will see continued inflationary pressures, commodity price volatility and pricing fluctuations caused by supply and demand. So, what should companies be doing now to prepare? AIG’s approach includes the following: > Take a more holistic approach to your supply chain risk management. Map out your suppliers and identify critical path exposures, going beyond the second and even third tier. > Understand where the pinch points are, what alternatives you have and whether you need to adapt some aspects of your business model. The key is being nimble, taking a wide-angle view of your supply chain in its entirety and having the operational resilience to adjust as circumstances change. > Recognise that choice of transport and logistics partners remain important. Larger organisations have the benefit of critical mass and purchasing power, facilitating access to ongoing capacity even when there are pronounced mismatches in supply and demand (as evidenced by the shortage of truck drivers, for example). From 2020, current contracted freight volumes have been consistent from year to year, while irregular shippers depending on the spot market have seen themselves competing among postings, volumes which are increasing by 30-50% per year—and securing that capacity comes at a price. There is also more onus on mid-market companies to ensure they have workable contingencies in place and maintain strong relationships with transportation partners.
SEIZING THE UPSIDE
As the world becomes increasingly complex and unpredictable, the need to partner with global, stable, and committed insurance carriers has never been more essential. Seasoned insurers and brokers have a wealth of claims data and risk expertise they can draw on to assist insureds as they address and aim to reduce the vulnerabilities in their supply chains.
This includes provider analytics and access to risk management and risk engineering services that can quantify physical or financial exposures, as well as strategies to transfer or reduce such exposures to minimise cost of risk.
Risk engineers can offer practical advice on where to locate facilities and how to mitigate the impact of physical risks, such as fires and natural perils. While large organisations have access to internal risk management resources, the help and advice of brokers, underwriters and claims adjusters can be particularly useful for medium-sized firms as they consider what potential disruptive scenarios may arise.
Scenario planning can be helpful, including sitting down with insurer and broker partners to plot out potential disruptive events and stress test how risk management frameworks and insurance programmes would respond in different circumstances.
Are logistics providers appropriately capitalised to respond to changing business conditions? Are your business inputs commoditised, exposing you to market rate risk, or specific enough to reflect supplier risk? Is that supplier risk geographically concentrated in a way that gives exposure to natural catastrophe or political risk? Do you have adequate backups in place and a risk transfer programme to cover the delta in costs?
As recent events have shown, it is important to think beyond physical loss or damage and consult with your insurance partners to assess and address the full extent of your risk exposures.
Jack Gould, AIG