
7 minute read
Risks of LNG
Need to focus on ` risk of transfer
Liquid natural gas (LNG) plays an important role in the global effort to reduce greenhouse gas emissions. Kenneth English, (left), LNG Specialist, Consultant Marine Engineer, Waves Group, and Paul Coates,(below) Fire Expert, Marine Fire and Hazmat Consultant, Waves Group, stress that the attendant handling requirements and hazards need to be taken very seriously and require investment
Vessels will need to be aware of Isolated vapour pockets, as any significant change in stability can lead to a situation whereby the gas at the top of the tanks has no path to vent, this could increase pressure in the tank to the point of rupture.
In November 2020, the International Maritime Organisation (IMO) agreed the next stage in meeting their 2030 Green House Gas ambitions, allowing LNG to be the viable fuel to bridge the energy transition as the world moves towards a carbon free future. As operators embrace LNG as a fuel, it is imperative that the risks and hazards of handling and transferring LNG are fully understood.
LNG needs to be kept at below -162ºC to stay in liquid form and once allowed to warm up to a gas, it will expand by 600 times. LNG needs to be scrupulously handled when being transferred from ship to shore or vice versa and from ship to ship under routine operational conditions. If it is handled incorrectly flash fires, brittle fracture and tank ruptures can occur.
LNG bunkers are now available, or will soon be available, in all major hub ports. As LNG is introduced into mainstream shipping operations new risks and hazards will emerge.
CRYOGENIC TEMPERATURE
state at -162ºC which requires a suitable low temperature steel containment unit. With the greatest risk of LNG leakage occurring during the transfer operation, it is essential that the operators have a robust procedure in place for the handling of LNG both as a cargo and as a fuel. It must be understood that any spillage to noncryogenic resistant steel will result in metal embrittlement and the risk of structural fractures. The effects of LNG on organic materials are no less damaging, with frostbite and cold burns being the result of LNG contact with skin.
HAZARDS
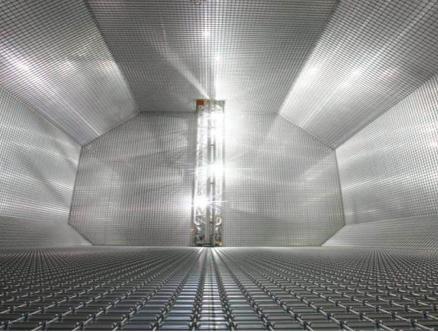
Other credible risks that need to be recognised and addressed include the risk of fire and explosion.
Once this odourless gas escapes it will warm up and rise and this potential gas cloud will host the risk of both asphyxiation and ignition. Once ignited it will burn back to its source as a flash fire. If not extinguished and isolated at source, the leak can continue to emit and re-ignite upon contact of any ignition source.
Thankfully, as LNG warms it can be visible because of the low temperature gas freezing any water in the air creating a white cloud, this does however restrict visibility. Other hazards unique to this fuel include RPT, or Rapid Phase Transition, whereby LNG spills onto water, as the LNG warms it evolves gas at a steady rate to a point where the transformation increases rapidly, this gives rise to an over pressurisation of the gas similar to an explosion.
In more confined spaces such as a ship engine room any sustained leakage will result in a concentration build up. As the gas moves out of the immediate gas safe zone towards an ignition source, such as a light fitting or overheated pump bearing, then an explosion will result.
Early detection of any leakage is required. This will be in the form of integrated gas detectors and shut down systems that are able to isolate the LNG source whilst maintaining fuel to the engines and propulsion.
Should a fire occur, then dry powder is the most efficient method of extinguishing, however, this medium will also require supplementing with carbon dioxide systems, water curtains and an effective emergency response plan. Evacuation must also initially be considered and covering sprays should be placed on surrounding structures. Any flames impinging on tanks can lead to a BLEVE (Boiling Liquid Expanding Vapour Explosion) if the tank insulation fails.
CONTAINMENT AND BOIL OFF GAS
Keeping the LNG as a liquid (below -162ºC) requires suitable insulation and careful management of the vapour produced.
As the LNG warms because of interaction with its surrounding environment there will be an increase in temperature and the cargo will begin to boil. The boiling of the liquid will release gas. This boil off gas (BOG) will need to be managed or a resulting over pressurisation of the tank will lead to an inadvertent discharge.
To manage this excess pressure, the vessel must operate a gas management system that can use this gas, either by using it as fuel within the vessels propulsion plant, flaring it or reliquefying it back to the tank. The latter is inefficient for LNG because of the high-power consumption required for reliquefication.
To satisfactorily use LNG as a fuel, appropriate engine management will be paramount as part of the vessel’s integrated automation system. With the inherent risk of an explosive gas in a permeable area - careful maintenance and understanding of this system will be required. But it will not end there.
Most vessels will require an inert gas system to be installed capable of generating nitrogen to purge pipework and inert tanks when not in use. This requires more equipment, more maintenance, more cost and a greater potential for damage.
Engine maintenance will also need careful attention. Poor maintenance and engine combustion will lead to methane slip and a release of this greenhouse gas to atmosphere in the unburnt condition as it fails to ignite in the engines.
Levels of awareness and cooperation will also need to increase. The vessel’s master will need to be mindful of the effects of navigation on the fuel and on the tanks as any increase in vessel movement will stir the tanks, liberating more gas and under certain conditions building up waves leading to sloshing tank damage.
To practicably transport LNG, it needs to be kept in a liquid state at -162 ºC which requires a suitable low temperature steel containment unit.
BUNKERING
Transferring cryogenic liquid between two floating vessels needs careful planning. This will be the most probable time to have
a loss of containment. To mitigate this risk a careful plan and a ship/ship/shore compatibility survey or check will be required.
The operation will need to be completed in a suitable location, with a gas safe zone mitigating the risk to the local area. Emergency plans will require review and competent personnel will be required to oversee the operation. Appropriate safe mooring and fendering arrangements and an emergency shut down system will be necessary to ensure no leakage occurs.
Operators will also need to understand the risks of cargo rollover, where two fuels of differing densities interact over time to produce a temperature inversion (the warmer fuel on the bottom of a containment tank flips over). This gives rise to a rapid surge in tank pressures and release of gas.
Class and shipyards have worked together to deliver the IMO expectations, but, once completed, operators will need a technical specialist to ensure that the vessels are maintained and kept operational.
The LNG industry has an impeccable safety record, but this has mainly been driven by project vessels with high investment. The International Code of Safety for Ships using Gases or other Low-flashpoint Fuels (IGF Code) has bridged the gap to make LNG more attainable to vessels than its platinum coated big brother the International Gas Carrier Code (IGC Code). The standard may have been adjusted, but, the risk remains the same.
With such a high safety record there have been few major incidents to date.
Collisions and damage are rare, but, that does not mean they will not happen and when they do occur new problems arise. If the vessel experiences a stability error and should a vessel list or ‘tip’ to one side, it may find a new equilibrium (angle of loll). This higher angle would lead to isolated vapour pockets, when the gas at the top of the tanks has no path to vent, this could increase pressure in the tank to the point of rupture.
Other considerations include collisions and tank breaches, whereby a loss of containment into say, a ballast tank or double bottom, is likely to result in secondary breaches as pressure builds up elsewhere and cannot be relieved as the LNG warms and expands. This is assuming that the LNG does not freeze and plug the leak on contact with any moisture or water!
With new technology being driven by legislation, any operator will need to carefully consider the risks and potential outcomes. Should an incident occur there will be a need for LNG and Hazmat expertise to manage the situation to bring about the best possible outcome.
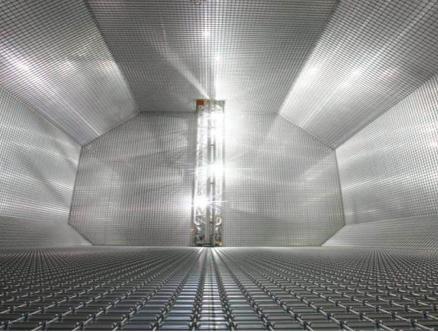
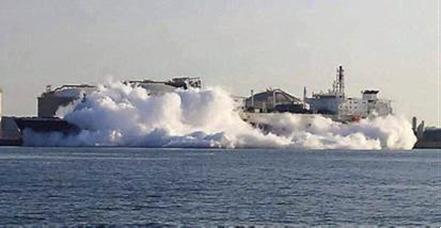