MILWAUKEE COMMERCE
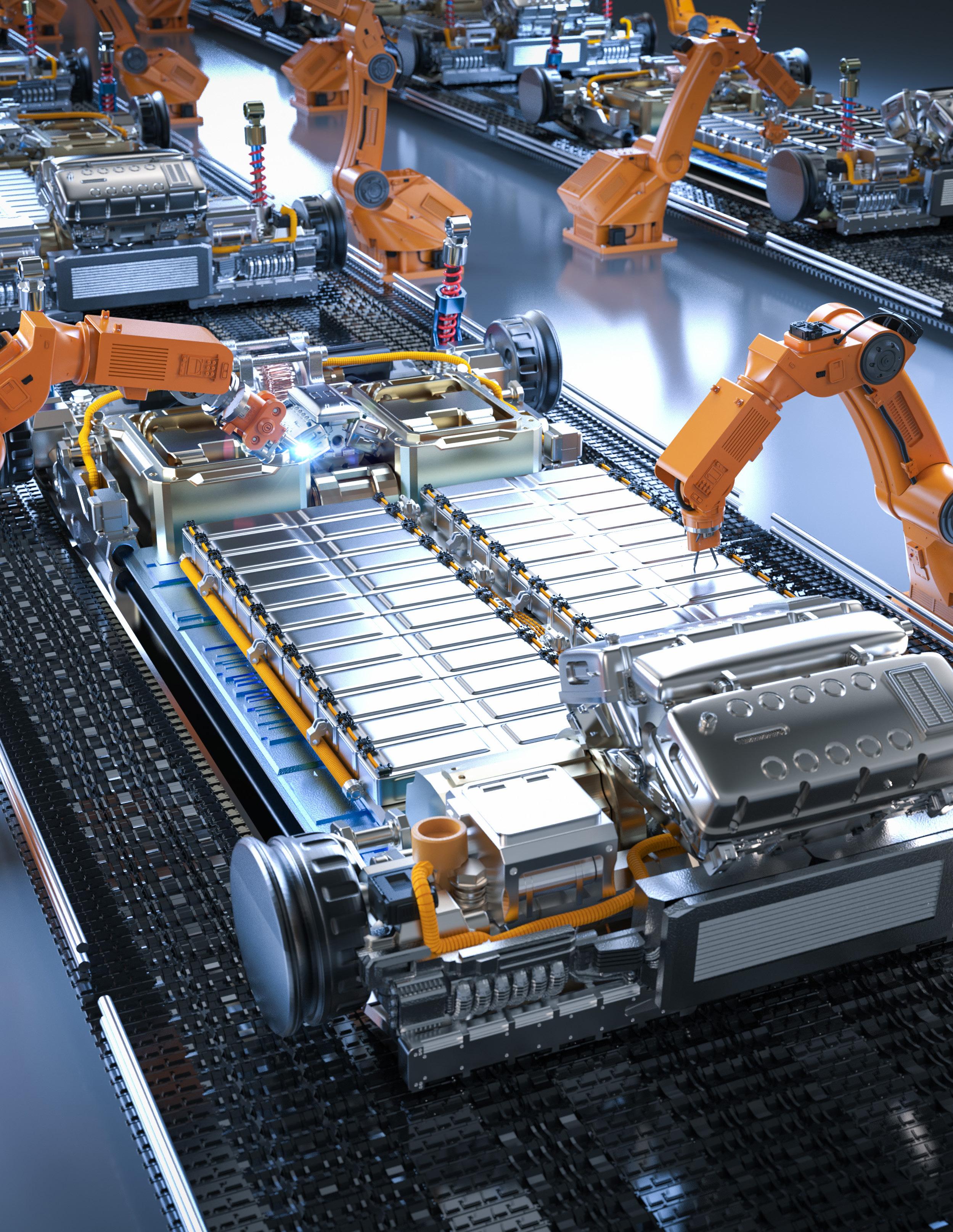
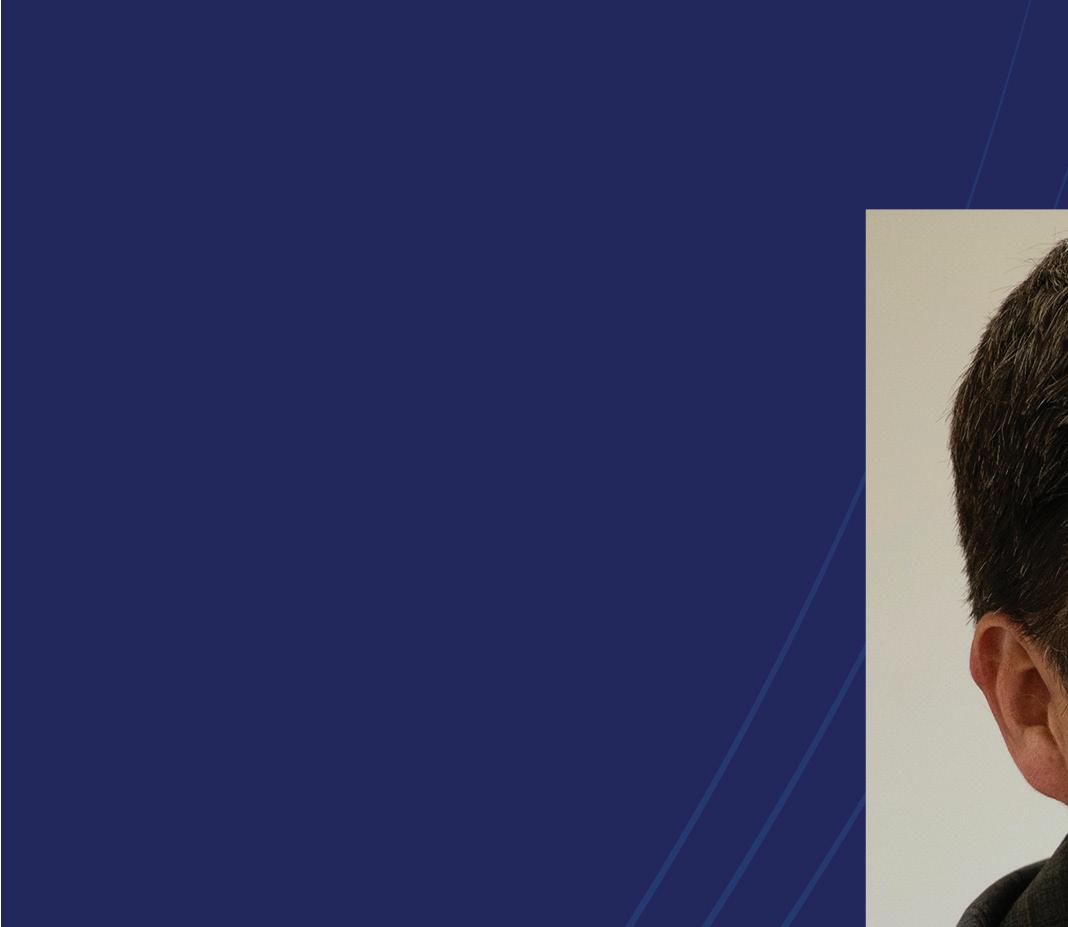
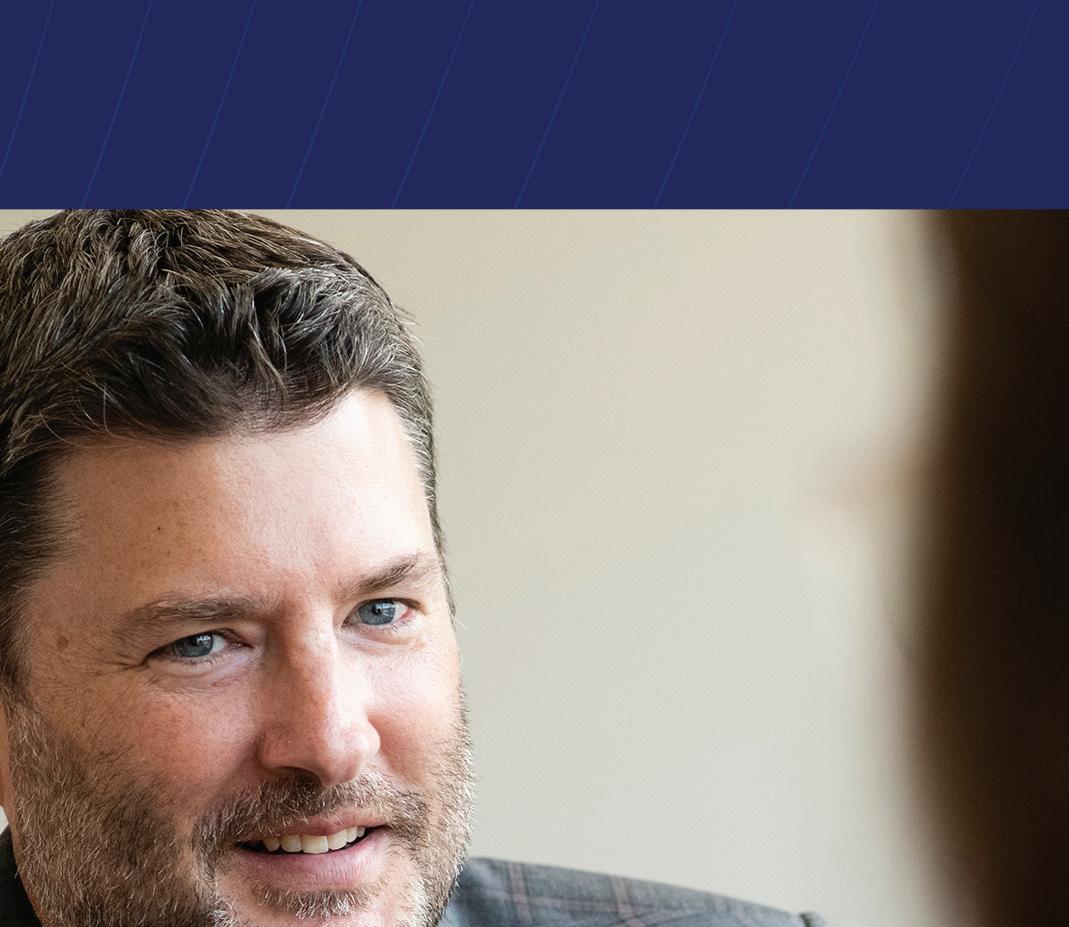

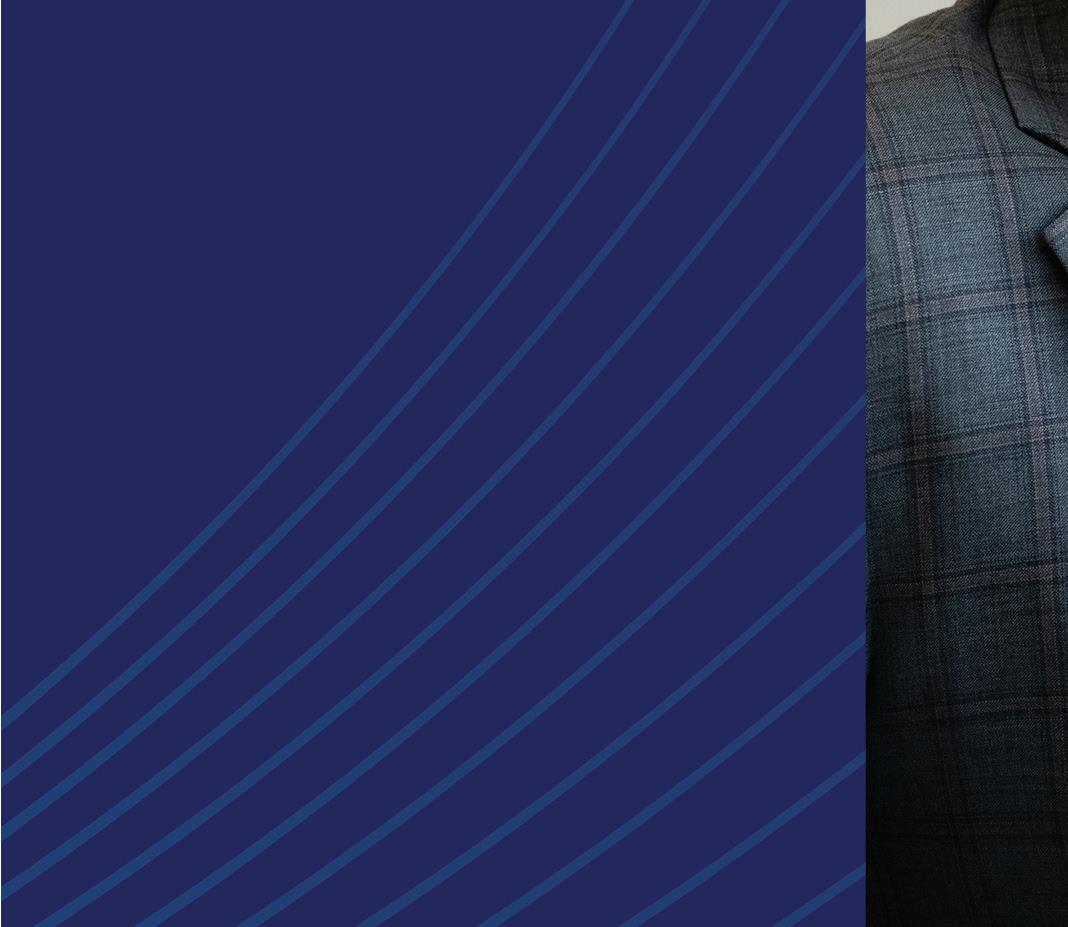
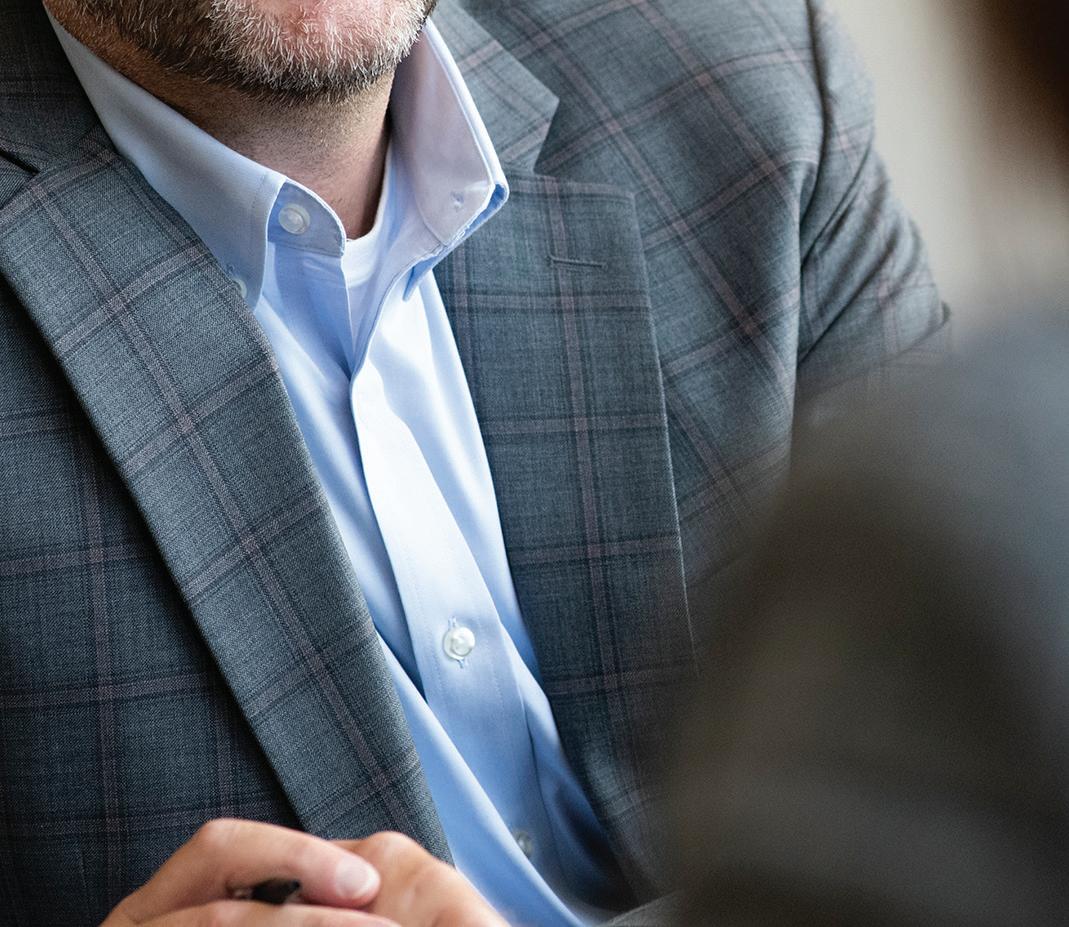
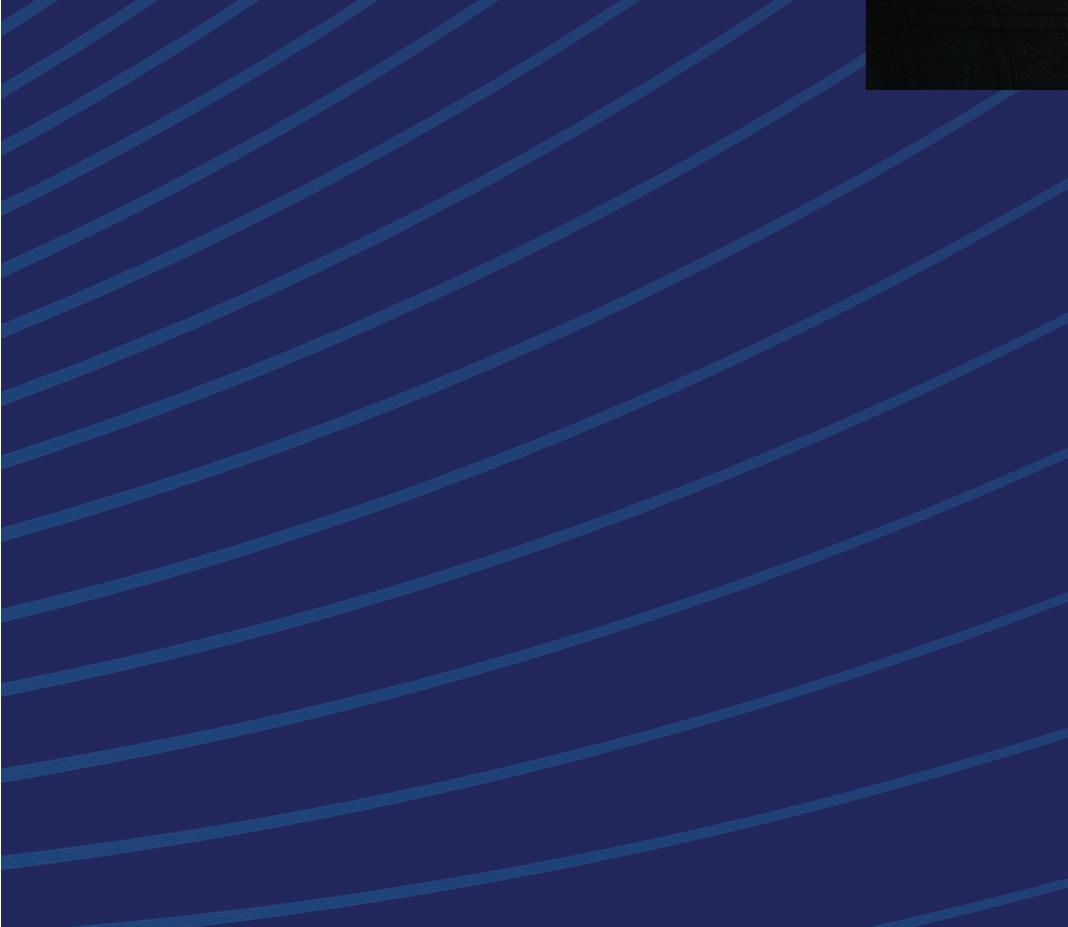
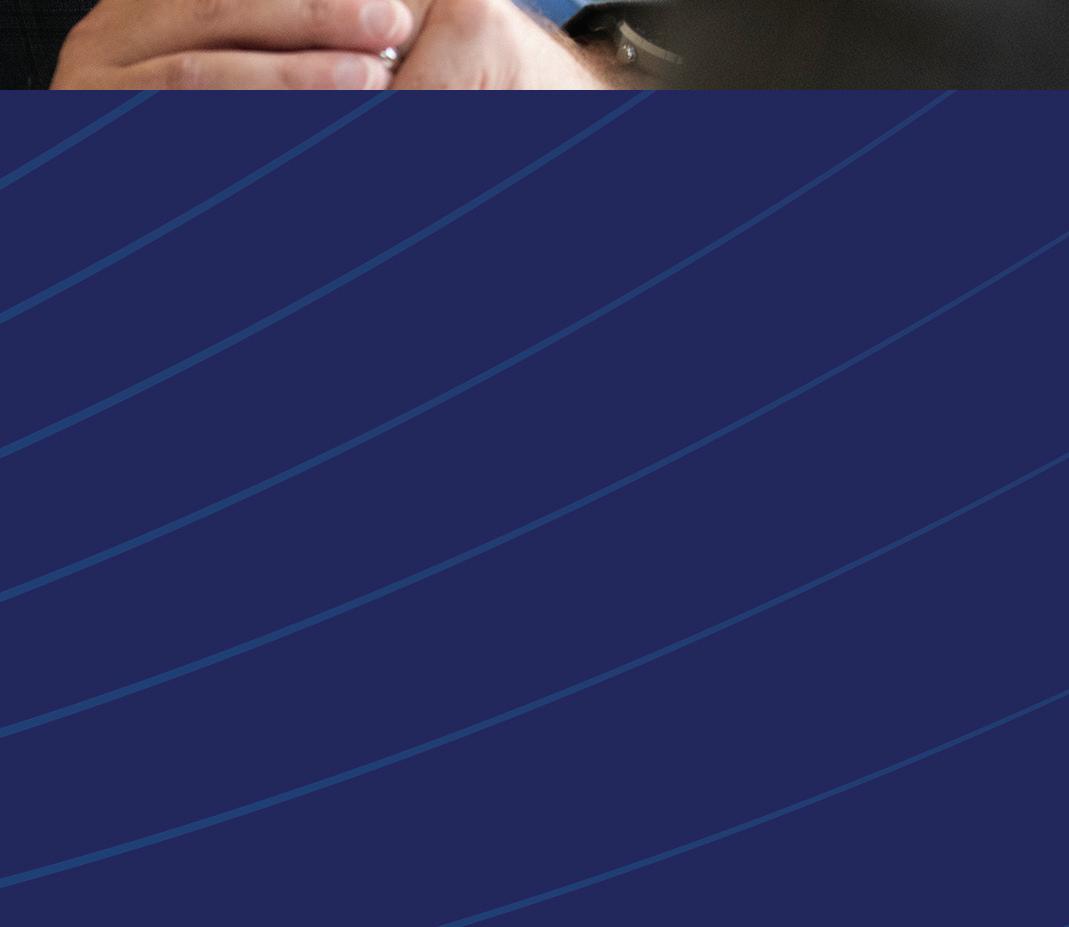
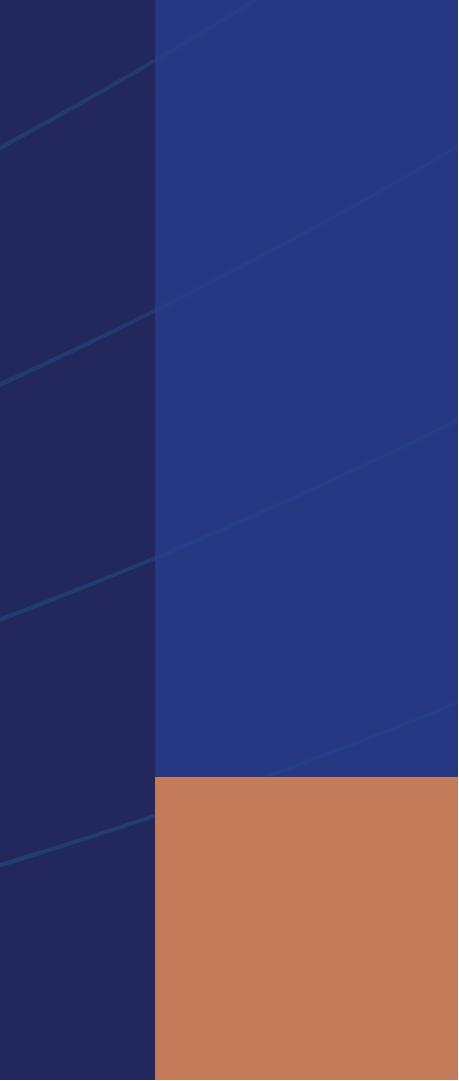

The evolution of the manufacturing industry continues to offer both unprecedented opportunities and ever-present challenges for Milwaukee’s manufacturers. Globalization, a next-generation workforce (that brings with it a mix of remote and in-person employment), evolving supply chain dynamics and advanced technology have made conducting business more competitive and fast-paced than ever before, while traditional manufacturing still plays a vital role in our region’s economy.
Since the firm’s inception, Reinhart has represented some of the world’s leading consumer goods and industrial manufacturing companies, always dedicated to helping each client achieve their greatest potential. We do this by delivering sophisticated yet practical legal guidance rooted in deep experience and knowledge of the industries we serve.
We know that it is essential for manufacturers to have a legal partner that understands the wide range of complex issues they face. Today, we serve as strategic advisers to clients across our region and worldwide, working with them to capitalize on opportunities and navigate obstacles regardless of the issues at hand.
With a deep bench of talent and attorneys with experience that extends beyond the law, we are uniquely prepared to help both new and long-standing manufacturing companies meet these dynamic challenges and extend their success well into the 21st century, and it would be a privilege for us to serve as your Partner in Possibilities
Jack T. Murphy Shareholder jtmurphy@reinhartlaw.com 414.298.8713Manufacturing goes with Milwaukee like beer, brats, the Hoan Bridge and Giannis. This issue of Milwaukee Commerce takes a deeper dive into the state of manufacturing in the region.
Briggs & Stratton. Allen Bradley. Bucyrus Erie. The list goes on and on. These are just a few of the names that helped shape Milwaukee.
From a business and commerce standpoint, they represent the companies that built our economy. But their importance to the region goes well beyond. They’ve shaped our community’s identity. They’ve impacted the lives of generations of families. It’s no mistake that Milwaukee became known as the “Machine Shop of the World.” It was built on the shoulders of these organizations.
While the times have certainly changed – the dirty, dangerous factory floors in many instances have given way to clean, safe, inviting spaces – the importance of manufacturing in our community, as well as its impact globally, is stronger than ever. To paraphrase Mark Twain – reports of manufacturing’s death are greatly exaggerated.
Some of our local legacy brands continue to thrive. Harley-Davidson is still the world’s foremost name in motorcycles. Rockwell has taken a prominent global role in industrial automation. A.O. Smith is a leader in water technology. These companies, and many others, have continued to thrive by employing sustainable practices to keep them competitive.
Examples like these - companies investing in the latest innovations like automation and artificial intelligence – represent the future of manufacturing here, across the U.S. and worldwide.
A recent report released by MMAC shows the industry still plays an outsized role in the region’s economy. With more than 111,000 workers, the industry is second only to the healthcare field in the number of employees. Among major metros, Milwaukee sits near the top for concentration of population employed in manufacturing -- second only to San Jose.
The report also shows the sector is a lucrative one for its employees. The average wage, nearly $74,000, is more than $12,000 higher than the average in all other sectors. These are still family-supporting jobs.
Throughout this issue, you’ll read about the priority MMAC places on manufacturing. We continue to see this sector as the lifeblood of our economy with a huge opportunity for growth.
We are bullish on manufacturing. The region’s success was founded on the sector. Its future will be reliant on it.
Tim Sheehy MMAC President52 men stand inside an enormous dipper for a model 950B stripping shovel (mining) at the Bucyrus-Erie plant in South Milwaukee. Bucyrus-Erie shovels were used to dig the Panama Canal. From the Milwaukee Public Library Digital Collections Several workers stand atop an enormous steam turbine in the Allis-Chalmers Erector shop. Turbines like these were used for the operation of blast furnaces in steel plants, refineries and other industries. From the Milwaukee Public Library Digital Collections
Among major metros, Milwaukee sits near the top for concentration of population employed in manufacturing –second only to San Jose.
Manufacturing goes with Milwaukee like beer, brats, the Hoan Bridge and Giannis. It has served as the backbone of our region’s economy for well over a century – providing the promise of a comfortable lifestyle for generations of families in the region.
Contrary to the popular narrative in some circles, those jobs and the promise they bring haven’t dried up here. According to figures released in a new report from the Metropolitan Milwaukee Association of Commerce (MMAC), manufacturing is still a vital part of the region’s economy. In fact, with more than 111,000 employed in 2021, the industry serves as the region’s second-largest employer behind only the health-care sector.
Produced by Bret Mayborne, Vice President - Economic Research, MMAC
Published November 2022
To view the full report visit, www.MMAC.org/manufacturing.html
Over the short-term, manufacturing job numbers have remained stable in the region, down only slightly - by 1,472 jobs – since 2010. Over the long-term, however, there has been a significant dip in manufacturing employment – falling from 164,699 jobs in 2000.
Nationally, the region compares favorably to the top-50 metros in the country when it comes to the concentration of those working in the sector. Milwaukee ranks second, only behind San Jose, in the percentage of its employees working in manufacturing.
Several occupational areas of manufacturing saw large gains in employment since 2010. On the production side, CNC tool operators (up 95 percent) and welders (up 45 percent) saw large increases. On the professional side, industrial engineers (up 120 percent) and electrical engineers (up 47 percent) were among the biggest gainers, indicating a strong pool of regional talent in these areas.
Manufacturing Statistics for Peer Metro Areas
2010 Jobs 2021 Jobs 2010 - 21 % Change 2021 Jobs L.Q 2021 Ann Pay/worker 2020 Mfg. GDP ($B) Good Exports ($B) 401,337 103,261 116,509 64,649 186,554 85,943 72,146 59,117 112,947 175,146 62,222 87,479 104,285
394,819 115,067 114,787 72,151 240,452 91,511 80,070 77,365 111,475 194,352 80,756 80,044 113,305
-2% 11% -1% 12% 29% 6% 11% 31% -1% 11% 30% -8% 9%
1.08 1.29 1.38 0.82 1.54 1.05 0.91 1.46 1.65 1.23 0.95 0.89 1.04
$85,061 $80,188 $69,242 $69,315 $74,951 $86,591 $68,213 $66,948 $73,786 $82,327 $67,868 $71,389 $76,098
$80.5 $25.5 $20.1 $13.1 $41.2 $20.2 $17.3 $18.0 $17.3 $36.8 $13.1 $13.3 $24.0
$41.3 $21.0 $7.4 $6.3 $30.7 $11.1 $7.9 $8.4 $6.6 $17.1 $6.6 $7.5 $9.1
+45% Welders Milwaukee Louisville St. Louis Pittsburgh
Nashville
+120% Industrial Engineers
+95% CNC Operators
These occupations added more than 6,000 employees since 2010
mmac.org | 7
Of the Top-50 US metros, Milwaukee has the 3rd-largest proportion of production workers as a percentage of all workers
The value of manufacturing product has remained relatively stable, as well, although lagging relative to numbers shown state- and nation-wide. In 2020 the real GDP of manufacturing goods produced in the region was $14.7 billion, a 0.7 percent increase from 2010. During that same period, the state saw an 8.7 percent increase, and the U.S. saw its real GDP in manufacturing increase by 10 percent.
Manufacturing remains a relatively good option for those looking for a well-paying job in the Milwaukee area. Those working in the industry averaged an annual salary of $73,786. That compares to $61,395 for all other industries. Local salary figures were boosted in four of five manufacturing clusters. Jobs in energy, bioscience, machinery and printing outpaced the average pay in all other industries.
Since 2010, wages in manufacturing have increased in aggregate by 27.8 percent in the region – outpacing inflation by 3 ½ percentage points. The increase in wages matched the state (28 percent) but trailed the rest of the country (33 percent).
$73,786 average metro Milwaukee annual pay in manufacturing (2021)
Metro Milwaukee lies in the heart of the industrial Midwest. Real gross domestic product in an 11-state region, all within a 500-mile radius of Milwaukee, represents one-third of national manufacturing output.
Thirteen major metros (1 million plus population) fall in this area and among these metros, Milwaukee stands tall as a manufacturing center. Milwaukee ranks No. 1 amongst these locales in the proportion of its workforce in manufacturing on an industry level (outpacing Detroit), and No. 2 in the percentage of its workforce in production worker occupations (second to Detroit).
Numbers suggest manufacturing is a major factor contributing to regional prosperity across the Midwest. In all 13 major Midwestern metros, pay levels in manufacturing outrank those for all workers in total – with premiums ranging from 43.6% higher in Indianapolis to 3.2% higher in Nashville. Overall, metro Milwaukee ranks in the middle of them on average annual pay in manufacturing ($73,786), but Milwaukee’s manufacturing pay level is notably higher than annual pay for all Milwaukee workers ($61,395), and the resulting 20.2% premium ranks as the fourth-highest in this group.
Also, while some look at manufacturing as blue collar, many in manufacturing are highly trained professionals. The metro Milwaukee economy employs 12,045 engineers, many in manufacturing, with a concentration of engineering talent second only to Detroit.
The metro Milwaukee area has lacked in manufacturing growth metrics. Manufacturing employment has largely moved sideways of late, declining 1.3% in the 2010-2021 period – in the bottom third of large Midwestern metros. Additionally, dollar export activity in goods has fallen year-to-year in six of the past 10 years for a total decline of 13.5%.
The MMAC is well aware of manufacturing’s importance to the region’s economy. Our fiscal wellbeing depends heavily on the health of manufacturing and the jobs it brings to southeastern Wisconsin. MMAC has placed a priority on the industry.
Since 2011, manufacturers filing their taxes with the state have counted on the Manufacturing and Agriculture Credit (MAC) to receive a 7.5% credit for all eligible production activities.
In one budget proposal, manufacturers were in danger of losing this credit in its current form. This would have put an undue burden on smaller companies. MMAC worked with legislators in Madison to save this tax credit.
Additionally, the organization lobbied for the repeal of the personal property tax – which taxes business owners on all goods it owns not considered land or buildings. That repeal appeared in the governor’s budget proposal and is estimated to save businesses about $200 million annually.
Wisconsin sends a significant portion of its manufactured goods to international destinations. According to the Wisconsin Economic Development Corporation, businesses exported more than $26 billion in goods to foreign countries in 2022– an 18% jump over the past 10 years.
MMAC appreciates that working with foreign countries can be complex and has instituted a number of resources for exporters, including:
• Led by experts, our compliance roundtable discussions will improve your company’s effectiveness in trade operations and provide you with actionable knowledge. Watch our newsletter for upcoming topics and dates.
• Access to visiting trade delegations and government officials from countries representing trade opportunities for Milwaukee-area products and services.
• Information on the latest global topics and trends through “Talking Trade,” a semimonthly program of WisPolitics featuring interviews with experts. See more at: wispolitics.com/category/talking-trade
• Certificates of Origin: MMAC is partnering with the American World Trade Chamber of Commerce to provide both electronic and printed Certificates of Origin for Exports.
Engaged in international trade or considering export/import activity?
We’d love to hear from you as we seek to provide the resources you need. Contact Julie Granger, jgranger@mmac.org
When COVID-19 began to spread across the globe in early 2020, ports closed, and ships stacked up as offshore manufacturers shuttered and loading at the docks came to a sudden halt.
As markets reopened in the months that followed, companies began to return to full production. But despite strong consumer demand, manufacturers experienced delays due to shipping problems. Ports were challenged by labor shortages, fewer available ships and even a container shortage, sending freight costs through the roof.
This year, 2023, has seen a much-improved situation, but the aftereffects of the pandemic continue. Even as recently as 2022, outbreaks of COVID-19 variants still spurred sporadic lockdowns in some countries, occasionally still slowing and even temporarily stopping the flow of raw materials and finished goods. In an effort to make up for lost time and sales resulting from uncertain sourcing, most manufacturers increased orders in hopes of catching up. However, now that suppliers are able to ship and deliver, a new issue has arisen—how to deal with increased inventory levels.
As Associated Bank’s Senior Vice President of Commercial Banking Dan Holzhauer explains, “The supply chain backup led companies to build up their inventory with the intent of filling an anticipated backlog of orders. Now all the inventory has come in.”
This leaves manufacturers with a triple problem: Not only are they saddled with excess inventory, but the price they paid for it went up—especially in shipping costs—and, due to inflation and other factors, consumer demand has taken a more cautious turn. However, the preceding years have been good financially; manufacturers are finding that they’ve been able to increase pricing when they needed to and are back to keeping up with demand. The situation has also caused businesses to get back to basics as far as dealing with inventory stocking and management—studying sourcing strategies, seeing inventory as an asset and finding efficiencies in reworking future product planning.
“2023 is still a bit uncertain, but working through their inventory and planning accordingly is a good step,” says Holzhauer. “Supply chain issues have mostly resolved. Now that manufacturers are back to having what they need to run their businesses, they can take this opportunity to take a closer look at how their inventory management system flows: from orders, to transit, to billing and, ultimately, to cash flow.”
The MMAC was pleased to welcome Asutosh Padhi, managing partner for McKinsey in North America, to serve as its keynote speaker during the State of Manufacturing event held in May. He was gracious to sit down for a Q&A to answer some questions about his book, “The Titanium Economy: How Industrial Technology Can Create a Better, Faster, Stronger America” and the future of manufacturing.
The Titanium Economy is a slice of the manufacturing sector known as industrial technology. There are thousands of Titanium Economy companies across the United States, creating things that are essential to our daily lives – but often invisible. For example, building tiny parts for your phone, or designing the process for getting peanut butter into a jar. These companies are primarily B2B, and you don’t often read about them on the cover of major newspapers. But the sector is brimming with innovation, well-paying jobs and profits that rival those of the biggest tech titans. We call the sector the Titanium Economy because it is resilient, pervasive and vital – just like its namesake metal.
For decades, the popular narrative was that the digital age and automation would cripple manufacturing. In your book you argue the opposite. Why is that?
Digital innovations have changed the very nature of factories, making jobs more efficient, comfortable, enjoyable for workers. Most Titanium Economy facilities boast, high-tech equipment that has transformed them into clean, safe and extraordinarily productive operations. In fact, Titanium Economy companies are among the most productive companies operating in the United States today – in large part thanks to these digital investments, paired with smart investments in complementary intangibles like workforce training.
There are many ways for a modern manufacturer to be successful. But we found Titanium Economy companies tend to follow a similar playbook that drives improved performance through a three-step approach.
First, they transform their core. The goal here is to achieve better margins by leveraging data and technology. This leads to more agile decision making, more efficient operations and better products for customers. The net result is enhanced profitability and cash generation.
Second is multiple expansions. These companies focus on portfolio shifts and changes to business models – including recurring revenues and services – to get the market valuation they deserve. In the past 10 years, multiple expansions have become the primary engine of shareholder value, contributing as much as 90 percent of total shareholder value creation.
Lastly, they leverage M&A to achieve a leading position in what we’d call a micro-vertical, or small clusters of 10 to 15 firms in specialty market segments. They then build a platform for future expansion.
In combination, the Titanium Playbook can help any industrial company achieve the next level of performance.
What can regions like southeastern Wisconsin do to attract these manufacturers?
I find it can be instructive to look at a success story – so let’s head to South Carolina and turn the clock back to the 1960s.
At the time, South Carolina was among the poorest states in the nation. It had limited infrastructure and a struggling economy. But it also had acres of sprawling land. Civic leaders recognized this land as a blank canvas for building warehouses and factories; if they could woo companies to the region, there was opportunity to revitalize the economy.
Public and private interests joined forces and worked together to improve everything from ports to roads. The governor even pushed for better technical education across the state, resulting in the establishment of the state’s first technical college. Then 40 years later when Michelin began searching for a place to land, the state was ready.
Michelin now has 9,000 employees spread across 14 sites in the state, with its headquarters in Greenville County. It’s joined by nearly a dozen name-brand companies and manufacturing plants that operate in what’s now known as the Golden Strip.
In 2023, what skills does a successful manufacturing employee have?
This is a workforce that must be trained to work in increasingly automated plants and modern workplaces.
Workers will need to learn new skills like writing software, contributing to the design of better products and conducting data analytics. They’ll also need to be critical thinkers, powerful communicators and strong problem solvers who can make use of the tremendous data at their fingertips.
How are successful manufacturers attracting these skilled employees?
One of my favorite examples comes from Casella Waste Systems, and it is focused heavily on training and career pathing.
A few years ago, Casella partnered with the Stafford Technical Center to offer training for a commercial driver’s license. The course brings students to the company’s facility for 80-plus hours of training on its waste removal vehicles, simultaneously giving them a look inside the company’s doors to get a sense for its culture and wider operations. Casella then pays for the course if attendees give them one year of service upon completion.
What this creates is a robust talent pipeline. Most of the company’s managers and general managers started as drivers. By getting them in the door and providing training along the way, Casella is paving the way for what could be a long, significant career.
The company also gives employees at every level a clear pathway to advancement. For example, a rear-load driver can train to become a front-load driver and later advance to rollout driver and so on. They can go from $18 an hour to $35 an hour in about five years. And this is just one example. They are building career paths for every position in the company.
Why are the next five years crucial for the tech industry in the U.S.?
We are at an inflection point where the U.S. has a clear choice between two paths. First, business as usual, which could see the U.S. fall behind global manufacturing players. Alternatively, a future where the U.S. regains its preeminence as a global manufacturing superpower, powering vibrant Titanium Hubs and a strong socioeconomic backbone across the U.S. But this can happen only if enough people embrace its potential to be a significant part of America’s future economic engine and to usher in a new era of sustainable and inclusive growth.
Brady Corporation, headquartered in Milwaukee and founded in 1914, is touted by the The Titanium Economy’s authors as an example of a thriving company in the Titanium Economy. The term is used to describe companies in the industrial tech sector that supply “aerospace parts, color enamels, and recycled plastic lumber; things consumers don’t necessarily buy but which we all rely on for the functioning of our economy.”
According to co-authors Asutosh Pahdi, Guurav Batra and Nick Santhanam, industrial technology companies, like Brady Corporation, are the fastest growing and most profitable companies in the U.S. economy.
Brady Corporation is a model of the modern, reinvented industrial sector because it has evolved to meet the needs of the marketplace. Today, the company is best known as the manufacturer of identification solutions that are sold to customers in a variety of industries, including electronics, telecommunications, manufacturing, electrical, construction, aerospace and healthcare. With products like labelling and material identification systems, printers, scanners and a whole host of visual workplace safety and compliance products, there are few U.S. companies that do not use at least one of Brady Corporation’s long list of products.
That wasn’t always the case.
Reinvention has been at the heart of the company’s growth since the beginning. The company began as a creator of promotional photographic calendars. It soon scaled its offerings to include point of purchase displays, marketing pieces and roadside advertising. Then, at the start of World War II, Brady Corporation expanded its product line to meet the growing needs of the U.S. military. The company created a new line of wire identification products that offered a solution to the problems faced by servicemen struggling to repair military equipment in difficult and highly variable conditions.
The company’s main production plant on Good Hope Road is used as an example of a modern manufacturing facility in the book. Its 5,700 employees around the world enjoy stable employment, livable wages, and opportunities for advancement while working in clean, well-lit buildings. The clang of machinery from the past has been replaced by the quiet hum of machines guided by skilled employees whose input is integral in the evolution of the business. And driving that manufacturing engine is a global R&D team of software, mechanical, electrical and chemical engineers who continue to introduce new technologies and materials.
Brady Corporation continues its spirit of innovation into the 21st century. By embracing automation and implementing lean process improvements into its operations, the company continues to thrive.
Manufacturing careers represent 140,000 jobs projected in the M7 region by 2025. Elevating the manufacturing industry’s profile in southeastern Wisconsin and aligning its skills needs with education and workforce development requires investing in highquality schools, innovative education and career-based learning. By doing so, we empower the next generation to explore and pursue their future within their own communities.
The workforce is undergoing rapid evolution with the emergence of Industry 4.0, posing a challenge for educators to adequately prepare students for high-tech careers. Lab Midwest is a cutting-edge curriculum, state-of-the-art training equipment
and e-learning solutions provider for education and industry. They provide hands-on, competency-based training programs that empower students with the knowledge and skills needed to pursue lucrative careers. Lab Midwest fosters strong partnerships between industry and educational institutions, including K-12 schools, technical and community colleges, universities and apprenticeship programs. Through these collaborations, Lab Midwest develops comprehensive programs, equips laboratories, and delivers STEM and skilled-trades education, ensuring the highest quality learning experiences available.
“Many high school students are not aware of all the rewarding career opportunities available in the realm of industry and manufacturing. This lack of awareness is partly due to the persistent misconception surrounding manufacturing as being ‘dark, dirty and dangerous,’” said Matt Kirchner, Lab Midwest President. “Moreover, many students do not have access to advanced manufacturing technology within their classrooms, further limiting their exposure to this field.”
To address this issue, several school districts have taken proactive measures by implementing progressive manufacturing curricula, learning systems, hands-on projects and opportunities for exploring manufacturing careers. By incorporating high-tech equipment into the classroom, these districts aim to emulate the modern manufacturing floor environment with curriculum devoted to courses like mechatronics and industrial robot operations and programming.
Top 50 U.S. metropolitan areas: Milwaukee ranks #1 in manufacturing as a percentage of total employment.
Region:
Manufacturing industry jobs
140,000+ are projected in the M7 region by 2025.
Participating students also visit the industrial facilities of each employer partner for a first-hand view of the technology and careers about which they are learning at school. When students pass by a classroom filled with industrial-grade robots, mechatronics systems, digital HMI panels and computers equipped with digital twin software, their curiosity is piqued. This emerging trend is effectively bridging the skills gap problem by generating interest and providing students with practical exposure to relevant technologies and skills.
8,700
Software Developers
7,700 First-line Supervisors of Production
5,900 CNC Operators
5,300 Electrical Assemblers
5,200 Welders
Tim Sheehy, MMAC president, remarked, “We all were kids once. Learning comes alive when you’re connected to something you can see and get excited about. It’s important we do everything we can as a community to get parents, teachers and students exposed to the fields that are strong here in Milwaukee. You can’t be what you can’t see.”
Lab Midwest also equips employers to provide in-house training to their team members in advanced manufacturing skills. Whether you’re onboarding new employees or upskilling and reskilling the current workforce, they have solutions to help your organization remain competitive, including interactive online eLearning, hands-on trainers, virtual simulators, software and certifications.
Sheehy said, “Visiting a (Lab Midwest) lab was an eye opener. It helped me to understand how we can break down the learning journey into bite-sized pieces where students, as well as employees, can add to the skill sets they have in a very disciplined way.”
5,100 Quality Control Technicians & Testers
4,300 Industrial Engineers
4,200 Mechanical Engineers
By 2025, the following positions will be in high demand in the Milwaukee
Our bankers are committed to crafting creative solutions, anticipating your needs, and helping you reach your financial goals. Working with us you gain a true financial partner, and access to a team of experts who know your business and Wisconsin as well as you do. Your success is our top priority. Let us help you achieve your
With the Federal Reserve increasing the interest rate in response to rising inflation, small business owners may be feeling the repercussions of measures to stabilize the economy on their bottom line. What is one way to answer this financing concern? A loan backed by the Small Business Administration (SBA).
The SBA is a government agency tasked with supporting small businesses. SBA-backed loans make it easier for business owners to receive needed funding in the form of a loan, while reducing lender risk. A lending institution processes the loans, which have become an invaluable way for businesses to fund a real estate expansion, or refinance high-priced debt. The SBA guarantees a percentage of the loan for the lender, reducing the risk.
To be approved for an SBA loan, you need to show that you and the business have a history and capability of paying back what you borrow. Many SBA loans will require you to prove at least two years of business activity with a focus on strong revenues. If you’re more than a 20% owner of the business, then your credit score is also important.
Not every business will qualify for each type of SBA loan. Instead, you will have to comply with the specific type of loan you’re seeking. If you’re in a federal disaster area, you could consider applying for an SBA Disaster Loan. If, instead, a falling tree landed on your business’s roof (outside of a disaster zone), then you would need to apply for a different loan.
The SBA 7(a) loan is the most common SBA loan. This loan offers low interest rates and long repayments, allowing for the business to pay back the funds in a cost-efficient manner.
An SBA microloan, on the other hand, is ideal for those situations where affordable funding is required for smaller goals.
Another common loan is the SBA 504 loan, which you might use when investing in large equipment but have few resources for the down payment.
Whatever the goal, when securing financing in the current interest rate environment, it’s important to check whether there’s an SBA loan that might work for your needs. It can help you grow, even in an unsteady economic climate.
Eric Wozny Vice President Wintrust Commercial Banking at Town Bank, N.A. www.townbank.usAs a young person pondering his post high school graduation plans, Fred Anderson was unsure of his path forward. Should he pursue college at his own expense? Keep working a job he had at a local grocery store? The answer came through a referral from a close friend who had recently been hired by a New Berlin manufacturing firm – WentheDavidson Engineering Co. Anderson took a job making $4.15 per hour – a full dollar more than he had been earning. And the growth opportunities at Wenthe were plentiful. Anderson was able to pursue technical training at Waukesha County Technical College (WCTC) and later earned a B.S. in business adminstration from Carroll University while working.
Today, 46 years later, Anderson is president and CEO of the company, which is still providing bright futures for its 250 employees.
Wenthe-Davidson is thriving because it is laser focused on its customers, according to Anderson. “If you give them what they want – they will stick around,” said Anderson. Wenthe customizes products in days, so customers don’t need to carry inventory, and ships roughly 15,000 products across North America daily. It continues to grow, now with two locations, and the potential to max out its current space with 30,000 additional square feet.
It’s the interaction between people, treated with respect and kindness, that keeps people here.
Anderson attributes the growth and longevity of the company to its workforce – one that is extremely diverse, including Black, Latino, Laotian and Eastern European immigrant employees. That diversity is important to Anderson, as evidenced by the company’s pledge to take part in MMAC’s Region of Choice initiative. Since launching the Region of Choice initiative in 2019, MMAC has tracked the progress of the 125-plus companies and organizations, including Wenthe-Davidson, that have committed to increasing the percentages of Black and Brown employees (by 15 percent over five years) and managers (by 25 percent over five years) at those firms in aggregate.
At a time when most manufacturers, and indeed most employers, are finding it extremely difficult to attract talent, Anderson says that most of Wenthe’s workers find them through word of mouth. “Networking is key. Our employees tell their friends and families so most candidates are referrals. If you can’t weld, we’ll teach you.” He added that after three to six months on the job, employees tend to stay long-term.
Employee retention is driven by the opportunity to advance within the company and become an owner. Wenthe-Davidson became an ESOP (Employee Stock Ownership Plan) in 1985 at 30% and in 2017 became 100%. “I talk to every employee as if they own the company – because they do,” notes Anderson. “Manufacturing can be mundane at times, but it’s the interaction between people, treated with respect and kindness, that keeps people here.”
Anderson believes the manufacturing industry would benefit from an overall rebrand to “technology support.” Says Anderson, “Nothing today is manufactured without tech. At every step there’s robots, computers, laser welders. People are in white coats more than overalls. If you want a high-tech career, it can easily be in manufacturing.”
Anderson’s operating philosophy and company culture has helped many employees develop personally and professionally. “I believe in promoting from within. New people see themselves represented in supervisory roles, so they envision a future here,” said Anderson. Some workers are starting a new chapter in their life when they take a job at Wenthe. One employee came to the company after serving a lengthy prison sentence. With a gift for communication and nine years of floor experience he was elevated to a Supervisor position. “We try to be supportive of everyone’s needs and go the extra mile. It’s a lot more rewarding to invest in people than equipment. And the payback is better,” explains Anderson.
Wenthe-Davidson Engineering Company was founded By William Wenthe and Arthur H. Davidson (yes, THAT Davidson of HarleyDavidson) on March 7, 1941, on 31st and Cherry streets in Milwaukee.
Originally the company was a progressive job shop fabricating processing tanks. By the late sixties, Wenthe had evolved into a modern supplier to the electric motor and generator industry, providing them with steel housings and other value-added services.
Wenthe-Davidson Engineering Co. is part of the Region of Choice initiative to collectively increase the number of African American and Hispanic/Latino employees in metro Milwaukee with the goal of making Milwaukee’s workplaces more inclusive. See more at MMAC.org
Anderson attributes the growth and longevity of the company to its workforce – one that is extremely diverse, including Black, Latino, Laotian and Eastern European immigrant employees.
Drought threatens an agribusiness’ stability, reducing yields and potentially wiping out harvests. This affects everyone in agribusiness, from farms, fisheries and ranches to those in food production and distribution. Currently two-thirds of the state of Wisconsin are experiencing drought-like conditions.
Developing a risk mitigation plan to minimize drought risk can help those in agribusiness prepare for dryer than normal conditions. Here are four ways to do just that:
The agriculture industry is operating under considerable pressure because of labor shortages, rising costs and heightened competition, so think about harnessing public-private partnerships, which were established to encourage innovation and provide aid for droughts. Take the Environmental Quality Incentives Program for example. This program aims to provide financial and technical assistance to agribusinesses. They can not only offer different irrigation methods but help producers identify additional water conservation methods, create soil additives and improve soil quality.
In addition, look into resources that help with employee management. This is especially important for those with employees using an H-2A visa. Employers who understand and know how to harness the tools and resources available to manage their employees more effectively will help ensure that seasonal workers come back, saving time and resources on training.
Perform a risk factor assessment.
Incorporating a risk factor assessment
- a historical study of drought - into your plan can help you mitigate and prepare for drought challenges. These can help inform decision making even if the intensity and probability of a drought can be difficult to predict. Here are five different methods that can help farmers reduce the overall impact of a drought:
• Evaluating and improving the management of existing irrigation systems
•Residue and tillage management
•Micro irrigation
•Crop rotation
•Creating an irrigation schedule
Obtain government assistance. Extreme heat, low water levels, and even surging power that can cause rolling blackouts are factors that can impact producers’ ability to water their crops. Taking advantage of the federal government assistance programs available can help mitigate the financial losses of drought, while harnessing conservation programs help farmers become more resilient to it. For example, the U.S. Department of Agriculture’s Regional Conservation Partnership Program provides funding to help with climate-smart agriculture and conservation efforts. There is also federal crop insurance available to help to mitigate risk, which can be especially beneficial for larger operations. The USDA Risk Management Agency provides financial assistance to farmers in drought-affected areas as well, which can be especially helpful for small agribusinesses.
Learn the early warning signs and identify risks.
There are two ways that farmers and food manufacturers can help identify drought risk. The first is to monitor water levels; the second is to create an impact assessment. Implementing these two measures can help secure proper insurance and government assistance.
More tools are becoming available to obtain short-term and long-term weather outlooks, such as the National Weather Service’s Climate Prediction Center, which can assess weather up to two weeks in advance. Those in agribusiness may even want to consider purchasing their own moisture evaluation tools to assess soil water levels vs. depending on an outside vendor to perform the assessment.
Growers might also consider parametric coverage for crops that are otherwise uninsurable. Parametric coverage insures against an event happening with payouts based on the magnitude of the weather event, no matter the damage to the crop or buildings.
Limiting the threat of a water shortage by incorporating drought preventative measures such as those mentioned above into your agribusiness strategy can help address drought-related risks.
The objective: Hammer a nail. Simple enough. It’s a task done millions of times a day around the world.
Now, try doing it in eight steps or more without the hammer in your hand by using a combination of applied science principles. Oh, and then theme your project in a fun, creative way.
A team of four 11-year-olds from Clarendon Avenue Elementary School in Mukwonago, naming themselves “Carnival Crew,” nailed it – literally and figuratively – at Contrapt Wisconsin, a Rube Goldberg-like contest for students interested in science, technology, engineering and math (STEM) education and coordinated by STEM Forward. The sixth-graders took home fourth place out of 44 teams competing at the May event on MSOE’s campus.
“We were given pretty vague instructions,” said Abigail Kutcher, a member of the team. “It’s fun to come up with the physics of it. You have to have persistence and grit.”
Kutcher’s teammate, Evelyn Witte, added, “I like the problemsolving piece.”
The two pre-teens were among hundreds who took part in the competition during two events in the region –one at MSOE, the other at Waukesha County Technical College. It’s opportunities like these that change the narrative for students.
“Our role is to provide as many onramps as possible … make engineering and technology fun,” said Rich Merkel, Executive Director of STEM Forward. “How they get engaged in STEM? It’s not a one-size-fits-all.”
STEM Forward looks much different than it did at its founding, all the way back in 1905. It started when a group of 59 area engineers formed the Engineering Society of Milwaukee, renamed Engineers & Scientists of Milwaukee.
At the time, the purpose of the Society was to form a “cooperative body, broad enough in scope to meet the needs of all engineers and technical men in the community,” according to the organization’s website. The priority has shifted in recent years.
“Since the 1990s, the focus has been on STEM education,” said Merkel.
STEM Forward is now southeastern Wisconsin’s leading non-profit, technical organization providing and promoting educational outreach programs – like Contrapt Wisconsin – emphasizing science, technology, engineering and math.
That priority and the work STEM Forward is doing to turn young people on to careers in these areas is more important than ever. This is especially true in the manufacturing sector. In a recent survey conducted by the National Association of Manufacturers, nearly 75 percent of respondents listed attracting and retaining a quality workforce as their primary business challenge. A study done by Deloitte and The Manufacturing Institute in 2021 showed that a manufacturing skills gap in the U.S. could result in 2.1 million unfilled jobs by 2030, potentially costing the U.S. economy $1 trillion annually.
Merkel is hearing similar things from those in the profession within the region. “Local manufacturers are concerned about the talent pipeline,” he said. “We have to get students thinking about engineering, manufacturing careers.”
Anecdotally, within the halls of MSOE during the Contrapt Wisconsin contest, the tide seems to be turning in that direction.
Connor Maier, 13, and an 8th-grader at Longfellow Middle School, said he loves working on engineering projects like the one he took part in at Contrapt Wisconsin. His love of math and science drove his interest in the contest.
“It’s always new, there’s nothing repetitive,” he said. “I’ve always been interested in putting things together and trying to figure out how they worked.”
Maier said he’d love to go into something in math or science when contemplating a career. “Maybe a mathematician,” he said.
“I like to search for new ways to get stuff done,” he added.
The curiosity and interest shown by the students at the contest in the sciences, and maybe a job in the manufacturing industry, is indicative of a changing mindset.
“There’s a gradual shift underway,” Merkel said regarding perceptions of the manufacturing industry. “It’s being viewed more positively.”
And regardless of the industry, the things students are learning today in STEM are becoming adapted universally regardless of the vocation.
“Across all industries, they’re becoming technology companies,” Merkel said. “They need employees with these problem-solving skills.”
Investment in real estate has traditionally been perceived as a good hedge against inflation over the long-term; however, due to the localized nature of real estate and existing lease terms, some properties are better positioned than others. This article briefly outlines why certain real estate will outperform in today’s market.
Rent Growth – Apartments and hotels can raise rents more frequently, due to the short-term leases/reservations. In contrast, office, retail and industrial leases are often measured in years, with rent increases at a fixed percentage. If inflation outpaces that fixed percentage, owners will realize below-market rents during the lease.
Vacancy – If not well-located or well-maintained, occupancy may suffer, and the property’s rents may not pace inflation. Trends of net migration to southeast and other tertiary markets (like
Madison, WI) have resulted in the strongest rent growth over the last three years, whereas markets with negative net migration have suffered.
Expenses – Inflation hedging works best in a demand-driven environment, but today’s market features both demand-driven and cost-driven inflation. Office, industrial and retail properties may be able to pass through increased expenses, depending on the lease terms. Owners who can push expenses to tenants and raise rents will be best positioned.
Patrick Carroll President and General Counsel Investors Associated LLP investorsassociated.comFOR MORE INFORMATION CONTACT:
jstefan@iallp.com investorsassociated.com
Tech sector titan is making a big bet on southeastern Wisconsin
In March, Microsoft announced plans to purchase a 315acre parcel of land in the Village of Mount Pleasant for the construction of a data center campus. Those plans were approved by the village and Racine County in April and the land sale completed in May, marking a huge win for economic development in southeastern Wisconsin.
“We are proud to move forward with this highly anticipated development,” said Village of Mount Pleasant President David DeGroot. “The purchase of this land, which has been transformed in recent years, is a win for taxpayers and residents alike.”
“Microsoft is clearly one of the world’s most successful technology companies – a global leader in creating customer and shareholder value,” said Gale Klappa, co-chair of M7, MMAC Board member, and Executive Chairman of WEC Energy Group. “This respected, innovative company will be an incredible addition to the regional and state economy.”
Per the development agreement, the 315-acre campus represents a $1 billion investment by Microsoft. It also represents another big win for our region. Microsoft is expected to construct multiple buildings on its Mount Pleasant campus.
“Village, County and State officials planned for a long-term future to accommodate development and investment by a variety of companies,” said Racine County Executive Jonathan Delagrave. “We have presented a tremendous opportunity for companies, like Microsoft, to invest.”
Microsoft Director of Community Engagement Paul Englis added that the company needs a skilled, highly educated workforce, and Wisconsin offers that. “All boxes are checked when it comes this location,” Englis said.
Microsoft’s commitment goes beyond the jobs it creates in the community. Englis stated the company has a history of investing in community programs, prioritizes sustainability to minimize environmental impact and is committed to transparency and engagement when laying down stakes in any community.
“I am excited by Microsoft’s decision to locate in Mount Pleasant,” said Missy Hughes, Secretary and CEO of the Wisconsin Economic Development Corporation (WEDC). “Microsoft joins a roster of innovative, worldclass companies that are choosing to grow in Wisconsin because of our highly educated workforce, outstanding infrastructure, central location, and unparalleled quality of life. We welcome Microsoft to our state and look forward to working with them to ensure they succeed.”
“This respected, innovative company will be an incredible addition to the regional and state economy.”
-Gale Klappa, co-chair, Milwaukee 7
Every two years, state budget negotiations take on immense importance in setting the priorities and charting a course for the state of Wisconsin.
Those negotiations took on a greater importance in 2023.
Issues the Metropolitan Milwaukee Association of Commerce (MMAC) have spent many years and thousands of hours working on – the future of state-shared revenue, a new sales tax for the city of Milwaukee and an increase in the existing sales tax in Milwaukee County, and a closure in the funding gap among students throughout the state – were on the front burner during the biennial budget process.
Compromise and collaboration resulted in big wins for the state and its residents.
“We applaud Gov. Tony Evers, Assembly Speaker Robin Vos, Senate Majority Leader Devin LeMahieu and their respective chambers for the hard work and collaboration they displayed in getting these groundbreaking items to the finish line,” said MMAC President Tim Sheehy. “While the political philosophies of those coming to the table differed, good governance resulted in decisions being made in the state’s best interests.”
The MMAC Board of Directors had the opportunity to engage with those members of state leadership this spring during two separate board meetings.
For two decades, a freeze in state-shared revenue has hamstrung municipalities and their ability to provide basic services to their residents. As part of the new state budget, all municipalities, regardless of size, will see an increase in shared revenue.
In the city of Milwaukee and Milwaukee County, stagnant funding from the state coupled with rising costs of pension liabilities has led to cuts for both governing bodies. Staffing in the city has been reduced by 1,000 positions since 2000. During that same period, Milwaukee County has been forced to cut nearly half of its staff, reducing headcount from 7,300 to 3,900.
“The freeze in state-shared revenue to the city of Milwaukee and Milwaukee County has led to decisions that impact public safety and the quality of life for residents and visitors,” said Sheehy. “This
increased funding is one piece of the puzzle when it comes to the region’s fiscal issues.”
Milwaukee, for many years, has been one of the very few large cities in the U.S. unable to enact a local sales tax without the approval of the state legislature. Under the state’s biennial budget the city, as well as Milwaukee County, will have that ability.
Language in the state budget item will allow the city to levy a 2 percent sales tax on top of its existing 5.5 percent sales tax. The county will have the ability to add a .4 percent sales tax.
The additional revenue can be used to fund public safety and pension liabilities.
“New sales tax revenue for the city of Milwaukee and Milwaukee County, coupled with an increase in state-shared revenue, is a clear-and-present solution to the fiscal cliff both bodies were facing if nothing had been done,” said Sheehy. “These new streams of revenue provide the region fiscal solvency and make it attractive to potential residents and businesses looking to make a move.”
The state budget also provided a big win for K-12 students across the state. The gap in spending between public school students and those attending choice or charter schools will decrease significantly.
For K-8 students in the choice program, vouchers will increase from $8,400 to $9,500 annually. For high school students, vouchers will increase from $9,045 to $12,000 annually. For charter school students, vouchers will increase from $9,264 to $11,000 annually.
“These increases create a more equitable playing field for students regardless of the school they attend,” said Sheehy. “More resources will result in a larger number of students prepared for life after school, and a richer pool of talent for employers in the region.”
A measure within the budget will also increase special education spending for those attending private schools, increasing funding from just over $13,000 per student annually to $14,677.
For years, MMAC has worked tirelessly for increased shared revenue, local sales tax, equitable educational opportunities
We applaud Gov. Tony Evers, Assembly Speaker Robin Vos, Senate Majority Leader Devin LeMahieu and their respective chambers for the hard work and collaboration they displayed in getting these groundbreaking items to the finish line.
OUR MEMBERS’ SUCCESS IS AT THE HEART OF
NORTHERN TRUST COMPANY
MEMBER SINCE 2000 Banks
www.northerntrust.com
MMAC’s Member Appreciation Tour randomly selects businesses located across southeastern Wisconsin to discuss their views on the top opportunities and challenges facing their company and the Milwaukee Region. Thank you for giving us your valuable time to connect in person.
HNTB CORPORATION
MEMBER SINCE 1962
Engineers-consulting www.hntb.com
MADER’S RESTAURANT
MEMBER SINCE 1932 Restaurants madersrestaurant.com
“It is imperative to be engaged with the business community, to leverage policies and make the region attractive for businesses and employees.”
MEMBER SINCE 1949 Dentistry
www.riverwalkdentistry.com
RIVERWALK DENTISTRY SC
LITERACY SERVICES OF WISCONSIN
MEMBER SINCE 2017 Education
www.literacyservices.org
MILWAUKEE ADMIRALS LLC
MEMBER SINCE 1973 Sports clubs
www.milwaukeeadmirals.com
AMERICA WORKS OF WISCONSIN, INC.
MEMBER SINCE 2016 Employment agencies
www.americaworks.com
ANDRUS INTELLECTUAL PROPERTY LAW LLP
MEMBER SINCE 1942
Attorneys – patent, trademark & copyright law
www.andruslaw.com
“We are members because we want to understand the direction the state is going...the information provided by MMAC has been very important to us.”
“MMAC’s advocacy for workforce engagement is great – as there is potential to find employment for those coming out of correctional facilities, immigrants and the unschooled.”
Professional development is a smart investment – in your employees as well as in your organization. Providing your employees with learning opportunities not only enhances their growth potential within the company but also contributes significantly to their overall job satisfaction. These opportunities can greatly assist your retention efforts as well which is a win-win for all.
Training programs, however, are not one-size-fits-all. UWM’s School of Continuing Education offers professional development and adult education programs across a wide variety of areas, all of which can be customized to meet your organization’s specific needs. For instance, you may have a select group of employees who could benefit from one of our many programs such as leadership, project management or digital marketing. Your training objective may be to:
• Establish baseline subject matter knowledge within a team
• Develop emerging leaders across your organization
• Create a credential specific to your business
Whatever your goal, our program content can be condensed or expanded to concentrate on the topics that are most relevant to your team. And if you prefer the content just as it is and simply want the program delivered conveniently in your own office setting, we can do that too!
Our customized training consultants are ready to help. Let us know how we can tailor our programs to meet your professional development needs – and watch your employees grow from ordinary to extraordinary!
Take your business to the next level by offering your employees the opportunity to increase their skills. From learning improved processes or something completely new, UWM’s School of Continuing Education is here to help. Explore our powerful lineup of programs ... and watch your team go from ordinary to extraordinary! Ask us about our custom programs where we can bring the classroom to your team.
Bradley Woods is a multi-faceted innovator.
Woods spent most of his career in software development. In his free time, he indulged in his passion for art. Both a painter and a sculptor, Woods longed to create art using metal, but he did not have access to a metal foundry.
Anna Lardinois StorytellerUndeterred, Woods began to experiment with ways to create a three-dimensional metal work. He tried electroplating, a process that uses electrical current to deposit metal onto a solid surface as a substitution for poured metal, but he was unsatisfied with the results.
Later, he received a 3D printer from a friend. The gift sparked an idea.
Woods was uninterested in the plastic models generated from the 3D printer, so he began to experiment with ways to create metal objects using the tool. He tried mixing powdered metals with a thermal polymer and ran it through the machine to see if he could create a metal object.
The results of this experiment were magnificent and became the basis of his company, The Virtual Foundry.
Launched in 2015, Woods patented the technology that allows people to create solid metal objects using his materials and a 3D printer. Sold by the kilo, his metal filaments start at $120 for copper or bronze and up to $1,200 for titanium filaments.
“If you consider $1,200 per kilo and you’re only using 12 grams of the material, it’s way less expensive than the other manufacturing techniques. A traditional manufacturing technique would be considered subtractive. You start with a large block, and you carve away the things you don’t want. All of the material you carve away is waste that gets thrown out. This is how traditional machining and CNC (computer numerical control) machining works,” Woods explained.
Continued on page 33
Spectrum Reach, a leading multi-screen advertising solutions company, is at the forefront of combating ad fraud, vexing actions that prevent digital ads from running where they are supposed to, or from being seen by intended audiences.
When ads are not seen by the right consumers—or sometimes by actual humans at all—they fail to generate brand exposure, leads, and sales. The result is wasted or even stolen marketing dollars. To make matters worse, publishers are also hurt by lower returns on ad spend and a decrease in the overall value of ads on their platforms. Most importantly, when business owners lack confidence that their ads are being seen by intended audiences, they lose trust in advertising providers and reduce their ad spend.
In an effort to fight ad fraud in all its forms, Spectrum Reach partners with third-party verification company Oracle Moat Analytics to ensure that all of their inventory has been seen by real people and is held to the highest key performance indicators. In 2022, Spectrum Reach also developed and issued a Brand Safety Guide*, which educates businesses on how to prevent ad fraud and protect their ad spend. They were the first local media sales organization to become a TAG Platinum member, a leading global initiative fighting criminal activity in the digital advertising industry.
To learn more about how Spectrum Reach is educating advertisers about ad fraud and providing them with a solution, go to SpectrumReach.com
*https://www.spectrumreach.com/publisher-sourcing-disclosure
continued from page 31
“This is a crucial advantage of additive manufacturing, you only add the parts you need,” he continued.
Woods spent years perfecting the process that allowed him to produce his filament on a commercial scale. Scientists are some of his most enthusiastic customers.
“Our biggest customers are the Office of Science National Laboratories…. The military also has a network of research labs, and we do all four branches of the military,” Woods said.
“The scientists working with this stuff are looking for, not an evolutionary improvement on something. They want a revolutionary improvement… It’s a chance to rethink manufacturing,” he said.
Not only are some of the most advanced labs in the country using The Virtual Foundry materials, so do some of the nation’s largest companies. Lockheed Martin, Mitsubishi and NASA are among the company’s long list of clients.
The bootstrapped company had a unique start. Woods launched a Kickstarter campaign to raise funds for the company. The online campaign collected $32,000 and, perhaps more surprising, an invitation to speak about this invention in the Hubble Auditorium on the Lockheed Martin campus. Woods calls the experience a “nerd highlight.”
The Qualified New Business Venture certified company is again considering a capital raise, but Woods knows the task won’t be easy.
“Part of what makes our company unique is that it’s based on an invention. What I didn’t fully understand is that anything based on something that’s new has no existing market. It’s been very difficult to get investors to understand what we’re doing,” Woods said.
“I think some of the upsides look improbably large… It seems improbable, but it is happening,” he continued. “For example, one of the materials we made is this moondust simulant. We’re about to release a filament 3D printable moondust simulant that scientists will use for developing methods of fabricating on the moon with the resources that are there.”
Employer-sponsored benefits are a key factor in keeping employees happy and attracting the best workers to grow your business. However, it can be time-consuming and costly for small businesses to be competitive when it comes to providing insurance.
That’s why it’s important to create a benefits plan that works for both your small business and bottom line. Here are some key factors to consider as your business grows.
Benefits offer advantages for your business.
While you may think of insurance as primarily helping your employees, they also benefit your business through:
• Increased productivity. Forbes reports that offering dental, vision, and wellness benefits leads to happier, healthier, and more engaged and productive employees with lower absenteeism.
• Tax advantages. Talk with your accountant to see if you can deduct your contributions for dental and vision benefits.
• Fostering a culture of caring. Dental and vision benefits are a good way to show employees you care about them and their families.
Dental and vision insurance are highly desired. Dental and vision benefits are the second-most requested benefits by job seekers. Employee Benefit News labels them as “must-have employee benefits.”
Insurance may be more affordable than you think. For instance, there are many options for dental and vision plans, including voluntary plans where employees pay part or all of the monthly premium.
Taking care of employees is the best thing businesses of any size can do to make sure they are successful. Offering dental and vision benefits and encouraging employees to have annual exams will help keep them healthy and productive.
Jackie Bloomer Sales Executive Delta Dental of Wisconsin (414) 659-0481 deltadentalwi.comSome Wisconsinites grow up around fishing or football. Anne Cookson grew up around pizza.
Emily Allen Communications Director“I have pizza sauce running through my veins,” she jokes. The co-founder of Crustology®, a pizza crust manufacturer based in Waukesha, Cookson is no stranger to the slice and has a long family history in the pizza business.
Cookson and her brother, Chris Miller, are thirdgeneration owners of Baker’s Quality Pizza Crusts, from which Crustology® emerged as a subsidiary in 2020. Cookson’s grandfather owned and operated the eight Milwaukee-area Shakey’s locations, supplied by a central commissary which was later taken over by Cookson’s parents and transformed into a food distribution business. By 1997, the family found their niche and sold everything but the crust manufacturing portion.
“Baker’s Quality was built on doing one thing really well,” explains Cookson.
Crustology® produces what they call a “Midwest cracker crust,” a callback to the “old-school pizza restaurants in Milwaukee.” Manufacturing approximately 20,000 crusts per year, the company utilizes a traditional 24-hour fermentation process for their dough, creating three crust options: The OG, Herb-Infused and The Micro Brew, a beer-infused crust born from a partnership with Lakefront Brewery.
While Baker’s Quality mostly sells to wholesale distributors, Crustology® is direct to consumer for baking pizza at home.
“Lots of people want to make their own crust because they want to know what’s in it...so we’re providing them
with basically that exact same thing. This crust is as good as somebody is going to make in their own house, if not better,” says Cookson.
In 2020, the company relocated to a larger plant, a move that Cookson says increased their production capacity several hundred times over and allowed them to make new equipment purchases that improved product quality. All Crustology® crusts are made in this 25,000-squarefoot production facility. Maintaining a dedicated staff has been key.
“We benefit from a robust labor pool in Milwaukee and enjoy the commitment to work that our employees have,” Cookson says.
Big things are in the works for the coming year, with plans to expand their product line to include pizza sauce and seasoning and “drastically increase” the number of crusts manufactured to make the jump into retail stores. Despite the accelerated growth, Cookson’s pride for Milwaukee and passion for Wisconsin tavern-style pizza aren’t going anywhere.
“Milwaukee has such a vibrant food scene, and pizza is a large part of that. The food industry is so fun and interesting. There is constant innovation and I love seeing the new products that come out each month.”
FaB, Wisconsin’s food and beverageWe benefit from a robust labor pool in Milwaukee and enjoy the commitment to work that our employees have.
City of Milwaukee Mayor Cavalier Johnson addressed attendees at MMAC’s annual legislative reception, thanking state-elected officials for all the work they do and showcasing the Milwaukee region and its companies.
At CG Schmidt, we’re committed to quality from conception to completion. We create spaces where businesses can grow, manufacturing advances are made and relationships are formed. As your trusted building partner, we recognize that the success of your work ultimately depends on ours, and we look forward to working with you today so we can build a better tomorrow, together.
MMAC’s Leadership Council members went behind the scenes at Milwaukee Tool’s $55 million manufacturing facility in West Bend, where for the first time, they are making hand tools in the U.S.
, Wm. K. Walthers, Inc.
MILWAUKEE 7
Guests heard insights from the MMAC’s State of Manufacturing report and views from Asutosh Padhi, co-author of “The Titanium Economy: How Industrial Technology Can Create a Better, Faster, Stronger America.”
Guests enjoyed the 3rd Street Market Hall and snapped some pictures in the Photoverse Selfie Museum at MMAC’s March Business After Hours. Pictured: Vania Jurkiewicz, United Performing Arts Fund; Bob Piekenbrock, Good Karma Brands; Ana Cook, United Performing Arts Fund; and Kylie
Milwaukee Downtown
1547 Critical Systems Realty
Chris Teeluck Sales Director, Midwest 324 E. Wisconsin Ave., Ste. 1010 Milwaukee, WI 53202 (414) 212-4355
1547realty.com
Data Center Operators
24:Up, Inc. 520 W. Juneau Ave. Milwaukee, WI 53203
24-up.com
Youth Organizations/Centers
Argon Industries, Inc.
Gregory Clement, President 11500 W. Brown Deer Rd. Milwaukee, WI 53224 (414) 354-8939
argonind.biz
Manufacturers
Atomix Logistics
Austin Kreinz, Founder & CEO 2203 W. Michigan St. Milwaukee, WI 53233 (414) 231-0788
atomixlogistics.com
Logistics/Transportation
Aventus Data Centers
Lance Dieken VP of Business Development 7901 W. Clinton Ave. Milwaukee, WI 53223
aventusdatacenters.com
Data Center Operators
Basic Crating & Packaging, Inc.
Nell Kohlwey-Frank Building Manager 5250 S. 6th St. Milwaukee, WI 53221 (312) 318-1080
basiccrating.com
Packaging Services
Bear Development S.R. Mills, CEO 4015 80th St., Ste. F Kenosha, WI 53142 (262) 842-0456
beardevelopment.com
Real Estate Developers
Bear Homes 4039 80th St. Kenosha, WI 53142 (262) 842-0600
bearhomes.com
Home Builders
Bear Property Management 4015 80th St. Kenosha, WI 53142
bearpropertymanagement.com
Real Estate Management
BEAR Real Estate Group
S.R. Mills, CEO 4015 80th St. Kenosha, WI 53142 (262) 694-2327
bearreg.com
Real Estate Bear Realty 4011 80th St. Kenosha, WI 53142 (262) 694-2327
bearrealty.com
Real Estate Advisors
Bell Ambulance, Inc.
Chris Anderson Director of Operations 549 E. Wilson St. Milwaukee, WI 53207 (414) 486-2000
264bell.com
Transportation Services
Bellwether Funding LLC
Bill Frey, Senior Partner 251 W. Broadway, Ste. 206 Waukesha, WI 53186 (414) 217-0369
bellwetherfunding.com
Financing
Best Buddies
Caroline Tyson Director, Development 10425 W. North Ave., Ste. 340 Wauwatosa, WI 53226 (414) 704-4043
bestbuddies.org/wisconsin Nonprofit Education
Construction Management Associates, Inc.
S.R. Mills, CEO 4015 80th St., Ste. F Kenosha, WI 53142 (262) 842-0452
cmaofwi.com
Construction Management
Fabricated Metal Products Company, Inc.
James Robinson, President 3240 E. Van Norman Ave. Cudahy, WI 53110 (414) 294-3000
fabmet.com
Metal Fabricators Federation Financial LLC
Tony Kosobucki, President 13555 Bishops Ct. Brookfield, WI 53005 (262) 204-7877
FederationFinancial.com
Financial Services
Finnco Fabricating LLC
James Robinson, President 2031 S. Aldrich St., Ste. 3 Milwaukee, WI 53207 (414) 486-1690
finncofabricating.com
Metal Fabricators
Full Sail Leadership Academy
Tim Dittloff
Chief Learning Strategist 11025 W. Armour Ave. Greenfield, WI 53228 (414) 839-9184
fullsailleadership.com
Consultants/Leadership
Hausmann Group
Barry Richter, President N25W23050 Paul Rd. Pewaukee, WI 53072 (262) 521-5700
myhaus.com
Insurance Hire Up LLC
Amanda Mast, Fractional Talent Acquisition Consultant/Owner 8425 Stickney Ave. Wauwatosa, WI 53226 (920) 723-3892
hireupresults.com
Recruiting Firms
Hyatt Place Milwaukee Downtown Kylie Helgestad, Sales Manager 800 W. Juneau Ave. Milwaukee, WI 53233 (414) 808-3814
hyatt.com/en-US/hotel/ wisconsin/hyatt-placemilwaukee-downtown/mkezd Hotels/Motels
Insight Investment Advisers
Brandon Bruckman, Adviser 200 S. Executive Dr., Ste. 100 Brookfield, WI 53045 (414) 322-3237
investwithinsight.com
Financial Planning-Consultants
Interim HealthCare of Milwaukee, WI Angelo Aguirre, Owner 700 W. Virginia St., Ste. 205 Milwaukee, WI 53204 (608) 888-9948
milwaukeewiinterimhealthcare. Home Health Care Services
IT’s UpTime
George Grubor, Partner Advisor PO Box 12011 Green Bay, WI 54304 (920) 214-8100
itsuptime.com
com
FEBRUARY - APRIL 2023
Kinn GuesthouseBay View
2535 S. Kinnickinnic Ave. Milwaukee, WI 53207 (888) 546-6021
kinnguesthouse.com/bayview-mke
Hotels/Motels
Kinn GuesthouseDowntown
Michael Dietrich, General Manager 600 N. Broadway Milwaukee, WI 53202 (414) 305-3658
kinnguesthouse.com/milwaukee
Hotels/Motels
Kwench Juice Cafe MKE
Lilah Calhoun, Co-owner 2220 N. Prospect Ave. Milwaukee, WI 53202 (414) 316-9785
Kwenchmilwaukee.com
Restaurants
Light the Hoan
Erika Smith, Executive Director 207 E. Michigan St. Milwaukee, WI 53202
lightthehoan.com
Community Engagement
Magnolia Tax Services
Eugene Marshall, CEO 6675 W. National Ave., Ste. 325 West Allis, WI 53214 (414) 285-2446
magnoliataxservices.com
Tax Deferral/Planning Solutions
Matthew Holbrook
COUNTRY Financial
Matthew Holbrook, Owner 757 N. Broadway, Ste. 202 Milwaukee, WI 53202 (414) 332-2137
advisors.countryfinancial.com/ usa/wi/milwaukee/matthewholbrook
Insurance
OF MILWAUKEE
Make a difference in the community when your company supports the Zoological Society and get your brand in front of more than 1 million guests a year.
BECOME A CORPORATE PLATYPUS CIRCLE MEMBER
• Transferable Membership Cards
• Invitations to VIP events
• Name recognition
• Special Zoo benefits for your employees
• Rental discounts and more Go to BeAPlaty.org to learn more.
GRANT OPPORTUNITIES
• Education programs for underrepresented populations
• Conservation efforts
• Capital investments
SPONSORSHIPS
• Event and attraction opportunities
• Boost your brand
• Engage with customers
Contact Mary Kay Gundlach at 414-918-6155 to learn how you can take advantage of these exciting opportunities.
Messmer Catholic Schools
Erica Zdroik, VP of Advancement 742 W. Capitol Dr. Milwaukee, WI 53206 (414) 264-5440
messmerschools.org
Education
Messmer High School
Shenora Jordan, Principal 742 W. Capitol Dr. Milwaukee, WI 53206 (414) 264-5440
messmerschools.org/studentsand-families/messmer-highschool
Education
Messmer Saint Mary
Kendra Kuhnmuench, Principal 3027 N. Fratney St. Milwaukee, WI 53212 (414) 264-6070
messmerschools.org/studentsand-families/messmer-saint-mary Education
Messmer Saint Rose
Elizabeth Fritsch, Principal 514 N. 31st St. Milwaukee, WI 53208 (414) 933-6070
messmerschools.org/studentsand-families/messmer-saint-rose Education
MLG Capital
David Binder, Senior VP 19000 W. Bluemound Rd. Brookfield, WI 53045 (262) 797-9400
mlgcapital.com
Real Estate
MWH Law Group LLP
Mercedes De La Rosa
Associate Attorney 735 N. Water St., Ste. 610 Milwaukee, WI 53202 (414) 436-0353
mwhlawgroup.com
Legal Services
Continued on page 50
FEBRUARY - APRIL 2023
115 years
Michael Best & Friedrich
WEC Energy Group
110 years
Quarles
75 years
GE Healthcare
45 years
Hyatt Regency Milwaukee
35 years
Bruck Law Offices SC
Great Lakes Roofing Corporation
Lauber Business Partners
30 years
Metro Business Publications
Westown Association
25 years
Heritage Printing
Hotel Metro
Lange Bros. Woodwork Co.
Marquette University High School
Metal-Era
Milwaukee Downtown BID #21
River Run
Rodrian & Associates/Rodrian Insurance
United Performing Arts Fund
20 years
AFFIRM Agency
Confluence Graphics
DHI Corp.
Founders 3 Commercial Services
Grace Matthews
Humana
Mandel Group/Trostel Square Apartments
20 years continued
SIGNARAMA MILWAUKEE
VJS Construction Services
Wagner Falconer & Judd
WisPolitics.Com & WisBusiness.Com
15 years
Bostik
Cornell Communications
Marsh & McLennan Agency
S3 AeroDefense
U-Haul Company of Eastern WI
Veolia Water Milwaukee
WMEP Manufacturing Solutions
10 years
Blue Ribbon Management
Chiropractic Company
Fairfield Inn & Suites by Marriott -
Milwaukee Downtown
Guy & O’Neill
Kahler Slater
Milwaukee Professional Firefighters Association
Really Resourceful Group
Rose & deJong SC
Ryan Companies
SEKO Logistics
STIR
Wolter
5 years
Alliant Energy
Ansay & Associates
Axley Attorneys
Carlson & Erickson Builders
Carlson Dash
CIBC Cleary Gull
DISTek Integration
Grant & Cohodes dba Grant & Cohodes Insurance Services
Granular
HUB International Limited
5 years continued
J Carpenter Environmental
Kane Communications Group
Lake Country Manufacturing
Life Storage- Glendale
Mid-States Concrete Industries
Milwaukee Composites
O’Reilly Motor Cars
Pediatric Home Service
Plum Media
Reed Street Insurance
Triple Win Strategies
WurkHub Digital Marketing
1 year
Agora Learning & ConsultingCrestcom Int’l Licensee
BI WORLDWIDE
Carl Collective
Chisel and Vine
ConsortiEX
Culligan Of Waukesha
Dykema Gossett
EWH University for Small Business
Expedient
Food For Health
Fox, O’Neill & Shannon SC
Frank Productions
Fusion Recruiters
Gateway Capital
Gimbel Reilly Guerin & Brown
Harwood Engineering Consultants
Horicon Bank
Horicon Bank - New Berlin & West Bend
Milwaukee Youth Arts Center
Port Washington State Bank
Prescient Solutions
Project Echelon
Signature Bank
SoftwareONE
The Trade Hotel Milwaukee
Wacker Neuson America Corp.
MMAC.org/Staff.html
Corporate Expansion & Attraction
Jim Paetsch | jpaetsch@mke7.com
Ryan Amundson joins MMAC after spending 17 years in communications at Potawatomi Casino Hotel. Prior to his time at the casino, Ryan spent six years reporting and editing at several newspapers in southeastern Wisconsin. He holds a journalism degree from the University of Wisconsin-Whitewater and resides in Wauwatosa with his wife and two boys.
Khenzer Senat comes to MMAC after spending six years at the Republican Party of Wisconsin where he was the African American Engagement Director. He has built relationships with faith-based leaders, business owners and community activists in the African American community as well as recruited candidates to run for local and state offices in Wisconsin. He is a graduate of Wisconsin Lutheran College with a B.A in communications with an emphasis in political communications.
Away from work, Khenzer lives in West Allis with his wife, Heidi; son, Sebastian (14 months) and their Whippet/Retriever, Harmony.
Economic Development
Lynn Olberding | lolberding@mke7.com
Economic Trends & Research
Bret Mayborne | bmayborne@mmac.org
Federal, State & Local Government
Andrew Davis | adavis@mmac.org
Equity & Inclusion
Corry Joe Biddle | cbiddle@mmac.org
GROW YOUR PEER NETWORKS AALAM
Walter Lanier | wlanier@aalamilwaukee.org
The Business Council
Marjorie Rucker | mrucker@mmac.org
Executive Roundtables
Chauntele Kreutz | ckreutz@mmac.org
Food & Beverage Industry
Gina Balke | gbalke@fabwisconsin.com
Hispanic Collaborative
Nancy Hernandez | nhernandez@mmac.org
Leadership Council
Barb Smith | bsmith@mmac.org
Networking Forums
Marjorie Yoshida | myoshida@mmac.org
GAIN EXPOSURE FOR YOUR BUSINESS
Advertising
Jane Trenchard-Backes | jbackes@mmac.org
Events & Sponsorship
Karen Powell | kpowell@mmac.org
Small Business
Stephanie Smith | ssmith@mmac.org
My goal is to make information accessible and engaging at MMAC. I’m focused on providing our stakeholders the information they need, as well as telling their stories, in new and exciting ways.”
I’m excited and blessed to join the Governmental Affairs team at MMAC! I’m eager to utilize the relationships that I’ve built with elected, civic, corporate and community leaders to advocate for a better Milwaukee and the state of Wisconsin.”
Anxiety affects nearly 30% of people1 at some point in their lives and often goes hand in hand with depression, which affects about 16 million American2 adults a year. Studies show that 4 in 10 U.S. adults who needed mental health treatment in the last 12 months did not get it3.
As these numbers continue to climb, accompanied by a flood of demand for mental health care, access to virtual behavioral health care resources may help to address unmet patient need.
The reasons are complex and numerous, but stigma, cost, convenience and access to affordable resources are among some of the factors impacting Americans’ ability to get help for their concerns or illnesses. People are often unsure as to whether their feelings require treatment or if it’s situational and something that can be managed through changes in lifestyle for example.
Virtual care, also referred to as telehealth, may be part of the solution. These resources have steadily gained popularity over the last few years and continue to accelerate —with technological advancement attempting to meet demand.
Not every situation calls for telehealth and digital solutions are still being studied for how they may fit into overall care planning for individuals, but virtual behavioral health services may play a role in helping to alleviate the mental health crisis.
Take inventory of what may be of interest for you in terms of care. Start with asking yourself whether you wish to be assessed by a licensed professional for your mental health. Would you prefer in-person or virtual care? Do you seek focused problem solving like personalized coaching, rather than treatment?
Your primary care physician (PCP) can be a great ally and guide—even if you want to explore virtual mental health options.
Speak with Your Insurance Provider
Describe the care you’d like to receive and ask about available options and therapists that are covered in-network, helping you understand your choices and keep costs down.
Don’t wait to seek support for yourself or those around you – resources are available.
1 https://www.psychiatry.org/patients-families/anxiety-disorders/what-are-anxiety-disorders#:~:text=Anxiety%20disorders%20are%20the%20most,people%20 lead%20normal%20productive%20lives.
2 https://www.cdc.gov/tobacco/campaign/tips/diseases/depression-anxiety.html
3 https://www.thenationalcouncil.org/news/more-than-4-in-10-us-adults-who-needed-substance-use-and-mental-health-care-did-not-get-treatment/