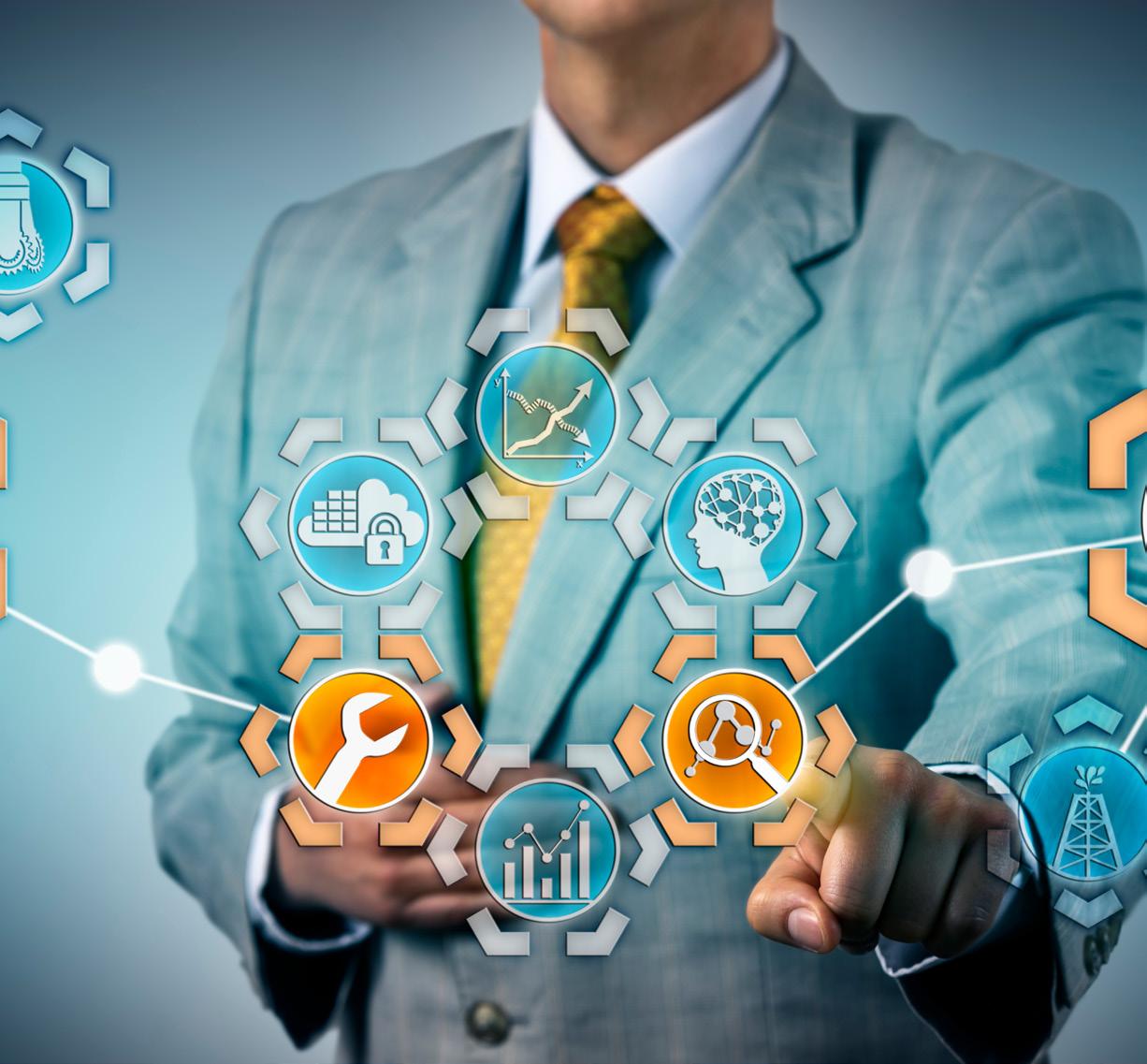
5 minute read
Transforming Oil and Gas Operations with Digital Twins
Digital twins are revolutionizing the oil and gas sector by enhancing efficiency, safety, and sustainability through real-time insights and predictive capabilities
The oil and gas sector, characterised by its high capital investment, complex operations, and stringent safety requirements, has increasingly embraced digital innovation to enhance efficiency and sustainability. One of the most transformative technologies in this regard is the digital twin. A digital twin is a virtual replica of a physical asset, system, or process, powered by real-time data and advanced analytics. This technology allows companies to simulate, predict, and optimize their operations in ways previously unimaginable. This article explores the applications, benefits, and challenges of digital twins in the oil and gas industry.
Applications of digital twins in oil and gas
Digital twins are being used extensively across various stages of the oil and gas value chain, from exploration and production to transportation and refining. In the exploration phase, digital twins of geological formations are created using seismic data, well logs, and other geological information. These digital models enable geoscientists to simulate drilling scenarios, assess reservoir characteristics, and optimise well placement, thus reducing the risk of dry wells and maximising resource recovery.
In production, digital twins of offshore platforms, drilling rigs, and other critical infrastructure help monitor and manage operations. By integrating data from sensors, control systems, and historical records, these digital replicas provide a comprehensive view of equipment performance and process efficiency. For instance, operators can simulate various production strategies, predict equipment failures, and schedule maintenance activities proactively, thereby minimising downtime and enhancing productivity.
Transportation of oil and gas via pipelines and tankers also benefits from digital twins. Virtual models of pipelines, for example, allow operators to monitor flow rates, detect leaks, and predict corrosion or other integrity issues. This predictive capability is crucial for maintaining pipeline safety and preventing environmental disasters. Similarly, digital twins of LNG (liquefied natural gas) carriers enable real-time monitoring of voyage conditions, optimising route planning, and ensuring the safe delivery of cargo.
In refining, digital twins of processing units such as distillation columns, reactors, and heat exchangers enable operators to optimise plant performance. By simulating different operating conditions and process adjustments, refiners can maximise throughput, improve energy efficiency, and reduce emissions. Additionally, digital twins facilitate advanced process control and predictive maintenance, further enhancing operational reliability and profitability.
Benefits of digital twins in oil and gas
The adoption of digital twins in the oil and gas sector offers numerous benefits, driving significant improvements in efficiency, safety, and sustainability. One of the primary advantages is enhanced operational efficiency. Digital twins enable real-time monitoring and optimisation of processes, leading to better resource utilisation and reduced operational costs. For example, by simulating various production scenarios, operators can identify the most efficient strategies, minimising energy consumption and maximising output.
Another significant benefit is improved asset management. Digital twins provide a detailed and dynamic representation of equipment and infrastructure, allowing for predictive maintenance and timely interventions. This proactive approach helps prevent unplanned downtime, extends the lifespan of assets, and reduces maintenance costs. Furthermore, digital twins facilitate better planning and scheduling of maintenance activities, ensuring minimal disruption to operations.
Safety is a critical concern in the oil and gas industry, and digital twins play a vital role in enhancing safety standards. By providing real-time insights into equipment health and process conditions, digital twins enable early detection of potential hazards and anomalies. This early warning system allows operators to take preventive measures, mitigating the risk of accidents and ensuring the safety of personnel and the environment. For instance, digital twins can predict pipeline leaks or equipment failures, enabling timely repairs before catastrophic failures occur.
Environmental sustainability is another area where digital twins offer significant benefits. The ability to optimize operations and reduce energy consumption directly contributes to lower greenhouse gas emissions. Additionally, digital twins help in monitoring and managing environmental compliance by providing accurate data on emissions, effluents, and other environmental parameters. This data-driven approach supports regulatory compliance and promotes sustainable practices in the industry.
Challenges in implementing digital twins in oil and gas
Despite the numerous benefits, the implementation of digital twins in the oil and gas sector is not without challenges. One of the primary challenges is data integration and management. Digital twins rely on vast amounts of data from various sources, including sensors, control systems, and historical records. Integrating and managing this data in real-time requires robust IT infrastructure and advanced analytics capabilities. Moreover, ensuring the accuracy, consistency, and reliability of data is critical for the effectiveness of digital twins.
Another significant challenge is the complexity of creating and maintaining digital twins. Developing accurate and detailed virtual models of complex assets and processes requires specialised expertise and significant investment. The models need to be continuously updated with real-time data to reflect the current state of physical assets accurately. This dynamic nature of digital twins adds to the complexity and demands continuous monitoring and maintenance.
Cybersecurity is a growing concern with the increasing reliance on digital technologies in the oil and gas sector. Digital twins, being connected to critical infrastructure and operations, present potential targets for cyber-attacks. Ensuring the security and integrity of digital twins and the data they rely on is paramount. Implementing robust cybersecurity measures and protocols is essential to safeguard against potential threats and vulnerabilities.
The adoption of digital twins also requires a cultural and organisational shift within companies. Traditional oil and gas operations have been primarily mechanical and manual, and the transition to digital and automated systems can face resistance. Training and upskilling the workforce to operate and maintain digital twins is crucial. Companies need to invest in developing digital competencies and fostering a culture of innovation and continuous improvement.
The cost of implementing digital twins is another challenge, particularly for smaller companies with limited resources. Developing and deploying digital twins involves significant upfront investment in technology, infrastructure, and expertise. While the long-term benefits are substantial, the initial cost can be a barrier to adoption for some companies. Demonstrating the return on investment and the value proposition of digital twins is essential to justify the expenditure.
Regulatory and compliance issues can also pose challenges to the implementation of digital twins. The oil and gas industry is highly regulated, and any new technology must comply with stringent standards and regulations. Ensuring that digital twins meet these regulatory requirements and obtaining the necessary approvals can be a complex and time-consuming process. Collaboration with regulatory bodies and standardization of digital twin technologies can help address these challenges.
A transformational technology
Digital twins represent a transformative technology for the oil and gas sector, offering significant benefits in terms of efficiency, safety, and sustainability. By providing real-time insights and predictive capabilities, digital twins enable optimized operations, enhanced asset management, and improved safety standards. However, the implementation of digital twins is not without challenges. Data integration and management, complexity, cybersecurity, organizational change, cost, and regulatory compliance are some of the key hurdles that need to be addressed. Overcoming these challenges requires a strategic approach, investment in technology and skills, and a commitment to innovation and continuous improvement. As the industry continues to evolve, digital twins will play an increasingly critical role in driving the future of oil and gas operations, ensuring they are more efficient, safe, and sustainable.
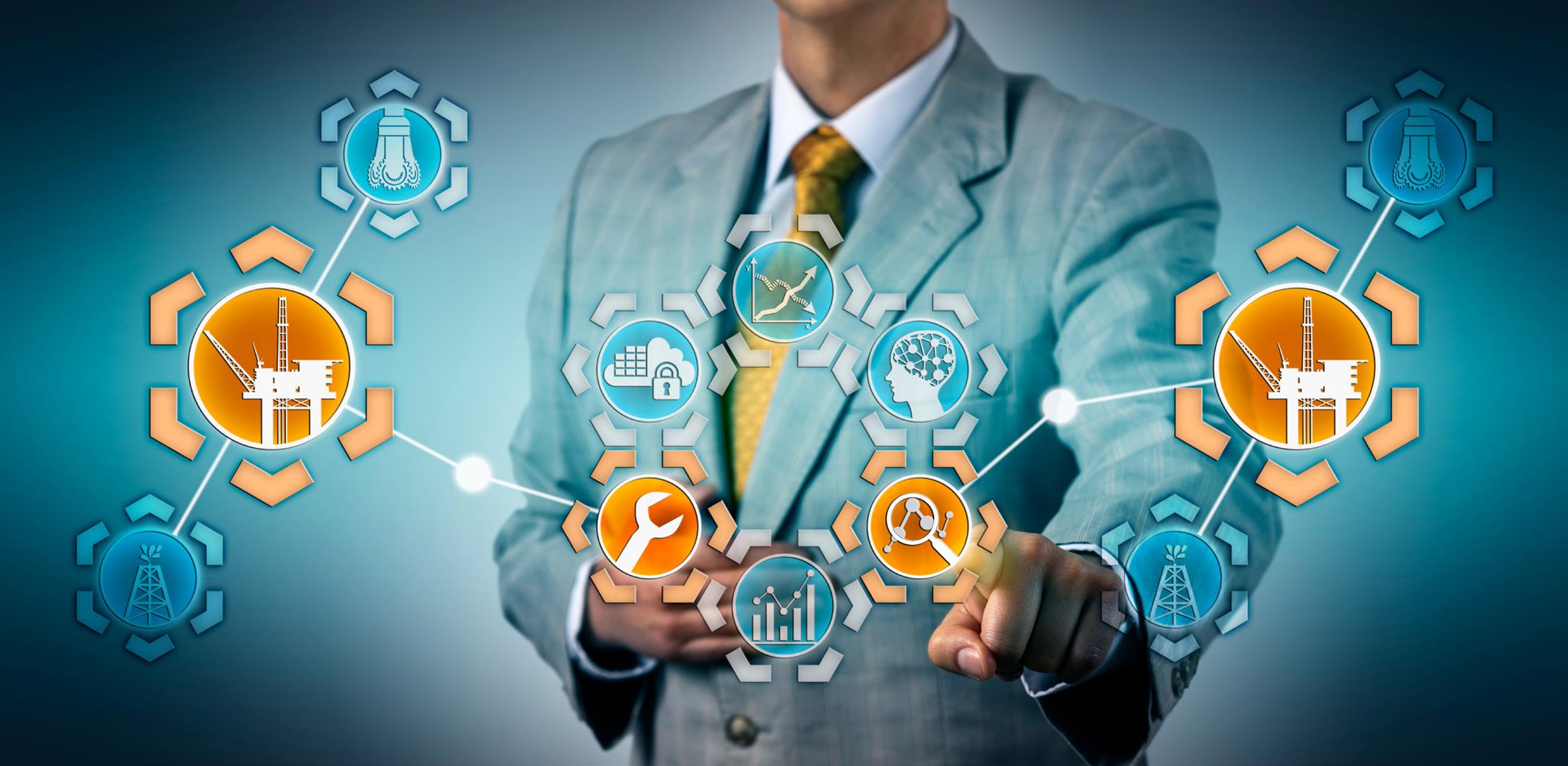
for the Energy Industry

IECEx / ATEX certified
LoRaWAN-based
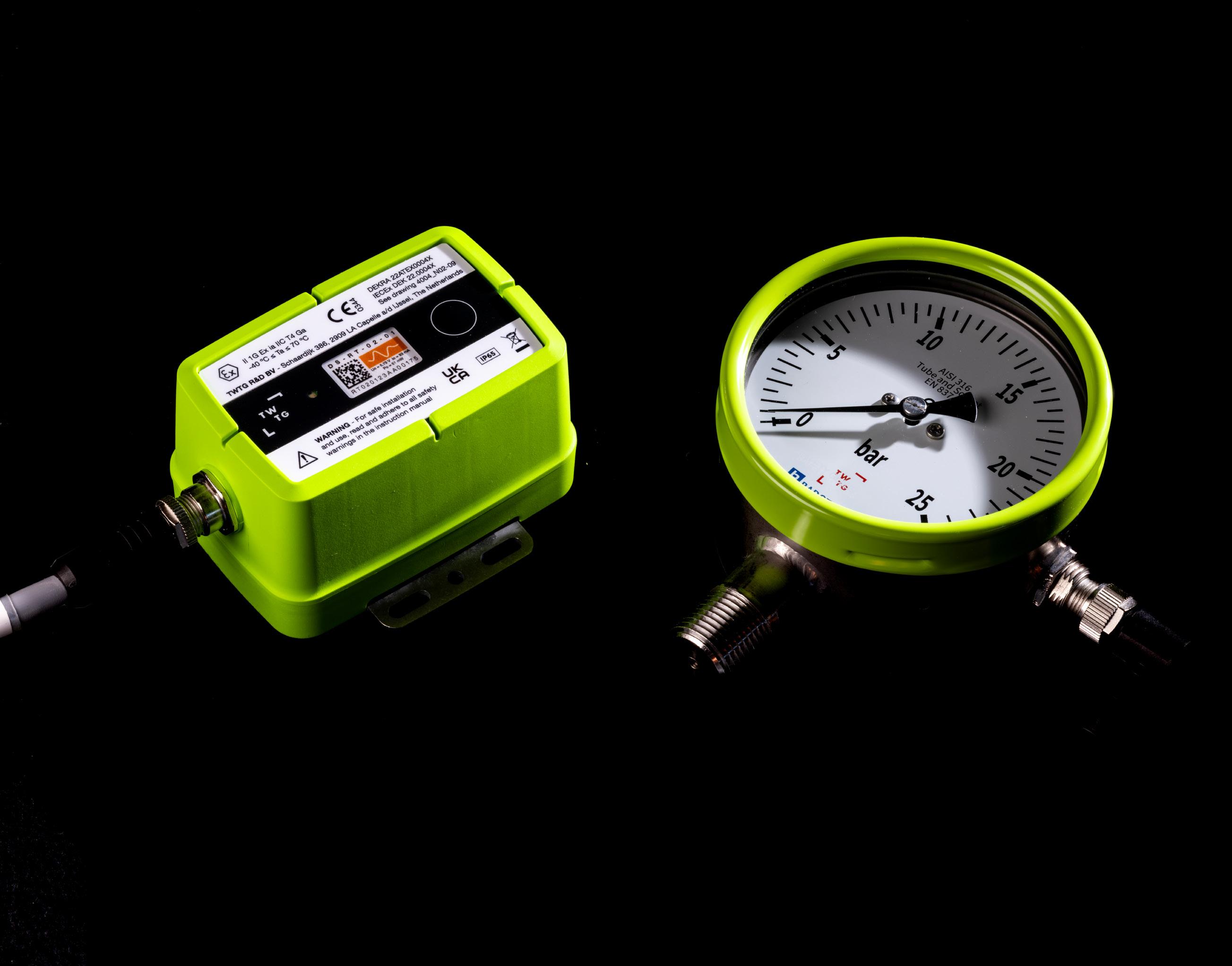