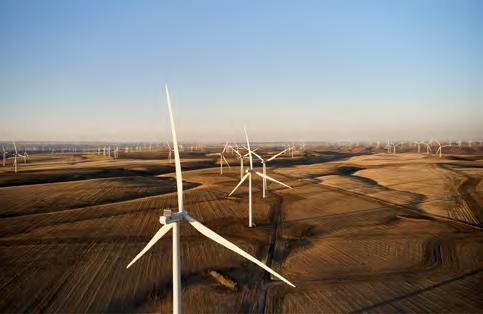
9 minute read
TRENDING GLOBALLY
Trending GL BALLY
Apple calls on global supply chain to decarbonize by 2030
Advertisement
Apple recently called on its global supply chain to take new steps to address their greenhouse gas emissions and take a comprehensive approach to decarbonization. The company will evaluate the work of its major manufacturing partners to decarbonize their Apple-related operations — including running on 100% renewable electricity — and will track yearly progress. Apple has been carbon neutral for its global corporate operations since 2020, and is laser-focused on its ambitious goal to become carbon neutral across its entire global supply chain and the life cycle of every product.
As the impacts of climate change are increasingly felt around the world, Apple also announced new initiatives and investments aimed at helping decarbonize the global economy and promote innovative climate solutions for communities. These include significant investments in renewable energy in Europe, partnerships to support businesses transitioning to clean energy, and new support for projects that advance natural carbon removal and community-driven climate solutions around the world.
“Fighting climate change remains one of Apple’s most urgent priorities, and moments like this put action to those words,” said Tim Cook, Apple’s CEO. “We’re looking forward to continued partnership with our suppliers to make Apple’s supply chain carbon neutral by 2030. Climate action at Apple doesn’t stop at our doors, and in this work, we’re determined to be a ripple in the pond that creates a bigger change.”
Mobilizing Supply Chain Climate Action
As part of Apple’s supplier engagement, the company is partnering with its worldwide supply chain to urge accelerated action to achieve carbon neutrality for their Apple-related corporate operations. The company requires reporting on progress toward these goals — specifically Scope 1 and Scope 2 emissions reductions related to Apple production — and will track and audit annual progress. Apple will partner with suppliers that are working with urgency and making measurable progress toward decarbonization.
Additionally, Apple is encouraging suppliers to address the greenhouse gas emissions beyond their Apple production, prioritizing clean energy. As part of the company’s work to achieve its 2030 goal, Apple has reduced its emissions by 40% since 2015, largely through improvements in energy efficiency, low-carbon design, becoming carbon neutral for corporate operations, and transitioning its supply chain to renewable electricity.
More than 200 suppliers representing more than 70% of Apple’s direct manufacturing spend have already committed to using clean power like wind or solar for all Apple production. To help suppliers meet their commitments and go even further, Apple offers a suite of free e-learning resources and live trainings through its Clean Energy Program and works closely with its suppliers and local partners to identify effective solutions for renewable energy and carbon removal. More than 150 supplier representatives have participated in live trainings this year alone. Apple plans to donate these resources to create a firstof-its-kind public training platform that is free for businesses across many different industries, ensuring that companies of all sizes — in Apple’s supply chain and beyond — will have access to the resources and advocacy networks needed to speed their transition to 100% clean energy and carbon neutrality.
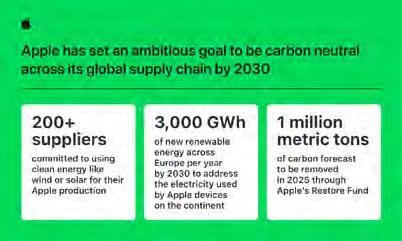
Four Ways Chief Supply Chain Officers Can Respond to Inflation
As inflation rates rise in economies around the world, there are four ways chief supply chain officers (CSCOs) can prepare their leadership response over the next months, according to Gartner, Inc. “While CSCOs primarily focus on developing strategy and enabling organizational capabilities, the economic headwinds they experience these days call for a steadying influence amid reactive stakeholder tendencies, such as defunding strategic investments and slashing overhead costs,” said Paul Lord, Senior Director Analyst, Gartner Supply Chain practice.
Position Flawless Execution as Supply Chain’s
Primary Mission: Most supply chain organizations have already developed plans for improving efficiency to offset a normal inflation rate. CSCOs should encourage their teams to implement these plans while remaining focused on their critical role in fulfilling demand to capture margin. “Uncertain times require steady leadership from the CSCO, particularly to operating functions that are critical for ensuring product availability and service delivery, such as logistics and customer service,” Lord said. Let the Planning Team Rise to the Challenge: An economically difficult situation is a good opportunity for CSCOs to evaluate and develop their planning teams’ capabilities and processes. For example, higher interest rates and material prices should prompt reductions in production batch sizes, where possible, to rebalance capacity and working capital economics. Manage Cost Reduction Carefully: Most supply chains already operate with very little overhead costs. However, periodic checking demonstrates due diligence to the C-Suite. Another way to reduce costs and further improve efficiency is role consolidation. CSCOs can, for example, consolidate functions such as site quality, safety, environmental compliance maintenance and continuous improvement into fewer teams with improved focus and alignment. “It’s important to focus on maximizing the ability of the supply chain to control inventory and optimize the cost of product supply,” Lord said. “The anxiety and fear created by unfocused overhead scrutiny during these times creates the risk of distraction from the primary mission of operating effectively to fulfill demand and serve customers.” Protect Investment Spending: One learning from the last period of economic downturn was that growth leaders reintroduced capital expenditure after a recession much faster than their peers. That’s why CSCOs should be protective about their planned technology investments to not fall behind their competitors. According to the Gartner survey, manufacturers and retailers are most protective of spending on product innovation, talent development and technology investment for price analytics and operations automation. Service-centric companies are most protective of technology investments such as back-office automation and operational visibility for increased efficiency. PepsiCo UK has recently announced a £14mn investment in new sustainable food packaging innovations that will remove 250 tonnes of virgin plastic from its supply chain annually. The outer plastic packaging on millions of Walkers 22 and 24 bag multipacks will be replaced with a new cardboard design which reduces the amount of virgin plastic the company uses.
“We are constantly exploring new scalable solutions and this investment marks an important step forward, delivering a huge reduction in virgin plastic across some of our best-selling ranges, while also helping to tackle our carbon footprint,” says Simon Devaney, Sustainable Packaging Director, PepsiCo UK & Ireland. “Reducing virgin plastic across our supply chain is a key part of our commitment to creating a world where packaging never becomes waste.”
After a successful trial with Tesco, the new and improved multipack outer packaging will be on-shelves in all major supermarkets in the UK in the coming weeks.
Alongside the new packaging design, PepsiCo has also invested in a new stretch film to wrap around its pallets before these are distributed to retailers. This new film is produced using nanotechnology which puts tiny air bubbles into the film to reduce the amount of plastic used, while retaining the same strength and stretch needed to protect the crisps as they travel to stores across the country.
According to the company, the use of this new technology will lead to a 40% reduction in virgin plastic year on year, compared to the previous film. Reducing the amount of fossil-fuel based virgin plastic in the shrink wrap will also reduce the company’s annual carbon emissions by 465 tonnes. The investment marks a major step towards PepsiCo’s goal of eliminating virgin fossilbased plastic from its crisp and snack bags across Europe by 2030.
PepsiCo UK invests in sustainable food packaging innovations
Mars, Incorporated announces major packaging innovation for KIND® bars
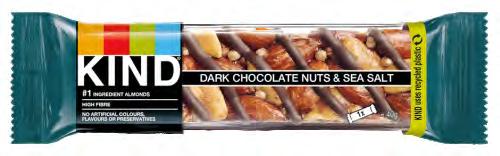
Mars, Incorporated has reached a key milestone in its commitment to a circular economy where packaging material never becomes waste. The new KIND® snack bar packaging incorporates recycled content made from advanced recycling, meaning it contains less virgin plastic to previous products. The new material has been completely redesigned for maximum circularity and is produced through the recycling of used mixed plastic that would otherwise be destined for incineration or landfill. This means that the new packaging is eligible for dropoff recycling in the UK, and curbside recycling in Ireland.
This transition to packaging designed for maximum circularity is the latest innovation in Mars, Incorporated’s
strategy to reimagine and redesign all packaging. Mars is focused on reducing the use of new virgin plastic by 25%, incorporating 30% recycled content into plastic packaging, and redesigning more than 12,000 packaging components across a diverse portfolio to fit with the recycling infrastructure that either exists today or is likely to exist in the future.
Barry Parkin, Chief Procurement & Sustainability Officer, Mars, Incorporated commented, “At Mars, we want to contribute to a circular economy where packaging material never becomes waste, but is recycled, reused or composted. For this to happen, we need new solutions and infrastructure to change the recycling landscape and to complement mechanical recycling. Today marks another important step in accelerating our sustainable packaging journey and in our collaboration with partners like SABIC that are enabling new opportunities to provide consumers with packaging designed for circularity.”
The project is a unique ‘closed loop’ collaboration, designed in partnership with SABIC®, Landbell®, Plastic Energy®, Taghleef®, and SIT®. Together, the partnership has created a lighter weight wrapper from recyclable monomaterial polypropylene for KIND®, removing the need to use complex laminated plastic incorporating multi-material layers.
Lada Kurelec, General Manager PP, PET, PS, PVC, PU & Elastomers Business for Petrochemicals at SABIC commented, “We are very excited about this pioneering closed-loop project that demonstrates the feasibility and speed of implementing circular plastic innovations when leading actors from across the entire value chain are closely collaborating. Used flexible packaging has a high feedstock value for new materials, and our TRUCIRCLE polymers and services form an instrumental element in tapping this vast potential.”
This innovation marks a real development in the potential for flexible plastic wrappers to become fully circular, as increased amounts of recycled content become available through investment in advanced recycling infrastructure.
STERIMED launches sustainable substrate for rigid packaging
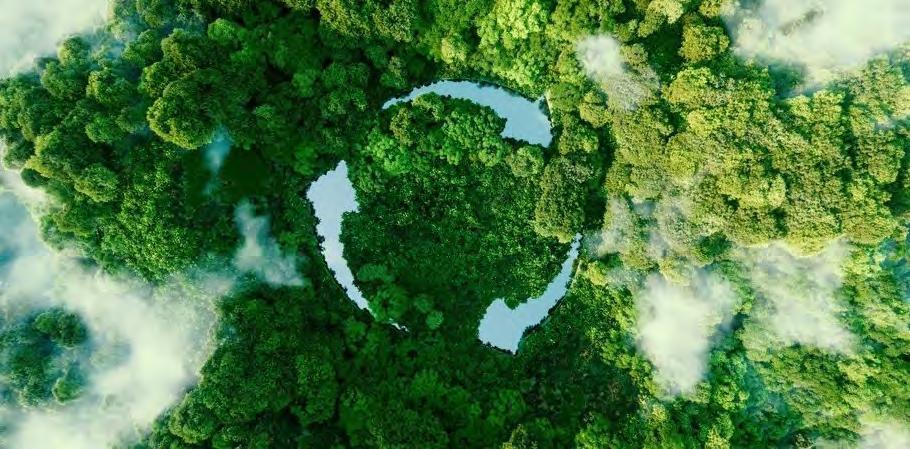
Polybond CGP 85 adds to a successful polymer-reinforced cellulose-based product range for the healthcare industry – Polybond. Medical device manufacturers, healthcare professionals and end-users are increasingly calling for environmentally friendly, sustainable products and packaging with less plastic content and a lower impact on the environment.
Sterimed has taken up the challenge and is introducing to the market renewable materials and intelligent rigid packaging solutions of tomorrow.
Polybond CGP is mostly composed of materials from renewable resources and bio sourced carbon – and contains 70% less plastic. The innovation lies in its unique fibre mesh structure, which mixes cellulose together with a high content level of synthetic binders. Synthetic binders are used for optimal mechanical characteristic and cellulose contributes to breathability and efficient sterilisation process, bringing Polybond CGP closer to polyolefin plastic material capabilities. This can help reduce your plastic footprint and contribute to reducing plastic waste on the planet.
STERIMED’s 5gsm grid-pattern coating allows excellent sealing performance. The optimal sealing integrity is balanced with an aseptic presentation, not admitting any compromises even at the most challenging opening conditions (180 ̊ peel open angle). The substrate facilitates superior performance in regard with the prevention of the risk of break, puncture & burst.
The choice of a water-based, solvent-free coating technology, in addition to a share of a renewable raw material, makes it an environmentally friendly solution. Even though the substrate does not rely on plastic, it is strong and safe in standard mechanical tests. As a result, the material is recommended to all rigid packaging applications.
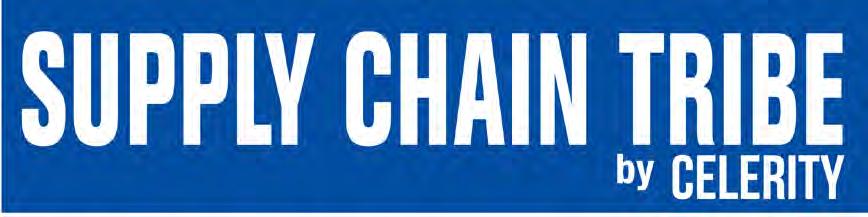
Celerity India Marketing Services Email: tech@celerityin.com | Mobile: 79771 05913 Website: www.supplychaintribe.com www.supplychaintribe.events www.supplychaintribe.jobs