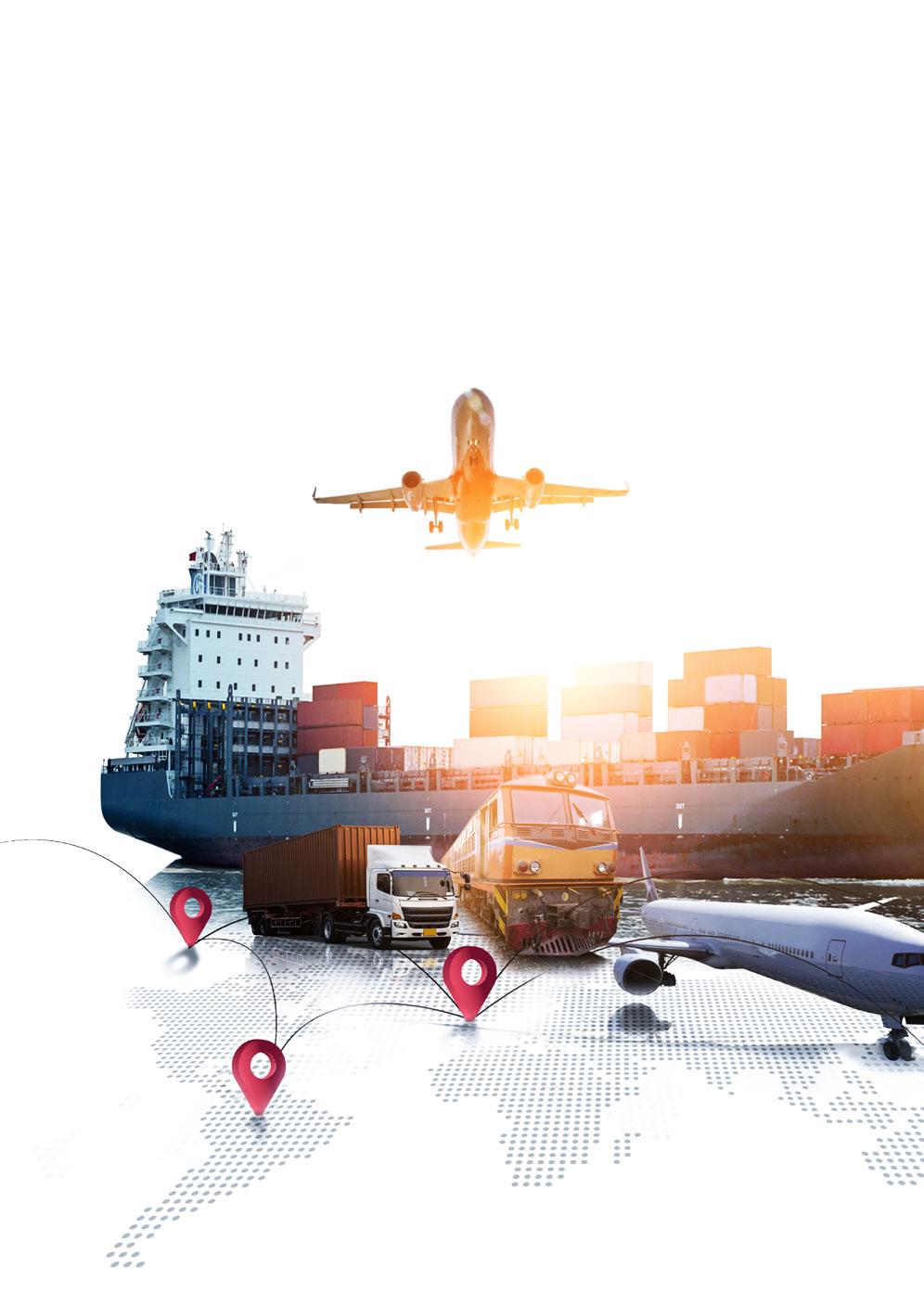
31 minute read
Drama, Disruption, and Daring to Defy Making of a RESILIENT SUPPLY CHAIN
Over the past few years, there have been more and more disruptions, from natural catastrophes to trade conflicts to pandemics around the world. Due to these interruptions, supply chains are now more vulnerable than ever, emphasizing the need for proactive actions to increase resilience. To cope with complexity and uncertainty, resilient planning is the need of the hour. Organizations need to take a comprehensive strategy if they want to detect potential hazards, diversify their sources of supply, and create backup plans. Adopting digital technologies like blockchain, predictive analytics, and real-time tracking systems can increase visibility and enable proactive risk management. This was the basic tenet of our panel discussion on the sidelines of our recently held Supply Chain Tribe Awards where the industry leaders deep dived into smart & sustainable ways to make their supply chains resilient and explored the enabling role of technology in achieving the same. Here’s presenting the stimulating strategies of supply chain leaders of leading organizations…
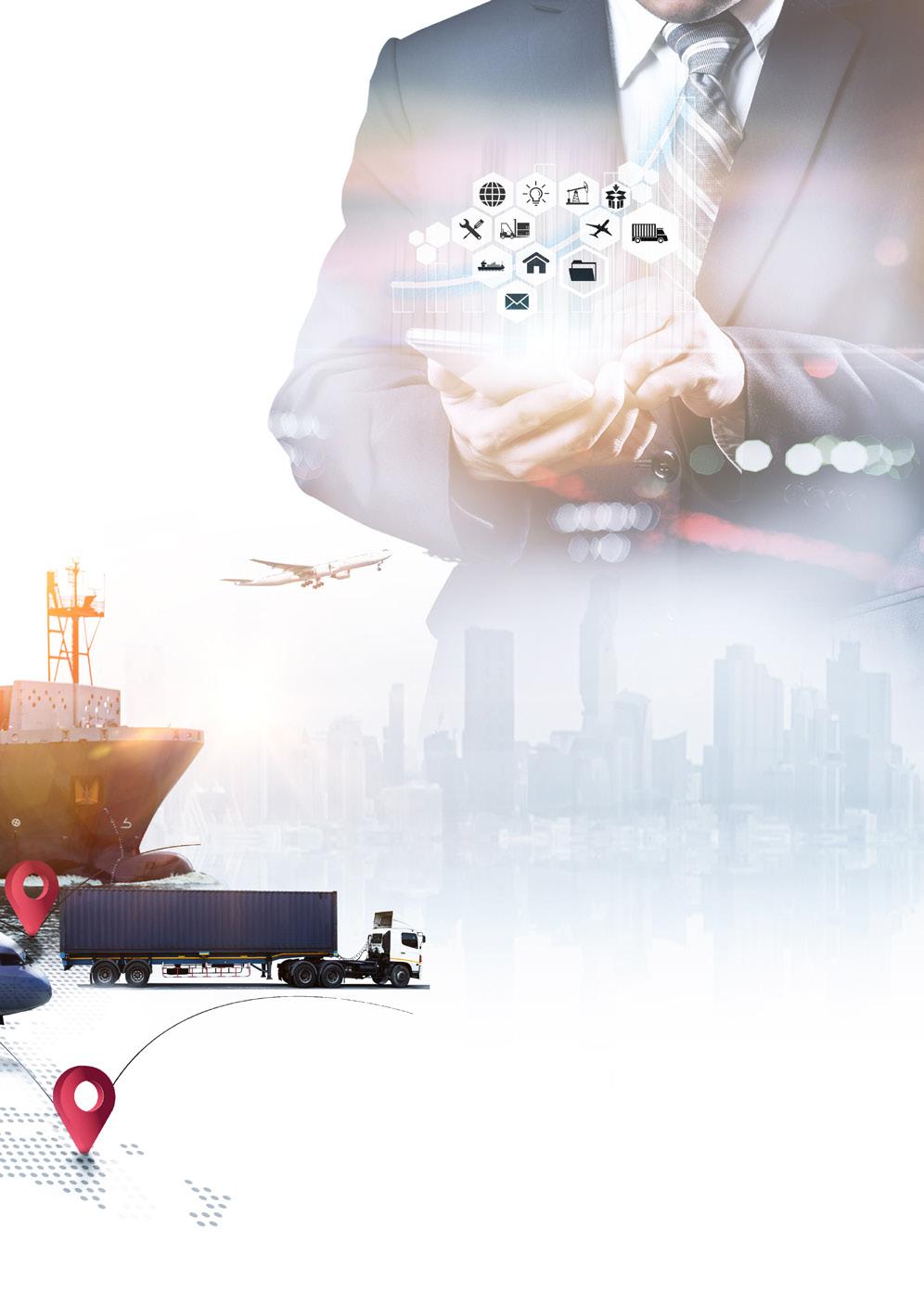
Advertisement
SUPPLY chain resilience, among other current buzzwords including economic diversification and de-risking, has become the key discussion agenda across global forums, be it World Economic Forum, G20 Summit, or any other bilateral event such as the G7 communique or the recent Indo-US joint statement. Global leaders have been echoing their voices on making their supply chains more resilient, efficient, and transparent.
In fact, at a recent press conference in Gandhinagar, US Treasury Secretary Janet Yellen praised India’s significance as an indispensable partner in the strategy of “friendshoring” to bolster supply chain resilience. “Friendshoring is an important foundation of our approach to increasing resilience of our supply chains, and we see India as an indispensable partner in that and I hope to use this trip to deepen what is already a significant relationship with respect to friendshoring that the US and India have,” said Yellen.
Such has been the testament of the country’s strong stance in achieving and enabling a resilient global supply chain. This statement also underscores the crucial importance of ensuing supply chain resilience in every industry vertical to sustain the growth momentum.
A recent Euromonitor report has aptly emphasized on this very notion that the increased economic uncertainty, rising geopolitical tensions, the need to improve operational efficiency and still prevalent transportation bottlenecks drive the need to improve supply chain resilience to better withstand future shocks. “Unsurprisingly, building supply chain resilience has become one of the top priorities for companies. Over 56% of companies globally indicated that they plan to invest more in supply chain resilience,” according to the Euromonitor International Sustainability Survey 2023. Industries with long supply chains, such as packaging, as well as industries highly reliant on efficient transportation networks, such as apparel or retail, are driving this trend. Apple is one of the key examples, as it builds new production capacity in India to diversify supply risks.
“Companies in the services sector are also aiming to better shield their business activities from future disruptions. Approximately half of companies in the leisure, foodservice and travel sectors are planning to improve their own supply chain resilience. For example, hotel chain Hilton plans to utilize double sourcing from SME suppliers by 2030 as part of its sourcing and procurement strategy. More diverse supplier networks will also contribute to lower sourcing risks and add greater operational flexibility,” the report mentioned.
“Supply chain management has become a crucial strategic component for organizations across industries in today's connected and globalized world. The COVID-19 pandemic has brought attention to the significance of effective and resilient supply chains, underlining the requirement for cutting-edge methods and sturdy frameworks,” states Naga Sundar Kumar P, Digital Business Consultant, Great Lakes Institute of Management.
To build resilience in future supply chains, companies are implementing strategies such as production globalization and regionalization of supply chains, while also aiming to create alternative transportation networks. Such actions are expected to help diversify supply chains, reduce production risks and improve operational flexibility. Besides these, in order to create resilient supply networks for a sustainable and prosperous future, Naga Sundar Kumar P identifies critical building blocks. These are:
Collaboration and Transparency: Encouraging trust and openness among all stakeholders is essential to the development of resilient supply chains. A cohesive environment where information and insights can be shared easily is made possible by collaboration with suppliers, partners, and customers. When disruptions occur, improved transparency ensures visibility throughout the whole
Nitin Kathuria, EVP & Head Supply Chain, Marico
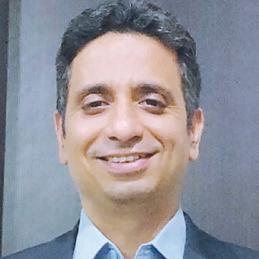
supply chain, enabling swift response and wise decision-making. Organizations should also actively engage in ethical and sustainable supply chain operations through responsible sourcing practices.
Harnessing Data and Analytics:
Data is the lifeblood of supply chain management, and organizations must use advanced analytics to promote reasoned judgement. Organizations may learn a lot about customer preferences, inventory management, and demand patterns by gathering, analyzing, and interpreting data from numerous supply chain touch-points. Lead times are shortened, supply chain risks are reduced, and proactive planning is made possible by predictive analytics. Operations may be further optimized, disruptions can be predicted, and routine jobs can be automated using artificial intelligence and machine learning techniques.
Building Flexibility and Adaptability:
For resilient supply chains, flexibility is a key characteristic. Organizations need to be ready to adjust to shifting consumer expectations, shifting market dynamics, and unforeseen disruptions. Organizations can react quickly to changes in demand and supply thanks to agile manufacturing techniques, just-in-time inventory management, and dynamic sourcing techniques. Rapid prototyping and customization
Piyush Agarwal, Vice President - Supply Chain, Pepperfry
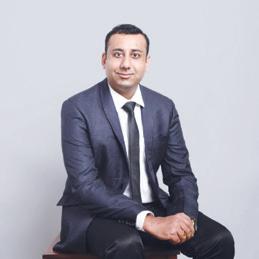
We have to look at all the parts of the supply chain in entirety, be it sourcing, manufacturing, inventory planning or distribution. All these steps have to factor in resiliency as the basic tenet, otherwise the overall supply chain will not be resilient. For us at Pepperfry, the last mile connectivity is the critical piece. If it’s broken, the supply chain will be impacted in a big way. Covid-19 pandemic has brought in a great shift in the way we take decisions. Earlier the asset-light model was the dominant model, but now Capex investment is also one of the pillars on which supply chain is based. We have, in fact, started taking initiatives towards that. Companies should identify critical parts of the supply chain and make them robust. Firefighting will always be there, but if your supply chain is robust, the time taken to rebound will be way less as compared otherwise.
are made possible by adopting flexible manufacturing technologies such as additive manufacturing (3D printing), which also reduces dependence.
Elaborating on these and many other critical pillars, our industry leaders share their insights on developing a resilient supply chain network of the future. Read on…
Complexity in the Supply Chain Planning Process. Is there a way to control it or manage it better?
Nitin Kathuria, EVP & Head Supply Chain, Marico: If I take you a decade back to understand shift in complexity, the end consumer used to purchase a product from the nearby kirana store primarily. Today, there are multiple channels for an FMCG company to reach his end consumer – e-commerce, modern trade, traditional kirana stores, supermarkets, just to name a few. The complexity accentuates when there are customized products curated for these channels and one has to ensure it is readily available on the shelf all the time. One can gauge the intensity of complexity that an FMCG company goes through now-a-days to serve the minutest needs of consumers every time wherever they are.
When we talk about managing complexity, the first thing that we need to deal with is resistance to change. We first need to accept that this complexity is here to stay. Secondly it is about enabling the processes and design of all the systems which can support complexity management. Next most important aspect in driving this change is through technology deployment. The supply chain today has become a source of competitive advantage for a forwardlooking company and who is actually able to manage complexities far better than its counterparts. Finally, it is equally important for the supply chain teams to push back to business to quantify the impact of creating complexity and whether it makes commercial sense to do so. Unless this entire loop is completed, we will not be able to fully manage the complexities well.
How are you planning to handle the variability in demand that seems to be here to stay?
Piyush Agarwal, Vice President - Supply Chain, Pepperfry: As an e-commerce company, we need to embrace variability. There are many techniques which can be used to handle the same. It includes having temporary spaces to store seasonal inventory, work with partners who provide us higher flexibility in terms of manpower and space availability, pre-planning the peak demand operations by hiring more people at the right time. It can also involve techniques like balancing out the dispatches much better so that even with higher load you are able to manage with less manpower. In the end, it all boils down to planning it well, having a highly motivated team who is ready to execute the plan and if something fails then quickly shifting to the backup plan. Some of the advanced forecasting & demand sensing technologies do help us when it comes to planning it well.
What is a resilient supply chain?
Please share some examples
Nitin Kathuria: When we talk about resilience, people start talking about black swan events like what happened during COVID phase. In the context of FMCG supply chain, resilience also means being agile. Agility for FMCG plays out on a day-to-day basis. To be agile, there needs
Sandeep Baxla, Sr Vice President Supply Chain, Indofil Industries
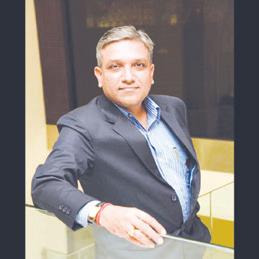
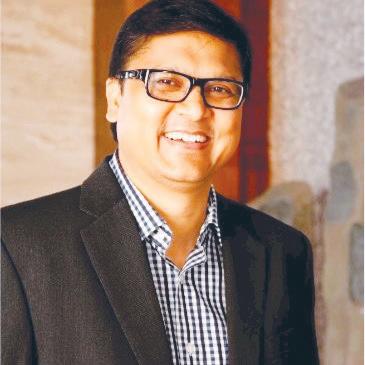
The word ‘Resilient’ has become more pronounced post Covid-19 pandemic. But I believe, as supply chain professionals, we have always been resilient. Resilience is all about firefighting and being prepared to take immediate steps in times of adverse and unforeseen situations. We have been doing that all throughout our professional lives as supply chain leaders. I think post pandemic with the extensive and frequent disruptions that we are witnessing whether they are political or geopolitical disruptions, we need to have a long-drawn strategy around resilience in order to ensure business continuity.
to be end-to-end operations visibility. Agility also corresponds to the velocity to respond to the changing scenarios. At Marico, we are investing towards raising the digital quotient across the value chain to make the organizations future ready. This is also reflected in our talent strategy and how we are imbibing new ways of working, which we believe will enable us to transform into a digitally savvy organization and win amongst evolving consumer and marketplaces. We have also made significant progress in our journey to build strong digitalled analytical capabilities to enable real-time data-led decision making. We will continue to strengthen this further for prioritized use cases such as spend effectiveness, demand sensing and social listening driven innovations, among others. We have also deployed a newly enabled forecasting system, which has increased the forecasting accuracy by over 10%. The new demand-sensing model improved the response to intra-month forecast changes, thereby lowering the possibility of stock-outs. We are pushing alerts for people to act on an immediate basis. This helps us respond to changes faster. We have also built a control tower to make our supply chain even more resilient and responsive.
Sandeep Baxla, Sr Vice President Supply Chain, Indofil Industries: The word ‘Resilient’ has become more pronounced post Covid-19 pandemic. But I believe, as supply chain professionals, we have always been resilient. Resilience is all about firefighting and being prepared to take immediate steps in times of adverse and unforeseen situations. We have been doing that all throughout our professional lives as supply chain leaders. I think post pandemic with the extensive and frequent disruptions that we are witnessing whether they are political or geopolitical disruptions, we need to have a long-drawn strategy around resilience in order to ensure business continuity.
Mohit Jauhari, Head (SCM), Shriram Pistons & Rings Ltd.
Collaboration will be the game changer for organizations to survive & thrive in the future. Companies can no longer win in isolation as data/information needs to be shared with the supply chain partners for the larger good of everyone in the chain. The concept of SME (Subject Matter Expert) will play a major role as companies try to cut down on time to market. Specialized tasks will be left to the SMEs so that the companies focus on other concurrent work to synchronize the tasks towards reducing the time to market. All this can be done seamlessly through Collaboration and the use of digital tools like AI/ML, etc. This collaborative approach, and taking timely & swift data-based decisions, will be the game changer and define the behemoths of the future.
I have seen companies joining the digitalization bandwagon in order to be resilient. I disagree with that strategy to a certain extent. I firmly believe that organizations need to start their journey towards being a resilient one by adopting a People-First strategy. In order to fully leverage a sound digitalization strategy, companies need to have the requisite resources and that can only happen when we have buy-in of our employees and an open mindset to drive the shift. Employees need to be skilled enough to drive the change. Companies must own up their mistakes in order to drive a much-needed organizational strategy.
Mohit Jauhari, Head (SCM), Shriram Pistons & Rings Ltd.: Supply chain resiliency is the ability to respond quickly to operational disruptions through flexible contingency planning and forecasting – from material sourcing to logistics and the final delivery of products and services. A resilient supply chain is defined by its capacity for resistance and recovery. That means having the capability to mitigate most supply chain disruptions and greatly limit the impact of those that occur and also regain the
Aswini Thota, Analytics and AI leader, Bose Corporation
Transparency and accountability have become essential for a good SCM function. Having transparency in SCM means leaders can precisely know the status of each step in the supply chain pipeline. A transparent supply chain function also assumes that the data retrieved is quality tested and is of the gold standard. A transparent and well-governed SCM function can help business leaders understand the pain points at any given period and help them provide timely solutions. AI algorithms are very good at analyzing historical data to identify abnormal trends.
pre-disruption status at the earliest. Companies which countered the impact of Covid-19 and rebounded to near normalcy in the shortest possible time (Apple, Alphabet, Microsoft, Accenture, Thermo Fisher, etc.) are some of the recent examples of 'Resilient Companies'.
Shifting from Leaner sequence to Digital Supply Chain Planning can help supply chains become more resilient. Can you elaborate on this with a few examples?
Mohit Jauhari: Collaboration will be the game changer for organizations to survive & thrive in the future. Companies can no longer win in isolation as data/ information needs to be shared with the supply chain partners for the larger good of everyone in the chain. The concept of SME (Subject Matter Expert) will play a major role as companies try to cut down on time to market. Specialized tasks will be left to the SMEs so that the companies focus on other concurrent work to synchronize the tasks towards reducing the time to market. All this can be done seamlessly through Collaboration and the use of digital tools like AI/ML, etc. This collaborative approach, and taking timely & swift data-based decisions, will be the game changer and define the behemoths of the future. For example, companies which used to take three plus years in design/development/launch of cars are now launching new models within one year by using the abovementioned approach.
Aswini Thota, Analytics and AI leader, Bose Corporation: Adopting Digital Transformation – the shift from a Lean Supply Chain to Digital Supply Chain Planning – can indeed bolster the resilience of supply chains. This process is akin to moving from a well-practiced manual sequence to a fully automated, data-driven operation. It offers a quantum leap in the ability to predict, adapt, and respond to changes.
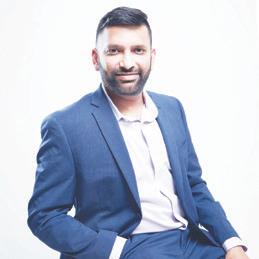
Let's look at cold-start or new product introduction forecasting as an example. This is a critical process of estimating the sales demand for completely new products. Traditionally, this task was performed using heuristics or rudimentary approximation methods, somewhat similar to a hawker guessing the potential popularity of a new item based on his past experiences.
However, in our current data-rich environment, we can do much better. We can build on sophisticated technologies like Deep Learning to understand and predict the demand for a new product before it even hits the shelves. It's like getting a glimpse into the future market trends and customer preferences, based on patterns learned from extensive historical data.
For instance, we can merge our historical sales data with additional datasets such as media spending and product features. This approach can significantly reduce forecasting errors and enable a more proactive strategy towards manufacturing and distribution. Instead of reacting to market demand, we can anticipate it. For example, imagine we're launching a new smartphone. By analyzing the sales patterns of previous models, their features, and correlating with media spending and market trends, we can get a reliable estimate of the demand for the new product. This insight allows organizations to adjust their production levels and distribution strategies, accordingly, preventing overproduction or stockouts, and ultimately, optimizing resource allocation.
Ashish Tripathi, GM & Head – Global Supply Chain, TORM A/S: Depending on the supply chain model whether it is a complex or agile, the concept of Connected Machinery can help shipping companies turn the tides in their favor. Supply chain intelligence can mitigate issues faced by the shipping industry. For instance, the Panama Canal is facing an exceptionally severe drought. Consequent restrictions have significantly reduced the volume of cargo that can be carried through the Canal. The shipping industry would be aided in dealing with such disruptions by using trusted data networks on the global supply chain – for instance, through the use of blockchain. Data points from sources such as customs authorities can be combined to chart the global supply chain. Supply chain parties can then respond to the updated information, mitigating the impact of any obstacles –such as the Panama Canal droughts.
AI can be used to optimize shipping routes, enabling shipping companies to reduce their fuel consumption and emissions, in addition to avoiding disruptions such as droughts. It may even also be possible to use AI to predict droughts, in much the same way as it is being used to predict water pollution in south-west England so as to minimize
Ashish Tripathi, GM & Head – Global Supply Chain, TORM A/S
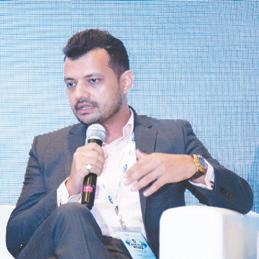
Developing a resilient supply chain is crucial for companies to navigate uncertainties, disruptions, and challenges effectively. How can companies carry out risk assessment and mapping i.e., by identifying and assessing potential risks that could impact your supply chain, such as natural disasters, geopolitical issues, economic fluctuations, or supplier vulnerabilities. Create a risk map to understand the likelihood and potential impact of each risk. Also, relying on a single supplier or sourcing location can leave your supply chain vulnerable. Diversify your supplier base and consider sourcing from multiple regions to reduce the risk of disruption. This would ensure smooth operations of the supply chain.
impact.
A major disrupter to supply chains is port congestion. High volumes of cargo can cause shipping delays and increased costs. The impact of this can be exacerbated by the sudden increase in demand for different types of cargo. Ports can use AI, particularly machine learning algorithms, to optimize schedules for vessels. Port managers can use AI to produce accurate demand forecasts and plan for rapid increases in cargo volume, while avoiding congestion and consequent delays. Similarly, AI can help to optimize cargo routes. This can reduce the number of vessels that require access to a port, reducing the demands on the ports. AI technology could be used to reroute shipments away from congested ports. Therefore, the impact of AI usage in ports could reduce delays in the wider supply chain.
TORM has been a frontrunner in digitalizing surveys and improving performance through remote monitoring. We now prepare for our inspections digitally by uploading the data before an actual inspection. Most surveys – apart from annuals, intermediates, and specials – can now be undertaken remotely and more efficiently, saving time and travel costs.
The dashboards replace the initial and annual MPMS survey on board and provides a complete breakdown of any class related maintenance already completed and overdue. Torm can access data in real-time to create a maintenance plan and can compare sister vessels to optimize performance. Recently we deployed PrimeServ Assist proactive service solution that constantly monitors and evaluates all parameters affecting engine performance. With the extensive data set and the history of the customer’s engine at hand, MAN PrimeServ service engineers sitting in Remote Operating Centres detect anomalies before potential breakdowns and advise on how to keep operations at peak efficiency. PrimeServ Assist acts in different ways to optimise machinery performance to avoid damages or downtime, including through ad-hoc notifications on engine performance (and auxiliary systems) and newly developed AI-based, advanced algorithms that predict the remaining lifetime of individual components and advise action accordingly.
What are the key pillars of supply chain resilience?
Sandeep Baxla: Vulnerability into unscheduled and unexpected events equals to supply chain disruption. How do we actually capture the associated risks and have a mitigate plan drawn around it is critical while devising resilience strategy. Another important aspect to keep in mind is our vendors. We need to establish a transparent relationship with them and empower them with the end-to-end visibility into the value chain. Supplier relationship management needs to be made robust. We need to make efforts to make planning centralized. With digitalization drives going on at a fast speed, I believe companies have already started taking this pillar seriously. We also must review our strategies on a frequent basis so that we can take corrective actions as per the changing market conditions.
What steps need to be taken so that the supply chain is able to become resilient so as to meet the ever-changing customer requirements?
Mohit Jauhari: Supply chain managers have to be good at predicting customer expectations. They should also be able to take action in advance so as to serve the customers as per their expectations. In order to do so, they need to have a seamless & real-time view of the entire chain from the customer's customer to the supplier's supplier. This can be done using the 3C Concept – Connect, Communicate & Collaborate. In essence, sharing data across the chain & using the same to collaborate & make decisions are the key to a successful Supply Chain. Companies which are willing to collaborate with their channel partners - and are also good at using data to build algorithms so as to predict/preempt customer behaviour will be the leaders in this day & age. Those who are secretive about their information and operate in siloes will find it tough to stay relevant in the ever-changing business landscape. As stated above, once the 3C State is achieved, companies will be able to leverage/mine the available endto-end data so as to predict customers’ behaviour. They will be able to optimally plan execution in sync with the projected customer behaviour. While doing so, they will also harness the benefits of optimal use of resources. Companies need to be aware of the importance of data and should have teams to make use of the available data to make decisions towards ensuring customer delight.
Piyush Agarwal: We have to look at all the parts of the supply chain in entirety, be it sourcing, manufacturing, inventory planning or distribution. All these steps have to factor in resiliency as the basic tenet, otherwise the overall supply chain will not be resilient. For us at Pepperfry, the last mile connectivity is the critical piece. If it’s broken, the supply chain will be impacted in a big way. Covid-19 pandemic has brought in a great shift in the way we take decisions. Earlier the asset-light model was the dominant model, but now Capex investment is also one of the pillars on which the supply chain is based. We have, in fact, started taking initiatives towards that. We own vehicles for transportation. We manage warehouses on our own. We need to have a fair balance on what parts of the supply chain we want to outsource and what parts we should manage on our own. When it comes to inventory, there are many models to adopt with lean being the most popular one, but it may not fit in every time. Companies should identify critical parts of the supply chain and make them robust. Firefighting will always be there, but if your supply chain is robust, the time taken to rebound will be way less as compared otherwise.
Ashish Tripathi: Developing a resilient supply chain is crucial for companies to navigate uncertainties, disruptions, and challenges effectively. How can companies carry out risk assessment and mapping i.e., by identifying and assessing potential risks that could impact your supply chain, such as natural disasters, geopolitical issues, economic fluctuations, or supplier vulnerabilities. Create a risk map to understand the likelihood and potential impact of each risk. Also, relying on a single supplier or sourcing location can leave your supply chain vulnerable. Diversify your supplier base and consider sourcing from multiple regions to reduce the risk of disruption. This would ensure smooth operations of the supply chain.
One of the most neglected areas is supplier relationship, which if done thoroughly helps in building suppliers as strong allies. This includes regularly communicating with them, sharing forecasts and plans, and work collaboratively to address potential challenges proactively.
Another aspect is leveraging technology like supply chain management software and data analytics to gain real-time visibility into your supply chain. This will enable you to identify potential bottlenecks and risks early on, allowing for more informed decisionmaking. Another roadblock in seamless supply chain operation is Inventory management. Striking the right balance between lean inventory and safety stock is essential. While lean inventory reduces costs, having some safety stock can act as a buffer during unexpected supply chain disruptions. And above all the most important bit is the employee training and development, ensuring that your
Naga Sundar Kumar P, Digital Business Consultant, Great Lakes Institute of Management
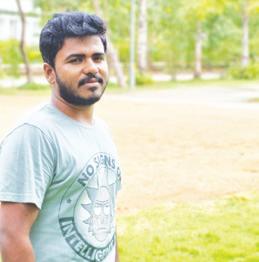
employees are well-trained in supply chain management and understand the importance of resilience. Encourage a culture of proactive problem-solving and continuous improvement.
By following these steps, companies can build a resilient supply chain that can better withstand disruptions and thrive in challenging environments. Remember that supply chain resilience is an ongoing process that requires dedication and adaptability to stay effective in an everchanging world.
Aswini Thota: We live in a digital world. From ordering food, and buying groceries, to purchasing cars, we have digital options for everything. But what if I told you that the function responsible for shipping goods and delivering products is still largely paper-based? Yes, according to the Digital Container Shipping Association (DCSA), only 0.1% of bills of lading – just one of many paperbased trade documents – are issued electronically. There are several obvious reasons businesses should digitize their supply chain operations. Some of them are:
• Delays in supply chain processes because of document errors
• Maintenance overhead
• Vulnerable to security threats
• Wastage of valuable natural resources
But the most significant opportunity lost by not digitizing service is the ability to gather data and make data-driven decisions.
Most successful companies were always innovative. They constantly try to gauge what their customers want and develop solutions that strike the right chord with them. For a company to innovate using service, all the components of its offering should work like a well-oiled machine, and the supply chain function is at the heart of this innovation.
Organizations realized a long while ago that innovation is key to success, and Covid-19 has created an environment where industry leaders must think on their feet and make fast decisions. The sudden shift in priorities caused by Covid-19 has exposed organizations that didn't have a foundational understanding of using modern technologies.
Perhaps a critical vulnerability that organizations realized after covid-19 was their lack of ability to make data-driven decisions. Enterprises that had a wellestablished data analytics practice were able to run what-if scenarios quickly and pivot to meet customer needs. Organizations that realized the value of timely information made data-driven decisions their top priority to correct these shortcomings. Data is turning out to be a key enabler for businesses, big and small. This is specifically true for supply chain functions.
Furthermore, data can significantly enhance supply chain transparency, which is critical for many reasons. For one, with increased transparency, businesses can better understand the path of goods from origin to destination, helping to ensure accountability and quality control. This level of detail can be instrumental in avoiding counterfeit items or mitigating the risks associated with unethical sourcing practices, factors that are becoming increasingly important to consumers. For instance, a luxury fashion brand could leverage data to trace the provenance of its raw materials, thus ensuring they are ethically sourced, and communicate this information to its customers. Moreover, in industries like pharmaceuticals, where the supply chain must comply with stringent regulations and standards, data transparency can help to quickly identify and resolve any potential issues, maintaining product integrity and patient safety. Real-time data can also provide early warning signs of possible supply disruptions due to a multitude of factors, such as political unrest, weather conditions, or supplier insolvency. Thus, by utilizing data, companies can proactively manage their supply chain risks and operate in a more responsible, ethical, and sustainable manner.
AI/ML/Chat CPT,
etc.,
What role do you see them playing in the near future towards transformation of Supply Chain Planning?
Piyush Agarwal: Pepperfry uses several AI and tech systems to streamline its operations and provide a better customer experience. Our recommendation engine suggests personalized products to customers based on their browsing and purchase history. The engine uses machine learning algorithms to analyze customer data and provide relevant recommendations. Chatbots provide instant customer support and assistance. The chatbots use natural language processing (NLP) to understand customer queries and provide accurate responses. Image recognition technology allows customers to search for products using images. The technology analyses the image and provides a list of products that are similar to the image. We introduced VR technology to allow customers to visualize how a product will look in their home. In addition to these systems, we intend to continue investing in AI and tech to further streamline its operations. The company plans to explore the use of predictive analytics to forecast demand and optimize inventory management. Moreover, Pepperfry aims to use AI-powered chatbots to provide more personalized customer support and improve the overall shopping experience. The company is also looking at incorporating blockchain technology to enhance the security of its supply chain and improve transparency.
In supply chain, we have designed a complex algorithm that works on a selflearning model and consistently seeks areas for further improvement. It is an optimization engine that works on pin code level and takes into consideration multiple factors including current orders in process, vehicle utilization, product volume, kilometers run per vehicle, absenteeism of manpower and frequency and type of vehicle utilized, etc. The algorithm is evolving as we continue to improve the inflection point at which timeline and SLA are in right balance. The strength of this algorithm is in operating its own logistics network, as we control end to end network, we have access to data points in all phases through which furniture travels. This vast set of data ensures accuracy in statistical modeling. Further, handling our own infrastructure also helps us achieve the lowest distribution cost and damage rates in the industry.
Aswini Thota: Every organization's supply chain deals with enormous amounts of procedural documentation. This can range from delivery orders, docking receipts, bills of landing, etc. The back-office team is expected to process and store this information. AI algorithms in computer vision and natural language processes can read through the document and translate the images to text, which can then be stored in a database for consumption.
Another popular application of AI that's penetrating every enterprise function is the chatbot. Chatbots can provide answers to the most commonly asked questions. Most consumer productcentric organizations have to answer questions about delivery requests, tracking, and order-related issues. Often, the questions your customers ask are repetitive and can be avoided by taking them on a guided search through your knowledge base that contains answers to frequently asked questions.
Forecasting may be the biggest opportunity your supply chain data can open up. Having a good forecast is critical for organizations on multiple levels. Forecasting helps organizations - procure the right amount of raw materials and parts to build the product, deliver the products to suitable warehouses on time, distribute the products to resellers, and finally meet the customer's demand. None of this is possible without having good historical data. Forecasting is not just limited to existing products in the market by combining historical sales data with related organizational data such as media spending, promotions, customer segments, etc. Organizations can develop intelligent algorithms to gauge the market share, customer interest, and product demand for new products before they are even launched.
Ashish Tripathi: AI, ML, and conversational AI like Chatbots can play a significant role in transforming supply chain planning in the near future. These technologies offer capabilities that can improve decision-making, optimize processes, enhance visibility, and drive efficiency within the supply chain. To plan for route optimization and logistics management, AI algorithms can optimize delivery routes, considering real-time traffic data and delivery constraints. This enhances the efficiency of logistics operations, reducing transportation costs and delivery lead times. Additionally, supplier risk management can be modeled with machine learning & it can assess supplier performance and identify potential risks or vulnerabilities, helping companies proactively address issues before they escalate.
Chatbots and virtual assistants can assist supply chain managers and employees in obtaining real-time information, tracking orders, and resolving issues. They can enhance communication and reduce response times. Additionally, Machine learning algorithms can analyze historical data to identify patterns and root causes of supply chain disruptions. This helps companies learn from past incidents and implement measures to prevent similar issues in the future. AI-powered planning tools can quickly assess various scenarios and their potential impact on the supply chain. This enables supply chain planners to be more agile in adapting to changing market conditions and uncertainties.
Overall, AI, ML, and conversational AI technologies have the potential to revolutionize supply chain planning by making it more data-driven, adaptive, and efficient. As these technologies continue to advance, we can expect to see a significant transformation in how companies approach supply chain planning, leading to more resilient and responsive supply chains.
Can you talk about Actionable AI & generative AI?
Aswini Thota: Actionable AI, as the name suggests, refers to artificial intelligence that is designed to produce specific, actionable outcomes based on its analysis of data. It goes beyond simply generating insights from data and provides recommendations on what to do with these insights. In the context of supply chain management, actionable AI can help identify patterns and trends, predict future outcomes, and suggest the best course of action. For example, it could analyze past and present demand data to forecast future product demand and then recommend appropriate inventory levels to prevent stock-outs or overstocking.
Generative AI has a transformative potential in demand forecasting. Its ability to generate new data instances similar to the training set enables more complex and accurate forecasting models. By simulating countless potential scenarios, generative AI can predict demand under various conditions, allowing for more robust and resilient planning. For example, it could simulate the effects of seasonal fluctuations, promotional events, or changes in market conditions on demand, enabling organizations to prepare and adapt accordingly.
On the other hand, Large Language Models (LLMs) like GPT4 can revolutionize the way supply chain functions communicate and process information. These models can understand, generate, and translate human language, which can be used to automate various tasks in the supply chain. For instance, LLMs can help automate responses to supplier inquiries, translate communication in multinational supply chains, or analyze and summarize lengthy supply chain reports. Moreover, LLMs can be trained to understand technical supply chain language and assist in tasks like inventory management by processing natural language queries about stock levels, order statuses, etc.
Both these forms of AI can transform supply chain function by enabling more informed decision-making, reducing risks, increasing efficiency, and improving overall supply chain resilience. Actionable AI can streamline decision-making processes by offering actionable insights based on real-time data, while generative AI can help businesses prepare for various scenarios by generating potential solutions in advance. Together, they can help create a more proactive, agile, and resilient supply chain capable of navigating the complex and unpredictable business landscape.
Your views on Industry 4.0 and Supply Chain 4.0 and how they can help achieve resilience?
Aswini Thota: Industry 4.0, what some people also call the Fourth Industrial Revolution, is all about how our industries are changing because of new technologies like the Internet of Things (IoT), advanced analytics, artificial intelligence (AI), robotics, and cloud computing. This is much like how a weaver's handloom got upgraded to power looms during the Industrial Revolution. The goal is to build "smart factories" where machines can chat with each other and make decisions on their own, much like a skilled craftsman, increasing our efficiency and productivity.
Similarly, we have Supply Chain 4.0. Here, we apply these advanced concepts to managing our supply chains. Technologies like IoT, AI, machine learning, and blockchain become key elements. For example, IoT devices act like the diligent postman, providing real-time tracking of goods, while AI steps in as the insightful store owner predicting what customers will need, and blockchain ensures all transactions are as transparent and safe as dealing with your trusted local shopkeeper.
When it comes to being resilient, both Industry 4.0 and Supply Chain 4.0 are like our ever-adaptable smallscale industries. They provide real-time visibility, much like the hawker's keen eye on his moving goods. With IoT sensors, companies can track shipments like never before, enabling them to take immediate action in case of delays or issues.
Additionally, advanced analytics and AI can help foresee potential disruptions and create contingency plans, much like our farmers predicting the weather for their crops. This enhances supply chain resilience and enables 'what-if' analysis and scenario planning, allowing organizations to prepare for potential challenges, be it sudden demand changes, supplier issues, or even global events. These technologies also enable automated and optimized decisionmaking, similar to how a seasoned manager would. Machine learning can analyze large amounts of data to find the best way to do things, freeing up people to focus on more strategic tasks. Technologies like blockchain can increase trust and collaboration among supply chain partners. Much like a signed and stamped agreement, it provides a secure and transparent record of transactions. This can make the supply chain more robust as partners can manage risks and disruptions together more effectively.
Ashish Tripathi: Industry 4.0 and Supply Chain 4.0 are closely related concepts that leverage advanced technologies and data-driven approaches to transform manufacturing and supply chain operations. They can play a significant role in achieving supply chain resilience by enhancing visibility, efficiency, and adaptability. Industry 4.0 refers to the fourth industrial revolution, characterized by the integration of digital technologies and the physical world. It encompasses technologies such as the Internet of Things (IoT), artificial intelligence (AI), big data analytics, cloud computing, and robotics. Industry 4.0 offers several benefits for achieving supply chain resilience:
Real-time data and visibility: IoT sensors and connected devices enable the collection of real-time data throughout the supply chain. This enhanced visibility allows companies to monitor operations, track inventory, and identify potential disruptions early on. Additionally, Predictive maintenance helps in smooth operations. IoT devices can predict equipment failures and maintenance needs, reducing unexpected downtime and disruptions in production. As companies adopt more digital technologies, cybersecurity becomes critical. Resilient Industry 4.0 strategies incorporate robust cybersecurity measures to protect against cyber threats and data breaches.
Demand forecasting has always been an issue with the degree of accuracy. Advanced analytics and AI algorithms can analyze historical data and market trends to improve demand forecasting accuracy. This ensures that supply chains are better prepared to handle fluctuations in demand.
By adopting Industry 4.0 and Supply Chain 4.0 technologies, companies can create more resilient supply chains. These technologies improve visibility, increase responsiveness, enhance datadriven decision-making, and enable more efficient and flexible operations, ultimately helping companies navigate disruptions and uncertainties with greater ease.
How do you see collaboration shaping the Supply Chain Planning Model - especially post Covid?
Ashish Tripathi: UNCTAD SecretaryGeneral Rebeca Grynspan, during a recent interview, highlighted, “Ships carry over 90% of the goods traded globally, with the percentage even higher for most developing countries, hence the urgent need to boost resilience to shocks that disrupt supply chains, fuel inflation, and affect the poorest the most. We need to learn from the current supply chain crisis and prepare better for future challenges and transitions. This includes enhancing intermodal infrastructure, fleet renewal and improving port performance and trade facilitation. And we must not delay the decarbonization of shipping.
In context to this, shipping lines have repeatedly tried to streamline their operations, but they haven’t been able to overcome the bottlenecks arising from thousands of players acting in individual slices all along the supply chain. It’s become more pressing to invest in smarter technology and logistics networks that extend beyond adding shipping capacity. We believe this environment of increased volatility is here to stay, and it will likely accelerate. This is where collaboration with partners will benefit every stakeholder.
Further to its commitments to the UN Global Compact and Sustainable Development Goal 13, TORM is pushing fast forward in our environmental efforts and will reduce carbon intensity by 40% compared to the IMO baseline by 2025instead of 2030 and zero CO2 emissions from its operating fleet by 2050. TORM integrates these goals into fleet management and investment strategies, which are in turn implemented through concrete activities designed to minimize pollution of the seas and the atmosphere. Our One TORM platform provides detailed insight into each vessel’s energy consumption patterns, enabling managers to identify and share best practices that promote fuel efficiency and quickly implement corrective actions when necessary. TORM has achieved a
37.1% reduction in Annual Efficiency Ratio (AER) compared to the IMO baseline (2008). TORM is a founding member of the ShippingLab, a collaborative effort to create Denmark’s first environmentally friendly ship through a new platform for maritime research, development, and innovation.
Steps To Achieve Optimal Resilience
Short-term solutions could work at a time when supply chains were more predictable than they are today. Preparing for long-term uncertainty and possible upheaval may encourage companies to build resilience into their supply chains. This process could evolve in stages, as highlighted in McKinsey report…
Firefighting: One potential response to supply chain problems is to focus on short-term, day-to-day actions, such as expedited delivery services to meet demand or speeding up production by purchasing components on an emergency basis. These tactics can help to some degree, particularly for identifying previously overlooked supply chain gaps. However, they don’t build resilience and aren’t fundamentally new, so overstretched suppliers may be reluctant to use them. In such cases, CEOs could consider implementing cross-silo efforts that ensure an agile response to fastmoving events. They could also exhort teams and suppliers to not only adopt appropriate short-term measures but also stay the course for the more difficult long-term reforms, which begin during the second stage.
Integrating and streamlining operations: In this stage, three actions can be critical to building resilient supply chains: creating a nerve center for the supply chain, simulating and planning for extreme disruptions, and reevaluating just-in-time strategies. Create a nerve center to consolidate organizational responses: A crossfunctional team for such a nerve center coordinates and manages proactive responses to issues that might range from caring for distressed colleagues to testing financial stability under a range of scenarios. The nerve center could be organized under four categories: people, operating cadence, decision-enabling tools, and an early-warning system, which could, for example, signal potential political developments or cyberthreats, as well as compliance or regulatory issues.
Simulate and plan for extreme supply-and-demand disruptions: This second category of actions involves ordering components earlier than usual and allowing extra time for delivery; accounting for the higher cost of energy, materials, and transportation; and checking inventories of critical materials to reprioritize production should shortages seem inevitable. If logistics disruptions are likely, try to get capacity on alternative routes. Another tactic to avoid building up excess inventory is simulating the effects of regional demand shifts on production. Examine the risks in supplier networks, labor, manufacturing, and delivery to determine if any part of the value chain is exposed to internal or external disruptions. Set up controls to minimize their effects.
Reevaluate just-in-time inventory strategies: If a crisis on the scale of the pandemic occurs, the absence of a back stock of inventory or materials can seriously threaten supply chains. Many of today’s most pressing supply shortages (semiconductors, for example) occur in supplier sub-tiers where manufacturers have little visibility. To achieve transparency beyond the first tier, companies could work to identify suppliers from spending data, N-tier mapping, or both. Prioritize them by their importance to the business and assess their vulnerability. Some potential measures to mitigate risk include finding new suppliers, redesigning networks, resetting inventory targets, keeping safety stocks, and sourcing locally or regionally.
