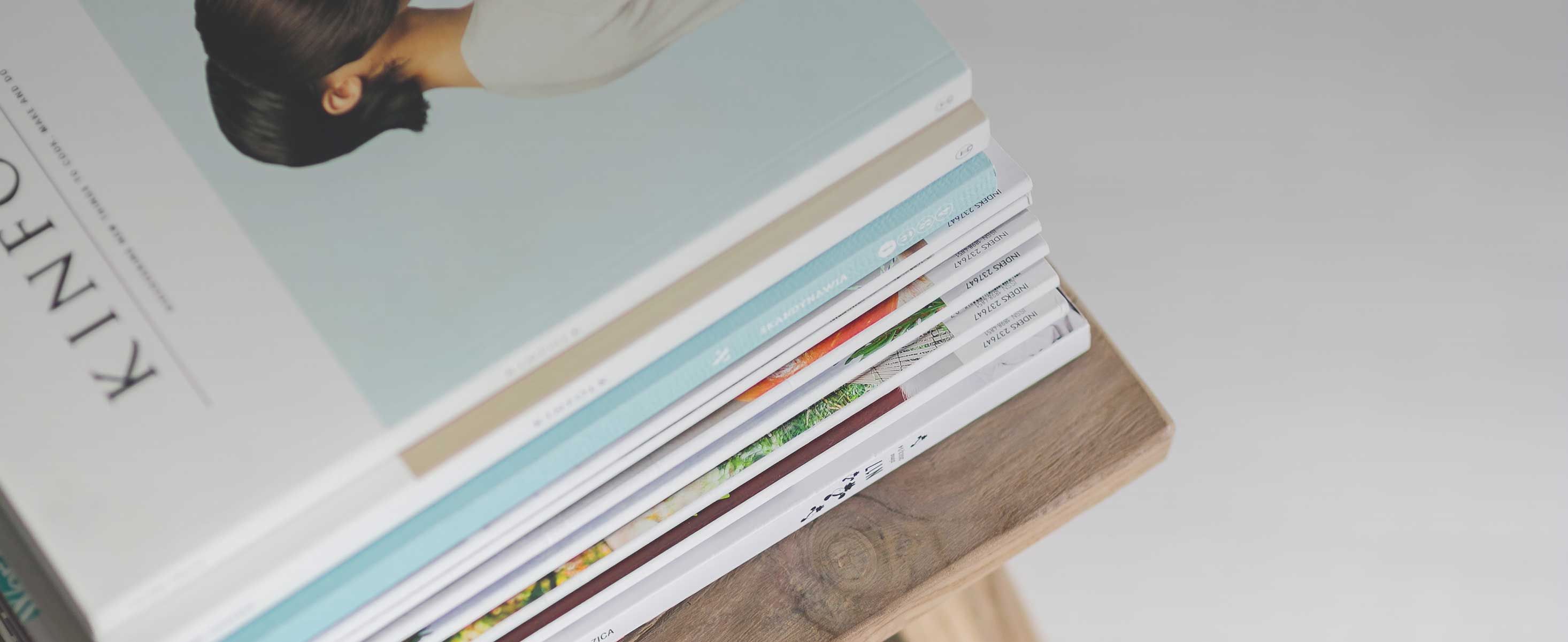
3 minute read
In with the TUNE TIMES
What are the peculiar challenges you see in managing last mile deliveries? How do you plan to mitigate them?
Till date, last mile operation is largely dependent upon untrained and unskilled resources. Our customers are well aware with the changing business dynamics and are up-to-date with advanced logistics offerings. In such scenarios, meeting up to their expectation levels is a bigger challenge for companies like us. Our emphasis has been on creating an organised & efficient way of working by skilling our workforce, which would help in meeting our clients’ delivery expectations.
Advertisement
Being in this industry for close to two decades, we have built checks and balances at every process. While on the one hand, our customers expect faster deliveries, and demand updated technology support, on the other, they want all these value-added services at reduced costs. Having said that, the highly competitive nature of the industry where we have new players entering the market every now and then, makes it more complex. Hence, last mile companies must always be on their toes as we can’t afford to commit even a minor error, which might result in a potential business loss. To mitigate such eventualities, we spend a lot of time and effort in training people and making our technology more inclusive and real-time.
How do you ensure Secure, Reliable and On-Time Delivery for your valued customers?
We have built robotic module where shipment cannot be held for more than 45-60 minutes at every last mile hub. The moment we receive a pick-up request for our customers, our backend work starts from there. Right from vehicle placement to tracking and closing of trip, the entire process is mapped in system and the processes are defined. We have evolved from a people-dependent organization to a process-reliant enterprise. In case of any anomalies, the system itself raises the flag and there is an escalation matrix, which takes care from solving the problem to ensuring that the customer is informed in a timely manner. We also use digital locks on a need basis, which is our one-of-akind solution. Moreover, we have a 24x7 control tower, which is managed by our operations team where they track & trace every delivery from start till the end.
Warehousing has witnessed a huge transformation in the recent years. Your views on the changing paradigms and what’s in store for customers?
Logicarts is a Purely Small Network company and works on Zero Inventory module. We believe in ensuring quick processing and faster deliveries to our clients. We have a robust system in place, which is equipped with advanced monitoring technologies, but our biggest strength is our people. Our people have helped us to scale up from one Hub to 60 Last Mile Hubs and we take pride in it. We see the Western world developing robotics and the same is demanded frequently by our clients, but the load factor is very different. While e-commerce companies are using robotics because of smaller shipments, our major fastmoving categories are bulk and semibulk shipments. As we grow or migrate to smaller packages, we see potential in using robots. Currently, we are using a hybrid model of Men and MHEs (material handling equipment) and automation in WMS for picking and packing.
Your insights on the shaping up technology trends in supply chain… A few years back, visibility used to be a big thing, now it has become a need of the hour. We also understand that today’s technology will become obsolete in few years, but we see a bright future in tech adoption in this so-called traditional industry. We can think of a few like:
• Warehouse formats will completely change into one giant hub (FCs) supplying many small spokes (DCs) with greater adoption of Robotics.
• Last mile depots, with the help of Big Data, will move from supply-based organization to a demand-based enterprise where forecast for the next day will be generated by a program and not ordered by an individual.
• Vehicles will be routed with turn-byturn map navigation and the traditional drivers with proprietary knowledge will be a thing of past.
• Vehicles will be locked and/or unlocked remotely.
What is Logicarts’ vision to drive supply chain efficiency in the near future?
We are having a continued track record of good growth backed by a great team of people and technology, which is ingrained in the Logicarts philosophy and culture. Our vision is to touch every city and village pin code of our great country. Our strategy is to grow organically and make Logicarts a household name.