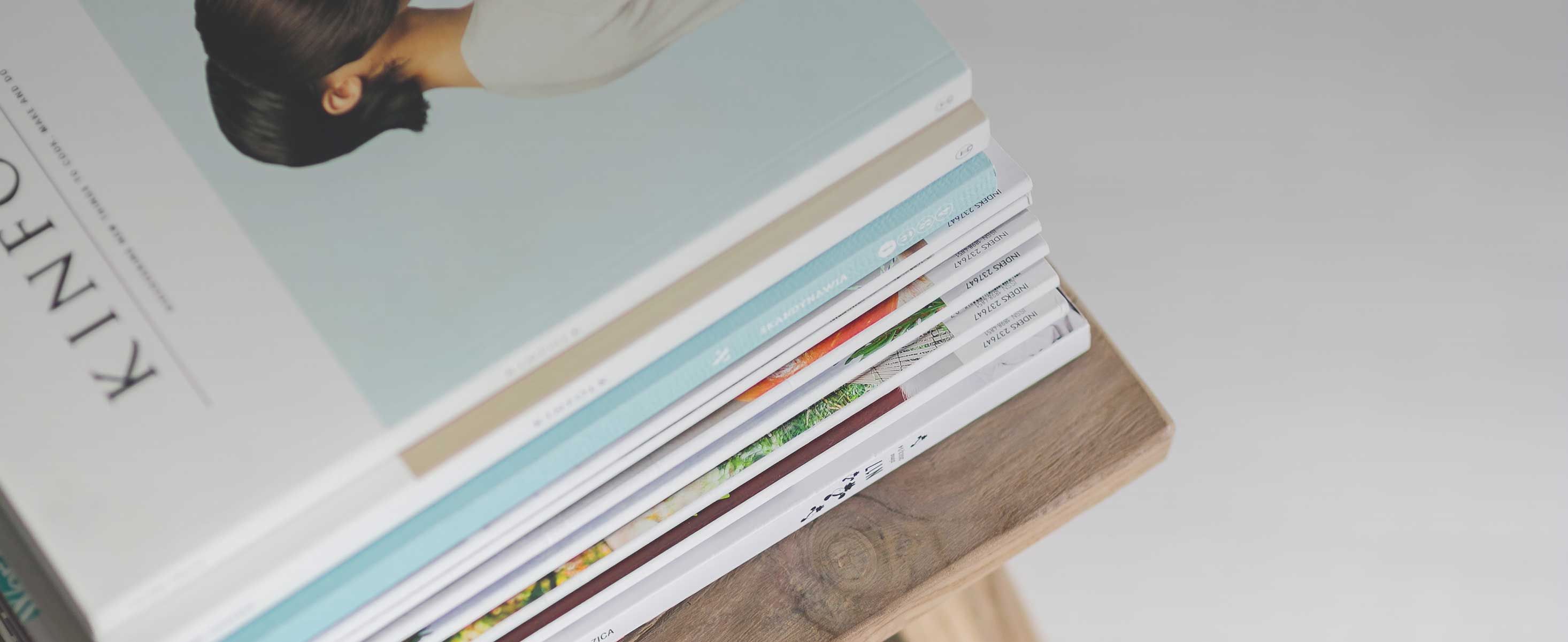
12 minute read
INDUSTRY 4.0 & DIGITAL SUPPLY CHAIN READYING FOR THE FUTURE
Manufacturing and supply chain management are in an era of transformation. The advances in technology, specifically in the context of digital transformation and industry 4.0 will change the landscape in Industry and Logistics. Global Supply Chains, including all players like vendors, manufacturers, retailers, and customers, are part of this digital transformation. That will result in new breathtaking breakthroughs in terms of productivity, delivery performance and the way supply chain ecosystems are managed. The use of these new technologies – autonomous robots, artificial intelligence, blockchain, digital twins and VR/AR to improve productivity and efficiency – will transform how manufacturing, warehouses and distribution centers operate, writes supply chain expert Dirk Stolte.
GLOBALIZATION, regionalization, insourcing, outsourcing, offshoring or nearshoring? The search for the right strategy for today’s and future supply chain management is like the quest for the holy grail in many corporations these days. The VUCA world was becoming a challenge during the last years. Supply chain disruptions triggered by crises, wars, pandemics, inflation, stagflation, trade wars, shortages of raw materials, high freight prices and shortages of skilled workers are the topics that are currently omnipresent in all companies, often termed as the New Normal to be managed when the stormy times are gone. But what is the new normal in supply chain management?
Advertisement
The answer is quite simple with a certain level of complexity. There is no "new normal" in the meaning of a newly established status quo. Rather, companies and their supply chains must be prepared for the fact that supply chain disruptions caused by economic, political, and technological change will continue to be on the agenda in the future. "Supply chain disruption is constant and impactful. Supply chain disruption is both omnipresent and unpredictable at the same time. The question you must answer is: Are we able to mitigate the next global supply chain disruption that comes our way?" Being able to deal with such shifts in the global economy including the associated risks and challenges has rather become a core competence for competitive supply chain management. Undoubtedly, this is a major challenge for all corporations, especially if they operate globally. As a consequence, existing supply chain concepts and designs need to be revaluated and redefined.
The future winning supply chain strategy requires new strengths and competencies as supply chain risk management, resilience, sustainability, and agility. But that is not enough. It's time to embrace digital supply chain management. Digital technologies such as artificial intelligence, machine learning and the Internet of Things (IoT) are changing how supply chains operate and increasing visibility, agility, and efficiency. Industry 4.0 key technologies are leading to a paradigm shift in industry and supply chain management. Digital supply chain networks and smart factories will define new standards.
Dirk Stolte is a Supply Chain & Industry 4.0 expert based in Germany. As Interim Manager and Consultant, he supports companies with focus on SCM, Operational Excellence and Industry 4.0 initiatives. With 20 years+ in Logistics & Supply Chain, he has held management roles in industry-leading companies, such as Honeywell, Federal-Mogul and Kennametal in Automotive, Metalworking and Technology businesses. Dirk holds an MBA in International Management from Liverpool John Moores University and is a certified Six Sigma Master Black Belt (ASQ®) and LEAN Master.
Digital Supply Chain Technologies Are Fundament To Design The Supply Chain Of The Future
The development from today's linear supply chain to a dynamic, networked supply chain ecosystem warrants embracing industry 4.0 and digital supply chain technologies as the fundament for the digital supply chain of the future. The power of this supply chain ecosystems comes from the fact that all improvement initiatives will focus on the entire supply chain network and delivers results (cost cutting, inventory reduction, service level) for all stakeholders and processes involved. This can be called as well as “digital supply chain network” where a digital core creates ´connectivity among traditionally unconnected links in the supply chain´ creating the linkage between the processes and activities of synchronized planning, connected customer, smart factory and dynamic fulfillment. The traditional SCOR model of plan-source-make-deliver will no longer be sufficient for the complex and interconnected supply chain of the future. In consequence, the SCOR model remains a reference model, it is, for sure, not a blueprint for the future. Digital control towers are expected to play a significant role in this future of digital supply chain management. They provide a centralized, real-time view of the supply chain and enable companies to make more informed and agile decisions.
Digital control towers can gather data from multiple sources such as suppliers, logistics providers, and transportation systems, and use advanced analytics and machine learning to provide insights into the performance of the supply chain. Overall, with digital control towers, companies can anticipate and mitigate disruptions, optimize inventory levels, improve lead times, reduce costs, and get end-to-end visibility of the supply chain.
The smart factory will feature robotrobot and human-robot interactions enabled by connected cyber-physical systems (CPS), ultimately resulting in an autonomous and self-optimized manufacturing process. By integrating the concepts, methods and technologies of Industry 4.0 and LEAN management, we can establish a new standard of operational excellence for Lean Industry 4.0. In today's interconnected and datadriven world, it is crucial for companies to collaborate and leverage digital tools to optimize their supply chains and gain a competitive edge. Digital supply chain technologies are undoubtedly the foundation of the future supply chain.
Are you interested to streamline your supply chain operations with cutting-edge technology, systems, and processes? If so, it's time to embrace digital supply chain management. The first step is to get an insight into what these mega trends and technologies are about. Which technologies should be prioritized to upgrade the supply chain operations? And when should you begin investing in them?
In order to upgrade supply chain operations towards state-of-the-art processes, businesses need to embrace the latest technologies that are most relevant to their industry and business model. It is worth noting that time is of the essence, as research from 2020 indicates that 50% of companies across various industries, including retail, manufacturing, and logistics, plan to invest in the latest technology to enhance their supply chain operations by 2023 (The Future of Supply Chain Automation - Neufeld, Dorothy, 2020).
The planned investments during this period are ranked as follows: warehouse automation (55%), predictive analytics (47%), IoT (41%), cloud logistics (25%), artificial intelligence (20%), blockchain (18%), autonomous vehicles (16%), machine learning (16%), fulfillment robots (11%), and 3D printing (10%).
It is crystal-clear that time is not on your side. Failing to invest adequately in digital technologies can put your company at a competitive disadvantage in your industry. On the other hand, it is evident that things have changed since then, and the ranking of technologies is not the same today, particularly with the emergence of artificial intelligence and digital twins. This represents a ‘Technology Investment Dilemma’ as dozens of developments in supply chain and Industry 4.0 are on the way and new ones are on the horizon. Adapting too early could also mean wasting money by investing in the wrong technology or in technology that will significantly change in maturity level in the coming years.
The ‘Technology Investment
In the near future, digital twins are likely to play an even greater role in supply chain and manufacturing. With the rise of Industry 4.0 and the Internet of Things (IoT), more and more objects and systems will be connected to the internet, generating vast amounts of data. Digital twins will be used to process and analyze this data, enabling companies to optimize operations in real-time. One area where digital twins are likely to have a significant impact is in the design and development of new products. By creating a digital twin of a product before it is physically manufactured, companies can identify potential issues and optimize the design, reducing time to market and improving quality.
Dilemma’ refers to the challenge faced by companies when deciding how and when to invest in new technologies. On one hand, companies may be eager to stay ahead of the curve and adopt new technologies early, which could give them a competitive advantage. On the other hand, investing in immature or unproven technologies could be costly and ultimately fail to deliver the expected benefits. The pace of technological change means that what may seem like a promising investment today may quickly become outdated or less effective in the near future. Therefore, companies must carefully consider the potential risks and benefits of investing in new technologies and evaluate their readiness to adopt them.
What else is on the agenda for Warehousing and Distribution Centers?
It should be noted that 55% of businesses have placed warehouse automation and upgrading distribution center operations with state-of-the-art technology as a top priority. While traditional distribution methods and processes have been considered best practices for many years, they will no longer be suitable for tomorrow’s market conditions. A survey conducted in 2022 showed that 44% of businesses believe that smart glasses are the future technology for the picking process in distribution centers and warehouses. Meanwhile, pick-by-voice technology is still relevant with 22% and smart gloves are also gaining traction with 20%. When it comes to warehousing and distribution centers, there is a particular focus on: a) automating laborintensive tasks and repetitive processes, b) autonomous mobile robots (AMR) to perform the order fulfillment, c) digital twins underlined with data analytics and artificial intelligence to improve efficiency and optimize operations. It should be noted that smart glasses, pick-by-voice technology, and smart gloves are still in the loop as also emerging solutions for the picking process in distribution centers and warehouses. It is important for companies to start planning for investments in these technologies sooner rather than later, as the market is becoming increasingly competitive and dynamic. Especially, for warehousing and distribution centers there is plenty room for maneuver by leveraging digital supply chain technologies and building tomorrow's operating models of distribution excellence.
THE RISE OF ARTIFICIAL INTELLIGENCE (AI) AND DIGITAL TWINS
The technology with most relevance for the entire supply chain is, for the time being, Artificial Intelligence (AI). Artificial intelligence (AI)-enabled supply chain management has the potential to supercharge demand forecasting, revolutionize end-to-end transparency and boost integrated business planning. 48% of companies rate Artificial Intelligence (AI) as the game changer technology with significance for the digital supply chain of the future. According to ASCM’s Research, Innovation and Strategy Committee (RISC) Sensing Subcommittee, AI and machine learning (ML) are among the 10 supply chain trends to watch out for. “They are foundational to integrating people, processes and systems in a wide array of operational environments,” the research states. “The technology-driven evolution to industry 5.0, which involves a more collaborative approach, as well as partnerships between humans and robots, will have significant impact on supply chain functions such as planning, demand management and fulfillment.” Research and analyses conducted by the consultancy industry concluded that early adaptors improve their logistics costs by 15%, inventory levels by 35% and service levels by 65%.”
Another technology all supply chain executives are supposed to have on the radar is Digital Twins. What this technology is about? Digital twins are used to simulate and optimize the performance of real-world objects and systems, enabling companies to improve efficiency, reduce costs, and enhance quality. They can be used to optimize production processes, predicting machine failures before they occur and identifying areas for improvement. They can also be used to simulate supply chain scenarios, helping companies to identify potential bottlenecks and optimize inventory levels. Combining digital twins with artificial intelligence (AI) will be the ultimate door opener for the future of supply chain planning processes.
In the near future, digital twins are likely to play an even greater role in supply chain and manufacturing. With the rise of Industry 4.0 and the Internet of Things (IoT), more and more objects and systems will be connected to the internet, generating vast amounts of data. Digital twins will be used to process and analyze this data, enabling companies to optimize operations in real-time. One area where digital twins are likely to have a significant impact is in the design and development of new products. By creating a digital twin of a product before it is physically manufactured, companies can identify potential issues and optimize the design, reducing time to market and improving quality.
Another stream where digital twins are being used to a greater extent is in supply chain risk management. By simulating different scenarios, companies can identify potential risks and develop contingency plans, reducing the impact of disruptions on the supply chain. This creates great opportunities to lever the supply chain risk management towards the next level.
Definitively, digital twins and AI are gamechangers for the supply chain and manufacturing industries.
Developing A Vision And Roadmap
What is needed here to go forward? Everything starts with the development of a vision and roadmap for industry 4.0 & digital supply chain aligned with the business objectives. Developing the vision and roadmap for Industry 4.0 and digital supply chain requires a holistic approach that considers the business objectives, organizational readiness, technology solutions, processes, change management plan and ongoing monitoring and optimization.
There are several industry 4.0 maturity models available on the market. Very powerful concepts especially for the manufacturing sector are the “Industry 4.0 Maturity Index” based on the acatach study (2017), and the “The Smart Industry Readiness Index (SIRI)” developed by the Singapore Economic Development Board (EDB).
The traditional SCOR model of plan-source-make-deliver will no longer be sufficient for the complex and interconnected supply chain of the future. Digital control towers are expected to play a significant role in this future of digital supply chain management. They provide a centralized, real-time view of the supply chain and enable companies to make more informed and agile decisions. Digital control towers can gather data from multiple sources such as suppliers, logistics providers, and transportation systems, and use advanced analytics and machine learning to provide insights into the performance of the supply chain. Overall, with digital control towers, companies can anticipate and mitigate disruptions, optimize inventory levels, improve lead times, reduce costs, and get end-to-end visibility of the supply chain.
The Industry 4.0 Maturity Index considers the four design fields of resources, information systems, organizational structure and culture and add value with the structured approach in creating systematic roadmaps with the phases: 1) Defining the scope and kickoff, 2) Status-quo analysis, 3) Roadmap development and 4) scaling and implementing. Furthermore, the Industry 4.0 Maturity Index provides six maturity levels (computerization, connectivity, visibility, transparency, predictability, adaptability), which is based on the development of an ideal industry 4.0 company.
The Smart Industry Readiness Index (SIRI) considers the three core elements of process (operations, supply chain, product lifecycle), technology (Automation, connectivity, intelligence) and organization (talent readiness, structure & management). The core elements are comprised of pillars and dimensions to be evaluated aiming to generate the Industry 4.0-readiness assessment.
A ROADMAP FOR INDUSTRY 4.0 & DIGITAL SUPPLY TYPICALLY INCLUDES THE FOLLOWING ELEMENTS:
Vision statement: A clear and concise statement that articulates the future state of the organization with Industry 4.0 and digital supply chain fully integrated into the business strategy.
Goals and Objectives: The first step in creating a roadmap for Industry 4.0 is to define clear goals and objectives that align with the overall strategy of the organization. This includes identifying specific business outcomes that the organization targets to achieve through Industry 4.0, such as reducing costs, improving efficiency, or enhancing customer experience.
Maturity Assessment: Before embarking on a digital transformation journey, it's important to assess the organization's maturity for Industry 4.0 and digital supply chain. This includes assessing the current technology infrastructure, skills and capabilities of the workforce, and the organizational culture. This is essential to identify the current state, identify gaps and areas that require improvement.
Technology Evaluation: Based on the goals and objectives and the maturity assessment, the next step is to evaluate the technology solutions that can contribute to achieve the targeted outcomes. This could include technologies such as digital twins, artificial intelligence, IoT sensors, cloud computing, and robotics.
Prioritization and Roadmap: Once the maturity assessment has been done as well as the technology solutions have been identified, the next step is to prioritize them based on their impact and feasibility. A roadmap is then developed that outlines the sequence of initiatives and their timelines. The roadmap in best way is a comprehensive plan addressing all the relevant elements means technology, people, processes and organizational culture.
Change Management: Implementing Industry 4.0 requires a significant cultural shift in the organization. A change management plan is developed to ensure that the workforce is prepared for the changes and is able to adapt to the new ways of working.
Governance and Stakeholder Management: A governance and stakeholder management plan is developed to ensure that the initiatives are aligned with the overall strategy of the organization and that all stakeholders are engaged and informed throughout the process. This includes identifying roles and responsibilities, establishing communication protocols and creating a feedback loop to incorporate feedback from stakeholders.
Regardless of which technology, trend or roadmap will be most influential in the coming years, technology adoption and organizational development will upgrade the business to stay ahead of curve. To stay competitive in today’s rapidly evolving business landscape, companies need to embrace digital supply chain management. Are you ready to take your supply chain operations to the next level?