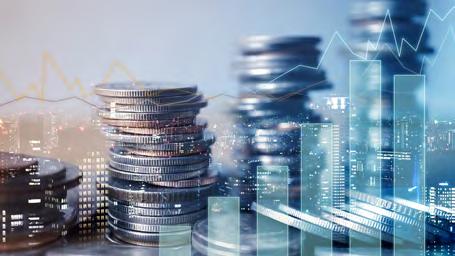
19 minute read
FOCUS
Finance and Supply Chains THE PERFECT MATCH
The importance of supply chains has been highlighted by the COVID-19 pandemic. Considerable media attention was paid to supply chain disruptions from delays at key ports, shortages of semiconductors, energy supply issues and increasing costs. Supply chains became topical. There are several areas where finance and supply chain teams can benefit from working together, which focus on a strong business partnering relationship. One of the key tenets of the function is to be more collaborative across the entity, reflecting the fact that increasingly finance teams are looking to both financial and non-financial performance measures. Clive Webb, Head – Business Management, ACCA Professional Insights Team, through this analytical piece, presents the synchrony that finance & supply chain have in common and how can they work together to bring Greater Good for companies.
Advertisement
THE pandemic has seen entities challenged by several disruptive forces from port delays to workforce shortages deliveries at all levels of the supply chains have been taking longer in certain cases. However, it should be appreciated that in many instances supply chains have proved resilient during the pandemic. Disruption is an ongoing reality, be that from natural events or from more human related activities, such as the Suez Canal incident. Manging the impact of these requires a focus on supply chain risk management and supply chain resilience. Both actions integrate across entity wide activities that include finance teams.
The longer-term impact of these disruptions, together with the macroeconomic impacts of the pandemic, are requiring entities to rethink some, or all, of their sourcing strategies. The late part of the 20th century and the early 21st century were focused on lowcost manufacturing and an increasing integration of supply chains. As some of those cost advantages are lessened, so entities are thinking about strategies such as nearshoring or moving away from just-in-time manufacturing processes, where these are possible.
CLOSING THE LOOP
“The supply chain is the lifeline of a company like [a] blood vessel [is] to the human body, and finance is the brain of a company. the healthy and effective cooperation of the two can ensure the sustainable development of company,” Stated a Finance Manager based in Mainland China. Supply chains are a fundamental part of the modern business environment. The management of these chains often presents entities with challenges and opportunities. The disruptions during the time of the pandemic have focused attention on this area. Technological advancements are changing the ways in which organizations manage their supply chains and the
Clive Webb is a qualified accountant who worked for one of the Big 4 firms. Clive's research focuses on the issues for the CFO and their team. His recent research covers the future of the finance function, the collaboration with supply chain professionals and the use of technology in business. He is the author of ACCA’s research, Learning for the Future, as well as Leading Inclusion, ACCA's review of diversity, equity and inclusion in the profession.
environmental, social and governance lens is requiring entities to develop a deeper understanding of their networks. The strong relationship between finance and supply chain teams is becoming ever more important to an entity’s success.
Below are few areas of common interest for finance and supply chains…
ROLE OF FINANCE AND THE FINANCE BUSINESS PARTNER
The role of the finance business partner is fundamental in a successful relationship between supply chains and finance functions. The finance business partner, especially those working with supply chains, needs to be fully conversant with the current risks and opportunities but also to be innovative in considering how to manage issues. The challenge is how to think of new solutions, as the problem is often not falling demand but a scarcity of resources, especially human capital, and this will define the coming few years. This
in turn has created inflationary pressures in a range of economies which further exacerbates supply chain issues.
UNDERSTANDING THE BUSINESS MODEL
One of the first fundamentals is to ensure that finance professionals fully understand the business model. The fourth Industrial Revolution and the impact of the pandemic are changing the way that entities operate. The need to adapt quickly to changing circumstances is becoming paramount if entities wish to survive. Only by understanding the business model and the supply chains can the finance professional be an effective contributor.
PRODUCT PROFITABILITY
Product profitability is a key area of collaboration between finance and supply chain teams. The pandemic has seen changes in customer behaviour, with an increased emphasis on online ordering. Small customers can be expensive to serve and have expectations of rapid delivery times. Those customers who you considered to be the most profitable might not be when full costs are considered.
The challenge of allocation can be considered by using the ‘Cost-to-Serve’ approach, which analyses the costs in a supply chain and shows how each product and customer combination involves a different series of activities and as a result has a different cost and profitability profile. Unlike Activity Based Costing, this approach is not resource intensive, and focuses on aggregate analyses of a blend of cost drivers. The approach gives an integrated view of costs at each stage of the supply chain, providing a factbased view to see through the complexity of multiple supply chains and channels to market. It enables a focus on both longterm decisions and the prioritisation of short-term actions.
There is a need for finance teams to support such approaches and to provide relevant data to make comparisons feasible. In an increasingly online consumer experience Cost-to-Serve is not only about the cost of shipment, but also the costs of managing the returns. There are variants in the approach to the calculation of the Cost-to-Serve, not least for allocation methods. The overall approach is to identify the relevant costs related to serving a customer. These may include the following categories:
Order management overheads Customer service overheads Factory planning overheads Materials planning overheads Cost of goods sold and carrying costs, including workforce costs Sourcing and procurement overheads Transportation, warehouse, and delivery costs Product returns and repair Cost of quality management.
Each of the overheads is apportioned across the product volumes. This can be a complex process and as a result several software packages have been developed that integrate with enterprise resource planning (ERP) solutions that can perform the calculation.
PAYMENT TERMS
At a time where liquidity is a key focus of entities, a closer collaboration between the respective teams is advantageous. CFOs need to recognize that lower margin products will not survive, and it is important to understand the relationship between the customer and the recoverability of the accounts receivable. There could be benefits in paying earlier, such as strengthening the relationship between the suppliers and the entity. Having an informed conversation can be beneficial. ACQUISITION OR DISPOSALS OF ENTITIES
One often-forgotten area of collaboration between the two teams was the due diligence process in the acquisition or disposal of entities, finance teams tend to perform it in isolation and what you find when you finish the transaction is that due diligence done at this high level has not really looked at the stuff that really matters operationally or day-today. The nature of the supply network should never be assumed to be static and the implications of strategic advantage via consolidation, as seen in Industry 4.0, should not be ignored. Finance professionals need to have a dialogue with their colleagues to consider these risks and how they affect strategic and detailed planning models.
ADVISING SMALLER ENTITIES
Smaller entities have distinct challenges in supply chains. As they often lack finance functions with the necessary breadth and depth of expertise, their external advisers can fill some of that void. Yet in every supply chain, there is a constituency of smaller entities. The level of understanding of the issues that they face, and how the developments in other parts of the supply chain affects them must be a cause for concern. With the growing emphasis on larger companies’ understanding of their tier II & III suppliers and beyond, there is a need to create visibility of key information throughout the networks. This enables the effective management of supply
With the increased globalization of treasury functions in large corporates, the ability to manage the cash and liquidity on a more holistic and timelier basis offered more opportunities for engagement. The advent of Logistics 4.0, with an increased capability for the capture of real-time data and the use of more predictive analytics permits a greater clarity on positions and allows the treasury team to take a more active role in managing cash positions in the light of expected funding requirements.
chain risks, at a time when sourcing strategies are being questioned by many entities, moving from single to multiple, and often geographically distributed, sources.
FINANCE AND LOGISTICS 4.0
The digital nature of the interactions between the various parties in the chains and networks is increasingly facilitating transparency at many levels of the process. Applying the techniques of Industry 4.0 can lead to efficiencies in processes and hence cost reductions. The use of smart contracts is one example of this trend, as is the use of blockchain more generally. The adoption of Industry 4.0 leads to opportunities to optimize the working capital requirements by using techniques such as supply chain financing. For some time, factoring has been used by entities to manage their debt burden. The use of supply chain finance is a more recent evolution of this. While factoring or invoice finance is used to discount the accounts receivable portfolio to achieve a more rapid payment, supply chain finance also brings into consideration the use of the credit ratings of the organisations in the supply chain into consideration.
TREASURY MANAGEMENT
Historically, there has been limited engagement between treasury functions and supply chain teams. The overall financing of the cash position was regarded as a strategic operation while the collection and payment processes were part of the finance function. With the increased globalization of treasury functions in large corporates, the ability to manage the cash and liquidity on a more holistic and timelier basis offered more opportunities for engagement. The advent of Logistics 4.0, with an increased capability for the capture of real-time data and the use of more predictive analytics permits a greater clarity on positions and allows the treasury team to take a more active role in managing cash positions in the light of expected funding requirements.
THE ESG AGENDA AND SUPPLY CHAINS
For a finance professional appreciating the activities of the entities in multiple levels of the supply chain is not just about addressing the disclosure requirements that are increasingly been required by governments and investors. This alone can be problematic as the level of appreciation of the nature of these chains, which are in reality networks, is an area that needs improvement. The ethical nature of some of the supplier interactions, such as workforce conditions, requires entities to make strategic decisions about those who they trade with.
In addition to disclosures, it is also a question to ensuring liquidity in the supply chain, especially in the face of disruption and inflationary times. Finance teams need to collaborate with supply chain teams in the application of ethical procurement policies, such as those outlined in supplier codes of conduct or in ISO 20400:2017 Sustainable Procurement. Supply chains are the focus of several the UN Sustainable Development Goals and as entities increasingly focus upon these so understanding the impact and reporting progress will become ever more important.
OPPORTUNITIES FOR COLLABORATION
Financing activities including treasury and supply chain financing are increasingly relevant as liquidity continues to be challenged. With the increased focus on vertical and horizontal integration across supply chains from Industry 4.0 either through acquisition or through collaborative structures such as joint ventures so ensuring that the agreements accommodate the impact of other entities in supply chains becomes valuable. These are just some of the areas of collaboration. Close cooperation is key to the fortune of many entities.
The similarity to the mission of the supply chain teams is clear, which is to have one integrated view of the organization based upon a common set of data. Generally, there is a lot of room for improvement in the communication between the two groups, namely the supply chain group, and the finance group, because historically the relationship is very functional. Yet, the events of 2021 and 2022 have caused further disruption to entities and their supply chains: disruption that may yet have a course to run.
‘Disruption’ is a key word of our time. The years 2020 and 2021 will go down as pivotal points of change in the way that businesses operate. Not only has the pandemic challenged many of our traditional ways of working, but so have the technological and data advances, which have in many cases been accelerated by the pandemic. The new world is one of collaboration: one in which professionals work together to address problems and execute plans. *Views expressed in the article are based on the report ‘Supply Chains: A Finance Professional’s Perspective’
In pursuit of a
BEST RUN SUPPLY CHAIN
Supply chains are pivotal to business success. However, when it comes to building a robust supply chain, only few companies are able to do it. While the task is certainly daunting, but once achieved, it can enable organizations to build resilient business models and deliver sustainable results. Shobhit Jain, Industry Leader (Retail and Wholesale Distribution) - EMEA South, SAP, offers a 10-point agenda that can help organizations in their endeavor to build a ‘Best Run Supply Chain’.
WHILE there is no denying that supply chains are the backbone of organizations, it is more important to underscore that best run supply chains lead to significant competitive advantage. These organizations outperform their peers on various metrics – Revenue growth, On Time in Full (OTIF), Time to launch new products, Cost of sales, Logistics & distribution cost and Sustainability KPIs. For example, they have upto 50% lower stock outs, 25% lesser supply chain costs and 40% fewer quality issues, which is a significant difference. They are not only efficient and reliable, but also more adaptive and resilient. So, what do these supply chains do to consistently deliver exceptional results? What is it in the DNA of these supply chains that enables this?
It certainly does not happen by chance, but through a rigorous and consistent set of actions, well enunciated in the quote by Michael Jordan, ‘Some people want it to happen, some wish it would happen, others make it happen’ THE 10-POINT AGENDA
In my view, here are the ten attributes of the best run supply chains. It is important to note that lot of these characteristics are interdependent (and in many cases synergistic) and hence being an outstanding supply chain requires excelling in most of them.
1. Completely aligned with business
objectives - They recognize that supply chain objectives need to be in sync with business objectives and priorities. This is because in the absence of this alignment, the supply chain agenda will not get required management focus and commitment, restricting its ability to deliver sustainable and long-term performance. It may also result in misaligned KPIs, with supply chain performance failing to improve business performance. Furthermore, with business dynamics changing fast, collaborating with business ensures that these supply chains can adapt much faster to the changing business reality. For example, if the business need is to deliver products with clean label (food industry), the right supplier base can be timely developed. Another example is to proactively expand distribution network in line with the envisaged business growth.
2. Collaborative mindset – The bestrun supply chains believe that having a collaborative mindset is essential for unleashing its full potential. This is demonstrated through improved inter-functional and intra-functional collaboration (within supply chain) as well as collaboration with external partners (eg: suppliers). Inter-functional collaboration calls for a deeper and frequent interaction with other functions. For example, working closely with the marketing team to reduce the time for new launch, or engaging with Finance to reduce Capex in order to
Shobhit Jain has over 19 years of experience across diverse areas covering end to end supply chain, manufacturing and operations, customer experience and engagement, Finance, and other functions. He has worked in different setups and ecosystems encompassing line leadership, consulting and business transformation, product management, sales enablement, and value realization.
achieve targeted returns. Collaboration and engagement with key suppliers can provide repository of innovative ideas which can be leveraged as a win-win proposition (eg: packaging innovation, value chain efficiency initiatives like yield improvement). Finally, they also ensure that intra-functional conflict and misaligned goals are not a hindrance to achieve its objectives. They ensure harmony amongst various supply chain teams by developing aligned goals and focusing on Total Cost of Ownership (TCO).
3. Set a rhythm through a robust
S&OP process – These supply chains drive an effective S&OP process with a well-defined objective, timelines, accountability and performance review mechanism while ensuring participation from cross functional teams (Sales, Marketing, Finance, Production etc.). They recognize the importance of a robust S&OP process in providing critical inputs (Campaigns, promotions, CRM activities or other causal factors such as sales incentives) to demand planning, supply planning and resource planning. It is also an excellent forum for cross functional collaboration, and these organizations make the most of it by effectively driving initiatives for longterm improvement. The S&OP process is typically enabled by appropriate technology / systems to make it more sustainable, reliable and effective.
4. Leverage demand data – Demand visibility is at the heart of any successful supply chain. They build a reliable and responsive supply system by ensuring availability of timely, accurate and granular downstream demand data. The extent to which downstream data is available is determined by the industry and channel. Some industries such as retail, automotive and QSR can have end consumer demand visibility. This data is critical during new launches, campaigns and promotions as well as periods of high demand volatility (eg: Covid-19), resulting in high responsiveness without causing upstream volatility and higher stock levels. Organizations that deploy good demand planning and sensing tools to capture, transmit, and use the demand data (vs. dispatch data), see significantly lower stock outs, inventory and writeoffs.
5. Supplier strategy - These companies have a well-crafted and differentiated supplier strategy. This could be based on multiple considerations like spend value, criticality of item / category to business, innovation capability or other factors relevant to the business. Based on this, they classify their suppliers (eg: Strategic, Core, Others or other variations) and develop a supplier engagement strategy. This includes how much time to invest in relationship, understanding the supplier’s ecosystem (its business and supply chain) and joint performance review. Supplier strategy may also influence the contracting approach and its tenure (eg: what method to adopt for price finalization – Cost plus, one on one negotiations, auction etc.?). Many companies do create a good supplier strategy, but they do not execute it in spirit (for example, not engaging well with strategic suppliers or just focusing on driving down cost with them). Best run supply chains do not make that mistake.
6. Upstream visibility – They focus on building upstream visibility of key material categories (based on spend value and strategic importance). This involves visibility and understanding of available capacities and key bottlenecks (critical for high growth companies), major supply risks (eg: raw material availability or financial stability of the supplier), cost structure & what causes cost volatility, and procurement and manufacturing lead time for suppliers. Upstream visibility improves responsiveness, and ensures early detection and timely response to any disruptions. It also helps in better cost management by tracking cost drivers and changes in the value chain. For companies in food service space, upstream visibility enables much better control on food safety and quality.
Demand visibility is at the heart of any successful supply chain. They build a reliable and responsive supply system by ensuring availability of timely, accurate and granular downstream demand data. The extent to which downstream data is available is determined by the industry and channel. Some industries such as retail, automotive and QSR can have end consumer demand visibility. This data is critical during new launches, campaigns and promotions as well as periods of high demand volatility (eg: Covid-19), resulting in high responsiveness without causing upstream volatility and higher stock levels. Organizations that deploy good demand planning and sensing tools to capture, transmit, and use the demand data (vs. dispatch data), see significantly lower stock-outs, inventory and write-offs.
The best-run supply chains believe that having a collaborative mindset is essential for unleashing its full potential. This is demonstrated through improved inter-functional and intra-functional collaboration (within supply chain) as well as collaboration with external partners (eg: suppliers). Interfunctional collaboration calls for a deeper and frequent interaction with other functions.
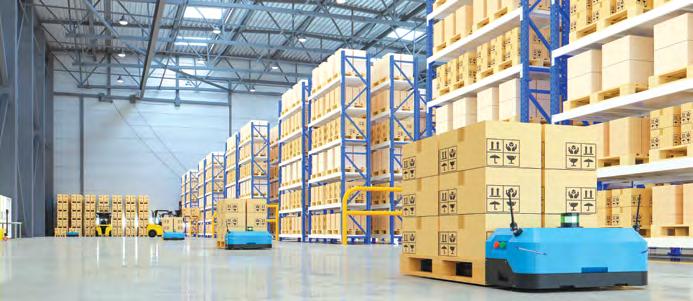
7. Investment in technology and
systems – Best run supply chains meaningfully leverage technology in alignment with overall business priorities, build longer term digitalization landscape and maintain a relentless focus on driving adoption & business benefit tracking (this is important as many times while the investment is made, the anticipated benefits are not realized. It is also important for incorporating learning in future initiatives). Technology is also a key enabler in effecting changes in operating model (eg: same day delivery). Some of the key areas of investment include demand planning & sensing systems, supplier collaboration platforms, transportation planning and execution system, control tower, manufacturing execution system, deployment of IOTs, digital twins, integrated dashboards and many others. They are capitalizing on opportunities provided by the confluence of IOTs, data analytics and AI / ML systems (eg: condition and rule based predictive maintenance of equipment). Finally, they are also open to experiment with new and emerging technologies (through POCs and pilots with a clearly defined success criteria).
8. Contingency / back-up planning
- In addition to robust processes, these businesses have effective backup and contingency plans. These plans are not charted just as a ‘formality’, but are practical and help them prepare and protect the business in case of unexpected events. This requires anticipating and envisioning various scenarios and planning responses to them. This could include supply disruptions (eg: capacity constraints or supply issues at a sole supplier), significant demand volatility (say demand is 3x of projections for a new launch), manufacturing and distribution network disruptions (eg: temporary closure of a manufacturing facility or a warehouse), cost volatility, and so on.
9. Innovation and sustainability –
These businesses challenge the status quo, and develop & implement innovative solutions. It is not always about developing a novel or disruptive idea, but also about accelerating the adoption of appropriate innovation developed by other companies. For example, deploying Blockchain based solution for enhancing visibility and reliability or early engagement with suppliers for reducing product development lead time. These supply chains also have laser sharp focus on driving sustainability initiatives which could include responsible sourcing, targeted reduction in carbon footprint & consumption of other resources, and social programs.
10. People management (It all comes
down to people) – Best run supply chains understand that while processes and systems are critical for driving high performance, consistently outstanding results hinge on people who run the supply chain. Hence, they invest in people right from selection, capability building and direction setting, and by allowing them to experiment. They ensure that people understand the vision and strategic priorities of supply chain and provide enabling ecosystem, which leads to higher focus and commitment from people leading to sustainable performance.
While building a detailed agenda for step-changing supply chain performance is the starting point, the real difference comes by driving a consistent and relentless execution on the plan.