ISOLATION ASSESSMENT & GUIDANCE
Spectrum Industrial have produced this guide with industry expert’s knowledge and experience in the methods of controlling hazardous energy. This has been collated to create a self-auditing document for safe isolation processes across varied industries. The advice of experts in the field of Lockout Tagout Tryout should be implemented on site in the form of a survey/audit, to ensure your isolation procedures and safe systems of work are of the highest standard. Helping avoid injuries and fatalities on plant.
We understand how busy many businesses are, so we wanted to create this document to allow high risk organisations the ability to follow a survey framework of what would usually be conducted by in person. The reason behind a survey is to assess risk, understand the current processes and highlight any areas of improvement on the lockout tagout procedures. Weaknesses in any area of this, could easily be magnified and result in injuries or fatalities. It is designed to be of use in any high-risk industry, from Quarries, Power Stations, Oil Rigs, Heavy Manufacturing, the Waste/Recycling sectors and more. HOWEVER, we are here to help any time, therefore please contact us for professional expertise and further advice and guidance.
This document should create a picture of what is working well on plant & what could be improved upon. Once completed, our expert teams will review and reply with a solution report including a bespoke quotation of products to fulfil the implementations. If weaknesses are discovered, the exercise is a success, as this can be the catalyst for change, meaning a safer working environment for operatives and contractors alike.
THE MOST COMMON REASONS FOR AN ISOLATION TO TAKE PLACE
• Cleaning
• Maintenance
• Repairs
• Inspections
• Decommissioning
• & More
The most common Energy Hazards & Sources to Identify (consider residual energy on all)
• Electricity
• Hydraulic Pressure
• Pneumatic Air Lines (Pressure/Steam)
• Kinetic Movement (Conveyors)
• Liquids (Fuels, chemicals, and water)
• Gases (Poisonous, suffocating & explosive)
• Gravity (Falls from height, steep conveyors, falling parts and mechanisms that work with or against gravity)
• Spring Tension
• Mechanical (Fan, belts, gears, saw blades, crushers, pressers, shredders, mobile plant)
• Thermal (Extreme temperatures)
• Nuclear
Human error accounts for a major portion of the accidents that occur, machines faults and malfunctions follow. All of which can be controlled by an effective isolation programme. The many factors involved in the process, need to be carefully considered as the breakdown and failure of any stage can prove fatal. Awareness & education around the necessities of actually implementing the procedures is still lacking in many industries, this guide is to help build the foundations of an ironclad isolation process and procedure.
However, failure to implement this is as good as having zero safe systems of work in practice. Lockout Tagout Tryout awareness courses are available by contacting spectrum-industrial.co.uk to educate on the sector and highlight the importance of practicing safe Lockout tagout every time. Here you will also find a downloadable “Total Isolation Guide & LOTOTO Best Practice Handbook”, which is widely considered as the highest standard for isolating energy hazards nationally.
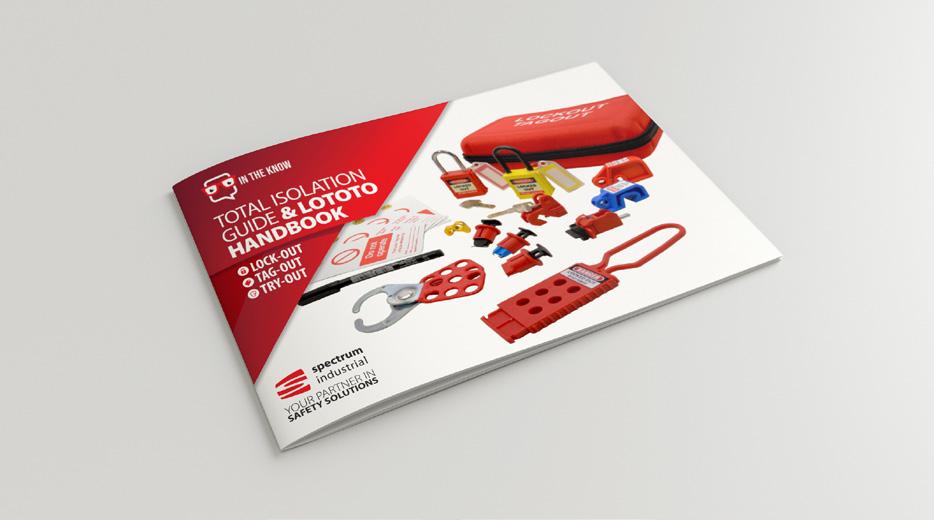
Following this audit, the aim is to have some actionable points to take away and implement accordingly. To assist in this, the team of experts are on hand to collate findings and write a solution report for you, along with a bespoke quotation of products to ultimately strengthen your safety offerings on electrical and mechanical isolation. Once completed, this can be returned to Spectrum Industrial to assist in the next steps. Including a follow up, in person site-survey.
Did you know?
• Contact with moving machinery is still in the fatal 6
• In the US it remains the 5th most common cause of incident
• The US & UK and governed by strict legal obligations and regulations to isolate safely
The regulations are covered under:
• HASAW 1974
• Electricity at work Regs 1989
• PUWER Regs 1998 – Reg 19 for isolation from Sources of Energy
• Quarry Regs 1999
• OSHA 1910.147 – Control of Hazardous Energy
This guidance covers the most commonality on energy sources and isolation points, with prompts to consider certain scenarios and thought-provoking areas which could impact how you build your process for your standard operating procedure. Please review anything you have on plant additional to this and include them in your findings. Most scenarios and questions have been covered. However, this can never be a fully comprehensive review as you would find with an expert on site. What this will give you, is a highly competent starting point, education, awareness, and will highlight areas for improvement to carry forward.
Auditing and reviewing safety procedures should be done on the regular instead of being a one off. Things can change with machinery, staff, or regulations. So, it is advised to keep on top of new developments as they arise. Isolation is not an optional activity, keep knowledge & awareness of the sector a necessity. It can save lives.
The Auditing Process
Please follow the questions and give extended explanations where necessary. The more information gathered, the better understanding everyone will have to build an appropriate, efficient isolation procedure. Ensure each piece of machinery, operative, contractor, energy source, isolation point and plant location. Are each given the same care and attention to detail when reviewing, if this means taking regular breaks or auditing over the course of a period of time, please do. The quality of information is paramount to the success and ability of the project.
Please visit spectrum-industrial.co.uk to download the LOTOTO Guidebook before commencing, this will give additional guidance to how a process could and should look with information explaining each step on controlling the unexpected start-up of stored energy.
Self-Audit Assessment
When answering these questions please consider the following 10 steps of the best practice LOTOTO (refer to the guidebook you have downloaded for explanations when progressing though this section).
DO YOU CONSISTENTLY COMPLETE EACH STEP WHEN ISOLATING MACHINERY ON PLANT?
Please Tick Yes or No
Process & Procedure
Q1: DOES EACH PIECE OF EQUIPMENT HAVE A WRITTEN PROCEDURE FOR SUCCESSFUL ISOLATION?
Q2:
Do you use a permit to work on each isolation task?
Q3: HOW DO YOU CONTROL CONTRACTOR LOCKS ON PLANT?
Do they bring their own?
Have you considered potential duplicates if so?
Think about who is responsible.
Do they know the procedural steps as your operatives do?
Q4: DOES ANYBODY EVER WORK UNDER SOMEONE ELSE LOCK?
Authorised persons task.
How does each person have guaranteed safety if so.
Q5: DO YOU MANAGE THE CONTROL KEY IN A SAFE/GROUP LOCK BOX?
Are personal locks used in group lockouts on the boxes and safes?
Q6:
Does the process and procedures get reviewed and updated when there are changes in regulations, staffing and/or machines?
Q7:
Is there an allocation in the procedure for the Tryout element to be successfully carried out?
Q8: IS EVERYONE AWARE OF THE MODE DIFFERENT MACHINES MUST BE IN TO ‘TEST’?
Out of sequence test could give a false result.
Q9: IS EVERYONE AWARE TO RETREAT TO A SAFE DISTANCE BEFORE TRYOUT IS COMPLETED?
Q10: DO YOU HAVE SEPARATE PROCEDURES AND REQUIREMENTS FOR SIMPLE VS COMPLEX ISOLATIONS?
Q11: DO YOU HAVE A HANDOVER PROCESS IN PLACE FOR NEW AUTHORISED PERSONS TAKING CONTROL OF AN EXISTING ISOLATION?
you plant labelled the points
Q2: DOES ALL MACHINERY HAVE THE ABILITY TO BE LOCKED OUT AND ISOLATED SUCCESSFULLY?
Q3:
Do you utilize personal or group/misc. locks?
Q4: CAN YOU ISOLATE ALL ENERGY SOURCES?
Q5: WHAT KEY METHOD DO YOU UTILIZE ON PLANT?
Do you utilize the 1 key per lock method?
Q8: HOW DO YOU CONTROL THE LOCKOUT STOCK ON PLANT?
plant
Q9: ARE THERE ADEQUATE VOLUMES OF CORRECT LOCKOUT EQUIPMENT AVAILABLE?
(such as gate and rotary valve covers)
Q10: DO ANY MACHINES RECEIVE THEIR ENERGY SOURCE FROM A CORD & PLUG?
many?
Are the locks and key singularly identified to employee, department and/or method of use
Q1: DO YOU HAVE AN ADEQUATE RECORDING SYSTEM FOR LOCKOUT PROCEDURES?
Q2: DO YOU HAVE A NEAR MISS RECORD?
This can include anything from an unsuccessful Tryout to actual contact with machinery
Do investigations follow accidents and are they recorded?
Q4: DO IMPROVEMENTS GET REVIEWED AND IMPLEMENTED FOLLOWING THE INVESTIGATION FINDINGS?
Q5: DOES COMPLIANCE FOR THE CONTROL OF HAZARDOUS ENERGY GET REVIEWED AND VERIFIED, IMPROVED AND KEPT ON FILE?
Q1: DO YOU HAVE A TRAINING & AWARENESS PROGRAMME IN PLACE FOR OVERALL COMPETENCY ON LOTOTO (LOCKOUT TAGOUT TRYOUT)?**
**Spectrum-Industrial have created a specific LOTOTO training course designed to raise awareness of the process, procedures and real-life risks associated. We ensure that all members understand the dangers of what can happen and how, to help avoid similar scenarios occurring again. We explain what to look out for, how to follow the processes effectively and safely. As well as making sure they are competent in applying the equipment onto their own plant set-up. Creating an individual, bespoke solution for the whole team to understand and follow as one. We cover real life scenarios, how accidents can affect you, energy hazards, sources and equipment used to isolate them. As well as explaining in depth the 10-step process and how to effectively implement this each time to an array of different procedures and standard operating systems. Its recommended that if you decide to improve your Lockout Tagout offering with equipment and updated procedures, that the LOTOTO course is conducted for everyone involved.
Do you train new employees to the same standard consistently?
Do you utilize an authorised person for each isolation task?
Q4: DO THE MEMBERS WHO CARRY OUT ISOLATIONS RECOGNISE AND CATER THEIR APPROACH ACCORDINGLY TO DIFFERENT TYPES OF ISOLATIONS?
Outlined in company/machine procedures
How can they go wrong?
How to help avoid any incidents
Questions & Answers
Have you ever had to cut a contract / staff lock off a machine?
When was the last Lockout Tagout awareness training course conducted?
Q3
How often are you company shutdowns, outages, turnarounds & how are they managed with lockout?
Please return for our LOTOTO safety experts to review, considers solutions and report back. If we have found any areas for improvement, we will make recommendations to allow and improve isolation safety on plant. We are also available following this for on-site surveys, training, and audits for other life critical safety procedures.