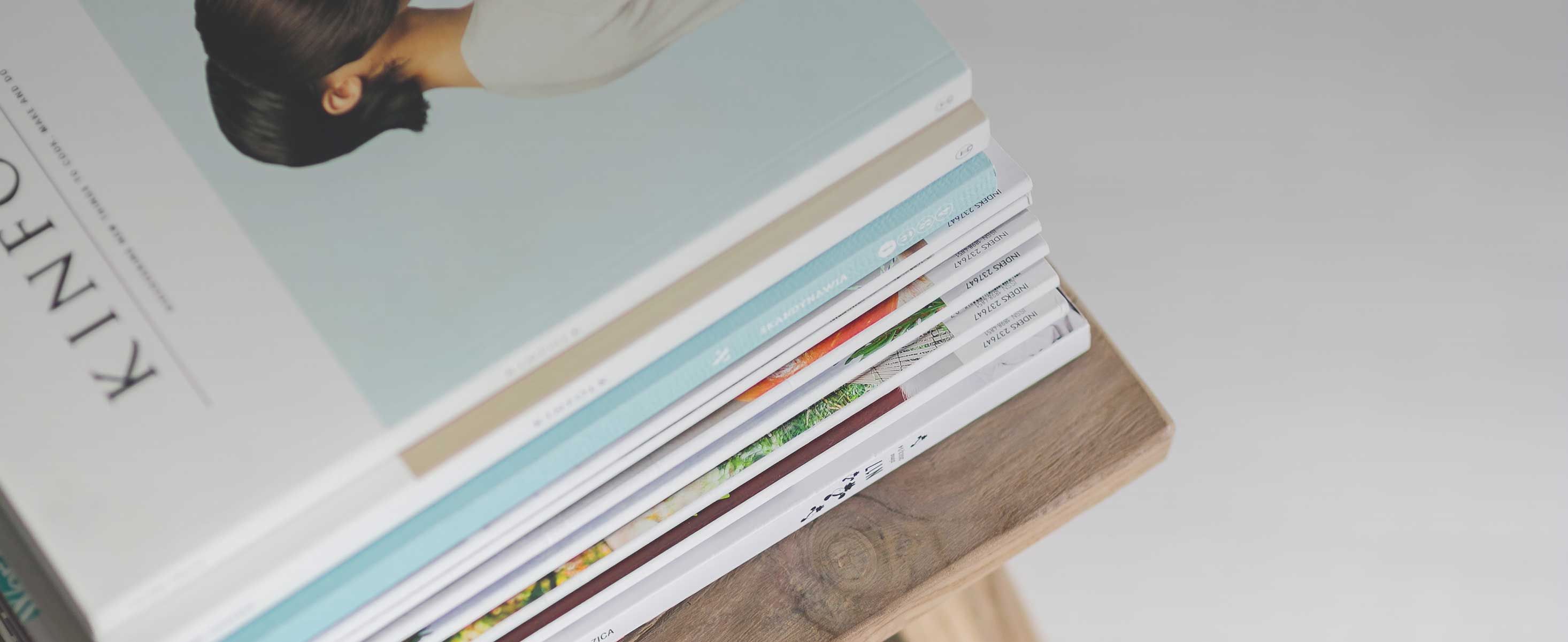
5 minute read
Why is it so hard to get new building products approved?
MIRIAM BELL
Murphy O’Neal has been trying to introduce a new way of building homes into New Zealand for more than 10 years, but he has encountered obstacles at every step of the way.
Advertisement
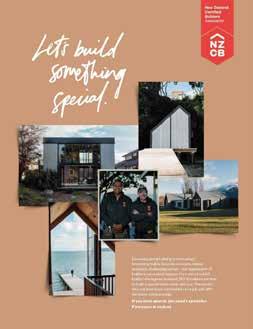
His crusade began after he migrated to Auckland from the United States, and discovered how much it cost to build houses in his new country. He was certain there was a better, more cost-effective solution.
That led O’Neal, who has a background in construction and environmental products, to develop a transportable modular building system which uses recyclable aluminium components and aerospace fasteners.
Weather-tight, seismic-proof buildings can be made with it, units can be added or removed, and traditional building techniques, including cladding systems, can be incorporated.
O’Neal says the Adaptable Structures system can be loosely described as a cross between Meccano, Lego, and Ikea, but it is fully scalable open architecture that anyone could build with simply.
The materials used are all made in New Zealand, and 99% of the materials are appraised or used in construction today, he says.
“But it is a different system of building, and we have to specify every product being used to gain consent to build from councils, so we test everything. It is costly, and time-consuming.
“Now the catch 22 – nobody gives assurance, only appraisal. Both Branz and Codemark are a system of appraisals, but they aren’t an assurance.
“That means there is little security from liability, and councils are risk averse.”
The system is not set up for innovation, and it favours large corporations doing R&D, and developing new products or importing them, he says.
“There are not many small players because the system is so controlled, and there is little engagement with, or support for, them.
“Find a small brand that is in every home that is Branz-appraised and allowed to be used. Pretty much every one is a large multinational corporation.”
O’Neal is frustrated, but is not giving up, and now has 60m² of proof of production and functionality units in the Adaptable Structures warehouse, and a committed team working on the system.
Napier businessman Baden Rawle is another small player who got fed up with the “excessive” costs involved in building a house, and decided to import prefab homes and materials from China.
It took him over five years, and nearly left him broke, but last year he obtained building consents to build steel-frame homes using prefab materials from China that meet the NZ Building Code.
The use of imported materials, and cost-savings from the construction methodology which reduces build time, cuts the cost of a typical build by about 30%, he says.
“It was a struggle to get the materials approved though. They had been approved in Australia, but I had to prove they met the Building Code requirements here.
“A council can’t deny a building consent to products that meet the code, but as the products are an ‘alternative solution’ it can require further information, and there was huge scrutiny of that information before the products were approved.”
Rawle has twice secured consents to build houses with his imported materials in Napier, and he is about to apply for consent for a build in Cromwell. With each consent, the products he used went through an assessment process again.
Getting the first consent from the Napier City
Council was a difficult process, but getting the second one was straightforward, and a similar pattern is likely with other councils, he says.
“Councils need to be diligent in this area, but the system does favour established product suppliers, like Fletchers, who have a hold on the market, especially as people don’t like change.
“But the price points of the products I’m using can’t be beat, and that is starting to get through to people, so interest is increasing.”
The difficulties in getting new building products, and processes, approved has long been recognised as an issue in the industry, but the Gib board shortage last year made it a matter of public concern.
Certified Builders chief executive Malcolm Fleming says part of the problem is that the cost of setting up a full service in a small market like New Zealand, which has some well-established suppliers in it, is not worth it for many international players.
The product quality, service, and ongoing support provided by the established manufacturers and suppliers is at a high level, he says.
“That contributes to a lot of brand loyalty, and designers, specifiers, and builders tend to be gun shy about using new products, and the leaky homes crisis also left many risk averse.
“On top of that, it takes time and money to go through Branz certification, and various approval processes. It all makes getting a foothold in the market very difficult for new players.”
The industry desperately wants to see more new, and alternative, products on the market, whether international or local, Fleming says.
“If there was recognition of a certain international certification standard for new products that could be aligned with CodeMark, it would cut back the approval process currently required, and make it easier for new entrants.”
While that is not happening, there have been some positive developments as a result of the Gib board shortage, he says.
“It led MBIE to tell all the Building Consent Authorities they had the latitude to consider alternative products to Gib, and it jolted those authorities into realising they do have flexibility in this space.
“The establishment of the Critical Materials Taskforce to prevent building product shortages bringing the industry to a standstill will also help pave the way for alternative products.”
When the Commerce Commission released its report into the building supplies industry in December, it said competition would improve if it was easier for new products to be introduced.
It recommended more clear compliance pathways for a broader range of key building supplies should be created, and that ways to remove impediments to product substitution should be explored.
The Government recently agreed to both recommendations, and tasked the Ministry of Business, Innovation and Employment with the work.
MBIE building policy manager Amy Moorhead says there is already a significant amount of work under way that will help address the issues identified.
“We have progressed short-term actions, and will leverage existing work programmes to help deliver further improvements to building products approved for use.”
That included the introduction of a new certification scheme for offsite manufacturing, changes to the CodeMark scheme to help new products show compliance, and new product information regulations to improve the use of alternative products.
The Government is also reviewing the building consent system to tackle barriers to competition for building products, and released its reform options paper on Thursday, Moorhead said.
“It puts forward some options for removing impediments to product substitutions and variations, and MBIE has started public consultation and wants feedback on the paper.”
But some believe more should be done.
ACT deputy leader Brooke van Velden has said that, if elected, the party would automatically allow building materials approved by jurisdictions with high-quality regulators and similar seismic situations, such as Japan and California, to be used in New Zealand.
The party would also require councils to accept any “equivalent material” certified by MBIE for use in building projects, she said.
And 2degrees founder Tex Edwards, who fronts lobby group Monopoly Watch, says the current incarnation of Branz should be disbanded, and the organisation should then be reformed.
“It needs a completely new start to become an organisation which works for consumers, not the incumbent industry provider.
“That would improve processes, and allow for better use of the industry levy which funds Branz.”
The case of Elephant board, which has not been able to break through 3% market share in plasterboard, and global plasterboard Knauf’s exit from New Zealand, shows why more reform in this area is necessary, he says.
Product competition is not just about price, but time to install and productivity, he says. “The cost of labour drops when you have products that are competitive on all fronts.
“But New Zealand uses Ferrari construction techniques and expects to get Toyota outcomes, and that is why we build houses, including entry level houses, for four times international best practice costs.”