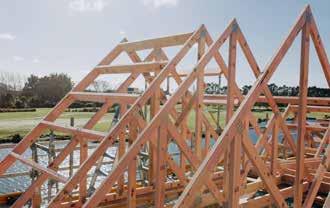
3 minute read
Tight summer ahead but the end is in sight
The August ‘Delta’ lockdowns stopped sawmill production right when mills traditionally start to build stock for the busy summer months and the Christmas maintenance shutdowns. As a result, the market looks set to be tight again this summer. This dynamic is being mirrored around the world, and is worse in Australia than here.
Looking further out there are several key demand and supply forces that will come into play. On the supply side, mills have tweaked as much volume as possible. Red Stag Timber and Carter Holt Harvey Woodproducts (CHHWP) have initiated plant upgrades, and that volume will come onstream in 2023. Waiting times, shipping delays and steel price increases have made plant purchasing expensive and slow compared to a few years ago. The only spare capacity in the market now is from the new Red Stag Wood Solutions factory producing Cross Laminated Timber (CLT) and, next year, glulam. The glulam will be lintels and beams out to 17m long from around March 2022. CLT is experiencing strong uptake in mid-rise buildings, as well as mid-floors and stairs for townhouses. The key to making that work is to design the building with CLT use in mind from the concept stage, rather than trying to get it into already-consented plans.
Advertisement
There are a number of forces that will both reduce and increase timber demand in the years to come. Key among factors set to reduce demand are rising interest rates, increases in building costs closing the speculative build window, low population growth and practically no immigration for the last two years. At 47,000 building consents – even if only 40,000 are actually getting built – we are very rapidly filling the housing shortage that developed since the Global Financial Crisis (GFC).
However, it’s not all doom and gloom. Firstly, there is sufficient momentum in the market to ensure two strong summer build seasons for the next two years.
Secondly, once Omicron circulates throughout New Zealand it will be harder to justify stringent border controls and the current MIQ system. Easier migration should follow. Those 20–30,000 kiwis in the MIQ queue trying to come home will add to demand.
Thirdly, there are regulatory levers waiting to be pulled pending availability of timber to fulfil the regulatory agenda the Ministry of Business, Innovation and Employment (MBIE) is driving around healthy homes and climate change. On healthy homes, MBIE has delayed introducing changes to wall thickness/insulation requirements so as not to put pressure on the already-tight structural timber market. They still plan to introduce the requirement for higher insulation and thicker walls once timber supply for ‘wider’ (150mm) timber comes available. 2023 would be a logical time to roll this out. On climate change, it is well recognised that wood reduces atmospheric carbon whereas steel and concrete add to it. The carbon within building materials is known as Embodied Carbon, and amounts to around 10 percent of New Zealand’s emissions. The government has reducing it in its sights in the form of the ‘Building for Climate Change’ regulation. This will require building designers to complete Life Cycle Assessments of the emissions of the buildings they design. Caps will be put in place from at least 2024, or potentially 2023. The caps will limit the carbon per square meter of building allowed, and will need to be met to obtain a building consent. The caps will gradually reduce this decade, driving out Embodied Carbon.
There is international recognition that emissions need to reduce by 50 percent this decade, and this is an easy area for government to make change. Those trying steel framing will have a hard time getting building consents under this regulation. Balancing all these factors up we expect good supply-demand balance from 2023, and stable pricing. There may be a small timber price increase next year, but it is still far below the 45 percent plus increase in heavy steel pricing during the last year or so.
Marty Verry, CEO, Red Stag Group. Red Stag Timber is an independent, privately owned timber company, based in Rotorua. It is currently New Zealand’s largest sawmill, focussing on producing high-quality timber products for the residential and commercial construction markets in New Zealand, Australia, and the Pacific Islands. A recent addition to their production portfolio is Cross Laminated Timber. For more information visit www.redstag.co.nz