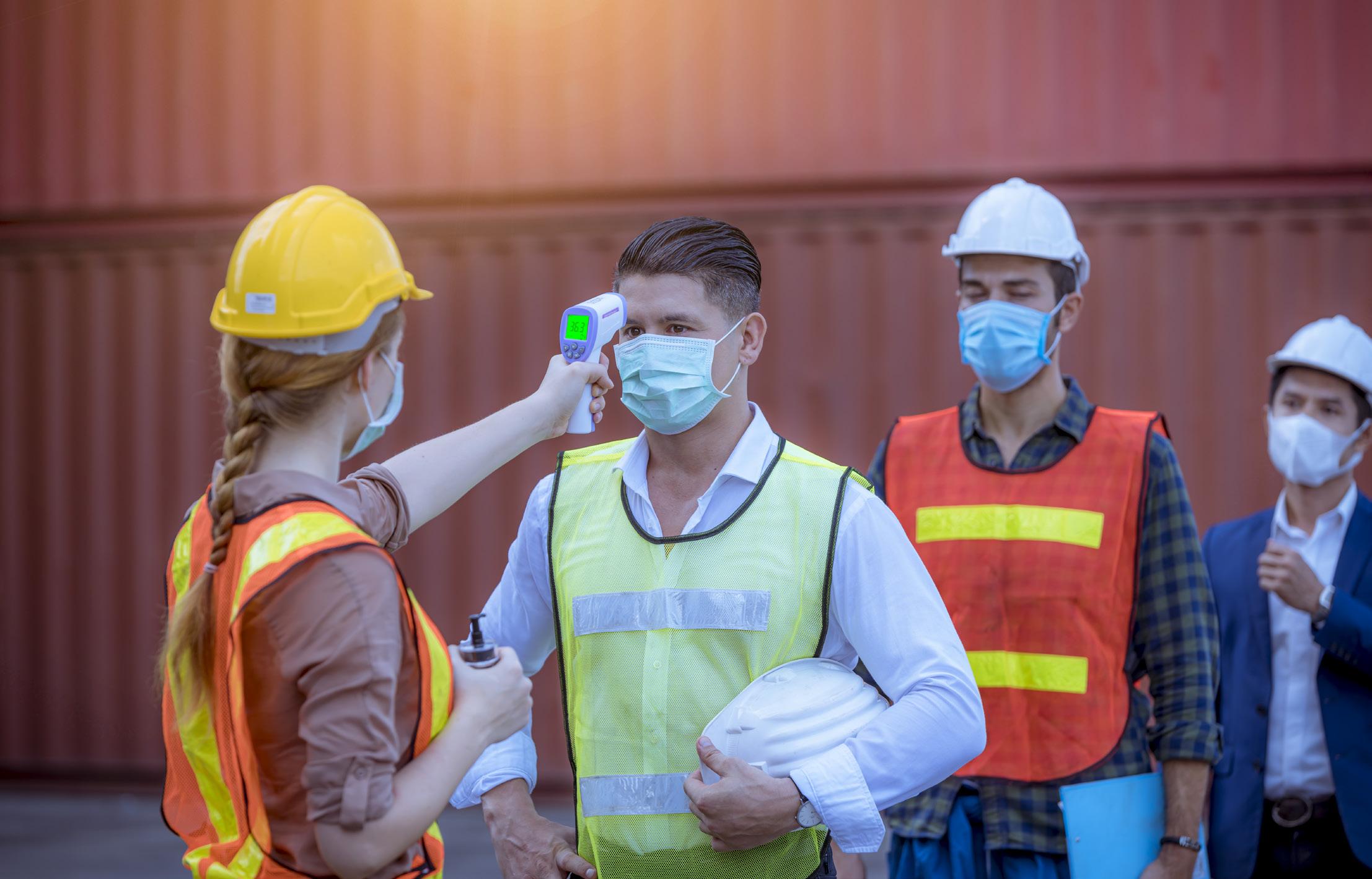
7 minute read
Production in the
Production in the New Normal Collected from CCN Members
Your production crews are essential workers and can't work from home. With COVID on the rise again across the country, this presents new management challenges every day, mainly to keep people safe and keep people feeling safe. Sometimes those are not the same thing. What happens if someone gets symptoms? What happens if someone is diagnosed? What if they come to work, regardless of your policies? What's the threshold for sending someone to quarantine? We're all learning together what works and work to keep crews in the field. Here are some of the interventions CCN members have been taking. As always, please consult your local ordinances as well as the CDC for the most up-to-date information.
Mindset
The biggest thing we did was switch mindsets and replace the word “issues” with “opportunities” COVID is a change agent allowing us to renew relationships with employees, subcontractors, customers, and stakeholders. We're now a stronger company because of these opportunities. It was a bit thing early on to not focus on negatives, to reframe those, and see the opportunity. We have to give up the short term for the long term. It’s easy to say we can throw around money from loans. If you can make lasting changes to help the company grow and be sustainable, there will be more dividends down the road.
There is opportunity in chaos.
Culture is a really big thing in our organization and making sure people feel we’re all in this together is a huge deal. So many opportunities have come out of the crisis. Our margin is up, and people have stepped up. We’re going to be a stronger company at the end of this. This made us a better company. We’ve had to strip everything in our company and rebuild. Now leads are up and there's heat on the demand side.
Incentives
We instituted hazard pay based on the PPP loans, which seems to be a mixed blessing. People were excited at first but got used to it pretty quickly and it pales in comparison with the nightly news, so it hasn’t been as effective at keeping people working as it was. We said the hazard pay is yours to keep if you earn it. The books are open and the profitability of each job is there for anyone to examine. If the crews can find efficiencies and increase productivity, and we can be profitable at a higher wage, we’re happy to pay it. Our incentives were focused on the long-term sustainability of the business. We did deep sales discounts for the salespeople, which then also benefited production and kept people working. We also implemented increased commissions, unlimited OT, and 40-hour minimums. We put a lot of money back into the company, which was difficult to do. We had to get everyone on the same page about how the biggest gift we can give them is uninterrupted business and continued employment. Everything became about making that happen. As a primarily external contractor, we haven’t had to incentivize working, because there haven’t been many interruptions to our sales. That may change, but for now, we’ve focused on keeping things as normal as possible. We didn't go with hazard pay, because we had to shut down. We had to go in the opposite direction and warned people they may come back to a reduction in pay. We didn’t end up having to do that with the PPP loans we received. We even gave some raises out that were scheduled with annual reviews. We offered discounts in April, which got the gears moving again, now we’re looking at price increases because demand is up.
We job costed and confirmed there's room for overtime, so we turned on unlimited overtime for 8 weeks to make up the 6 weeks we were out and are evaluating keeping unlimited overtime on through the rest of the year. We downsized by 30% in anticipation of the slowing economy, which was a good opportunity to get rid of B and C players. We are hiring now and being very picky.
Absences
The most successful thing we did was to work with individuals in our in-house workforce. We didn’t issue blanket policies but talked one-on-one about their comfort zones and individual circumstances. We lost some folks along the way, but now we have an amazing team invested in the sustainability of this business. We sent a letter saying they have to stay home during the lockdown and when it is over, they can continue to stay home, but we'll have to terminate and cut off medical benefits once the office is open again. Everyone is now back at work. We have much closer relationships with our subcontractors. They’ve been essential in keeping jobs going.
Cases
We did have one employee test positive for COVID-19, but fortunately, it didn't become a mutiny or turn into an outbreak because we’ve been so militant about social distancing that other people around him didn't feel threatened. We had one positive case, a crew member. Luckily early on, we isolated crews. The field crews always work with the same team so if we did have an outbreak, it would be limited to that team. We "contact traced" and only had to quarantine him and his working partner. You can’t prevent one case — depending on who people live with or where they go, they will be exposed. What you need to prevent is cases two through ten. We quarantine employees if they're symptomatic while they wait for test results or until their symptoms resolve. Usually, the teams around them have continued to work, unless someone is in close physical contact with them for longer than 10-15 minutes and we send them home too. This is why social distancing is so important.
Operations
Meetings happen in the warehouse or the parking lot. We do monthly and TQM meetings using Zoom. Fortunately, we have everything in the cloud, including our financials and job info. We’ve done town halls with the entire company over Zoom. We shut down for eight weeks. The production managers and sales team kept working. Fortunately, everyone is back now. We’ll never get back the two we were shut down, but it’s allowed us to get our ducks in a row. Subcontractors were a critical component in providing timely service.
Supply Chain issues
We communicated more proactively and frequently with vendors. We haven't, fortunately, had supply chain issues, and have been enjoying renewed relationships with vendors, new materials, deeper discounts, and better payment terms. We haven’t experienced supply chain issues. Our main issue is getting permits, with all the deficits at the state and county level. Permitting is going from 4-6 weeks to 4-6 months. So now the challenge is to sell jobs that don't require permits to fill in the time until the permit jobs can get done.
Scheduling
Scheduling changes took a lot of time — more time communicating with customers and teams and more time reading changing regulations. But with a lot of communication and patience, we've been able to keep everyone satisfied. We did have a fair amount of customers putting off their projects for safety reasons, but they've mostly come back on our schedule. Flexibility was key. We were shut down for six weeks by our local government, so we had a lot of time to figure out rescheduling. A lot of our work is inside work and we had a ton of people who didn't want us in their houses, but with the enhanced PPE and everyone earning more, we have recovered to about 70% of our old business.

Safety Measures
If we’re in the home, we wear masks and require homeowners to wear masks, temperature checks at the beginning of the day and keep hand sanitizer everywhere. Masks are essential. According to the CDC, it’s becoming more and more clear the virus is spread through respiratory droplets. Catching those droplets is a big priority. We’ve spent $5,000 in PPE by now, but our governor has issued a $10,000 fine if companies show up without PPE, so the $5,000 is still a bargain. CDC guidelines were a major cost, particularly the amount of time we spent getting them implemented. Getting PPE, sourcing sanitizer, and sewing masks, was a huge part of the job and continues to be an ongoing challenge. Social distancing seems to be a universal intervention. We’ve asked people to stay six feet away from crews and customers. Crew sizes are limited to two men across the company, which led to efficiencies we didn't expect and has prevented outbreaks. We’ve instituted washing stations in the truck with buckets for disinfecting and sanitizing right at the job site. The biggest thing for us was the messaging — pushing information out to employees about the rules, why they are what they are, and how they change. With cases spiking across the US and regulations shifting every day, keeping crews in the field has been a constantly shifting challenge. Don’t hesitate to reach out to CCN if you have questions or ideas.